2025 Author: Howard Calhoun | [email protected]. Last modified: 2025-06-01 07:12
Acid treatment of wells is one of the technologies used in the development of wells and their operation. Its main purpose is to clean the bottomhole to stimulate the inflow of reservoir fluid. There are several modifications of this technology, depending on the reservoir stimulation mode and geological conditions.
Purpose and principle
Acid treatment is used in drilling, operation and maintenance of oil production facilities to solve the following problems:
- treatment of the bottomhole zone during the development of the well (for the inflow of formation fluid after completion of its construction);
- intensification (debit increase);
- cleaning the filter and bottomhole from contaminants accumulating during operation, after water injection or well repair;
- remove deposits in casing strings and other underground equipment.
Acids pumped into the well dissolve calcium-containing rocks (limestone, dolomite and others), as well as particles of cement compositions that remain at the bottom hole after cementing the annulus.
Processing types
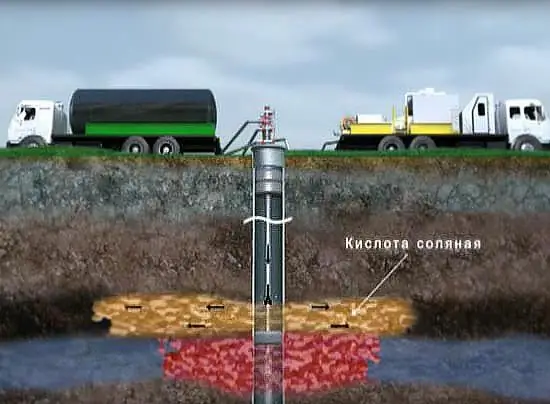
In the practice of operation and maintenance of oil production facilities, the following types of acid treatment are distinguished:
- matrix (injection of a reagent under pressure, the value of which is less than hydraulic fracturing);
- in-situ acid baths (simple treatment);
- under high pressure (acid fracturing, while fracturing occurs);
- interval exposure;
- thermal acid treatment.
The latter type of technology is used in situations where the reservoir pores in the bottomhole zone are clogged with paraffin deposits, tar and high molecular weight hydrocarbons.
Acid well baths are mainly carried out in the following cases:
- primary development (commissioning of wells);
- cleaning open filters;
- cleaning the filter blocked by casing pipes from acid-soluble materials.
Types of reagents
The basic substances used in the acid treatment of wells are hydrochloric HCl and hydrofluoric HF acids, as well as their mixture (clay acid). Less commonly used other acids:
- acetic;
- sulfamic;
- ant;
- sulfuric;
- mixtures of organic acids.
If the geological formation is in high temperature conditions, then acetic or formic acid is pumped into the formation. The use of sulfamic acid is justified in cases where the reservoirs consist of sulfate and iron-bearing carbonate rocks, sincetheir reaction with hydrochloric acid results in precipitation of gypsum or anhydrous calcium sulfate.
The working solution of the reagent is prepared at commercial acid bases and transported in road or rail tankers, painted inside with resistant enamel, rubber or ebonite coating.
Acid treatment is carried out not only in oil wells, but also in water injection wells (to maintain reservoir pressure), as well as in artesian wells. Work in Abyssinian wells, at shallow depths, can be done with a bailer to clean the wells.
Main parameters
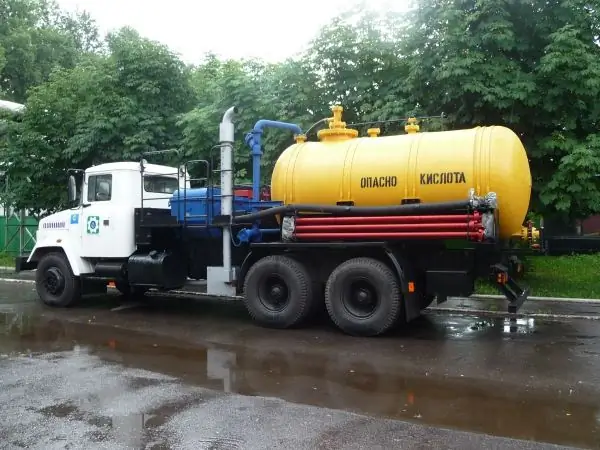
The following factors influence the choice of reagent composition:
- Fracturing of the rock. With a high value of this indicator, it is advisable to use thickened acids and foams. This helps to increase the coverage of the formation. To thicken the acid, carboxymethylcellulose (CMC) is added.
