2025 Author: Howard Calhoun | [email protected]. Last modified: 2025-01-24 13:10
Electroplating is a method of coating one metal with another by means of electrolysis. This procedure is carried out using traditional immersion methods. After preliminary preparation, printed circuit boards are loaded into a galvanic bath, which is a container made of a dielectric, which is filled with an electrolyte and equipped with anodes (they can be soluble and insoluble), as well as a device for maintaining the temperature and mixing the solution.
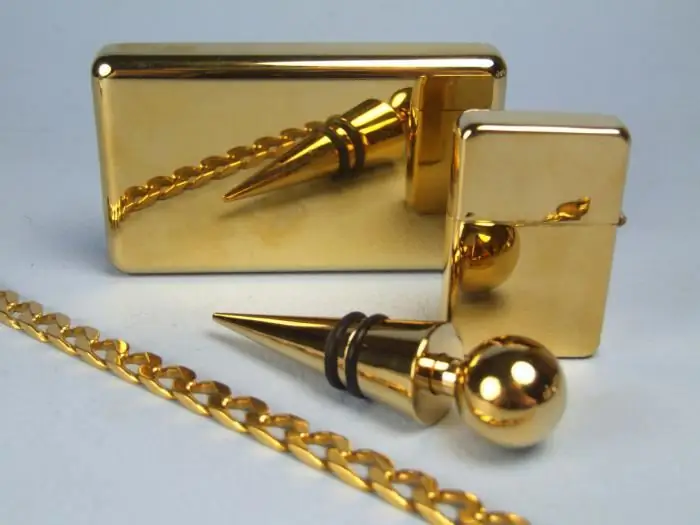
Card processing
The transmission of direct current leads to the fact that the sections of the board not covered by a protective mask and connected to the electrode are covered with a layer of nickel or gold of a certain thickness. Proper positioning of the anodes ensures that the coating thickness is approximately uniform.
Printed circuit board gilding is usually done using a two-stage process. First, they are immersed in a bath where nickel is electroplated. In this case, a high current density is used, due to which a layer of nickel is deposited from the acid solution, the thickness of which is 0.05-0.1 μm. Therebya strong adhesion of nickel and copper is provided, which makes it possible to reduce the porosity of the coating, as well as to prevent the penetration of copper into the gold layer. After washing, the products are usually transferred to the gilding bath, where the gold layer is built up to 0.5 microns from the electrolyte.
Electroplating and decoration
Already in ancient times, there was a decorative finish of artistic metals. Modern production suggests that galvanic treatment will be used to impart some special properties to the metal surface. Precious metal protective coatings can be obtained by the deposition of metals from saline solutions under the action of an electric current. Thanks to such coatings, it is possible to preserve the color and brilliance of jewelry for quite a long time. They not only prevent darkening of products, but also have an excellent polishing effect. For example, electroplating with gold or silver allows you to retain the color and brilliance of jewelry for a long time.
There are several different variants of this process, each of which involves the use of a particular metal:
- chrome plating;
- copper plating;
- galvanizing;
- Nickel plating;
- tin-bismuth coating;
- chemical oxidation;
- chemical passivation;
- anodizing;
- electropolishing.
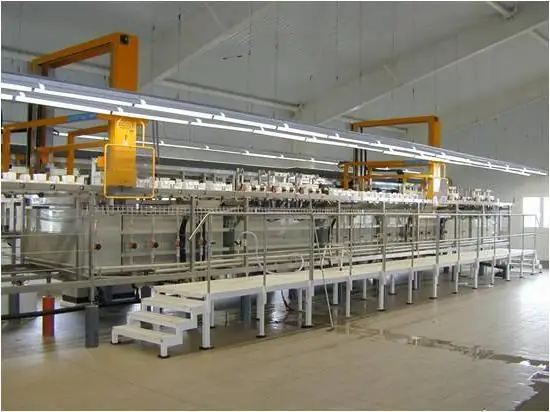
Chrome plating
This is a diffuse saturation of the steel surface with chromium or deposition on the details of a layer of substance from the electrolyte underthe action of an electric current. In this case, electroplating is focused on corrosion protection, used for decoration or to increase the degree of surface hardness. Chrome plating in industry can also be used for decoration. In this case, the main goal of the procedure is to give the metal surface a beautiful spectacular shine. The part must be polished before applying chrome.
Coating Properties
Hard chrome plating is characterized by heat resistance, high wear resistance, poor wettability, low friction coefficient, and low ductility. In addition, the surface obtains properties such as resistance to friction, the ability to withstand a distributive load, as well as the disadvantage of being easily broken under the action of concentrated impact loads. Electroplated coating in the form of milky chromium has a low degree of wear resistance and hardness, low porosity. The surface is protected from corrosion while maintaining an attractive decorative look.
