2025 Author: Howard Calhoun | [email protected]. Last modified: 2025-01-24 13:10
Forge welding is perhaps the oldest method of metal bonding. Blacksmithing was the only method of processing steel for several millennia, until in the 19th century specialists mastered foundry production. And in the 20th century, technological progress developed, as a result of which other progressive methods of metal bonding became available to mankind. Because of this, forging has lost its relevance. Today, this craft exists only formally, at the request of some handicraft specialists.
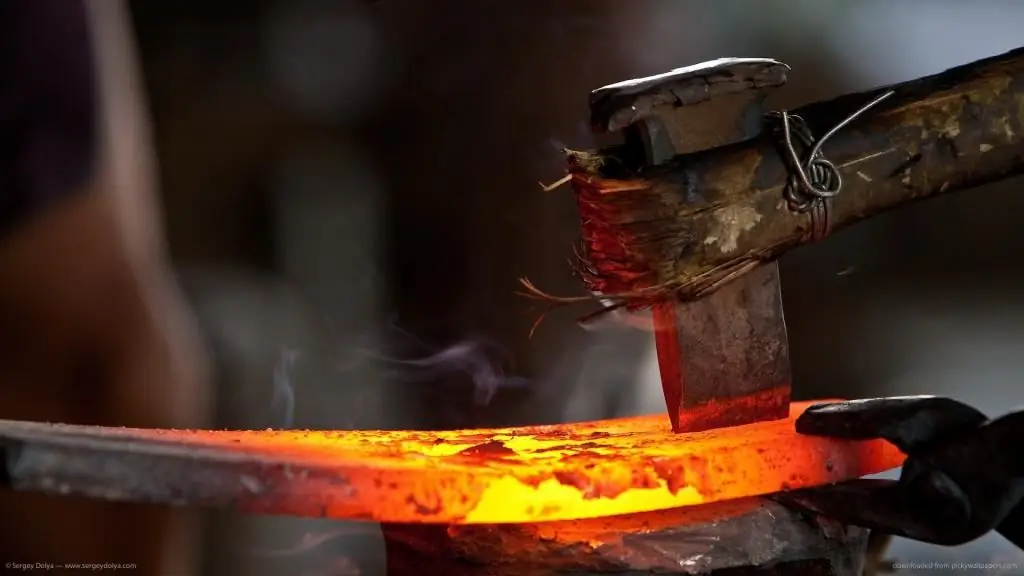
Guidelines
Forge welding is a manufacturing process that creates inseparable bonds between metal components using high temperature and impact pressing. In other words, metal fragments are heated in a special furnace to a fluid state and, using percussion instruments, onmetal base carry out their connection. The whole process consists of the following steps:
- preliminary preparation of surfaces to be joined;
- thermal heating to the set temperature;
- connection with percussion instruments;
- final forging, allowing you to set the desired shape.
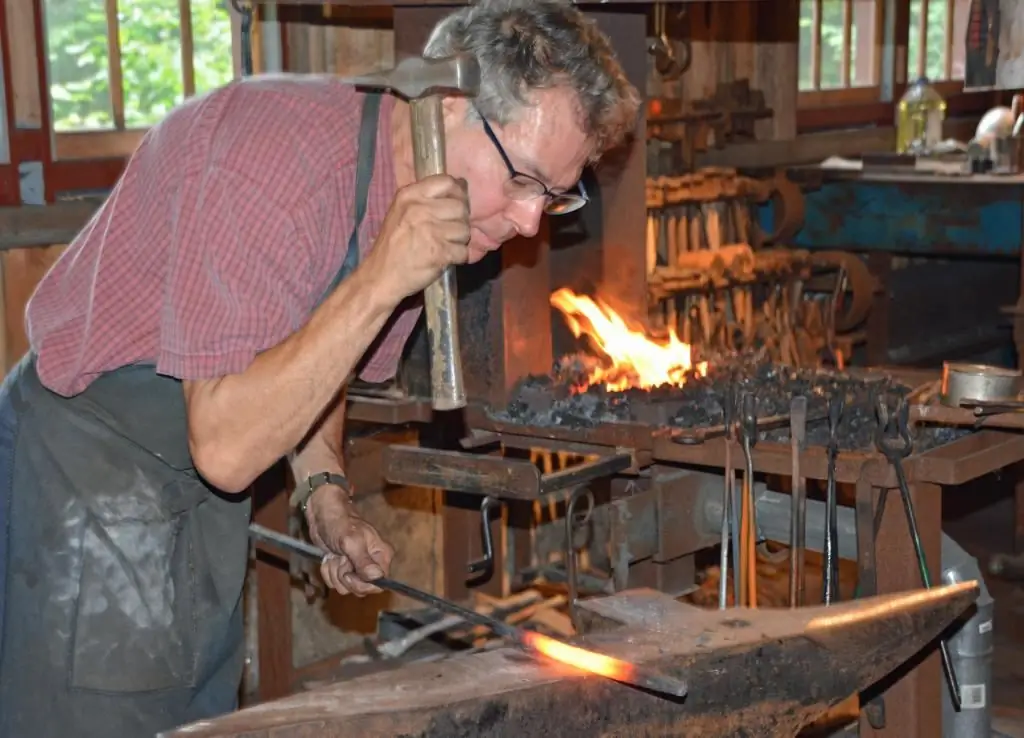
The most important condition in this case is the heating of the metal using high temperatures. Bringing the metal to the required temperature is controlled by changing the color of the hot surface. Thus, reaching a temperature of 1300 degrees, the iron becomes bright yellow. When the heat is increased to 1400 degrees, it begins to become bright white. When the required temperature condition is reached, the connection should be made immediately. Otherwise, the quality of the product may suffer due to overburning of the material, which is accompanied by the formation of an excessive layer of scale.