- Contamination of the bottom hole with mineral suspensions and low permeability of the porous reservoir. In this case, to improve the penetration of the reagent, carbonated acids are preferable, in which the surface tension at the boundary with the rock is reduced. Air, nitrogen, carbon dioxide are used to aerate liquids.
- Mineral composition of rocks. Seams consisting of sand, sandstones and siltstones are treated with clay acid.
- Bottomhole temperature. Thus, the use of sulfamic acid is limited by the fact that when heated to 80 ° C, it decomposes with water by 43%. At temperatures above 115 ° C, concentratedhydrochloric acid.
The required volume of acid is calculated by the formula and depends on the following factors:
- thickness of the acidized formation interval;
- rock porosity;
- processing depth;
- well radius.
Maximum injection pressure is determined by the following criteria:
- purposes and processing method;
- strength of production casing;
- thickness of the bridge between the working and adjacent formation interval.
The duration of acid exposure is determined empirically - by measuring its concentration in the solution displaced at the wellhead through the tubing. The average value of this parameter is within 16-24 hours.
Supplements
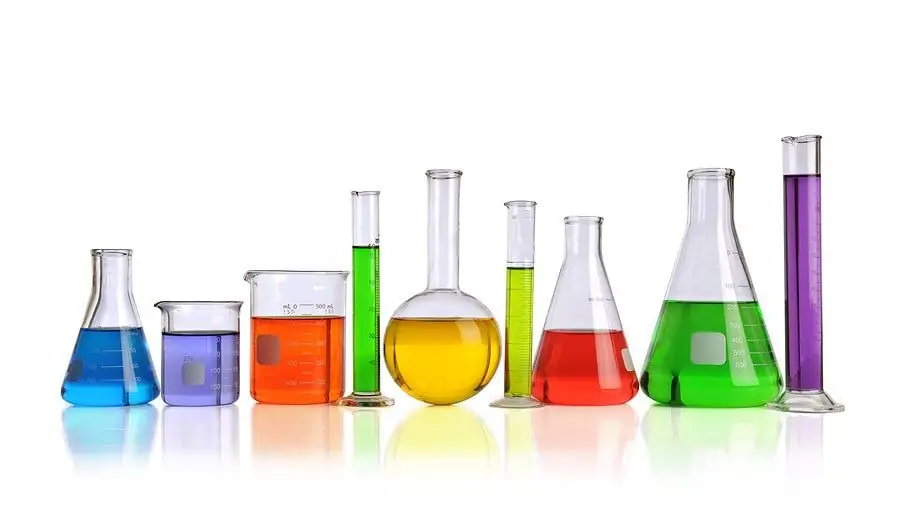
In its pure form, acids are rarely used. The following substances are used as additives to them in the oil industry:
- corrosion inhibitors - to prevent damage to casing, tubing and other equipment;
- complexing compounds that prevent the formation of a gel or iron hydroxide that clogs the pores of the collector;
- potassium nitrate for the treatment of anhydrites (sulfates);
- stabilizers to keep reaction products in a dissolved state;
- citric or acetic acid for treating iron-bearing carbonate rocks;
- surfactants, or intensifiers (OP-10, OP-7 and others) to improverock wettability and facilitate the removal of reaction products from the bottomhole.
Hydrochloric acid
When acidizing wells using HCl, its optimal concentration is 10-16%. More saturated solutions are not used for the following reasons:
- decreased dissolution rate;
- increase in corrosivity;
- increase in emulsifying ability;
- Increase in s alt precipitation when mixed with saline formation water.
When processing sulfate-containing rocks, additives from table s alt, potassium or magnesium sulfates, and calcium chloride are introduced into the working fluid. The latter substance also serves as an acid neutralization retarder at elevated bottom hole temperatures.
Hydrofluoric acid
Fluoric acid is a highly potent and is used to dissolve the following materials:
- silicate compounds in terrigenous formations;
- clay or cement slurry absorbed while drilling or well workover;
- cement crust at bottomhole.