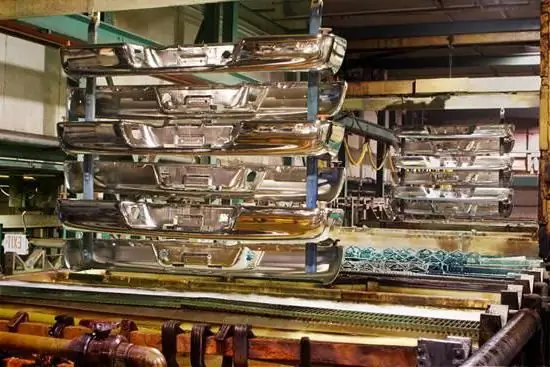
Use of chromium plating in industry
The main purpose for which it is used in industry is to give the part properties such as increased wear resistance, increased corrosion resistance, and reduced friction. Thanks to this process, steel becomes stronger, does not undergo gas corrosion, and also does not collapse in sea and ordinary water, nitric acid. Electroplating of this type leads to the fact thatsurface imperfections only get bigger, requiring post-processing as there is no leveling effect.
Copper plating
The use of copper coatings is relevant in cases where it is necessary to increase electrical conductivity, and they are also used as an intermediate layer on steel products before chromium, nickel or other coating is applied. This results in better grip and improved protection. Electroplating with copper is not usually used as a stand-alone or decorative. Due to the fact that this metal is able to prevent the formation of sparks, the product can be used in the oil and gas industry.
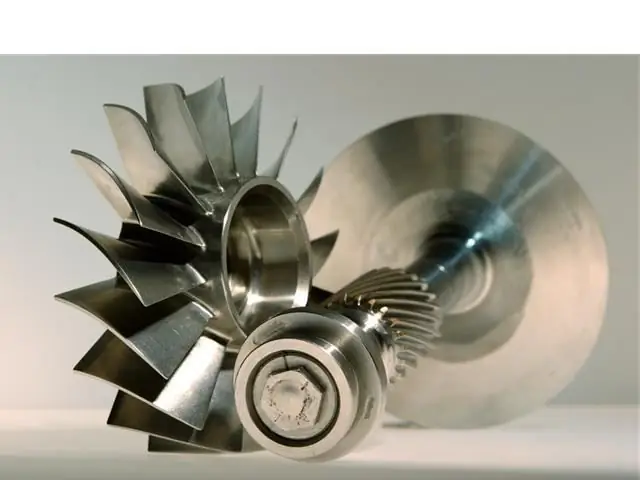
Copper plating application
This process is used to apply copper plating to steel products or steel wire. Often this type of coating is used to protect individual sections of steel products from cement, while processing those sections that are supposed to be machined further.
Electroplating of metals in this case is often used in the oil and gas industry to eliminate the formation of sparks, in the electric power industry for subsequent application of multi-layer coatings intended for protection and decoration, in the production of printed circuit boards, to improve soldering, and also for many another. The surface acquires a color from light pink to dark red. Shades are usuallynormalized.

Zinc coating
One of the most common methods for protecting metal products is zinc plating. It is usually used to process a variety of alloyed or carbon steel grades. Electroplating of this type is quite in demand for the protection of wire products and fasteners. Once in a humid environment, the zinc surface acts as an anode, which slows down oxidative reactions, while the base metal receives reliable protection from negative environmental factors.
This type of electroplating can only be used after metal products have been processed in a special way. To do this, they should be cleaned of rust, scale, technical means of lubricating and cooling purposes. When the galvanizing process is completed, the product must undergo clarification, that is, it is pickled with a weak solution of nitric acid, after which passivation is carried out. So not only it is possible to increase the resistance of galvanized products to negative factors, but also to make them more decorative, that is, to give shine and a certain shade. Electroplating technology in this case assumes a zinc layer thickness from 6 microns to 1.5 mm.
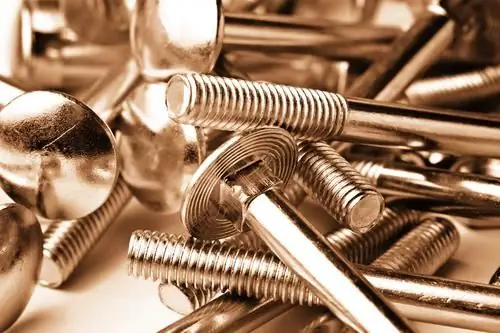
Nickel plating
Protection of metal products can be carried out using various technologies. One of the most popular and widespread at the moment isnickel plating. Such popularity is due to the chemical properties of nickel. It has a high degree of resistance to corrosion in the aquatic environment, and nickel oxide prevents subsequent oxidation of the metal. In addition, nickel is weakly affected by s alts, acids and alkalis, with the exception of nitric acid. For example, a galvanized coating with a thickness of 0.125 mm reliably protects against most industrial gases, which are characterized by increased aggressiveness. This point is also very important: almost all metals lend themselves to nickel plating, so this method can be used for additional processing of products.
