2025 Author: Howard Calhoun | [email protected]. Last modified: 2025-01-24 13:10
A lathe is a special machine, the processing of parts on which is carried out without the participation of a worker. This type of equipment is more expensive than usual. However, it is also considered more convenient to use. All operations on such machines are performed automatically. The worker only monitors the loading of blanks and controls the quality of manufactured parts.
Varieties of machine tools
There are several types of such equipment. Parts can be manufactured on single-spindle or multi-spindle automatic machines. Structurally, they differ little. The only difference is that on equipment such as single-spindle lathes, turning is performed using only one working tool. There are several of them in the design of multi-spindle machines. According to the type of workpieces, all lathes are divided into:
- screw-cutting;
- carousel;
- face turning;
- turning-milling;
- turret turning;
- longitudinal turning.
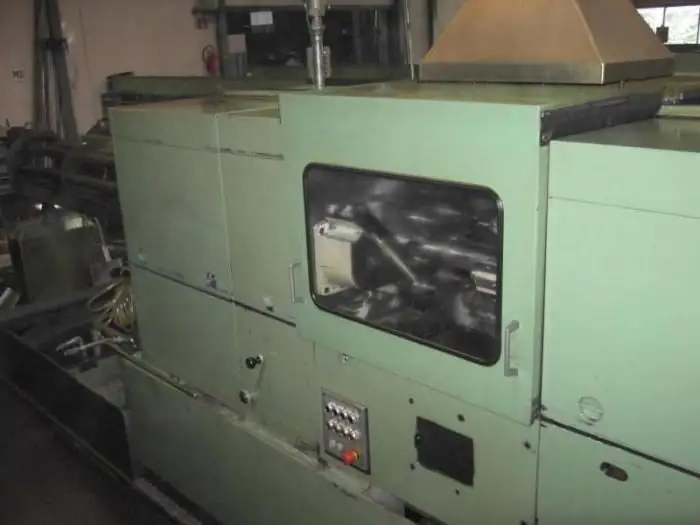
Screw-cutting machines are used to perform all types of turning operations, carousel - to process workpieces of large mass. Face turning machines are used for turning cylindrical, frontal and conical products. Milling equipment is used for relief processing. Turret lathes are used for the manufacture of parts of complex shape. About what longitudinal section machines are intended for and what are the features of their design, we will discuss in detail below.
Assignment of automatic lathes
As with conventional machines, this type of equipment performs work such as:
- longitudinal turning of cylindrical and stepped surfaces;
- outer bevel processing;
- grooving, facing and shouldering;
- boring holes;
- drilling;
- thread cutting;
- grooving;
- profile turning.
General design features
All automatic and semi-automatic lathes, as well as conventional machines, are therefore designed to remove certain parts of the workpiece while rotating the latter. By design, different types of this equipment can vary greatly. However, the main features for most types are common. The design of any lathe includes: a bed,front and rear headstock, carriage. The latter is designed to hold the tool and move it in the right direction. A special feed mechanism is responsible for this process.
On the headstock of such equipment as an automatic lathe, a spindle and a speed change mechanism are attached. It is fixed very firmly, as it can cause vibrations that are transmitted to the workpiece and reduce the quality of the finished part. The spindle in the headstock is fixed on bearings and equipped with special clamping devices (loops or chucks). It is driven by a separate electric motor through a gearbox.
Beds in lathes can be used different (inverted, V-shaped, flat). This structural element should be located as accurately as possible. Any deviations lead to a significant reduction in the quality of manufactured products.
The tailstock is used to support long workpieces while turning. It is usually located along the table and fixed in the most convenient position for manufacturing the part.
Lathes can be automated using a controller or a mechanical command device. Equipment of this type differs from simple CNC machines in that the workpieces in this case are also automatically fed for processing. CNC such machines can be equipped additionally.
The difference between automatic machines and conventional machines
Works on machines of this type can thus be performed the same as on simple turning equipment. The difference lies in the fact that the turning of partson automatic machines it is made according to the rigidly set cycle. On a conventional machine, a worker, having completed the manufacture of one part, can immediately begin turning another. On the machine, the cam changeover takes several hours, and preparation for it takes several days.