Features
Gliability to compounds, due to thermal diffusion, using high pressure, when bringing the material to a soft plastic state, as a rule, for different types of metals and components has significant differences. Thus, low-carbon steels with a percentage of carbon not exceeding 0.6% are considered malleable to joints. As the percentage increases, the overall ability to combine is weakened.
Alloy steels are difficult to forge, as well as non-ferrous metals, including themalloys. In addition, all varieties of cast iron are completely impossible to connect in this way. The main obstacle to the joining process in the process of thermal diffusion is the formation of a layer of scale on the heated surface. This layer is formed by refractory oxides called FeO and Fe3O4, which have a weak ability to melt when exposed to a temperature that is sufficient to weaken the main surface of the metal.
To reduce the influence of oxides that create interference, the surface to be treated is coated with special fluxes for forge welding. They are acidic. Most often, table s alt or boric acid is used for this purpose. A calcined drill for forge welding may also be suitable. In other cases, the use of flux is replaced by some improvised materials. This, for example, can be glass cullet, as well as fine sand from the river bank, which can replace blacksmith welding with brown.
This welding is considered one of the most complex processes in terms of technology, as it requires a lot of knowledge and practical skills from a specialist. For example, it should be understood that the ability to join the metal appears only when a certain temperature is reached. In case of insufficient heating of the surface, a defect called lack of penetration will result. And if the metal is overheated, then a burn is formed, which also will not lead the product to a high-quality form.
Ways
There are a number of simple connection methods that do not require longpreparatory actions during forge welding. The following technique names are used:
- overlapping;
- butt;
- in girth.
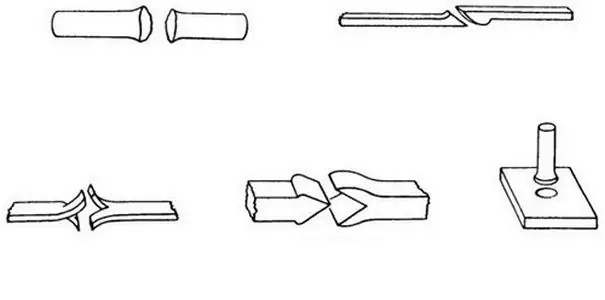
Conditions
To perform actions using these techniques, you should follow only one mandatory rule - the ends of the workpieces must have a convex shape, and also have thickenings at their ends. This condition must be observed because in the process of making connections by the forge welding method, during the heating of the workpiece, a slag film is formed on the metal surface. And if the surface has bulges, then slag particles can be squeezed out. Thickenings formed at the ends of blanks intended for forging serve as a technological reserve in the process of acquiring the required shape.
Other technologies
There are also more complex forge welding technologies that allow you to create products that play the role of components in complex mechanisms or represent decorative elements in various design compositions:
- One of these methods is proven split welding. This technique was used in the past, joining strips of steel in the process of making the metal tires needed by village carts.
- The next method is welding using checkers. This technique is effective when connecting the overall components.
