2025 Author: Howard Calhoun | [email protected]. Last modified: 2025-01-24 13:10
An electroplating shop is currently needed in order to apply a special coating to a metal product. By itself, this material is subject to corrosion, and its service life is not too long. That is why a method is used in which a thin layer of another metal is deposited on the surface of the raw material in an electrolyte solution and using electric current. This is the main purpose of the electroplating shop.
Equipment for work. Bath
In these workshops there is a variety of equipment, but the main one is a galvanic bath. This device is divided into two types. The first is called active, the second - auxiliary. They differ in that in the first types of baths, the desired coating is directly applied to the product. In the auxiliary equipment of the electroplating shop, the stage of preparing the part for the further procedure takes place. Here it is important to understand that auxiliary equipment is just as important as the main one. Among them are washing, drying, mixing baths.
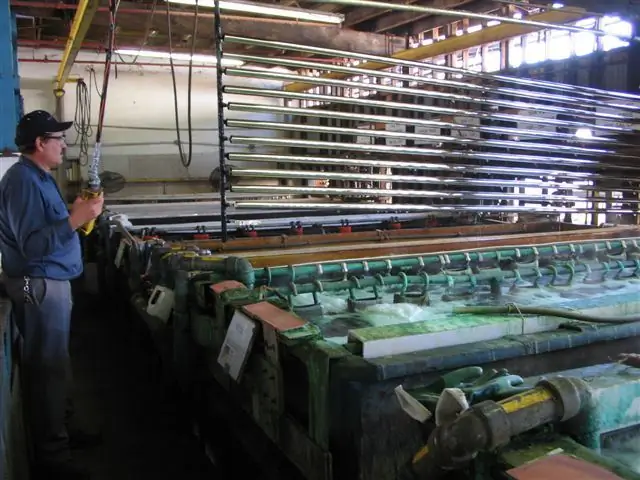
Bath design
By their design, the electroplating shop baths are quite simple and are a cube that has additional stiffening ribs, as well as some additional elements. Among such additional devices, for example, there is a heating element, a cover, filtration, a cooling system, a water supply and discharge system, cleaning systems, suspensions, anodes, and more.
Stainless steel, PVC, polypropylene, and other raw materials with similar characteristics can be used for the production of such things. However, PVC and polypropylene are currently the most widely used, while steel and metal products have faded into the background. This is due to the fact that polymer materials are more resistant to aggressive chemicals and high temperatures.
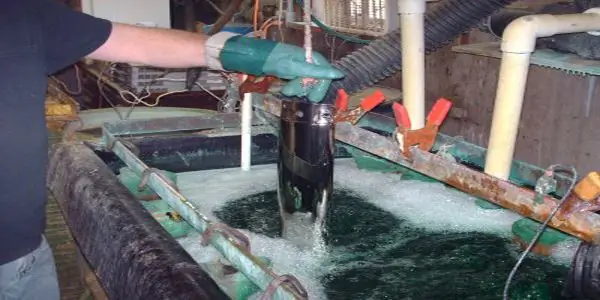
Special Purpose Devices
The electroplating industry needs special purpose baths that are designed to work with small parts.
The first equipment of this type is a bell bath. The main difference between this type of device and the main one is that it has a special bell, and the main purpose is to apply galvanic coating to small parts in bulk. The bell itself is truncated and has a multifaceted design. Such a device is used both as an independent machine and in line.
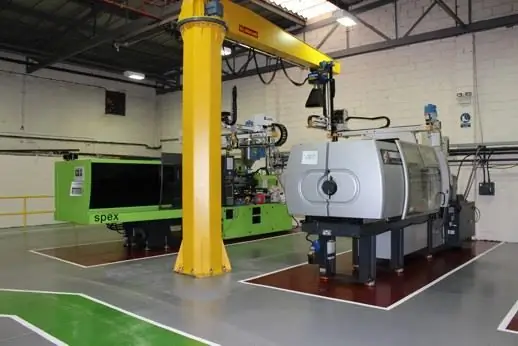
Electroplating production periodically needs equipment such as a galvanic type drum. It is a prism thatmade of either PVC or polypropylene, which has many facets, and all of them are perforated. To rotate such a prism, a motor with a gearbox is used, and the torque is transmitted through a system of gear-type wheels. You can use the drum in a manual, automated and mechanized type of line.
