2025 Author: Howard Calhoun | [email protected]. Last modified: 2025-01-24 13:10
Techniques for applying external coatings represent the most extensive group of methods for the anti-corrosion protection of metal. Priming is often used in the protection of car bodies, which are subjected to various kinds of influences that contribute to the development of rust. One of the most effective methods of such protection is a cataphoretic coating, which simultaneously combines elements of physical and chemical insulation.
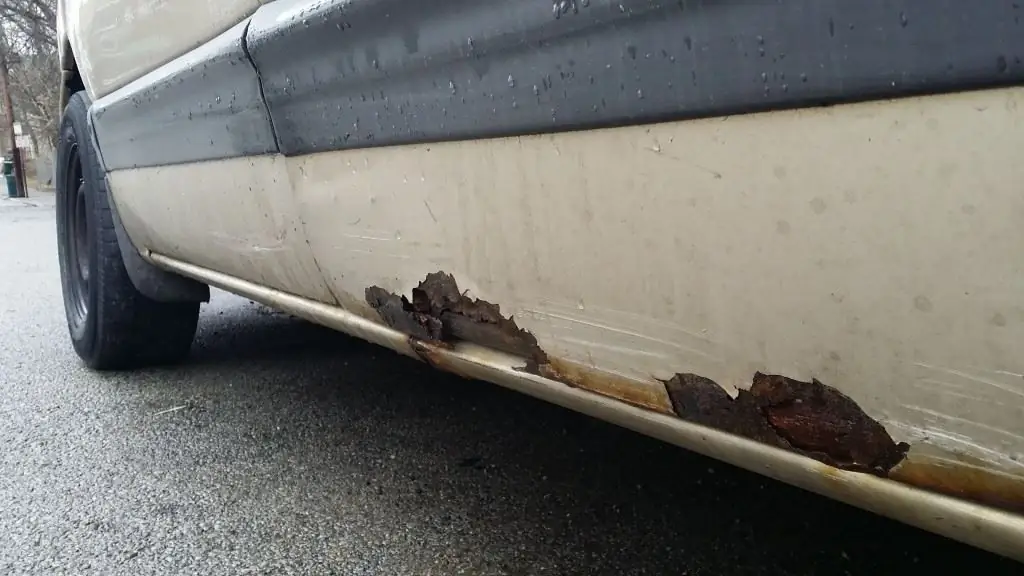
Preparation of technological equipment
The technical basis for performing the cataphoresis treatment is the limiters for body elements, including the hood, trunk and side doors. All these parts must be slightly open so that the active mixture freely fills the cavities from the inside, leaving no gaps. From the point of view of in-line production, the solution for cataphoretic coating is thus saved on the line, since the unused compositioncompletely drained into a special container and used in subsequent operations. The function of the drain channels is usually performed by holes in the bottom of the car body. Care should also be taken to ensure that they are open in advance.
Washing body surfaces
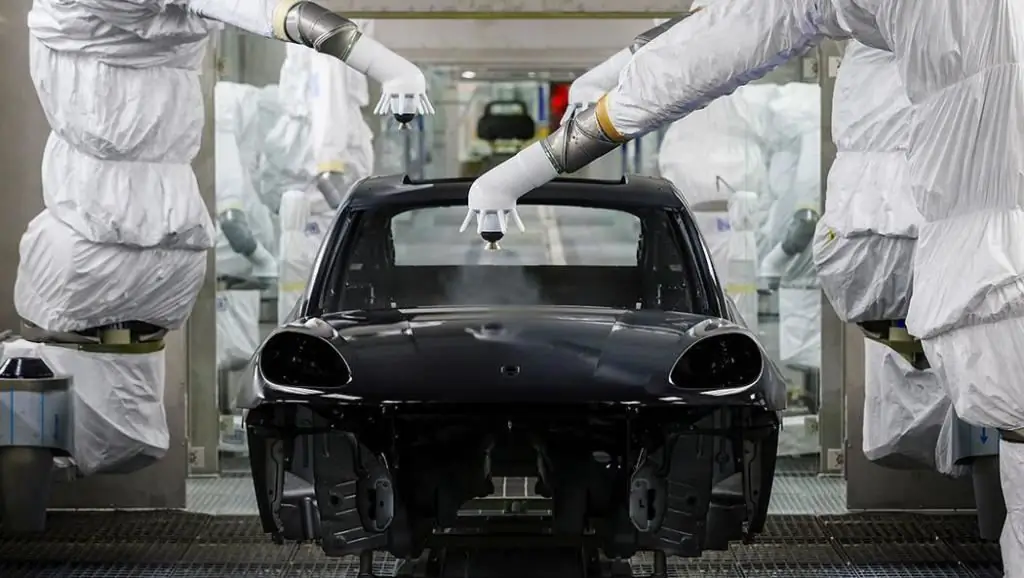
The next step in preparation is the pre-wash. Not only from the outer surfaces, but also from the inside of the body, all foreign particles should be removed from dirt and dust to welding products and factory grease. On professional lines, chambers with many nozzles are used for such purposes, directing water with a cleaning solution. A simpler option involves the use of mini high pressure washers with the connection of compressor units. In any case, the better the initial cleaning, the more likely it is to get a stable and durable protective coating of the car body with an emphasis on the formation of an anti-corrosion barrier.
