2025 Author: Howard Calhoun | [email protected]. Last modified: 2025-01-24 13:10
The operations of machining workpieces on lathes rarely become final in the technological process. Creating holes is the main step in obtaining the desired shape of the part. But it is usually followed by a revision stage. In part, these are finishing correction measures, but sometimes methods of basic change in the parameters of the completed cut are also used. Such operations include countersinking and reaming of holes, as a result of which the operator receives a workpiece that is optimal in terms of characteristics. Firstly, the prepared recess acquires the required dimensions, and secondly, its edges and surfaces are cleaned of excess burrs and chips.
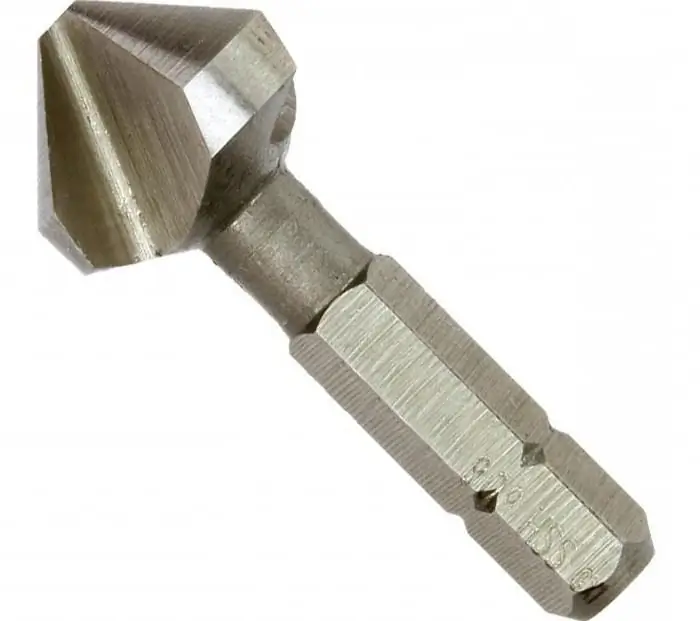
What problems does reaming solve?
Holes of different origin are allowed for the countersinking procedure. These can be cast, stamped or drilled niches, on which the reaming master will work in the future. What is the essence of this operation? She may have two purposes. At a minimum, cleaning of the hole surfaces will be ensured. This is especially important in cases where rough drilling and reaming of holes is preliminarily performed, the edges of which need to be finished. Depending on the qualityhole formation, semi-finishing or finishing countersinking can be used. As a result, the degree of smoothing of the working surfaces also changes. The task of calibration is even more responsible. In this case, the master is not limited to cleaning and adjusts the parameters of the hole, such as depth and thickness. The need for such actions arises if the initially obtained hole does not fit the target stud, screw or other fastener. After reaming, threading is just performed in accordance with the dimensions of the hardware.
What is a countersink?
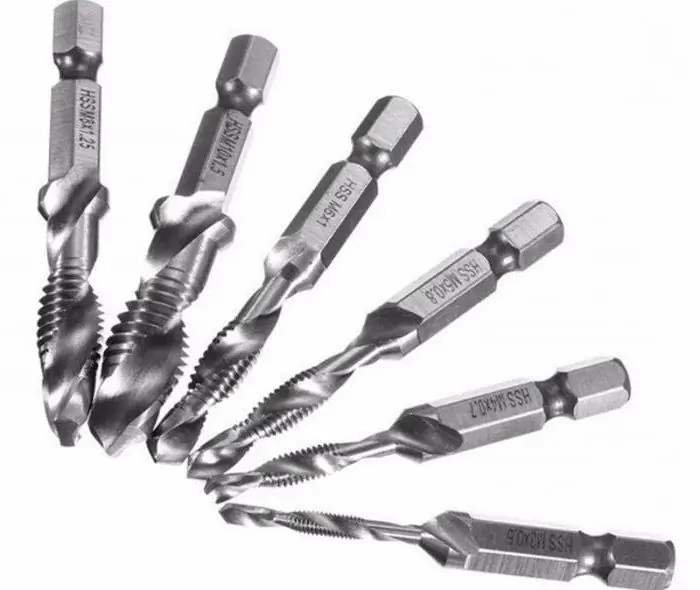
This is a cutting tool whose design is formed by a functional machining part and a holder shank. Outwardly, some types of countersinks resemble drills, but they are much stronger. And an even more important difference is the presence of at least three cutting edges, which provide more efficient removal of excess metal mass. Incidentally, this is also the case with reaming holes, which sometimes requires intensive chip removal in order to achieve a more accurate workpiece shape. But in a countersink, several cutting edges also act in some way as a tool stabilizer. This aspect ensures that the edges are processed uniformly, which affects the accuracy of the operation. However, the quality of the result will also depend on how correctly the type of instrument was chosen.