Use area
Automatic lathes are much more productive than conventional machines. Since their frequent changeovers lead to a loss of production time, this equipment is usually used in large-scale production. In addition, since such equipment is quite expensive, it is advisable to use it only if there is a need to manufacture parts of very complex shapes with a large number of transitions. Very often, enterprises use highly specialized machines of this type, designed to produce one part or a small group of products.
Multi-spindle machines
This kind of automatic turning equipment is used in factories to mass-produce parts of various shapes and sizes. In this way, such machines differ from single-spindle machines, which are used mainly for the production of serial identical products. There are two types of such machines:
-
Horizontal. The main advantage of such machines is the convenience of loading the source material. Therefore, they are used where continuous bar feed is used.
- Vertical. The advantage of multi-spindle machines of this variety is considered to be small size. Places indoor equipmentthis type does not take too much.
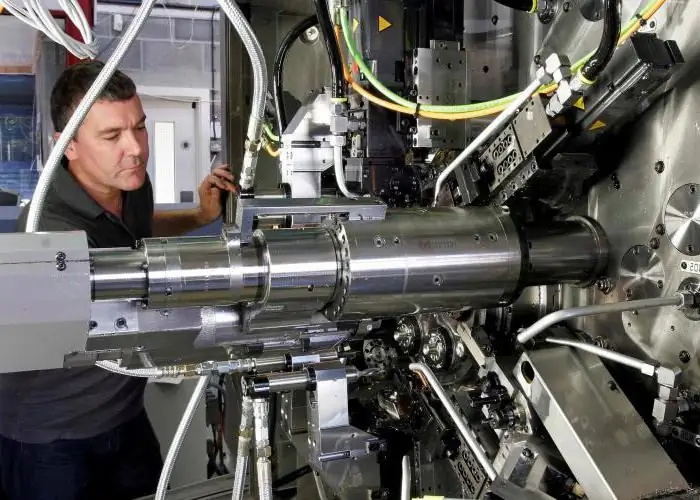
Multi-spindle automatic lathe can sometimes be used in small-scale production. But only if equipped with a CNC.
Longitudinal turning machines
Equipment of this type has recently become more and more popular. Longitudinal turning machines are used for the manufacture of mostly small parts of a very complex shape. A distinctive feature of their design is the presence of a movable spindle headstock. The type of clamp in such machines is used collet. The counter spindle in sliding head machines is mounted on high-precision linear guides.
A feature of the machines of this variety, among other things, are small dimensions. Their working area is also not too extensive. Machines of this type usually operate at a very high speed.
The automatic longitudinal turning lathe can be used in both mass and mass production of parts. Most often, equipment of this type is used in the optical, electrical and instrument-making industries. The cutters in such machines are mounted in calipers and move only in the horizontal direction. In production, longitudinal turning machines are used, both single-spindle and multi-spindle.
Sliding turning automatic lathe is designed to perform operations such as:
- turning steps;
- grooving and coning;
- boringshallow holes;
- treatment of shaped surfaces;
- threading internal and external;
- reaming holes;
- knurling of outer surfaces;
- milling slots for screws;
- drilling.
Surfaces on automatic machines of this type can be processed very different: conical, cylindrical, stepped, etc. To expand the capabilities of longitudinal turning machines, all kinds of additional devices are used. For example, the use of gear levers reduces wear on the cams and pusher shoes.
