2025 Author: Howard Calhoun | [email protected]. Last modified: 2025-01-24 13:10
Classification of machines involves the division of these devices into some groups. Most of them are designed for processing workpieces by grinding, cutting or drilling. In addition, these devices do an excellent job with wood, textolite, plastic and other inorganic materials. Some models are designed for processing glass and ceramics. Let us consider in more detail the features and characteristics of this equipment.
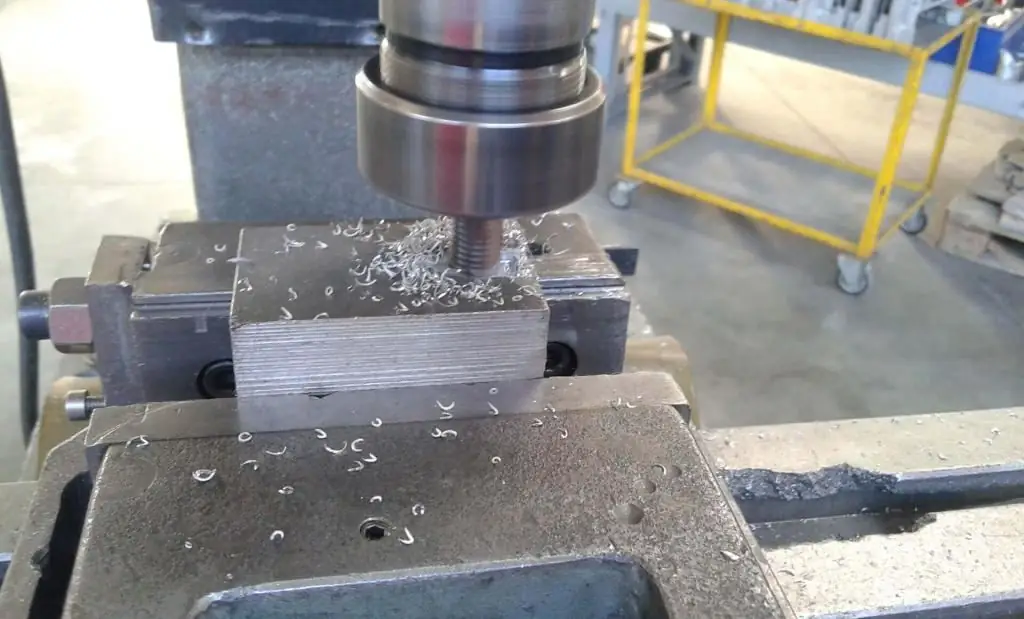
Classification of machines
These devices are divided into several main groups:
- Turning modifications. They are designed for machining rotary workpieces. The only generalization factor for these tools is cutting the part while it is rotating.
- Drilling machines. This group also includes boring models. They are designed for processing metal and other parts by drilling holes in them of the required diameter and length. In horizontal boring versions, this operation can be performed by moving the working table with the workpiece.
- Grinding group combinesmachines that use special nozzles as a working body (abrasive wheels of different specifications and diameters).
- Polishing and finishing machines. The classification and purpose of these devices is focused on finishing workpieces with abrasive powders, tapes, pastes.
Other groups
Gear processing units are included in the category of machines used for processing grinding and other teeth. The class of milling manipulators uses cutters of various configurations and diameters as a cutting tool.
The planing versions are summarized by one common feature: the process is carried out by the method of rectilinear reciprocating motion. Another specific category is cutting and sawing of rolled blanks (channels, angles, similar materials). Also in the classification of machines, the following variations are distinguished:
- extended models that use a multi-blade tool (broaching);
- versions aimed at the processing of threaded connections and its manufacture;
- auxiliary units that include most of the options that the above devices have.
