2025 Author: Howard Calhoun | [email protected]. Last modified: 2025-01-24 13:10
There are no minor details in construction. Any elements used in the construction of buildings and structures must be of good quality and have a long service life. This also applies to various kinds of fasteners, including, of course, their most popular variety today - self-tapping screws. How such construction consumables are made - we will talk about this later in the article.
What are they made of
Self-tapping screws in construction are used in the assembly of frame walls of houses, truss systems, floor and ceiling lining, sheathing of enclosing structures. That is, the load on such fasteners during the operation of the house is significant. Therefore, the material for the production of such elements must be used very durable and also quite plastic.
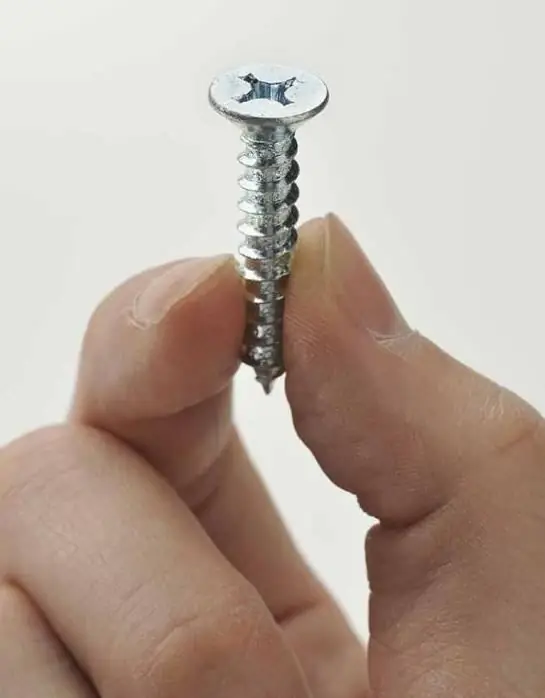
In modern enterprises, self-tapping screws are made, of course, from steel. At the same time, the production of such elements is usually chemically and thermally treated material of this type ST 10 KP or ST 08 KP. Such steel has rather high indicators of superficial hardness and plasticity. Its only drawback is an increased tendency to ageing.
From steel ST 10 KP or ST 08 KP, a wire is pre-made, the diameter of which corresponds to the diameter of the legs of future self-tapping screws. Further, such material is wound into coils and sent to factories specializing in the manufacture of building fasteners.
The first stage is the production of blanks
So, how are self-tapping screws made in factories? At enterprises engaged in the production of such consumables, steel wire is fed to special cold heading machines. On such equipment, it is pre-straightened. Then, directly on the machine, blanks for self-tapping screws are made from wire. That is:
- cutting into segments of the required length is performed (along the length of the self-tapping screws);
- a hat with a slot is made by pressing.
The slot on the heads of self-tapping machines on cold heading machines can be printed for both Phillips and regular screwdrivers.
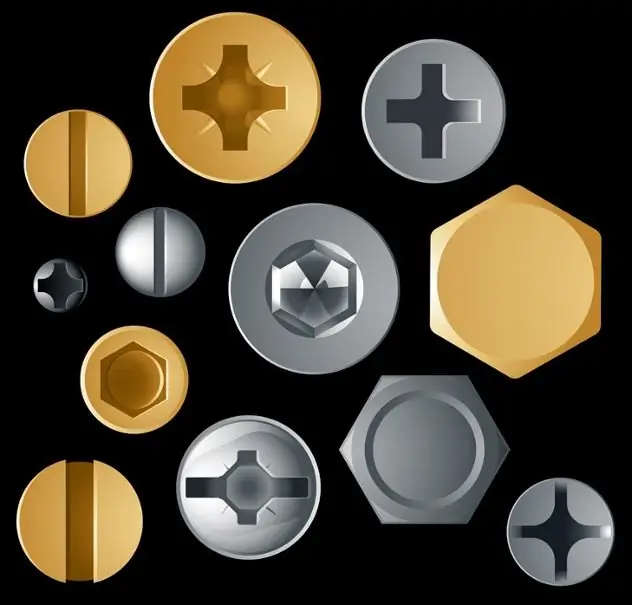
Threading
After the manufacture of blanks for self-tapping screws, the most thorough quality control is carried out at the factories. Specialists selectively measure the length of fasteners and their diameter. A visual inspection of the workpieces is also carried out in order to detect mechanical damage on their surface. Some batches of ingots can therefore be rejected after passing through the cold heading machine.
