2025 Author: Howard Calhoun | [email protected]. Last modified: 2025-06-01 07:12
Cast iron in its composition is an alloy of iron and carbon, which may also include impurities and some alloying additives. This metal is widely used in industry for the manufacture of various load-bearing parts and structures. In domestic buildings, most sewer risers and heating radiators are made of cast iron.
High carbon content makes it difficult to connect cast iron parts to each other and to other metals. Violation of technological requirements often leads to overheating, and hence to an increase in the brittleness of the metal. Therefore, before proceeding with the connection of cast iron structures, it is necessary to thoroughly study how to cook cast iron by electric welding, as well as the necessary materials and technology for performing such work.
Types of cast iron
The composition of cast iron includes not only carbon (2-6%) and iron, but also manganese (up to 1%), silicon (3%), phosphorus, sulfur, as well as additives for alloying - aluminum, vanadium, chromium,magnesium, nickel and some other components. It is alloying substances that give hardness, strength and ductility to the material, depending on its application.
Electric welding of cast iron is performed depending on the form and amount of carbon that is in the metal as graphite or cementite. It is according to these indicators that cast iron is divided into the following types:
- White cast iron has a light fracture surface color because the carbon in this metal is a form of cementite. The processing of such material is difficult due to its high hardness.
- In gray cast iron, carbon is in the form of graphite. Gray metal fracture surface. This cast iron is easily machined and has good casting properties.
- The heat treatment of white cast iron turns it into a malleable metal, which is widely used in engineering.
- Half cast iron contains carbon in the form of cementite and graphite. This ratio gives the metal high wear resistance.
- Globular graphite gives cast iron high strength. Ductile iron is used to make quality pipes for oil and water pipelines.
Features of welding cast iron