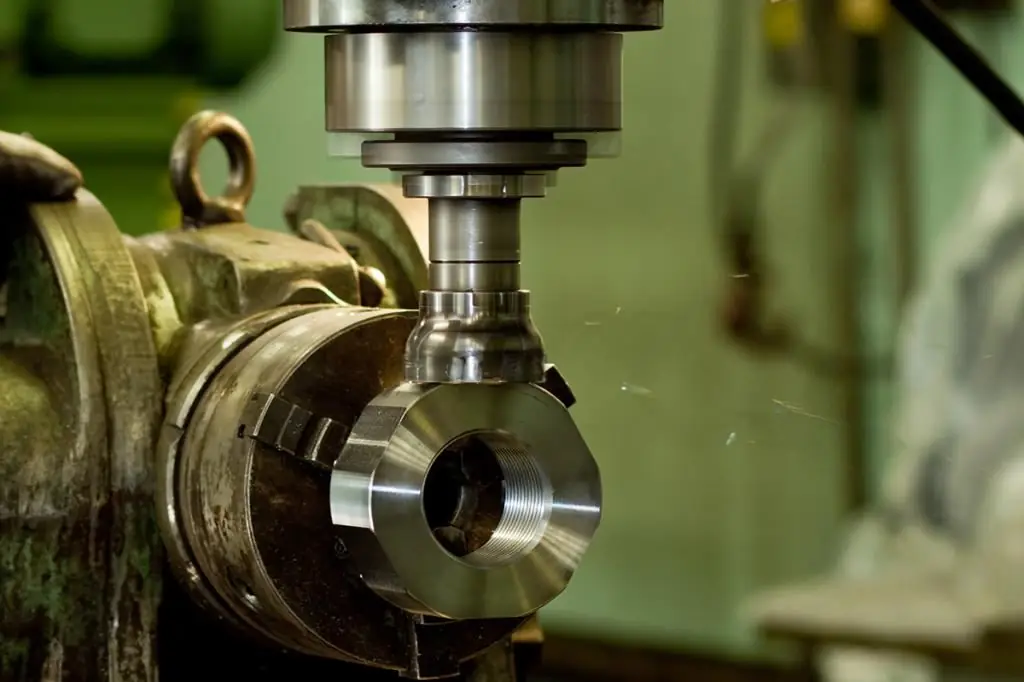
Indices and numbering in the classification of lathes
In the Soviet Union practiced a single system of symbols. According to the standards of the experimental research institute, each group of machine tools was divided into the same number of subgroups.
The table below shows the main parameters.
Name | Turning | Drilling and sharpening | Grinding and Finishing | Gear and thread machines | Cutters | Slitting and planing | |
1 | Single spindle, carousel and multifunction options | Semiautomatic | Multi-spindle | Cut off with drilling capability | Working with provided modes | Standard operations | |
2 | Cylindrical grinding | Light Beams | Automatic machines | Boring by coordinates | _ | _ | |
3 | Light Beams | Conical finish-oriented | Internal grinding | Specialized grinding | Standard program | Standard | |
4 | Automatic | Continuous cutters | Complemented with light beams | Electrochemistry | _ | Standard | |
5 | For cutting worm, round and other wheels | Fortaper machining | _ | For worm gear machining | Machining all the parts provided for in the instruction manual | _ | |
6 | Vertical cantilever and milling models | Vertical milling versions | _ | One for longitudinal version | _ | _ | |
7 | Longitudinal versions with one working line | Continuous machines | Cross planer units |
Longitudinal leveling performance |
_ | _ | |
8 | Longitudinal cut-offs | Two- and single-column | Grinding wheel | Circle trim | Drill vertical and horizontal holes | _ | |
9 | Coupling modifications | Include pipe processing tools in their segment | Centerless organization | All options available | _ | _ | |
10 | Other options | Saws and notches | _ | _ | All characteristic services | _ |
Features
From the indicated classification of machines, it can be understood that the units are combined according to alphanumeric designations. The union includes numbering as such in the following sequence:
- The first digit indicates the group to which the product belongs.
- The second digit is the type of equipment.
- Subsequent numbers define the conditional size in decimeters.
- Models 162 (A, B, K) have up to 1200 rpm.
- Simplified modifications of the 6H82 and 6H12 types are made on the basis of an improved machine of the second dimension. The most modern machine tool unit is identified as model 2620.