Varieties of countersinks
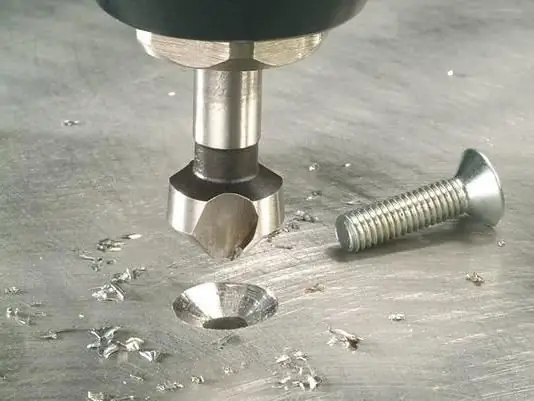
The simplest conicalcountersink models consist of a cutter and a shank. The angle of the cone in the working part can vary from 30 to 120°. A more complex variation of the tool is a cutter with end teeth. The number of teeth averages from 4 to 8. Accordingly, the more precisely countersinking is required, the smaller the surface of the cutter should be. There are also cylindrical devices in which a guide pin is provided. It enters the formed holes, thus ensuring that the formed cylindrical recess coincides with the axis of the hole. This is a universal technique in which drilling, countersinking and reaming of holes are performed with a tool of a single formation. As a result, the hole formation cycle is simplified and the quality of cleaning of adjacent surfaces is improved. Almost all models of countersinks are made of tool alloyed and carbon steels.
Reaming technique
Typically, reaming is done on drilling machines. Just like drills, countersinks are installed in appropriate chucks or clamping mechanisms. Further, the outlet parts of the holes are processed with conical countersinks. This technique forms conical recesses suitable for rivet heads and countersunk screws. Recesses for bolts are made in the same way, but already with cylindrical countersinks. This tool also performs trimming ends, sampling corners and protrusions. Both countersinking and reaming of holes on the machine are controlled by the operator. In modern models of pneumatic and electric machines, it is possible to processin semi-automatic and automatic modes. CNC machines can use similar countersink settings for serial maintenance of parts.
Deploy operation assignment
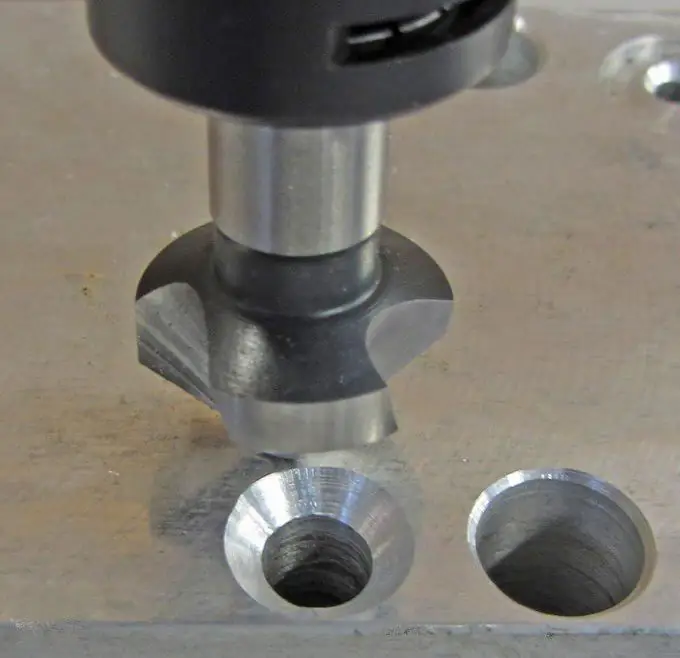
The reaming operation is in many ways similar to countersinking. It is also designed to form optimally sized holes with the possibility of shape correction. But if countersinks prepare holes for the subsequent use of rivets and bolts, then reaming allows you to get accurate calibrated niches for shafts, plunger parts and bearings. Also, the deployment of holes allows you to minimize friction in the treated area and provide a high density of contact between the elements. These objectives are achieved by reducing the roughness of the hole surfaces.