The use of nickel plating is appropriate for a range of applications:
- ensuring the protection of metal products;
- use as a decorative coating;
- formation of a preliminary layer, which will be subjected to further processing;
- restoration of parts and assemblies.
The coating is characterized by increased wear resistance and hardness and is recommended for parts that operate in friction conditions, especially in the absence of any lubrication, is used to protect against corrosion, as well as to ensure high-quality soldering of low-temperature solders, all this is prescribed in GOST. Electroplated coatings are highly brittle, so it is not recommended to perform flaring and bending of parts that have undergone nickel plating. It is recommended to use it for complex profiled parts. After the heat treatment procedure at a temperature of 400 degrees Celsius, the coating acquires the maximumhardness.
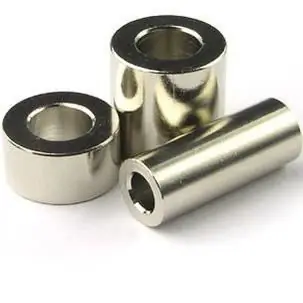
Tin-Bismuth
Tin plating is resistant to sulfur compounds and therefore recommended for parts that come into contact with rubber and plastics. Among its properties are excellent adhesion to the base metal, elasticity, ability to bend, draw, stamp, flare, press fit, as well as good retention during make-up. Freshly deposited tin plating lends itself well to soldering.
Conclusions
Electroplating improves the conductive characteristics of parts, giving them excellent electrical insulation properties, as well as protecting them from various substances. In addition, this method allows you to get excellent surfaces that have a mirror appearance, as well as imitating enamel coating. It is difficult to overestimate how important electroplating is in modern production, as the development of technology has made it possible to make the process more perfect.
Recommended:
How to make glass? Glass production technology. glass products
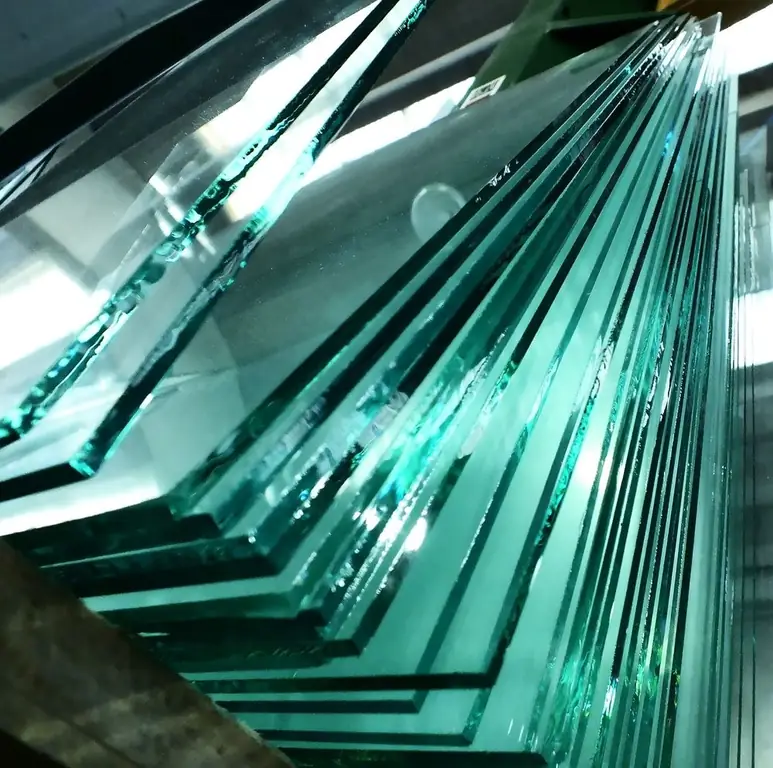
