2025 Author: Howard Calhoun | [email protected]. Last modified: 2025-01-24 13:10
Gas fuel has been known since the middle of the 19th century. It was then that the famous engineer Lenoir built his first gas internal combustion engine. This apparatus was primitive and worked without pre-compression of the combustion chamber. Modern engines are no match for it. Today, the use of gaseous fuels is not limited to cars. This environmentally friendly, cheap and affordable type of fuel is actively conquering more and more new niches and is actively used in all sectors of the national economy. This article provides a description, characteristics of the fuel. In general terms, it describes how they are produced and used.
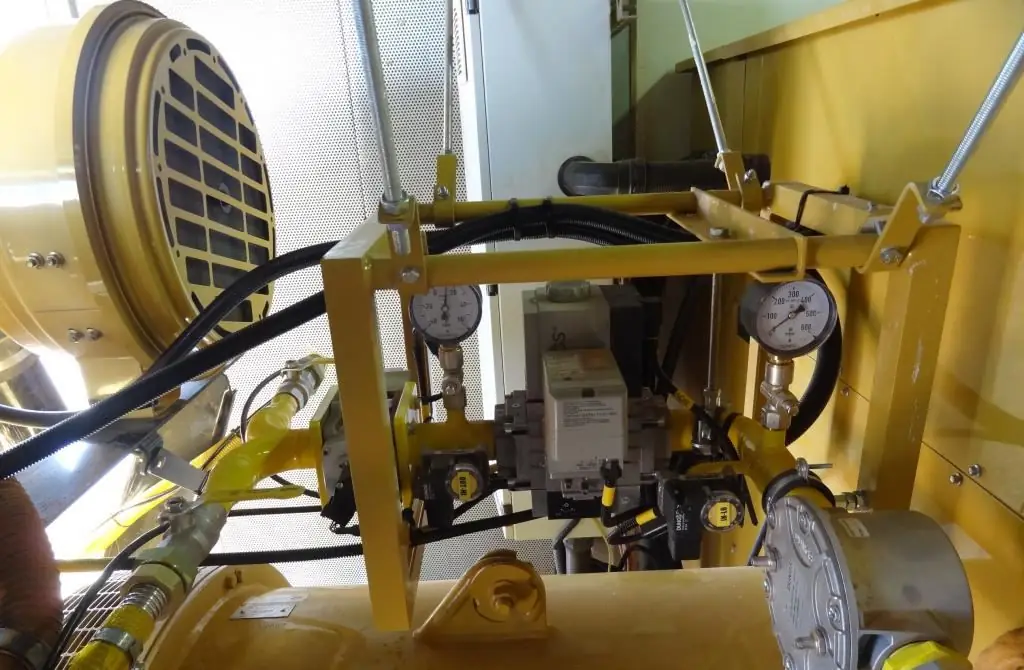
General information
A gaseous fuel is a substance that is highly flammable. This quality and useful property is used in various branches of science andtechnology. For example, the population and industry are increasingly using gaseous fuel boilers. In this fuel, oxides (dioxides) of carbon, carbon dioxide vapors, as well as elements such as nitrogen, hydrogen, oxygen and other impurities can be present in various quantities. Modern devices operating on gaseous fuels are very sensitive to the chemical composition of the working gas. If it does not meet the standards recommended by the manufacturer, then the equipment will most likely fail and costly repairs will be required.
All substances that make up gases can be divided into combustible and non-combustible. The first, in addition to methane, are ethane, propane and butane. Explosive and, accordingly, combustible are carbon monoxide and hydrogen. Hydrogen is especially dangerous. It is for this reason that it is not recommended to store it in gas cylinders. The best solution is to purchase a hydrogen generator. This device extracts hydrogen from distilled water as needed. Thus, the threat of detonation of a large volume of gas is eliminated.
The state is a monopoly in the wholesale trade of liquid and gaseous fuels. This indicates the strategic importance of this type of raw material.
