2025 Author: Howard Calhoun | [email protected]. Last modified: 2025-01-24 13:10
Thermal imaging control of electrical equipment is an effective way to identify defects in power equipment that are detected without shutting down the electrical installation. Special products, which are called thermal imagers, measure the temperature of the connections, which makes it possible to determine the degree of heating of the metal surface. In places of poor contact or violation of integrity for a number of other reasons, it will be higher than usual. Identification of such problems allows you to eliminate the defective area in time, which will save the equipment from more detrimental damage and emergency shutdowns.
Why spend?
Carrying out thermal imaging control of electrical equipment allows you to:
- Carry out operational monitoring of the state of power equipment, identify bottlenecks at various stages of defect development.
- Perform independent oversight that ensures compliance with maintenance measures and responsibilitieselectrical installations in good condition. Relevant for external audit of consumer equipment.
- Ensure fire safety of electrical installations. During emergencies, there is a risk of damage to other equipment due to fire. Acceptable for power transformers where oil release is possible.
The main purpose is to prevent accidents in the early stages of a defect.
Types of control
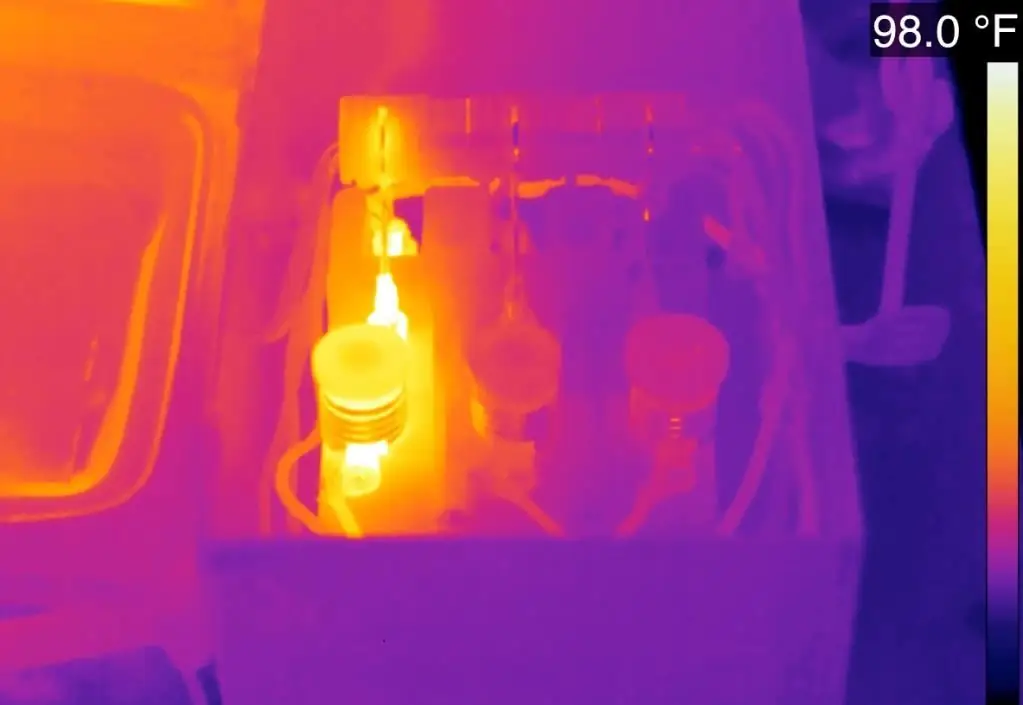
In modern practice, the following types of thermal imaging control of electrical equipment are used:
- Periodic. It is set by regulatory documents and involves inspection of power equipment within the established time frame.
- Current. It is aimed at identifying defects and malfunctions of the power plant before and after the overhaul (current) repair.
- Emergency. Provides monitoring of the status of other equipment after the emergency has been eliminated.
This is the main gradation that predetermines the time and place of specialized measurements.
