2025 Author: Howard Calhoun | [email protected]. Last modified: 2025-01-24 13:10
Today, sheet metal cutting is one of the fairly common technological processes that allows you to get blanks of the desired size and shape. However, there are many methods for performing this procedure and a wide variety of equipment.
Mechanical cutting type
Mechanical sheet metal cutting requires a tool. The main requirements for a cutting object are strength and hardness. These two characteristics must necessarily exceed those of the metal being processed, otherwise it will not work to cut the workpiece. In some cases, this cutting method is also called cold cutting.
The main mechanical methods include guillotine cutting, band saw cutting, waterjet cutting, and grinder cutting.
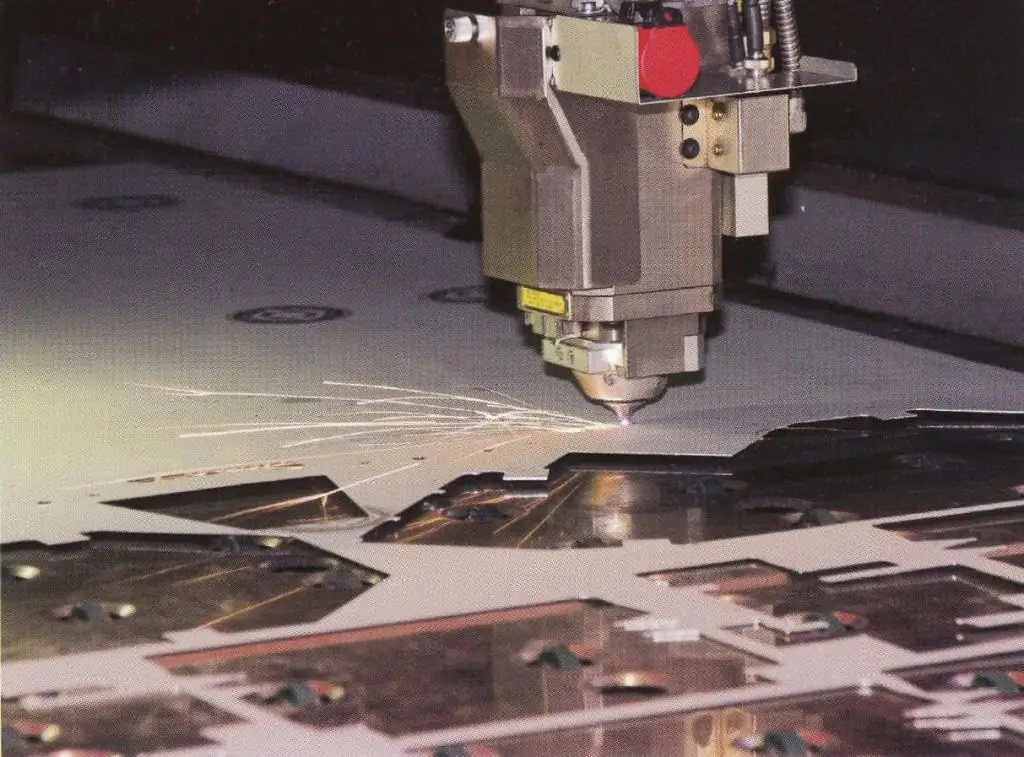
Using scissors
The easiest way to cut sheet metal is to use a guillotine shear. This method can be used only in cases where it is necessary to cut thin metal, for example, galvanized or profiled sheet. The cutting part in such a tool is a knife, and the scissors themselves can be not only manual, but also automatic, pneumatic, hydraulic. If we talk about the prices of this tool for cutting metal, then manual and pneumatic devices are the cheapest. However, low productivity and a large amount of effort do not make this device popular. For these simple reasons, the electric unit is more popular. In this case, a grinder (a special type of grinder) is widely used.