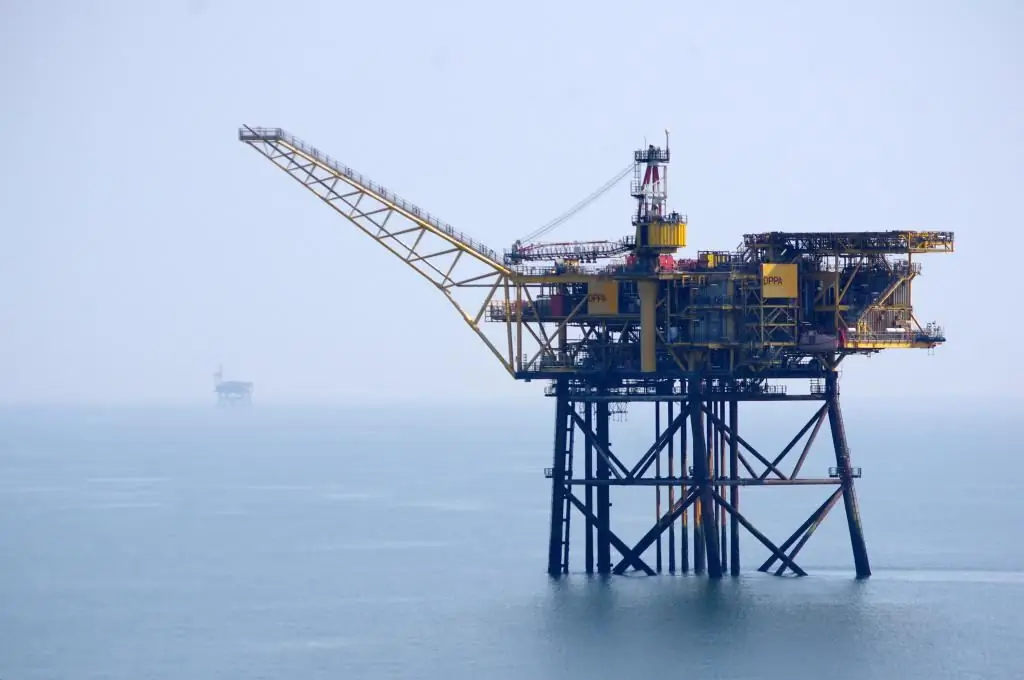
Classification of fuel by origin
Like liquid, gaseous fuels can be mined as a mineral, and can be produced in artificial conditions. In the first case, such fuel is called natural, and in the second -artificial.
Specialists have recorded differences in the composition of liquid and gaseous fuels extracted from different regions. Due to differences in chemical composition, there are also slight differences in the amount of heat released during combustion. Natural gaseous fuel is almost completely (95-99%, depending on the field) consists of the so-called methane (chemical formula - CH4). This fuel is called natural gas. And this is the cheapest source of energy today. It is for this reason that this type of energy resources is actively used in all sectors of the national economy. However, all the advantages are overshadowed by the low level of safety of devices operating on gaseous fuels. Disturbing news regularly appears in the media about accidents and human casu alties as a result of violations of the rules for operating gas installations.
Artificial gaseous fuels include substances obtained from the processing of solid or liquid fuels. Its most common and popular types are coke cracking gases. Lighting, water and blended fuels may also be included in this group. Depending on the chemical composition of a particular gas, the level of heat released during combustion varies over a wide range. Such substances are highly explosive. For this reason, they are recommended to be mixed with natural gas before combustion. This measure increases the safety of operation of devices operating on gaseous fuel by an order of magnitude. These manipulations are carried out on specially equipped bases. Then suchgas is supplied to the end user in cylinders or otherwise. But despite the fact that such a mixture is less dangerous, it still needs to be handled with extreme care, in compliance with all rules and regulations for working with pressure vessels and safety regulations. And this is not the only danger. This substance is toxic and inhalation can cause serious consequences and even death.