Quality-checked workpieces are then fed to the threading machine. FROMOn the conveyor line, the blanks are poured into a special screw, which, turning a large number of blanks at once, exposes them with a hat up. In this position, the blanks are subsequently fed into a special threading device. In this unit of the machine, each workpiece is pulled by a rolling motion between special flat dies. As a result, a thread is formed on its leg, as well as a self-cutting point.
How self-tapping screws are made: hardening
After the threading machine, fasteners at the factory take on the shape already familiar to everyone. Having passed the flat dies, almost finished self-tapping screws are poured into a special bunker and transported to a thermal furnace. Previously, such products pass one more quality control at the enterprise.
Firing fasteners in thermal ovens is rather slow. In this case, heat treatment is usually carried out at a temperature of more than 930 ° C. After the furnace, the self-tapping screws are also fed along the line into special containers with coolant. In this way, fasteners are hardened.
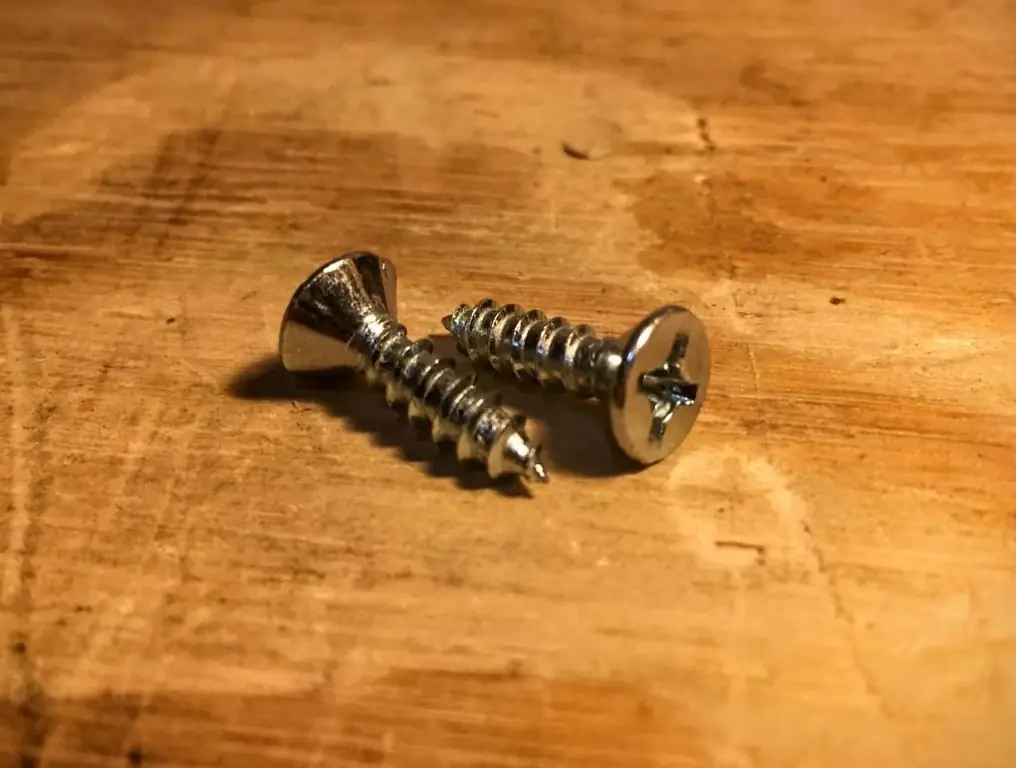
Coloring
After hardening, the self-tapping screws are fed into special equipment for applying a protective coating against corrosion. Depending on the purpose of fasteners (for wood, metal, etc.), they can be processed at this stage by:
- phosphating;
- oxidation;
- galvanizing with white or yellow zinc.
For example, self-tapping screws designed for metal work are usually yellow.
Finalstage
The technology described above is the answer to the question of how self-tapping screws are made for wood, metal, stone, etc. In any case, after applying a protective coating, finished self-tapping screws are fed to the packaging line. They first go through a final quality control procedure. After such a check, only the most durable fasteners that fully comply with standards and regulations remain.
In large enterprises, the packaging process is usually also fully automated. Special equipment at such factories makes boxes from cardboard blanks, into each of which a certain number of self-tapping screws is poured by weight. Next, the boxes filled with fasteners are assembled into blocks of several pieces and fed to the finished product dispatch shop.