Degreasing surfaces
The presence of traces of technical oil or other chemicals on body surfaces can lead to the preservation of open areas, which often become centers of rust development after damage. Therefore, it is very important to carry out the degreasing operation. Usually, before applying a cataphoretic coating, this problem is solved by spraying. The car passes through a special tunnel, where it is also supplied with water under high pressure, but with the addition of special chemicals. Practiced and the method of immersion inbaths with degreasing solutions, but this approach only pays off in high-volume, high-volume workshops.
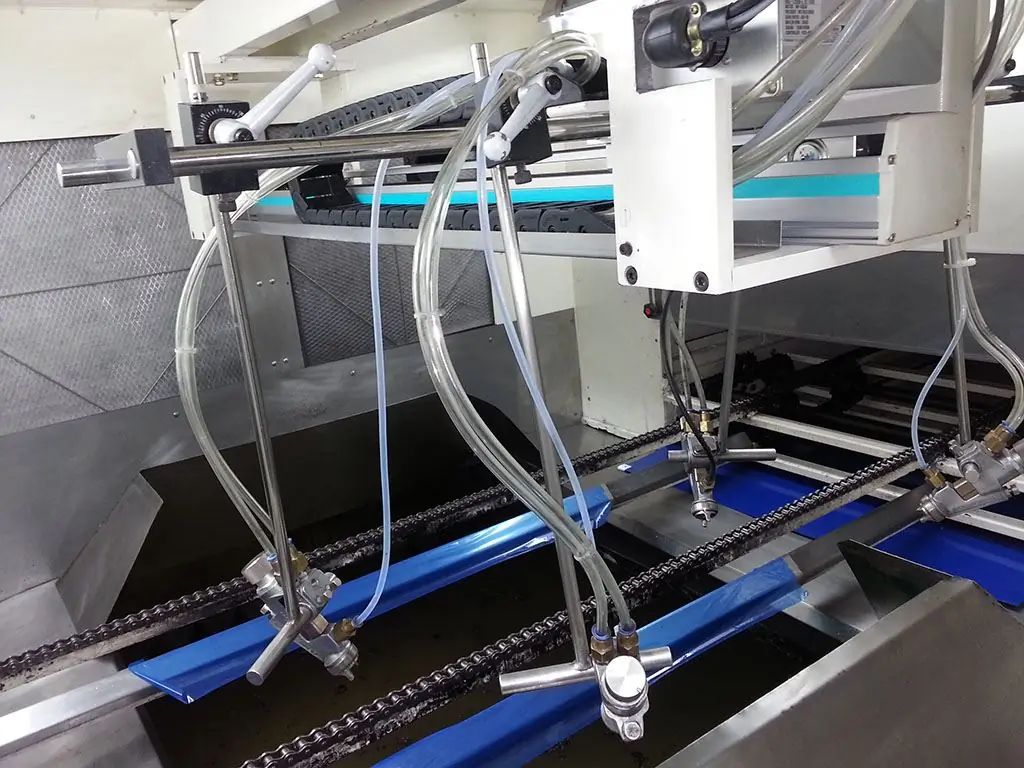
How to degrease metal?
