2025 Author: Howard Calhoun | [email protected]. Last modified: 2025-01-24 13:10
Currently, engineers are actively working to create new and improve traditional methods of restoring parts. And there are objective reasons for this: firstly, in some cases, the manufacture of new products from expensive steel is more costly in terms of resources, and secondly, the enterprise simply does not have the technological ability to produce new parts that are complex in shape and technical requirements.
Organizations that operate complex and expensive equipment (for example, heavy-duty mining trucks) are interested in improving various methods of restoring worn parts.
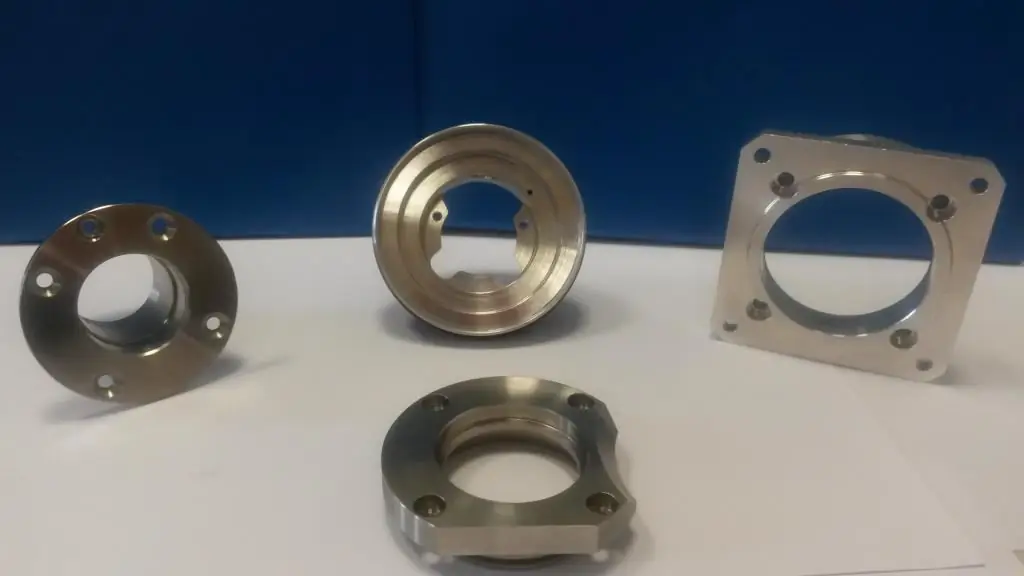
General provisions
All methods of restoring parts are aimed at regenerating the performance properties and original characteristics of the product. In the process of work, rubbingthe surfaces of friction pairs can wear out (as a result of which their dimensions change), crumble (as a result of the accumulation of fatigue stresses under frequent alternating loads), receive mechanical damage, and change their physical and mechanical properties. A separate type of damage during operation is the violation (damage) of the protective anti-corrosion and wear-resistant coating.
Methods and methods of restoring parts are very diverse. However, the wear of machine parts can have different consequences and a different mechanism of formation and causes. When choosing a specific technology for the restoration of worn surfaces, the engineer must first of all consider what properties (mechanical and physical) the product should have.
So, in some cases, it is necessary to achieve maximum fatigue strength of the structure and elasticity. Sometimes the chemical composition of the surface layer is critical, which makes it possible to increase heat resistance, red brittleness (cold brittleness), resistance to aggressive media, therefore, in each specific case, preference should be given to the method of restoring parts that can meet all requirements. Special technological and design requirements also include integrity (the absence of pores, microcracks, non-metallic inclusions), the mass of individual structural elements and the product as a whole, roughness indicators, mechanical properties (hardness and microhardness), the possibility of machining and pressure (additional hardening due to deformation surface layer andhardening), the accuracy of geometric deviations of surfaces and shapes.
