2025 Author: Howard Calhoun | [email protected]. Last modified: 2025-01-24 13:10
One of the most popular tools in metal machining is a cutter. It allows you to perform many technological operations. In this article, we will consider a turning tool for metal, its constituent elements, classification and purpose.
Composition elements
There are a huge number of different cutters, and they all consist of two parts: a holder and a working part.
The first is designed to fix the cutting tool in a metal-cutting machine, and the second is used to process the required surface.
Depending on the type of cutter, it can be either solid or prefabricated. From the name it becomes clear that the latter is not completely cast, and the working part of the tool has a mechanical fastening of a replaceable plate. When one of the cutting edges is ground, the insert is unscrewed and turned over. If the turning tool for metal is one-piece, then when the cutting edge is dull (the so-called wear), it must be re-sharpened or soldered.
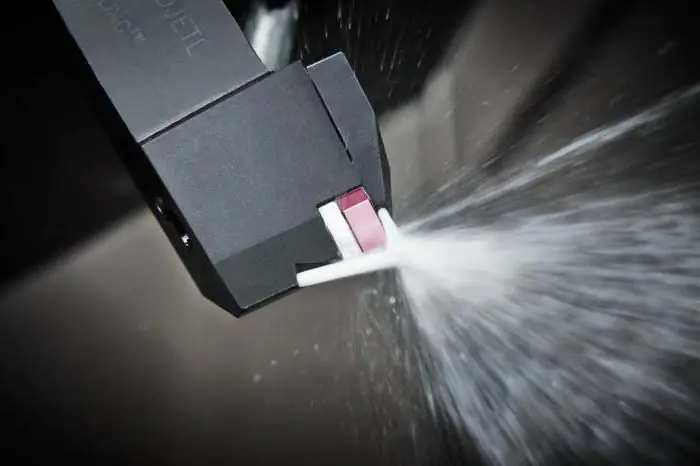
Installation and operation method
Veryit is important to correctly install the cutter in the tool holder, since the quality of the resulting product and the wear rate of the working tool will depend on this. It must be fixed so that the top is on the line of the center of the machine. The method of operation of a turning tool for metal is quite simple - it cuts off the necessary layer of metal. To do this, the cutter is brought to the part fixed in the chuck and rotating at the required speed. As a result, chips are formed from the removed layer. For rough turning, the machining allowance is chosen much more than for finishing. In addition, be aware that if the feed is too high, the surface quality of the part may be significantly reduced.
Classification
As mentioned earlier, there are a huge number of different incisors.
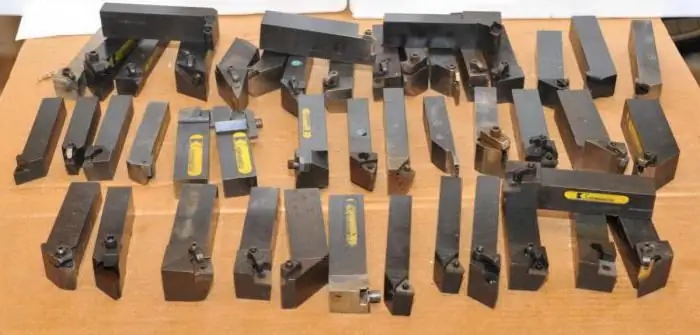
They are classified:
- By purpose: for turning external conical and cylindrical surfaces - through passage, for boring holes - boring, for cutting - cutting. With the help of a turning tool for metal, you can cut threads, turn shaped and transitional surfaces, and machine annular grooves.
- According to the material of manufacture. The thing is that the cutting part of the tool must have increased hardness, high toughness, wear resistance and red hardness. It is for this reason that the so-called rapids are used for the manufacture of certain types of turning tools - these are high-speed steels P9, P12, P6M5 and the like. Another group is tungsten-cob alt alloys VK8, VK6. The third group -tool steels U11A, U10A, U12A.
- According to design parameters: solid and prefabricated, straight and bent, drawn and curved.
- According to the shape of the section: round, square, rectangular.
- According to the quality of processing: roughing (cutting off), semi-finishing and finishing (through passage).
