2025 Author: Howard Calhoun | [email protected]. Last modified: 2025-01-24 13:10
Brick is by far one of the best and most common building materials. It is used by both private builders and professional companies. There are small and large enterprises that are engaged in the manufacture and sale of these products. You, too, can create your own business that will meet your requirements and also become a source of income. However, in order to obtain high-quality bricks, it is necessary to comply with the technical conditions and adhere to the manufacturing process. The production of bricks at home does not involve the use of expensive equipment. The most important condition is the correct preparation of raw materials.
Production Features
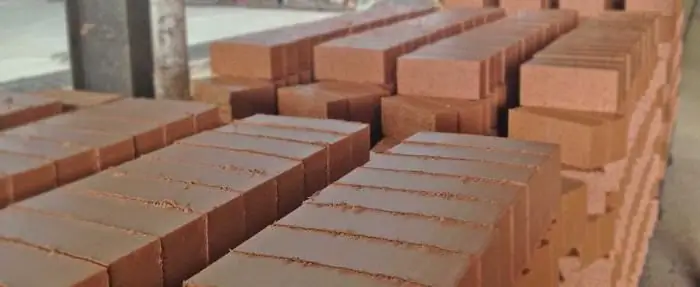
Forms can be boards that are pre-knocked together. Subsequently, raw materials are placed in them. Forms should be completedsizes so that the finished product matches the dimensions and appearance of a traditional brick, which has dimensions within 25x12x6.5 cm. The lid will allow tamping the raw materials that fit into the molds. Brick production will be faster if multiple templates are made.
Work technology
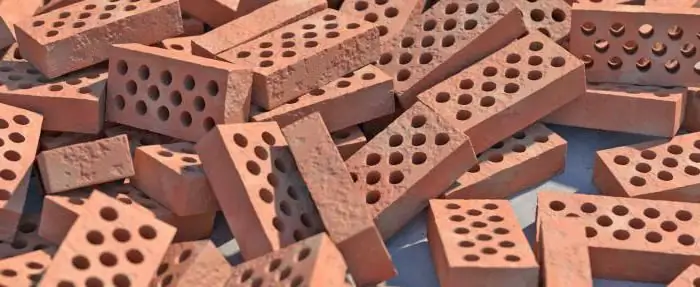
The inner side of the form must be moistened in advance or sprinkled with dry cement. Next, the prepared solution is laid. As you fill the form, you need to tamp the mixture so that all corners and voids are filled. Excess solution should be removed with a spatula. Next comes the turn of the lid, which fits on top. At the next stage, a certain time is expected, after which it is necessary to turn the form over and remove the resulting semi-finished product. The room should be equipped with shelving under a canopy, on which bricks are to be laid for drying. Natural shrinkage will occur within 15%. At this stage, the water evaporates. This becomes a catalyst for the convergence of substances in the mixture.
In this case, exposure to direct sunlight should be excluded. The production of bricks is carried out in a room that is well ventilated. Drying lasts from 7 to 14 days. It must be remembered that the manufacture of bricks without firing is one of the fastest and easiest methods for obtaining the described building material. As the only, but important drawback, it is considered that the resulting productscan only be used to form partitions inside the premises. This is because moisture can damage them.
Area of use of raw

It will be possible to use raw material in the arrangement of partitions and walls that will be located inside buildings. It can be buildings, as well as baths, which are used for economic purposes. However, it will be necessary to perform waterproofing from the inside without fail. This material can also be used in the construction of capital walls in buildings that have one floor. In this case, the roof must be wooden.