Ammonium fluoride-bifluoride is also used as a substitute for this reagent, the consumption of which is 1.5 times less.
Simple hydrochloric acid treatment
Simple treatments are done with a single pump unit. Before acid is injected, the well is flushed with water to preliminarily remove sludge particles and other contaminants. If there are deposits of paraffin or resins at the bottomhole and in tubing pipes (tubing), then inas a flushing liquid, organic solvents are used - kerosene, liquefied propane-butane fraction and others. Processing in depleted fields can be done with a well cleaning bailer.
Preliminary activities also include the following operations:
- installation of the underground repair unit at the wellhead;
- removal of downhole equipment (for operating wells);
- descent tubing to the lower perforations of the treated interval:
- wellhead equipment with fittings for piping and check valve;
- piping of the pumping unit with tubing, acid carrier, tank trucks with displacement fluid;
- hydrotesting injection pipelines under pressure 1.5 times higher than the working one.
Next, acid is pumped into the well in a volume equal to the tubing cavity, after which the annular valve is closed. Then the remainder of the reagent and the displacement fluid are injected. Crude degassed oil is used as the latter in production wells. You can see how the acid treatment process looks like in the picture below.
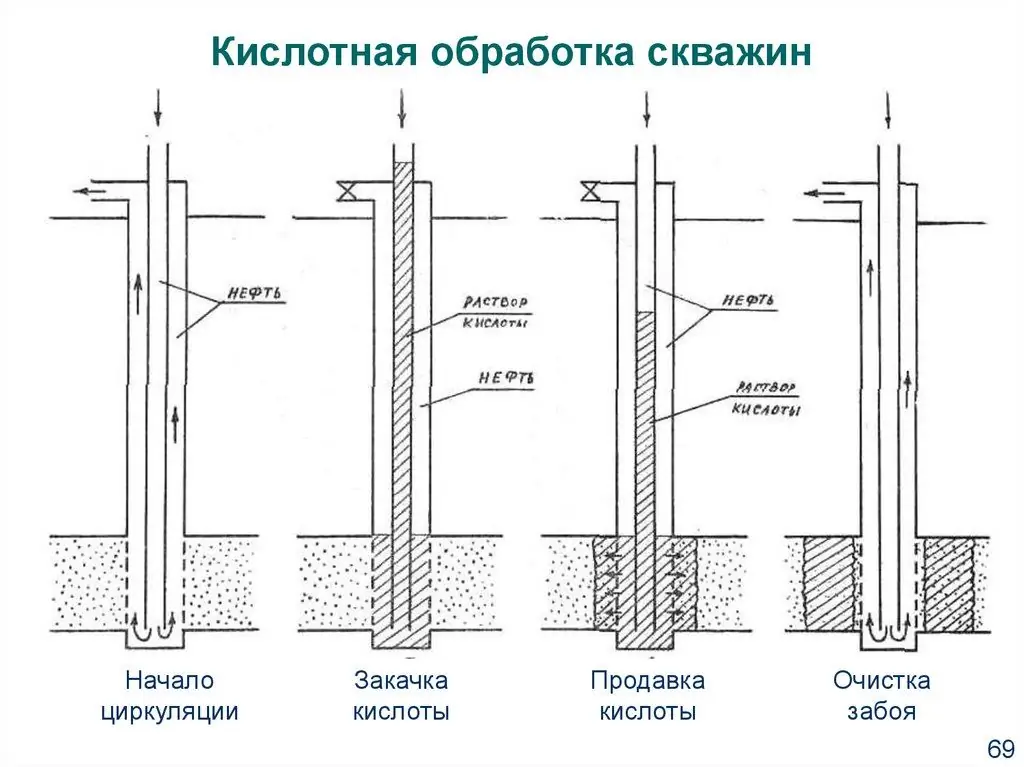
After pumping the full volume, close the buffer valve, disconnect the pump and other equipment. The acid remains in the well for the required time to dissolve, after which the products of the chemical reaction are pumped out by backwashing.
Interval technology
When opening an oil and gas reservoir with layers with differentpermeability, a simple acid treatment of wells leads to the fact that it affects only the most permeable layer. In such cases, it is advisable to use interval technology.
To isolate each layer, 2 packers are installed in the well. The flow of the acid solution through the annulus is prevented by cementing it. After processing the selected section of the reservoir, they proceed to the next one.
