2025 Author: Howard Calhoun | [email protected]. Last modified: 2025-01-24 13:10
Edwards (or Edward) Deming is a well-known American consultant on the theory of quality management, as well as the creator of the "lean manufacturing" system and the 14 principles of quality improvement. This man made a huge contribution to the development of management and economics. Although he mainly worked in Japan, his works are popular all over the world. Many companies use the principles and suggestions developed by Deming to develop and improve the quality of their production.
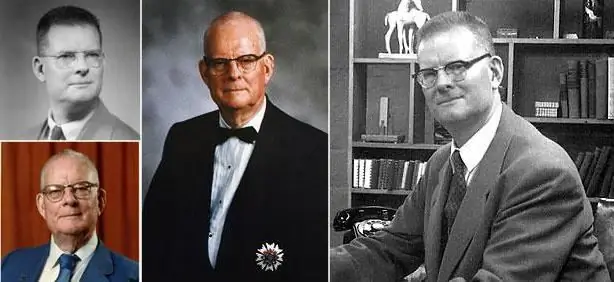
Deming's Life
Back in 1900 in the USA, in the state of Iowa, the future scientist Edward Deming was born. The biography of this person is rich in awards and prizes that he received for his contribution to the development of statistics and management. Deming Edward devoted sufficient time to training. He was educated at the University of Wyoming (in 1972 he received an award as the most outstanding student of this university), Colorado, Yale University. Over the years, Edward Deming received degrees in physics, mathematics and electronics.
Before starting work in Japan, in 1946, Demingtaught physics at the Colorado School of Mines (1923-1925) and worked for the US Department of Agriculture (1927-1939). Working in Japan became the peak of his career and made him famous all over the world. In addition to her, Edward Deming consulted in Greece, India, Argentina, Mexico, France and other countries. In the period 1947-1952 he was a member of the UN subcommittee on statistical samples.
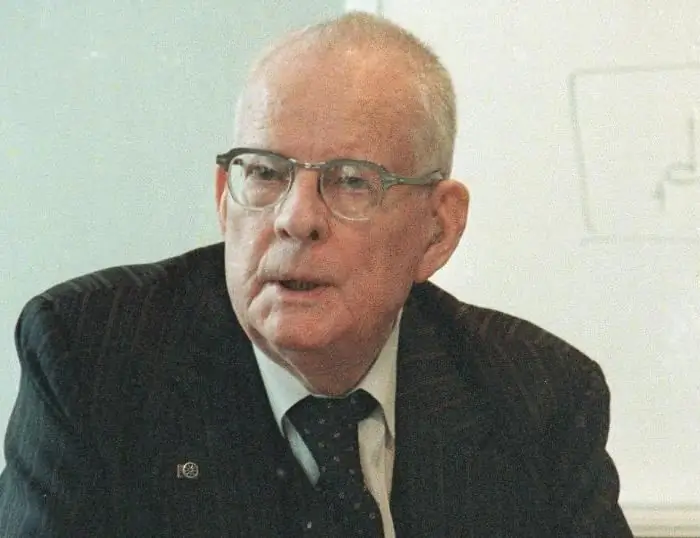
After arriving in Japan, Deming had practically no connections, except for one statistician, Ishikawa Kaoru, who taught at the University of Tokyo. By a happy coincidence, his father was the head of an influential organization called the Federation of Economic Organizations of Japan (Nihon Keidanren). It was he who helped organize the first Deming seminar in 1950, which was attended by the leaders of the 21st company. These companies accounted for 85% of Japan's national capital.
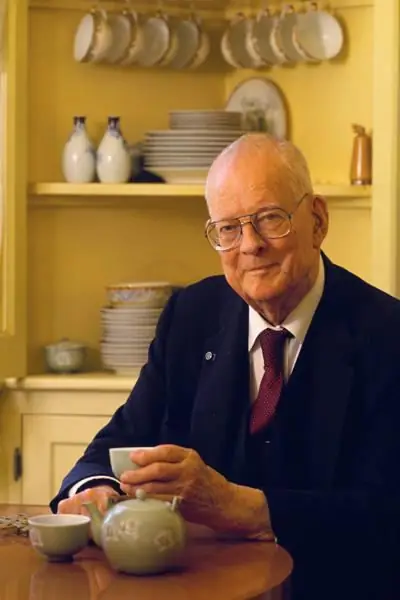
The seminar was a success, and after it Deming became a leading consultant for large companies in Japan.
