2025 Author: Howard Calhoun | [email protected]. Last modified: 2025-01-24 13:10
One of the most common sheet metal processing processes has become material bending. This process is not energy intensive, and therefore, if there is no need for high productivity, then most often this work is performed on manual machines.
Hand bending
It's worth starting with the fact that any metal that is subjected to bending has elastic properties. For this reason, during sheet metal processing, when a short-term deforming force is applied to the workpiece, the characteristics of the material do not always have time to be fully realized. In other words, after applying force to a metal workpiece, it will partially restore its original shape. In the industry, this has become known as springback. It is also worth adding that using a mechanical sheet metal bending machine rather than a manual one will not solve this problem, as the contact time of the punch with the workpiece will not change.
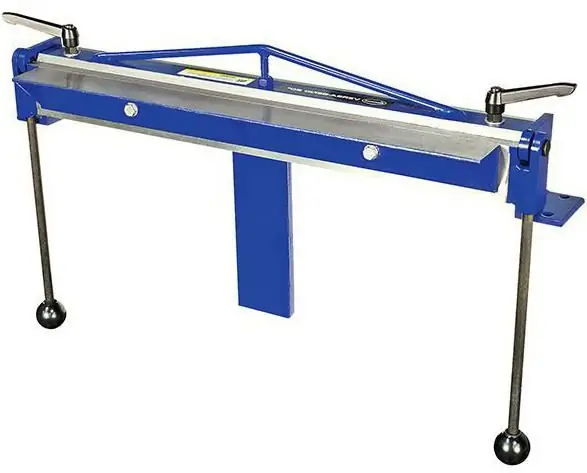
Compensation Methods
Were designedcertain methods by which it is possible to compensate for the effect of metal springback.
- The first method is to increase the metal bending angle by the springback angle. This method will be most effective if the characteristics, as well as the alloy grade, were accurately determined before starting work with sheet metal.
- In certain cases, a hydraulic sheet metal bending machine is used. This addition makes it possible to withstand the load under the influence of a load for a longer period, which significantly reduces the springback coefficient.
- Before being processed, the plates may be annealed. This operation significantly increases the plasticity of the material, however, there is also a certain minus - scale is formed, which will have to be removed before proceeding with bending.
- Some punches or, in rare cases, dies are equipped with additional structural elements - recesses or undercuts. The use of these devices significantly reduces the manifestation of plastic forces.
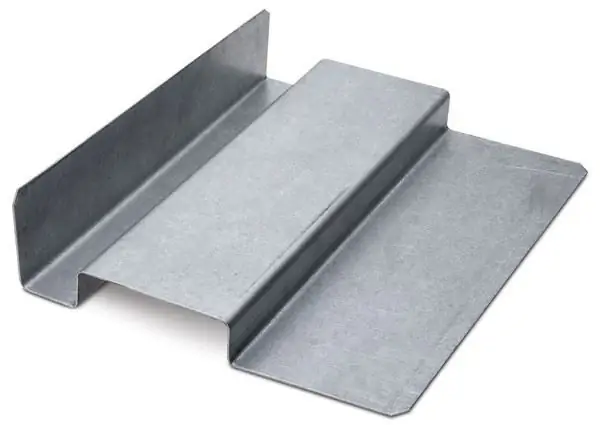
Varieties of technologies
Naturally, in the case of using a manual machine for sheet metal processing, the force that can be applied to the workpiece is greatly limited by the physical capabilities of a person. For this reason, various technological methods have been invented to carry out this procedure.
- The first method is free bending with a non-profiled tool. When using this methodthe workpiece is fixed with the help of two supports, which are located opposite each other. The deformation occurs with the help of a punch, which has a certain radius of the working area. This method is most commonly used for sheet metal processing, single-angle V-bending. The peculiarity of the technology is that minimal effort is required for bending.
- Another method is gauge bending. This process is carried out within the matrix. It follows that a machine designed for sheet metal working should therefore be equipped with a more powerful bed and table.