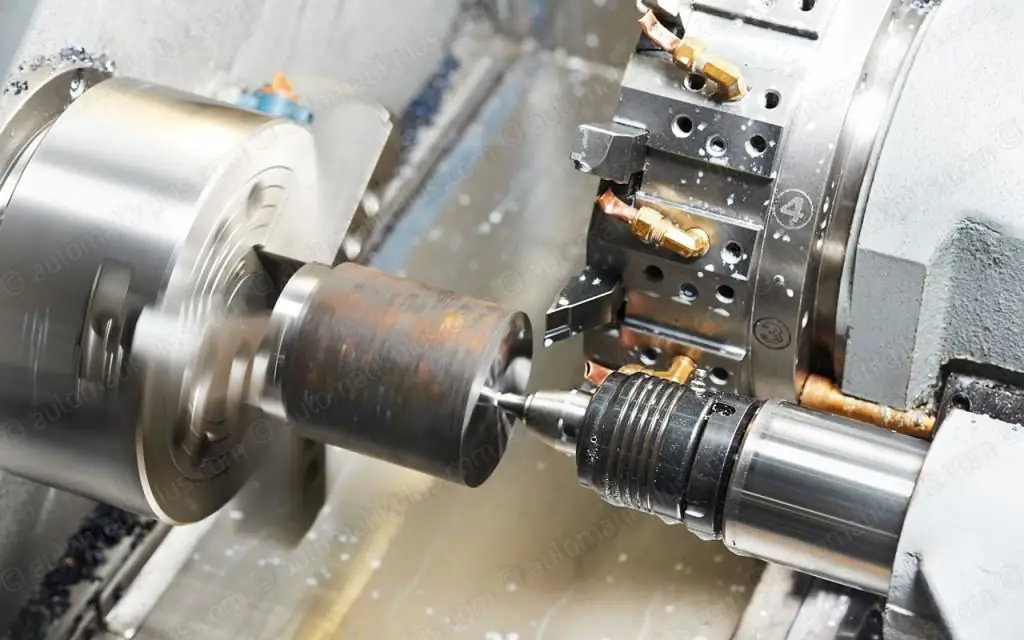
Classification of ways to restore parts by type of defects to be eliminated
The whole variety of recovery methods, depending on the nature of defects, is usually divided into the following groups:
- cutting and metalworking;
- welding and soldering;
- plastic deformation;
- fusion;
- diffusion metallization and sputtering;
- electroplating technology;
- chemical heat treatment (CHT) as well as traditional heat treatment;
- use of composite materials.
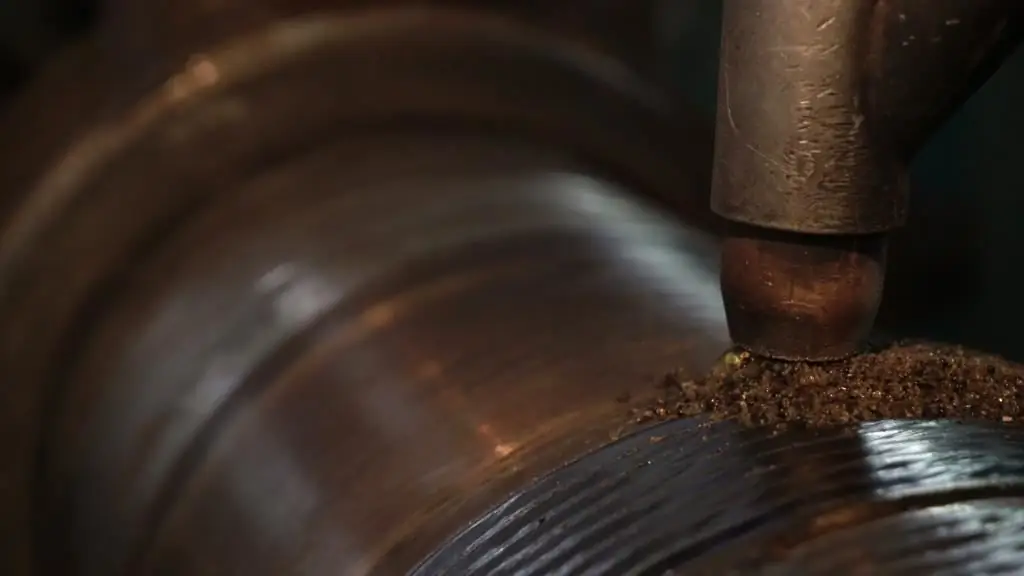
Classification of recovery methods depending on the nature of the impact on the part
According to this principle, all recovery operations are divided into three groups:
- processing without removing allowances;
- machining parts with material removal;
- technological operations associated with the application of coatings and materials in one way or another.
