2025 Author: Howard Calhoun | [email protected]. Last modified: 2025-01-24 13:10
Useful properties of oil have been known to mankind since time immemorial. It is used to obtain fuel and raw materials for the production of synthetic fibers and plastics. At the same time, humanity has always sought to maximize the benefits received from the processing of fossil fuels. One of these methods was catalytic reforming, a process that gave rise to high-quality gasolines and aromatic hydrocarbons.
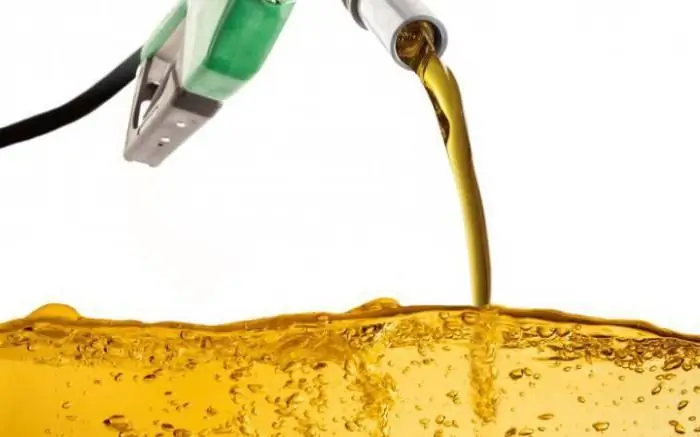
This method of oil refining was invented back in 1911, and since 1939 the technology has been used on an industrial scale. Since then, the method of distillation of fossil fuels has been constantly improved. Today it represents one of the most complex and efficient ways to produce high octane gasoline.
Fuel distillation
Catalytic reforming is a process of dehydrogenation (removal of a hydrogen molecule from organic compounds) of six-membered naphthenes in the presence of nickel and someother platinum group metals at high temperature, which leads to the formation of aromatic compounds. In other words, this is a process that makes it possible to obtain a high-octane product - reformate - from low-quality raw materials - straight-run gasoline.
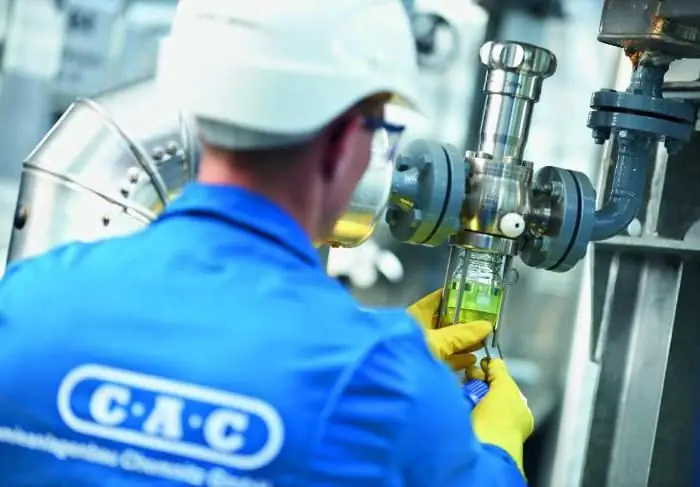
The main reason why reforming has become so widespread is concern for the environment. Prior to this, lead-based anti-knock agents were used to produce high-octane gasoline. Almost no emissions from reforming.
Products Received
Using this technology, it is possible to extract the most valuable petrochemical raw materials - benzene, toluene, aromatic hydrocarbons. Today, catalytic reforming is a process that produces up to 480 million tons of petrochemicals per year worldwide.
The main end product of the production cycle is reformat - gasoline with an octane rating of 93-102.
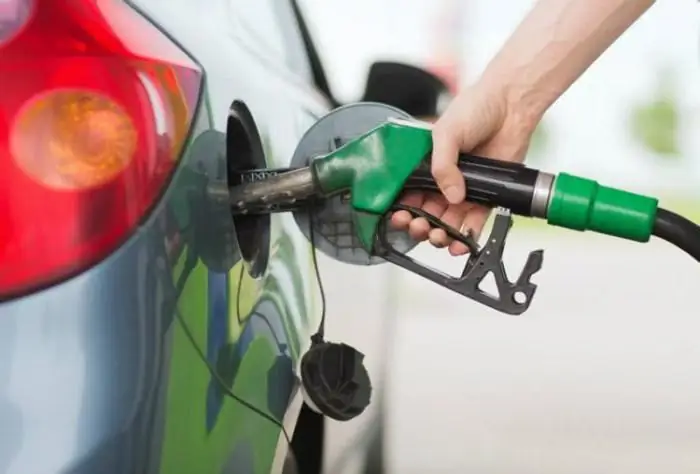
At the same time, paraffinic by-products are created, as well as 90% hydrogen gas, which is the purest than obtained by other methods.
