2025 Author: Howard Calhoun | [email protected]. Last modified: 2025-01-24 13:10
To protect metal from corrosion, many methods and methods have been created. Their essence lies in the fact that a special substance is applied to the surface of the metal. At the final stage, a thin film is formed. It prevents the ingress of moisture, oxygen, and aggressive substances to the surface. Among these methods, metal galvanizing is distinguished. It is the most effective.
General information
As mentioned earlier, zinc plating is the process of applying a special substance to the surface of a product.
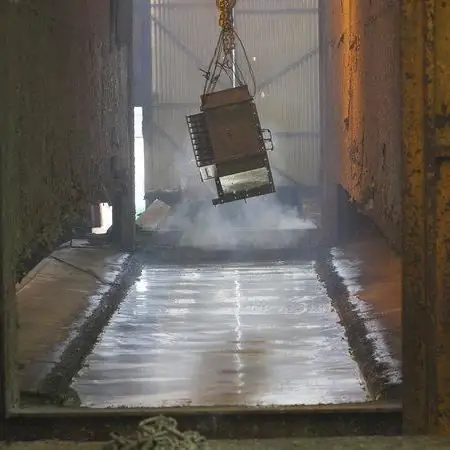
These solutions are based on zinc, which is the most suitable starting material. It prevents corrosion and also protects the surface from the effects of aggressive substances. The processed sheet has a number of advantages:
- increases the strength of the product;
- resistance to various temperatures;
- not exposed to aggressive substances;
- increasesproduct life;
- product does not oxidize.
Technological basis
Zinc coating of metal is a popular procedure all over the world. This process consists in the fact that a special zinc solution is applied to the steel surface. After that, a thin film is formed, which performs protective functions, that is, prevents corrosion. Corrosion changes the structure of the metal and renders the product unusable.
How does it rust?
As mentioned earlier, products are affected by moisture, as well as oxygen and corrosive substances.
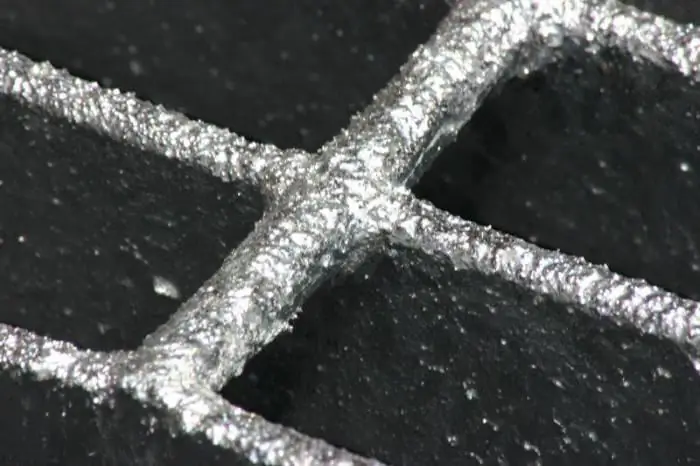
Their molecules get into the deep structure of the metal, which leads to rust. As a result, holes appear on the surface. This process can take a long time. Zinc solution is used to slow down the oxidation process.
Steps
Zinc coating of metal consists in covering various types of products with a protective zinc film. To perform this procedure, you must have special equipment. Each element of the device must not be exposed to moisture and aggressive substances. The galvanizing process is divided into the following steps:
- Preparatory. First of all, you need to put the product in order. Its surface must be cleaned of various substances, and then degreased. Next comes the etching process. The metal product is lowered into a container with an acidic environment. As a rule, a sulfuric acid solution is used. By etching the metal on the surfacean oxide film is formed. This means that the zinc solution will last longer. At the final stage, acid residues are removed from the product and dried.
- Galvanizing process. This stage consists in the fact that a solution is applied to the prepared surface. To make it, it is necessary to melt zinc in a special bath at high temperature. When the solution is ready, a metal product is immersed in the bath and kept for several minutes.
- Drying the product. The galvanized product is dried at room temperature.
The process of galvanizing metal products takes place in special baths.