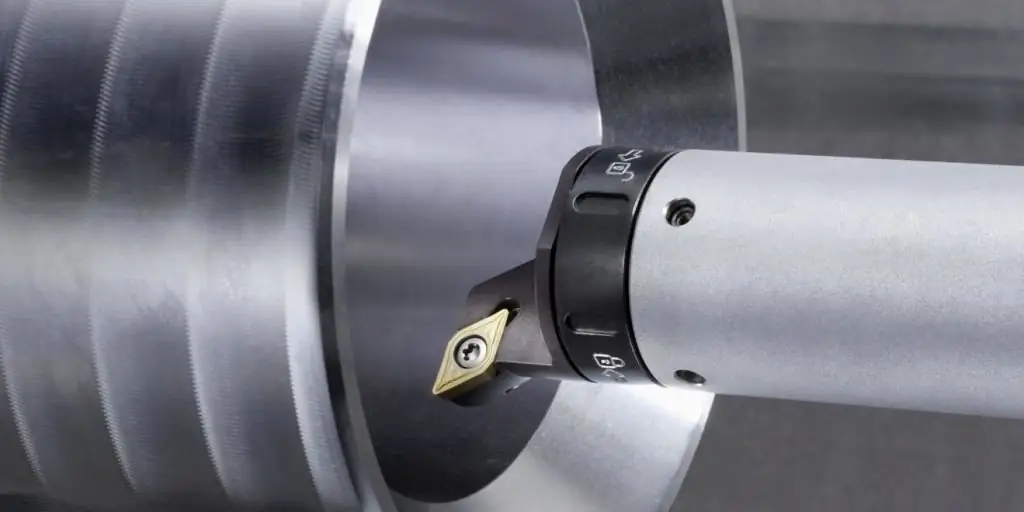
It makes sense to give a more detailed classification of the listed groups, since each of them includes many processing methods using very different equipment and principles. In some cases, duplication in the name of the method of restoring parts is possible, since one method can simultaneously apply to severalgroup.
Restoration without removal of allowances:
- hardening and shaping by cold and hot plastic deformation, calibration;
- chemico-thermal treatment (carried out in order to increase hardness, improve performance);
- heat treatment (increasing hardness, removing dangerous stresses, and so on).
Methods for restoring worn parts involving the removal of a layer of material:
- machining;
- electrophysical processing;
- combined methods.
The last subgroup includes methods that allow applying an additional protective layer of material to the surface of the part. The main recovery methods for coated parts include:
- deposition of metal and non-metal coatings in the furnace (metallization, spraying, surfacing and others);
- electrophysical coating methods (electroplating baths, electrospark methods, and so on).
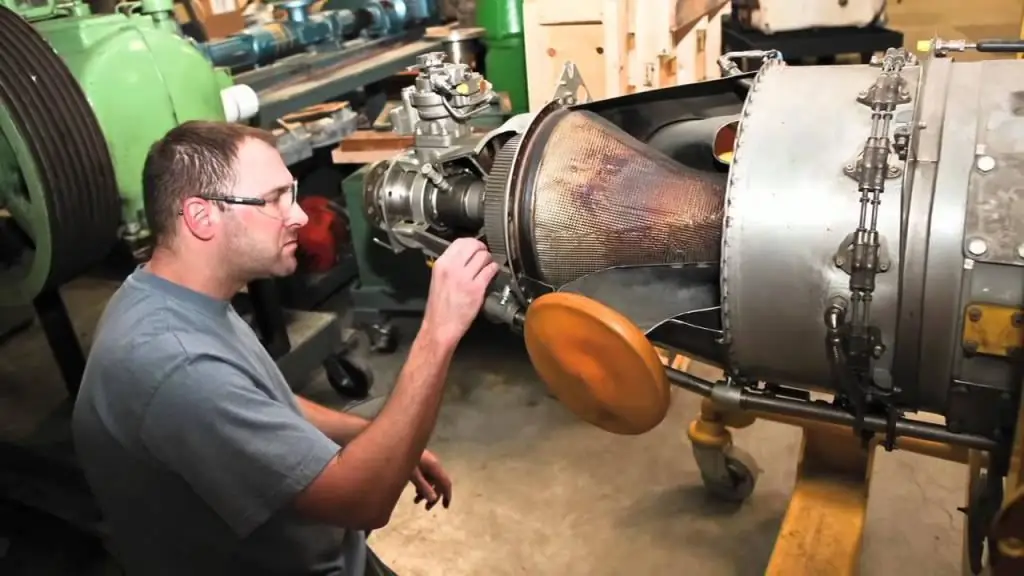
Characteristics of metalwork and mechanical restoration operations
This method of restoration and hardening of parts is used in cases where it becomes necessary to obtain a new or old repair size of the product, as well as when it is necessary to install a new element of the restored engineering product. So, mechanical and locksmith processing can serve as a kind of intermediate operation,aimed at preparing surfaces for application and deposition of additional hardening coatings. However, most often, cutting is final and is aimed at correcting shape and surface defects that have arisen for one reason or another. Such reasons can be surface and volume deformation of parts and blanks in order to give them greater strength and the most favorable performance characteristics, surfacing of metal powder and electrode, and so on.