Due dates
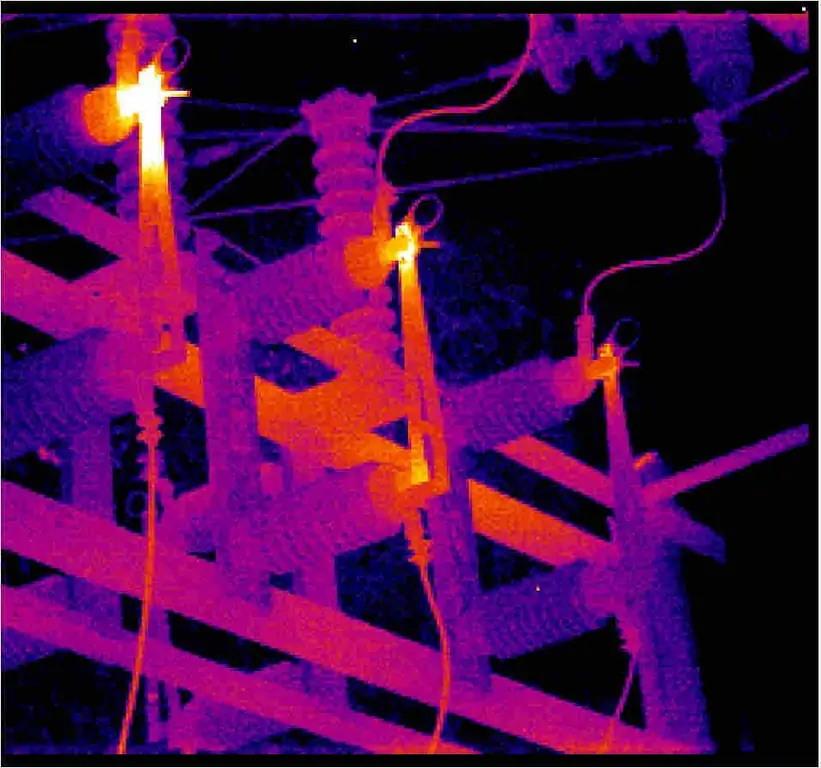
The frequency of checking the thermal imaging control of electrical equipment is determined by regulatory documentation, including PTE, methods for measuring and calculating, RD 34.45-51.300-97 (for Russia). The documentation provided provides the following recommendations for conducting a survey of electrical installations:
- up to 35 kV - at least 1every 3 years;
- 110-220 kV - at least 1 time in 2 years;
- above 220 kV - annually.
There are exceptions that can be set by the chief engineer of the power company not below the norm, as well as in the following cases:
- Before and after overhaul or maintenance of an electrical installation.
- For newly commissioned overhead lines after a year of operation.
- For electrical installations, the service life of which has exceeded 25 years and with the development of contact connections of at least 5%. Such a procedure should be carried out at least once every 3 years.
- When operating power equipment with maximum current loads, where overload is possible, as well as in places with adverse physical or natural conditions (ice, wind, fog) at least 1 time per year.
The method of thermal imaging control of electrical equipment is the main document to be guided by. Some equipment manufacturers recommend shortening the survey interval. A number of experts note that to maintain the network in working condition, constant monitoring is required due to wear and tear. This practice cannot be implemented due to the amount of work.