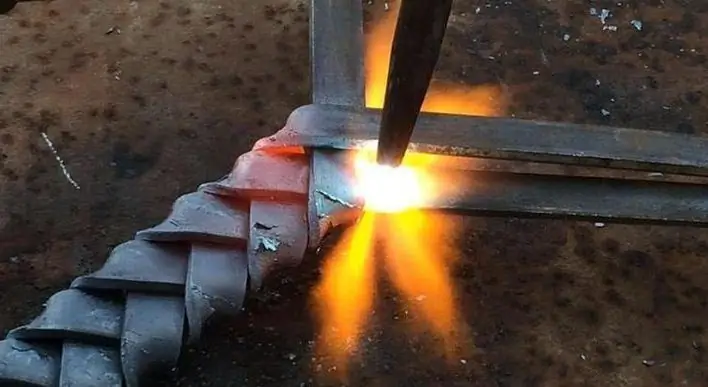
For split welding, the processed edges of the strips passspecial training. They are first pulled and then cut in such a way that before welding, it becomes possible to connect by overlapping. Only after that the fragment is heated up to the required temperature and welded by forging. The second method of forge welding of steel involves the use of an additional element. These elements are called checkers.
Scope of application
Forge welding today is no longer the main method of joining metals. It is used mainly for the manufacture of complex metal components in intricate patterns of artistic forging masters. Artistic welding of metal fragments allows you to create the most incredible forms that decorate various facades.

In addition, this welding method is sometimes used for the manufacture of some hand tools needed in everyday life. And it has lost its industrial significance due to low productivity against the background of other connection methods.
Cons
The disadvantages of this technology include:
- low heating rate;
- insufficient strength of the resulting joints;
- significant heterogeneity in the passage of upsetting processes;
- high qualification requirements from performers.
Only a few industries continue to use forge welding. Currently, using this technology, they continue to produce metal water pipes, the diameter of which does not exceed 100 mm. Creating conditionsto carry out this procedure, the strip steel is heated in special furnaces, and then rolled linearly through the rolls. Then it is dragged through the mandrels at high speed. In this way, the general seam welding of the water pipe occurs under the influence of high pressure.
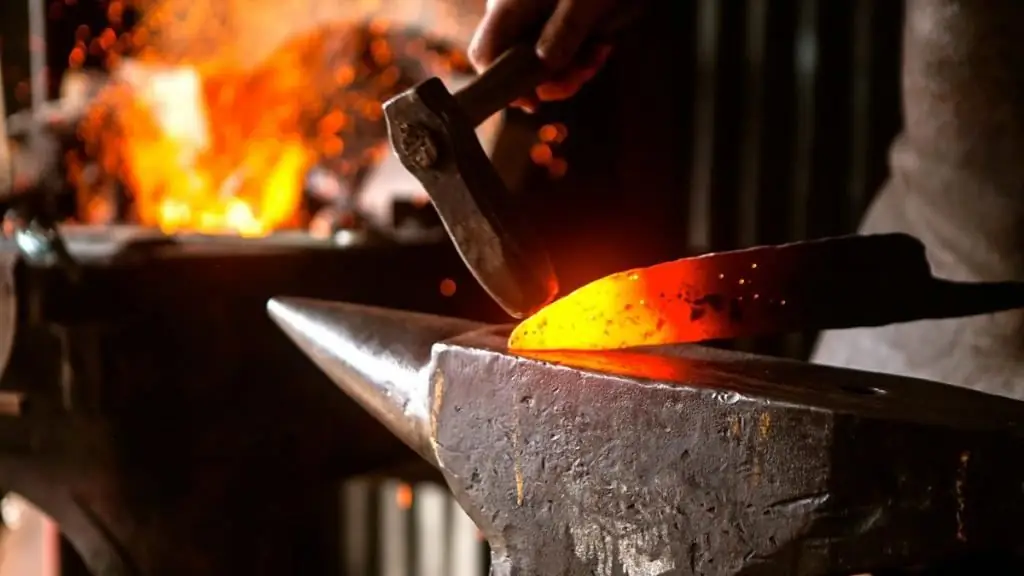
Also on an industrial scale, forge welding is still used in the manufacture of complex bimetallic plates. Usually, for this, a joint rolling of hot billets through special rollers is used, or a pressing method is used, using thermal furnaces, with vacuum conditions. Forge welding allows you to give a multilayer structure to products, which in some cases is of great importance.
Equipment and supplies
It doesn't take much to set up a small forge for handicraft production of some items or art forging elements.
With certain equipment and a few tools, you can easily set up your own production of metal forge welding:
- First of all, you need one stationary bugle and one portable. This is a special device necessary for heating the surfaces to be welded. An ordinary gasoline autogenerator may well become a portable forge.
- Next you need a group of anvils. It is important that it must be both large and small. In addition, it is not enough to have only a two-horned anvil. One-horned should also be present.
- Set of blacksmith tongs,made up of as many sizes as possible.
- A set of blacksmith hammers that will allow you to carry out the basic forging process.
- Two containers designed to cool materials. One of them must be filled with water and the other with oil.