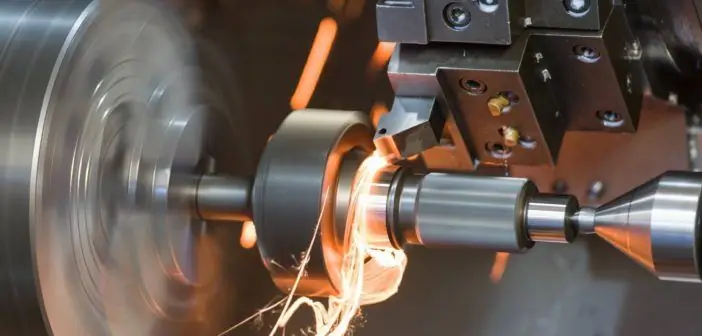
Classification of milling machines
Speed parameters are calculated by the formula:
V=Dn/1000, where D is the diameter and n is the speed of the cutter. One thousand revolutions - the speed of movement of the table relative to the working tip. The feed of the cutter is indicated by the letter S, taking into account the frequency and dependence of processing, in terms of one revolution. Serve dependency:
- Z - number of teeth.
- T - depth of cut.
- T/min - removed thickness in width and thickness in millimeters.
Milling can be carried out in the opposite way to the feed of the cutter, or with the coincidence of the feed of the work item and the rotation of the working platform.
Versatile and accurate
Classificationmachine tools are sometimes defined by their degree of versatility:
- Instances configured for a wide range of different sizes. For the specified group, several categories of operations can be performed.
- Production of parts of the same type (different-sized parts of the skeletons, shafts and other structures of the same configuration, but differing in size).
- Individual elements produced according to a standard template with different overall dimensions.
- Special options for specific manipulations.
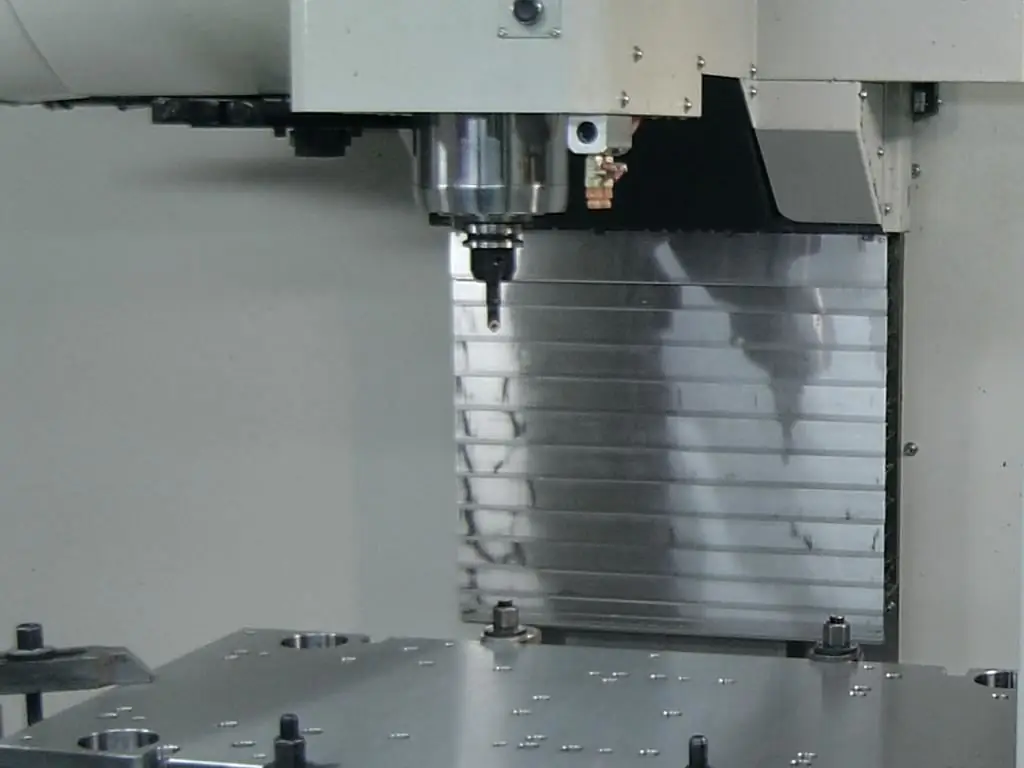
Cutters
In the classification of milling machines, a separate place is given to cantilever-horizontal and universal units. These modifications allow you to process horizontal and vertical surfaces at any angle, and on the "universal" with a turntable, it is possible to mill screw and gear parts with maximum accuracy. Expand the technological operations of these machines with all kinds of nozzles according to the type of unified heads and other devices.
