2025 Author: Howard Calhoun | [email protected]. Last modified: 2025-01-24 13:10
Processes of exploitation of oil wells in the fields are often accompanied by flooding of the treated formations, against which stable water-oil emulsions are formed. The result is the formation of precipitates, which increase the viscosity of the mixture and increase its pour point. In this state, the resources must undergo primary processing, one of which is the stabilization of oil and related emulsions.
Characteristic of the processed material
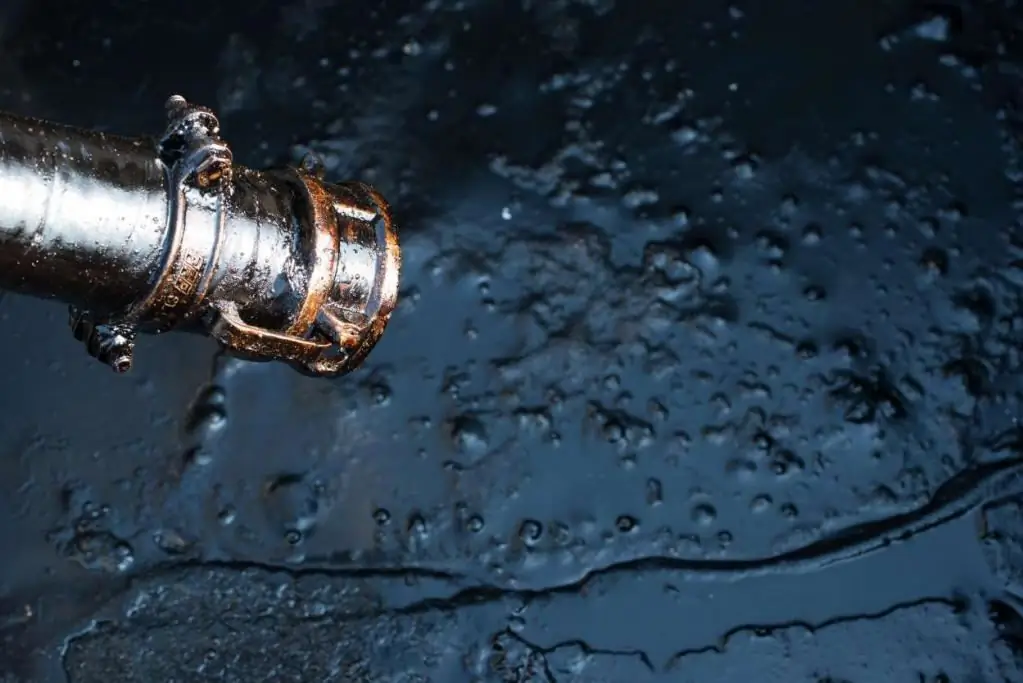
As well as preparatory processes for des alting and dewatering, stabilization is applied to oily materials contaminated with foreign liquid phases and particles. As already noted, mainly we are talking about water-emulsion mixtures containing surface-active components. The presence of emulsifiers, in turn, makes the emulsion more stable and immune to external factors.impact, which prevents the oil fraction from exfoliating at the molecular level in a natural way. Also, the composition may include mechanical impurities, elements of heavy metals, resins and paraffins. Under natural conditions, oil stabilization is a dynamic process determined by the characteristics of competing adsorption of emulsifying components on water droplets. Determining the composition of the interfacial layers of a particular emulsion allows you to find out the properties of its stabilizer and choose the most effective method of exposure at the industrial level in an artificial environment.
What is stabilization for?