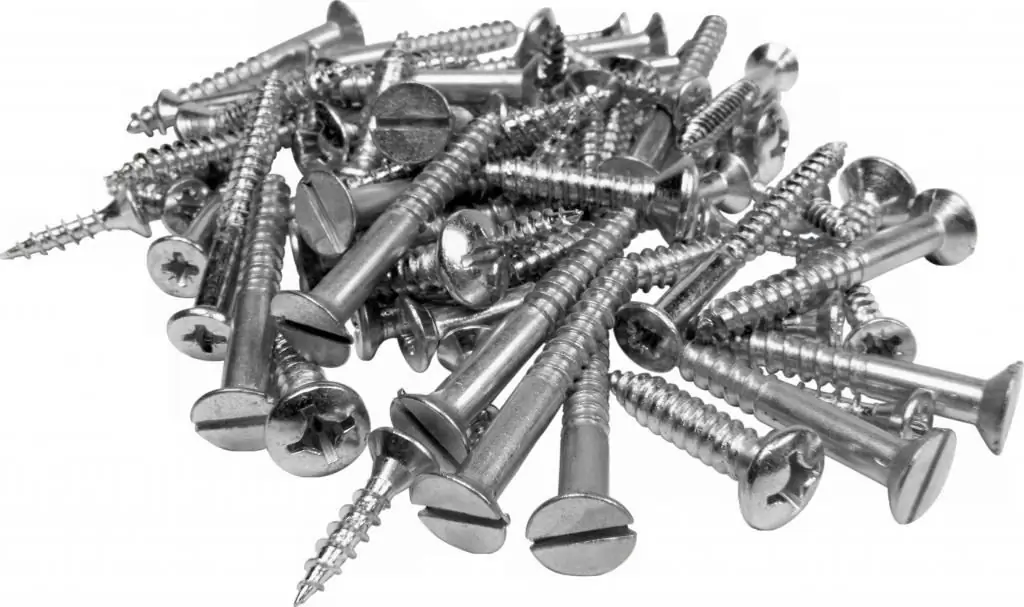
Automatic lines
So, we found out how self-tapping screws are made. In small enterprises, for the manufacture of such elements, usually only cold heading machines and threading machines are used. At the same time, such workshops are engaged in the production of the simplest wood screws in most cases. At large enterprises, automated, very expensive lines are installed for the manufacture of such fasteners.
From one type of equipment to another, self-tapping screws in such factories are fed along conveyor lines. At the same time, they can be transported between the tiers of the production workshop in bunker elevators.
In addition to cold heading and threading, the design elements of automatic lines for the production of self-tapping screws in Russia can be:
- heat ovens;
- hardening tanks;
- color lines;
- packaging equipment.
What is a cold header
Such equipment belongs to the group of machines:
- stationary medium-sized;
- universal express;
- automated two-strike;
- continuous action.
Machines of this variety can be used for the production of not only self-tapping screws, but also almost any other type of fasteners - bolts, screws, etc. In this case, everything depends on the settings of such equipment.
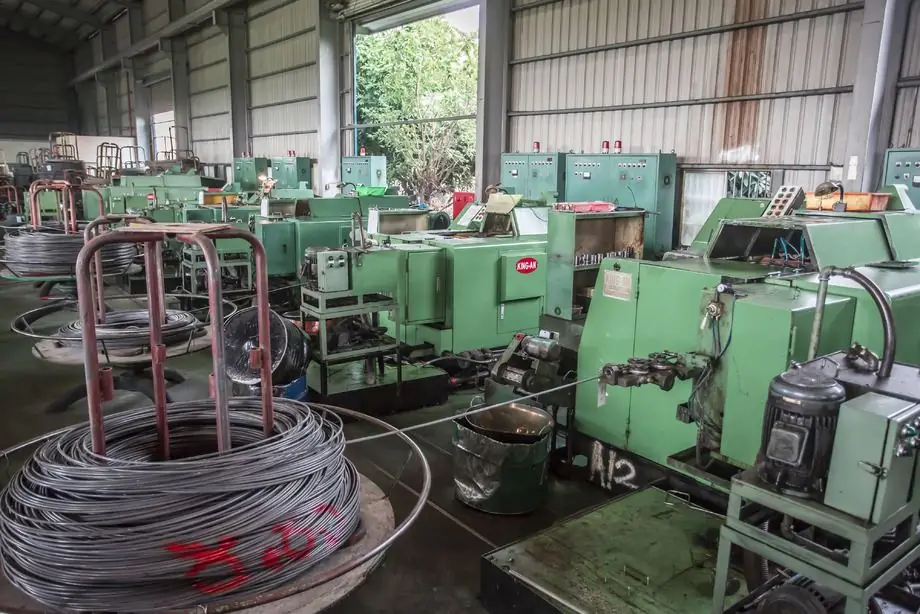
Cold heading machines are mounted on the basis of a rigid welded frame. The wire is fed to the main unit in them from the bay with a ratchet device step by step. The length of the workpiece in machines of this type is regulated by the rearrangement of the stop. Heading strokes in the equipment are performed by a punch. The first blow drives the rod to the stop, and the second one forms the head.