Console modifications differ from vertical-horizontal versions in that they are equipped with a table rotation about its own axis. Multifunctional devices are provided with a special trunk on the skeleton, which aggregates with the spindle head and other structural elements. On such equipment, operations are performed on the processing of cast iron, steel, non-ferrous metals. The console is located on vertical guides that hold the sled with a longitudinalplate and related parts used for horizontal processing of the material.
Automation
According to the degree of accuracy, the classification of machines is displayed as follows:
- "H" is normal.
- "P" - increased accuracy parameter.
- "B" is a precision machine.
- "A" - a unit with especially high accuracy characteristics.
- "C" - professional super precision machines.
For example, marking 16-K-20P indicates that the classification of machines for metal of this type indicates its increased accuracy.
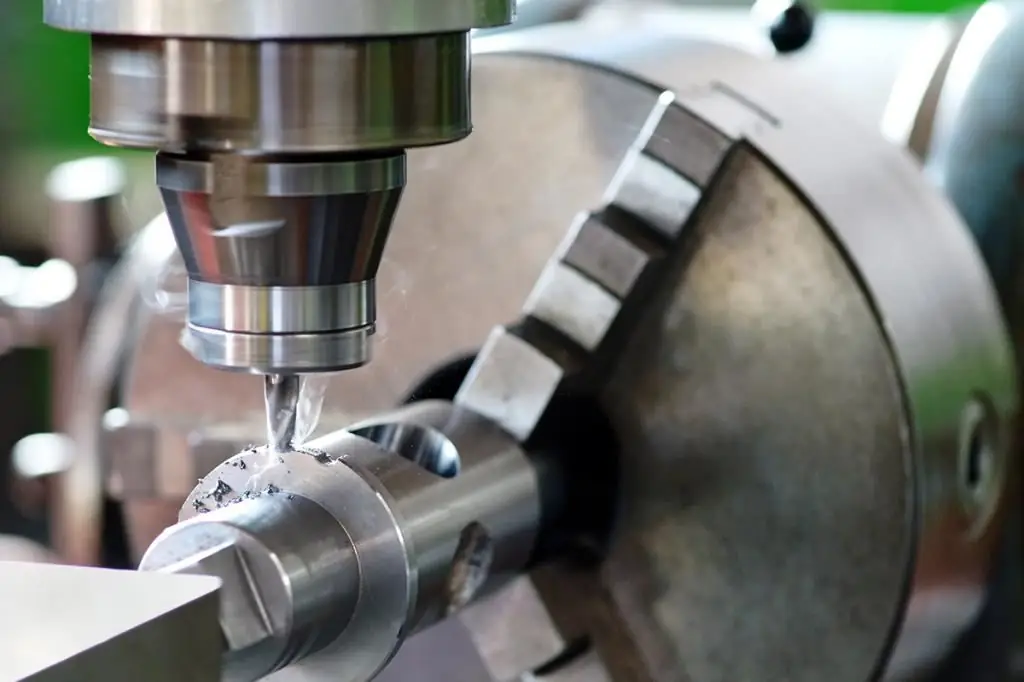
Automation
The devices under consideration are divided into autonomous and semi-automatic samples. In the last units, the fastening of the workpieces and their subsequent removal is performed by the operator. The classification of CNC machines implies their operation autonomously, with the delivery and dismantling of parts by flexible production modules.
The numerical designation of the units is given below:
- Ф-1 - digital indication with preliminary selection of coordinates.
- F-2 - system with positional control configuration.