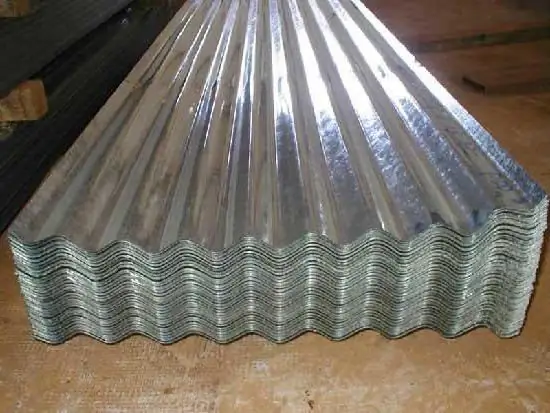
If necessary, they are equipped with sockets. Despite their significant volumes, they also process a large number of small products. Thus, equipment for galvanizing metal and hardware can be not only small, but also large.
Main Processing Methods
The most popular way to protect metal products from corrosion is zinc plating. There are various ways of this process. Each of them is used for a certain type of metal. Some species may react with zinc. There are four types of processing: hot, cold, thermal diffusion, galvanic. Let's consider each type in more detail.
Hot
Coating products in this way is popular in many countries. Its main positive properties are high quality and long service life. That's whythis method has become one of the best. There are also a number of negative properties. First of all, the method is not environmentally friendly, as many chemicals are used in the preparation and galvanizing stage. In addition, there is a significant difficulty in hot working. It is necessary to maintain the temperature of zinc in the range from 500 to 5000ºС. To maintain this level of heating, a lot of electricity is expended. Hot dip galvanizing of metal at home is a rather complicated process.
Technologically, the process is divided into two stages. This is the preparation and galvanizing of metal. At the first stage, they are engaged in the preparation of a metal product. Its surface must be degreased and cleaned of debris. This is followed by pickling, washing and drying.
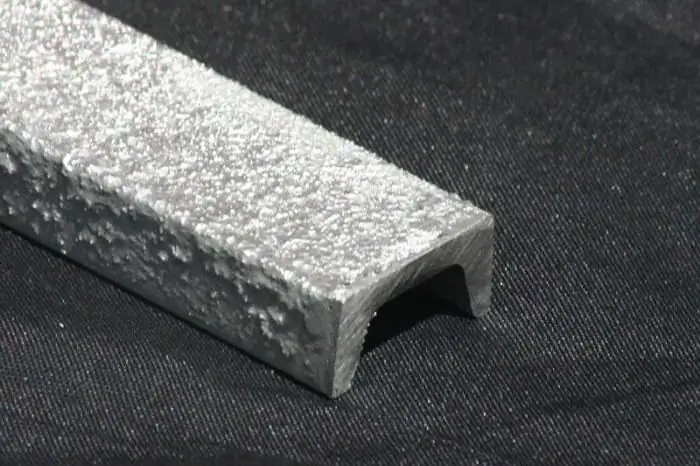
These operations are specified in the regulatory documentation.
To zinc a part, you need to immerse it in a special bath. It contains a special solution that prevents corrosion. Methods for fixing metal during hot-dip galvanizing can be different. They depend on the type and shape of the product. This technology is used in many industries. For example, for the manufacture of galvanized wire, pipes, etc.
After applying the hot method to them, the products have a long service life, that is, they are reliably protected from corrosion. Baths are the only problem. To process large parts, it is necessary to find a bath of appropriate volumes, which is quite difficult. Suchfeatures affect costs. Where is hot-dip galvanizing done? Kursk, Moscow, Chelyabinsk, Yaroslavl - this is just a small list of cities where various companies offer this service. Often they work with large volumes.
Galvanic galvanizing of metal - technology
This method is used when a smooth surface is required. The technology of galvanizing metal by galvanizing is based on fixing a substance on the surface of the product due to electrochemical action. This method is suitable for absolutely all types of metal. The product receives a uniform shiny coating. This is due to the fusion of the metal coating and zinc.