Brick firing
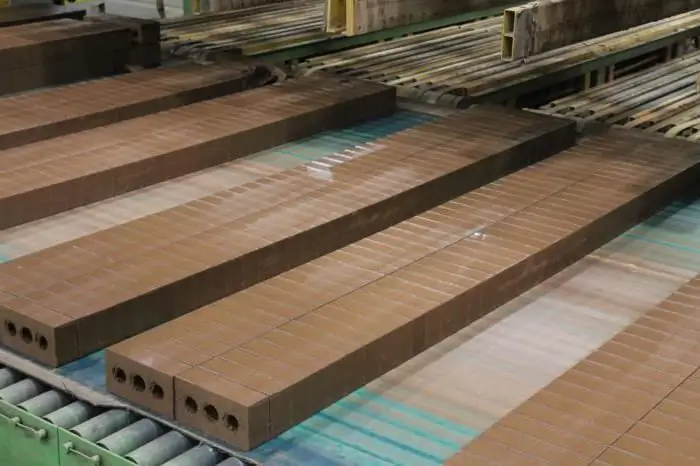
The production of bricks at home involves firing at the next stage. This will allow you to get high-quality building material. In the conditions of industrial enterprises, special furnaces are used for this. Whereas with self-manufacturing, you can build a product that is made from available materials. To do this, a recess up to 0.5 meters should be prepared in the ground. Above it, with a deviation from the bottom of 20 cm, a metal barrel should be installed, which is devoid of a bottom. Holes should be made in the walls of the container in which fittings are installed. On the resulting shelf, you need to lay semi-finished products that have undergone preliminary drying. From above the barrel is covered with a sheet of metal. A fire should be made in the prepared recess.
Roasting nuances
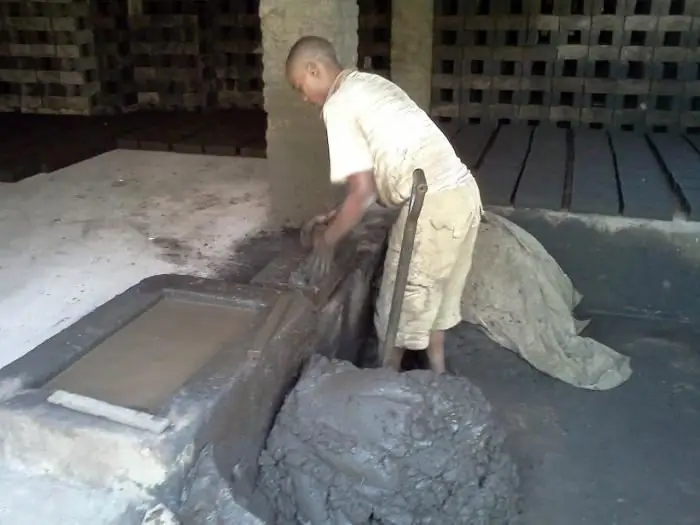
The technology of brick production involves the observance of a certain temperature regime, so that the finished product is of high quality. During the first eight hours, the temperature should be kept within 200 degrees. The firing process is carried out from 12 to 16 hours, during which the temperature must be kept from 800 to 1000 degrees. The next 4 hours the temperature should be gentle, from 500 to 600 degrees. Gradual adjustment of the temperature will allow you to get the desired result, eliminating the occurrence of cracks. You can make a fire with coal or wood. The filled container should cool with a well-closed lid. Only after that it will be possible to release the brick by checking its readiness.
Making lots of bricks
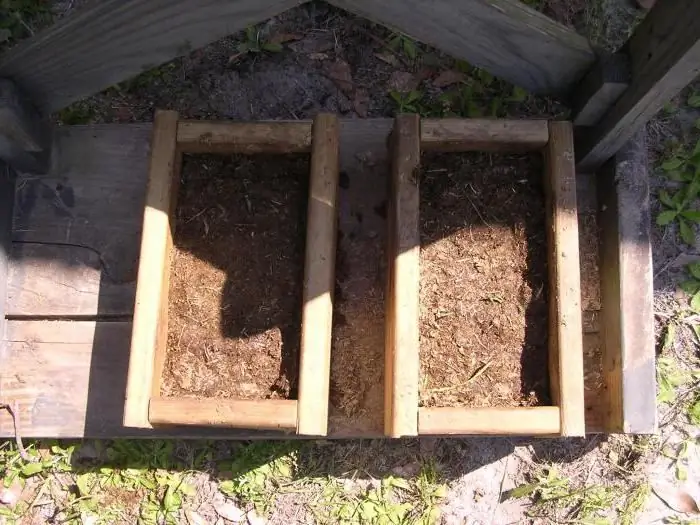
Installation for the production of bricks, or rather for firing, can be designed for a more impressive amount of building materials. To do this, a furnace is equipped using a container. Its shape should resemble a design narrowed upwards. Raw is placed in it, covered with sand or soil to provide thermal insulation. After that, a fire is made inside, and the temperature regime should remain the same as the one described above. The production of hyper-pressed bricks is also possible at home. To do this, you will need to use a special machine that compresses the prepared mixture into a denser mass. To work will not arisethe need to use electricity. While the process will be quite simple.