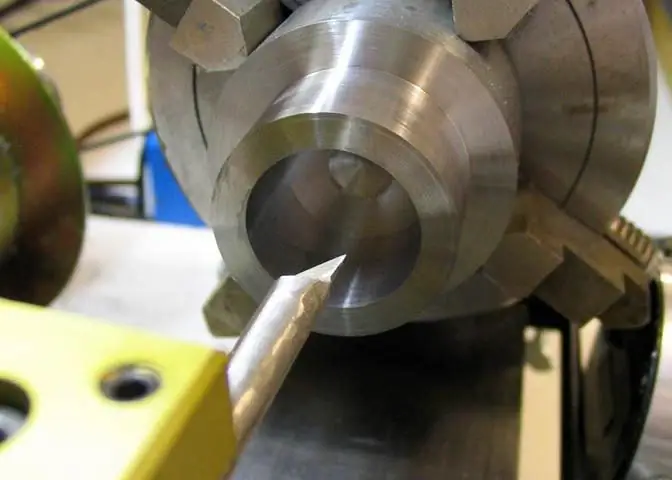
Design features of longitudinal turning machines
The headstock of such machines is fixed on the upper plane of the bed. Ahead of it there is a special plate designed to install additional devices. A vertical caliper is installed on its upper plane, and a swinging stop is installed on the back. Equipment such as a longitudinal lathe is controlled by a system of cams and camshafts fixed in the frame.
Key Benefits
The advantages of longitudinal turning machines primarily include:
- possibility of obtaining shaped and conical surfaces when using prismatic cutters;
- smooth quality finished product surface;
- possibility of milling both along the axis of the part and acrossher;
- ability to roll small numbers, signs and letters.
Machining parts on automatic lathes of this type can be done with maximum precision.
Working principle
In the process of processing, the source material on such machines is given not only rotational motion, as on conventional ones, but also translational - along the axis. The cutters themselves in equipment such as sliding bar lathes move only perpendicular to the bar. The radial forces arising during the machining process are taken up by the steady rest. This eliminates all kinds of vibrations and deflections and, accordingly, ensures high machining accuracy.
The cycle of movement of the headstock and tools in automatic longitudinal turning machines is set by cams tuned specifically to this particular part. The latter are mounted on a special shaft, the number of revolutions of which can vary even at a constant spindle speed.
Maintenance of Swiss Machines
In operation, this type of machine is simple. However, of course, they require some care. For example, in order for the cooling system to function smoothly, it needs to be periodically changed oil. It is also recommended to rinse the liquid bath monthly. The design of the cooling system also includes a filter, which should be cleaned at the same frequency. These recommendations must be followed. Repairing a lathe is expensive.
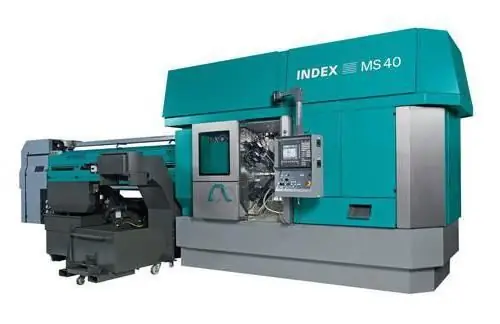
CNC machines
As already mentioned, machines designed for the manufacture of metal parts can be additionally equipped with CNC. Such control systems are usually used if the automatic lathe is intended for the production of parts in mass or small-scale production. The software used in the CNC allows:
- automate the processing process;
- improve the quality of machined parts;
- significantly reduce machine setup time.
Different types of drives and converters in the CNC are used digital. They are electric motors that run on either AC or DC. When using the CNC, special sensors are built into the kinematic scheme of the machine. The working tool in machines equipped with CNC is used as durable as possible, as they operate at a very high speed and productivity. The base structure of such machines must be extremely rigid.
CNC multi-spindle longitudinal turning machine
Actually, the numerical software itself is nothing more than a computer system with special software installed on it that controls the drives of the machine. Usually the standard equipment of CNC machines is as follows:
- spindle;
- cooling system;
- counter spindle;
- lighting for work area;
- machine ejection sensor;
- sleeve variable;
- special device designed to receive finished products;
- tools for external and internal turning;
- front and transverse driven tools;
- the CNC system itself.
Simple lathes multi-spindle longitudinal turning without CNC are mainly used for mass production of a large number of various kinds of small parts, most often long and small sections, complex shapes. The latter usually serve as structural elements of modern medical and laboratory equipment, electronics, watches, etc.