Before answering the question of whether it is possible to cook cast iron by electric welding, it is necessary to understand the features of the metal joining process. According to its structure, as well as many physical properties, cast iron belongs to alloys that are subject to the welding process to a limited extent.
During the electric welding of cast iron inat home, you need to pay attention to the following complexities of this process:
- Formation of a quality seam complicates the fluid nature of the cast iron alloy.
- Failure to observe the temperature regime of welding leads to overheating of cast iron. This causes the carbon in the weld pool to burn off and therefore increases pore formation.
- Also, the high temperature of the electric arc contributes to the bleaching of cast iron at the welding site. This effect, due to the heterogeneity of the metal structure, leads to cracking of the seam.
- During the welding process, cast iron is able to oxidize, creating a refractory oxide, the melting point of which is much higher than that of the original material.
To avoid all these troubles when welding cast iron, you must responsibly select the correct mode of operation.
Preparing cast iron for welding
Before welding cast iron by electric welding, it is necessary to prepare the edges of the surfaces to be joined. Preliminary cleaning of the surface can be carried out both manually and with an electric tool with a metal bristle nozzle.
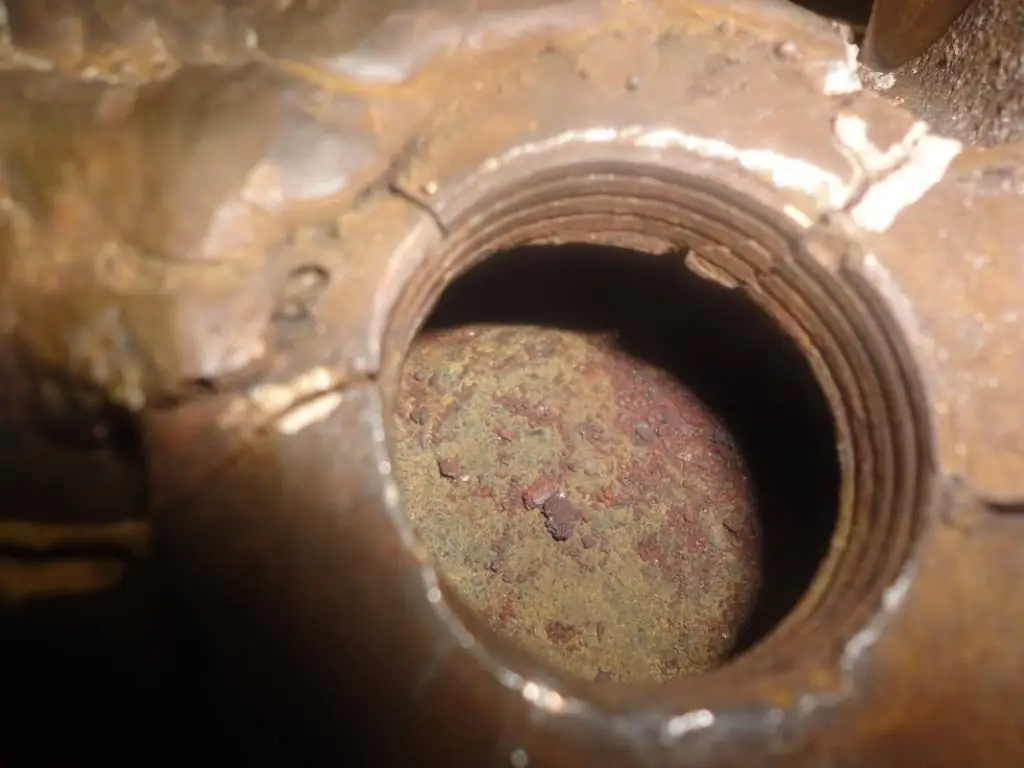
Next, it is imperative to cut the edges to bare metal, since it is much more difficult to cook cast iron by electric welding in home workshops than steel.
Defective places of cast iron are cut according to the following rules:
- cutting is carried out strictly along the crack;
- non-through cracks are drilled with a drill, and then they are cut down tomain material;
- depending on the thickness of the metal, through cracks are cut from two or one side;
- it is recommended to weld a patch on closely spaced cracks, which should cover the defect by 15-20 mm from all sides.
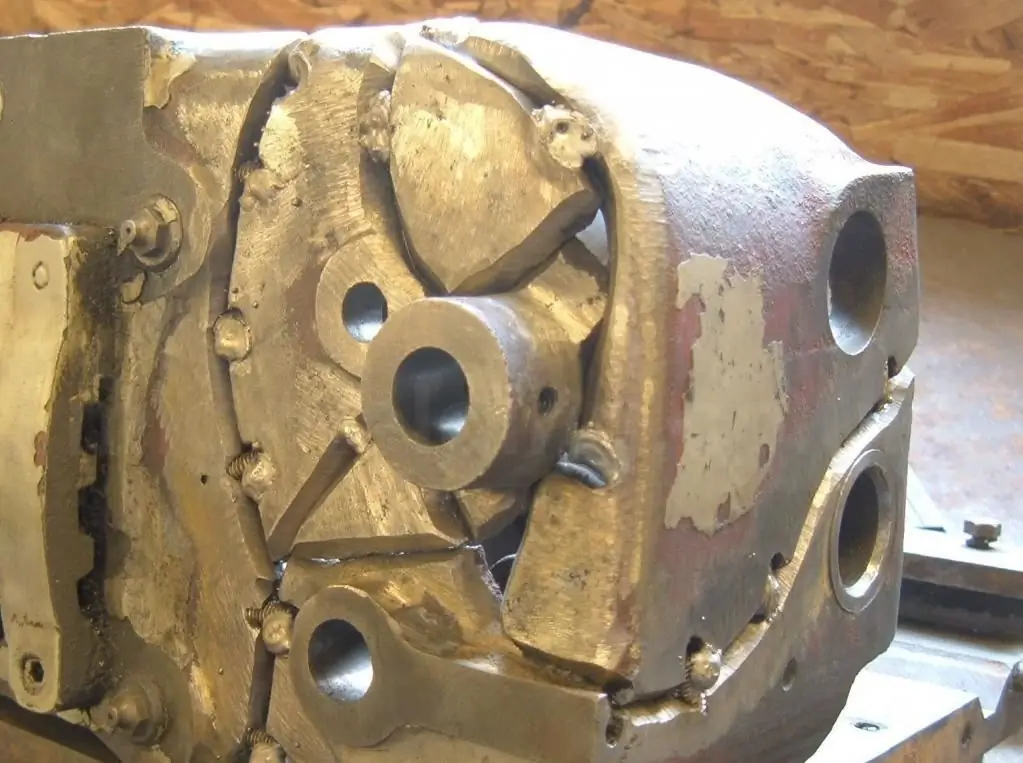
After cleaning the surface and cutting the edges, it is necessary to carefully degrease the joint with acetone or solvent.
