2025 Author: Howard Calhoun | [email protected]. Last modified: 2025-01-24 13:10
The spindle of machine tools is usually presented as one of the elements of the drive mechanism responsible for fixing and shaping the workpiece. At the same time, its interface with the power plant, the bearing part and the working equipment of the unit is so tight that we can talk about the whole infrastructure of this part. One way or another, the spindle assembly (SHU) should be considered as a responsible basic mechanism of the machine, providing the function of transmitting torque and directing the processing force.
Product overview
This mechanism is also called a motor spindle and forms one of the key assembly units of modern wood and metalworking machines. The performance and, to an even greater extent, the accuracy of the mechanical impact on the workpiece depend on its characteristics. As already noted, we are talking about a whole complex of elements,forming the basis of spindle units. Supports, lubrication system, seals, torque transmission and bearing parts form the basis of this mechanism. Mostly these are components that perform supporting and auxiliary functions to ensure the operation of the nozzle in the form of a cutting tool.
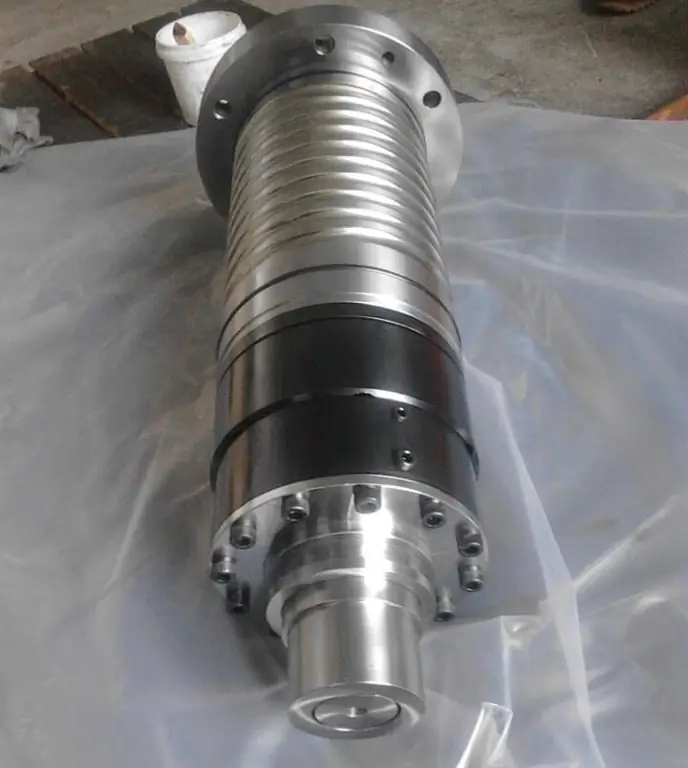
It is generally accepted that the power potential of machine tools primarily depends on the engine. This is true, but only partly. For example, the spindle units of metal-cutting machines have their own frequency range of rotation, causing restrictive conditions for cutting speeds. But it is important to understand that this range is more of a function of adjusting the optimal processing rate with the support of a sufficiently high accuracy.
Another of the key functions of the spindle is the direct holding of the machining tool, and in some cases the workpiece itself. For this kind of fastening, special clamps and clamps are used, like a tool holder and cartridges. Therefore, it is important to take into account the characteristics of the spindle when choosing a tooling according to the dimensions of the shank and determining the permissible parameters of the machining process.
ShU design
During the development of the design solution for the motor spindle, task executors should focus on the maximum reduction of dynamic and vibration loads on the mechanism. Achieving this quality of the working group directly affects the durability of the machine and the quality of processing. For this reason, the spindle assembly is increasinglydesigned as an independent device in a separate housing, which is called a headstock.
The following are taken as initial data for the design algorithm:
- Power.
- Rotation accuracy.
- Speediness.
- Maximum heating for supports.
- Vibration resistance.
- Rigidity.