Installing CNC on such machines also allows you to produce a large number of products, but not the same, but different shapes (that is, in small batches). Ordinary automata are most often set up to produce a particular part, and only once. The fact is that the mechanical "reprogramming" of this type of equipment, as already mentioned, is an extremely complex and lengthy procedure. The downtime of production during changeover greatly affects its profitability. Therefore, the use of conventional machines for the production of small batches of parts of various shapes is considered inappropriate.
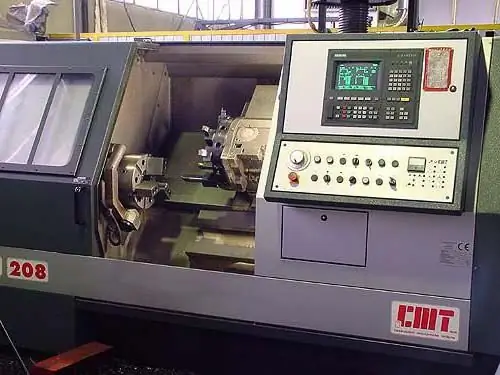
CNC installation helps to solve this problem and combine the advantages of the machine with the possibility of expanding the range of manufactured products. If the machine has a numerical control system, you can reconfigure itvery fast. For example, the change of the cutting insert is carried out directly on the machine itself without removing the holder. To change the speed of rotation of the tools and the order of their work, you only need to enter certain values in the program window on the CNC computer.
Production of parts on CNC lathes: features
Participation of the worker when using machines of this type is reduced to a minimum. All that is required from a specialist is to monitor the smooth operation of the equipment. Of course, the quality of products in this case directly depends on the accuracy of setting the machine. Therefore, NC programs must be as thoughtful as possible.
The main task of those industries that use equipment such as CNC automatic lathes of longitudinal turning is to produce parts with precisely specified parameters and at the same time low cost. The bars used as starting material on such machines usually do not have a very geometric shape (even calibrated). At the same time, all errors and inaccuracies can be easily transferred to the finished part. After all, working tools, of course, cannot arbitrarily change their position or speed of rotation without human intervention. This feature of cutting on automatic machines is called "heredity" and is the main problem for technical programmers of enterprises. It is usually solved by reducing the speed of processing modes along the entire cutting length. Which, of course, leads to an increase in the cost of products due to an increase in time costs.
Meanwhile, it is possible to get rid of "heredity" with minimal losses using special modern CNC application programs developed taking into account the dynamic characteristics of the processing system that determine it. Their use allows you to set the most accurate cutting mode with a reduction in time loss by more than two times.
Top brands
Thus, the correct adjustment of the Swiss-type lathe using CNC programs allows you to make the production of small parts as cost-effective as possible. But of course, only if the equipment itself is of high quality. Repair of automatic longitudinal turning machines with CNC is complex, expensive and time consuming. Therefore, the choice of such machines is a very serious and responsible matter.
When buying equipment such as an automatic lathe, first of all, you should pay attention to its manufacturer. For example, CNC multi-spindle longitudinal turning machines of the following brands deserve good reviews:
- Tornos of the MultiSwiss series.
- LA155F30.
- HJM SQC38.
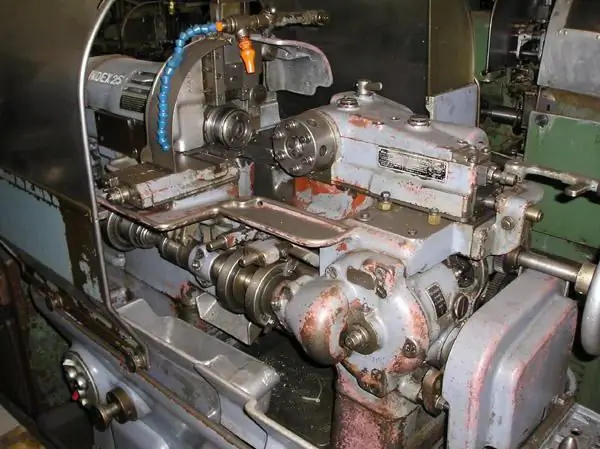
Tornos machines
The advantages of the MultiSwiss series of machines include, first of all, high productivity and a relatively simple design. The Tornos multi-spindle CNC lathe is quite easy and quick to set up and reconfigure. In order to work on such a machine, you do not need to be a specialist in multi-spindle machines. Controlproduced entirely by CNC. The technical characteristics of the machines of this line are presented in the table.