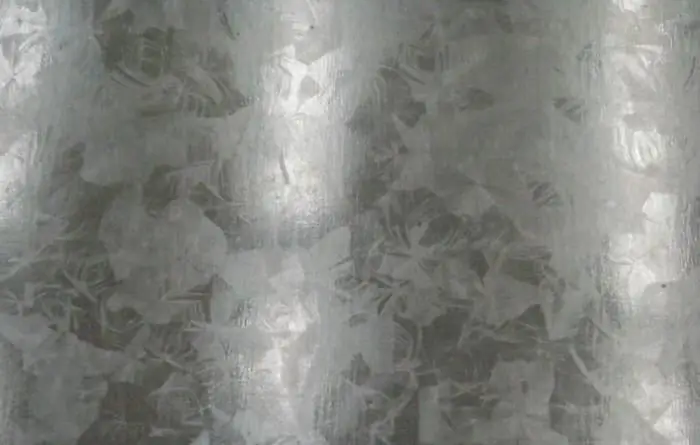
This interaction is affected by the presence of various debris or other films on the surface. Therefore, before starting the procedure, you should do the cleaning. In mass production, this is difficult to follow, so galvanizing may be of poor quality.
The galvanic method is based on immersing a metal product in a bath containing an electrolyte solution. A power source is connected to the workpiece. In this case, the process of electrolysis occurs. Zinc is exposed to it, which covers the metal part.
Pros
The main positive quality is the appearance of the product - the surface is smooth and shiny. However, there is also a significant drawback. Before draining the solution that was in the bathroom, it is necessary to clean it from zinc. With this method, a largethe amount of waste that harms the environment. Therefore, it is necessary to purchase special expensive equipment. It will release the zinc from the solution. Therefore, this method is one of the most expensive.
How to make galvanized metal at home?
This procedure is used by many masters when it is necessary to process small details. First you need to find a suitable container and make an electrolyte. The procedure is carried out in a well-ventilated area and in protective clothing, as electrolyte particles can harm a person. Contact with skin may cause chemical burns. For cooking, they take water, zinc sulfide, magnesium and vinegar. The finished concentrate must be filtered. Next, the metal part is lowered into the container and the anode product is prepared. A copper wire is attached to a small piece of zinc, which is connected to the mains. The product is lowered into the electrolyte and the processing process begins. After that, the metal part is dried. Galvanizing metal at home is quite easy to do.
Features of the cold method
In recent years, this method has become widespread. Its essence lies in the fact that the metal product is painted with special substances that contain zinc. This method does not require special skills. However, there are also disadvantages: finished galvanized products are subjected to mechanical stress. In addition, it is necessary to constantly monitor the technical personnel who prepare the solution and perform the work. As saidpreviously, this method is quite simple. Therefore, equipment for cold galvanizing of metal is not required. Work must be carried out in accordance with sanitary and hygienic rules. Using this method, pipes are processed, as well as products that are in a fixed version. To do this, prepare the solution and apply it to the product with a brush or roller. The only cold galvanizing equipment that is used is a spray gun. It helps to get to inaccessible places and perform painting evenly and efficiently. Among the shortcomings, many users note low reliability.
Thermal Diffusion Galvanizing Technology
This method has been used for a long time, but it is still popular today.
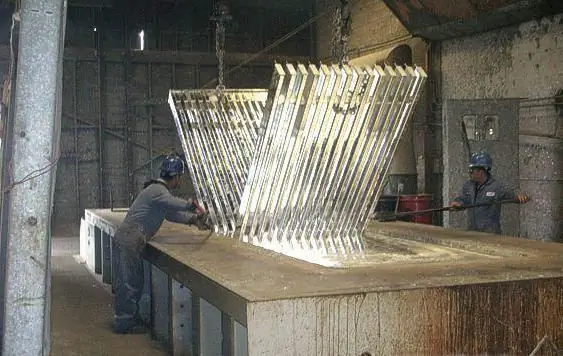
It was first used in England at the end of the 19th century. The invention became famous thanks to the famous scientist Sherard. However, this method was quickly forgotten, replacing it with another one. Its revival falls on the end of the twentieth century. The technology of the thermal diffusion method lies in the fact that the surface of a metal product is treated with zinc in a vapor state. To do this, it must be heated to 2500ºС. The process is carried out in a closed container with a zinc-containing mixture and metal elements in it. The technology for carrying out this procedure is determined not only by domestic, but also by imported regulatory documents.