Advantages and disadvantages
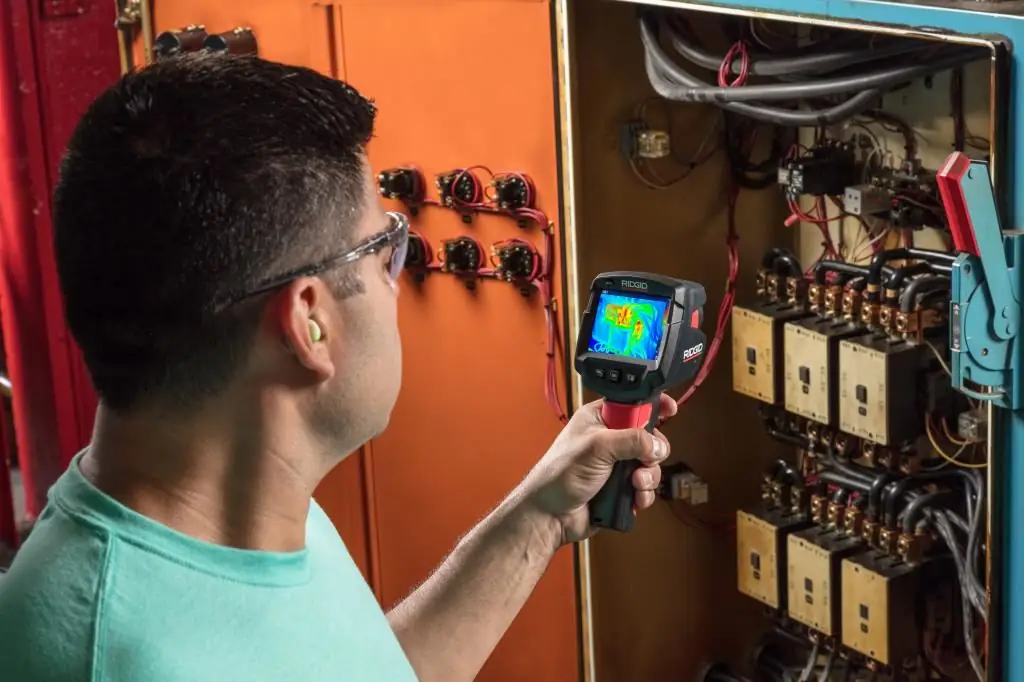
Thermal imaging control of electrical equipment is accompanied by the following advantages:
- Portability that allows inspection of any electrical installation.
- Increased measurement accuracy compared to a pyrometer or similardevices.
- Most models allow you to fix the result, which is the basis for further decision-making by the management of the organization.
- Detection of defective connections at an early stage of their occurrence, which prevents the development of accidents.
As for the shortcomings, they are minor and are expressed in ease of use and accuracy of measurements. Devices of individual manufacturers have large dimensions, where stands are not provided. Some models have low latch response.
The thermal imager device
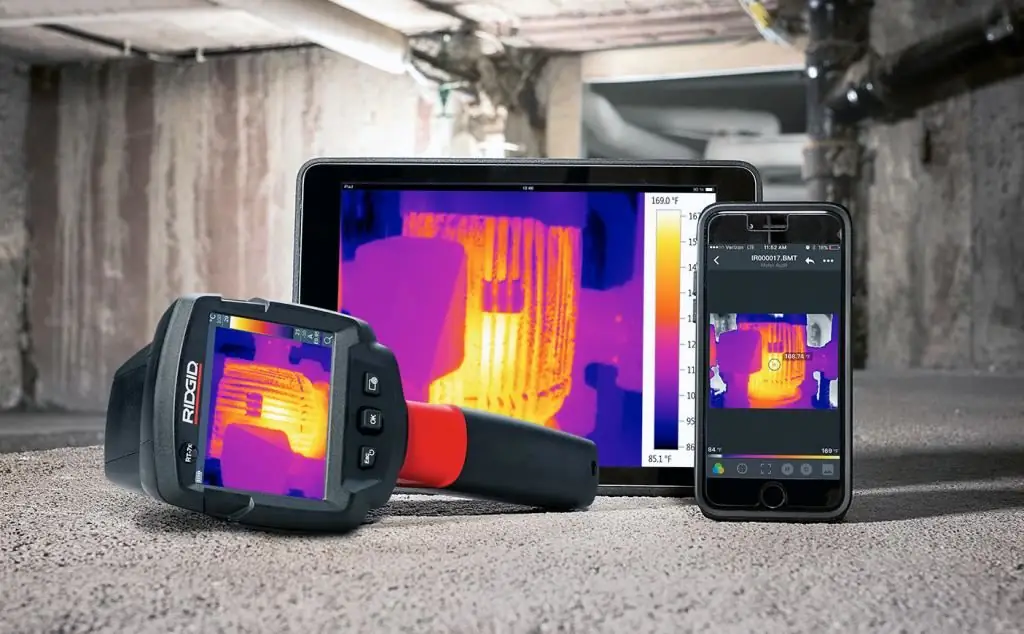
In fact, thermal imagers are ordinary digital cameras that use special optics that can compare the temperature range. Due to the large coverage area, the quality of the results obtained does not depend on the distance to the object, which ensures that the procedure is carried out in the operating state of the power plant.
