2025 Author: Howard Calhoun | [email protected]. Last modified: 2025-01-24 13:10
Today, people actively use the pipeline system. It connects many different buildings to each other, and then leads to special places, if it is, for example, a water sewer. For the high-quality arrangement of such a system, one very important thing is required - a reliable connection of the pipeline. There are many different connection methods. All of them are selected based on various factors, the most important of which is the material used in the production of pipes.
Main types of connections
There are a lot of pipeline connections in our time. However, all of them are conditionally divided into two large groups - these are detachable and one-piece.
Naturally, the main advantage of the first category is the ability to disassemble the pipeline if necessary. Most often, this need is a repair. Detachable pipeline connections allow repair and replacement of damaged sections without disturbing the entire structure as a whole. This type of connection isflanges, as well as threaded connectors (fittings).
If we talk about the second method, then such a system can be repaired, however, when disassembling the whole structure, it will inevitably be damaged. Among the non-detachable types of pipeline connections, welding is the most common today. In addition to this method, there are several more, for example, gluing, pressing, mounting a socket using a cement mixture.
All of these methods are widely used. These connection methods allow you to create a reliable system for transporting a wide variety of media, it can be water supply, gas networks, heating pipes, sewage, industrial and technical highways.
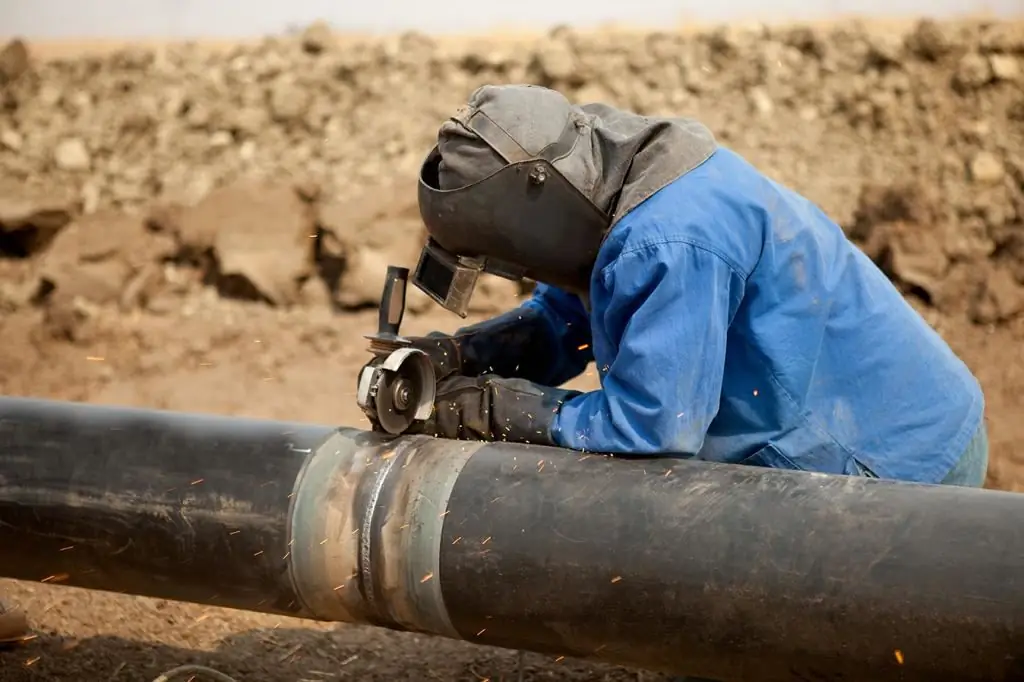
Using welding
Welded pipe connections are currently the most popular, especially in the field of creating technical communications at production facilities. With their help, you can easily connect the individual parts of the pipe together into an integral system.
It should be added here that this method is not limited to welded joints in steel pipelines. By welding, plastic products can also be joined. In certain cases, welding is even used to join glass elements. This method uses two main methods of conducting work, which differ from each other in the way they affect the material being processed:
- Fusion welding.
- Under pressure.