Based on the initial parameters, a structural scheme, layout details and manufacturing materials are selected. The type of the future machine also has an influence on the selection of certain design solutions. For example, the design of spindle assemblies for high-precision machining equipment is based on the layout of hydrodynamic bearings that can ensure the accuracy of mechanical action in the range from 0.5 to 2 microns. For especially high-speed units with internal grinding heads, special sliding bearings are used, which require air lubrication. Typically, the principles of constructing a spindle base with an emphasis on supporting high processing speeds from 600 rpm are used for diamond boring and universal metal-cutting machines. The parameters of components to support low speeds are traditionally calculated for milling, turret and drilling machines. Here the rule applies, the more delicate the accuracy of the mechanical action, the higher the torque should be at the spindle. For complex roughing and cutting, low RPM configurations are used.
Calculation of the spindle assembly
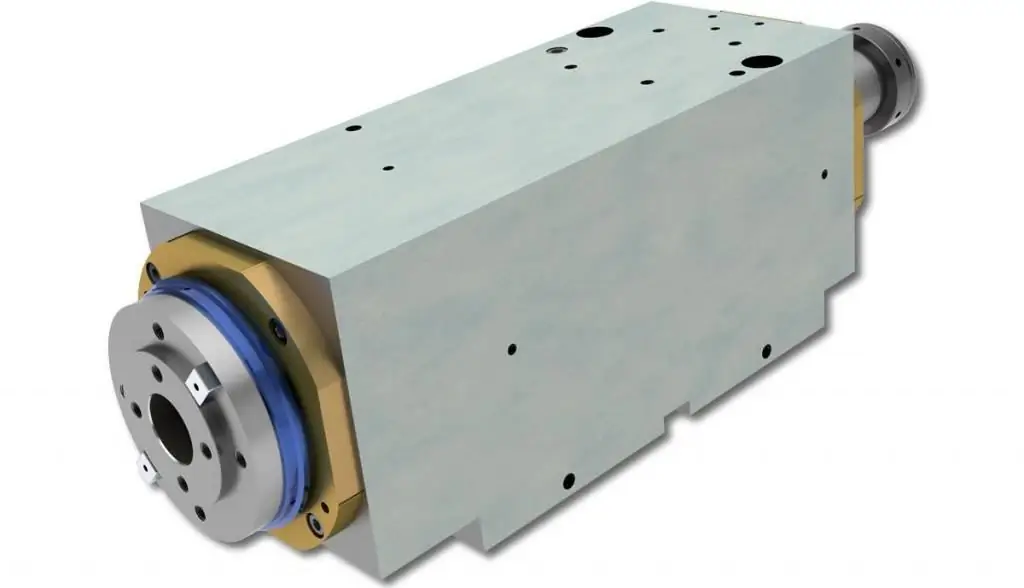
Bstiffness is considered as the main design characteristic. It is expressed as an indicator of elastic displacements in the processing zone under the total acting force from the own elastic deformation of the spindle with its supporting elements. Strength is also used to characterize heavily loaded assemblies, and for high RPM headstocks, a minimum resonance value, i.e. high vibration resistance, will be a key factor in successful processing.
Practically all spindle assemblies for metal-cutting machines are separately calculated for cutting accuracy. This calculation is performed for bearings based on the radial run-out coefficient of the spindle end. The allowable runout value depends on the design accuracy class, in the definition of which the designers proceed from the requirements for the machining process.
The index of radial runout on the inner surface of the bearing ring depends on its eccentricity and the errors of the tracks with rolling elements. This accuracy parameter is expressed through the effect of the so-called wandering beat. In the process of bearing control, their compliance with the established standards is determined, after which, if deviations are detected, the products can be sent for revision. Among the measures to further improve the accuracy of the bearings for the spindle assembly during assembly, the following can be distinguished:
- The eccentricities of the inner rings and bearing journals are in opposite directions.
- Eccentricities of bearing outer rings andbody holes are also placed in opposite directions.
- When installing the eccentricities of the inner rings of the bearings of the rear and front parts, they must be kept on the same plane.
ShU performance
The set of important technical and physical indicators of the spindle is not limited to rigidity and accuracy. Among other significant properties of this mechanism, it is worth highlighting:
- Vibration resistance. The ability of the SHU to provide stable rotation without oscillation. It is impossible to completely eliminate the vibration effect, however, thanks to careful design calculations, it can be minimized by reducing the effect of sources of transverse and torsional vibrations, such as pulsating forces in the processing zone and torque in the machine drive.