Processing to size should ensure all technological and design requirements: cleanliness and roughness of surfaces, values and magnitude of the gap or interference (if the landing is carried out with an interference fit), deviations of the geometric shape, and so on.
An engineer makes a choice in favor of one or another mechanical method of restoring a part, taking into account a number of different factors. So, if the degree of wear of the part is very large, then it makes sense to install an additional repair part. In this case, surfacing with subsequent processing will cost much more and require very high qualifications from the performer. All kinds of bushings and adapters serve as such parts.
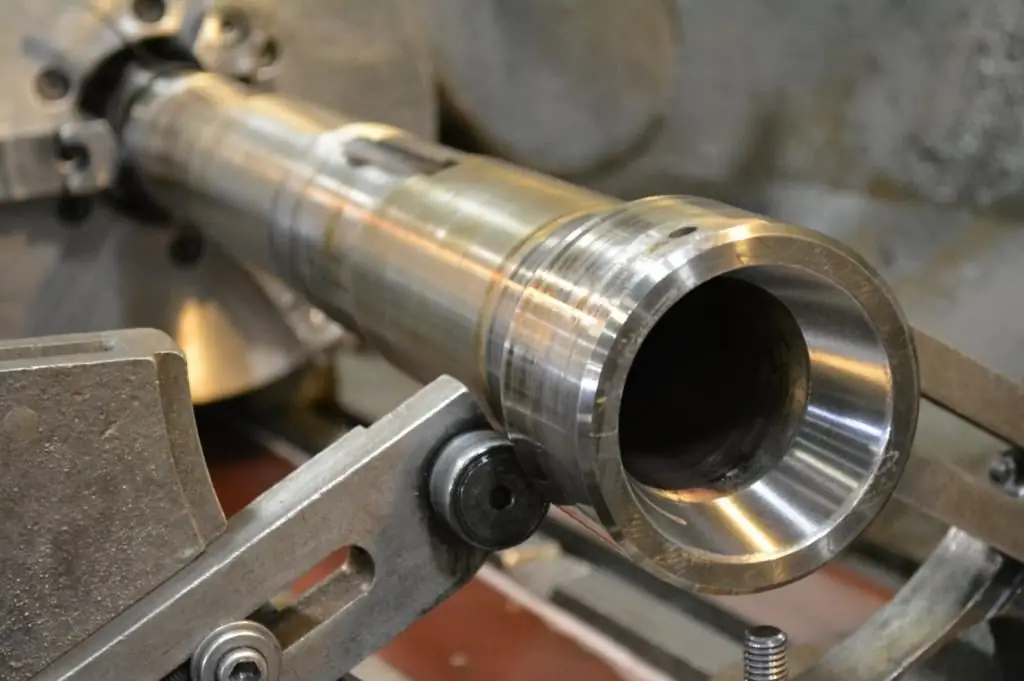
Characteristic of restoration of parts by plastic deformation
Deformation is used both to change the shape and geometric dimensions of the part, and to improve the operational characteristics of the surface of the product (indicator of hardness and wear resistance).
With a change in shape, everything is clear:when a significant load is applied to a solid body and then removed, residual deformation remains. This method of restoring machine parts is used in practice if it is necessary to align products that have been damaged as a result of a collision. This type of work includes both body work on a car that has been in an accident, and straightening of a thick steel sheet. Often the need for pressure treatment arises after welding treatment: when applying a seam, certain local zones become very hot, which leads to a linear expansion of certain elements of the welded structure. During cooling, the reverse process occurs - a decrease in size, which leads to warping and violation of the geometry of the entire product. Therefore, if there are strict requirements for the shape and design deviations, it is subjected to pressure treatment in order to correct the defect.
