2025 Author: Howard Calhoun | [email protected]. Last modified: 2025-01-24 13:10
Drilling is one of the types of material machining by cutting. This method uses a special cutting tool - a drill. With it, you can make a hole of different diameters, as well as depths. In addition, it is possible to create polyhedral holes with different sections.
Assignment of operation
Drilling is a necessary operation if you want to get a hole in a metal product. Most often, there are several reasons for drilling:
- required to create a hole for tapping, countersinking, reaming or boring;
- necessary to place electrical cables, fasteners in the holes, pass anchor bolts through them, etc.;
- blank separation;
- weaken collapsing structures;
- depending on the diameter of the hole, it can even be used to plant explosives, such as when mining natural stone.
This list can be continued for a long time, but we can already conclude that the drilling operation isone of the simplest and at the same time quite necessary and common things.
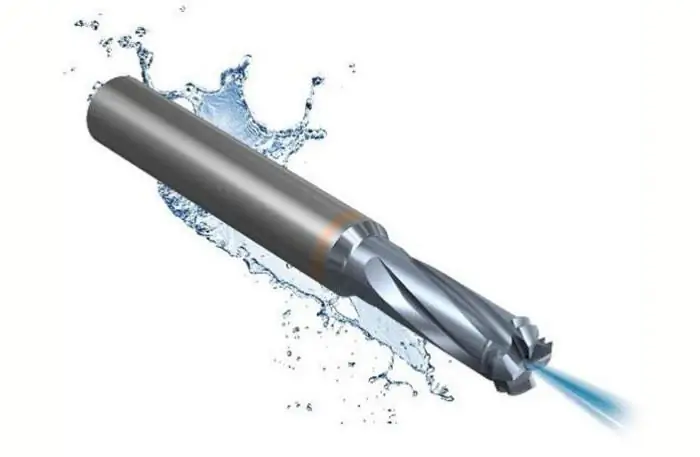
Consumables
Naturally, to carry out the drilling process, it is necessary to have drills. Depending on this consumable, the diameter of the hole will change, as well as the number of its faces. They can be round, or they can be multifaceted - triangular, square, pentagonal, hexagonal, etc.
In addition, drilling is an operation in which the drill will heat up to high temperatures. For this reason, it is necessary to precisely select the quality of this element, based on the requirements of the material to be worked with.
- A fairly common material for the production of drilling fixtures is carbon steel. Elements of this group are marked as follows: U8, U9, U10, etc. The main purpose of such consumables is drilling holes in wood, plastic, soft metals.
- Next are drills made from low alloy steel. They are intended for drilling the same materials as carbon ones, but their difference lies in the fact that this brand of elements has an increased heat resistance value of up to 250 degrees Celsius, as well as an increased drilling speed.
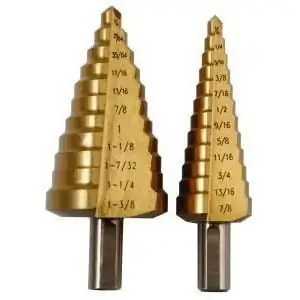
Improved drills
There are several types of drills that are designed for higher quality materials:
- The first type of drill is made from high speed steel. The heat resistance of these consumables is much higher- 650 degrees Celsius, and they are designed for drilling any structural materials in a non-hardened state.
- The next group is carbide drills. They are used to make holes in any structural non-hardened steels, as well as in non-ferrous metal. A feature is that drilling at high speeds is used. For the same reason, heat resistance has been increased to 950 degrees Celsius.
- One of the most durable elements is Borazon drills. Used for work with cast iron, steels, glass, ceramics, non-ferrous metals.
- The last group is diamond drills. Suitable for drilling the hardest materials, glass, ceramics.
