2025 Author: Howard Calhoun | [email protected]. Last modified: 2025-01-24 13:10
The process of development and subsequent maintenance of the working condition of the well is a complex of technological operations aimed at extracting the target material. The formation of the drilling tunnel is carried out in different ways, differing both in technical support and in the configuration of the use of units and devices. The choice of the method by which the development of gas wells is planned, to a large extent, depends on the conditions of the work. Engineers preliminarily calculate the loads on the bottomhole zone and, based on the data obtained, develop a work plan.
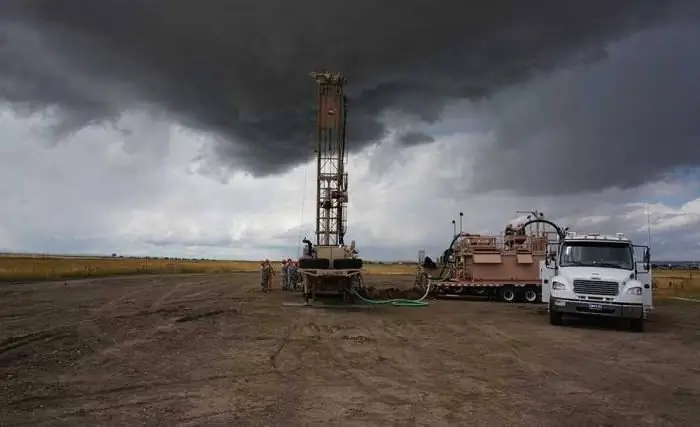
Preparing for development
Before the start of development, mounting fittings are supplied to the wellhead, with the help of which the technical organization of the development process will be possible. Regardless of the chosen completion method, a high-pressure gate valve is placed on the flange of the installed casing string. It will be required if a decision is made to block the trunk. As part of the preparation, the working is perforated and the bottom is installed, after which it is possible to start diving into the formed well of pumping and compression equipment. Compulsory learningthe well provides for the possibility of removing influx from the reservoirs. This operation is also included in the list of preventive measures in case of accidents or unwanted stress on the equipment.
Well analysis
Research work is being done to clarify or correct the development method. By breaking down the colmatation products of the well through water flows, specialists reveal the characteristics of the formations. At the same stage, surface finishing with dry ice can be carried out. Further, bypassing the working cavity, the workers clean the filters. Flushing of the annulus is carried out through the filter shoe. Then the final project is prepared, in accordance with which the development of wells is carried out. The development methods presented below are selected based on the recorded parameters of the well and the external conditions for the operation of the equipment.
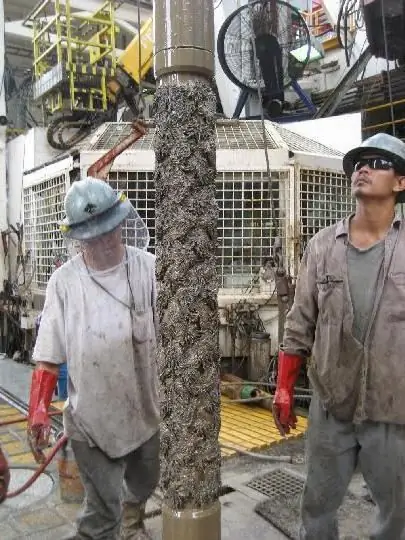
Tarting
In accordance with this technique, the liquid is extracted, which is lowered by means of a winch and a bailer on a thin rope about 16 mm thick. The bailer is an 8-meter pipe circuit, the lower part of which is provided with a valve with a stem. At the moment of exerting a persistent action on the stem, the valve will open. On the reverse side of the bailer is a rope mount - usually a hardware fixture. The pipe is usually no more than 70% of the casing thickness in diameter. For one trigger approach, it must carry out liquid in a volume of up to 0.06 m3. As practice shows, the development of a well by bouncingis a labor-intensive process with low productivity. The main disadvantage of this method lies in the limited possibilities of its use. This is due to the fact that the valve must not be closed during the removal of the bailer in case of fountain manifestations. On the other hand, workers get the opportunity to effectively remove the sediment with full control of the liquid level in the well.