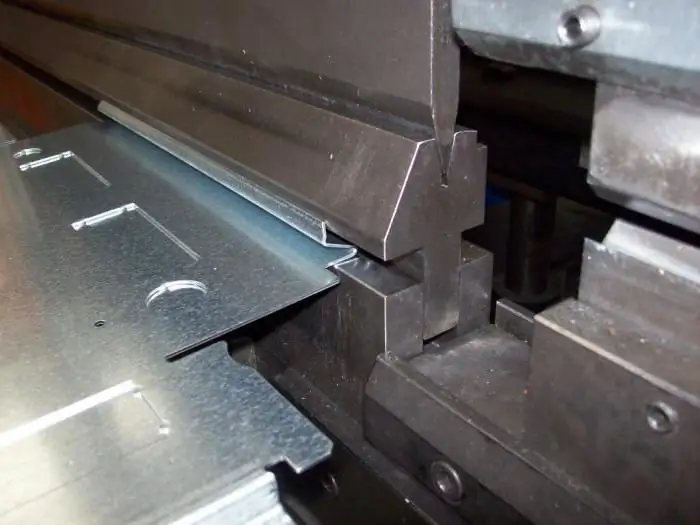
When metal bending is selected
The processing of such raw materials with a bending operation is selected based on certain factors.
- Features that the machine has to perform this operation.
- Depends on the grade of metal used in production.
- Highly dependent on device performance. It is important to understand here that most often sheet metal processing is required by flexible, cutting, punching holes and other operations.
- The maximum effort that a bending or rolling machine will require to perform the desired operation is also important.
- An important selection criterion will be the accuracy with which the machine can handle the task. This specification depends on the clamping devices available on any bending machine.
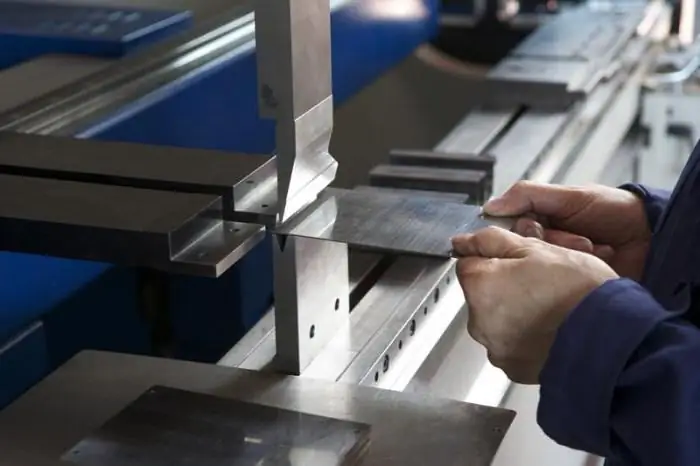
Types of equipment for coldbending
The main advantage of manual bending is that the protective coating does not peel off during processing, and therefore the presence of a layer of paint, zinc, etc. is allowed. There is also a classification of machines for cold bending:
- An important factor is the width of the desktop. This factor determines the maximum workpiece width.
- It is also important to have sheet metal cutting equipment. Most often, this role is played by an additional knife used for roller cutting of edges.
- Also an important factor is the maximum amount of torque that is applied to the handle of a hand tool.
- In addition, the equipment is divided into classes depending on the drive that controls the movement of the slider. It can be a handle or a pedal. There are also combined types.
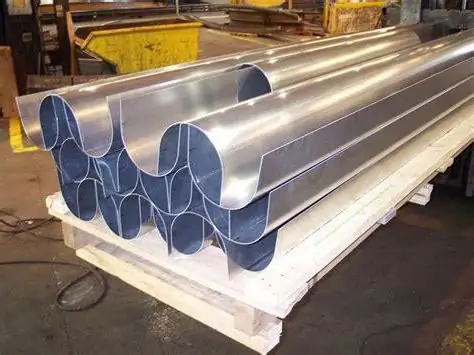
These options are standard. The leading manufacturers of this equipment are trying to provide it with the maximum number of additional options.
Additional processing methods
In production, there are additional processing methods that are considered simplified. Such methods include stamping with elastic materials, metal spinning, high-speed stamping, etc.
For example, if we consider stamping with elastic materials, then there are some peculiarities here. The machine on which such an operation is carried out has only one working element made of metal - it can be a punch or a matrix. The second onemade of rubber, plastic, polyurethane and liquid.