So, what additives are used after complex washing before applying the cataphoretic composition? The simplest and most accessible material are alkaline solutions. These are useful active components, which, together with degreasing enhancers, give a good cleaning effect and basic protection. With a high degree of fat concentration, specialized tools will have to be used. For example, how to degrease metal if the surface fat content exceeds 3 g/m2? In this case, you can use specialized auto chemicals from Henkel, Chemetall or ECOHIM, made on the basis of solid and chlorinated particles of polyvinyl chloride and acrylonitrile butadiene styrene. As practice shows, the key factor in the effectiveness of a degreasing solution will not even be its concentration, but the correctly selected temperature regime during processing.
Activation and phosphating of surfaces
The transitional step between cleaning the target surface and creating a base for cataphoretic coating is phosphating. In turn, metal activation will act as a preparatory operation, which is carried out in order to improve crystal formation in the bath. For this, insoluble compounds, manganese phosphate and titanium s alts are used. They provide a settling effect on the surface, contributing to the compaction of the phosphatelayer.
Activation forms the basis of the protective coating of the car body, helping to increase adhesion. After phosphating, a coating control is carried out, in which properties such as total acidity, density, mass, etc. are evaluated. The composition of the solution can also be analyzed. The standard set of components is formed by zinc elements, fluorides and additional modifying additives, which are selected individually.
What is a cataphoretic primer?
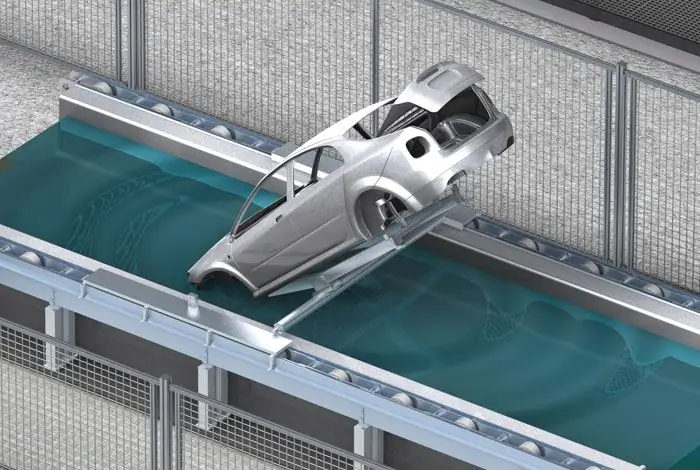
The main component of the coating is a lead-free two-component mass, which can be presented in the form of a paste or emulsion. In the latest generations, such primers are distinguished by environmental safety and high penetrating power. With the help of modifiers, the indicators of thermal stability and protection from corrosive processes are also improved. In addition, during operation, rust removal is improved without damaging the body base. Directly in cataphoresis, emulsions containing several cationic polymers are used. The formed layer is an elastic film with blocked isocyanate. Also, a pigment paste based on mineral components, binding active substances and demineralized liquid can be used in the composition.
Applying primer
The protective structure is formed in the bath, which was previously loaded with an emulsion with a paste, including the necessary additives. The average volume of the bath for the cataphoretic method of corrosion protection is 100 m3 based onfor one body. Simultaneous processing of several cars is also allowed. In this case, containers of 200-300 m3 are used.