Piston method
This technique is also called swabbing, since both a piston and a swab can be used as a working unit. Both devices are lowered into the tubing using a rope. The piston can have a diameter of 25 to 35 mm on average, and by design it is a small tube with a valve that opens the top of the device. For this device, reinforcing strapping on external surfaces is especially important. Rubber cuffs or wire mesh can be used as reinforcement elements. As drilling proceeds, well development by pistoning is realized in the form of water intake. The valve opens under fluid pressure and moves to the upper level. Conversely, during the lifting of the unit, the valve closes, the water drops, and the piping tightens the pipe walls more strongly. One descent makes it possible to extract exactly the volume of liquid that was drawn into the cavity above the level of the valve when immersed. In terms of productivity, the pistoning method is about 10 times higher than that of the tartan method.
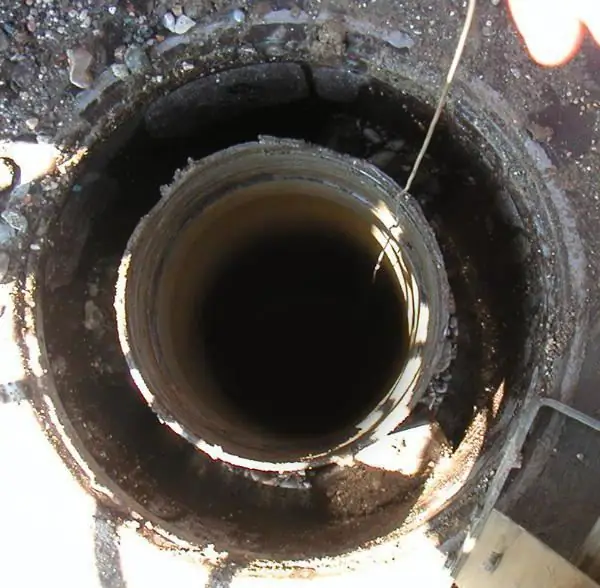
Method of well replacementfluids
The technology also involves work with pumping and compressor units, but on condition that the mouth is completely sealed. The creation of a damper at the surface prevents blowouts and blowouts from the well, which increases the reliability of the method. At the exit from the drilling process, the well is filled with clay mass, and after flushing with degassed oil or water, the bottomhole pressure coefficient can be significantly reduced. This method effectively shows itself in the development of wells characterized by high pressure formation influx. Actually, this is the advantage of well development by replacing the fluid and cleaning the field. Updating can be done with the help of pumping and compressor units, and by means of drilling rigs. Sometimes, if there is confidence in the safety of the well in terms of high loads on the equipment, the piston mechanism for extracting fluid is also activated.
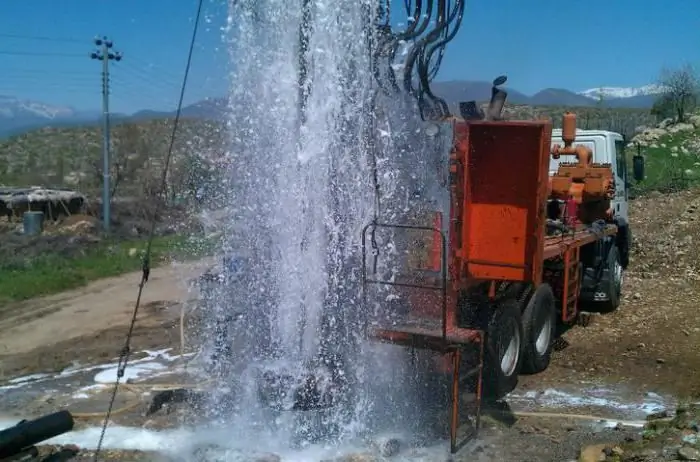
Gas injection development method
In this case, the development technology is implemented, similar to the replacement with liquid mixtures. As a working filling, a combination of gas and oil liquid is used. The resulting mixture fills the space between the submerged pipes. As a result, tension is created between the supplied mixture and the well fluid, under which conditions it becomes possible to regulate the development process. This method is optimal for working at great depths, but its implementation involves the use of pipes and compressorhigh pressure installations. Since well development occurs under constant temperature fluctuations, equipment surfaces must also have enhanced external protection. In addition, working with gaseous mixtures places high demands on safety measures during work, and this increases the cost of the event.
Development methods for injection wells
Working with injection wells is not much different from similar activities with producing fields. Methods are also used to obtain a targeted inflow from the reservoirs through drainage with cleaning of the bottomhole area. But there are also certain differences. The main one is to use the soft start method. This means that during the intake process, a slow increase in speed occurs, at which a larger volume of liquid is served at peak power. Also, methods of development of wells of injection type are guided by a high degree of openness of channels with growing injectivity. That is, the absorption capacity of well support is growing, which also affects the increase in productivity.