Parameter | Meaning |
Number of tool carriers | 7 pcs |
Max bar diameter | 14mm |
Maximum workpiece length | 40mm |
Number of spindles | 6 pcs |
Maximum spindle speed | 8000 rpm |
Power | 5.6 kW |
Maximum torque | 7.5 Nm |
Number of counter spindles | 1 pcs |
Maximum counter spindle speed | 8000 rpm |
Power of counter spindle | 5 kW |
CNC system | Fanuc |
Weight of the machine | 7000 kg |
Dimensions | 1440x5920x2120mm |
LA155F30 models
Three-spindle automatic lathes of this brand belong to the accuracy class "B". The main advantages of LA155F30 machines are reliability and long service life. Even after a longusing these machines allow you to process parts with maximum precision. In addition, LA155F30 machines are not too expensive and maintainability.
The characteristics of automatic lathes of this manufacturer are as follows:
- diameter of processed bar min/max - 6/16 mm;
- maximum product length - 160mm;
- main spindle speed - 80-8000rpm;
- electric motor power - 5.5 kW;
- machine weight - 2270 kg;
- dimensions with attachments - 5600x900x1720 mm.
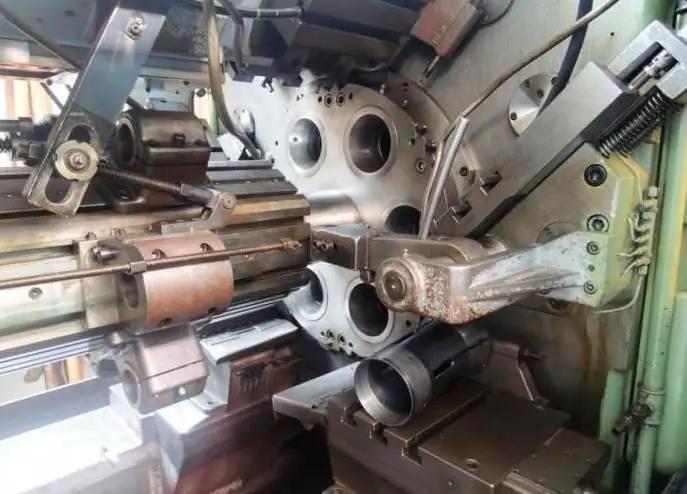
HJM SQC38 machines
This brand's multi-spindle automatic lathe also ensures maximum precision in machining parts. This equipment is intended for high-speed processing of parts (longitudinal turning and milling). Below are the specifications of HJM SQC38.
Parameter | Meaning |
Number of driven tools | 6 pcs |
Max bar diameter | 38mm |
Maximum product length | 210mm |
Drive tool speed | 4000 rpm |
Spindle speed | 8000 rpm |
Machine weight | 4500 kg |
Dimensions | 2100x1450x1700 mm |
Conclusion
Thus, modern CNC longitudinal turning machines are very convenient, productive and, in most cases, reliable equipment. The most important thing in its operation is to use the most thoughtful software. This will increase the profitability of production and produce quality products with accurate dimensions.