Acid fracturing and thermal acid treatment
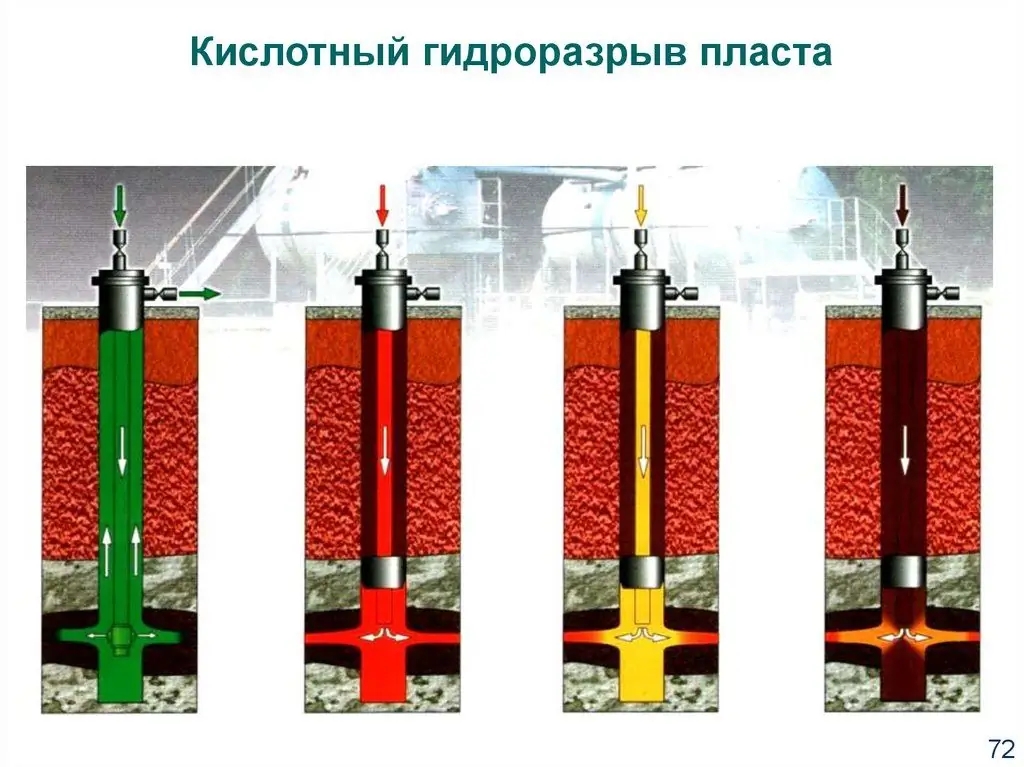
Acid treatment of wells under high pressure is carried out during the operation and development of reservoirs with heterogeneous permeability. Simple acid baths are ineffective in such cases, because the acid "leaves" in well-permeable layers, while other areas remain uncovered.
Before injection of the reagent, high permeability layers are isolated using packers (similar to the previous technology). Preparatory measures are carried out according to the scheme of simple acid treatment of wells. The casing string is protected by installing an anchored packer on the tubing.
As a working reagent, an emulsion prepared from a solution of hydrochloric acid and oil is used. How the layout of the Azinmash-30A unit for acid injection into the reservoir looks like is shown in the figure below.