Another product accompanying catalytic reforming is coke. It is deposited on the surface of the catalysts, significantly reduces their activity. They are trying to reduce its number.
Catalytic reforming technology
Straight-run gasoline, a fuel with a low octane number, acts as a feedstock for catalytic reforming. The whole process is carried out in 3-4 reactors, which have a fixed catalyst bed. The reactors are interconnected by pipes with a complex multi-chamber system and heating of the transition product.
Catalysts for catalytic reforming are a carrier - aluminum oxide (A1203) interspersed with platinum crystals. In reactors at a temperature of 480-520 °C and a pressure of 1.2 to 4 MPa, the raw material is converted into high-octane isoparaffin and aromatic compounds.
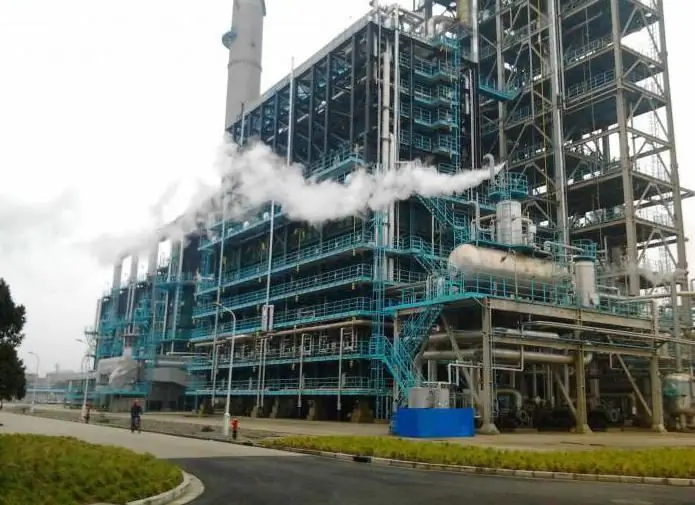
Very often, to increase the process stability, more expensive metals (rhenium, germanium, iridium), as well as halogens - chlorine and fluorine, are introduced into the technology.
Types of catalytic reforming
To date, many methods have been invented to produce high-octane gasoline and aromatic hydrocarbons through catalytic reforming reactions. Each foreign company keeps its own production method secret. However, they are all based on three main methods:
- Oil reforming carried out simultaneously in three or four reactors continuously. Its essence lies in the fact that the catalyst of the process first fully develops its potential, after which the reactors are stopped until the accelerator restores its properties.
- Continuous reaction in 2-3 installations - the reagent is periodically restored in each system as it is produced. At the same time, the process does not stop, and the regenerative reactor is replaced by a "floating", additional one.
Greatestproductivity can be achieved with a continuous reaction with the use of regenerating units and reactors. The catalyst, as its properties deteriorate, is placed in a regenerating chamber, and a “recently reduced reagent” comes in its place, the circulation of aluminum-platinum compounds takes place.
Main problem
The main problem that accompanies reforming is the formation of a large amount of coke, which reduces the catalytic ability of alumina-platinum materials. The solution to this problem is to burn out coke deposits on the surface of the reacting elements using an oxygen-inert mixture at a temperature of 300-500 degrees Celsius. This process in the scientific community is called regeneration.
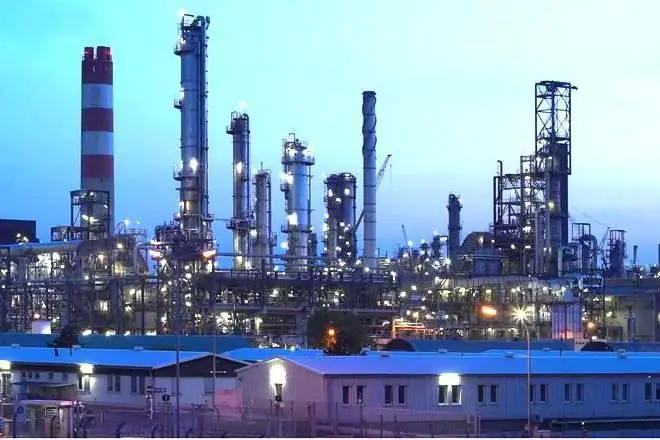
It is impossible to completely restore the catalytic element. As it is used, it ages irretrievably, after which it is sent to special factories, where platinum and other expensive metals are extracted from it.
Catalytic Reformers
This method of processing natural fuels is carried out by various types of installations. To name a few of them:
- Selectoforming. Here, the reformer combines a catalytic dehydrogenation process with selective hydrocracking.
- Platforming. It has 3 reactors, and the operating time of the catalysts is from 6 to 12 months.
- Ultraforming. One of the first installations with a "floating" reactor, which carries out the process of reducing the reagent.