However, such an apparatus can not be used for all metals. Those blanks that are coated with a polymer layer cannot be cut in this way, otherwise their coating will be damaged. In addition, when working with an electrical appliance, it is necessary to observe safety precautions very precisely. The greatest danger is represented by fragments that can fly off. Cutting and bending sheet metal with an abrasive wheel, which is used in a grinder, reduces the strength characteristics of polymer-coated metals. Another very important parameter is overheating. To avoid problems, you have to turn off the machine every 5 minutes of continuous operation.
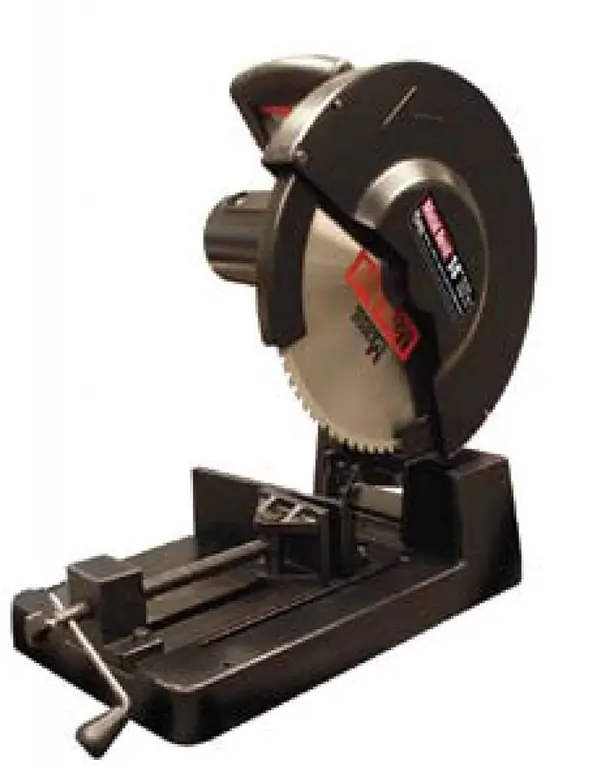
Band saw method
To implement this method, a sheet metal cutting machine is already used. Its cutting part is a band cutter, which is characterized by a different distance of teeth between each other. The interval between them depends on how high-quality the material needs to be cut. It is worth highlighting here that thisthe technological process is characterized by a fairly high productivity, the thickness of the cut is not more than 2 mm, and the cleanliness of processing is also at a high level.
It is worth noting that the band saw method can be applied to any alloy, and the cutting angle can be any that is required. Of the minuses, it is worth highlighting only the fact that such a productive machine completely lacks the possibility of curly cutting.
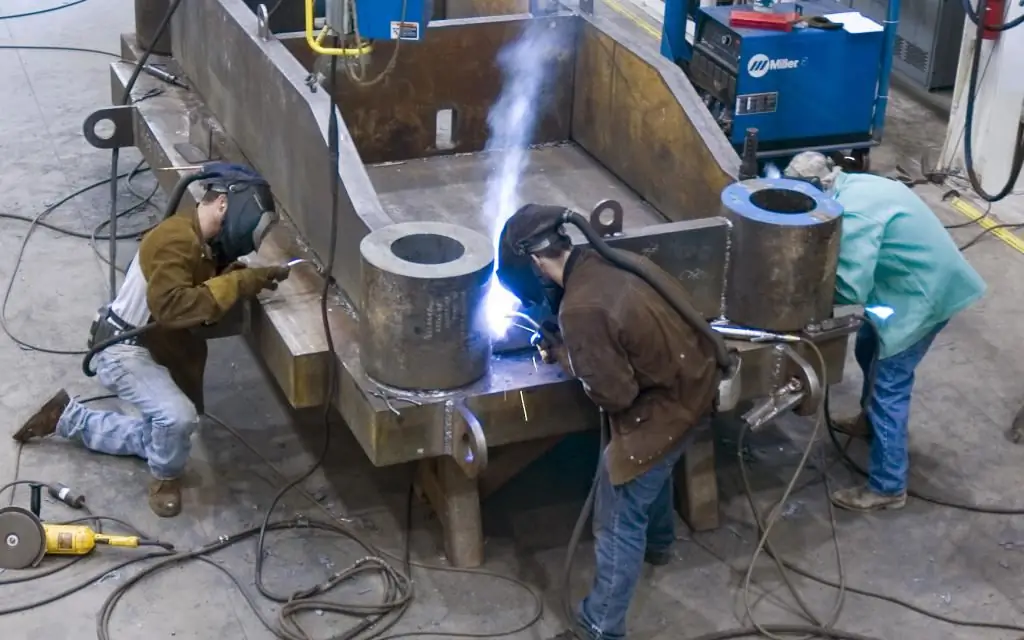
Plasma method
Plasma cutting of sheet metal is currently considered one of the modern methods, and also belongs to the thermal processing group, and not to the mechanical one. In this case, not metal teeth, knives, etc., but a plasma jet are used as a cutting tool.