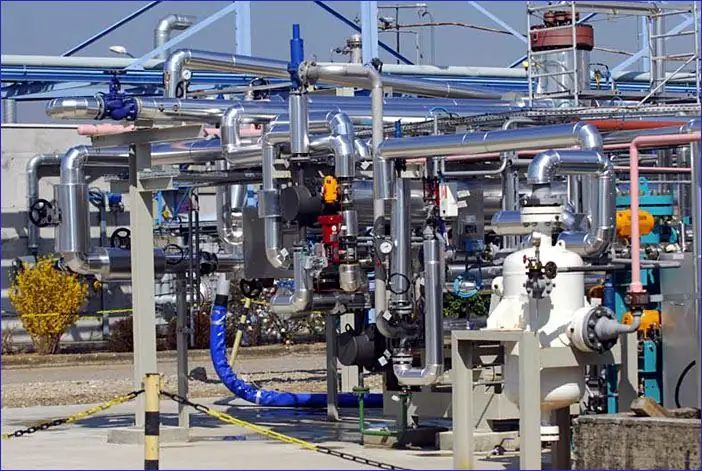
Physical-chemical stabilization processes in the oil and gas industry can have several tasks. To begin with, it is worth noting the shortcomings of oil production technologies, which are expressed in the loss of light fractions of a useful substance. On the other hand, a number of sludge and harmful volatile gases are recovered and transported along with the oil phase directly to the purification steps. In turn, the technology of oil stabilization, depending on the activity of emulsifiers and other active components in the composition of the emulsion, can perform both preservation functions and act as a separation agent. In the first case, the emulsion sealing effect is provided, which makes it possible to carry out light and heavy carbon fractions together with the oil base, which can be used in the oil and gas industry. As for separation, within the framework of this function, the phases of oil, water, gas, mechanical impurities and other sludge are separatedinclusions. Moreover, it should be emphasized that the separation technique itself does not at all mean the automatic release of components other than oil. The composition may also contain useful fractions, but their further processing will take place separately from oil.
The principle of operation of the stabilization process
Technology can be produced in two main ways - by separation and by rectification. In the first case, the accompanying gas phases and hydrocarbons are separated. For example, separation can be organized as an evaporation process, provided by changes in temperature and pressure in the working chamber. What is the process of oil stabilization through rectification? This method also involves the separation of certain phases, but the emphasis is on the process of heating the emulsion. In both cases, the parameters and additional processing processes will be set by the requirements for specific fractions that need to be isolated or stored in the composition.
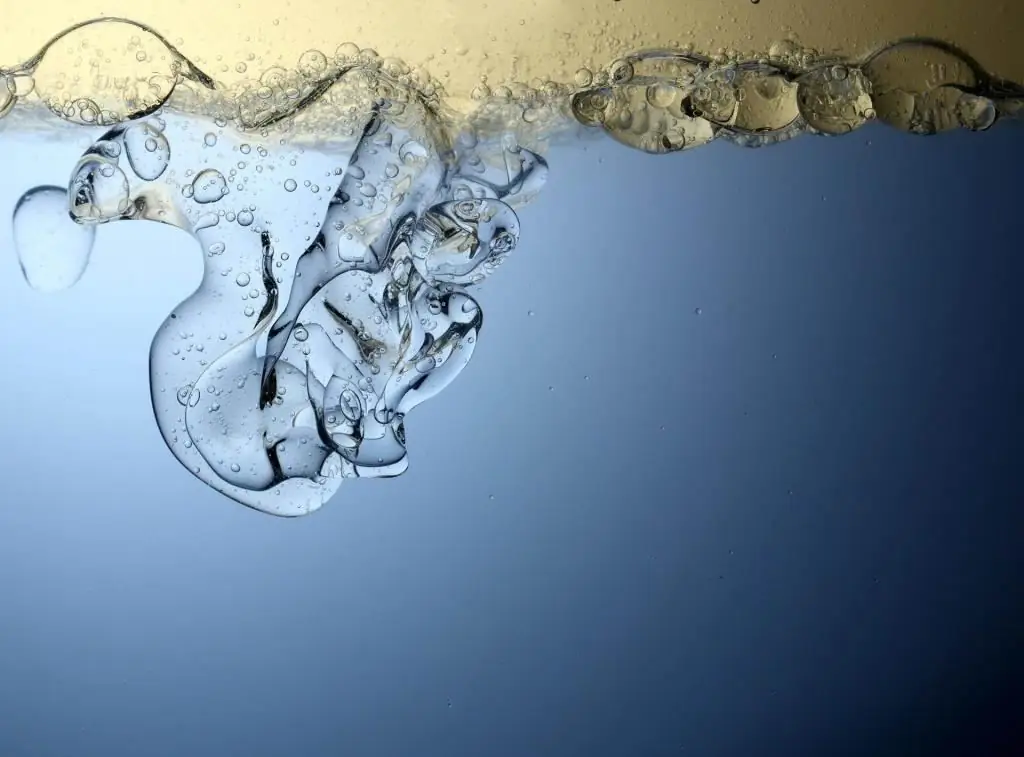
Technological stabilization process
In the extended scheme, the stabilization of water-oil emulsions can be represented by the following sequence of operations:
- Examination of a sample of the extracted emulsion. In laboratory conditions, based on the analysis of the sample, the composition, density, viscosity, volatility, flammability and other characteristics of the mixture are determined.