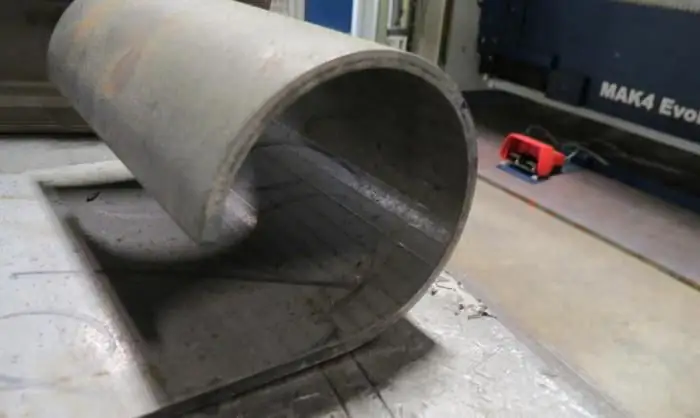
Assume that the template used for laying the workpiece will be selected as the metal part. This means that a rubber pad will be used in the press slider, which will press the material against the template. It is worth noting here that if the template is characterized by sharp edges, then the free edges of the workpiece are first bent, and then cut off along the cutting edge. In this way, punching and punching of the material can be performed.
Sheet metal polishing
This process is designed to give the finished product an aesthetic appearance, shine. In addition, this operation is also used in cases where it is necessary to apply any additional layer of paint, protective agent, etc. to the surface of the workpiece in the future.
This operation can be carried out in the following ways:
- mechanical or abrasive polishing;
- treatment with chemicals;
- electrochemical method;
- electrolyte-plasma method.
It can also be added that the technology for some types of polishing does not require special equipment. For example, the mechanical method can be carried out independently at home. However, the natural disadvantage is that it will not be possible to achieve a significant result or high quality of grinding.
Recommended:
Plastic processing: technology, equipment
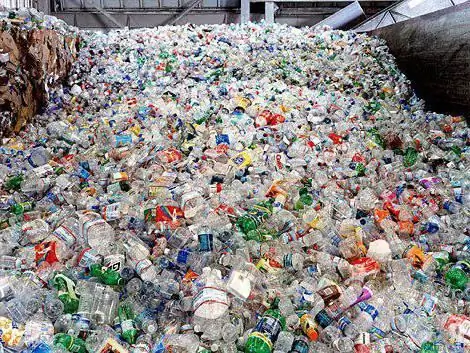
Plastic materials over the past 10-15 years have formed a wide range of applications in which their products can be used. The synthetic material itself is currently undergoing a period of radical technological changes, as a result of which the market for building materials is filled with new proposals. Suffice it to mention the families of composites that displace both metals and wood