Edward Deming did not stop his work until his death in 1993. In the United States, his ideas were recognized only in 1980. Despite his already advanced age, the scientist continued to work and advise the heads of large companies both in the United States and other countries of the world.
Deming's career and success were not easy at the beginning of his career as a scientist, but he was able to ensure that he was recognized all over the world and not forgotten after his death. Deming's works and teachings are relevant to specialists today.
Family
In 1922, Edward Deming married for the first time. His family with Agyness Bell did not last long, until 1930. Well-being was interrupted by the sudden death of his wife.
Two years later, the scientist remarried Lola Shoop. This time, family happiness lasted for 52 years, until Lola's death in 1984. From two marriages, the scientist left three daughters. All three and Edward Deming (pictured below) were no doubt a strong and loving family. His daughters gave him seven grandchildren, and then five more great-grandchildren.
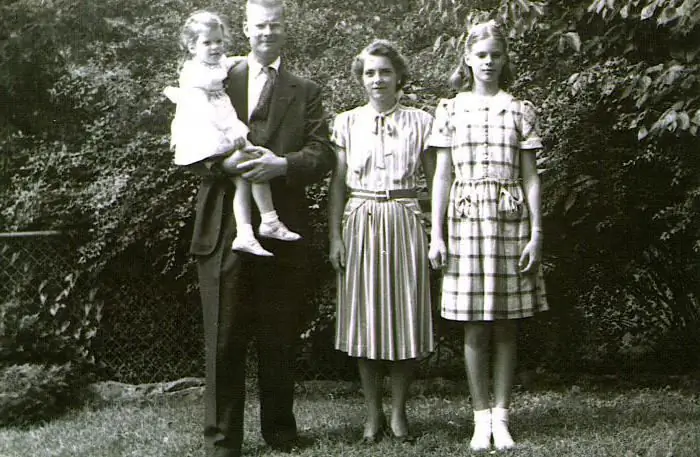
Proceedings of a scientist
During his career, Edward Deming made an unprecedented contribution to the development of management. His books have received recognition and popularity. To date, three of his books have been published in Russian:
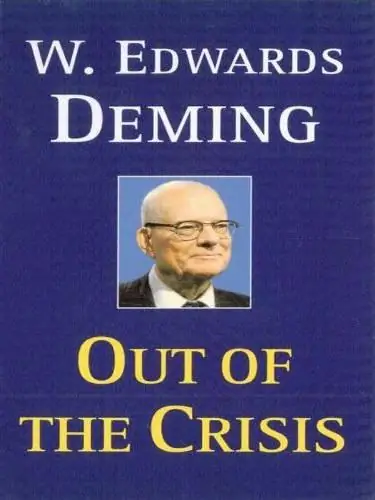
- "Out of the Crisis: A New Paradigm for Managing People, Systems and Processes".
- "Out of the crisis".
- "New economy".
Edward Deming made a huge contribution to the development of the Japanese economy. The "new economy" just tells that "western" business principles are already outdated and the economy is entering a new era with new rules of the game.
Awards
Deming has received worldwide recognition and respect over the course of his career. His contribution to the development of management and economics is confirmed by a number of awards:
- Order of the Blessed Treasure of the second degree (received in 1960 in Japan).
- National Medal of Technology (received in the USA in 1987).
- His namecarved on a wall at the Dayton Hall of Fame (1986).
- Distinguished Career in Science Award (received in the USA in 1988).
Also in Japan in 1951, an award was approved that bears the name of a scientist. It is given to people who have contributed to the development of the theory and practice of quality management.
Deming and his quality tips
It took Americans 30 years to appreciate Deming's work and recognize its relevance. The 14 principles of Edward Deming have become known and recognized only recently, although they were formulated back in 1980.
Deming began working on these management rules after the end of World War II. Despite the fact that quite a lot of time has already passed since the moment of the emergence of this idea and the final formulation, Deming's principles are still relevant today. All of these rules will work to improve efficiency if enough time is given to implement them into the modern business process.