What is a line
Galvanic line is a set of several devices that operate in one area. The main parameters for the design of such systems are their performance, as well as the dimensions of the product for which this line should be designed. The type of the line will directly depend on how large the dimensions of the product will be and what kind of serialization it will have. Galvanic lines can be of the screw type, they can be manual or manual with a hoist. Today, the automatic operator line type with program control is becoming very popular.
Auxiliary equipment may also be included in the line. It is necessary in order to withstand the technological process, as well as to ensure the complete safety of the work of people on the site.
Varieties of auxiliary installations
Electroplating equipment used in the field should prepare raw materials and components for further work. For this, for example, there are two filter installations. One of them is stationary, the other is mobile.
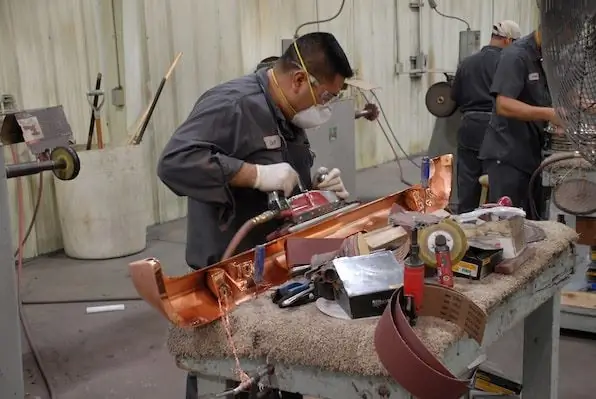
If we talk about the first type of installation, then the UFE-1C model is usually used. It is intended forfiltration of either water or electrolyte from any impurities of a mechanical type. An additional feature of the stationary type is that it can be connected to an airless mixing system, where there is a solution filtration function.
The mobile type filter is usually represented by the UV 2400 model. It can be used, like a stationary one, to filter the electrolyte or water from mechanical impurities. Their difference lies in the fact that this pump can also pump this water or other aggressive chemicals.
Liquid demineralization devices are also used. The unit is presented in the form of the UVD-500 unit, which is capable of removing s alt from the liquid so that it fully complies with such a state standard as 6709-97. This water is used for the preparation of new electrolyte, as well as for any washing operations carried out in the shop.
There are also smaller scale equipment, such as conventional pumps, but with increased resistance to chemicals in order to successfully pump the electrolyte. Drying equipment is used.
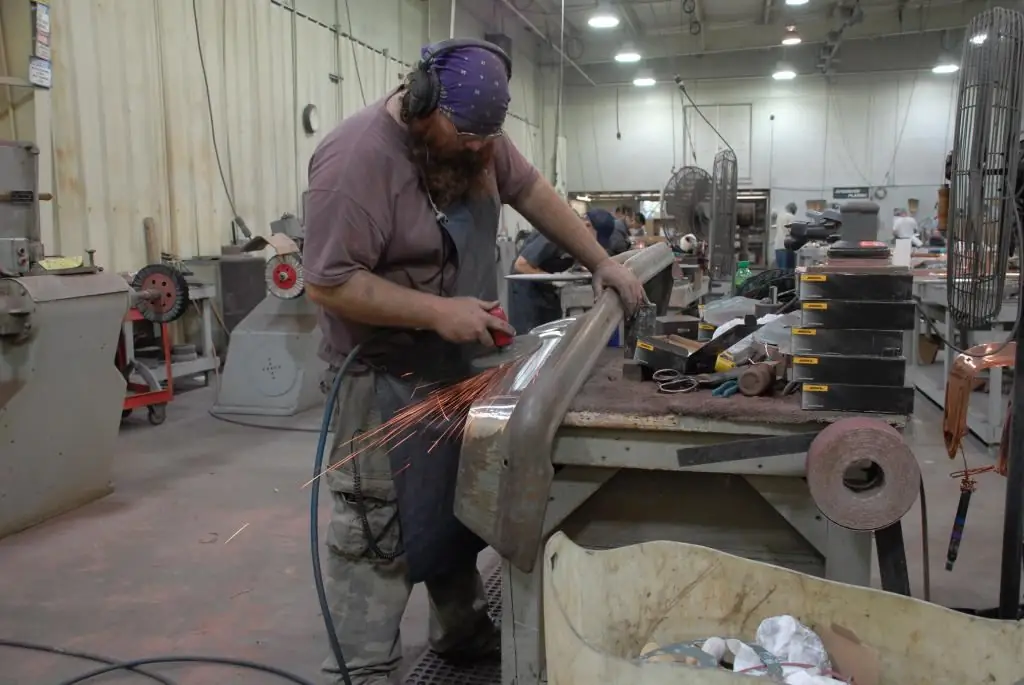
Ventilation
Ventilation of the electroplating shop is one of the most important safety requirements. This is very important, because during the galvanic process, that is, coating products, harmful vapors are released into the air, which are dangerous not only for humans, but also for the room where they are released. Because of this, when designing a workshop, special attention is paid to ventilation equipment andventilation in general.