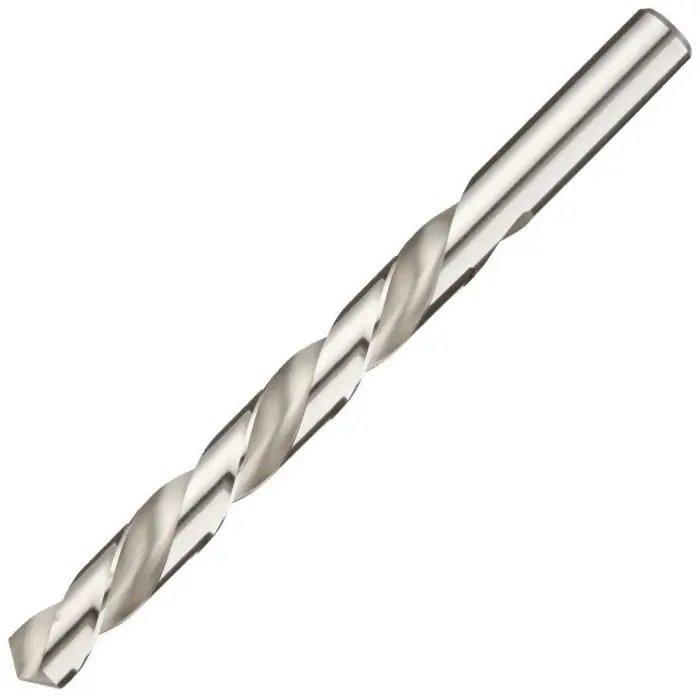
Types of drilling machines
The following types of drilling machines can be used to carry out the drilling operation:
- Vertical and horizontal drilling devices. Drilling holes for such machines is the main operation.
- Vertical and horizontal boring type machines are used. Drilling is considered ancillary operations for these devices.
- Vertical, horizontal and universal milling machines. For these units, drilling is also a secondary operation.
- Lathes and lathes. On the first type of devices, the drill is a fixed part, and the workpiece itself rotates. For the second type of device, drilling is not the main operation, and the drill is a fixed element, as in the firstcase.
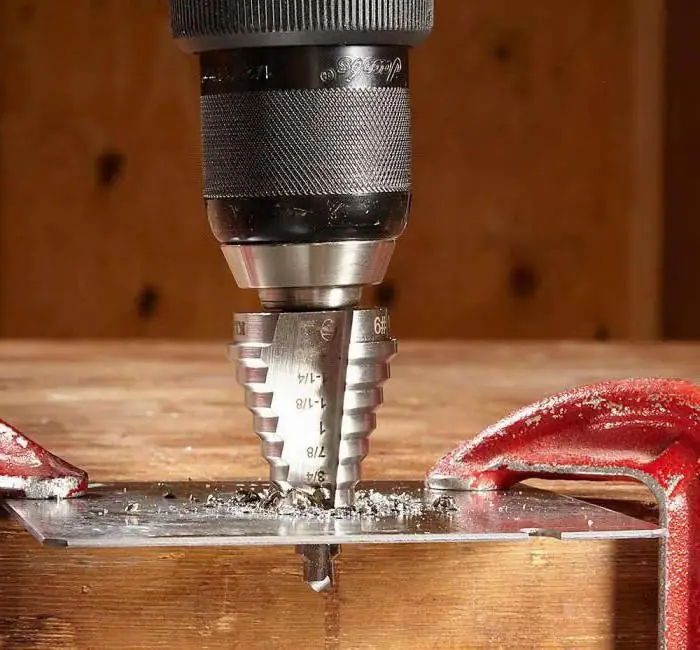
These are all types of drilling machines that can carry out all the required operations.
Hand tools and auxiliary operations
In order to facilitate the drilling process, several auxiliary operations are used. These include the following:
- Cooling. When drilling, a variety of cutting fluids are used. These include, for example, water, emulsions, oleic acid. Gaseous substances such as carbon dioxide can also be used.
- Ultrasound. The ultrasonic vibrations produced by the drill are used to increase the productivity of the process as well as to enhance chip breaking.
- Heated. In order to improve the drilling of metal having a high density, it is preheated.
- Strike. Some surfaces, such as concrete, require the use of rotary impact motions to increase productivity.
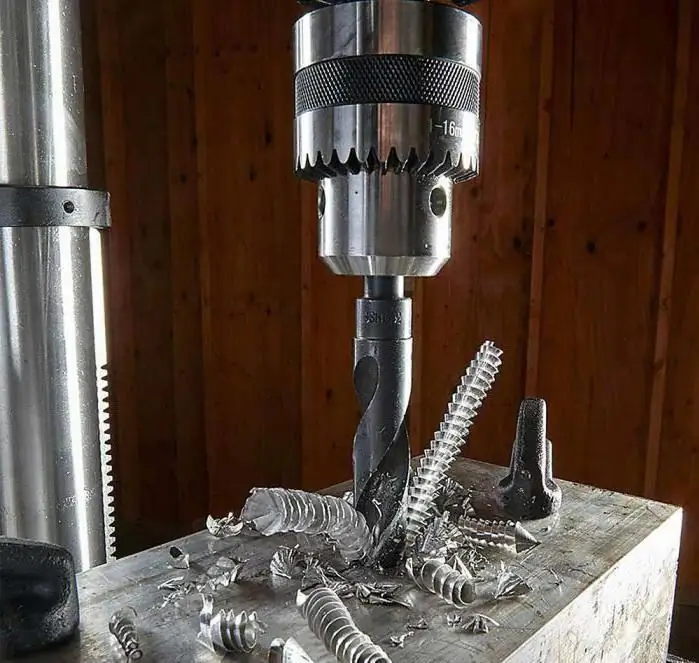
This procedure can be carried out not only on machines in automatic mode, but also on manual equipment. Manual drilling involves the use of tools such as:
- Mechanical drill. Drilling uses human mechanical power.