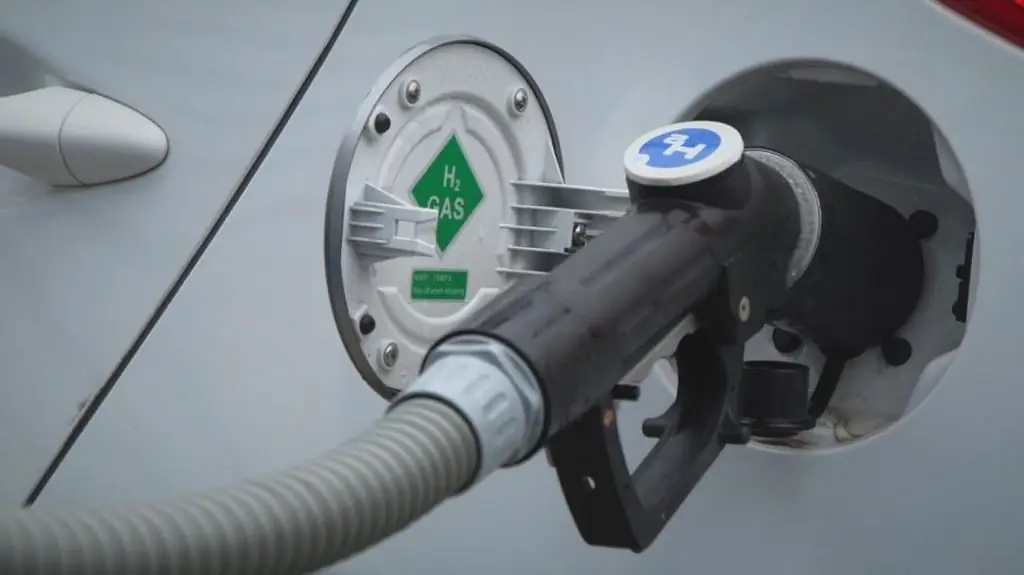
Fuel classification by purpose
Fuel in gaseous form is used both in thermal installations and in internal combustion engines. Accordingly, on this basis, it can be divided into motor fuel and boiler-furnace fuel.
Natural gas is traditionally used as boiler and furnace fuel. In rare cases, artificial fuel is used. The same type of fuel, with only some additives, is also used to refuel cars.
Description of natural gas
It is difficult to overestimate the importance of this mineral for the economy of our state and the economic development of the world as a whole. Many cars, gaseous fuel boilers, power plants and combined heat and power plants use it. Based on the projected prices for blue fuel (as natural gas is sometimes called), state budgets are drawn up.
More than 90% of this gas consists of methane molecules (CH4). In addition to methane, natural gas also contains butane with propane, nitrogen, carbon dioxide, water vapor and other impurities (they are considered harmful). ATIn small quantities, natural gas also contains inert gases (helium and others). It is believed that the latter have a beneficial effect on machines, devices and mechanisms operating on gas, and also improve the physics of fuel combustion processes. The suitability of fuel for use, its quality is judged by the percentage of hydrocarbon components.
Natural gas is not only a valuable fuel, but also a raw material for a number of industries. So, from the methane it contains, large chemical plants produce hydrogen. For this reaction to take place, it must be oxidized. In addition to hydrogen, acetylene is produced from it. Based on these substances, all kinds of aldehydes, methyl alcohol (a very toxic and dangerous substance), ammonia, acetone, acetic acid, and so on are produced. However, the fact remains that the main area of application of natural gas is the combustion of gaseous fuels for the purpose of various drive mechanisms (car engines) and boiler devices.
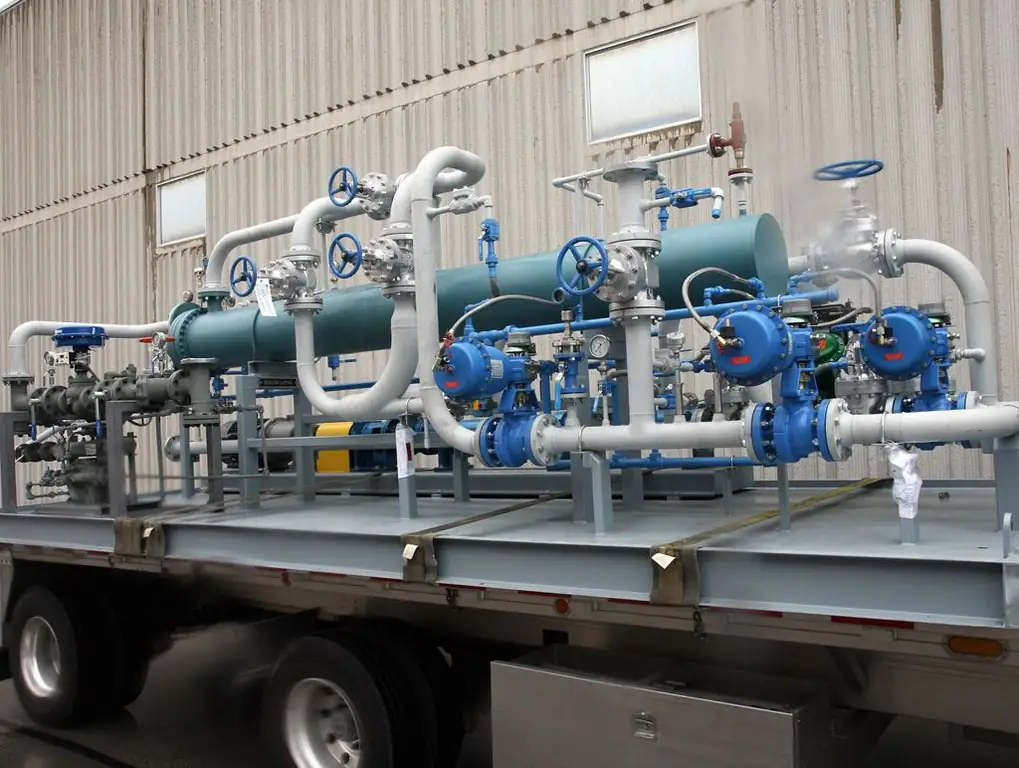
Basic properties of gases
All gases (not just fuel) are united by a relatively small density index. For the considered natural gas and its artificial analogues, its value is kept in the region of 0.8 kilograms per cubic meter. The density of liquefied gaseous fuel is slightly higher and is approximately 2.3 kilograms per cubic meter.
Gases are mostly toxic substances. Toxicity increases as the content of carbon oxides increases andsulfur compounds with hydrogen in gas. With a content of one or more percent of the described harmful gases in the atmosphere, a person will inhale a lethal dose of a poisonous substance in three minutes.