Thermal diffusion galvanizing is performed when it is necessary to achieve the thicknessat 20 µm. The technological process is similar to hot dip galvanizing. However, there are also differences. The prepared product is lowered into a drum furnace, where processing takes place due to rotating forces. This process is completed in 3 hours of operation of this equipment. With it, various small parts are painted, such as washers and screws.
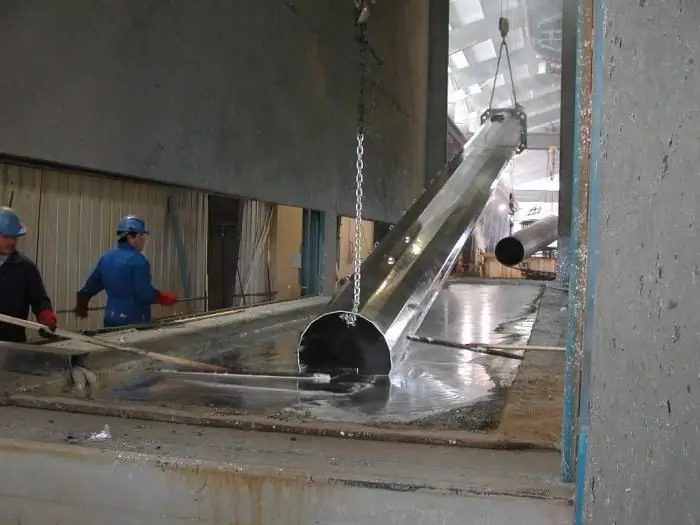
Unlike the hot method, the application of zinc dusting occurs evenly over the entire surface.
Conclusion
This process helps protect various metal parts from corrosion, moisture, and aggressive substances. There are 4 technological types of galvanizing. Each of them has its own characteristics and is suitable for a certain type of metal. The incompatibility of such components will lead to poor-quality staining and, as a result, to a decrease in the strength of the finished product. Galvanizing takes place in special baths or drum furnaces. However, the process can be done at home. To do this, you need to purchase consumables. Work is carried out in a ventilated area in special protective clothing, as some components are harmful to the human body.