- Electric drill. It can carry out conventional and shock-rotary drilling. Powered by electricity.
Types of treatment and cooling
There are several basic types of drilling - these aremaking cylindrical holes, polyhedral or oval, as well as drilling existing cylindrical holes to increase their diameter.
The main problem that occurs in the process of drilling metal is the strong heating of the consumable element, that is, the drill, as well as the place of work. The temperature of the material can reach 100 degrees Celsius or more. If it reaches certain values, then combustion or melting may occur. It is important to note here that many of the steels that are used to make drills lose their hardness when heated, which will only increase friction, so the element will, unfortunately, wear out faster.
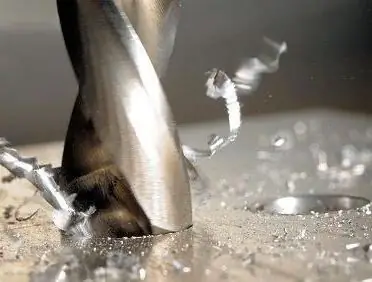
In order to combat this shortcoming, various coolants are used. Most often, with vertical drilling on the machine, it is possible to organize the supply of coolant directly to the place of work. If it is carried out using hand tools, then after a certain period of time it is necessary to interrupt the process and dip the drill into the liquid.
The essence of drilling
Hole drilling technology is the process of forming grooves by removing chips in a solid material with a cutting tool. This element performs rotational and translational or rotational-translational movements at the same time, which forms a hole.
The use of this type of material processing is used to:
- obtain non-critical holes with a low degree of accuracy and roughness grade used for mounting bolts, rivets, etc.;
- get holes for tapping, reaming, etc.
Processing options
Using the procedure of deep drilling or reaming, holes can be obtained that will be characterized by the 10th or 11th degree of surface roughness. If it is necessary to obtain a better hole, then after the completion of the processing process, it is necessary to additionally countersink and ream it.
In order to increase the accuracy of work, in some cases, you can resort to careful adjustment of the position of the machine, properly sharpened consumables. A method is also used in which work is carried out through a special device that increases accuracy. This device is called a conductor. There is also a division of drills into several classes. There are straight flute twist drills, spade bits used for deep or core drilling, and center drills.
Description of drill design
Most often, a conventional twist drill is used for work. Specials are used much less frequently.
The spiral element is a two-tooth cutting part, which includes only two main parts - a shank and a working part.
If we talk about the working part, then it can be divided into cylindrical and calibrating. On the first part of the drill, there are two helical grooves opposite each other. Mainthe purpose of this part is to remove chips that are released during operation. It is important to note here that the flutes have the correct profile, which ensures the correct formation of the cutting edges of the drill. In addition, the necessary space is created, which is necessary for the removal of chips from the hole.
Drilling technology
Here it is important to know a few specific rules. It is very important that the shape of the flutes, as well as the angle of inclination between the direction of the axis of the drill and the tangent to the belt, be such as to ensure easy chip evacuation without weakening the section of the teeth. However, it is worth noting here that this technology, and especially the numerical values, will change markedly depending on the diameter of the drill. The thing is that an increase in the angle of inclination leads to a weakening of the action of the drill. This disadvantage is more pronounced, the smaller the diameter of the element. For this reason, you have to adjust the angle for the drill. The smaller the drill, the smaller the angle, and vice versa. The total angle of the grooves is from 18 to 45 degrees. When it comes to drilling steel, it is necessary to use drills with an inclination angle of 18 to 30 degrees. If holes are made in brittle materials such as brass or bronze, then the angle is reduced to 22-25 degrees.
Work principles
Here it is important to start with the fact that depending on the material of the tool, the cutting speed will also change. For example:
- If drilling is carried out using tool steel elements, then the minimum speed is 25 m/min, and the maximum speed is 35m/min.
- If machining is done with HSS drills, the minimum speed is 12 m/min and the maximum speed is 18 m/min.
- If carbide drills are used, the values are 50 m/min and 70 m/min.