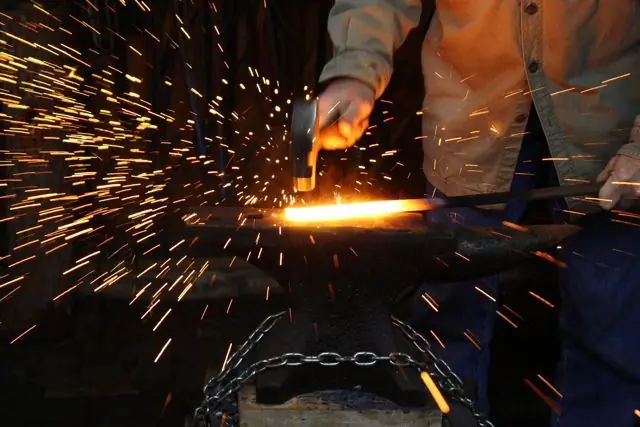
Important
It is imperative to provide the forge with all the necessary security equipment. In addition, the kit should have personal protective equipment - glass glasses, a protective leather apron, thick canvas gloves.
Recommended:
How to cook cast iron by electric welding: work technology and necessary materials
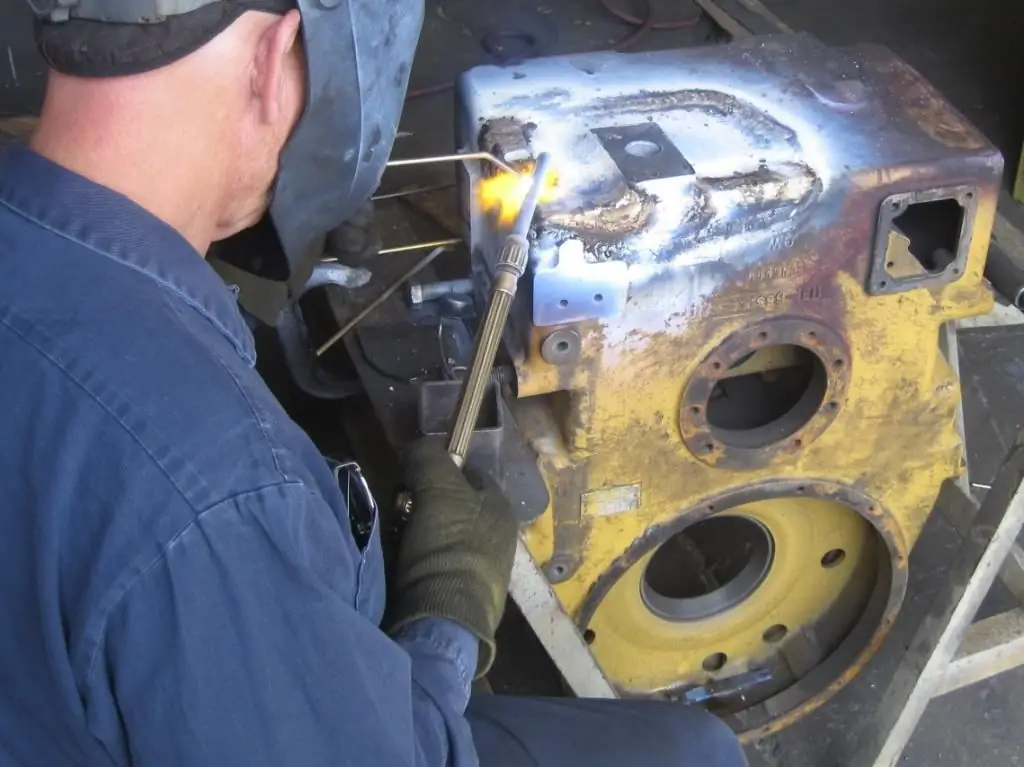
The main composition and types of cast iron. Difficulties and features of welding cast iron products. Cast iron welding methods. Preparatory operations before welding. How to cook cast iron by electric welding in a cold and hot way, as well as gas equipment. Features of the electrodes used for welding cast iron. Safety measures during welding
Work permit for work in electrical installations. Rules for work in electrical installations. Work permit
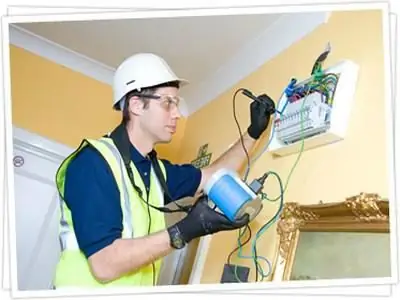
From August 2014, Law No. 328n comes into force. In accordance with it, a new edition of the "Rules on labor protection during the operation of electrical installations" is being introduced
Shaft grinding: technique, necessary materials and tools, step-by-step work instructions and expert advice