Basic Cast Iron Welding Methods
It is possible to cook cast iron both by electric welding and in an inert gas environment. The second method is used mainly for joining heterogeneous metals. Gas welding is most often used for repair work on sewer pipes, as well as the restoration of car parts.
It is possible to cook cast iron by electric welding both hot, with preheating of workpieces, and cold, without heating the junction. Heated welding is technologically more complex than cold welding, so its use in domestic conditions is impractical.
Gas welding
Welding of cast iron in a protective gas cloud is used to create a seam of high strength, which is achieved under the condition of a small penetration of the metal. The practical experience of the welder, as well as the choice of the correct mode for creating a weld, is of particular importance to the final result of the work.
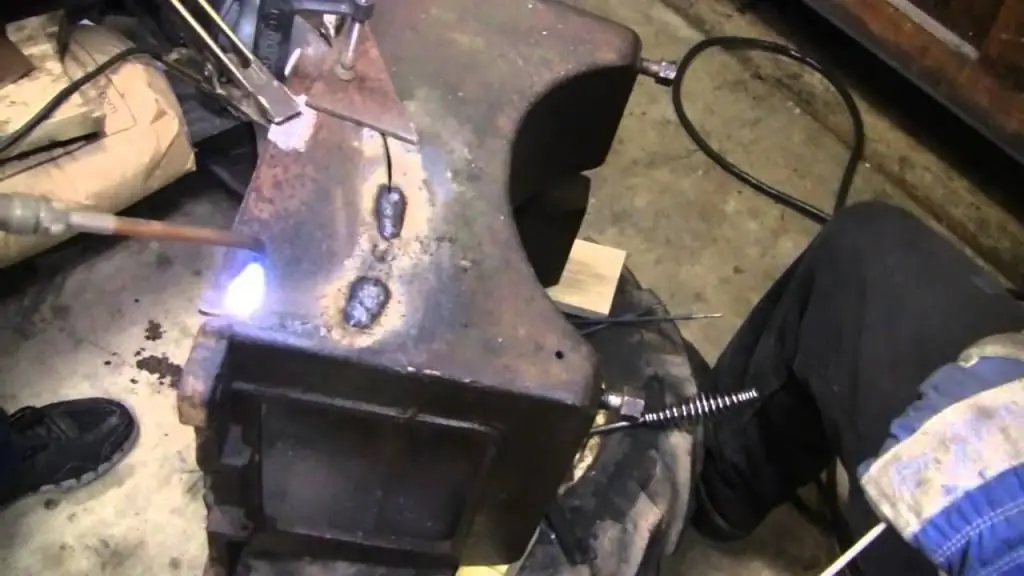
The process of gas welding is recommended to be done with two burners. At the same time, one burner providespreheating of the junction, and the second one melts the wire and directly welds the cast iron parts. Cooling of welded parts must be slow, so it is often used to cover products with a layer of sand or asbestos.
Hot welding cast iron
Welding of cast iron products with preheating of the edges of the joined surface is most often carried out in industrial enterprises. Heating of workpieces can be carried out in inert furnaces, as well as various special burners.
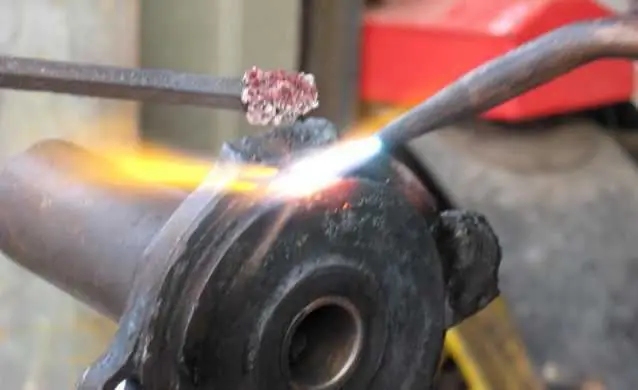
Heating the welding site to 600-650 ℃ eliminates the possibility of tension and overheating of the metal at the joint.
