2025 Author: Howard Calhoun | [email protected]. Last modified: 2025-01-24 13:10
To cover materials in our time, a whole range of different technologies is used. There are vacuum coating technologies, electron-proton radiation, high-temperature fusion and many others.
Coating steel with titanium nitride
In the modern world, "gilded" decorative ornaments and products are becoming more and more popular. In industry, this is hardening (sputtering) of tools and parts with titanium nitride. This chemical element has both an external decorative appearance and valuable operational qualities - high hardness, resistance and chemical inertness. In industry, titanium nitride coating is carried out:
- Vacuum deposition method. It is implemented in various ways - ion deposition, a plasma phase condensation system and sputtering in magnetron installations: PVD (Physical Vapor Deposition), or FOP technology.
- Chemical Vapor Deposition Method: CVD (Chemical Vapor Deposition), or CVD technology.
- Plasma spraying in microwave plasma torches.
- SHS technology (self-propagating high temperature synthesis).
Coating steel with titanium nitride by deposition methods gives good quality results, but requires technically complex installations (vacuum, steam-gas) in industrial enterprises. In addition, it requires specific equipment, materials and industrial gases (eg nitrogen). In addition, toxic waste is generated in electroplating shops.
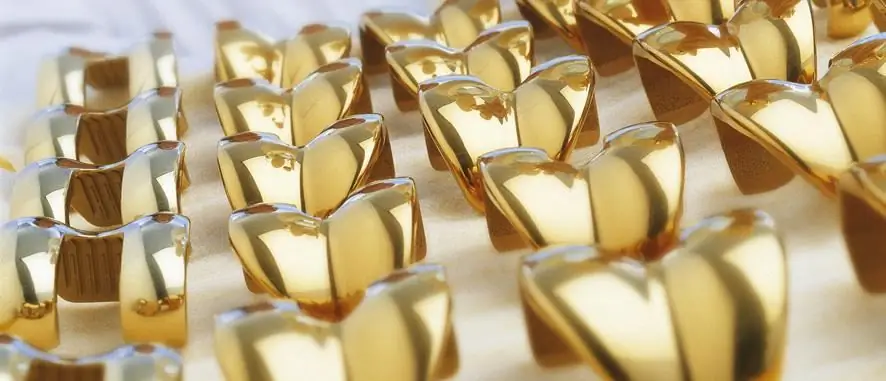
Plasma installations. Process
In plasma-type installations, titanium nitride coating is carried out by electro-plasma sprayers using ready-made powder raw materials (titanium nitride in powder form). Plasmatrons for spraying are relatively simple, the process is carried out there without vacuum and a special gaseous environment. But in order to reduce the oxidation of titanium nitride by oxygen, argon is used to form a plasma. It has inert properties. Nitrogen is used in the microwave plasma torch. This powder coating technology can be used in small equipped rooms, such as private businesses.
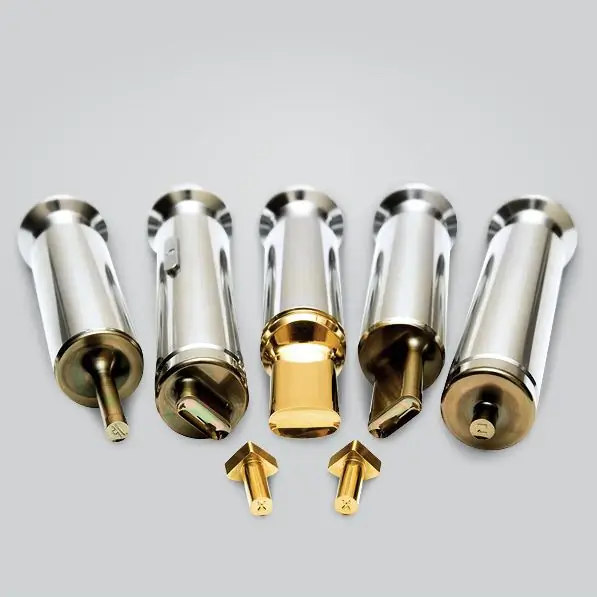
Disadvantages of the plasma spraying method
In plasma-type installations, titanium nitride coating technology has the following disadvantages:
- weak adhesion. Coating adhesion strength is inferior to PVD or CVD methods, spraying tends to settle;
- film covering the surface is strictly uneven;
- decorative properties of such a film of poor quality;
- sputtering over a certain period of time can be done several times, so the product is prone to wear.
Obviously, if titanium nitride coating is carried out in small, poorly equipped rooms, the result has significant drawbacks. This coating is used only for decorative purposes. For example, this quality is required in the production of souvenir products, furniture fittings, jewelry, etc.

Fire technology
In high-temperature synthesis, titanium nitride is coated in closed reactors using heating of the finished product. In such installations, the coating is obtained clean and uniform. It surpasses known composite materials in strength, hardness and refractoriness.