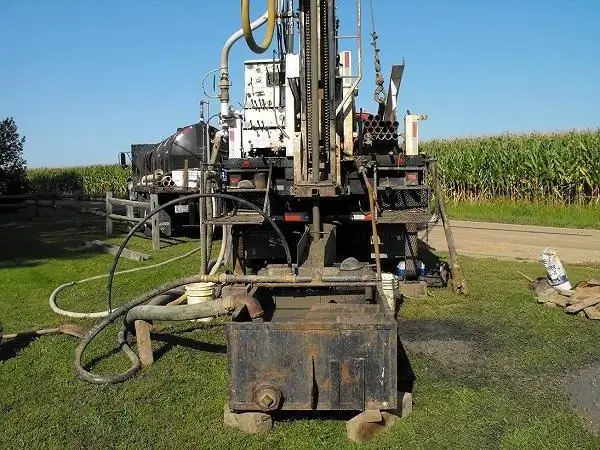
Using compressor units
Most of the methods of field development involve the connection of compressor stations. Typically, mobile plants of various designs are used with a delivery volume of about 8 m3/min. The most productive crawler units are able to service wells with a pumping capacity of 16 m3/min, but they areto highly specialized tools capable of working under high pressure conditions. Diesel free-piston stations can be attributed to the most modern compressors from a technological point of view. Such units for well development are launched from cylinders with compressed air without the need for preheating. The choice of compressor equipment for a particular field depends on the characteristics of the well. Moreover, the power with the feed does not always play a key role in the choice. So, in deep and narrow wells, it is more expedient to use compact, accurate and at the same time functional installations.
Mastering coiled tubing compressor plant
Some projects that explore the potential of an as-yet undeveloped field involve some form of exploration using flexible pumping equipment. This activity precedes the implementation of actions related to the influx call. At this stage of well development, the following operations are usually performed:
- Preparing for punching.
- Direct perforation.
- Preparing to call inflows.
Perforation refers to the drilling of a well in order to increase the volume of inflows. That is, at this stage, it is not necessary to organize the inflow in certain volumes, but at least efforts are made to increase the productivity of this part of the process in the future.

Repair work on wells
Under renovationmeasures are understood as a set of measures aimed at maintaining or improving the performance of the cement sheath, casing strings and other elements of the well structure. Emergency recovery actions include the elimination of collapses - especially on descents and ascents. Well workovers are more often performed, during which specialists can restore equipment, change configurations and schemes of its installation, carry out cleanup operations, etc.
Well workover, in turn, aims at full or partial restoration of the bottomhole zone. As a result of the implementation of such measures, the recovery of reservoirs should be improved against the background of strengthening their structure. In each case, the repair of wells is carried out according to a project prepared in advance and is supervised by a foreman. After its completion, an acceptance certificate is drawn up.
Safety during well development
Only persons who have undergone special training are allowed to work. In addition, before the start of work activities, a briefing is conducted in order to familiarize with the nuances of performing operations at a particular facility. Only the necessary technical means, inventory and devices should be present on the site. The equipment must receive a special permit, indicating the serviceability of all functional parts. Fire safety during well development is especially important when working with oil and gas fields. Fire extinguishers must be present at the facility in case of ignition of a gassed area. Local communications for temporary storage of oil and itstransportation (barns, pipelines) must have reliable fire insulation.
Conclusion
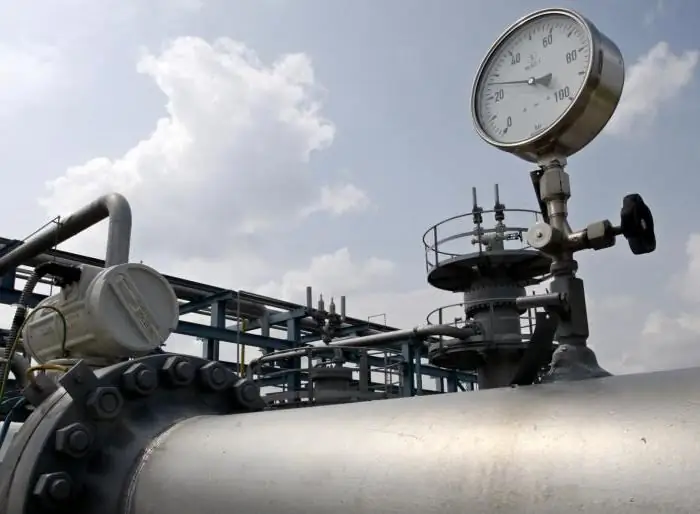
The technical organization of field development requires serious training in a wide range of different aspects. In some cases, the emphasis is on the power of the equipment, when you need to get large volumes in a short time. In others, strict safety standards are taken into account. By the way, the same development of oil wells is characterized by increased requirements not only in terms of safety, but also in terms of technological support. Petroleum products, due to their physical and chemical properties, limit the use of certain methods, which often forces engineers to modify them specifically for specific conditions. Of course, in such cases, the cost of development also increases - but, provided that the work is done well, the invested resources and efforts justify themselves.