Welding technology is as follows:
- Preliminary preparation of the junction is in progress.
- The product is located in such a way that it is possible to weld with the lower position of the seam.
- The welding machine is configured to work with straight polarity. The current strength when welding cast iron is set much higher than when welding steel.
- The part is heated to a temperature of 300-600 degrees.
- The weld pool must be filled with molten metal during the process of creating a seam. It is recommended to stir the liquid melt with the tip of the electrode.
- After welding, it is better to leave the product in a cooling furnace, or cover it with heat-insulating material. Slow cooling of cast iron is the key to a quality connection.
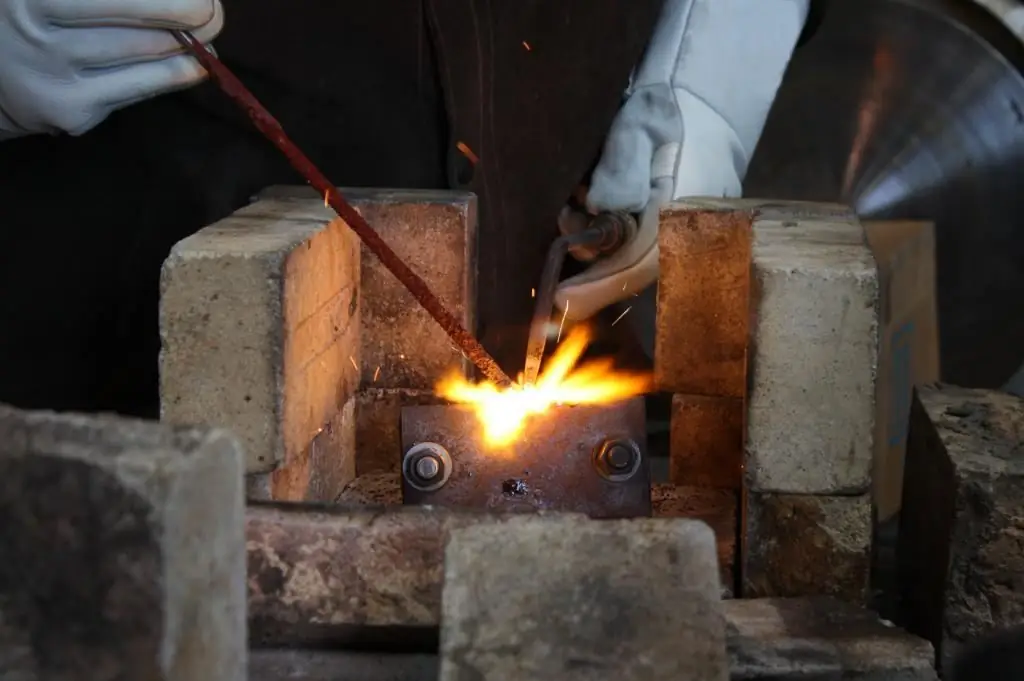
Of course, welding hot ironmethod is considered laborious work, but it is precisely such conditions that make it possible to obtain a seam without defects and with high quality.
Cold welding method
In cases where high requirements are not imposed on the weld, it is possible to cook cast iron by electric welding at home, both cold and with slight heating.
Technological features of cold welding are as follows:
- The welding machine is set to the minimum power that is allowed for a certain thickness of the electrode in order to prevent overheating of the metal.
- Welding is carried out on reverse polarity current.
- Welding seam should be done in 30-50 mm lengths.
- Overheating of the joint is eliminated by interrupting or staggering the seam.
- When multi-layer welding, each seam must be forged with a hammer.