- F-3 - contour group.
- F-4 is a versatile design in terms of control.
Numbering and weight
Classification of drilling machines includes their division by weight. The equipment in question is distinguished by this factor in this way:
- Weight up to one ton - light aggregates.
- Up to 10 tons - average.
- Heavy - up to 16 tons.
- Large - up to 30 t.
- Especially heavy - up to 100 t.
Classification of grinding machines and their analogues is determined by an alphanumeric code. This index indicates the belonging of the tool to a certain group, as well as the limiting dimensions of the workpieces being machined and the drilling diameters. Equipment of the same size, but with different parameters, is characterized by a letter placed between the first and second digits. For example, models 162 and 1K62 differ in speed. The first version has 600 rotations per minute, the second - 2000. In addition, you can distinguish the machines by the last letter at the end of the defining index. The basic modification of a horizontal milling machine is 6H82, a simplified version is 6H82G.
In some standard sizes, the numbering indicates the purpose of the devices and the classification by the fourth digit. For example, the 262 horizontal boring machine has an improved version of the 2620. This identification makes it easy to identify the necessary equipment in special catalogs, as well as to select the appropriate spare parts.
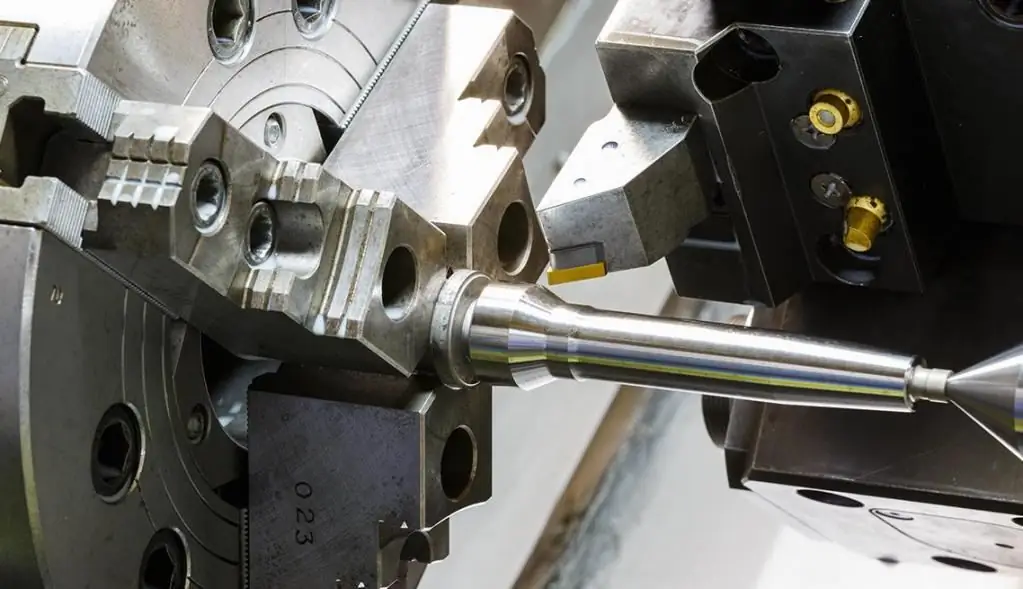
Main categories
The turret turning unit has a horizontal swivel head. On the skeleton there is a headstock with a high-speed box, as well as a spindle with a revolving cam. The movement is transmitted by the drive shaft and the bar feed mechanism.
Single column vertical lathe functions by placing the workpiece to be machined on the faceplate. The traverse is on verticalguide elements. The movement from the gearbox is transformed by moving the turret-shaped caliper.
The classification of double column lathes has more calipers. In this case, the second supporting element can be installed on the second rack, the gearbox is mounted in the lower part of the housing.
Multi-cutting equipment is equipped with a bed with a headstock, a gearbox and a spindle. The design includes several calipers, two front blocks and one rear counterpart. The longitudinal movement of the part is provided by interchangeable wheels and a guitar that determines the magnitude of the working feeds. Guiding elements are mounted on the tailstock.