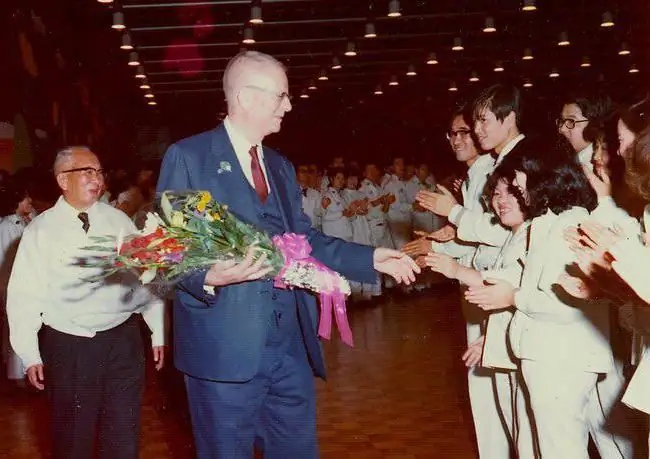
1. Setting the main goal
Don't chase instant and one-time profit. It is necessary to tune in to the long term and constantly improve. You need to strive to ensure that your company is competitive, provided with labor resources and provides high-quality and necessary goods.
2. Rebuilding to a new philosophy
Western style of management no longer justifies itself and slowly leads the economy to decline. To stay afloat, you need to learn new principlesworks and apply them. Japan has begun a new economic era, and these principles must be followed today.
3. Independence from checks
Constant tight control and checks should not be the way and the main goal to improve the level of quality. The results of the checks should show that the quality is already at the maximum level, and will not be there after.
4. Cheap does not mean quality
Don't chase cheap goods, pay attention to quality. If the supplier could not confirm the quality of his product, then you should not continue cooperation with him. By reducing the number of suppliers, you will come to long-term relationships and, as a result, lower overall procurement costs.
5. Don't stop there
The process of improvement and improvement should never stop. Even if the system seems to work perfectly, at the highest level, then know that there is always a process that can be contained even better. The earth does not stop for a minute, and every moment new ideas and new needs arise. Manufacturing, service delivery and planning processes can always be better and better than they are now.
6. Workforce training
Strive to ensure that staff are aware of and prepared for all the changes that occur with the production and provision of goods and services. Engage in continuous training of workers so that the staff is the most highly qualified.
7. Effective Leadership
The leader should be asis aimed at the process of quality improvement, showing by example high production performance and a responsible attitude to work. The manager must ensure the functioning of the production system in such a way that if defects or malfunctions occur, immediate measures are taken to eliminate them. Leadership should not be just a word, but a way of working. The leader should be primarily responsible for quality, not statistics.
8. Cast out fear
Fear is always a bad adviser, both in life and at work. Subordinates should not be afraid of their leadership. If a subordinate is afraid of his boss, then he will never be able to fully devote himself to work, since most of his thoughts during the working day will be aimed at how to avoid a collision (meeting) with the leader. Go towards your subordinates, be open to communication. Two-way communication always has a positive impact on the relationship between employees and their supervisors. And as a result, it helps to improve the quality of work.
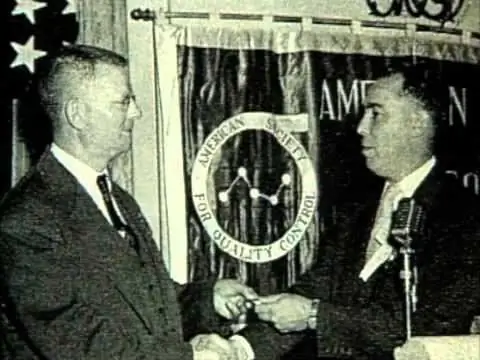
9. Say no to functional work
Many companies today work according to this principle, that is, each division does its own narrowly focused work and does not cooperate with other departments. Edward Deming argues that working in teams, specialists of different profiles will come to the required result much faster and more efficiently.
10. Cancel slogans, sermons and installations foremployees
Slogans and sermons do not affect the overall process of work, but are directed only at workers. Quality and performance depends on the overall design of the system, and not on a single worker in particular. Slogans and attitudes are a waste of time and effort, which only leads to zero results.