Glass is familiar to everyone. But the process of making it is extremely exciting. Each stage is important and affects the quality of the final product. The basis is sand, soda, lime. The process is almost entirely automated. Surprisingly, glass can even be made at home
Heat-treated wood: main characteristics, production technology, pros and cons

Almost every one of us has come across such a concept as heat-treated wood. However, few have thought about what it really means. Meanwhile, this material can be considered innovative. Due to the high temperature - from +150 °C to +250 °C - the material is strong and durable
Keeping bees in multi-hull hives: technology and methods
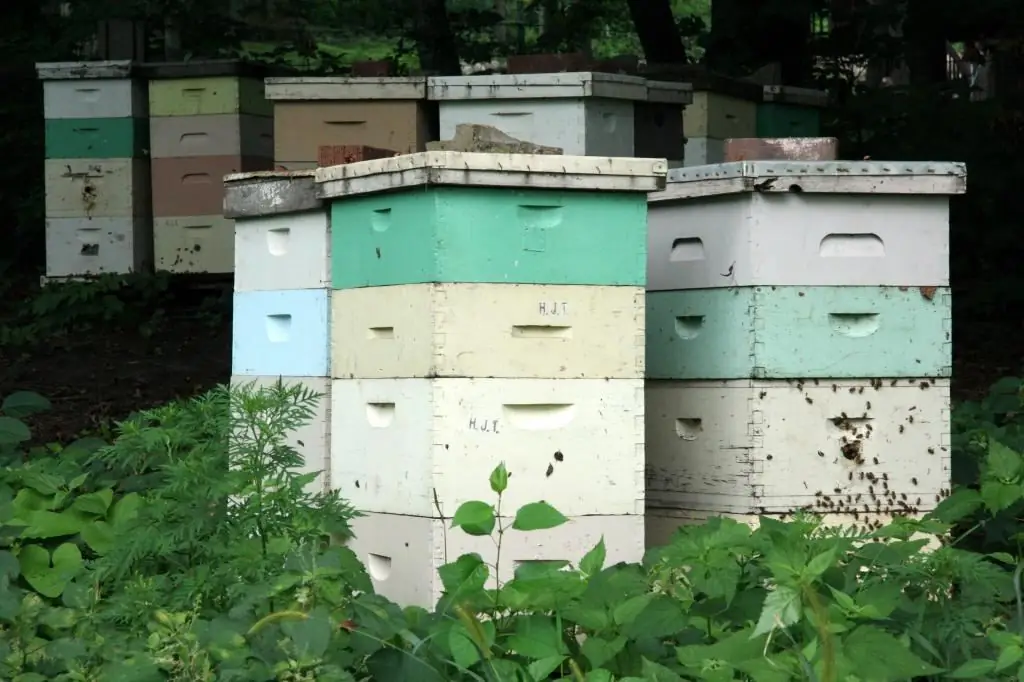
Hives of this design fully meet the modern requirements of beekeeping. The multi-hull variety has gained wide popularity in countries such as America, Russia, Canada and Australia. This is due to the convenience of this design. Keeping bees in multi-hull hives simplifies the work and facilitates the work of the beekeeper several times
Electroplating shop: description, equipment, safety requirements, harmfulness
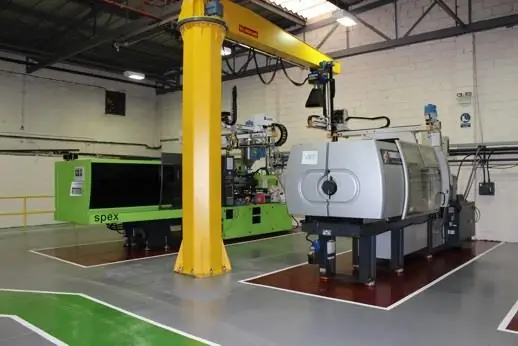
An electroplating shop is a rather important area in any production, however, it is characterized by high danger and harmfulness. In such workshops, it is necessary to equip good ventilation, fire safety and many other protection factors
Resource-saving technology. Industrial technologies. The latest technology
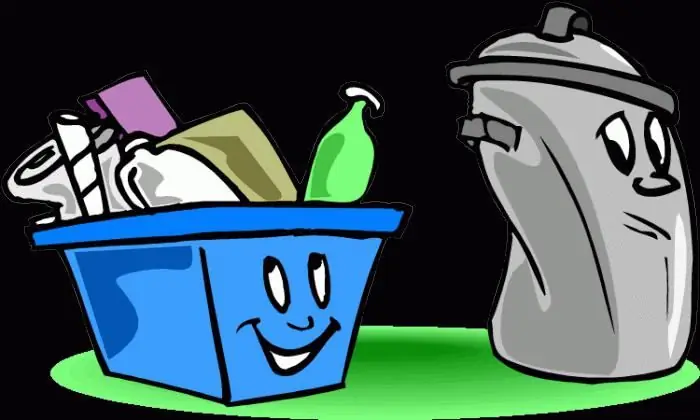
Modern industry is developing very dynamically. In contrast to past years, this development is proceeding intensively, with the involvement of the latest scientific developments. Resource-saving technology is of great importance. This term refers to a whole system of measures aimed at a significant reduction in resource consumption, while maintaining a high level of product quality. Ideally, they try to achieve the lowest possible level of consumption of raw materials