2025 Author: Howard Calhoun | [email protected]. Last modified: 2025-01-24 13:10
Drill pipes are designed for gas and oil well equipment. With the help of such equipment, a rock cutting tool is lifted and lowered into the well, torque is transmitted, a load (axial) is created on the tool, and compressed air or flushing solution is supplied to the bottomhole. Their production is mainly carried out according to the standards of GOST No. 50278-92. According to this regulation, products are made of steel, formed in a seamless way and have upset ends to which locks are welded.
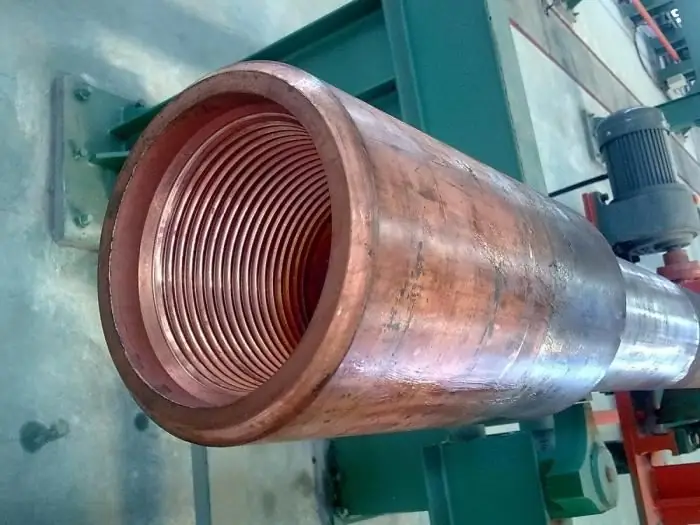
Drill pipes can have different types of upsets, including: internal, external, or combined upsets (referred to as ST, DL, or PC, respectively). Products of the PV group are produced with a nominal outer diameter from 73 to 101.6 mm, wall thickness from 8.4 to 11.4 mm, the estimated weight of one meter of a smooth pipe is from approximately 14 to 22 kg.
Diameters of drillpipes of the PC class reach a nominal value of 139.7 mm (the minimum value is 114.3 mm). And pipes with external upset (PN) have a smaller nominal diameter in accordance with the above GOST (127 mm). In addition to the diameter, for the nominal value for pipes, parameters such as the diameter of the lock (produced in accordance with GOST 27 834) and the diameter of the welded joint, including the inner and diameter for the elevator, are considered. Also an important parameter is the length, which is represented by three groups: from 5.9 meters to 6.3, from 8 to 8.6 m and from 11.9 to 12.5 meters. Modern production facilities allow the production of pipes of both longer and shorter lengths, but in this case they will not fit the established standards.
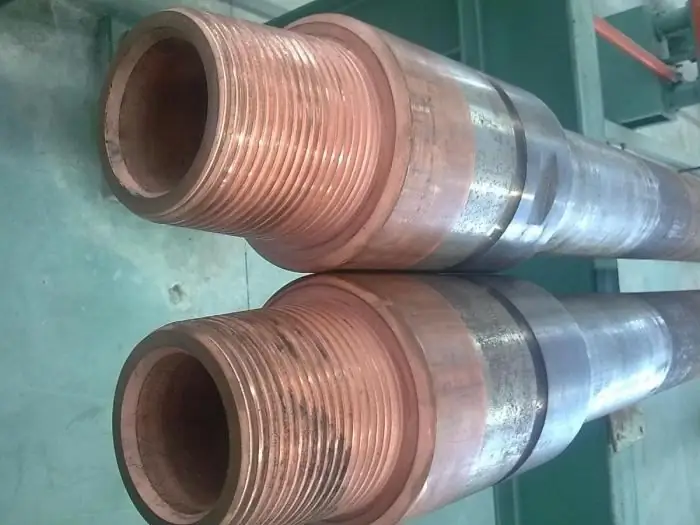
Quality drill pipes should be produced in such a way that their surface does not have cracks, delaminations, pits and other defects. Such flaws can be corrected only along the axis of the pipe, while sealing, caulking and welding of problem areas are not allowed, they can only be cleaned or cut down.
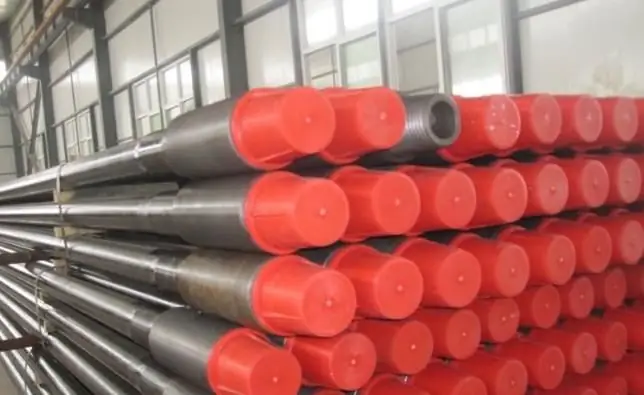
The production of drill pipes is organized in such a way that the mass fraction of phosphorus and sulfur in each heat is carefully controlled. If the company uses third-party raw materials, then the manufacturer requires documents on quality compliance. Today, some companies produce products with an internal coating (for example, TK-34R), which allows you to protect pipes from abrasive and corrosive wear, rack corrosion, reduce the likelihood of fatigue failure, and alsohydraulic losses during drilling. The coating surface is applied by powder method and allows the pipe to withstand more than 500 hours of operation at temperatures above 150C, to obtain an impact resistance of more than 8 J at a temperature of 20 C, etc.