11. Remove arbitrary norms
Instructions and standards for working with arbitrary norms and quotas should be avoided, or better not used at all. The most effective way to influence the production process will be the help and feedback from higher management.
12. Eliminate barriers that prevent employees from taking pride in their work
The goal of the work of the staff should not be quantity, but quality. Performance appraisals of workers should be kept to a minimum.
13. Encourage self-improvement
Today we do not need workers who mindlessly carry out their tasks. In the conditions of the current market of services, which changes every minute, knowledge and skills win. Provide employees with a self-development and professional development program. From this, the quality and efficiency will increase very quickly.
14. The most important thing is transformation
If the goal of a production system is high quality, then the production system must strive and be ready for constant change. Moreover, everyone in the company should be focused on changes in the system. And the leadership structure should be organized in such a way that each day gives impetus to the advancement of each subordinate.
Recommended:
Mind management: concept, definition, basic principles and thematic books
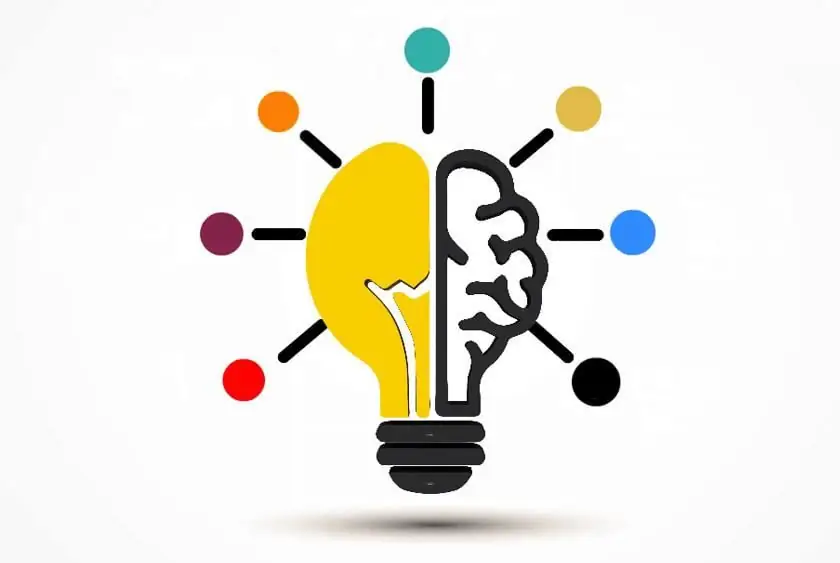
Few modern people know how to manage their time. Despite the popularity of time management, people get lost in the flow of information, and they can’t manage to fix their lives. And all why? For the reason that they do not have a single system for structuring information. Mind management will help you bring order to eternal chaos