- Preparation for the chemical demulsification process. Heat is usually used to lower the viscosity of the emulsion and facilitate further separation.
- To be determinedseparation technology - gravity, electromechanical or electrochemical method.
- Directly the process of oil stabilization, in which several phases are released. Further, technologies for preparing the separated oil for production operations can be produced.
- Modification of isolated product with active chemicals.
Preparing oil for stabilization
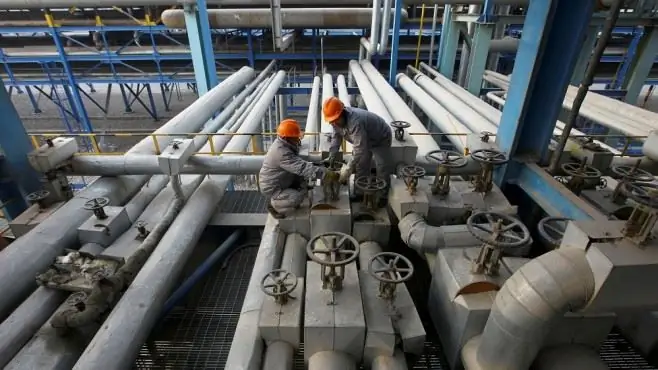
Before starting the technological processes of primary treatment, oil passes through several transportation hubs, within which pre-rough cleaning points can be organized. This may be a general filtration, ridding the emulsion of large particles of sand and sludge. From the field to the nearest crude oil reservoir, the product passes several metering stations, where primary samples are also taken and the volume lost is recorded. At the primary separation unit, the raw material is separated from formation water and associated gas in certain quantities. Oil is partially suitable for stabilization processes in a degassed and dehydrated state, but this is not the main requirement. Moreover, crude oil can be accumulated at collection points without any preliminary purification and sent to processing facilities in this state - then desalination, dehydration and stabilization procedures are performed in a different order. Today, complex purification and separation plants are also used, where a group of technological processes for preparing raw materials for a production operation takes place in a single processing cycle.
Setting forensure the stabilization process
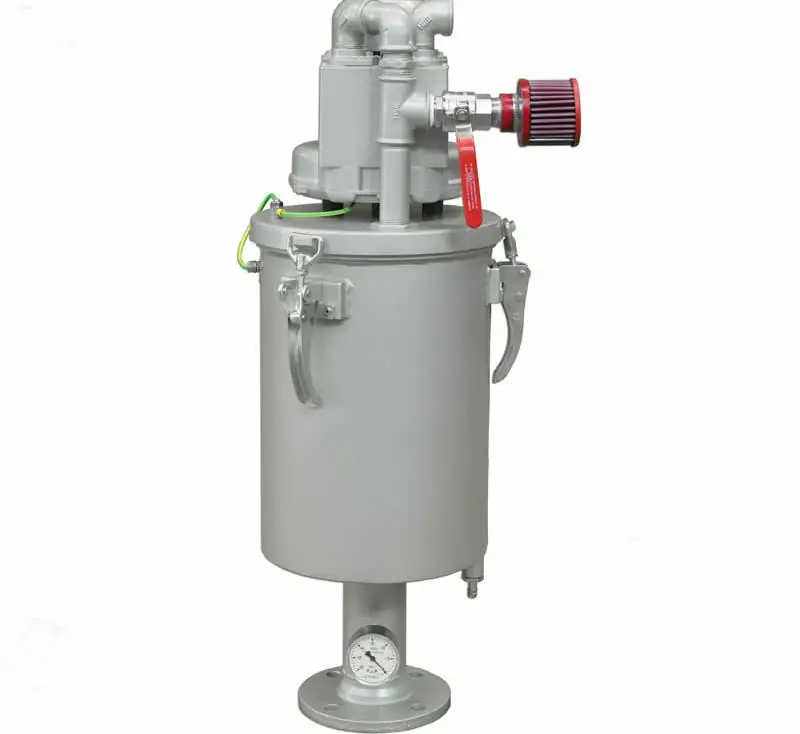
Most often, universal commercial separators are used for stabilization. They are integrated into oil and gas transmission networks and operate on the principle of flow-through service. The typical design is a cylindrical gravity separator with branch pipes for connection to pipelines and communication channels for power supply. The design of the oil stabilization unit (OSN) provides for several sections with a distributing manifold, through which the separated phases are transported through different channels. Oil, for example, is sent to a settling unit for the subsequent separation of occluded gas bubbles. Hydrocyclone double-tank separators operate on the principle of centrifugal forces, separating oil and gas into separate streams.