If we talk about weldedpipeline connections made using the first option, the following welding methods can be used here:
- conventional electric;
- electric arc apparatus;
- laser;
- gas welding;
- electrobeam.
The most common option is the use of electric arc welding to connect steel pipelines. In this case, an electric arc is used for heating and carrying out work. Due to this type of source, there are two ways to carry out welding. The first is with a DC arc, the second is with an AC arc.
Since in this case a variety of equipment can be used for pipe installation, according to GOST 16037-80, where the rules for joining steel parts by welding are prescribed, manual, semi-automatic or automatic welding should be used.
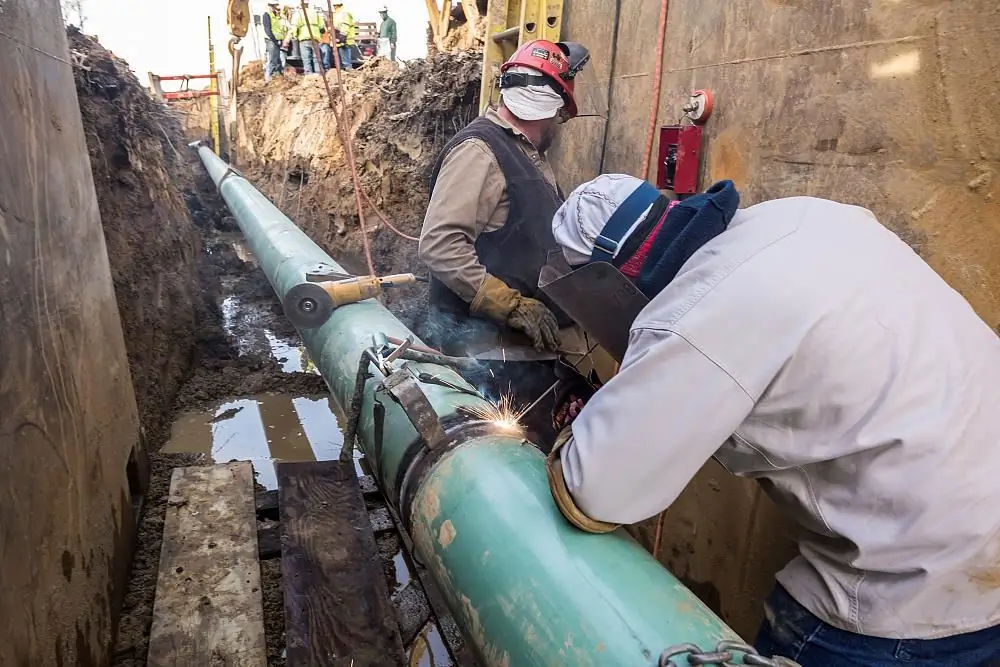
Main types of connections
Several different types of pipeline element connections are used to create highways. There are 4 main options: butt, overlap, corner, with welding of different elements.
The following three ways of connecting pipelines are considered the most popular and common today:
- Butt longitudinal and transverse fastening. In this case, additional applied parts - rings - can be used for welding. As for the seam, in such places it can be both one-sided and two-sided. The second option is used incases when the cross section of the pipe is too large - more than 500 mm.
- Corner connection is one-sided and two-sided. This method of welding in different cases is performed in different ways. Sometimes the corner joint is fastened with a beveled edge, other times without it.
- The last option is the socket lap joint. According to the rules for connecting the pipeline, the socket method is used in cases where it is required to join materials with a high coefficient of plasticity. Most often this is the assembly of non-ferrous metal parts, as well as other plastic components.
It is worth noting here that welding is quite actively used not only for the articulation of round pipelines, but also for square ones. Typically, such elements are often used in construction, in the manufacture of furniture. However, they are not used in the arrangement of technical highways. The main drawback is their shape. The square section significantly degrades the throughput. Round, on the contrary, is one of the best.