Drill pipes are known as equipment that often breaks due to wear of the lock diameter (outer, up to 60% of all cases). At the same time, the remaining parts of the pipe remain suitable for operation. Recently, to solve this problem, methods of hard-alloy surfacing of locks have been practiced. This avoids cracks caused by high stress and other extreme operating conditions.
Recommended:
Well development: methods, process description, safety. Well repair
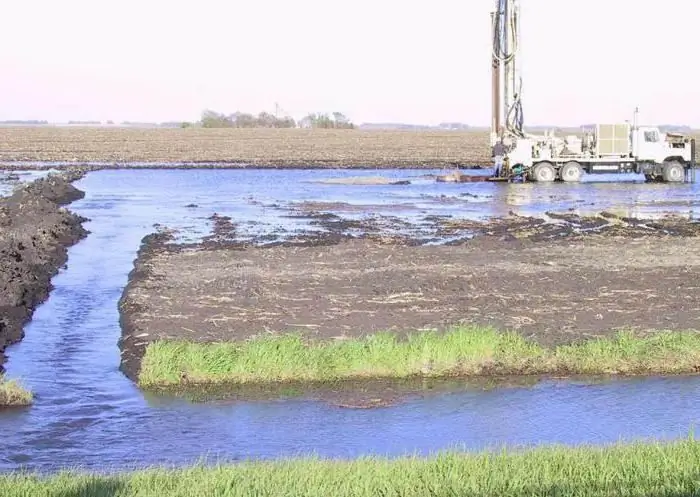
The article is devoted to the development of wells. The methods, features and nuances of the implementation of this event, as well as security measures and repair work are considered
Sales Consultant Job Descriptions: How Should They Be Designed?
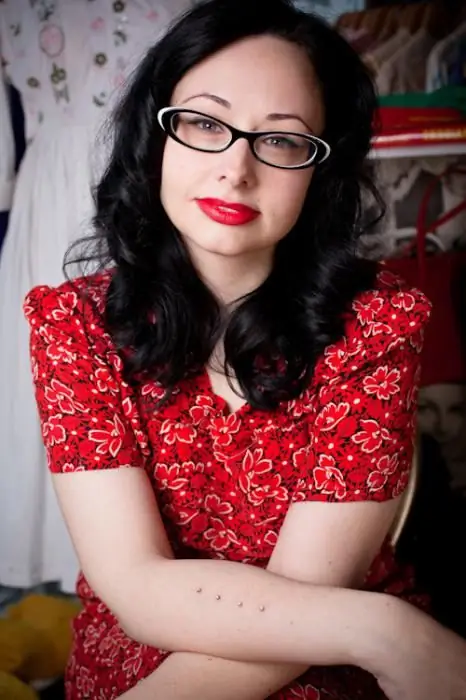
What should be the job descriptions of a sales assistant that will help organize the work correctly? Main principles: logic and consistency! What else?
Types and diameters of metal pipes. Metal pipes of large diameters
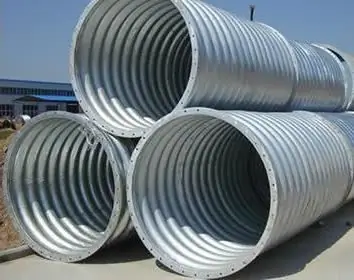
Steel pipe is a cylindrical tube and is the most used product in the steel industry. The main use of steel pipes is to transport oil, gas and water over long distances. In household appliances, such as refrigerators, ordinary steel pipes are used, as well as in heating and water supply systems
How gantry cranes are designed and used
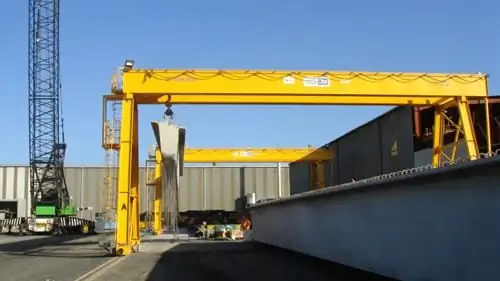
Gantry cranes are one of the types of overhead cranes. Such equipment is used in many areas of the national economy. Typically, such structures are installed in warehouses, open areas of manufacturing enterprises, in ports, etc. One of the most commonly used types of lifting equipment
Diameters of polyethylene pipes: external, internal, purpose of pipes
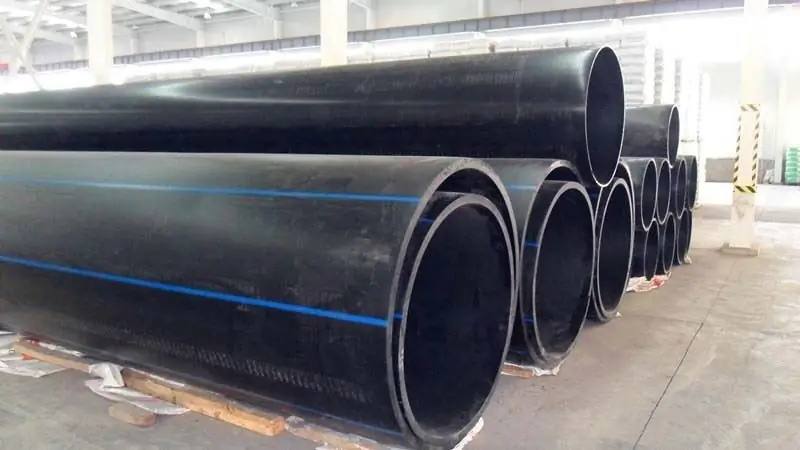
What diameters polyethylene pipes have, you now know. However, for the installation of these products, it is necessary to familiarize yourself with the features of docking. Connections may or may not be detachable. The former provide for the possibility of disassembling the system during operation. To create such a connection, steel flanges are used. During operation, disassembly cannot be carried out if the connection is one-piece