Alternative brick options
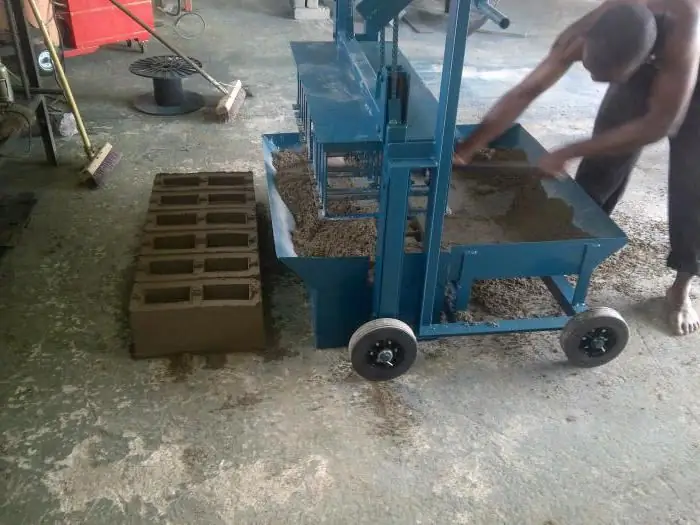
The production of clinker bricks involves the use of somewhat more sophisticated equipment. Products are formed using semi-dry pressing technology. This has the potential to save energy. In production, a vacuum press is used, which is sometimes replaced by a lever press. In some cases, the wizards use a tape installation. After the blank is formed, the brick is sent for drying. For this, special electric fireplaces are used that maintain a high temperature. Refractory clay is the most important raw material. It is characterized by plasticity and a high temperature threshold. When preparing a solution, metal oxides or minerals that belong to the group of kaolins are added to the ingredients. This results in stronger products.
Production of ceramic bricks
The production of ceramic bricks at home involves the preparation of raw material, its formation, and subsequent firing. Clay mined in a quarry is not suitable in its original form for the formation of quality bricks. The mass is brought to readiness, during which processing measures are carried out. This may be natural or mechanical. During the drying stage, the percentage of moisture content in the products is reduced to 6%. This indicator is needed so that during the firing there are no formationscracks, and the finished product was not deformed. If chamber dryers are used, they will be able to provide temperatures ranging from 120 to 150 degrees. Depending on the humidity of the raw material, as a rule, this stage takes no more than 3 days. The final step is firing. For its implementation, ring or tunnel ovens will be needed.
Making sand-lime bricks
The production of sand-lime bricks involves the use of autoclave synthesis. In order to make one unit of material, 9 parts of quartz sand, which is pre-screened, additives, and one part of air lime will be needed. The last component must be special.