- Isoplus. Forto obtain the product, the processes of reforming and thermal cracking are combined.
The most widespread oil reforming has received in North America - here annually processes up to 180 million tons of natural fuel. In second place are the countries of Europe - they account for about 93 million tons. Russia closes the top three with an annual production of about 50 million tons of oil.
Recommended:
Voronezh brewery: a large enterprise with a century of history
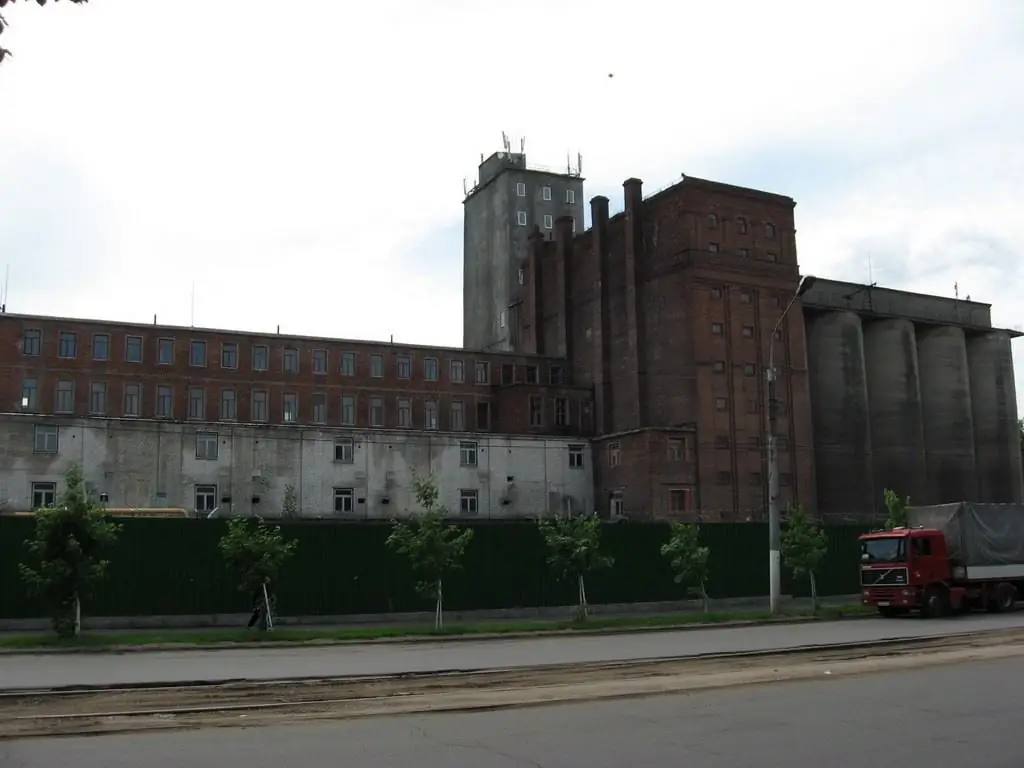
Voronezh brewery has been on the map of the capital of the Black Earth region for many years. This enterprise was able to survive the Soviet rise in industry and even the hard times of perestroika. Today it is part of the mighty beer industry and supplies its products to all corners of Russia
Resource-saving technology. Industrial technologies. The latest technology
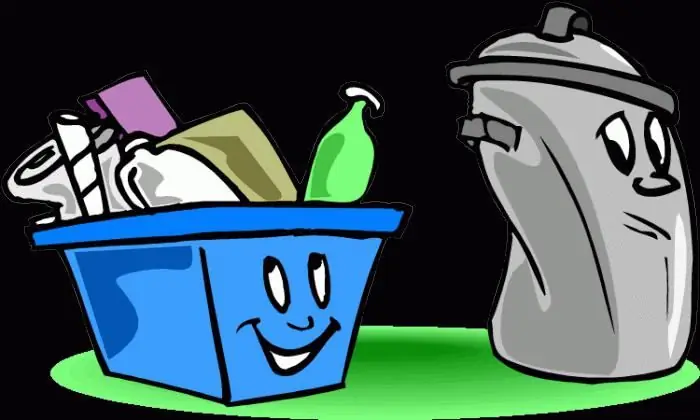
Modern industry is developing very dynamically. In contrast to past years, this development is proceeding intensively, with the involvement of the latest scientific developments. Resource-saving technology is of great importance. This term refers to a whole system of measures aimed at a significant reduction in resource consumption, while maintaining a high level of product quality. Ideally, they try to achieve the lowest possible level of consumption of raw materials