Deployment Tool
Reamers are also a drill-like tool. The working part in this case is provided with teeth located around the circumference of the rod. In addition, there are auxiliary functional parts of the cutter. These are the intake, calibrating and cylindrical parts. Direct cutting is performed by a guide cone, the edges of which remove the metal allowance, but at the same time protect the top of the cutting edge from nicks. And here it is possible to single out separate structural parts that distinguish this technique and countersinking. Countersinking and reaming of holes converge in cutting operations, however, the calibrating part of the reamer also performs the functionsdirection and removal of chips. Special grooves are designed for this, making the tool more independent.
Machine and manual reamers
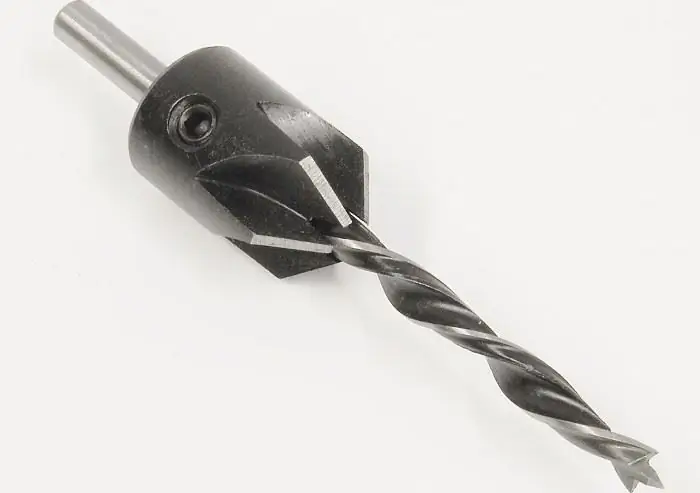
Reaming can be done manually and by machine, that is, on the same machines. The tool used for manual operations is characterized by an elongated working part. The diameter of the inverse cone in this case varies from 0.06 to 0.1 mm on average. For comparison, machine tool reamers have a cone thickness of 0.05 to 0.3 mm. By means of manual reaming it is possible to obtain holes with a diameter of 3 to 60 mm. In this case, the degree of accuracy will be low. The machine tool is guided by certain standard sizes, often by special orders. For example, reaming holes in structural parts can be performed according to the technical data for a particular project. The advantages of this method include high cutting accuracy, high-quality stripping and the absence of a deformation effect.