Equipment for oil stabilization and refining processes
The combined method of oil treatment in this case involves the implementation of processes for cleaning the product from light mercaptans and hydrogen sulfide. In the conditions of the oil field, this is the optimal combination of methods for the preliminary preparation of raw materials for further production stages. In the general technological process of cleaning and stabilization, heating, steam spraying, gas separation and removal of cleaned residues are used. An important condition is the regulation of pressure in the ranges of 0.1-0.2 MPa at temperatures up to 160 ºС. When using a properly selected stripping agent, it is possible to achieve high quality oil stabilization in the fields with the necessaryselection of distillates. The quality of the final product increases with the rapid decrease in temperature and pressure, which increases the intensity of separation of mixtures.
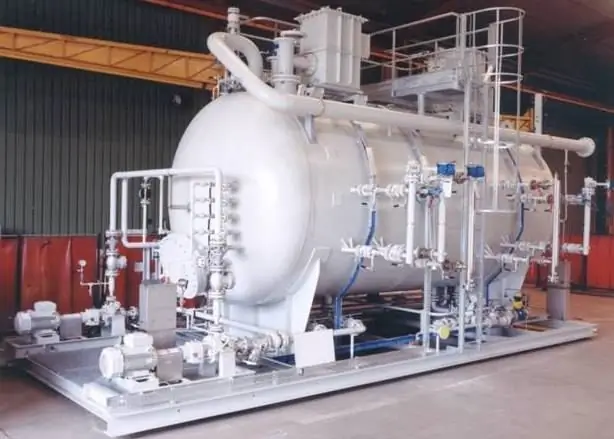
Device of distillation columns
Complex multi-functional installations use column groups to save logistics operations. Each of them performs a certain technological process, and related procedures take place in the common infrastructure at different levels. In this case, oil stabilization columns by means of rectification are considered. As a rule, this operation is organized after the processes of dehydration and desalination. The column has a heat exchanger in which the oil is heated to the optimum temperature, after which it is removed in the form of a vapor-gas-liquid mixture and separated into phases. On special plates of the rectifier, the liquid phases are irrigated with a stripping agent. Then the processes of cooling and enrichment with other active elements can follow, depending on the requirements for the selected distillate.
Positive stabilization effects
Technological organization of oil preparation processes requires considerable energy costs. The complexity of such procedures is also due to the fact that they are often performed in the field without a high level of infrastructure support. However, stabilizing oil in the early stages of refining provides the following benefits:
- Reducing the volume of excess fractions that are sent to fine lines before production.
- Simplification of technological schemes for oil treatment in oil and gas plants.
- Improving the safety of oil transportation due to the preliminary removal of sulfur-containing compounds.
- Increase in the volume of commercial oil due to the preservation of useful hydrocarbon components.
- Low requirements for processed raw materials.
Conclusion
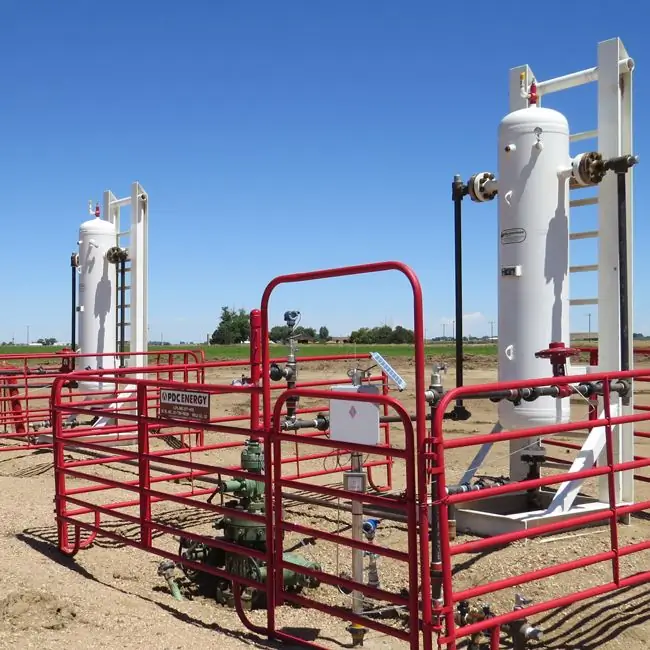
Stabilization methods are part of the general process of cleaning water-oil emulsions, but have their own characteristics in terms of application. First, it is a flexible procedure for its intended purpose. It can be performed both for the purpose of conservation of certain elements in the composition during the extraction and transportation of the resource, and for separation with the removal of unnecessary components. Secondly, the stabilization methods converge in execution technology with the general techniques of physical and chemical preparation of oil and gas raw materials, but with certain differences in the parameters of exposure to active media.