Destination
Cutters are used on lathes, slotters, planers, carousels and turrets. Their design allows you to perform a variety of operations: turning, boring, cutting, cutting external and internal threads, chamfering, chiselling, hole making, etc. It is also interesting that prefabricated turning cutters, the plates of which are made of carbide metals, may differ.
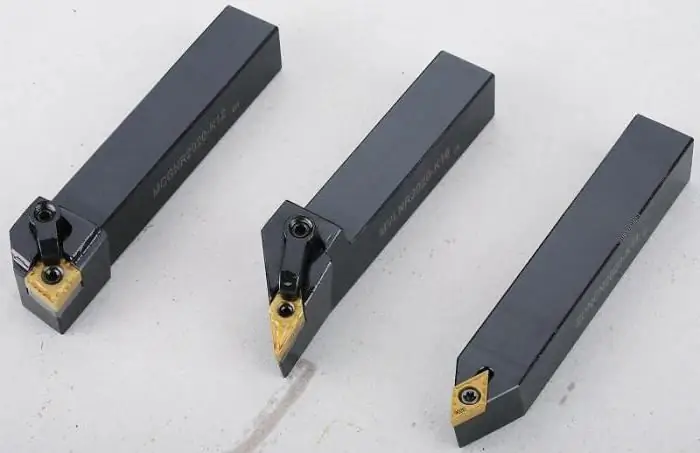
This is very convenient. On the same holder, you can alternately attach different cutting parts and get a completely different tool. In addition, their use helps to avoid such operations as soldering and sharpening. This greatly facilitates the work and increases the life of the tool. In order to correctly perform this or that operation with the help of a cutter, the cutting conditions for each pass are calculated. They must take into account the type of cutter and its material. It is from the calculations obtained that the cutting speed, the feed rate during turning, boring and other operations using this cutting tool depend.