Performing deployment
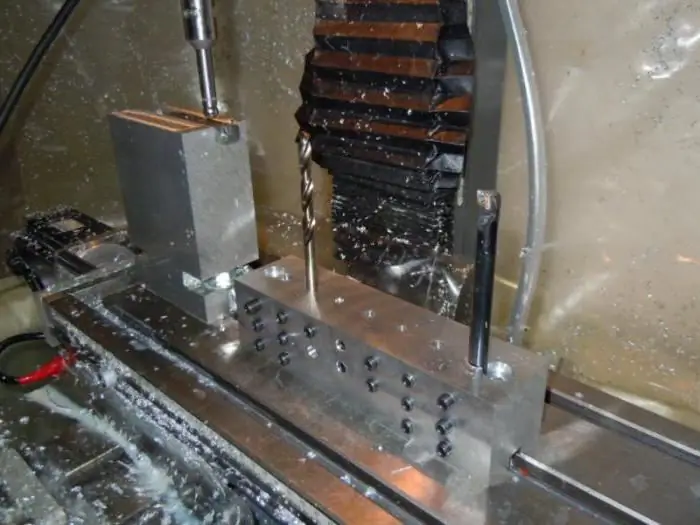
Machine reaming follows the same principles as countersinking. The tool is fixed in the chuck, and then sent to the machined area by the machine. The only difference is the higher requirements for cooling of the working equipment during operation and lubrication of the holes. Mineral oil, turpentine and synthetic emulsions are used as a lubricant composition. Otherwise, manual processing of holes is performed. Deployment of suchtype involves the initial fixation of the workpiece in a vise. Next, the tip of the reamer is inserted into the hole and the result is achieved by twisting the knob. Moreover, you can rotate the tool only in one direction - until the necessary parameters of the product are formed.
Conclusion
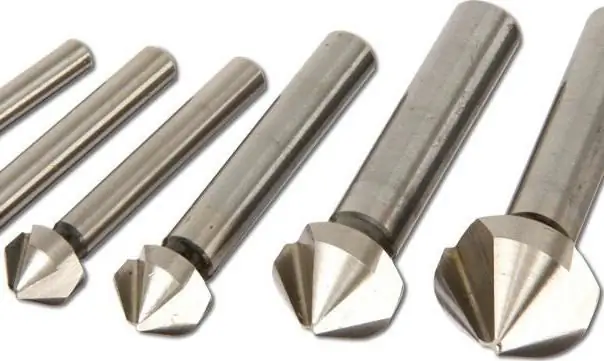
Mechanical processing of metals is gradually giving way to technological laser and thermal methods. Also, the competition with traditional cutting methods is waterjet technology, which is characterized by high cutting speed and accuracy. Against this background, what advantages can countersinking, as well as reaming holes, offer as advantages? First of all, this is the possibility of manual processing without the use of complex equipment in the form of machine tools. In addition, unlike hydroabrasives and thermal devices, these technologies do not require the connection of additional consumables. Therefore, we can talk about the advantages of an economic, organizational and ergonomic nature. But the quality of processing and the pace of the production process, of course, will have to be sacrificed.
Recommended:
Shelf life of water meters: period of service and operation, verification periods, operating rules and time of use of hot and cold water meters