Turn and occipital versions practically do not differ from screw-cutting models. The headstock with the spindle is located on the frame. An occipital support with a cutting holder and an apron is mounted on guides and adjusting parts. In addition, the design includes a tailstock, lead screw and shaft.
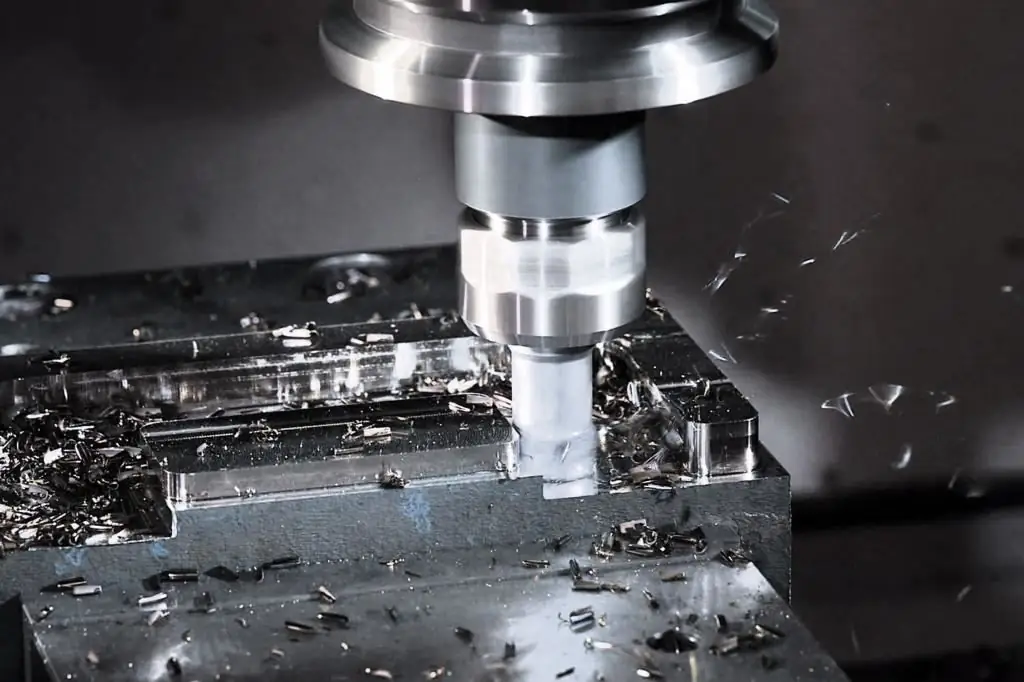
Frontal units differ from metal-working "brothers" in that they do not have a tailstock. In the front there is a speed box with a spindle and a fixed faceplate. The bed is located transversely on a separate plate with a tool holder and a caliper.
Recommended:
Machines for fertilization. Classification of machines, methods of fertilization
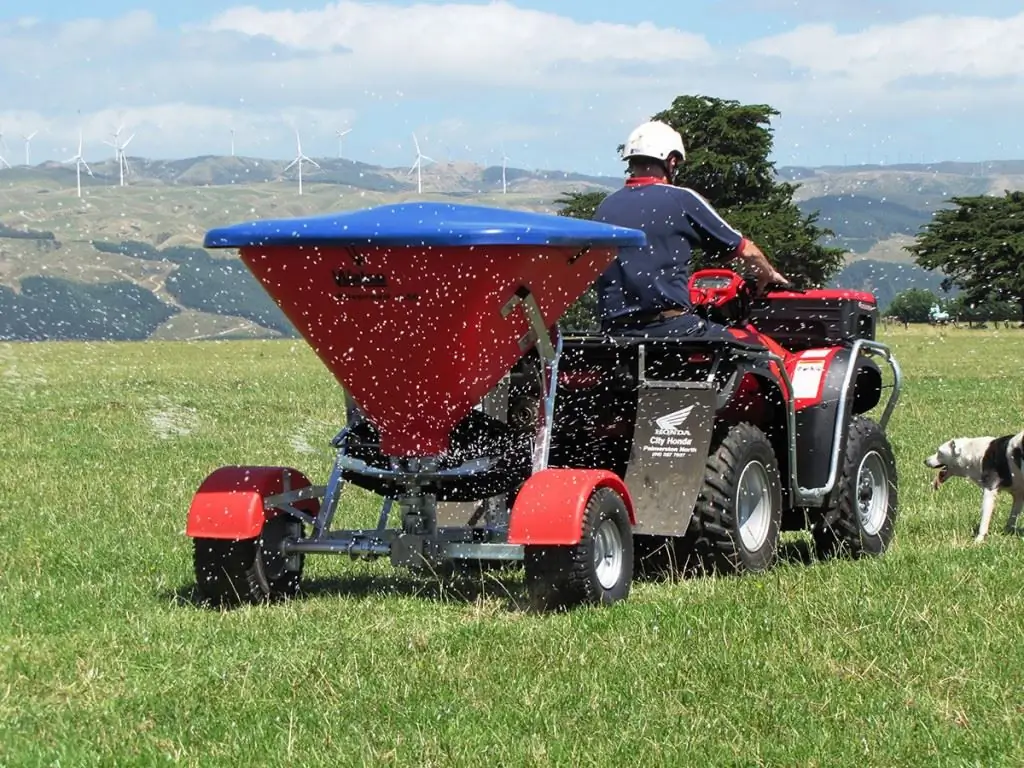
Fertiliser machines are designed to replace human manual labor in this operation. In relation to mineral fertilizers, spreaders and seeders with fertilizer seeders are used. Aggregates are also used for making those in liquid form