How self-tapping screws are made in enterprises, therefore, is understandable. The production technology of such fasteners, in principle, is not too complicated. At the same time, the cold heading machines themselves produce workpieces very quickly. Depending on the performance and power indicators, one such unit can produce up to 100-300 self-tapping screws per minute.
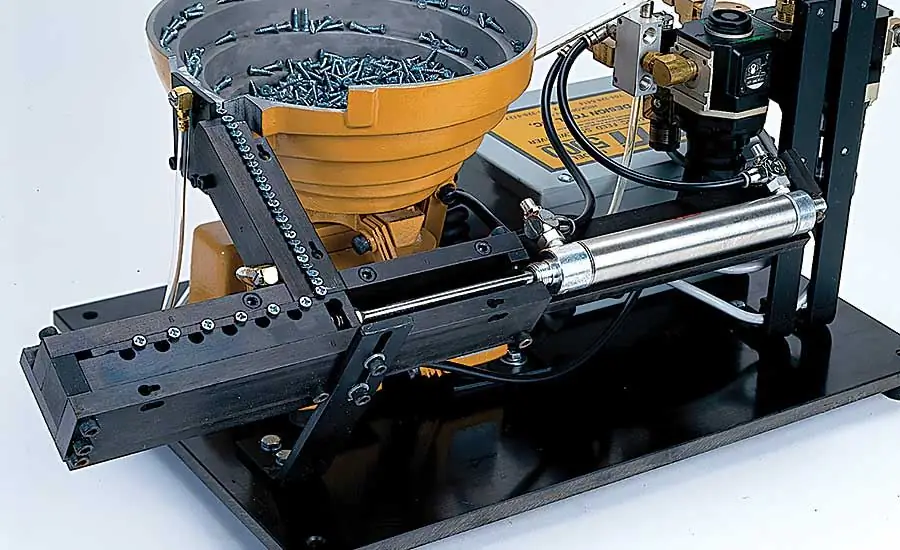
Thread rolling machine forproduction of self-tapping screws
In such equipment, blanks are fed between the dies one by one. At the same time, as already mentioned, they are strictly oriented in relation to such work items. Flat dies in the machine move towards each other parallel and perpendicular to the axis of the self-tapping screw. Such working elements of machine tools are manufactured according to the required thread parameters. At the same time, domestic manufacturers of self-tapping screws take metric sizes as a basis, while foreign manufacturers take inch sizes.
Recommended:
Mineral enrichment: basic methods, technologies and equipment
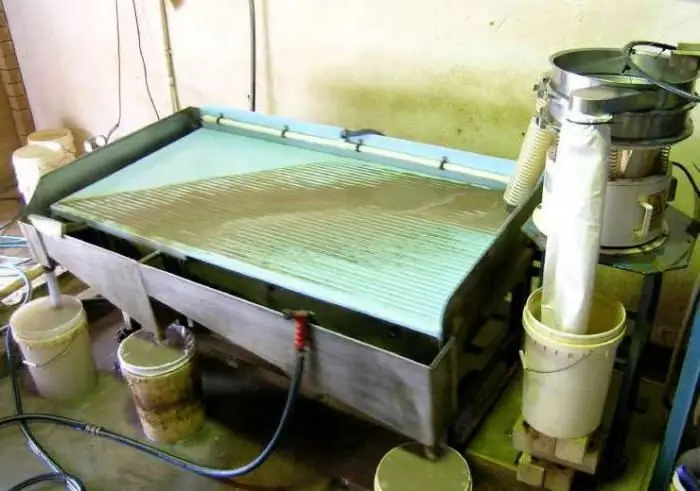
The article is devoted to the technology of mineral processing. The stages and methods for performing such processing are described
What billiard balls are made of: history, materials, technologies
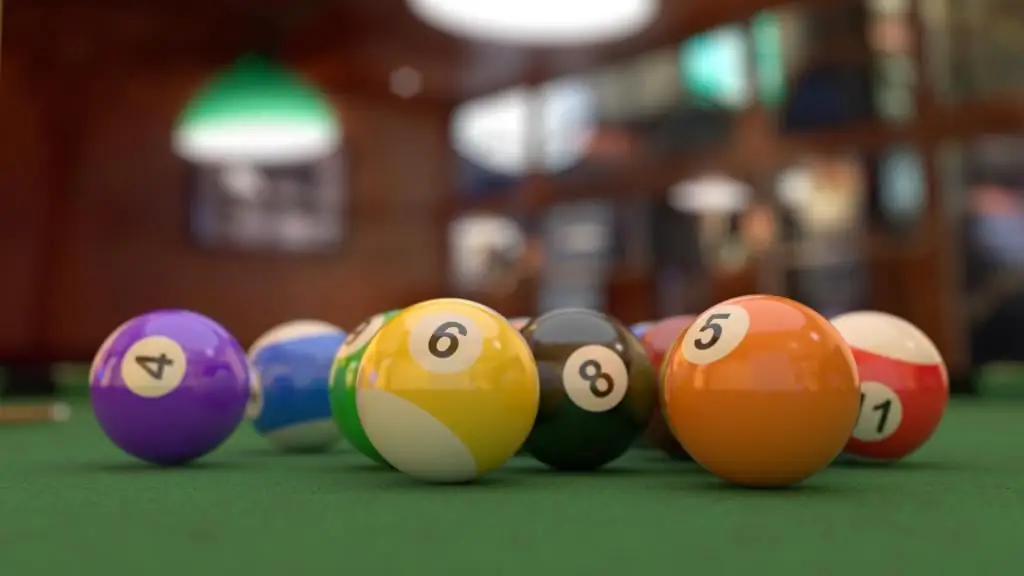