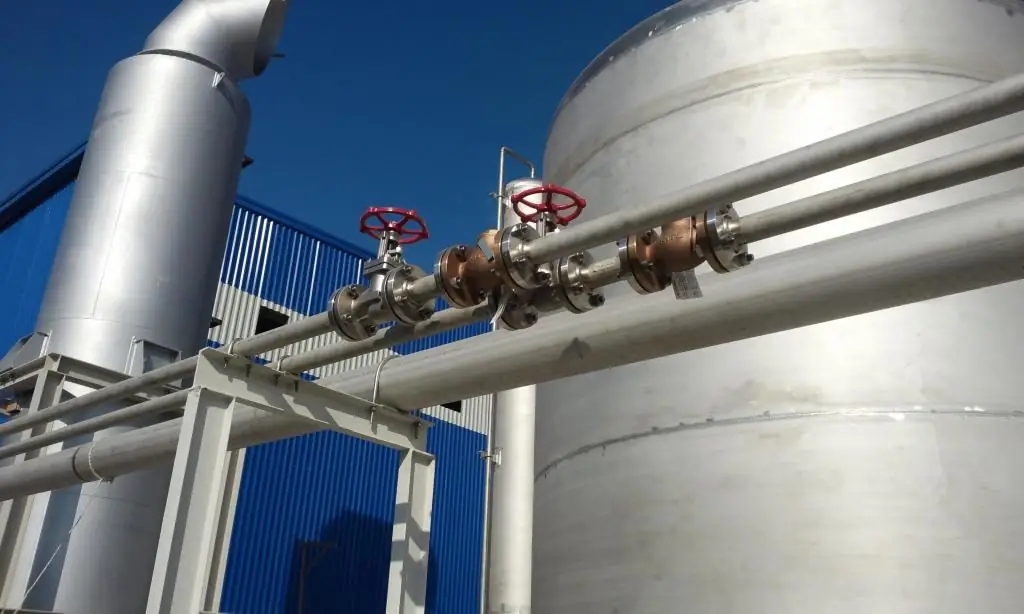
Thread Joints
Naturally, in practice there are cases when there is no opportunity to carry out welding work. In such cases, other docking methods are used, which are also quite numerous. The most common is threaded installation. For threading pipes, either special machines or a regular die are used. If the part has very thin walls, then the method is used to thread the surface.knurling.
Subject to all the rules, the connection of pipes of this type will turn out to be quite strong and tight. This method has several undeniable advantages: ease of installation, the possibility of repairing the pipeline connection, all installation work can be carried out without the use of special equipment.
In this case, some parameters of the thread itself will be important, which will determine the scope of its operation. Firstly, the cutting step is important here, secondly, the depth of the thread and, thirdly, the direction. The thread pitch will determine the distance between the top of the coil and its base. When carrying out installation work, it is very important to correctly understand and take into account the direction, since it can be right and left.