The basis of this method is that gaseous substances are used in a state of high temperature (plasma). To obtain this effect, an electric arc discharge is used. Two methods are used to perform the operation: plasma cutting of sheet metal with a jet or an arc.
In the first case, the cutting jet will be formed between the two electrodes of the machine. In the second case, cutting will take place using an arc that will form between the electrode and the metal. This is made possible by the fact that the metal blank is included in the chain. The plasma temperature during operation can reach 30,000 degrees Celsius.
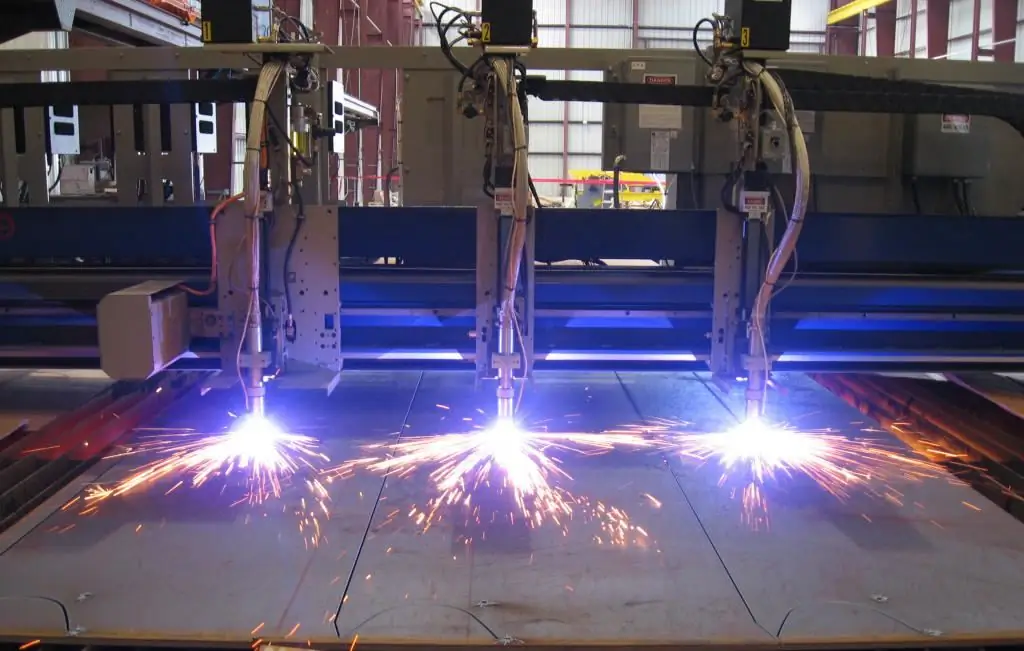
Laser cutting
Laser cutting of sheetmetal is the use of thermal energy of a narrowly focused thermal laser beam. The main advantages of this processing are that it is as accurate as possible, the thickness of the cut is minimal, and the highest purity of processing is also observed. It is advisable to use this method only if the thickness of the metal is not more than 15 mm. In addition, on such a machine, you can easily perform curly cutting. Sheet metal laser cutting is most often used for making jewelry, which, in addition to cutting, also requires shape bending.