Recommended:
Garlic cultivation as a business: a business plan, methods and features of technology. Growing garlic on an industrial scale
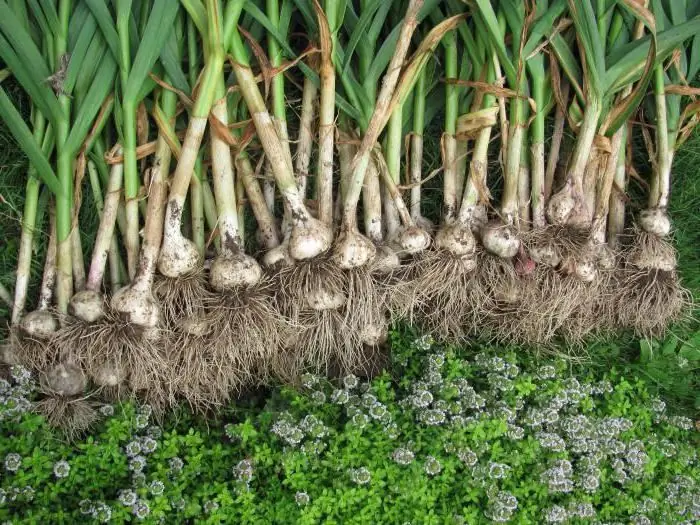
The owners of suburban areas, by definition, have a few more opportunities to organize a home business. You can, for example, not only engage in gardening or growing fruits and vegetables, but also have pets. Although, of course, many summer residents and aspiring entrepreneurs prefer crop production to caring for animals. This is not only a less labor-intensive undertaking - growing vegetables and fruits does not require such large financial investments and pays off faster
Styrofoam production business plan: step-by-step opening steps, manufacturing technology, calculation of income and expenses
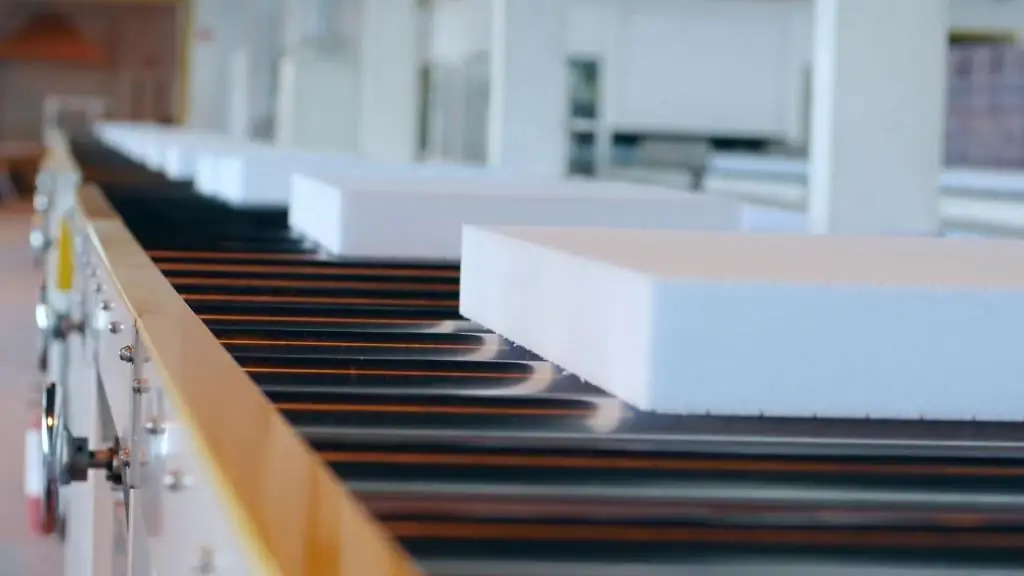
Polyfoam can be attributed to one of the most widely used building materials. The demand for it is quite high, as there is a development of sales markets, which, with a competent marketing approach, can provide stable profits for a long period of time. In this article, we will consider in detail the business plan for the production of foam plastic