Warren Buffett is the best investor in the world. Biography, books, sayings, the path of the "oracle from Omaha"
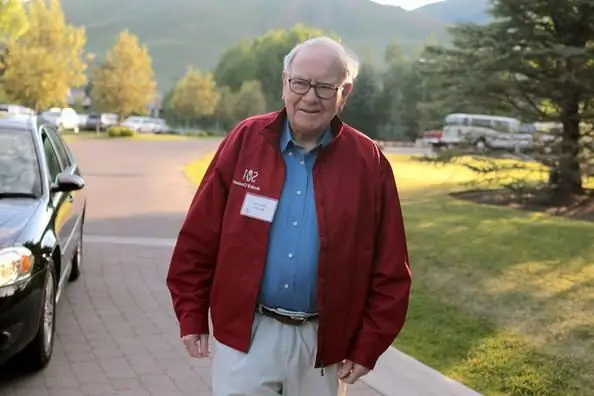
Warren Buffett is called the Oracle of Omaha by his compatriots for a reason. This financier and businessman has a paradoxical sense of economic processes. In addition, he leads his investment company with a firm hand, where like-minded people work
Best books on investing to read
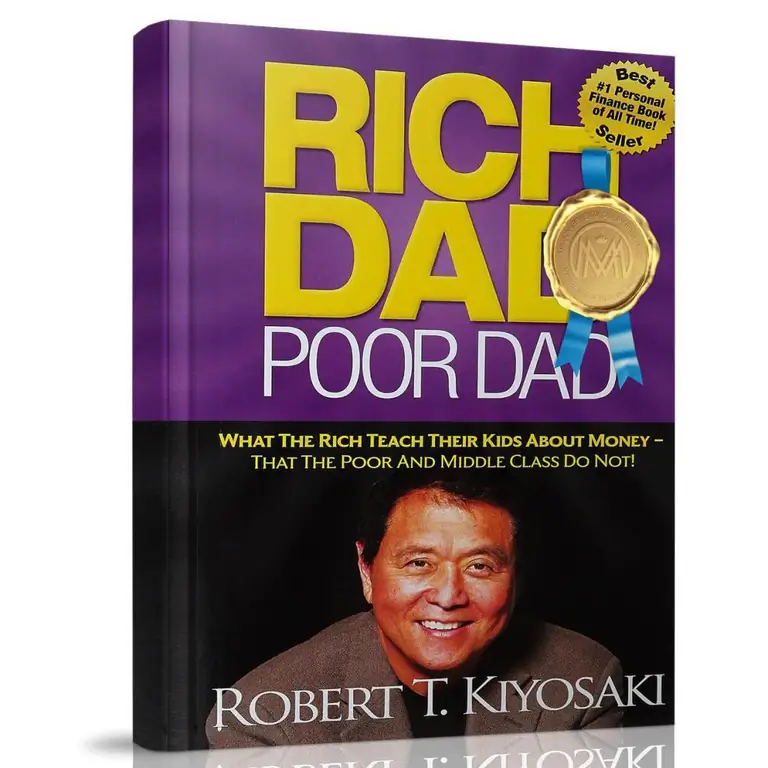
To make your money work effectively, you need to stock up on knowledge. A selection of the best books on investing will help with this. Really interesting and useful literature written by ordinary people who have come a long way in investing
Jack D. Schwager - futures and hedge fund expert: biography, books
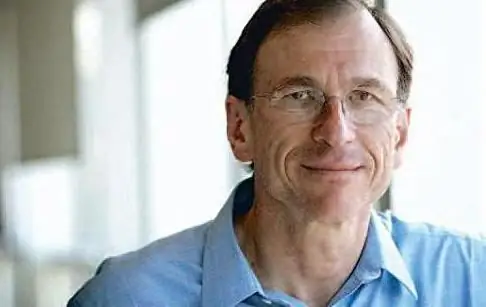
Today's article is about Jack Schwager. This is a writer and a successful trader who built his career and showed everyone that it is possible to achieve any heights. We will look at the biography of the expert, we will also talk about his books and tips for beginners
Jack Welch: biography, books
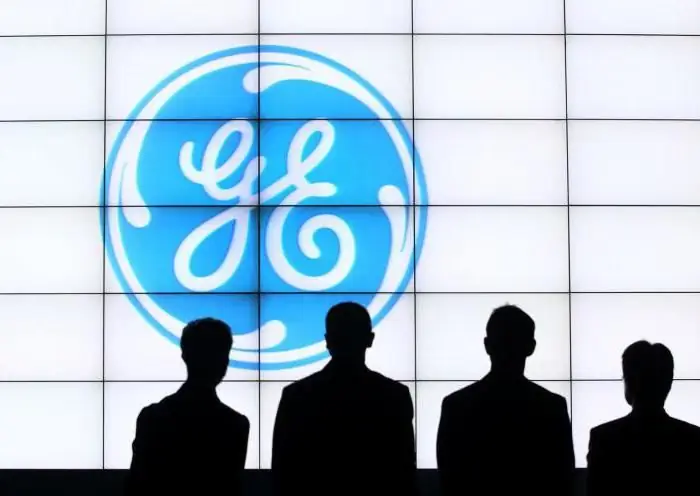
Jack Welch did not start General Electric - the company was over a hundred years old when he took over the reins, but he managed to transform it and write books about it. To the surprise of many experts who argued that GE was too big for its shares to grow, and investing in it only for the sake of dividends, during two decades of leadership, Welch increased its value by 40 times