Heating the reactor to high temperatures occurs due to exothermic processes. As a result of the reaction of several chemical elements, a part is formed. The temperature reaches 4000 degrees. So you can get excellent pure nitride, diborite of titanium, silicon and aluminum and other materials with finished coatings. The process of coating with titanium nitride in the variants of high-temperature powder synthesis can be carried out additionally. In the new SHS reactors, any material turns out to be unusual and exquisitely decorative.
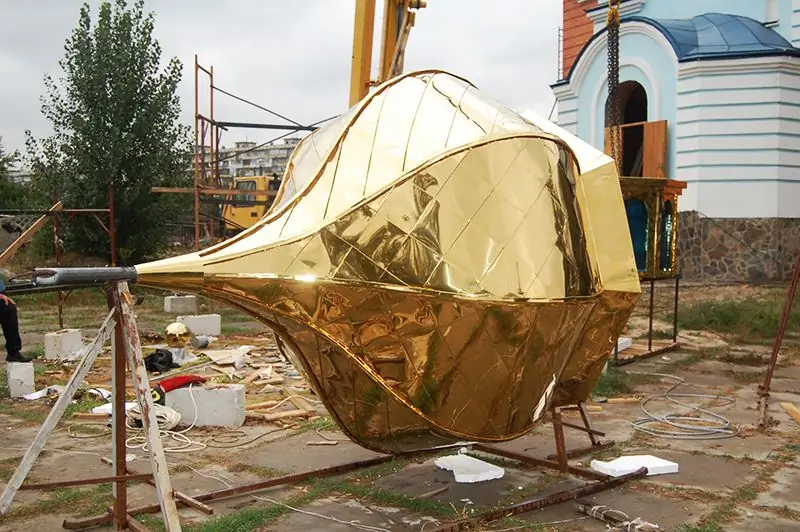
Advantages of titanium nitride coated materials
These include:
- significant resistance to mechanical damage;
- variety of coating colors;
- functional durability;
- sustainability of innovative production;
- convenience and ease of use;
- is used in many areas of production, from decoration (gilding) of church domes to the production of souvenirs.
It can be argued that the cost of titanium nitride plating in production is much lower than in other industries where gold plating is required. For example, one square meter of a stainless steel sheet with "gilding" will cost approximately 2.5 thousand rubles. The TiN coating does not tarnish and protects the material from rust. The service life of the titanium nitride shell is much longer. This connection is resistant to temperatures of 800 degrees.
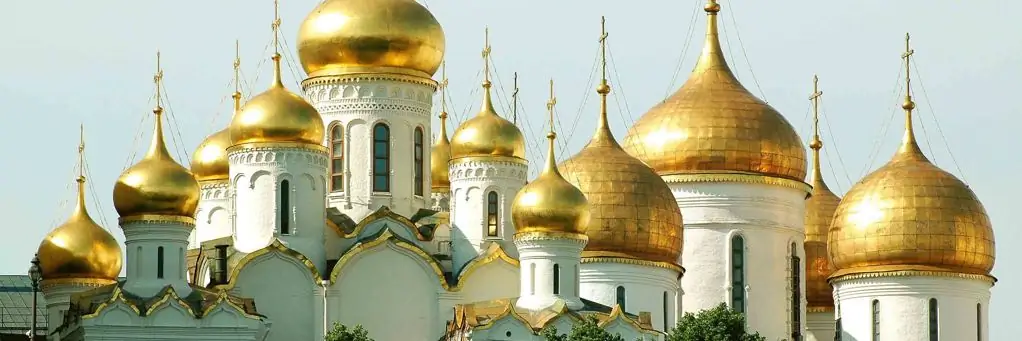
Conclusion
The coverage being carried out has many features. Nitride coating is used in the manufacture of integrated circuits because this material is both a conductor and an insulator. Spraying gives the surface a different flower, the products are more decorative. It is the color of gold, burgundy, green and blue, as well as silver and crimson All of them are stable, do not fade or wash out.
Recommended:
Food stainless steel: GOST. How to identify food grade stainless steel? What is the difference between food stainless steel and technical stainless steel?

The article talks about grades of food grade stainless steel. Read how to distinguish food stainless steel from technical
Abrasive powder: production, consumption. Where can abrasive powder be used?