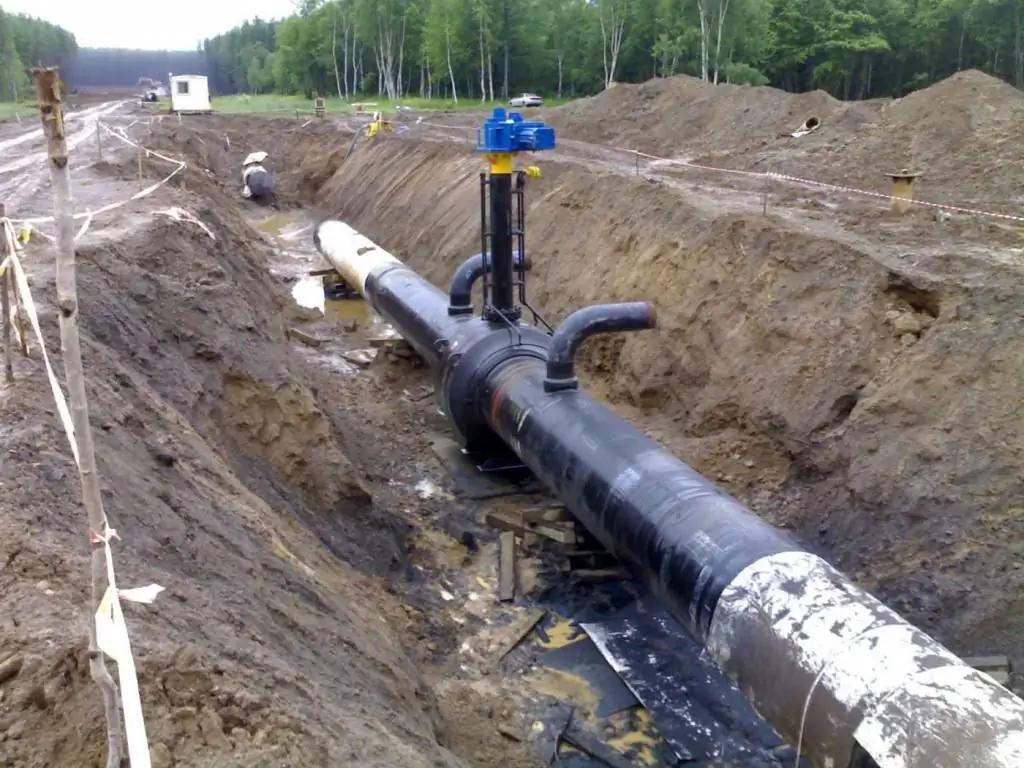
Other docking methods
Despite the fact that threaded connection is considered one of the most popular methods in case of impossibility to use welding, there are other methods that are used quite actively. As for the choice of a particular method, it usually depends on the material from which the pipe is made. To date, all pipes are conventionally divided into two categories - flexible and rigid. The first subgroup should include pipes made of polymeric materials, for example, polypropylene pipes, polyethylene, metal-plastic. The second category of products does not have such plasticity, and therefore it includes cast iron, steel, copper and others.
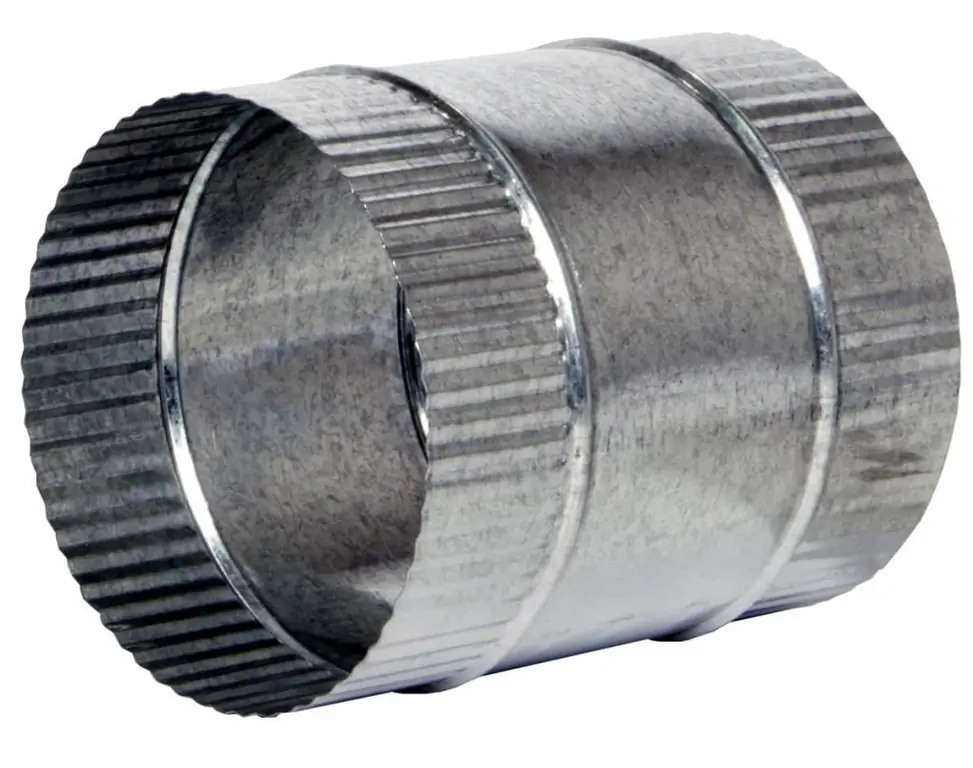
Assembly of flexible and rigid pipes without welding
Most often, in the absence of the possibility of welding, fittings are used to connect pipes. These are special connectors. To ensure a reliable and tight joint of flexible elements, it is necessary to use fittings with a greater coverage than for rigid ones.