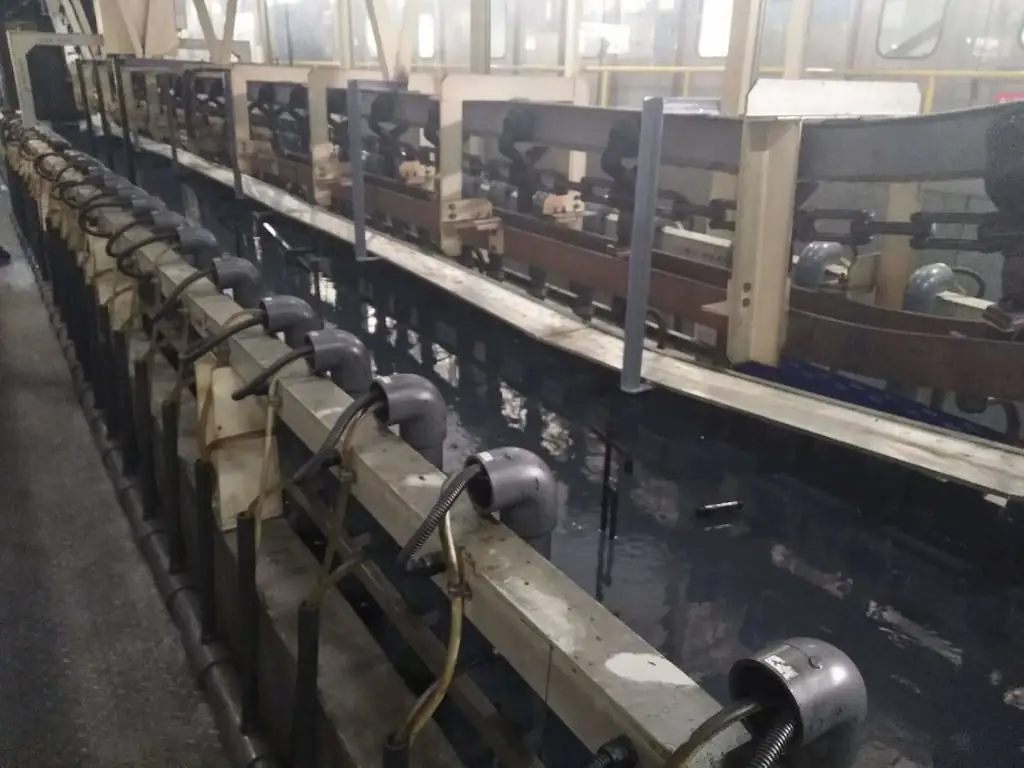
Dialysis cells with metal cathode rods are connected to the bath along the perimeter. This is an important part of the technology, thanks to which, in principle, an electrochemical effect is provided. When voltage is applied, the cataphoretic soil is charged, followed by the formation of a protective layer up to 25-30 microns thick. As for the charge parameters, the current strength should be from 350 to 700 A at an average voltage of 400 V. In time, the operation lasts 2-3 minutes.
Drying metal surfaces
Unlike other quick drying technologies, in this case, the polymerization process also has the character of a mild thermal effect with burning. For this operation, special ovens are used that allow several stages of drying to be carried out. At each stage, an appropriate module is connected with an independent burner (usually on gas fuel), which heats the air to the desired temperature. Heat flows in the direction of the body are supplied by fan installations. Moreover, each thermal exposure circuit contains filters that purify the air from the smallest particles that can harm the structure of the coating. With regard to the choice of temperature regime, much depends on the characteristics of a particular metal. For a car body structure, corrosion protection is fixed under polymerization conditions at 180-200 °C. Moreover, for each separate part, the temperaturemay vary due to special sensors. A special approach is usually applied to the roof, dashboard and bottom.
Advantages of Technology
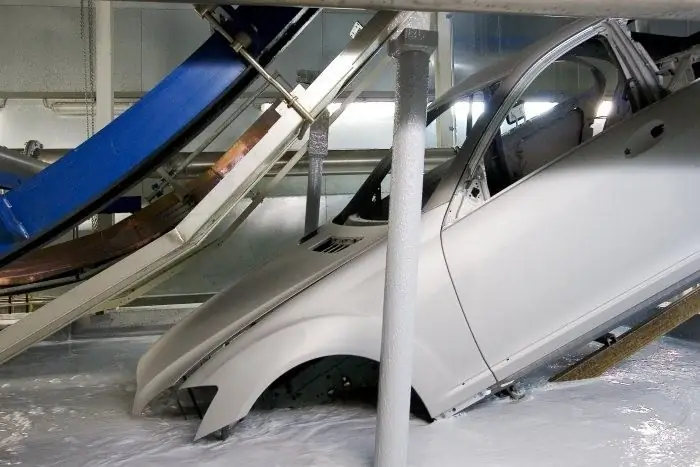
Among the main advantages of this technique is the high resistance of the soil to external negative influences, which create conditions for the formation of corrosion. Having performed rust removal with abrasives of the desired fraction at the very first stage, in the future you can forget about the risks of such damage from high humidity and s alt exposure. At the same time, cataphoresis is used not only as a technological protective coating, but also as a decorative one, if the primer solution is combined with powder paint. Other advantages of this method include high processing speed, uniform laying of the layer, high penetrating power and the already mentioned environmental friendliness.