Fodder production as a business: features, technology and reviews
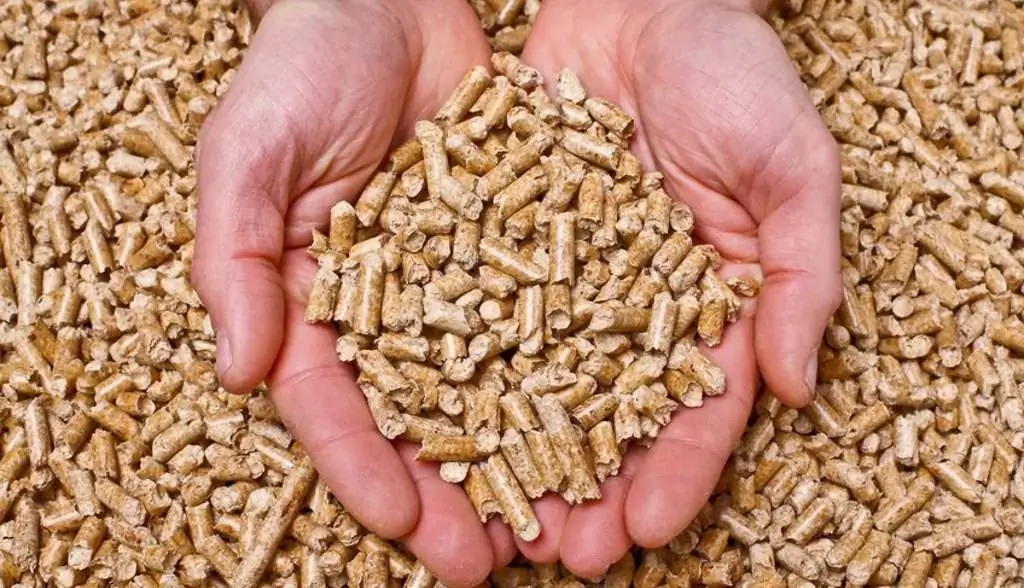
Fodder production as a business will be a profitable enterprise only if everything is organized correctly. The agricultural industry today presents many opportunities. The constant growth of farms makes their maintenance services in demand
HDPE pipe: do-it-yourself installation, installation features and instructions
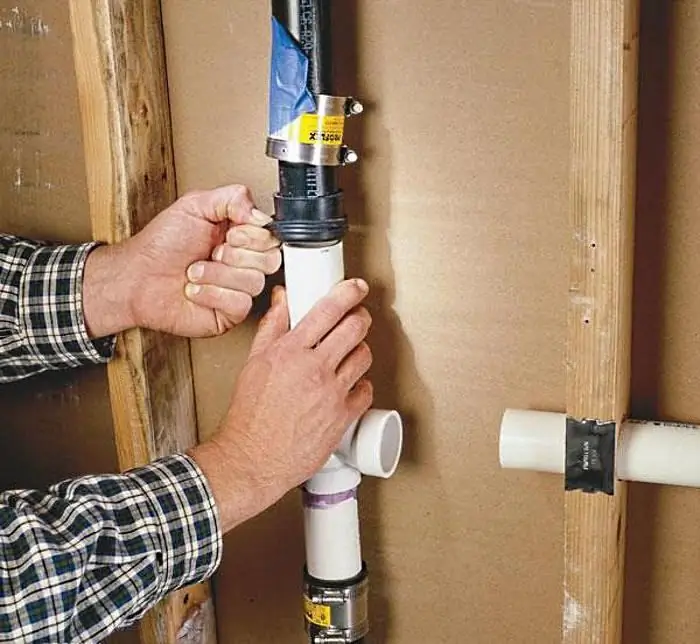
When HDPE pipe is installed, the installation is done mainly by welding or compression fittings. If the installation rules are followed, the connections will be airtight and durable for many years
Business idea: production of covers for documents. Cover production equipment
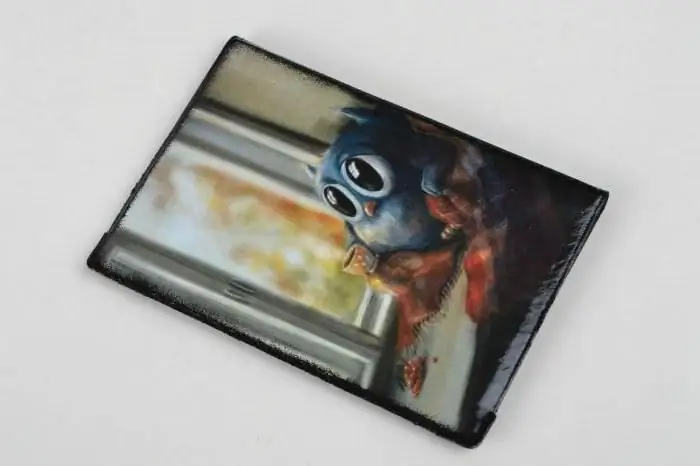
Document cover is quite a popular accessory in everyday life, but not because of its intended purpose. There has long been no shortage of products that ensure the safety of documents on the goods market. A new feature of the cases has been highlighted: individual design. Demand for products is high, the price of manufacturing a product, as a rule, is the opposite. Now let's take a look at the specifics of this activity