Currently, fittings for assembling pipelines from flexible material are used only in cases of small and medium section of the element, from 20 to 315 mm. If the parts have a cross section of more than 315 mm, then the use of a fitting is considered inappropriate. The main problem is the low reliability of such a connection.
For the articulation of low-density polyethylene or HDPE pipes, a special type of pipeline connection part is usually used - a compression fitting. The main advantage in this case is the speed of installation. Additionally, it should be noted that the use of compression fittings is a budget option for joining flexible pipes. However, it also has its limitations. Compression parts are able to connect reliably only pipes with a small cross section. A coupling is used for a medium section pipeline. The pipe coupling is considered the most common among all other fitting options.
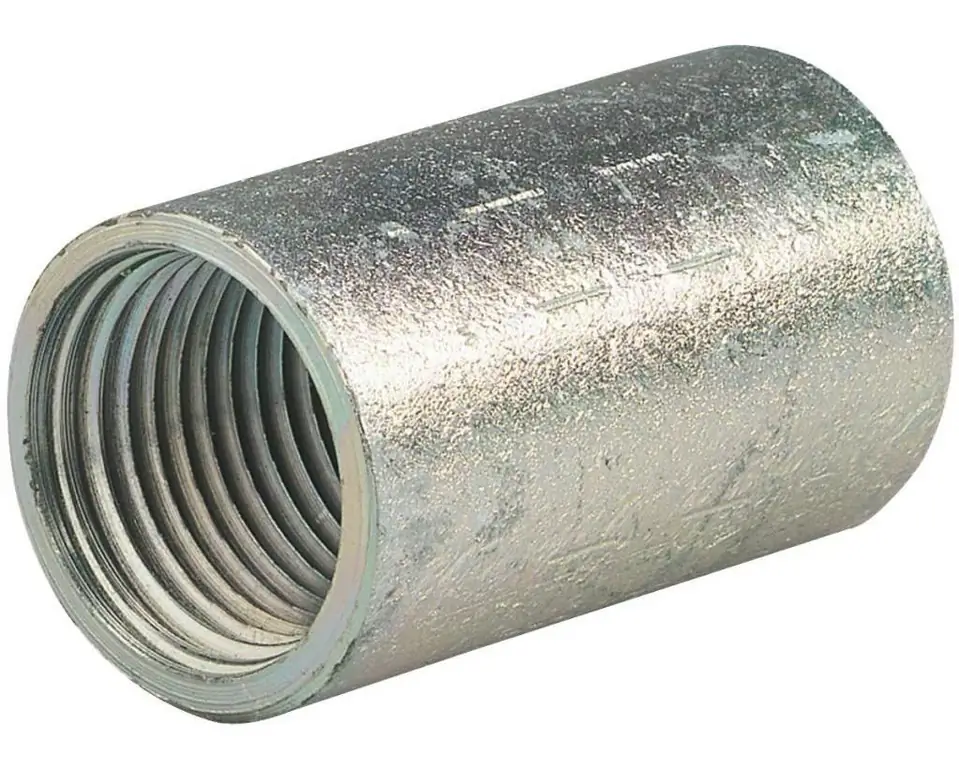
Next, you should pay attention to the joining of rigid pipes. The use of welding and threading are not the only ways. However, there is a certain rule according to GOST 16037-80, which says that all structures with a cross section above 600 mm can only be connected by welding. Usually, if notthreading and welding are used, then they resort to connecting through a coupling. This method will allow you to fasten together pipes of equal diameter, different sections, as well as from different materials. The main features of this connection are high strength and good tightness.