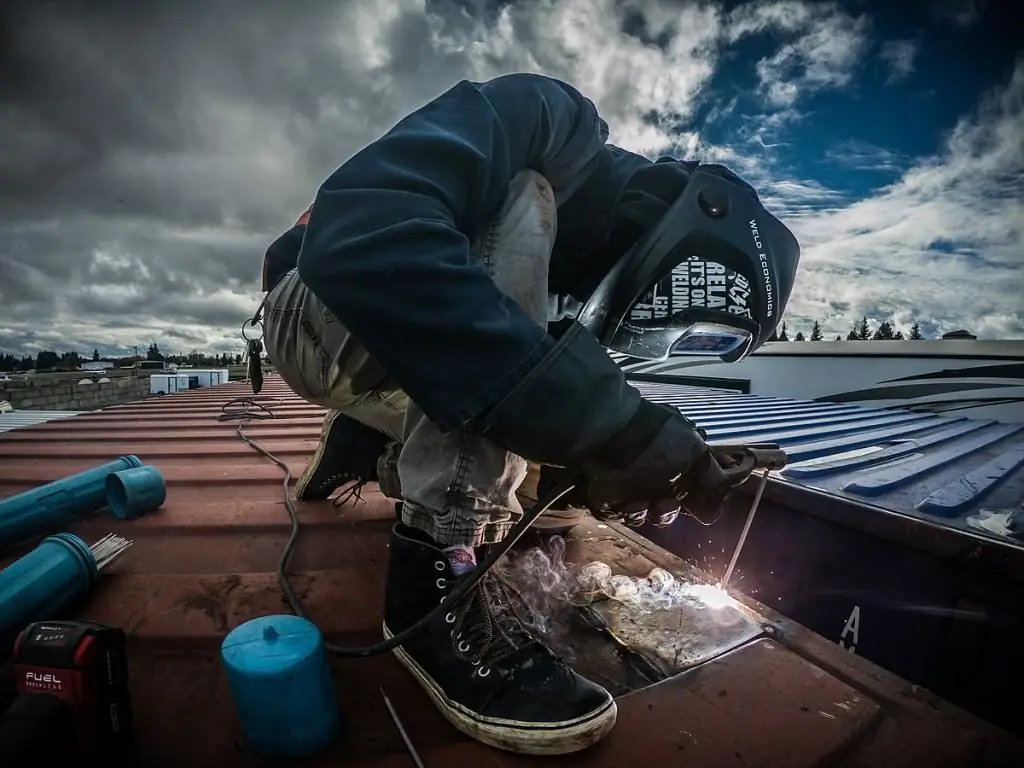
The quality of the cast iron connection depends entirely on the correct choice of electrodes.
Electrodes for welding cast iron
It is possible to cook cast iron by electric welding both with an electrode for cast iron and with products containing nickel or copper. Carbon does not combine with these non-ferrous metals, so white cast iron does not form in the weld. Most often, welding with such electrodes is performed in several stages, with a break for cooling.
The following electrodes for cast iron are used for electric welding of cast iron products:
- OZCH-2 and OZCH-6 - electrodes based on copper and iron, which are used for welding gray orductile iron;
- OZZHN-1 - this grade contains iron and nickel, very effective for ductile iron;
- MNCH-2 - these products contain copper, nickel and iron, suitable for welding all types of cast iron.
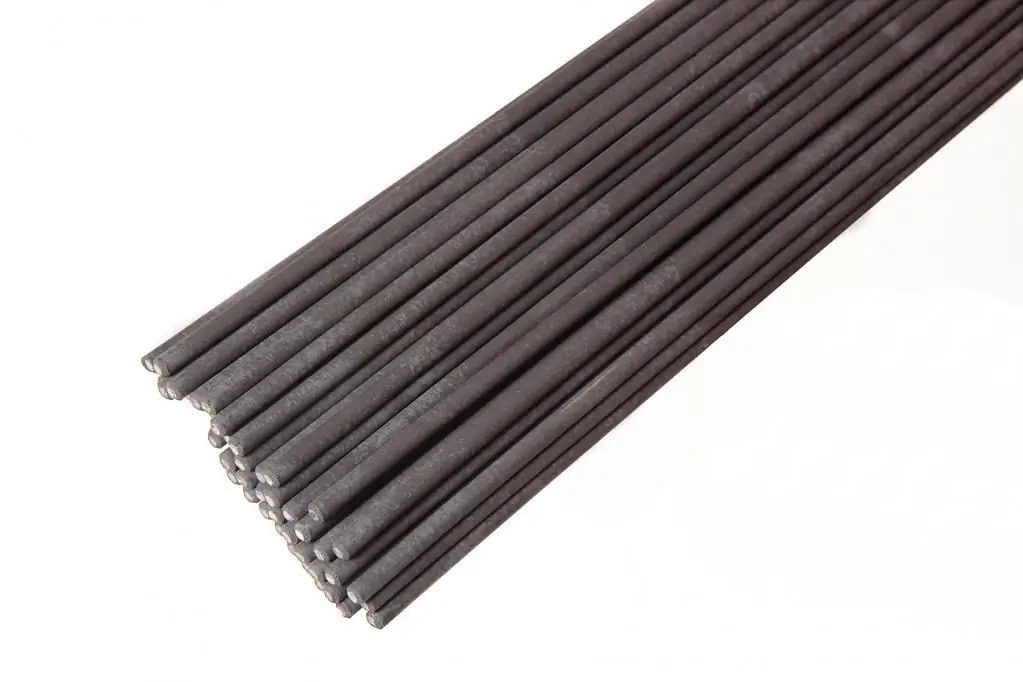
Welding safety basics
Welding is classified as an increased risk to the he alth of the welder. Therefore, compliance with safety regulations when welding cast iron is a prerequisite for work.