Main types and types of business plans, their classification, structure and application in practice
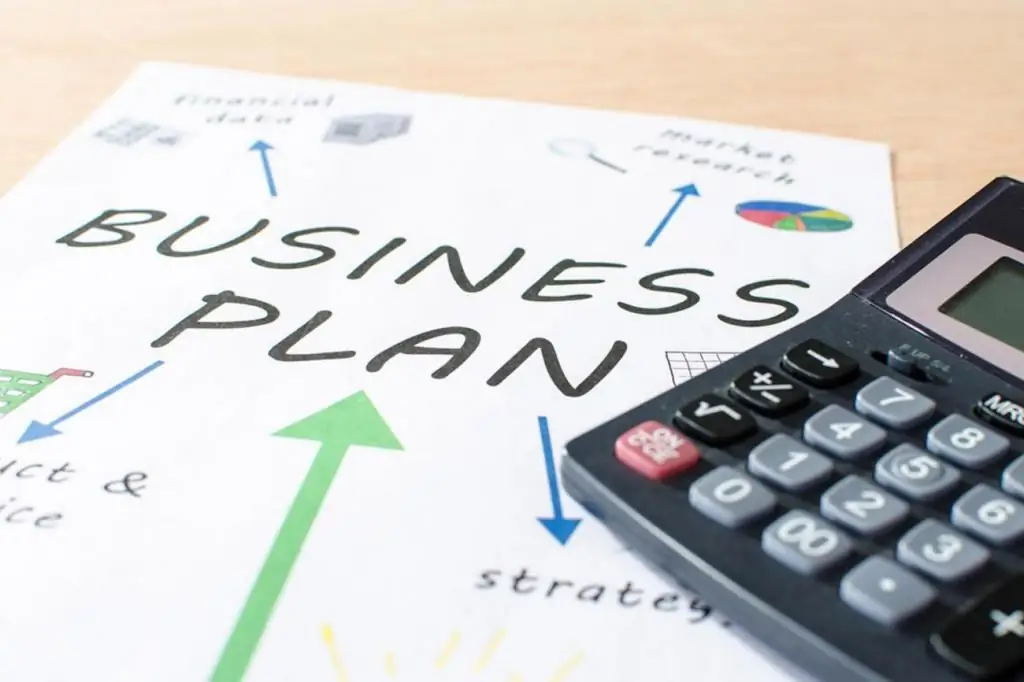
Each business plan is unique, because it is developed for certain specific conditions. But you need to familiarize yourself with the features of various types of business plans in order to understand their key features. Experts recommend doing this before compiling your own similar document
Industrial flotation machines for wastewater treatment: types, device, principle of operation
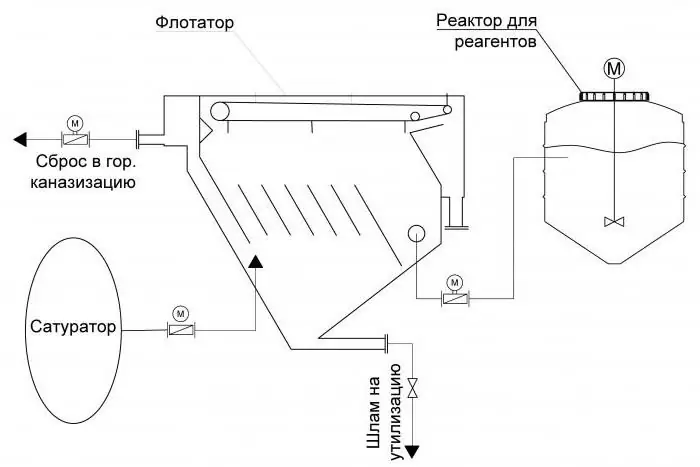
2017 has been declared the year of environmental protection in Russia, and therefore environmental education is one of the tasks for this year. Wastewater generated during the economic activities of enterprises contains a large amount of pollutants in concentrations exceeding the permissible and