The date of creation of billiards, as well as the name of its inventor, is unknown to historians. The first evidence of the existence of such a game dates back to the 15th century: French explorers discovered a table similar to a billiard table built around 1470 and dating back to the era of Louis 11. History is silent about what the billiard balls of that time were made of, but some data allow one to speculate
What is milk made of? How is milk powder made?
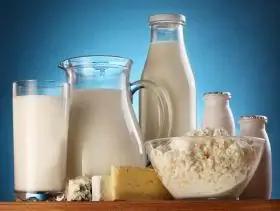
Surely everyone is concerned about the question of what milk is made of. In this article we will try to find answers to it and learn a lot about this product familiar from childhood
How were matches made before and how are they made today? Swedish matches
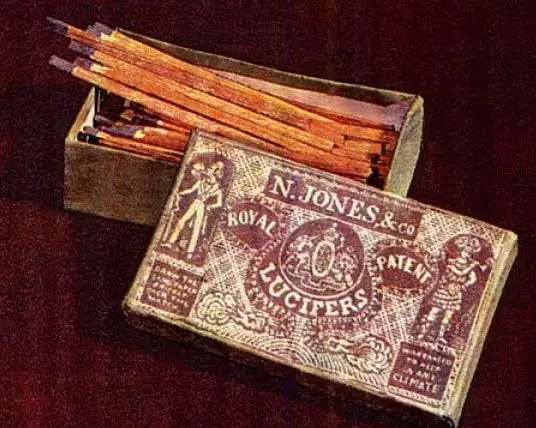
The article is devoted to the history of the creation of matches - from their very first prototypes to modern ones. It also tells about the famous Swedish matches, the evolution of the chemical components of the match head and stickers for the box
Welding of copper and its alloys: methods, technologies and equipment
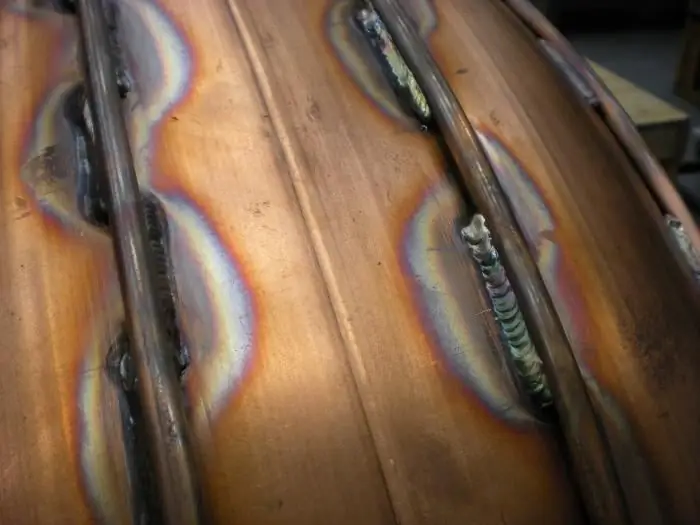
Copper and its alloys are used in various sectors of the economy. This metal is in demand due to its physicochemical properties, which also complicate the processing of its structure. In particular, the welding of copper requires the creation of special conditions, although the process is based on fairly common thermal treatment technologies