Recommended:
Pyrotechnic composition: classification, components, application
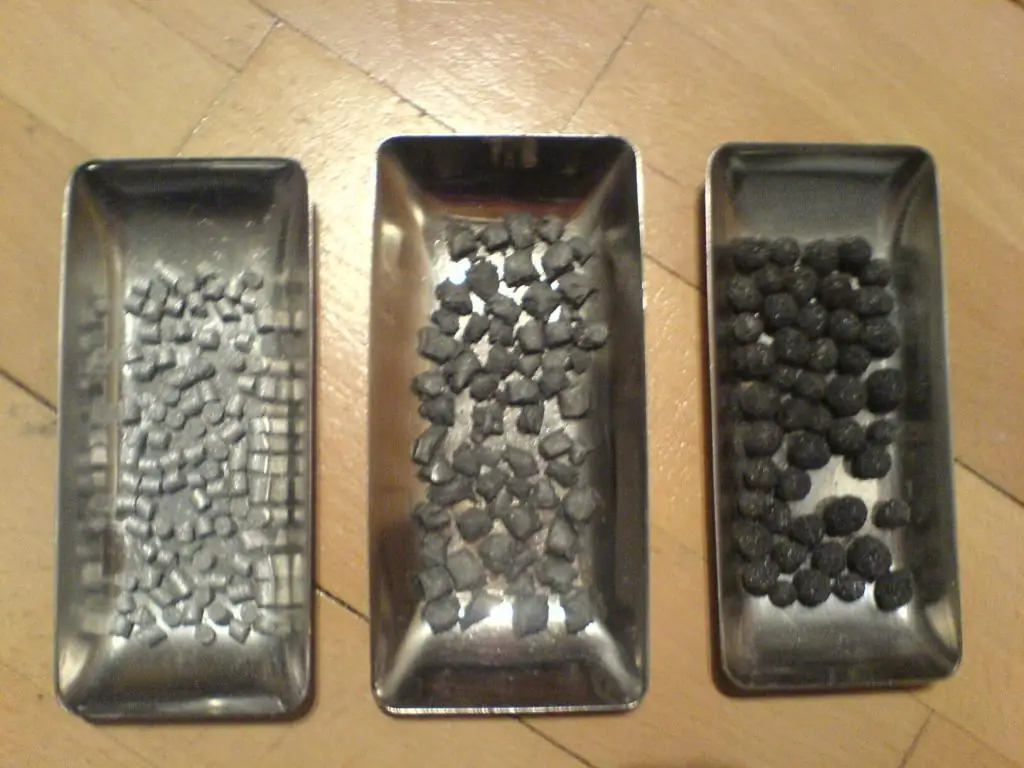
A pyrotechnic composition is a substance or mixture of components designed to produce an effect in the form of heat, light, sound, gas, smoke, or a combination thereof, as a result of self-sustaining exothermic chemical reactions that take place without detonation. A similar process does not depend on oxygen from external sources
Automatic lathe and its characteristics. Automatic lathe multi-spindle longitudinal turning with CNC. Manufacturing and processing of parts on automatic lathes
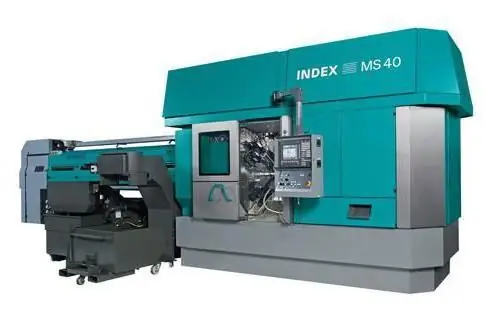
Automatic lathe is a modern equipment used mainly in mass production of parts. There are many varieties of such machines. One of the most popular types are longitudinal turning lathes
Tool shop: description and purpose
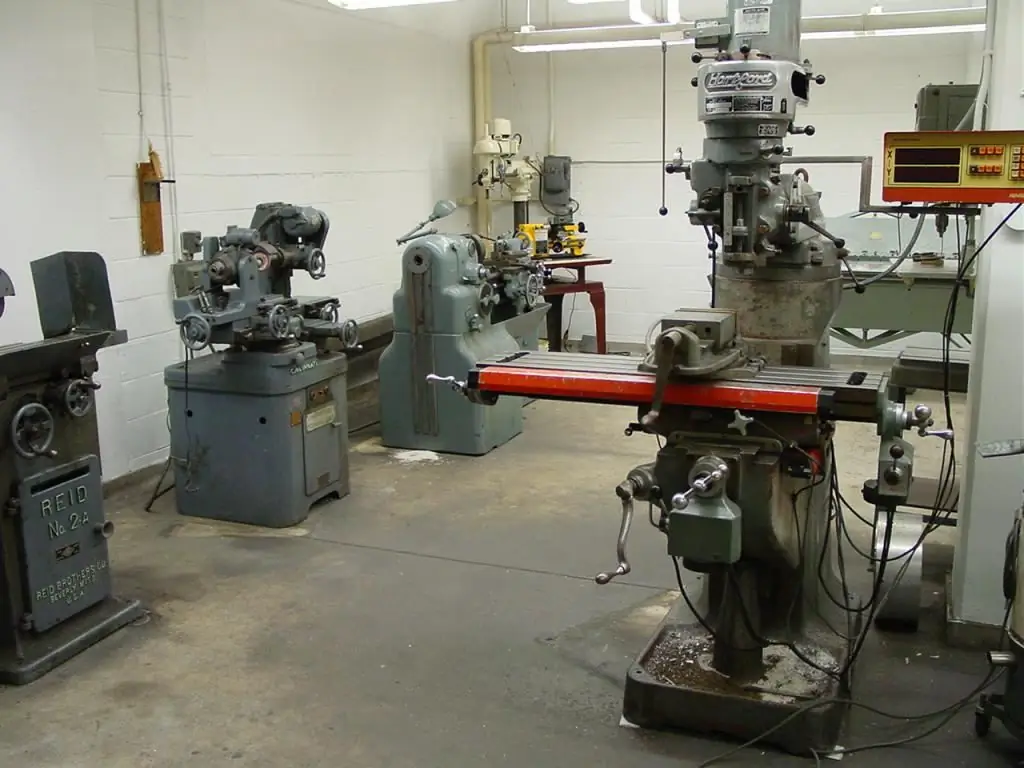