The gases in question are explosive. Moreover, with an increase in the percentage of carbon monoxide and hydrogen, the risk of detonation increases. An interesting feature: when the content of these substances is more than 74%, the probability of gas detonation is almost zero.
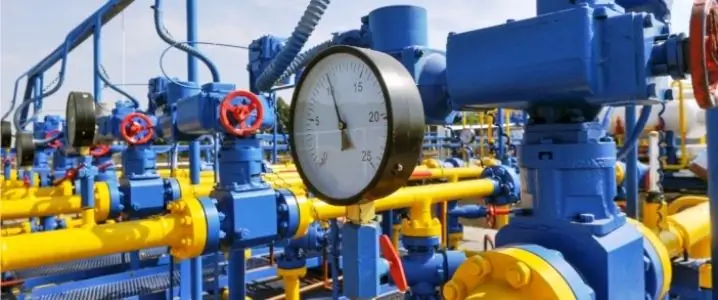
Key fuel characteristics
In a comparative analysis of a particular type of fuel, experts operate with the following concepts: fuel moisture, sulfur content, ash (residue), calorific value and heat output.
Heating capacity refers to the temperature sufficient for the combustion process with a minimum oxygen content. At the same time, neither air nor combustible mixture is additionally heated.
The solid residue from the combustion field is called ash. She can no longer burn. Slag is the same ash, only after melting. The formation of this substance adversely affects the operation of the entire system, clogs the fuel equipment. Therefore, this indicator is important to take into account during design work.
An important indicator is moisture. It negatively affects the characteristics of the fuel. Its presence causes an increase in exhaust volumes, a decrease in the efficiency of the installation.
Combustion products of sulfur and its compounds cause and activate corrosion processes on surfacessteel parts of engines and exhaust systems. In addition, they have a negative impact on the environment and human he alth. Therefore, this indicator is also very important to consider.
The calorific value is a very important characteristic. It is taken into account in the calculation and design of equipment and allows you to determine the fuel consumption. This value is determined experimentally. For these purposes, a special calorimeter is used. A known amount (mass) of fuel is burned and the change in the water temperature of the calorimeter is recorded. Then it is enough to substitute the obtained information into the formula and calculate the heat of combustion.
Associated gas
If natural gas is extracted from boreholes, associated gas is a by-product of oil production. The content of methane in such gas is somewhat less than in traditional natural gas. However, combustion of gaseous fuels produces comparable heat.
Associated gas is also produced by metallurgical plants. At these enterprises, fuel is emitted in furnaces. These are the so-called coke oven and blast-furnace gases. As a rule, these gases are burned on site (fed to a furnace or boiler station). A similar by-product is produced in deep mines, which often leads to disasters.