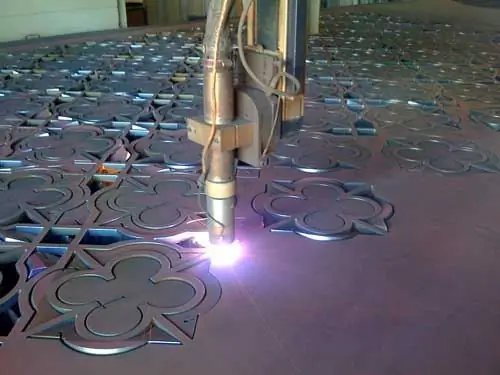
Bending of metal blanks
Naturally, the main difference of this method is that there is no cutting of the workpiece. The deformation is carried out only due to the plastic properties of the metal. The main advantages of this method over cutting are that material is saved due to the fact that there is almost no waste. Due to the fact that there are no joints, welds, etc., the mechanical strength of the product remains at the same level. Corrosion resistance is also maintained as there is no significant structural change at the cutting points.
If we consider both methods, then cutting and bending sheet metal are the two main methods today, which are used to obtain metal blanks with a wide variety of shapes, sizes, and more.
Recommended:
Metal band saw. Metal cutting machine
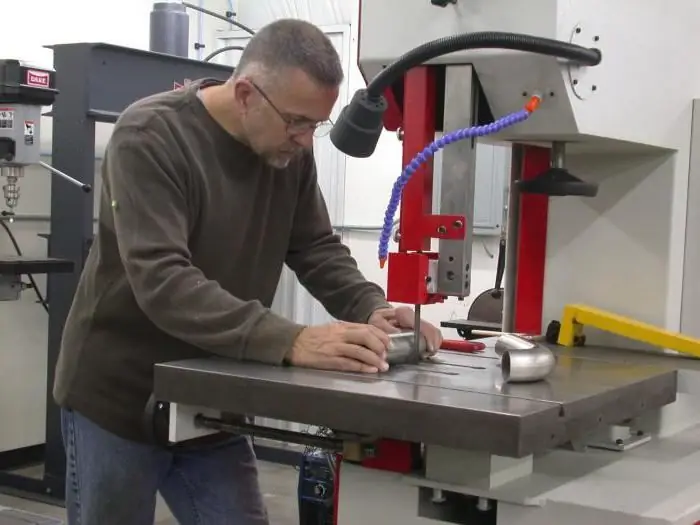
Metal band saw is a high-performance equipment that is responsible for a variety of functions, such as cutting metals and cutting a variety of strong and high-strength materials
Bending machines: types, description, principle of operation
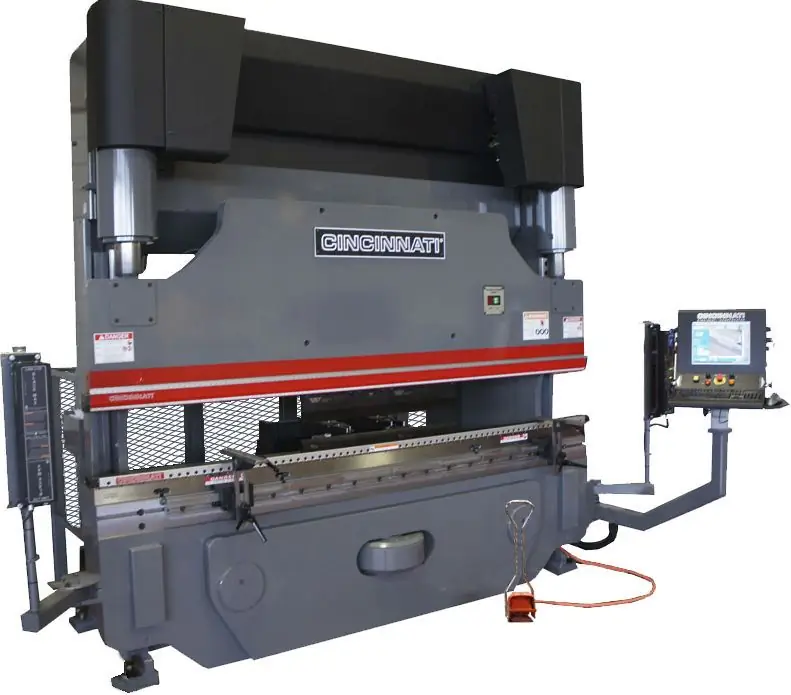
Bending machine: description, specifications, features, principle of operation, photo. Edge bending machines: varieties, device, design, parameters, manufacturers. Manual and rotary hemming machines: what's the difference?