Recommended:
Coating steel with titanium nitride. Powder technology
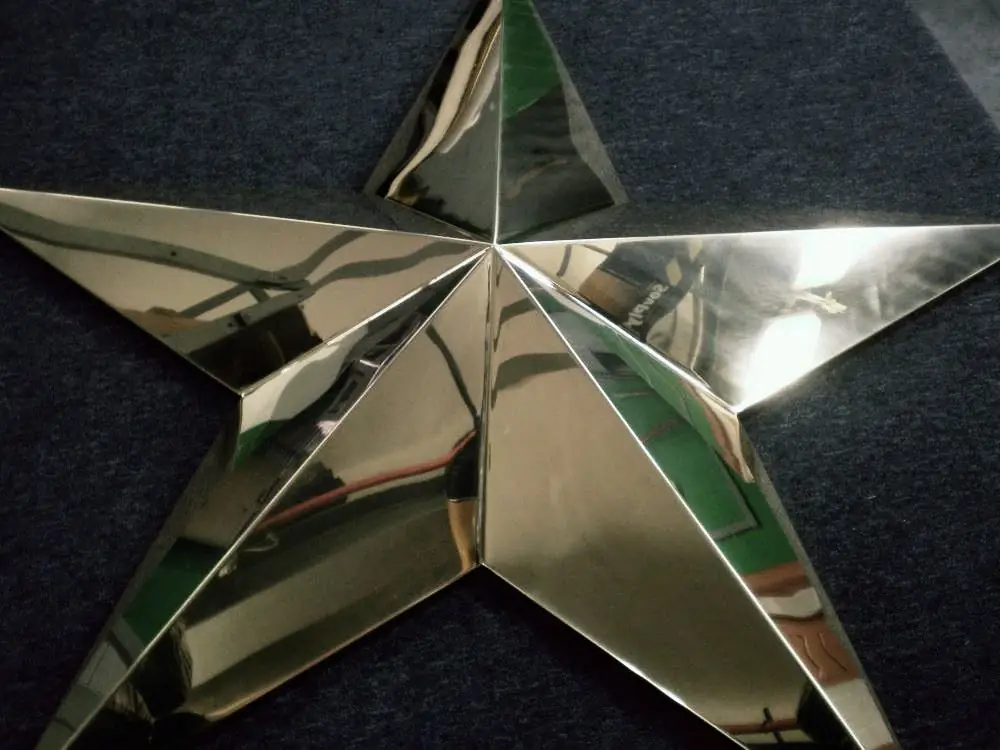
To cover materials in our time, a whole range of different technologies is used. There are vacuum coating technologies, electron-proton radiation, high-temperature synthesis and many others. In the modern world, "gilded" decorative ornaments and products are becoming more and more popular
Slaughter of cattle at meat processing plants: rules, technology, methods and methods
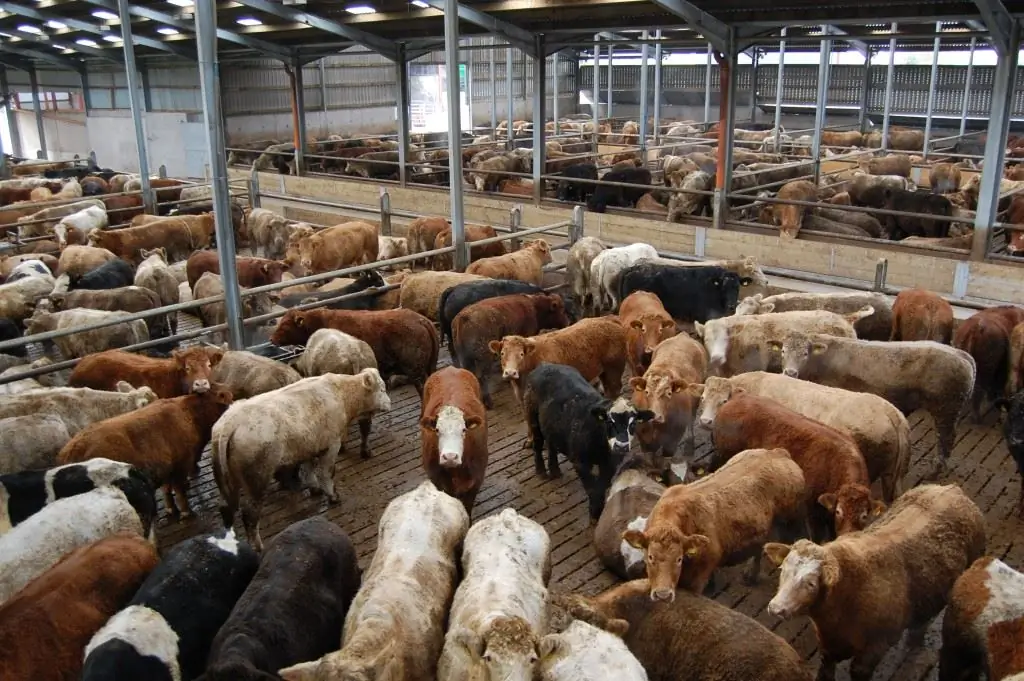
Providing the consumer basket with meat products directly depends on the slaughter and processing of cattle. Delicious beef and veal dishes are largely the merit of livestock breeders who know how to properly slaughter bulls and cows. There are various technologies, methods and methods for slaughtering cattle, which make it possible to obtain high quality meat products
Metal casting: process, methods, methods
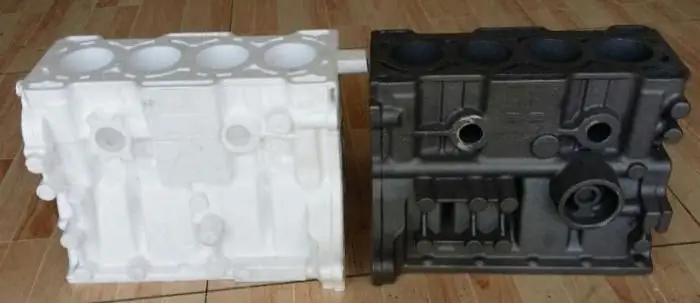
Metal is the basis of all modern civilization. In a year, modern humanity mines and processes such an amount of iron alone that before the whole world would have been digging it for at least a couple of centuries