The newest professions of the 21st century. The most in-demand professions in the 21st century
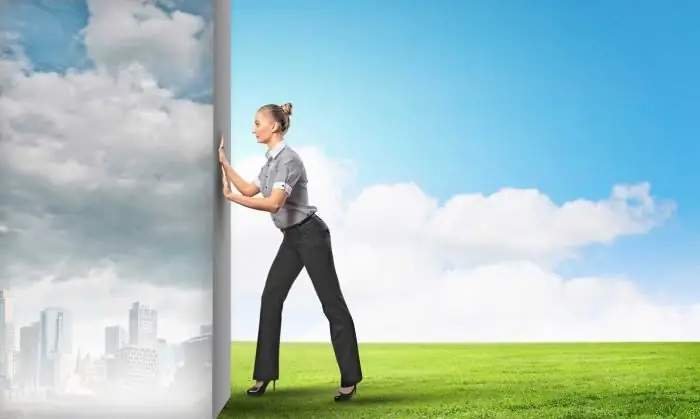
What are the most popular professions of the 21st century today? What will be relevant in ten or twenty years? Where to go to study, so as not to be without a job after graduation? Find answers to all these questions in this article
History of porcelain: a brief history of development, types and description, technology
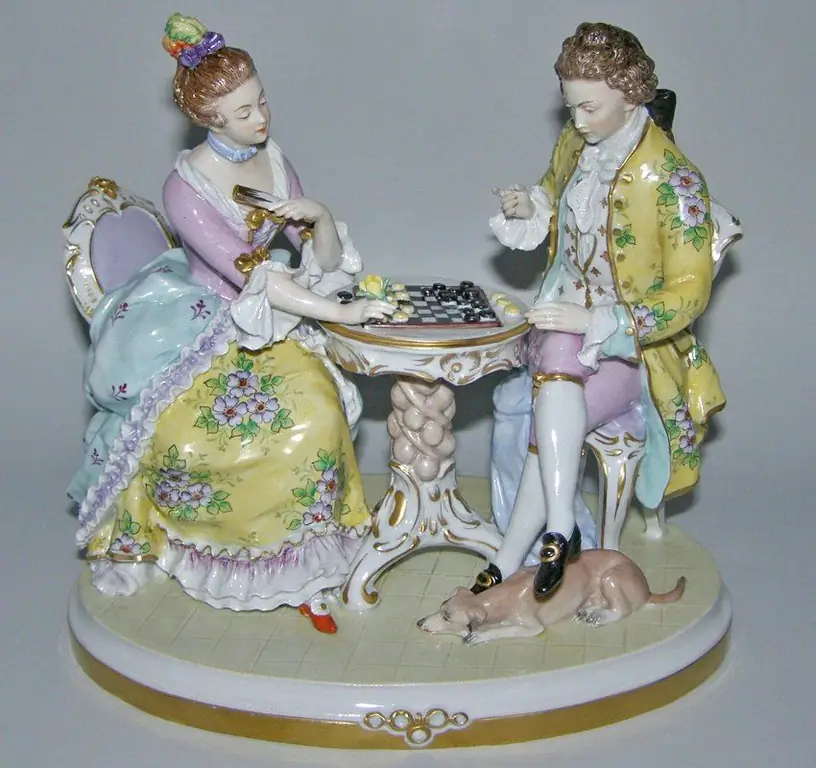
Ceramic products are the oldest kind of craft from all the skills mastered by man. Even primitive people made primitive utensils for personal use, hunting decoys and even earthenware utensils like hut ovens for cooking. The article tells about the history of porcelain, its types and method of obtaining, as well as the distribution of this material and its path in the artistic work of various peoples
Progressive tax is Progressive tax scale
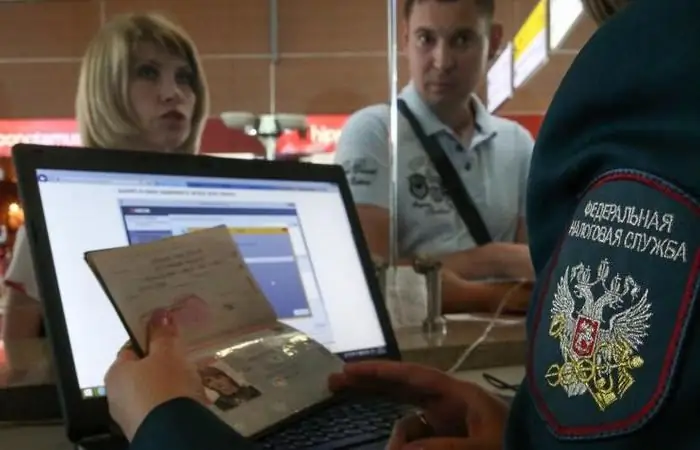
The first attempt to introduce progressive taxation was made in Russia in 1810. This was due to the exhaustion of the economy by the war with Napoleon. As a result, the exchange rate of the paper ruble fell sharply. The progressive tax system assumed an initial rate of 500 rubles, which gradually increased to 10% of net profit