Also, pressure treatment can be used to harden the surfaces of the restored product, for example, after surfacing or after mechanical removal of a certain allowance from the part by cutting. Hardening by deformation is a rather rare way of restoring parts. The choice in favor of this technique is extremely rare. This is due to the fact that rather expensive equipment is required for hardening by surface plastic deformation. It is not economically feasible to purchase such machines in order to occasionally use them in case of need for restoration.
The essence of strain hardening. Physicsprocess
Due to what the strength qualities are improved when the surface layer is deformed? Good question. The answer lies in the radiation theory of the atomic structure of crystalline substances.
Scientists managed to prove that the strength depends on the number of defects in the crystal structure. According to their calculations, a thin metal thread made of perfectly pure iron without point and linear structural defects is capable of withstanding enormous loads. However, real bodies always have defects, so the bearing strength of such a wire under real conditions is quite small. But when the number of defects increases, a paradoxical phenomenon arises - the strength characteristics improve. This is due to the fact that a large number of defects creates obstacles for their movement and exit to the surface of the grains, that is, it prevents the occurrence of stress concentrators.
This is exactly what the hardening effect of pressure treatment is based on: during deformation, a huge number of defects occur inside the grains. In this case, the grains themselves acquire a characteristic shape - the so-called texture. It should be noted that this method allows not only to increase strength and wear resistance, but also to reduce the roughness of the machined surface.
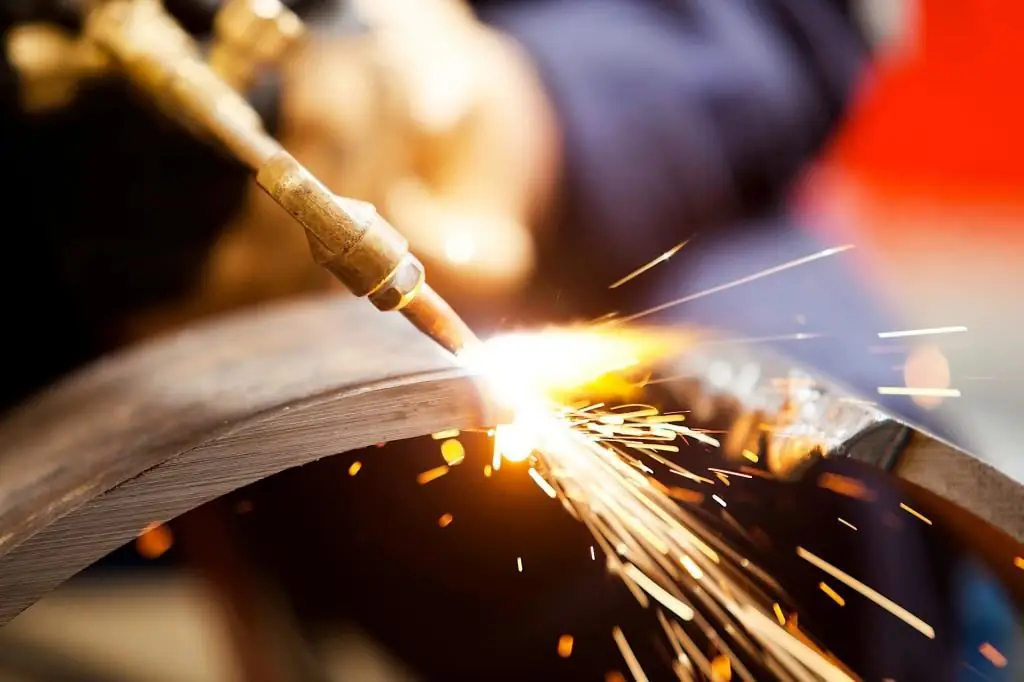
Method of restoring parts by surfacing
This method is the most common when restoring the original dimensions of a part. The reason for this is the relative cheapness and simplicity. To restore the geometry of the product, you only need a weldingapparatus and necessary material for surfacing.
In the event that the size is very broken, then the so-called combined surfacing is used. Its essence is as follows: first, ordinary steel or cast iron is applied by means of gas-flame or electric-arc heating. And only then is the electric arc surfacing of a strong alloy with a good set of mechanical and physical properties. The surface quality after surfacing can be described as unsatisfactory, so an allowance is necessary. This operation can be carried out on a lathe, milling or boring machine. The use of chiseling and abrasive tools is also allowed (if the deposited material is very hard).