It is important to note here that the drilling technology involves the choice of the speed of the procedure depending on the diameter of the element itself and low feed (with increasing diameter, the speed also increases).
A characteristic feature of the work is the use of a standard angle at the top for the drill, which is 118 degrees. If it is necessary to work with raw materials that are characterized by high alloy hardness, then the angle should be increased to 135 degrees.
Safety of drills
One of the important tasks in this type of machining was to preserve the cutting properties of the consumable. The safety of these parameters directly depends on which method of operation was chosen and whether it was suitable for this material. For example, in order to eliminate the breakage of a drill on the pass, it is necessary to greatly reduce the feed at the moment the drill is withdrawn from the hole.
Particular attention should be paid to drilling technology in situations where the hole depth exceeds the length of the helical groove of the consumable. At the time of insertion of the drill, chips will still form, but during the exit it will no longer be. Because of this, drills break very often. If there is no way out of the situation, then you need to periodically remove the drill and manually clean it from unnecessary elements, that isshavings.
Drilling bits
In order to make a hole in a certain coating, it is necessary to use crowns. However, they also need to be chosen correctly, based on certain parameters. Currently, three main types of material are used to create crowns - this is diamond, win and tungsten carbide. A feature of the diamond crown is that it performs shockless drilling. In this case, a more correct hole geometry is obtained.
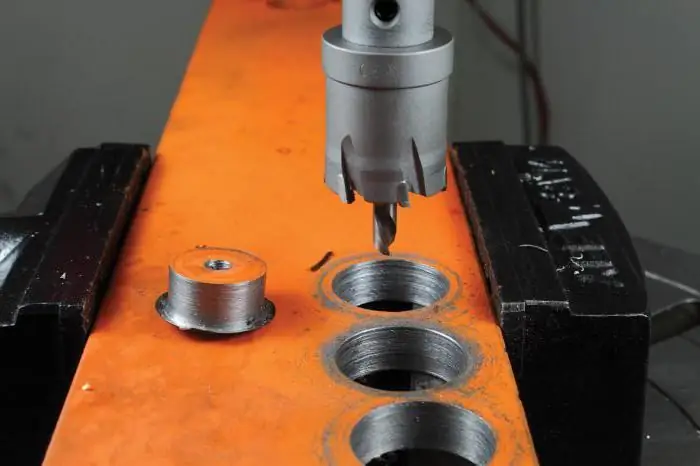
The main advantages of diamond nozzles were the following: the ability to cut reinforced concrete materials, low noise and dust levels, no structure structure damage, since the technology does not use impact force.
Recommended:
Exploratory drilling: features, equipment. Assistant driller for production and exploration drilling
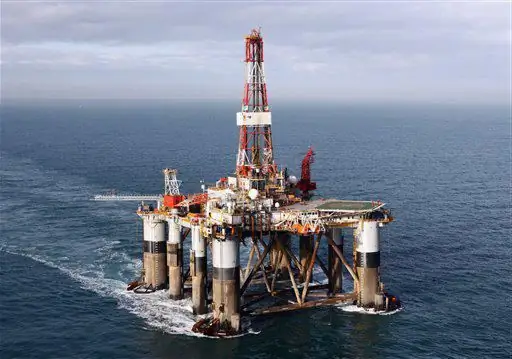