The shelf life of water meters varies. It depends on its quality, the condition of the pipes, the connection to cold or hot water, the manufacturer. On average, manufacturers claim about 8-10 years of operation of devices. In this case, the owner is obliged to carry out their verification within the time limits established by law. We will tell you more about this and some other points in the article
Silicate industry - and the house, and the roof, and dishes
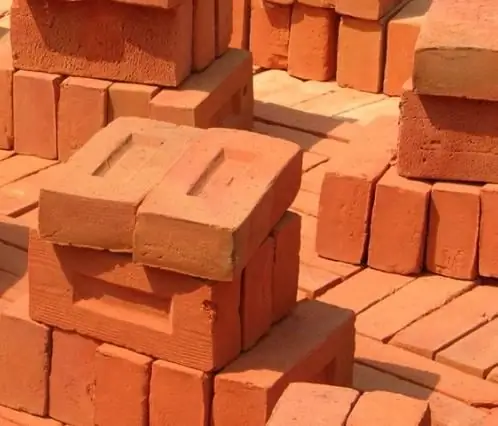
Like mushrooms after the rain, grandiose skyscrapers began to grow in many cities of the world, which are bright design solutions that organically combine concrete and glass. It is the building materials that are so in demand at the present time that the silicate industry produces
Drilling holes in metal, in wood. Drilling large holes in the wall
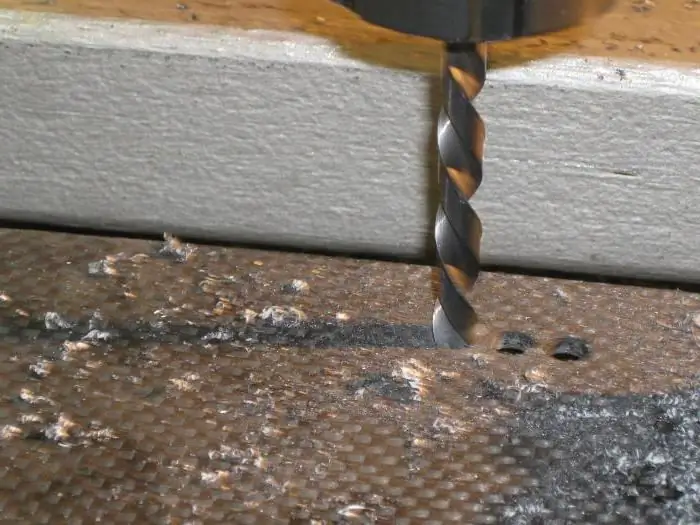
The article is about drilling. Considered operations for creating holes in wood, metal materials and walls
Diamond Drilling Rig: Precise holes in all materials
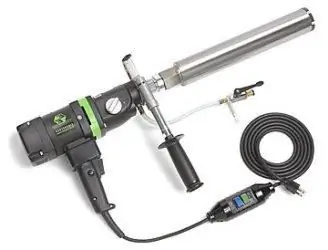
Construction and installation work is very often associated with making holes in concrete, stone and other similar hard materials. The diamond drilling rig is one of the most high-tech tools for their creation
What you need to work in a taxi: necessary documents and requirements, regulations and legal aspects. Feedback and advice from taxi drivers, customers and dispatchers
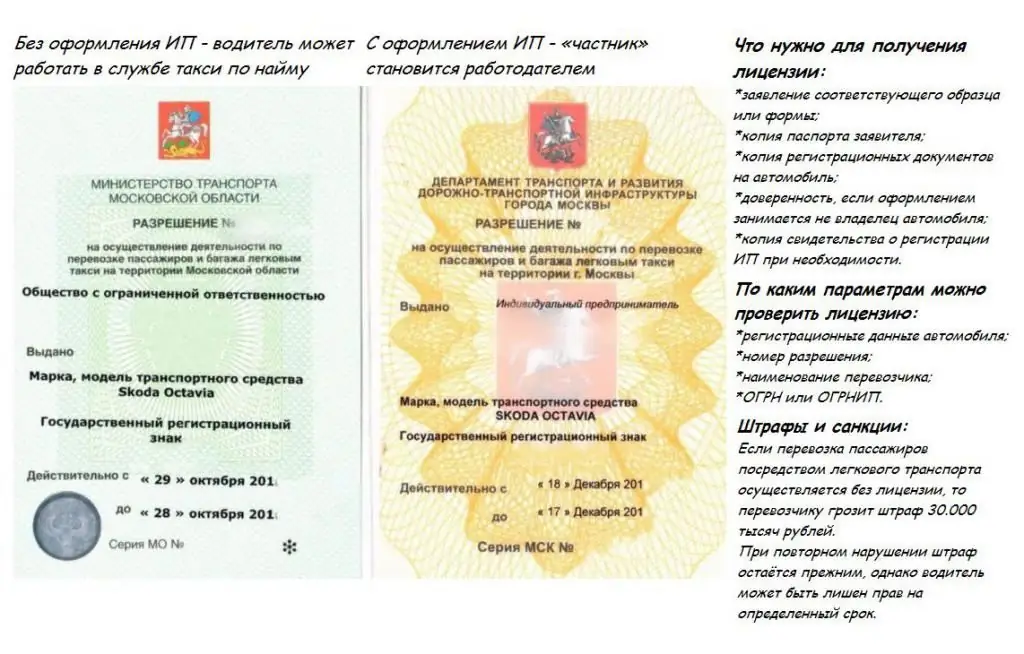
According to many passengers, the job of a taxi driver is the easiest. You sit, listen to pleasant music and drive back and forth. And they give you money for it. But this is only the outer side of the coin. The reverse is much less rosy. We will talk about it in this article. And we will also highlight what you need to work in a taxi