Galvanic methods in parts restoration
When considering the classification of methods for restoring parts, one cannot fail to mention electroplating. This method is very common. Electroplating baths have long been firmly established in the industry and are actively used both in manufacturing plants and in research laboratories. The scope of their application is incredibly extensive: from applying decorative coatings to etching materials.
As a rule, this method is applicable only with a slight degree of wear of rubbing surfaces, since the thickness of the galvanized coatings is very small. In addition to restoring the specified dimensions, such a coating can act as a protective film and prevent corrosion and oxidation of materials.
The advantage of this method is the possibilityobtaining coatings using a variety of materials: nickel, chromium, aluminum, iron, copper, silver, gold, and so on. Therefore, electroplating is used in many sectors of the national economy.
Characteristics of thermal and chemical-thermal treatment methods in the restoration of products
It is difficult to exaggerate the role of heat treatment in general in mechanical engineering, and in the field of restoration of parts in particular. It allows you to obtain the necessary operational (wear resistance, hardness) and technological (machinability, thermal conductivity) qualities.
Chemical-thermal treatment is a separate issue. Unlike traditional heat treatment, in the course of chemical treatment, the product is subjected not only to temperature, but also to a chemical reaction with atoms and ions of other substances. Atoms diffuse to a certain depth inside, thereby changing the chemical composition of the surface layer. The properties of the diffusion layer are significantly different (for the better) from the original material. So borating (saturation with boron atoms) and carburizing (saturation with carbon atoms) significantly increases hardness and helps to reduce the coefficient of friction. In practice, silicon, nitrogen, aluminum and other elements are also used as saturating elements.