Key safety precautions include:
- all work must be done using personal protective equipment (mask, gloves, special suit and shoes);
- welding must be carried out in a well-ventilated area;
- welding equipment must be maintained in good condition;
- Electrical equipment must be properly grounded.
Cast iron refers to metals that are difficult to weld technology. Therefore, before proceeding with the process of joining cast iron products, it is necessary to carefully study the main nuances of the high-quality performance of such work.
Recommended:
Welding of ultrasonic plastics, plastics, metals, polymeric materials, aluminum profiles. Ultrasonic welding: technology, harmful factors
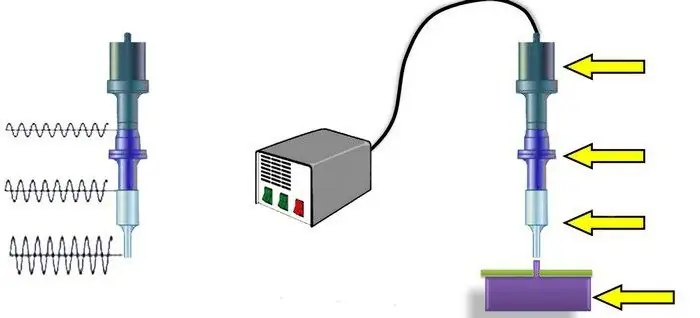
Ultrasonic welding of metals is a process during which a permanent joint is obtained in the solid phase. The formation of juvenile areas (in which bonds are formed) and the contact between them occur under the influence of a special tool
Forge welding: description, work technology and necessary tools
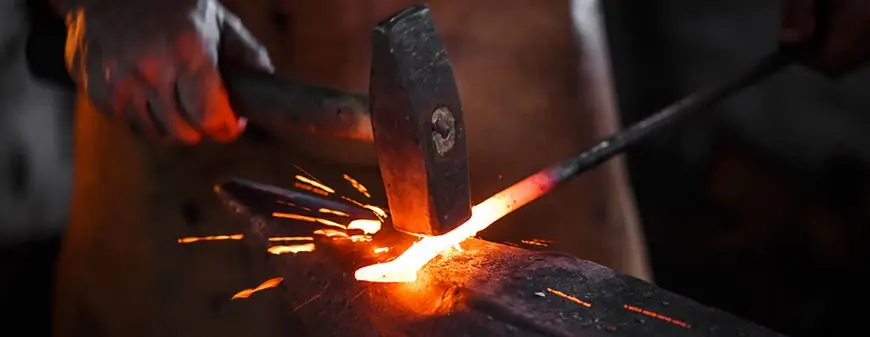
Forge welding is perhaps the oldest method of metal bonding. Blacksmithing was the only method of processing steel for several millennia, until in the 19th century specialists mastered the foundry industry. And in the 20th century, technological progress developed, as a result of which other progressive ways of connecting metals became available to mankind. Because of this, forging has lost its relevance