Gas production by dry distillation
Artificial gas is obtained by additional processing of solid (liquid) fuel. In this way, so-called producer gas and dry distillation gas can be obtained.
When drydistillation fuel decomposes under the influence of high temperatures. In this case, it is necessary to exclude the access of an oxidizing agent (air). After a series of steps, the original fuel decomposes into its own gas, tar compounds and coke. The exact composition of the products formed depends on the initial composition of the fuel and the conditions of the process (primarily on temperature).
The distillation process, which takes place at high temperatures (in the region of 1000 - 1100 degrees Celsius), is called coking. The decomposition products in this case are the actual gas (coke) and coke. The density and heat of combustion of the resulting gas are relatively low (0.5 kilograms per cubic meter and 16,000 kilojoules per cubic meter, respectively). One ton of coal during this treatment is converted into 350 cubic meters of gas. This indicator may vary and depends on the conditions of the process and on the chemical composition and origin of the feedstock (coal).
There is also low-temperature dry distillation. It consists in processing solid fuel with temperatures in the region of 500 degrees Celsius. With this method, a minimum amount of gas is formed (no more than 30 cubic meters per ton of raw materials). The main product in this case is resin, which is further used in the production of motor oils and fuels.
Getting gas through gasification of solid fuels
One of the common methods for obtaining gaseous fuels is the so-called gasification. It consists in the chemical-thermal treatment of solid fuels (the combined effect of high temperaturesand chemical processing). The carbon atoms contained in solid fuel interact and react with water and steam, forming a gas (fuel). During the gasification process, dry distillation also occurs. A gas generator is a device for the gasification of solid fuels (primarily coal). This device produces the following substances: methane, hydrogen and carbon monoxide. In addition to sounded gases, non-combustible substances are also produced (carbon dioxide, oxygen with nitrogen and water vapor).
Designs of gas generators - a huge variety. The scheme and the list of nodes depends primarily on the type of feedstock. In general, it is a cylinder with metal walls. It has openings for ventilation (air intake) and for the exit of the generated gas. Air supply is forced, using powerful fans. The design must provide a hatch for the operator. Fuel is loaded through the roof. Thus, outwardly, this unit painfully resembles the well-known "potbelly stove". However, there is one difference - the absence of a chimney.
The gas generator is just the basis of the entire installation, the core, so to speak. If you look at the diagrams of such equipment, it becomes clear that all other components and devices are designed to bring the gas to a normal state (cleaning, cooling, and so on).
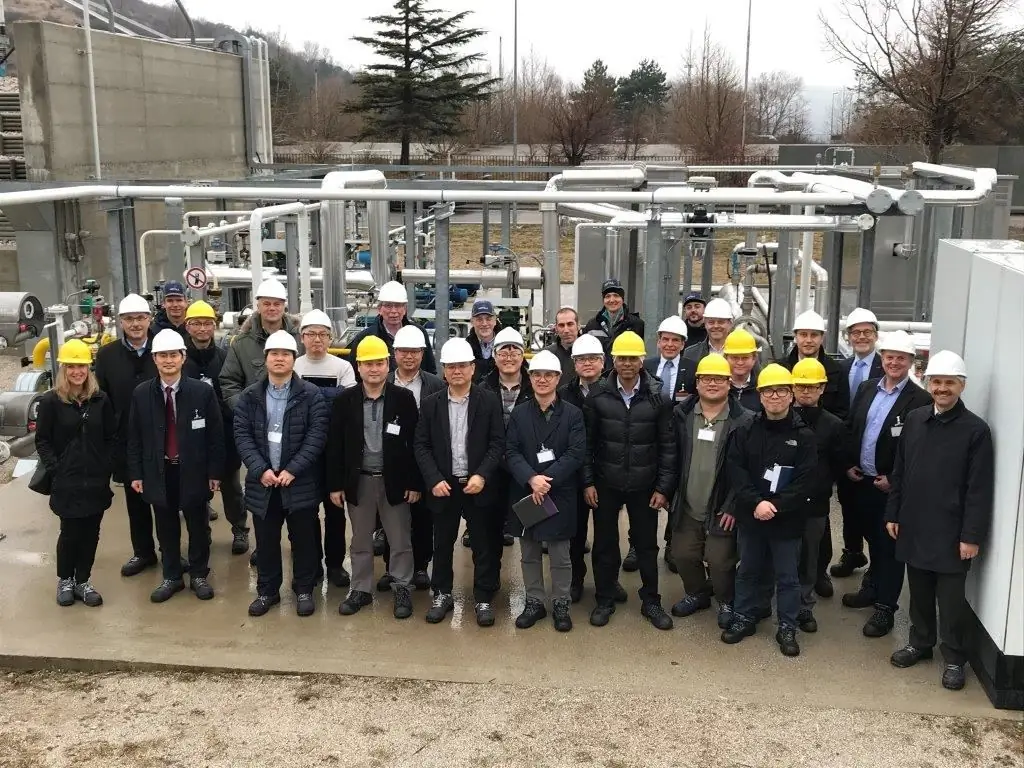
Advantages of using and using gas
The composition of gaseous fuel allows it to be effectively used as an alternative to traditional gasoline, fuel oil anddiesel. Oil reserves are depleted. According to experts, it will last for several decades. There are much more gas reserves. Thus, the active introduction and use of gas equipment in all sectors of the national economy will, if not solve, then at least postpone the acute problem of the shortage of hydrocarbon raw materials.