Exploration drilling is an activity aimed at finding raw materials in the bowels of the earth. At the beginning of the 19th century in France, they searched for water in this way. In the 50s of the same century, oil was searched for with the help of exploratory drilling
Meat: processing. Equipment for meat and poultry processing. Production, storage and processing of meat
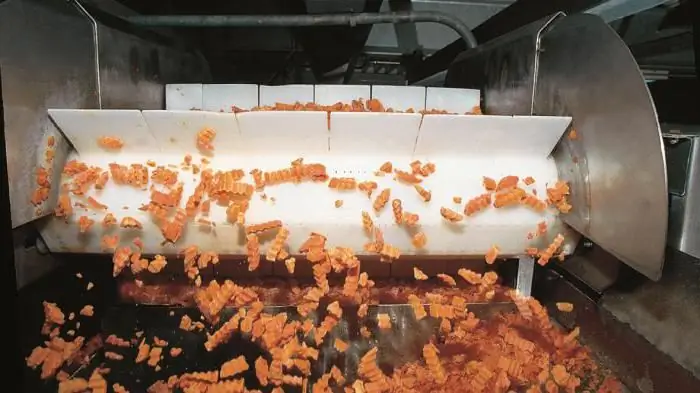
Information of state statistics show that the volume of meat, milk and poultry consumed by the population has significantly decreased in recent years. This is caused not only by the pricing policy of manufacturers, but also by the banal shortage of these products, the required volumes of which simply do not have time to produce. But meat, the processing of which is an extremely profitable business, is very important for human he alth
HDD - drilling technology. Horizontal directional drilling
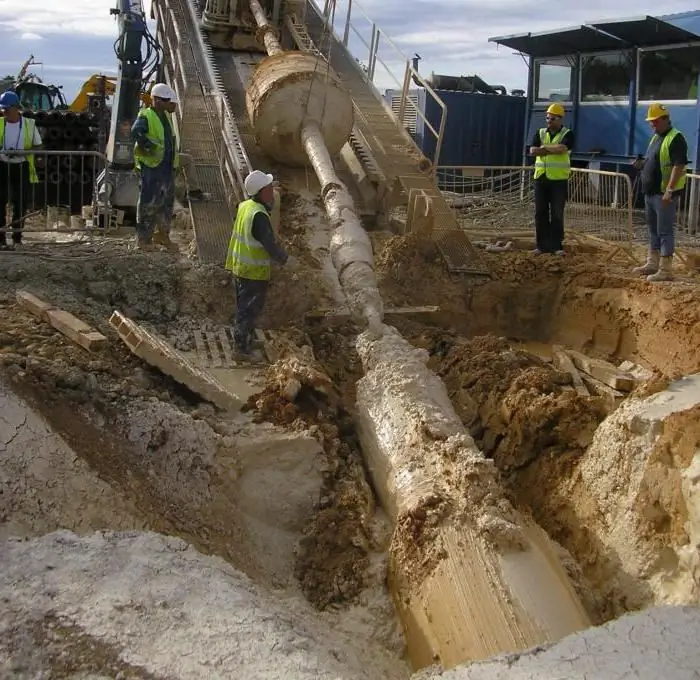
The article is devoted to the technology of horizontal directional drilling. The features of the method, the nuances of its implementation, etc. are considered
Production of polyurethane foam: technology, raw materials, equipment
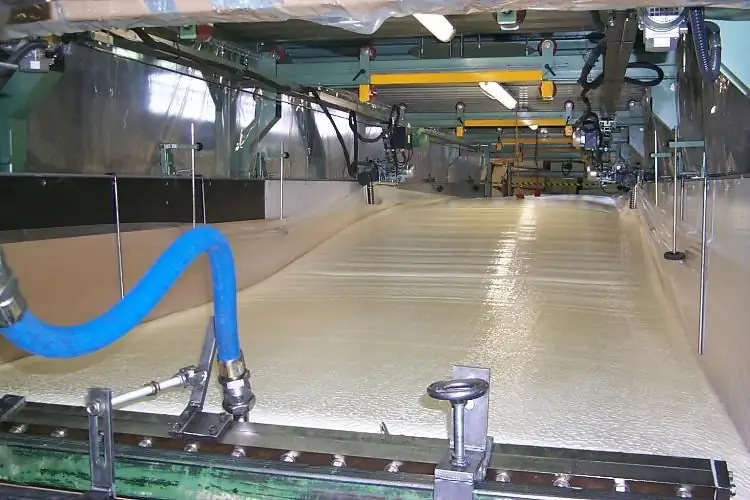
Mounting foam from the usual means of sealing window openings has long passed into the status of a full-fledged building material, which is widely used in a variety of types of work. The variety of applications of this product also determines the need for a differentiated approach to the technologies of its manufacture. However, the differences in foam production methods are more of a cosmetic nature, without affecting the basic technological processes
PVC pipe production: technology, raw materials and equipment
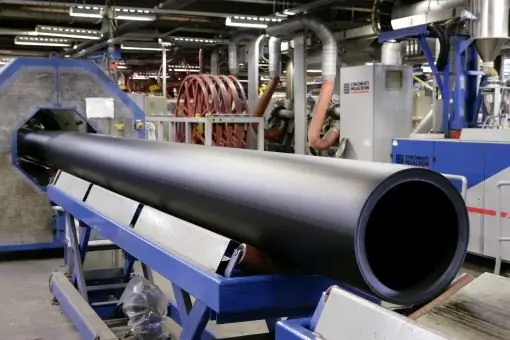
Tubular products based on polyvinyl chloride (PVC) are widely used today in a variety of areas and industries from the private sector to large oil and gas enterprises. But the process of their consolidation on the market was gradual, since the physical and technical properties of the polymer material are inferior to traditional metal counterparts in a number of criteria. However, the modern production of PVC pipes, due to the introduction of advanced technologies, has significantly increased the performance of products