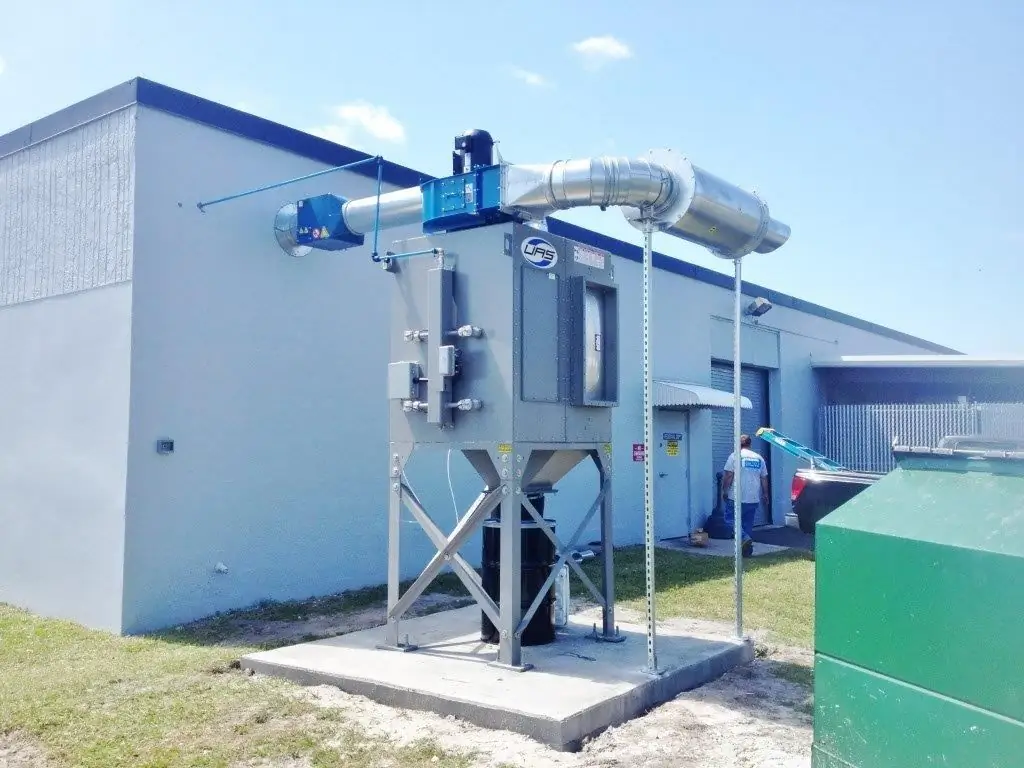
Polypropylene ventilation pipes are allowed for this type of workshop. This is due to the fact that this material belongs to the group of non-combustible, is moisture-proof, resistant to chemical attack, and it is also very easy to mount them both on the ceiling and on the floor or walls.
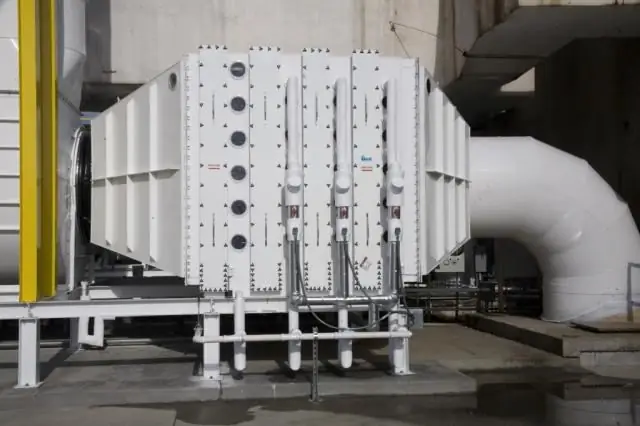
Shop Safety
The hazard of the electroplating shop for human he alth is quite high. The thing is that there are several very dangerous factors. Firstly, there is the possibility of receiving a strong electric shock, secondly, there is a risk of chemical, alkaline or acid types of burns, and thirdly, there is a risk of explosion and ignition.