The main and most important element of any thermal imager is the focal array (FPA). The latter has a high sensitivity, which ensures the accuracy of determining the level of heat generated. To work with a personal computer, cameras of this type received USB connectors. This ensures that the results of the examination are preserved, which confirms or refutes the need for maintenance.
Equipment cost
Thermal inspection of electrical equipment is expensive, as installations of this type cost on average from $300 for domestic use and about $3,000 for professional use. Consideringseveral crews for the maintenance of high-voltage and distribution lines, as well as other electrical installations, accumulate a significant amount. Nevertheless, such an acquisition pays off in full due to the reduction of network breakdowns and energy undersupply.
The price tag is largely determined by the additional functionality, as well as the complexity of the matrix. Some items cost up to $25,000. Such equipment allows shooting from a distance of up to 500 meters, which is great for surveying large overhead lines.
Checking and verifying the device
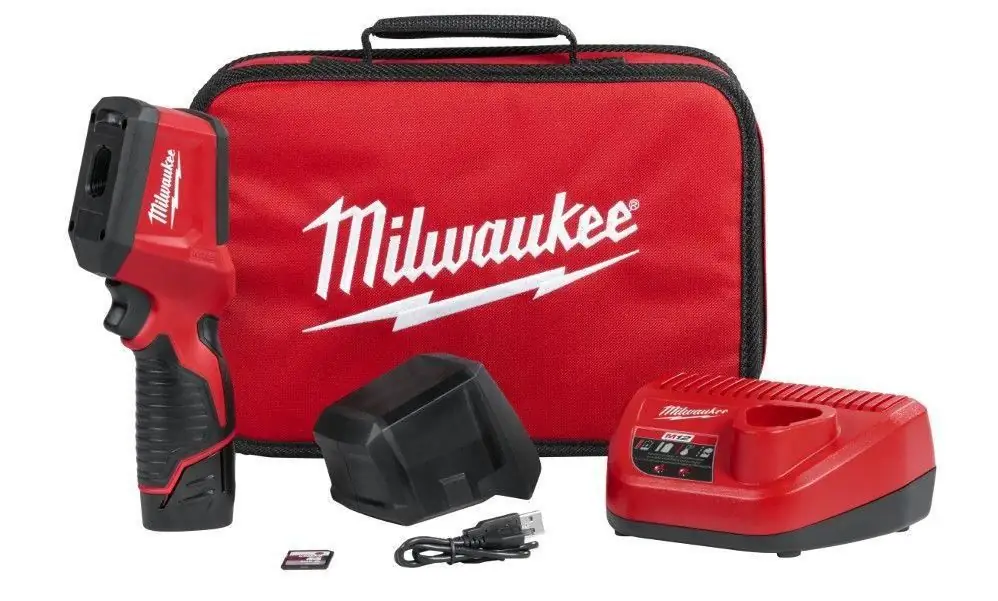
Checking the performance of the device is carried out immediately before the examination of the connections. The norms of thermal imaging control of electrical equipment require the implementation of such actions before each temperature measurement. However, in practice, such a process is not carried out.