normative ones. As a rule, we are talking about heavy metals (iron, nickel, copper, lead, mercury, cadmium, etc.), oil products, suspended solids, aluminum, and surfactants. These substances, getting into water bodies, violate the norms
Milking machines for cows: types, device, characteristics
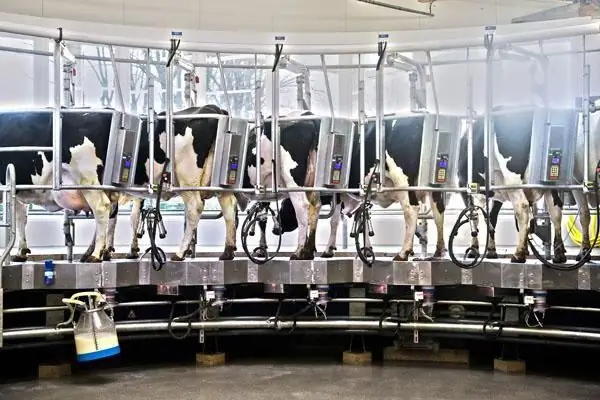
Milking machines pay off quickly enough and soon turn into a plus, unlike workers who will always need to be paid
AC machines: device, principle of operation, application
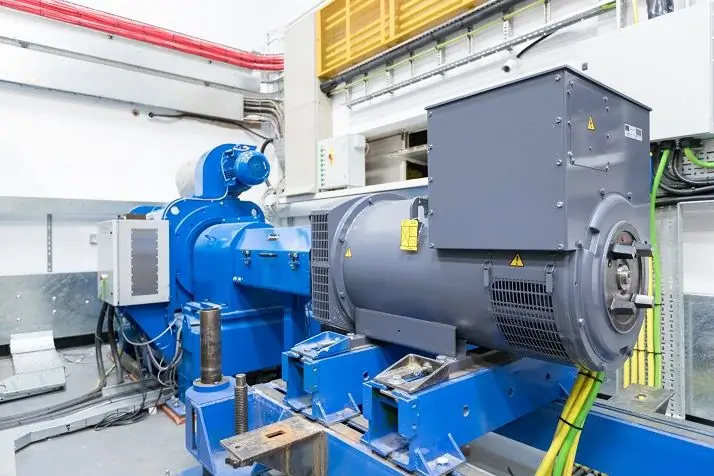
Electric machines perform the critical function of energy conversion in working mechanisms and generating stations. Such devices find their place in different areas, supplying the executive bodies with sufficient power potential. One of the most demanded systems of this type are AC machines (MCT), which have several varieties and differences within their class