Periodically, pipes connected without welding and threads have flanges, with the help of which the articulation takes place. In some situations, certain sections of pipes need frequent inspections or repairs. To control the welded joints of pipelines is a rather laborious task, and therefore in such places, if the pipe section allows, it is the flange connection that is installed. This is due to the fact that this type of docking is quite simple to disassemble and assemble back. It consists of the following elements:
- two main elements - connecting flanges;
- O-rings are used for greater tightness;
- bolts and nuts are used for fastening.
Unusual Articulation Methods
In addition to the usual methods of joining, which are popular, there are non-standard, rarely used, and for pipes made of special material. Among these connection methods, there is a gluing method, a socket joint, a quick-connect method connection.
Gluing is used when pipes are made of plastic. In such situations, the gluing method helps to obtain a reliable and tight connection, however, it will be one-piece. As the name implies, the assembly uses a special adhesive base applied topipe surface.
As for the second option, the socket connection, it is most often used in cases of arranging non-pressure sewers. Such systems are distinguished by the fact that the wastewater in them moves naturally, without the effort of the pumps, that is, the pipes are installed at an angle. The socket connection can be both detachable and one-piece. The choice will directly depend on the material from which the pipes are made. Detachable communications of this type can only be made of plastic. If the parts are made of cast iron, then only one-piece docking can be carried out. In addition, cast iron pipes require sealing, which is made on the basis of a cement mixture or special hermetic compounds.
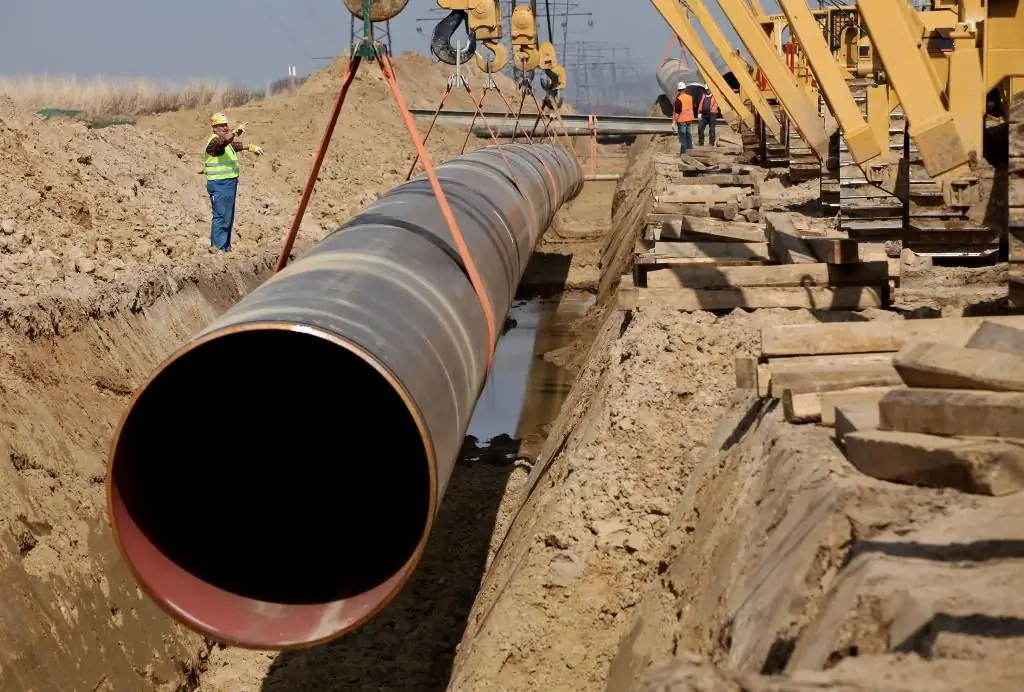
Quick couplings
There is a small group of separate connections that are called quick-release or quick-release. They are usually installed only in those areas where frequent analysis of the highway is required for any reason. There are three main options for such joints:
- using clamps with special wedges for fixation;
- cam connection or Camlok;
- ISO connection.