However, the harm to human he alth does not end there. For example, when preparing a product, it is subjected to mechanical types of processing. This can be grinding, blast cleaning using mechanical dust, and many others. All of them are united by the fact that during their conduct a huge amount of dust is released into the air. In addition, the level of noise and vibration exceeds the permissible. Since an electric current is applied during coating, the probability of being hit by this very current is greatly increased. For this reason, 12 V direct current is most commonly used. However, there are some operations that require a voltage increase to 120 V. For example, this happens when aluminum is oxidized.
Fire safety requirements forelectroplating shops are also quite high. To prevent fire in such premises, it is necessary to use fire prevention and fire protection systems that will comply with GOST 12.1.004-76. Explosion safety in such areas must be ensured using explosion prevention and explosion protection measures in accordance with GOST 12.1.010-76.
Fluid cleaning
It is worth saying that electroplating shops should have facilities for cleaning the liquid that was used in the work. This is very important, because during the technological process, water is mixed with acids, alkalis and heavy metals. Conventional water treatment plants are unable to cope with such pollution, and therefore, when designing a building, you must initially allocate space for special installations.
Chromic anhydride
From a technical point of view, this is a combination of two substances such as chromium and oxygen. It is often used in the chemical industry, and therefore is often called a chemical acid. This substance is quite soluble in water, which is excellent for use in shops where most operations are carried out with liquid content to one degree or another. Chromic anhydride is currently most widely used in three areas: mechanical engineering, metallurgy, chemical and petrochemical industries. Depending on its purpose, this substance is produced in three categories: A, B and C.
- Grade A is used when under production conditionsyou need to get metallic chromium or other materials, but with sufficiently high hardness.