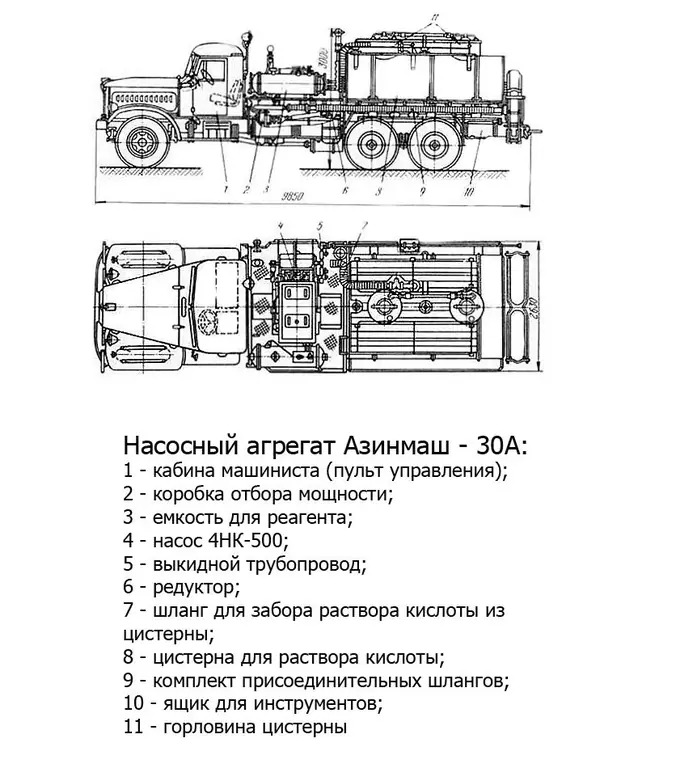
This unit is equipped with high pressure triple plunger horizontal pumps. Sometimes 2 pumping stations are used for processinginstallation. The oil industry also produces other units - UNTs-125x35K, ANTs-32/50, SIN-32, manufactured on the KrAZ or URAL chassis. A typical layout of the units includes a wheeled off-road chassis, an assembly platform on which the main process equipment is installed, high-pressure pumps, a tank for transporting and supplying a reagent, an acid-resistant manifold consisting of pressure and suction pipelines.
In case of thermal acid treatment, reaction tips are lowered into the well. Their inner cavity is filled with magnesium in the form of chips or granules, and the outer surface has perforated holes. When exposed to acid, magnesium releases a large amount of thermal energy.
Protecting equipment from corrosion
Reagents used in acid treatment of wells are corrosive environments with respect to metals. The corrosion rate of parts made of St3 steel at a temperature of 20 °C and a concentration of HCl 10% is 7 g/(m2∙h), and for a mixture of 10% HCl and 5% HF - 43 g/(m2∙h). Therefore, inhibitors are used to protect equipment metal:
- formalin;
- catapine;
- urotropine;
- I-1-A inhibitor;
- unicol and others.
Safety for acidizing wells
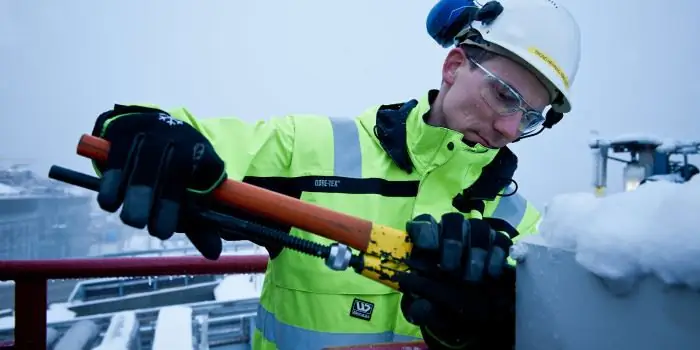
Toxic and flammable substances are used when acidizing the formation. In the event of a leak or spill, great damage can be doneenvironment.
An acid treatment plan is being developed and approved by the Chief Engineer of the OGPD. Works are carried out according to the permit and technological regulations. The following security measures apply:
- Remains of chemicals and washing liquids are collected in special containers for subsequent disposal.
- The concentration of acid vapor is monitored using a gas analyzer.
- Pumping equipment and tanks are installed at a distance of at least 10 m from the wellhead, car cabs are located in the opposite direction.
- During the injection of acids, only those workers whose activities are directly related to the maintenance of equipment remain near the units; all other persons are removed to a safe distance.
- It is forbidden to carry out work in strong winds, fog and at night.
- Repair and installation work on pipelines and process equipment is not carried out until the pressure in the system is released.
- To protect against the effects of acids, personal protective equipment is used - special clothing (rubber aprons, boots), rubber gloves, glasses, masks, gas masks.
The field should also have an emergency supply of overalls and chemicals to neutralize acids (lime, chalk, chloramine and others). All operating and engineering personnel are required to undergo periodic training and certification for knowledge of safety regulations according to a schedule approved by the head of the enterprise.