All three options are quite simple in terms of their installation, but at the same time they have good strength characteristics. On an industrial scale, additional three types of docking are often used: nipple, telescopic, articulated. The nipple connection is used in cases where pipes are joined between measuring equipment,telescopic - for the articulation of rigid pipes with flexible elements. Articulated are used only for arranging highways with a complex structure.
GOST connection requirements
The regulatory document specifies certain requirements for pipeline connections made on the basis of welding. The document contains the following items:
- In some cases, welding of pipes with different diameters is required. In this case, if the difference does not exceed a certain value, then the work is carried out in the same way as it would be carried out if there was the same cross section. The structural elements of all prepared edges, the final seam and other details must be suitable for a pipe with a large diameter. In addition, in order to ensure a smooth transition from a larger diameter to a smaller one, it is allowed to make an inclined seam. If the diameter of the pipes differs too much, then a bevel must be made on a product with a large cross section. Work is carried out until the diameter decreases to a value equal to the smaller one. In this case, the seam and structural elements must match the part with a smaller diameter.
- There are requirements for the roughness of surfaces that are prepared for welding. The value of this characteristic should not exceed 80 microns.
- All elements remaining on the pipes (couplings, linings) must be made of steel of the same grade as the pipe itself.
Seam quality control
The welded joint is very strong, but it needs quality control. Currently, there are only two verification methods. The first method is characterized by the absence of violations in the integrity of the structure, while the second is carried out with a violation. To assess the quality of all welds, the first method is usually used. It is used both during the work and after.
Non-destructive verification method is divided into 5 options:
- permeability test;
- control by X-ray or magnetic method;
- ultrasonic variant;
- carrying out measuring work;
- implementation of external inspection.
Destructive testing methods are also carried out, but already on those pieces of the product that are cut from the main pipe.
Any connection quality check begins with an external inspection. It is important to note here that it can be not only visual. This also includes the use of measuring equipment and the use of any other technical means. This check helps to determine whether there are problems in external factors, as well as to verify that the connection meets the requirements of the state standard.
There are capillary tests that use special fluids. Welded seams are covered with a contrast agent. In the presence of the smallest damage or cracks, these compounds will penetrate inside. When using such substances, defective areas will be painted in a certain color. Penetrants are the names of these special liquids. They may consist of bases such as transformer oil, turpentine, benzene, kerosene.
The easiest way to check with this method isuse of kerosene. This composition has one of the most important properties for this method - high penetrating power.
There are several points that play a decisive role in choosing a verification method. One of the most important factors is financial savings and technical data, then the features under which this welded structure was manufactured play an important role. Attention should also be paid to the condition of the surface being checked, the thickness and type of weld. It is important to correctly determine the grade of metal and understand its physical properties.
Recommended:
Sberbank: details for transferring to the card. Sberbank details for transfer to the card
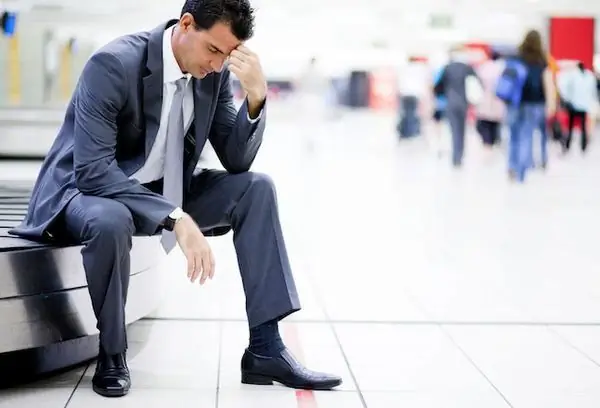
Most of the owners of bank cards from Sberbank and other banking institutions do not even suspect that their plastic card, which they use daily, has its own bank account
Gas pipeline to China. Project and scheme of a gas pipeline to China
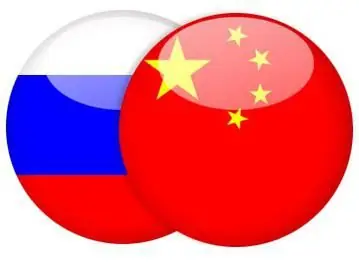
Russia and China have signed a long-awaited gas contract. To whom is it beneficial? Will the fact of its signing affect the geopolitical situation?