Recommended:
Real estate development and its role in economic development. The concept, types, principles and foundations of development
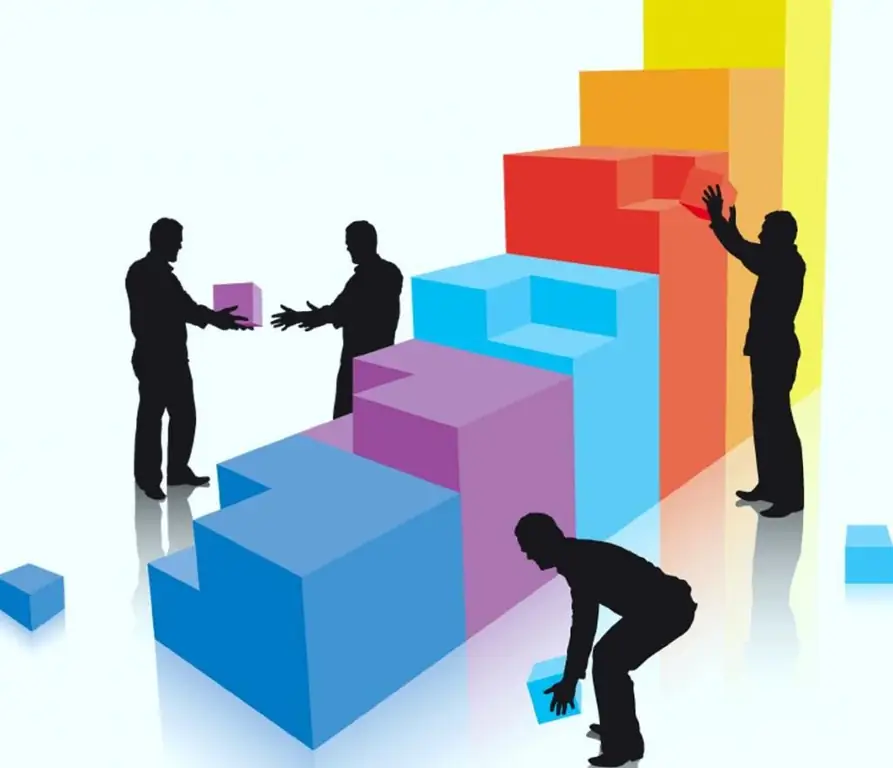
In the framework of this article, we will consider the organization of the real estate development system and its role in economic development. The basic concepts, types and principles of organization of the development system are considered. The characteristic features of the system in Russian conditions are considered
Process engineer: job description. Process Engineer: Job Responsibilities
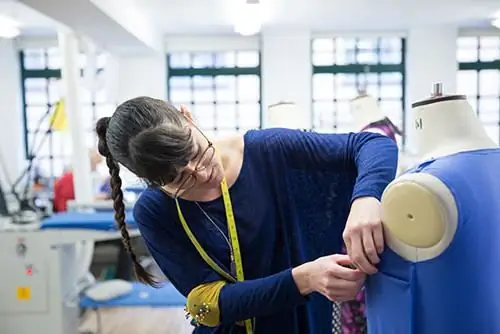
The job description of a process engineer is an addition to the employment agreement and defines the duties, rights and degree of responsibility of the person applying for the specified vacancy. This administrative document is intended to specify the powers of the administrative apparatus in relation to the specialist technologist, as well as to designate the functions of an employee
Occupational safety specialist: job description. Occupational Safety Specialist: Key Responsibilities
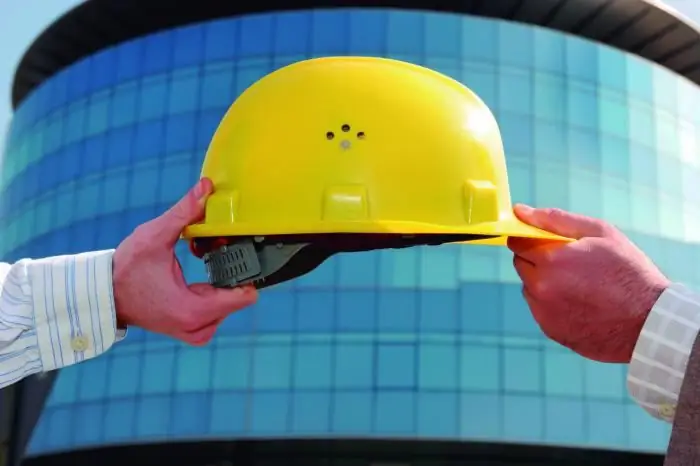