Recommended:
Mineral enrichment: basic methods, technologies and equipment
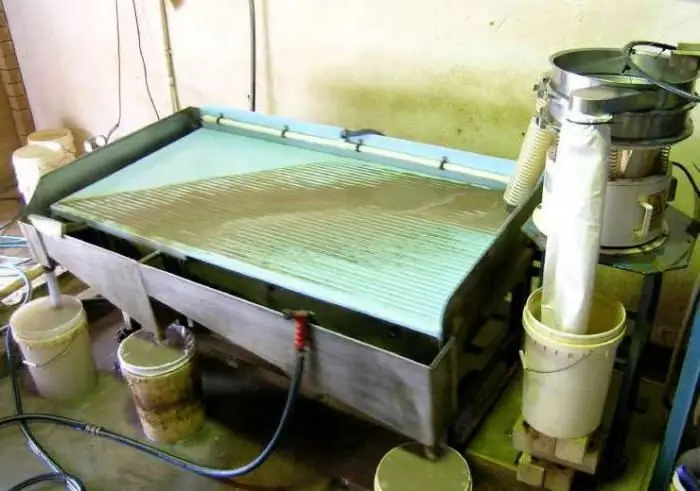
The article is devoted to the technology of mineral processing. The stages and methods for performing such processing are described
How self-tapping screws are made at the factory: technologies and equipment. Machine for the production of self-tapping screws
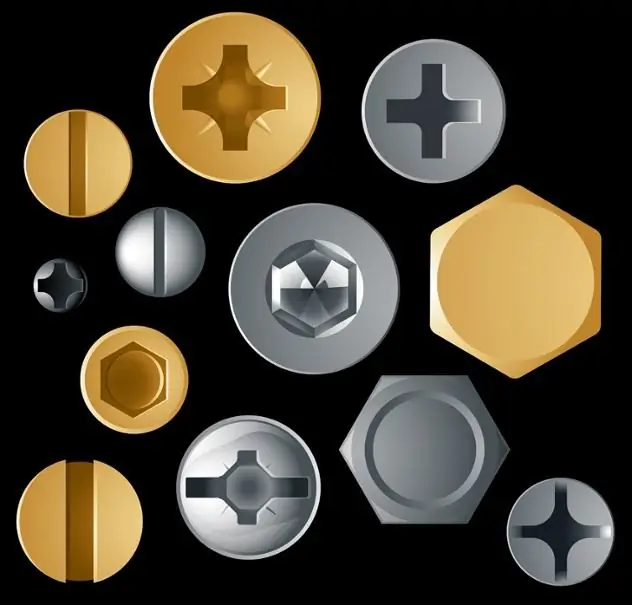
How are self-tapping screws made at the factory? The answer to this question is a fairly simple technique. At the enterprises, blanks with hats are first made from steel wire. Further, threads are cut on such blanks
Clothing industry as a branch of light industry. Technologies, equipment and raw materials for the clothing industry
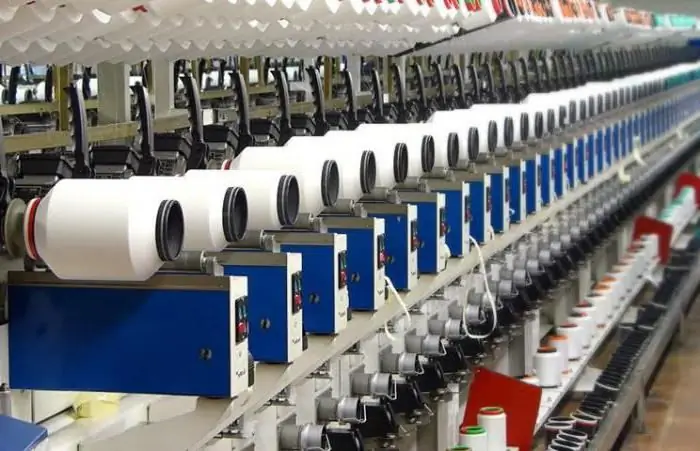
The article is devoted to the clothing industry. The technologies used in this industry, equipment, raw materials, etc. are considered
Equipment for gas-lift operation of wells