Alternative corrosion protection methods
The closest technology of anti-corrosion protection, which in principle can be compared with cataphoresis, is anaphoresis. It is also a kind of electrolytic staining, but with some differences. In particular, the anaphoretic method of corrosion protection provides for a negative charge of the priming solution, and the target surface is associated with a positive contour. From the point of view of the quality of the coating device, this is not of fundamental importance, but on the other hand, organizational processes are facilitated due to the elimination of the obligatory grounding device for the bath and the supply of dialysis cells. In addition, the requirements forpaint deposition and drying of the applied coating.
Conclusion
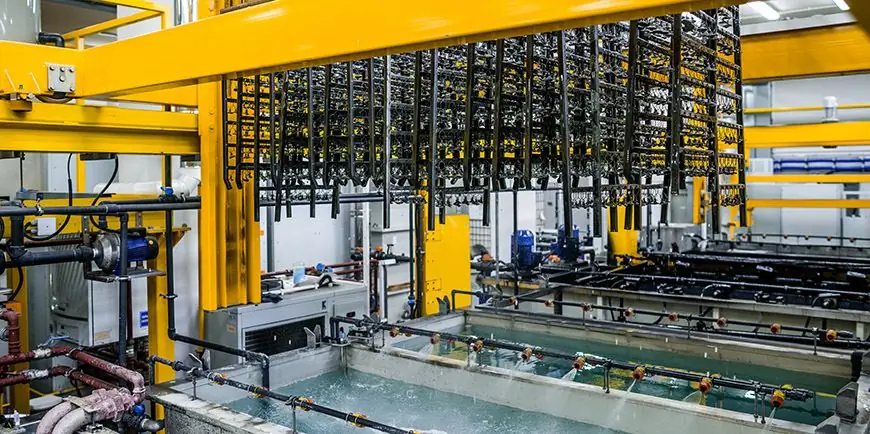
The cataphoresis technique is complex and costly. The quality of the result in this case will be guaranteed only by the competent execution of each stage of processing. The slightest violation of technology can cause the destruction of the applied soil already in the first months of vehicle operation. But in other cases, cataphoretic treatment of metal fully justifies itself as an effective way of anti-corrosion protection for many years. The secret of the formation of positive technical and operational properties after the formation of the coating lies in the balanced combination of chemical components and electrical effects on the metal structure. This is far from an innovative method, since its principles have long been used to protect pipeline networks from the same corrosion. But in relation to the protection of car bodies, we can talk about an unprecedented optimization of cataphoresis processes, albeit with high organizational costs.
Recommended:
Tread protection against corrosion. The main ways to protect pipelines from corrosion
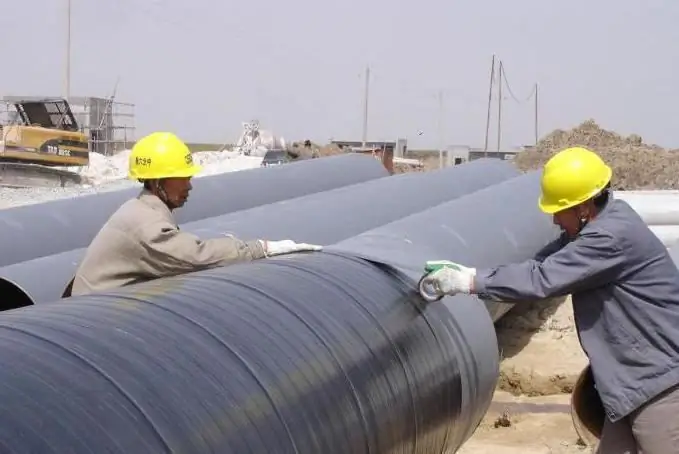