As for the verification of the product - like any measuring device, it must take place within the time specified by the manufacturer. The device must have a CSM label, which confirms the accuracy of the measurement. Please note that the use of Chinese-made pyrometers often give an error and do not pass the test in metrology.
Applicability in practice
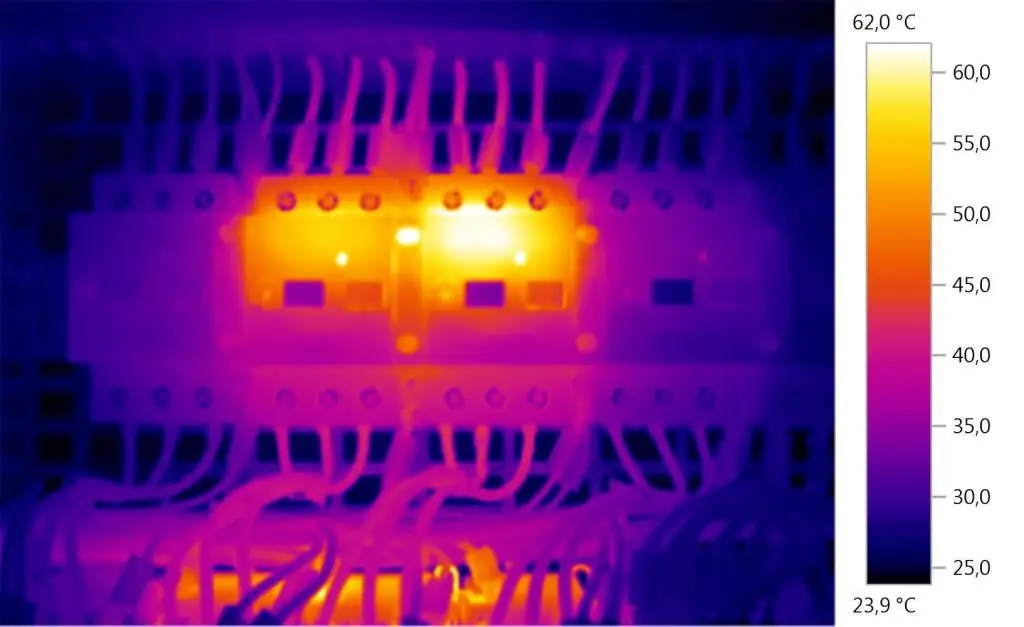
The use of thermal imaging control of electrical equipment has proven itself on the positive side. This is due to the efficiency of detection of defects, safety and ease of implementation of the settasks. Proper measurement involves:
- Checking the performance of the device by taking temperature measurements on the skin. There are other methods of verification operations.
- Installation of equipment on a special stand, which ensures maximum measurement accuracy. In practice, the presented stage is carried out by hand, which shows slight differences in the results.
- Direct the matrix directly to the contact connections of the electrical installation. With a weak lens, there are difficulties in fixing. It should be noted that some models do not reflect the temperature background when pointing the device at the paint.
- Fix the result, and then transfer the information to a PC or laptop. The implementation of the presented operation is performed by standard methods via a USB connector.
- Review the results in detail, write out a protocol, which is the final stage of thermal imaging control of electrical equipment.
Based on the documentation and control data, a decision is made on the criticality and the need to eliminate the defect.
Protocols
The protocol for thermal imaging control of electrical equipment is a local or state standard document that reflects the main and important points of the study of electrical installations. Here a conclusion is given regarding the examination, defects are recorded. If necessary, photographs are attached, confirming the need for repair work. The standard form is presented in the application of the administrativedocumentation 34.45-51.300-97.