The second and very important advantage is the relative purity of gas combustion products compared to gasoline engine exhausts. In other words, machines and mechanisms operating on gaseous fuels are more environmentally friendly and do not pollute the environment so much. In metropolitan areas and large cities, this problem is especially acute. Therefore, the authorities are striving to transfer the entire fleet of urban public transport to new environmental standards.
The third advantage is the ability to adjust the engine to personal needs and preferences by adjusting the composition of the mixture. In the future, this will allow you not to overpay extra money.
The fourth benefit is to increase the useful life of the engine and increase the time between complete engine oil changes. After all, gas, unlike petroleum products, does not remove grease (oil) from the surfaces of the rubbing parts of the mechanism (engine).
Fifth - the gas mixture has a much greater detonation ability compared to traditional fuel. This allows you to significantly increase the power of the vehicle's engine.
Sixth - unlike solid and liquid fuels, gaseous fuels do not need to be heated before injection. It's positiveaffects both the reliability of the entire system and all performance indicators without exception.
Seventh advantage: with the use of gas injection into the cylinders becomes more uniform. Thus, smoothness of the course and operation of driving mechanisms increases, wear of highly loaded parts decreases.
Unfortunately, not always all the described benefits are achieved. Most often, vehicle owners convert gasoline engines to gas fuel in order to save money on the difference in fuel costs. However, the engine was designed for gasoline or diesel. Hence the not very well-coordinated work of all parts. Engineers have calculated that when a car is switched from petrol to gas, the engine loses about 20 percent of its power. To compensate for the loss, many owners increase the compression ratio of the combustion chamber space. This greatly reduces the life of the engine. Another measure is the installation of a turbocharging system. But this event will have to invest a lot of money. The operation of an engine or boiler house on liquid and gaseous fuels demonstrates completely different performance indicators. Moreover, the advantage is far from being on the side of solid fuels.