Shaft grinding: technique, necessary materials and tools, step-by-step work instructions and expert advice
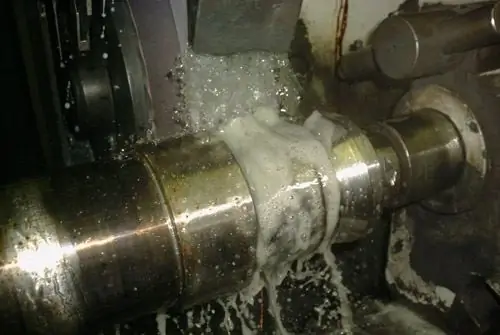
Today, shaft grinding is quite widely used in such an industry as mechanical engineering. This operation allows the preparation of parts that will have a small roughness, a slight deviation from the shape, etc
Thermite welding: technology. The practice of thermite welding in everyday life and in the electrical industry
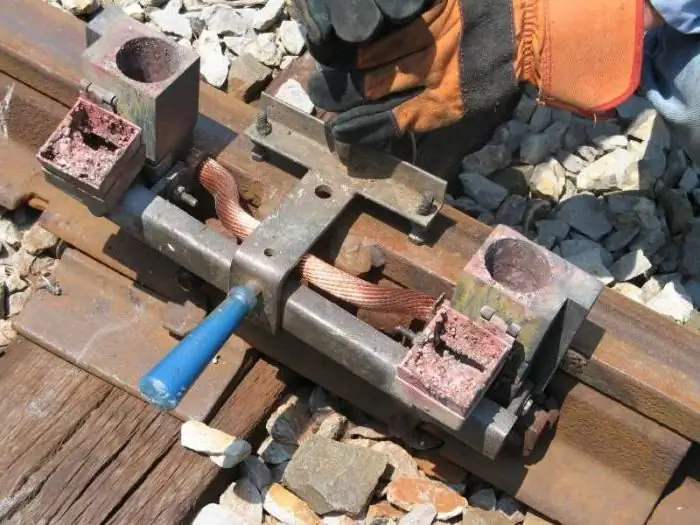
The article is devoted to thermite welding technology. The features of this method, the equipment used, the nuances of use, etc. are considered
Welding in a shielding gas environment: work technology, process description, execution technique, necessary materials and tools, step-by-step work instructions and expert advice
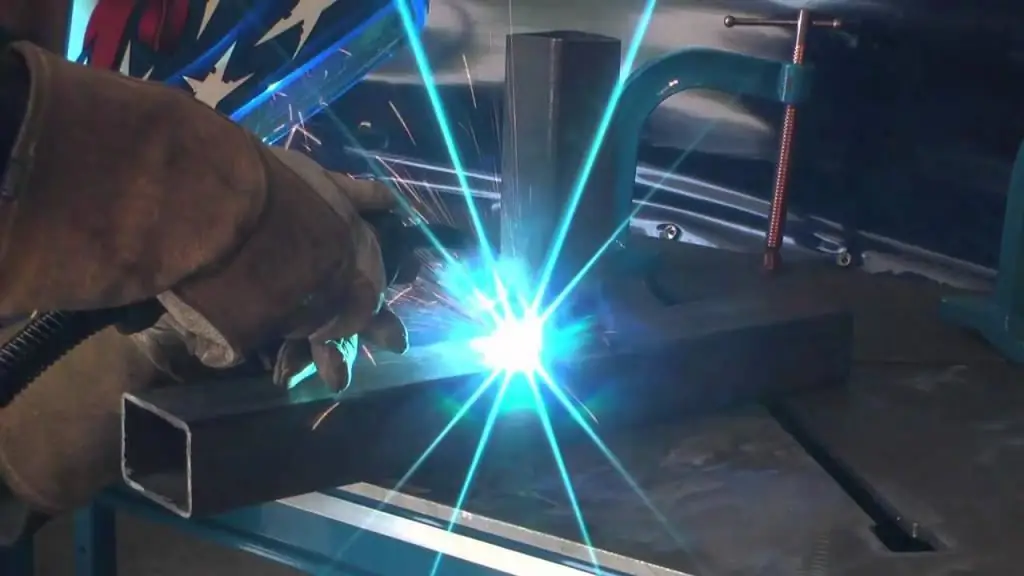
Welding technologies are used in various branches of human activity. Versatility has made welding in a protective gas environment an integral element of any production. This variety makes it easy to connect metals with a thickness of 1 mm to several centimeters in any position in space. Welding in a protective environment is gradually replacing traditional electrode welding