Safety
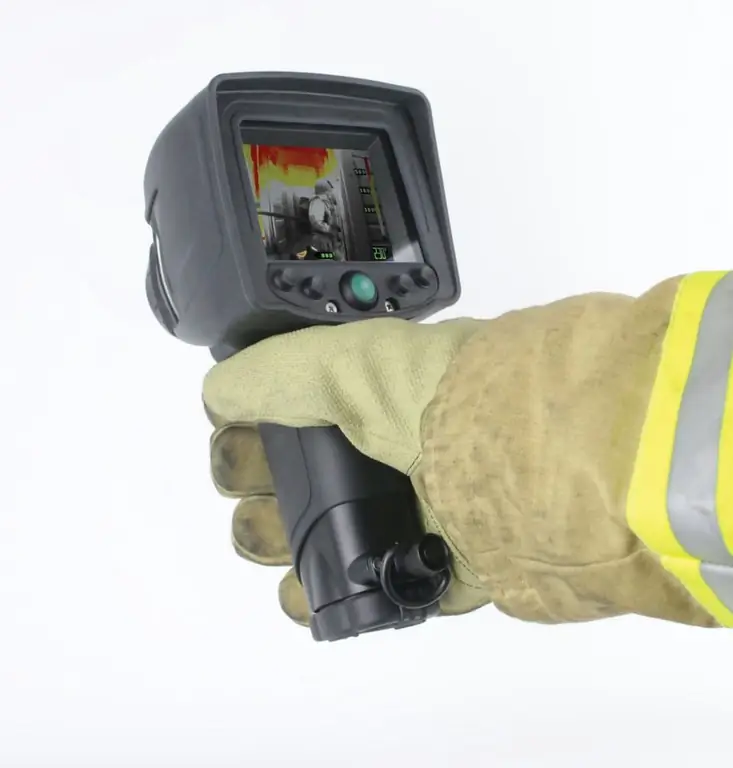
The RD "Thermal imaging control of electrical equipment" clearly spells out the safety measures that must be observed during the inspection. This includes:
- Workers who have been instructed, trained in safe work with the device, and also have fire safety skills are allowed to work independently with a thermal imager. During the examination, the use of overalls is required.
- During a periodic or unscheduled inspection, it is forbidden to eliminate the identified defects. This type of work can be done by order.
- It is forbidden to approach live parts closer than the permissible norms. It must be remembered and understood that the installation is energized, which is an increased source of danger.
These are the main positions that predetermine the safe conduct of work. Approximate conditions and requirements apply to periodic inspections of electrical installations.
Conclusion
The thermal imager is a special device that has found wide application in the electric power industry. A product of this type is very expensive, but due to its purpose and efficiency in performing its tasks, it is an integral part of accident prevention. The frequency of thermal imaging control of electrical equipment, as well as the methodology for performing the survey, is prescribed in the regulatory documentation: in the operating rules, in RD 34.45-51.300-97.
The control of the state of connections is recorded in the protocol, on the basis of which the equipment should be taken out for repair. The need to eliminate such defects is determined by the chief engineer of the power plant. The technology is life-saving for high-voltage networks, which reduces the accident rate by at least 70%. In most cases, the elimination of defects does not require extinguishing the overhead line.
Contact testing must be carried out exactly with safety precautions. Note that thermal imagers have a much greater application. The device is used in construction, hunting, medicine and many other fields of activity.