Recommended:
Solid fuel is Types, characteristics and production of solid fuel
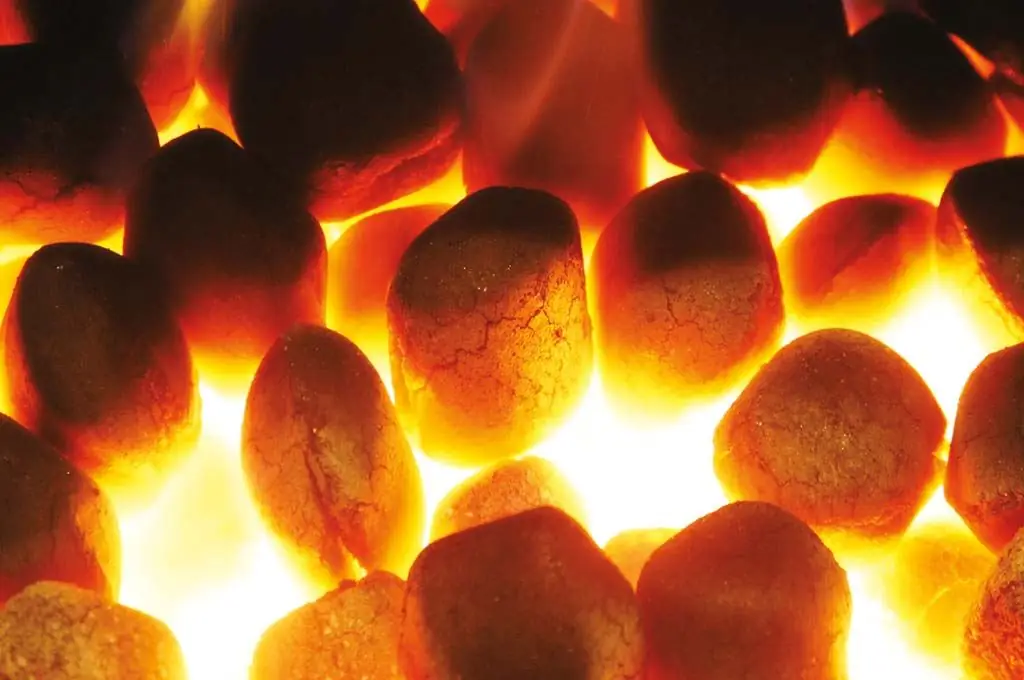
Non-fossil solid fuel based on wood and industrial waste - affordable and efficient fuel. The modern market offers a wide range of solid fuels, differing in efficiency and characteristics
Gas production. Gas production methods. Gas production in Russia
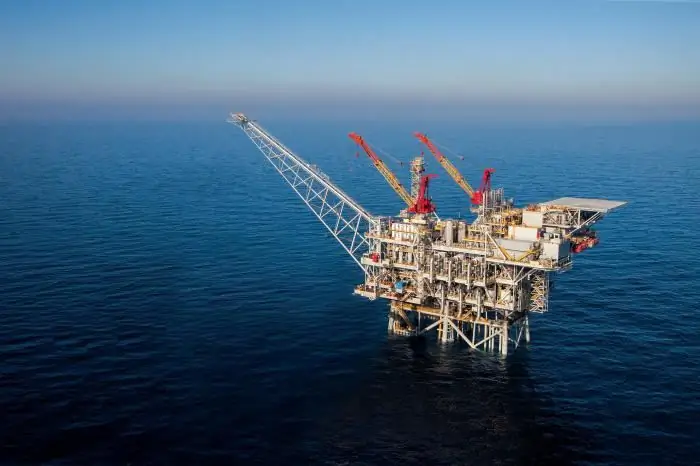
Natural gas is formed by mixing various gases in the earth's crust. In most cases, the depth of occurrence ranges from several hundred meters to a couple of kilometers. It is worth noting that gas can form at high temperatures and pressures. In this case, there is no access of oxygen to the place. To date, gas production has been implemented in several ways, each of which we will consider in this article. But let's talk about everything in order
Diesel fuel: GOST 305-82. Characteristics of diesel fuel according to GOST
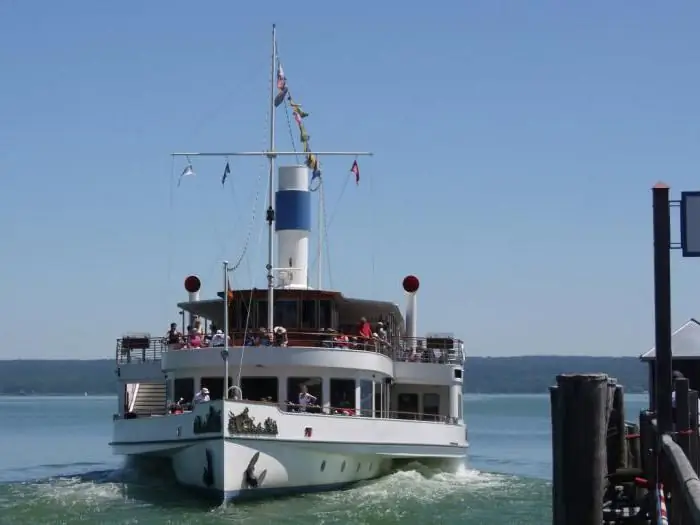
GOST 305-82 is outdated and replaced, but the new document, which came into force at the beginning of 2015, did not change the requirements for diesel fuel for high-speed engines so noticeably. Maybe someday such fuel