Cutting mode for milling. Types of cutters, calculation of cutting speed
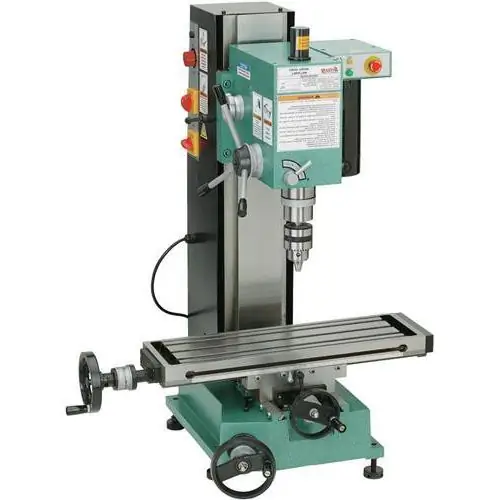
One of the ways to finish materials is milling. It is used for processing metal and non-metal workpieces. The workflow is controlled by cutting data
Bending machines: types, description of designs, characteristics, settings
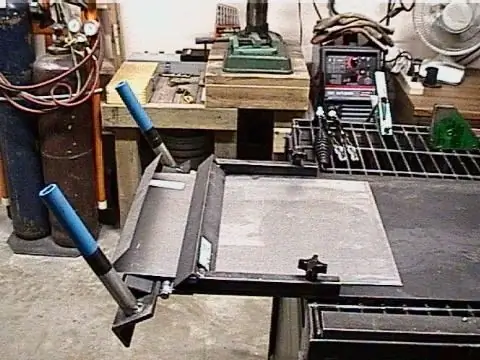
Bending machines: types, design features, application, photo. Description of machines, technical characteristics, settings, modifications
Metal cutting machine. Plasma metal cutting machine
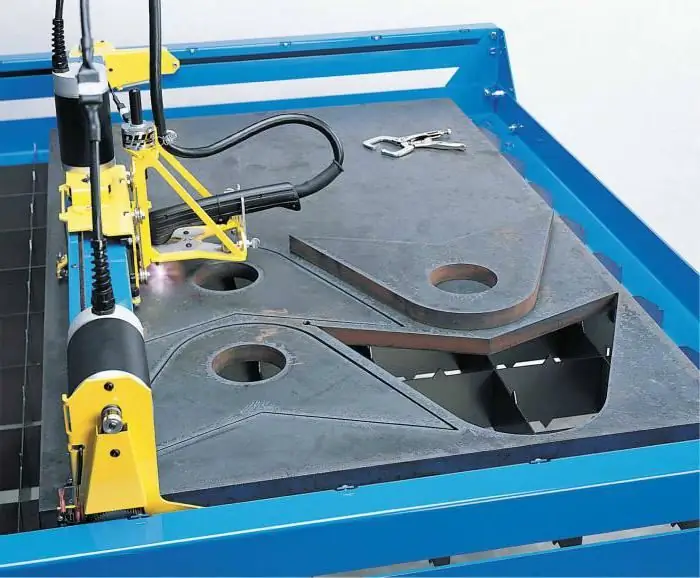
The article is devoted to the apparatus for cutting metal. The technology of plasma cutting, as well as the device and features of the equipment are considered