Recommended:
Conversion of thermal energy into electrical energy with high efficiency: methods and equipment
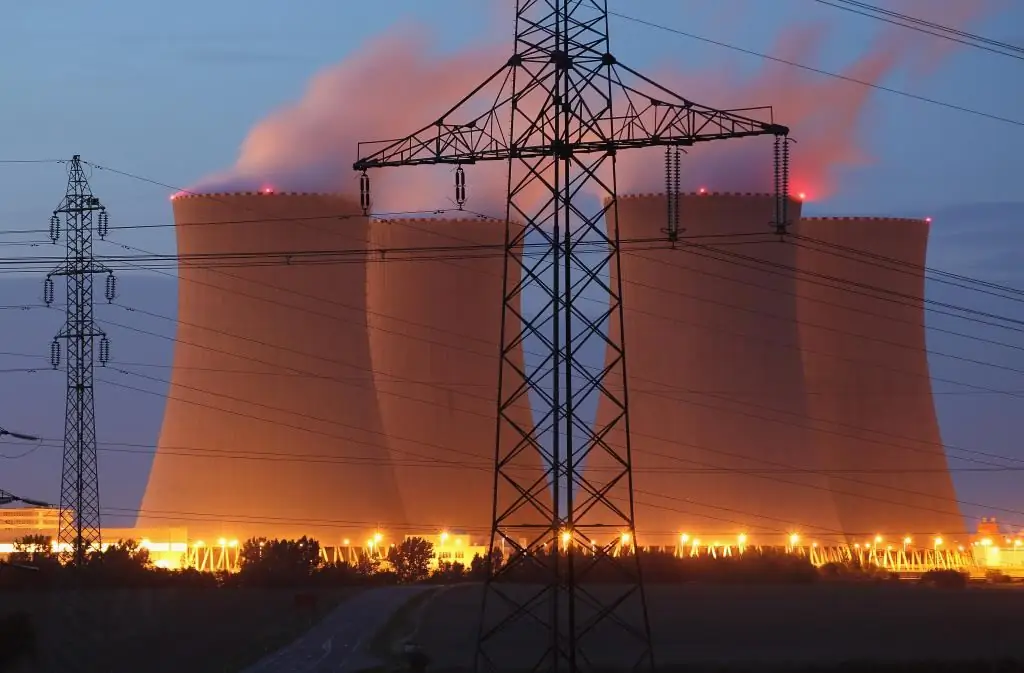
There is growing concern around the world about the catastrophic decline in the levels of natural energy resources needed for modern life, such as oil, natural gas and coal. Nevertheless, this fact contributes to the development of new technologies based on the use of alternative natural resources: solar energy, hydropower, wind energy, bioenergy, geothermal energy. This is popular in the article
Access control to the premises: concept, features, varieties and principle of operation
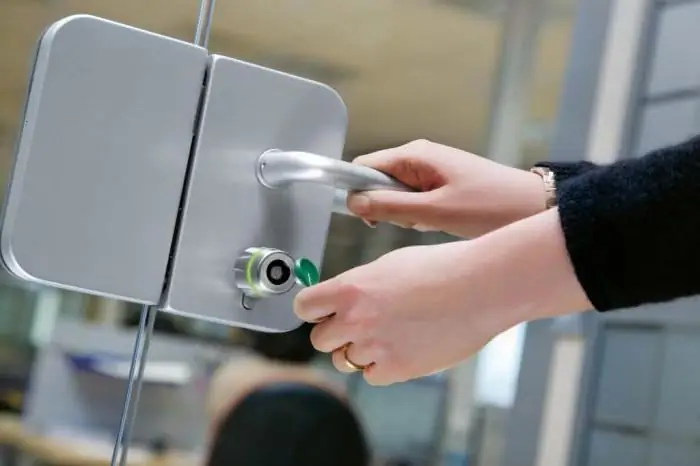
With the help of access control to the premises, you can not only maintain the protection of the object, but also facilitate the work of regulatory authorities. With low installation costs, it helps to save on security
Thermal conductivity of sandwich panels: concept, main characteristics, dimensions, thickness, thermal conductivity coefficient, installation rules, pros and cons of operation
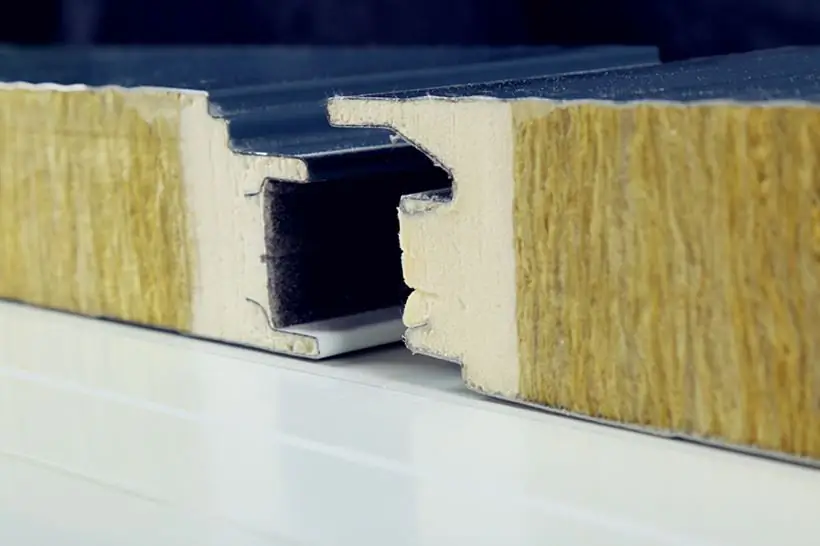