will be banned for use altogether, but today it is still used both in power plants and on diesel locomotives, heavy military equipment and trucks, the fleet of which has been preserved since the days of the Soviet Union due to its versatility and cheapness
Flow methods of production organization: parameters, characteristics and standards. The need for this method in production
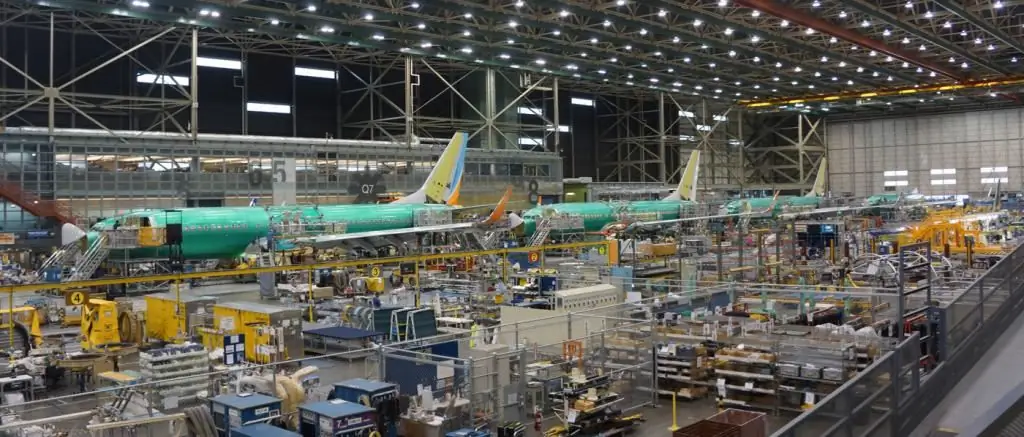
Today, in-line production is the most progressive form of organization of the production system. Optimal speed of work, minimum labor intensity and maximum quality of production - this is not a complete list of the advantages of the method under consideration
Fuel consumption of an aircraft: types, characteristics, displacement, amount of fuel and refueling
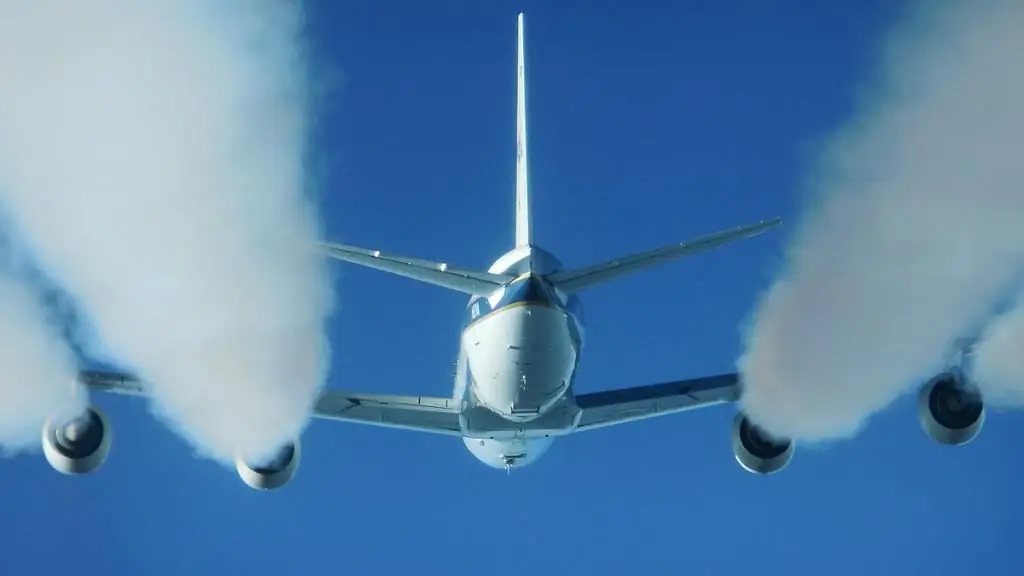
Fuel consumption of an aircraft is one of the important indicators of the efficient operation of mechanisms. Each model consumes its own amount, tankers calculate this parameter so that the airliner is not loaded with excess weight. Various factors are considered before allowing a departure: flight range, availability of alternate airfields, weather conditions of the route