The tool shop, which is located on the territory of the machine-building plant, is an auxiliary site. The main purpose of this department is the manufacture, as well as the repair of equipment that is used at this machine-building plant
Mineral wool density: classification, advantages and disadvantages, purpose of mineral wool and application
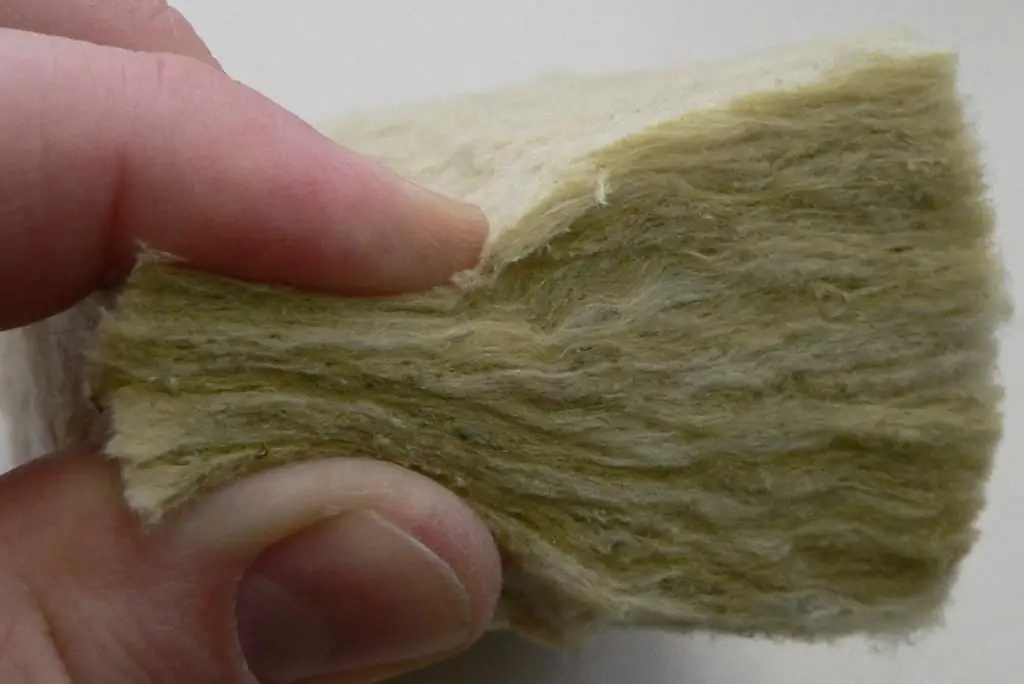
Mineral wool is the most popular type of insulation for an apartment or house. Today it is used by everyone, from builders to the owner of the apartment, who wanted to insulate the room. The simplicity of its installation allows you to immediately insulate the entire house (ceiling, walls, floor). We will study the features and characteristics of the named material further in the article
Equipment for agriculture: classification and types, purpose and application
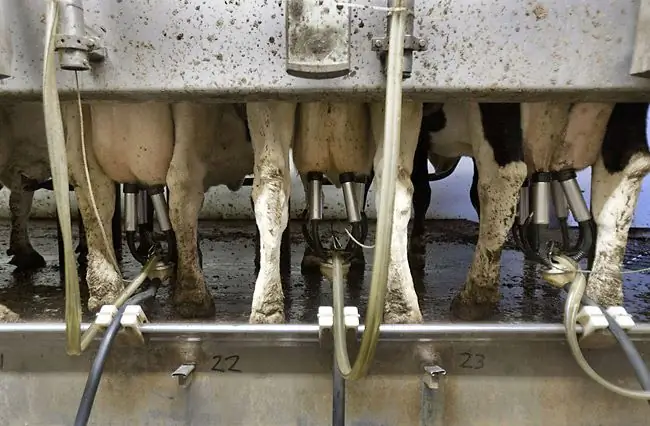
Modern industry produces a variety of equipment for agriculture. It can be, for example, soil-cultivating equipment, as well as fodder, harvesting or sowing. Of course, tractors are also widely used on farms