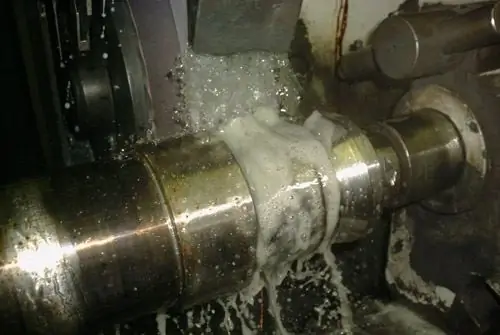
Today, shaft grinding is quite widely used in such an industry as mechanical engineering. This operation allows the preparation of parts that will have a small roughness, a slight deviation from the shape, etc
Thermite welding: technology. The practice of thermite welding in everyday life and in the electrical industry
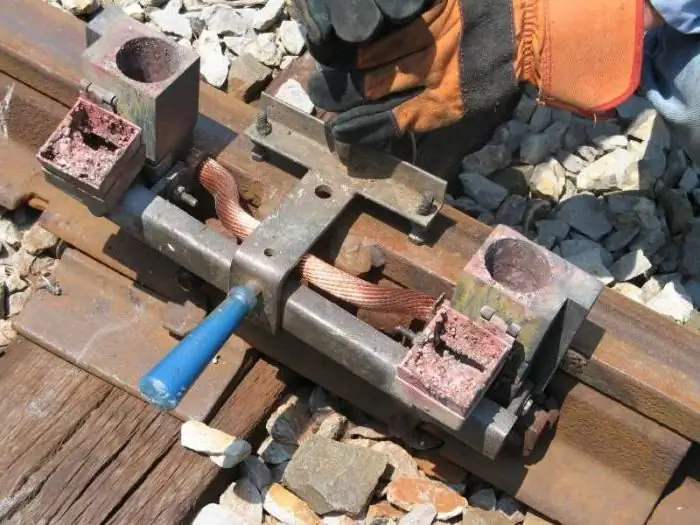
The article is devoted to thermite welding technology. The features of this method, the equipment used, the nuances of use, etc. are considered
Welding in a shielding gas environment: work technology, process description, execution technique, necessary materials and tools, step-by-step work instructions and expert advice
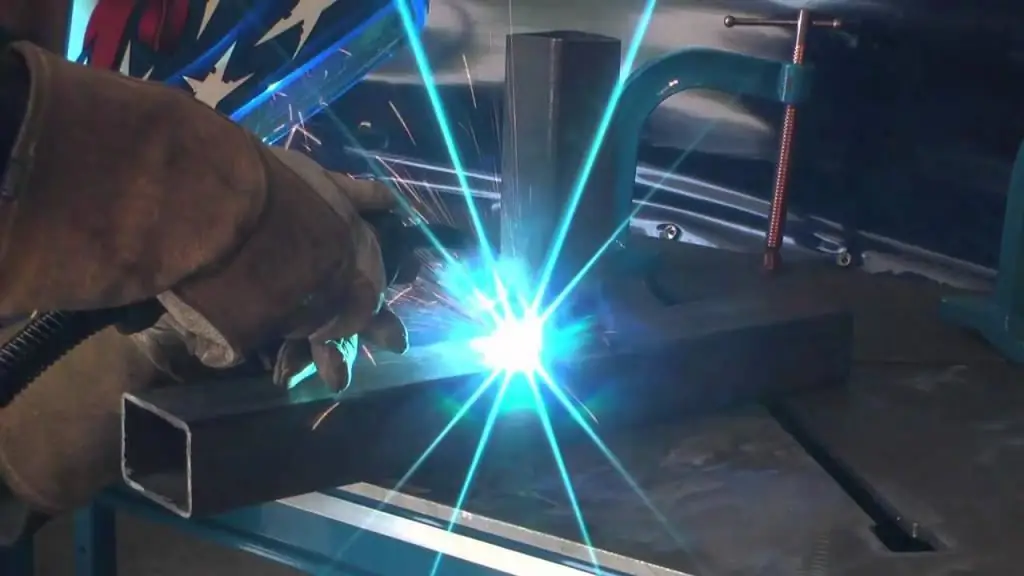
Welding technologies are used in various branches of human activity. Versatility has made welding in a protective gas environment an integral element of any production. This variety makes it easy to connect metals with a thickness of 1 mm to several centimeters in any position in space. Welding in a protective environment is gradually replacing traditional electrode welding