Recommended:
Motor oil production: characteristics, technology and manufacturing process
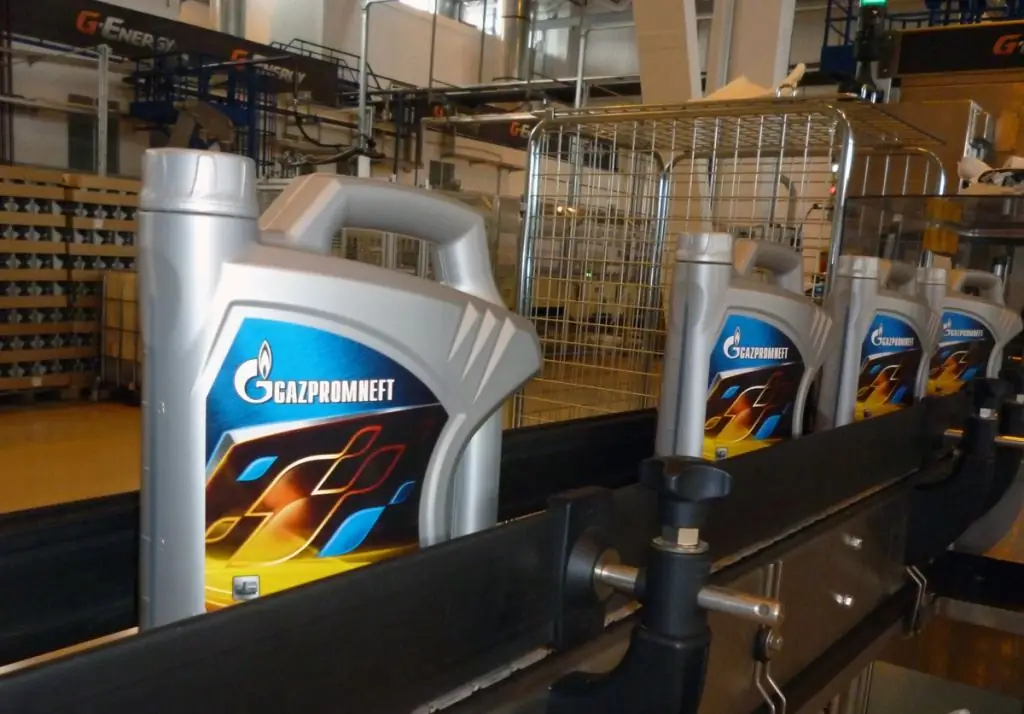
The production of motor oil, like any other, is not complete without raw materials - the substance from which the final product is obtained. Mineral oil is made from petroleum. But before it gets to the lubricants plant, it needs to go through a series of cleanings at oil refineries
What is produced from oil? Oil refining technology
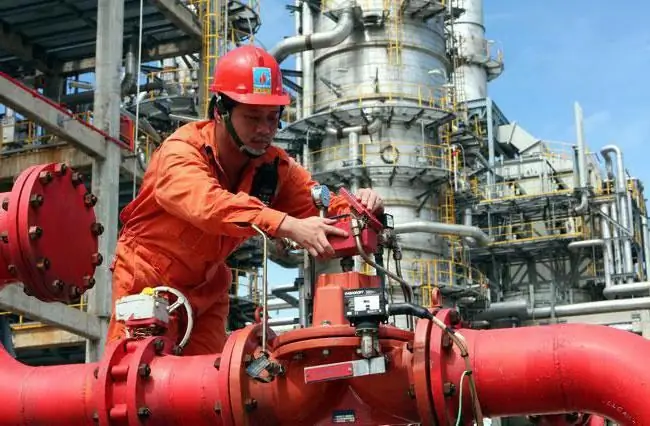
What is produced from oil: features, composition, types of products, photos. Oil refining technology: methods
Oil is a mineral. Oil deposits. Oil production
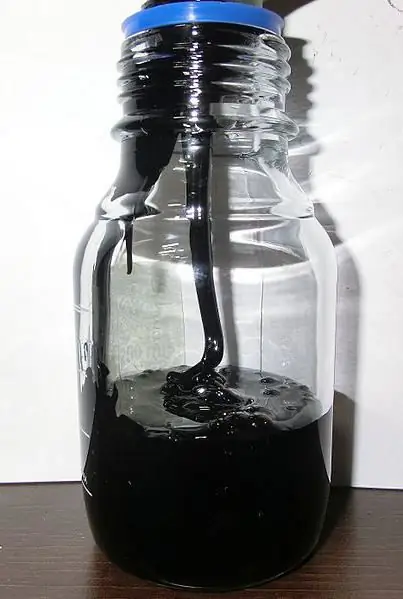
Oil is one of the world's most important minerals (hydrocarbon fuel). It is a raw material for the production of fuels, lubricants and other materials
Preparation of oil for processing: the main process, methods and technologies