Restoration of parts by welding and surfacing: methods and methods of restoration, features, technological process
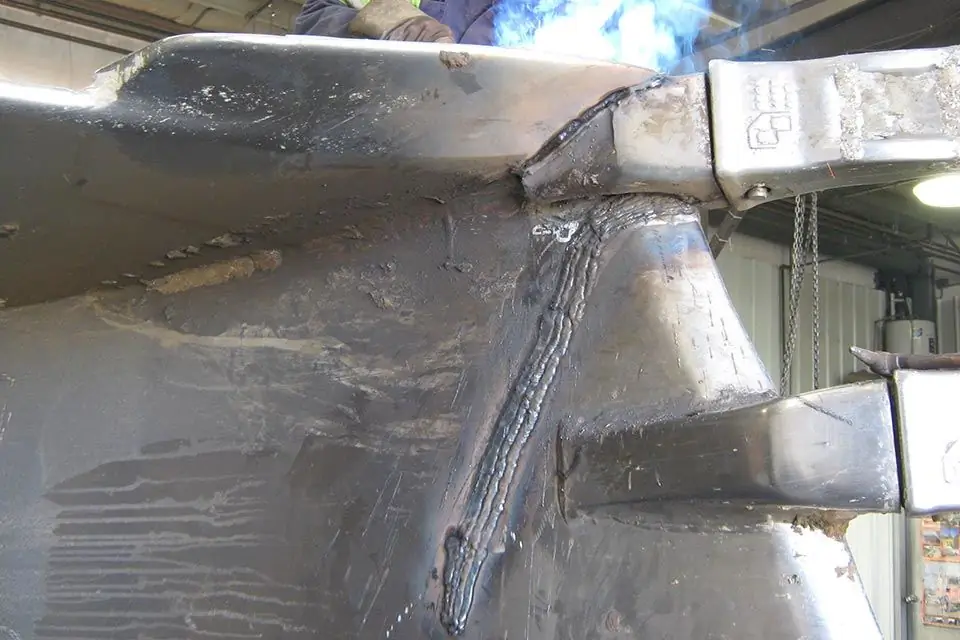
Welding and surfacing technologies allow efficient restoration of metal parts, providing a high degree of reliability and durability of the product. This is confirmed by the practice of using these methods when performing repair operations in a variety of areas - from car repairs to the production of rolled metal. In the total amount of work on the repair of metal structures, the restoration of parts by welding and surfacing takes about 60-70%
Cataphoretic coating: description of the technology and its advantages. Corrosion protection methods
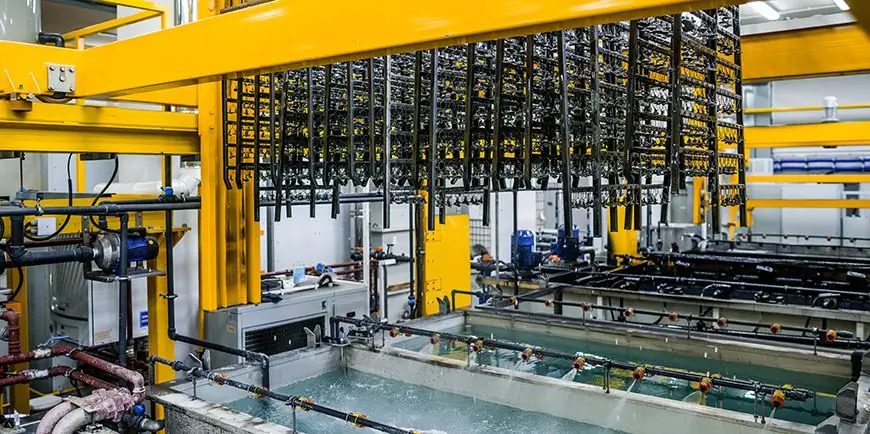
Techniques for applying external coatings represent the most extensive group of methods for the anti-corrosion protection of metal. Priming is often used in the protection of car bodies, which are subjected to various kinds of influences that contribute to the development of rust. One of the most effective methods of such protection is a cataphoretic coating, which simultaneously combines elements of physical and chemical insulation