As you know, every employee in any enterprise should have their own job description. The labor protection specialist is no exception to this rule. He, like other employees, has a number of duties and functions that undoubtedly require a detailed presentation on paper
Metal casting: process, methods, methods
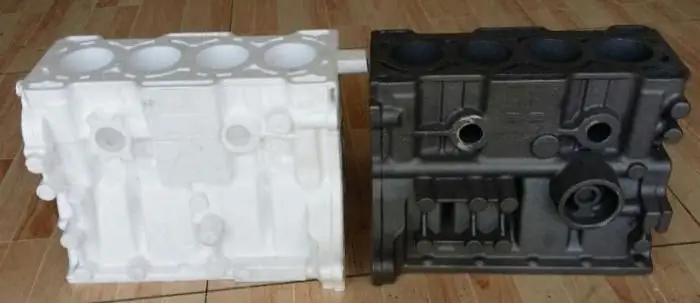
Metal is the basis of all modern civilization. In a year, modern humanity mines and processes such an amount of iron alone that before the whole world would have been digging it for at least a couple of centuries
Restoration of parts by welding and surfacing: methods and methods of restoration, features, technological process
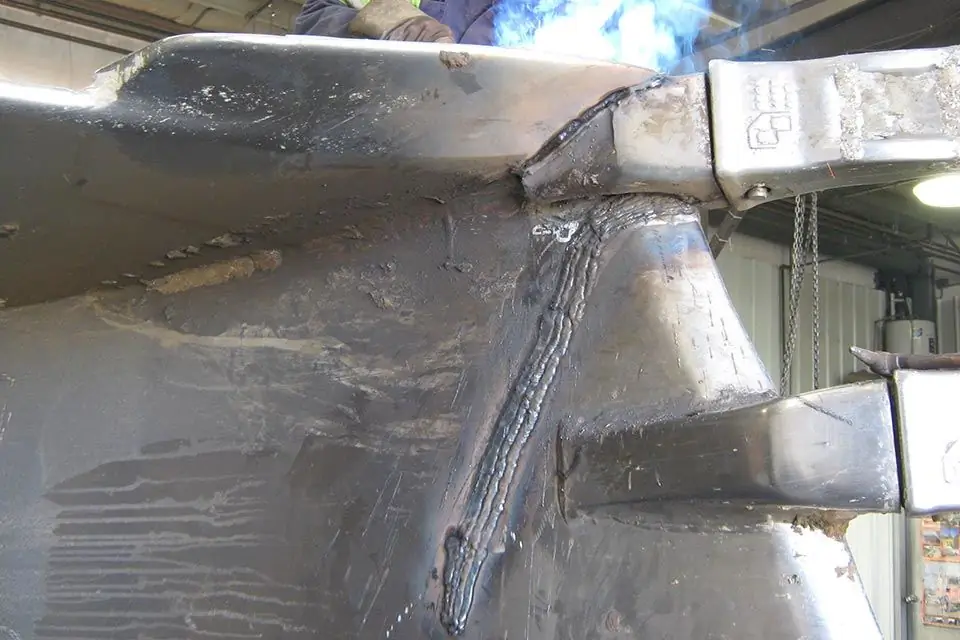
Welding and surfacing technologies allow efficient restoration of metal parts, providing a high degree of reliability and durability of the product. This is confirmed by the practice of using these methods when performing repair operations in a variety of areas - from car repairs to the production of rolled metal. In the total amount of work on the repair of metal structures, the restoration of parts by welding and surfacing takes about 60-70%