Thermal conductivity of sandwich panels will be the lowest if polyurethane foam is the basis. The parameter under consideration here varies from 0.019 to 0.25. The material is strong, dense and light. It is chemically resistant and does not absorb moisture. Rodents are indifferent to polyurethane foam, fungi and mold do not develop inside it. Working temperature reaches +160 ˚С
Low pressure heaters: definition, principle of operation, technical characteristics, classification, design, operation features, application in industry
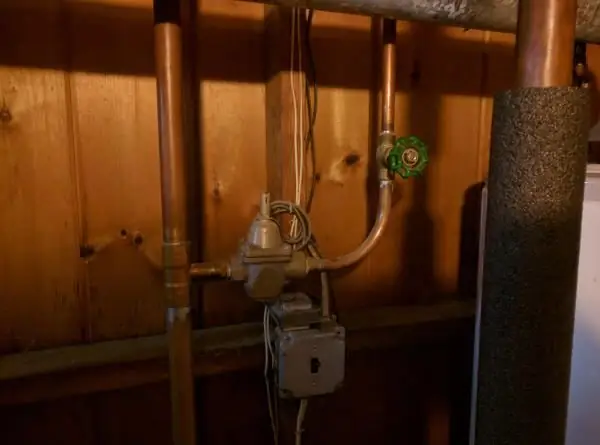
Low pressure heaters (LPH) are currently used quite actively. There are two main types that are produced by different assembly plants. Naturally, they also differ in their performance characteristics
Alternative energy in Russia: concept, classification and types, stages of development, necessary equipment and application
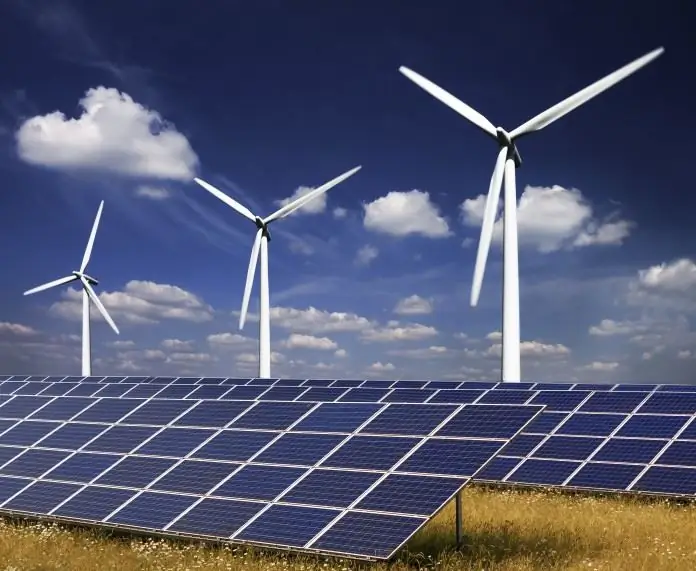
Alternative energy in Russia is currently quite poorly developed. This is supported by the fact that less than 1% of all energy produced comes from such sources. On a national scale, this is extremely small