- Grade B is used for the production of electrolytic chromium and in the production of catalysts. It is this anhydride that is used in electroplating shops.
- As for Grade B, it is most suitable for raw material foundry operations.
Generally speaking, this type of workshop is extremely necessary, but at the same time quite harmful and dangerous. Because of this, all safety requirements must be met in it, as well as the best ventilation.
Recommended:
Oxyfuel cutting of metal: technology, necessary equipment, safety precautions
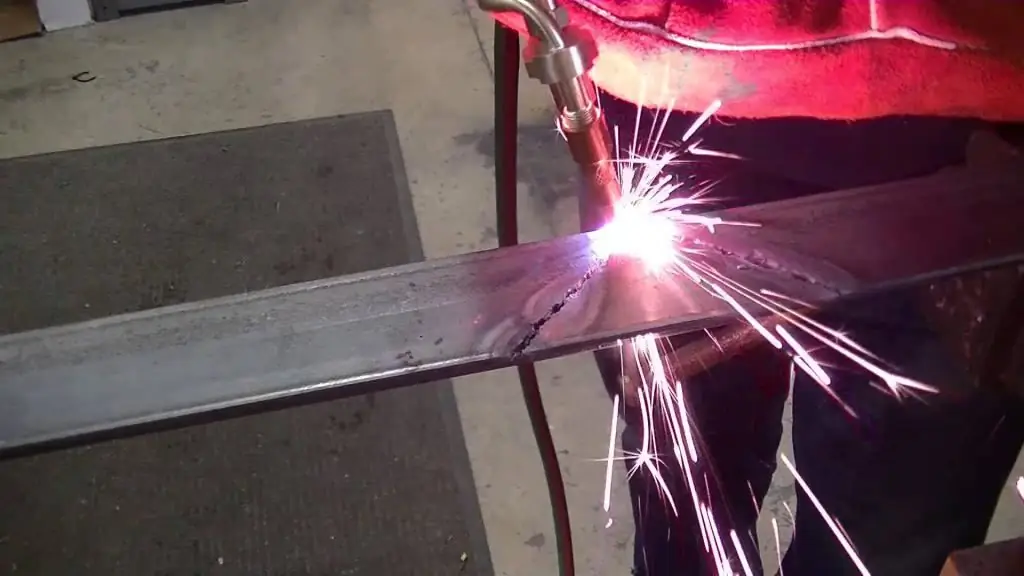
Oxy-fuel cutting of metals (in the literature you can find the term "oxy-fuel cutting") is actively used in industry for cutting sheet material from steel and other alloys into workpieces of the required length. The article contains information about the technology itself, about the necessary equipment and basic safety precautions for oxygen cutting of metals and other materials
Electroplating. Electroplating technology. Electroplating
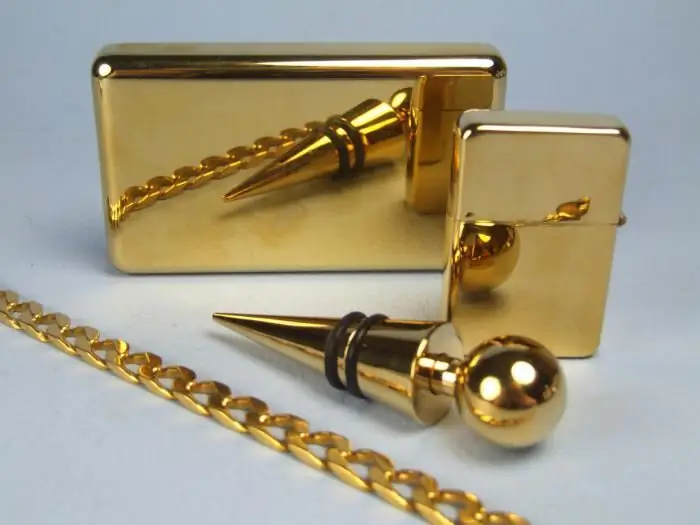
Electroplating is a method of coating one metal with another by means of electrolysis. This procedure is carried out using traditional immersion methods
Busbar installation: technology, equipment, safety
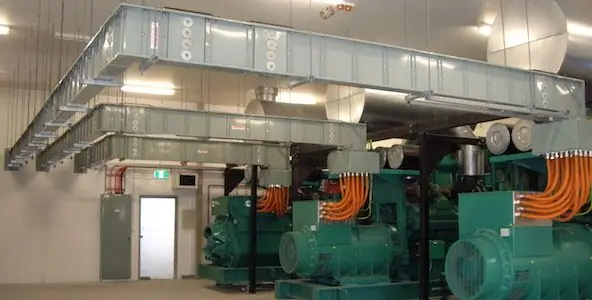
The quality of laying power lines depends not only on the stability of equipment and communications, but also on the safety of personnel. Busbar trunkings help organize reliable and compliant wiring, the installation of which increases the design possibilities when laying cables, and also provides a high degree of physical protection from external threats
Occupational safety specialist: job description. Occupational Safety Specialist: Key Responsibilities
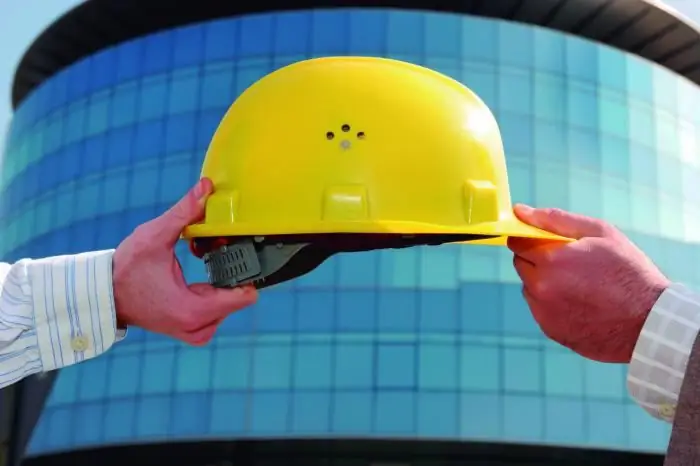
As you know, every employee in any enterprise should have their own job description. The labor protection specialist is no exception to this rule. He, like other employees, has a number of duties and functions that undoubtedly require a detailed presentation on paper
Industrial safety of hazardous industrial facilities: rules and requirements
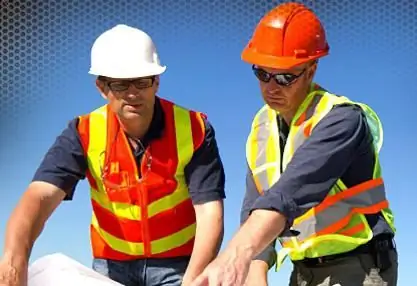
In modern production, unfortunately, there are accidents. However, there are special instructions, the observance of which helps to prevent disasters. Consider further the basic rules of industrial safety