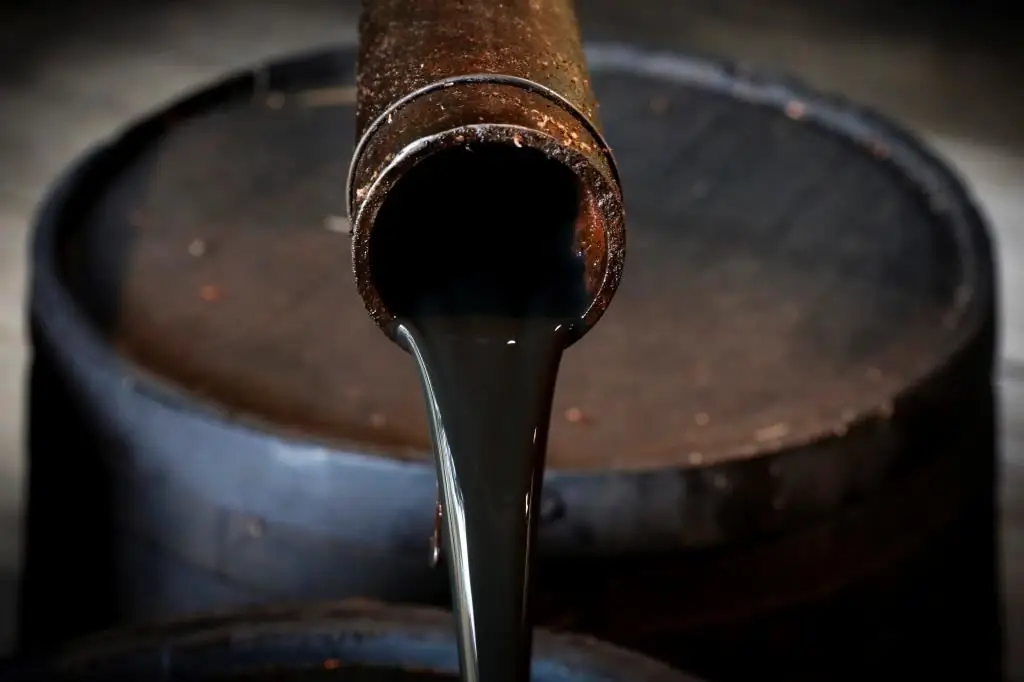
Produced from the wells of oil fields are not a raw material in its pure form. Before the stages of the production process of the main processing with the receipt of a trade item with the necessary consumer qualities, the future energy resource goes through several technological stages of processing. The need for the implementation of these processes is due to the initial contamination of crude oil
Cold smoking technology: the concept of the process, the construction of a smokehouse, the main rules of smoking and food preparation
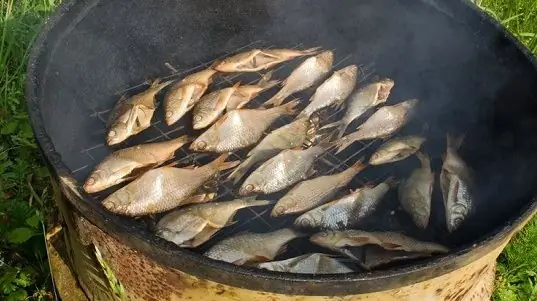
When cooking fish or meat in the country, if desired, you can also use cold smoking technology. Using this technique, it will not be difficult to get a very tasty homemade product. However, to smoke fish, meat or sausage in a cold way, of course, you need to do it right