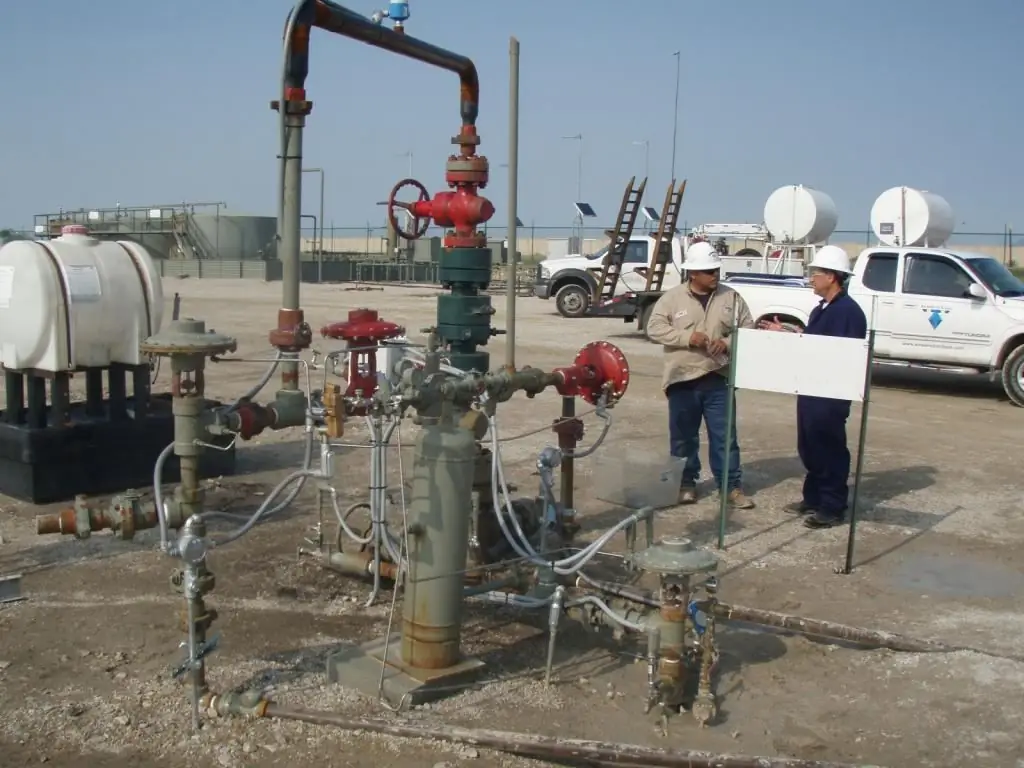
Gas-lift production of oil and gas resources can be considered as a more progressive alternative to the traditional method of flowing well development. It is distinguished by elements of passive extraction of target materials, which is facilitated by the energy of the gas. This feature of gas-lift operation of wells determines the specifics of the technical organization of the production process, which is directly reflected in the characteristics of the equipment used
Welding of copper and its alloys: methods, technologies and equipment
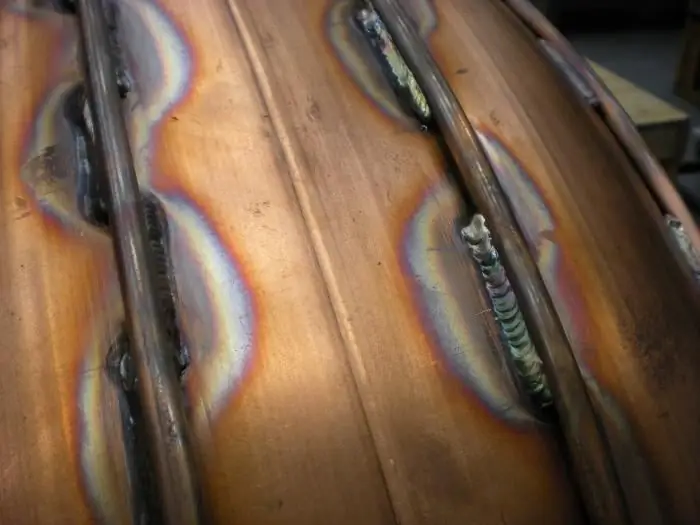
Copper and its alloys are used in various sectors of the economy. This metal is in demand due to its physicochemical properties, which also complicate the processing of its structure. In particular, the welding of copper requires the creation of special conditions, although the process is based on fairly common thermal treatment technologies