What is radiographic testing? Radiographic control of welds. Radiographic control: GOST
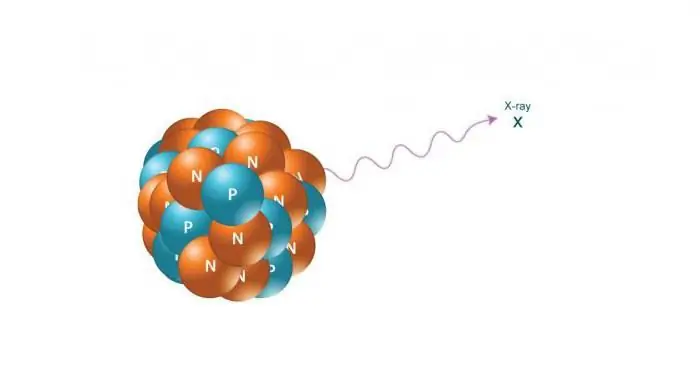
Physical bases of radiation control methods. Features of radiographic control. The main stages of radiographic control of welds. Safety precautions in the production of radiographic control. Normative and technical documentation
Laying a gas pipeline: methods, equipment, requirements. Gas pipeline security zone
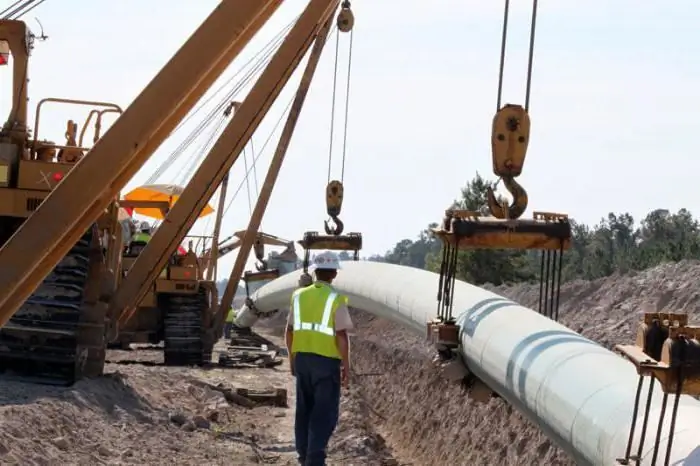
Laying of the gas pipeline can be done by underground and ground methods. When choosing equipment for such systems, safety standards should be followed. Actually, the laying of highways is carried out with strict observance of all the required technologies
Gas pipeline to Crimea. "Krasnodar Territory - Crimea" - the main gas pipeline with a length of 400 km
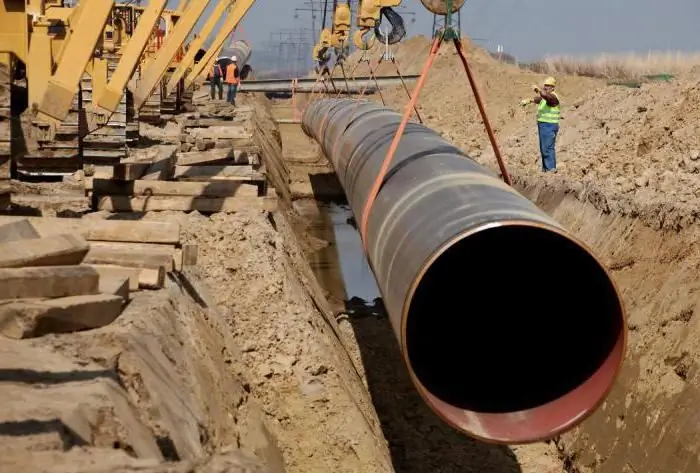
The gas pipeline to Crimea was commissioned in December 2016. Its construction took place at an accelerated pace in order to solve the main problem of the Crimean gas transportation system: the lack of own gas to fully supply the peninsula due to increased consumption