Protective corrosion protection is a universal solution when it is required to increase the resistance of metal surfaces to moisture and other external factors
Corrosion of aluminum and its alloys. Methods for combating and protecting aluminum from corrosion
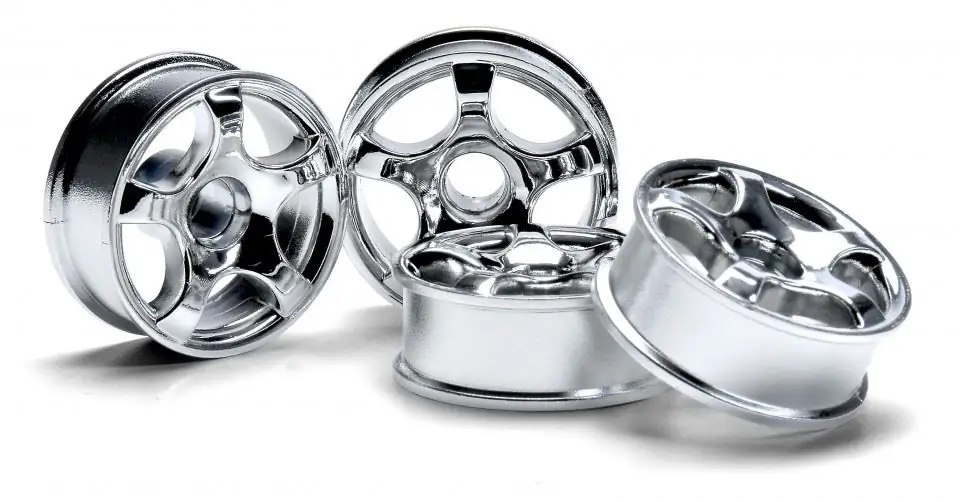
Aluminium, unlike iron and steel, is quite resistant to corrosion. This metal is protected from rust by a dense oxide film formed on its surface. However, in the case of destruction of the latter, the chemical activity of aluminum greatly increases
Corrosion inhibitors. Corrosion protection methods
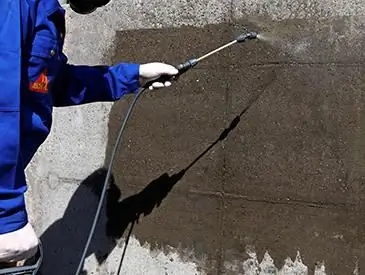
Each year, about a quarter of all the metal produced in the world is lost due to the development and occurrence of corrosion processes. The costs associated with the repair and replacement of equipment and communications of chemical industries are often many times higher than the cost of materials required for their manufacture
Zinc coating of metal: technology and methods
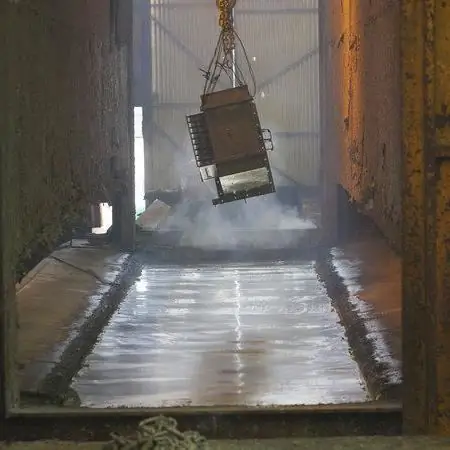
To protect metal from corrosion, many methods and methods have been created. Their essence lies in the fact that a special substance is applied to the surface of the metal. At the final stage, a thin film is formed. It prevents the ingress of moisture, oxygen, and aggressive substances to the surface. Among these methods, metal galvanizing is distinguished. It is the most efficient
Corrosion and erosion of metals: causes and methods of protection
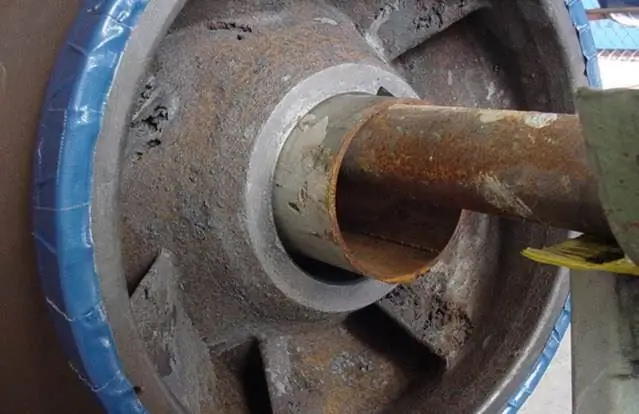
Chemical, mechanical and electrical external influences often occur in metal product operating environments. As a result, with improper maintenance of such elements, as well as ignoring safety standards, there may be risks of deformation and damage to structures and parts. This is due to the emerging processes of corrosion and erosion of metals, which in the long term contribute to the complete destruction of the structure of the product