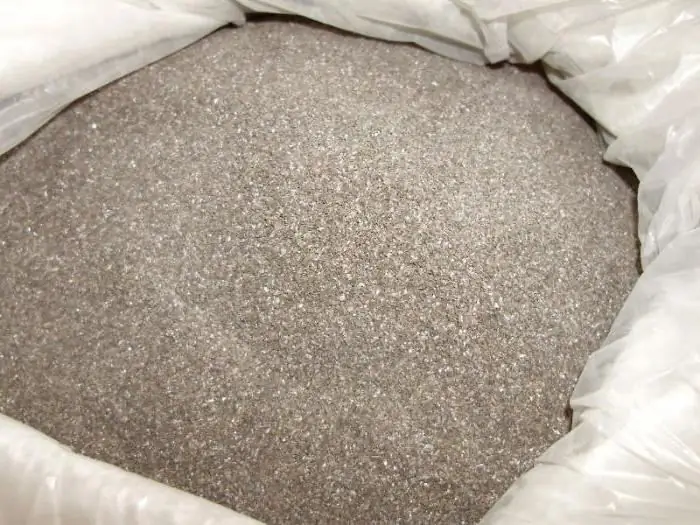
Abrasive powder is mainly used to clean metal surfaces from rust. Most often, for this purpose, its varieties such as cooper slag and nickel slag are used. Diamond powder is used to make abrasive pastes and grinding tools
Zinc coating of metal: technology and methods
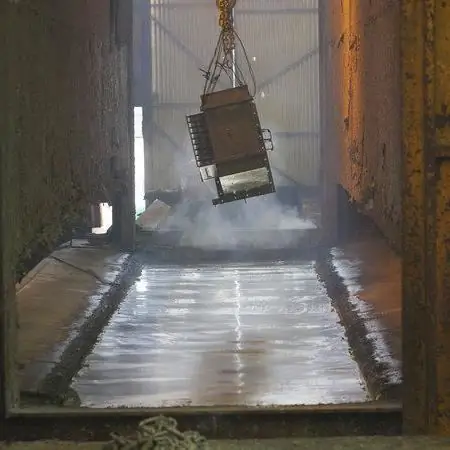
To protect metal from corrosion, many methods and methods have been created. Their essence lies in the fact that a special substance is applied to the surface of the metal. At the final stage, a thin film is formed. It prevents the ingress of moisture, oxygen, and aggressive substances to the surface. Among these methods, metal galvanizing is distinguished. It is the most efficient
Coiled galvanized steel with a polymer coating: characteristics, purpose
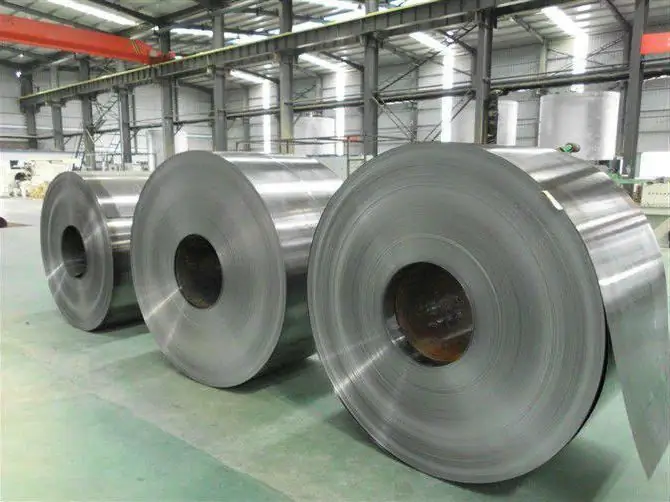
Rolled steel is one of the most common types of rolled metal. To make a successful purchase of this material, you should know several important features
Cataphoretic coating: description of the technology and its advantages. Corrosion protection methods
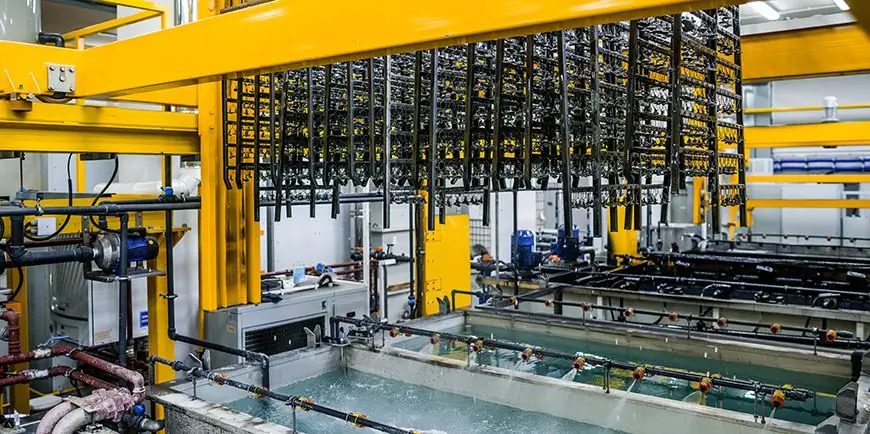
Techniques for applying external coatings represent the most extensive group of methods for the anti-corrosion protection of metal. Priming is often used in the protection of car bodies, which are subjected to various kinds of influences that contribute to the development of rust. One of the most effective methods of such protection is a cataphoretic coating, which simultaneously combines elements of physical and chemical insulation