Conclusion
The above description of the ways to restore parts is not exhaustive. Only the basic and most common methods are presented. All in all, there are many more of them. Moreover, scientists around the world are constantlyare working on the creation of new and improvement of already known methods of applying coatings and restoring the geometric dimensions of parts.
Recommended:
Types of auctions, their classification, characteristics and conditions
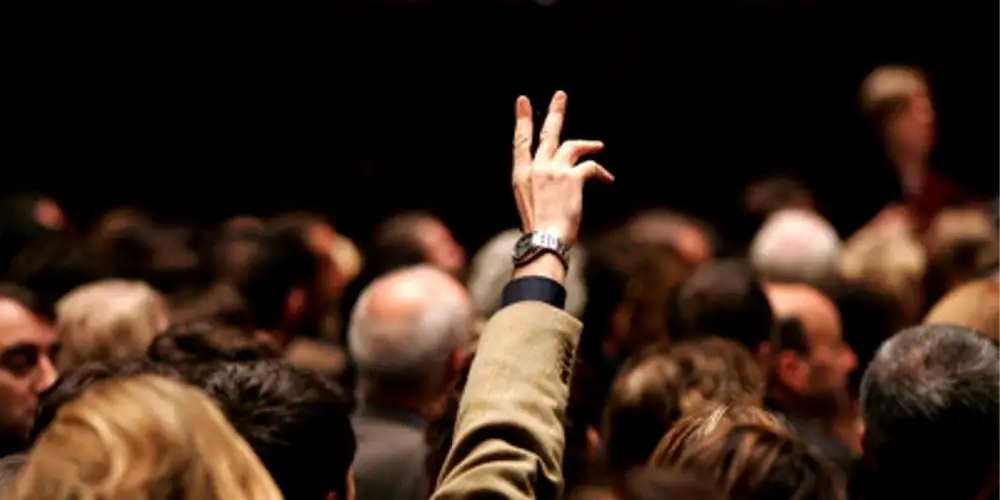
What is an auction, what types of auctions exist. How to participate? What are the rules? Is it possible to refuse a purchase and what will happen for it? Let's try to figure it out
Automatic lathe and its characteristics. Automatic lathe multi-spindle longitudinal turning with CNC. Manufacturing and processing of parts on automatic lathes
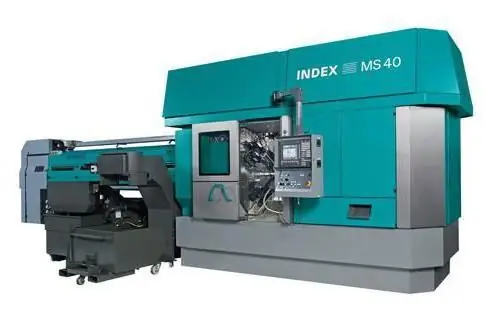
Automatic lathe is a modern equipment used mainly in mass production of parts. There are many varieties of such machines. One of the most popular types are longitudinal turning lathes
Classification of excavators, their technological characteristics and purpose
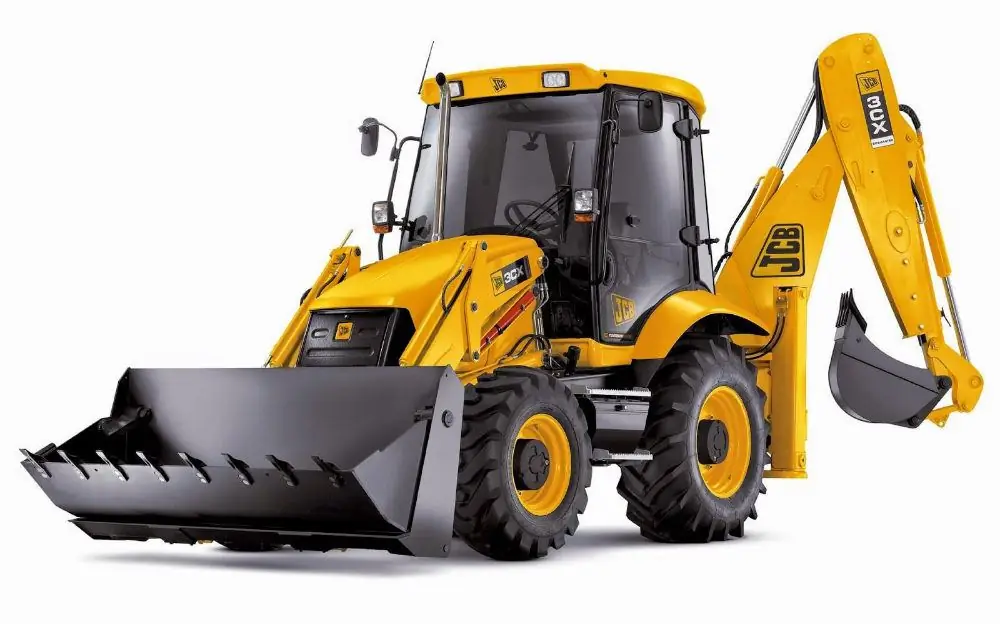
Currently, people use a large number of the most diverse techniques. This type of equipment, such as excavators, is now very popular, as earthworks are significantly accelerated and not only. The classification of excavators is quite extensive and it is worth considering
Reserves of banks and their formation. Required bank reserves and their norm
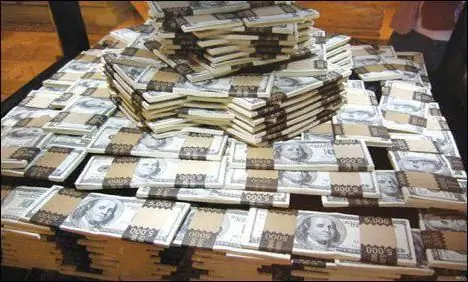
Bank reserves ensure the availability of funds for the uninterrupted fulfillment of payment obligations regarding the return of deposits to depositors and settlements with other financial institutions. In other words, they act as a guarantee
Chrome plating parts. Chrome parts in Moscow. Chrome parts in St. Petersburg
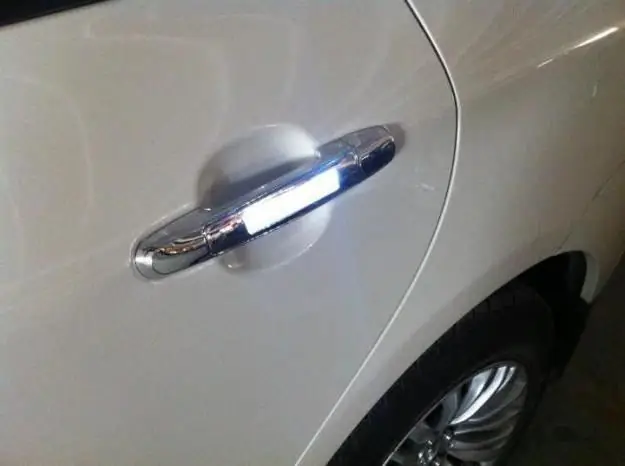
Chrome plating of parts is an opportunity to give them a new life and make them more reliable and of high quality in operation