Recommended:
Turning various parts
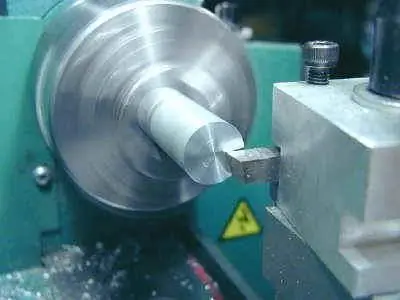
Turning today allows you to make a variety of products. This production uses both wood and metal
Meat: processing. Equipment for meat and poultry processing. Production, storage and processing of meat
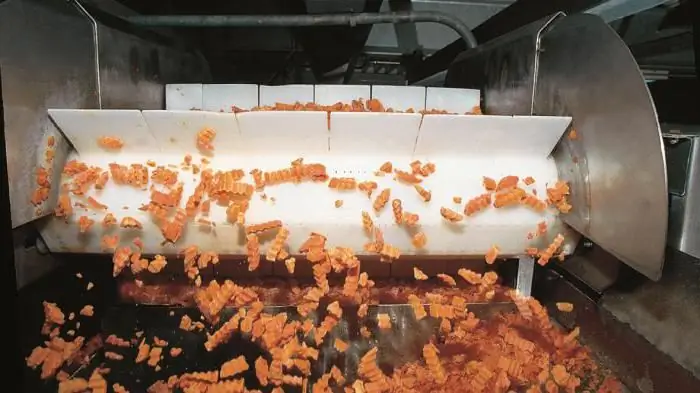
Information of state statistics show that the volume of meat, milk and poultry consumed by the population has significantly decreased in recent years. This is caused not only by the pricing policy of manufacturers, but also by the banal shortage of these products, the required volumes of which simply do not have time to produce. But meat, the processing of which is an extremely profitable business, is very important for human he alth
Cutting speed for milling, turning and other types of mechanical processing of parts
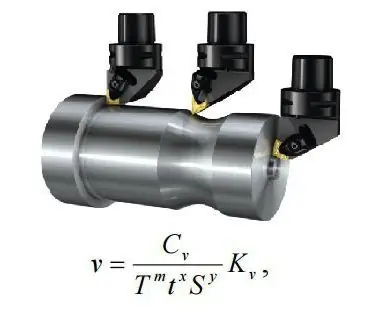
Calculation of cutting conditions is the most important step in the manufacture of any part. It is very important that the calculation itself be rational. This is due to the fact that for various mechanical operations it is necessary to individually select the cutting speed, spindle speed, feed rate, and also the depth of cut. A rational mode is one in which production costs will be minimal, and the quality of the resulting product will be as accurate as possible
Lathes 1K62: device, characteristics, repair and operation
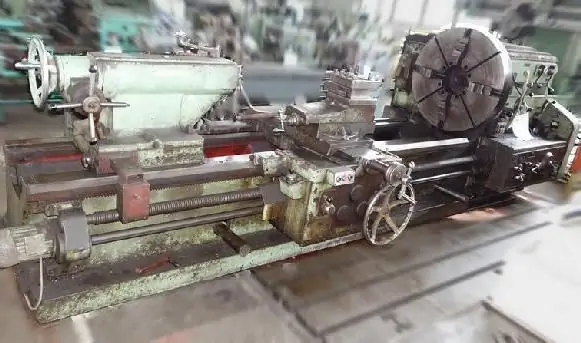
1K62 lathes are reliable and productive devices designed mainly for use in individual and small-scale production. They can be used for processing parts made of various structural materials: non-ferrous and ferrous metals, cast iron, etc
Chrome plating parts. Chrome parts in Moscow. Chrome parts in St. Petersburg
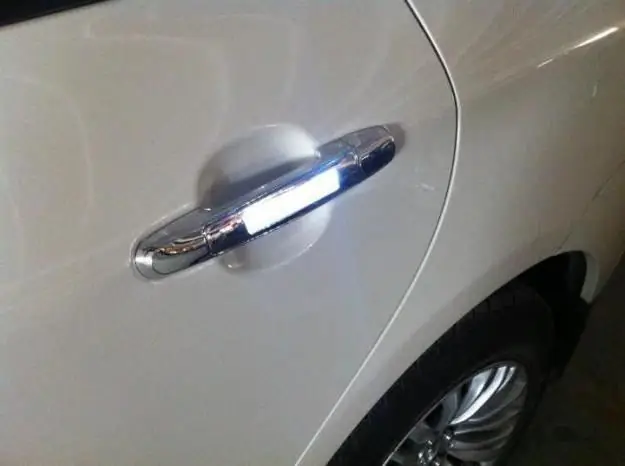
Chrome plating of parts is an opportunity to give them a new life and make them more reliable and of high quality in operation