Meat: processing. Equipment for meat and poultry processing. Production, storage and processing of meat
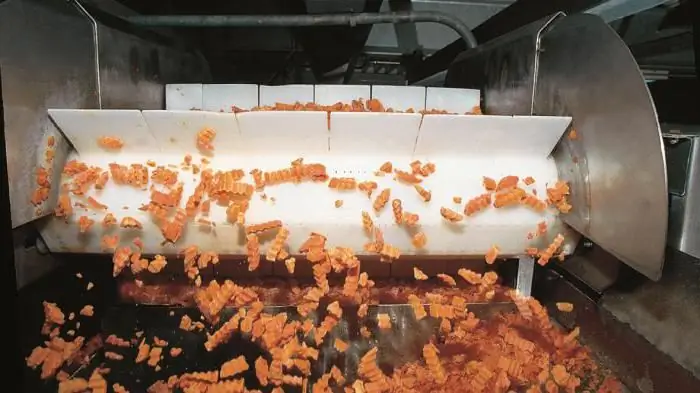
Information of state statistics show that the volume of meat, milk and poultry consumed by the population has significantly decreased in recent years. This is caused not only by the pricing policy of manufacturers, but also by the banal shortage of these products, the required volumes of which simply do not have time to produce. But meat, the processing of which is an extremely profitable business, is very important for human he alth
Liquidation balance sheet is Definition of the concept, approval, form and sample of filling out the liquidation balance sheet
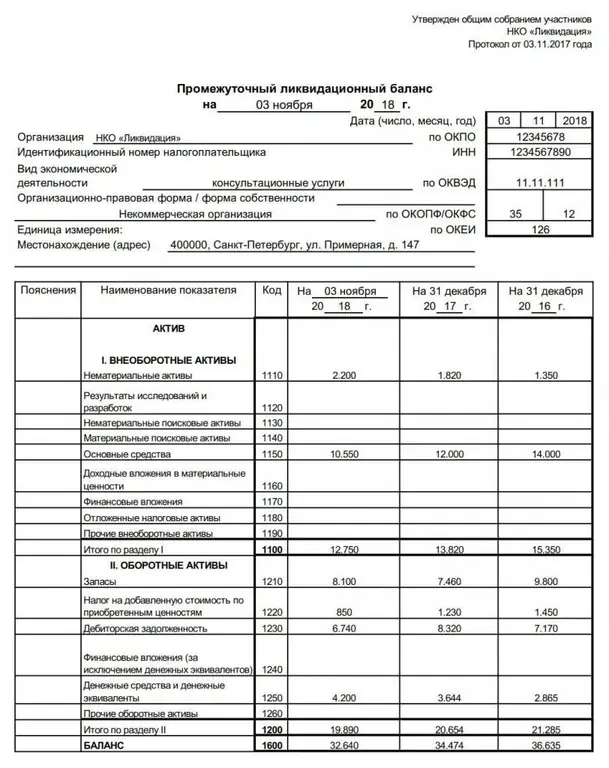
The liquidation balance sheet is an important financial act drawn up during the closing of an organization. It can be intermediate or final. The article tells what is the purpose of these documents, what information is entered into them, as well as how and when they are approved and submitted to the Federal Tax Service
Sheet metal cutting: description, types. metal bending
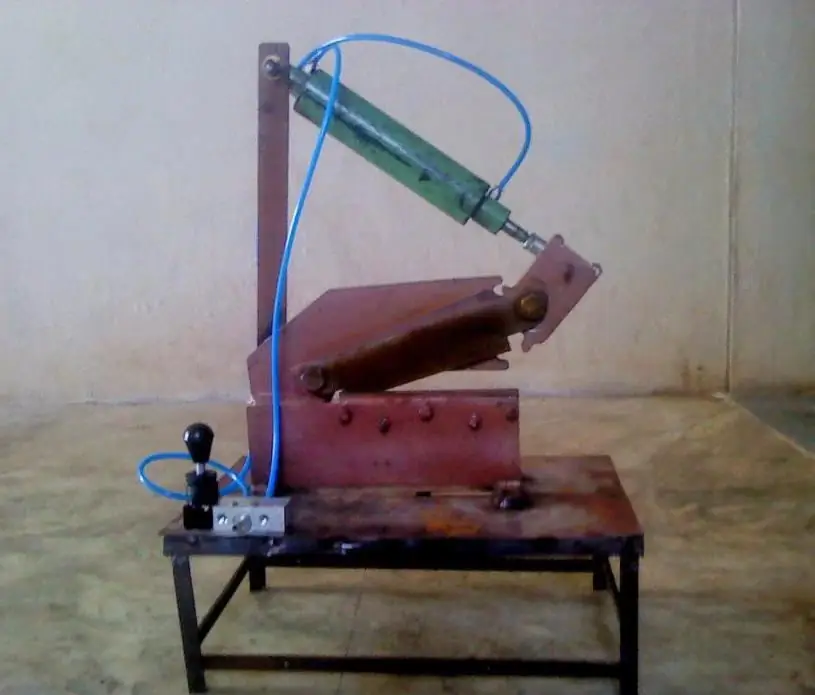
Today, sheet metal cutting is one of the fairly common technological processes that allows you to get blanks of the desired size and shape. However, there are many methods for performing this procedure and a wide variety of equipment
Drilling is a type of mechanical processing of materials. drilling technology. Drilling equipment

Drilling is one of the types of material machining by cutting. This method uses a special cutting tool - a drill. With it, you can make a hole of different diameters, as well as depths. In addition, it is possible to create multifaceted holes with different cross sections