- Speediness. Characteristic of the speed of the spindle assembly, reflecting the number of revolutions per minute allowed for the optimal operating condition. In other words, the maximum permissible rotational speed, which is determined by the structural and technological qualities of the product.
- Heating bearings. Intensive heat generation is a natural derivative factor during machining at high speeds. Since heating can lead to deformation of the element base, this indicator should be calculated during the design. The most heat-sensitive component of the assembly is the bearing, whose change in shape can impair the function of the spindle. In order to reduce thermal deforming processes, manufacturers shouldadhere to the norms of permissible heating of the outer bearing rings.
- Bearing capacity. Determined through the performance factor of spindle bearings under conditions of maximum permissible static loads.
- Durability. Time indicator indicating the number of hours of operation of the product before overhaul. Provided that the axial and radial rigidity of the spindle assembly is balanced, the durability can reach 20 thousand hours. The minimum time to failure is two and five thousand hours, which is typical for grinding and internal grinding machines, respectively.
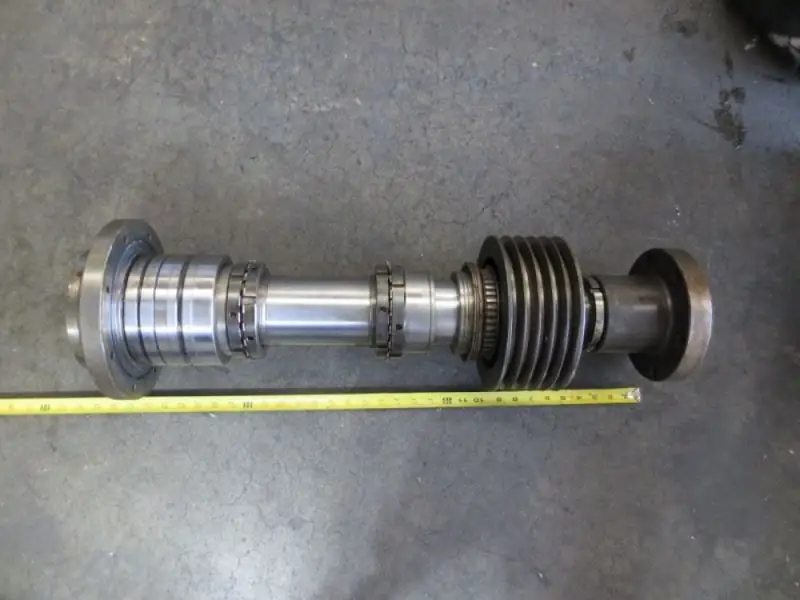
Materials for making SHU
Selection of materials for the element base of the spindle is also a factor in ensuring certain technical and operational properties of the equipment. In lapping, threading and drilling units, emphasis is placed on protection against the effects of torque, and the spindle assembly of a milling machine, for example, is assembled based on the effects of bending moments. In each case, the material must have sufficient wear resistance on the actuating surface as well as on the bearing journal. The stability of shape and dimensions is the main condition for the proper operation of the product, largely dependent on the characteristics of the grade of material used.
In machines with accuracy classes H and P, spindles made of steel alloys of grades 40X, 45, 50 are used. In some cases, design decisions mayrequire and special refinement of the metal by hardening with induction thermal action. Usually hardening of products by hardening is applied to the performance surfaces and bearing journals as the most critical parts of the part.
For elements of complex shape with conical holes, grooves, flanges and stepped transitions, volume-hardened steel is used. This processing technology is allowed only for workpieces from which it is planned to produce the front parts of the machine spindle assemblies with subsequent carburizing. In this case, steels 40XGR and 50X are used.
Equipment with accuracy classes A and B is supplied with spindles made of steel grades 18KhGT and 40KhFA, nitrided. The nitrogen treatment process is required to increase the hardness of the part, as well as to maintain the original shape and dimensions. Increasing strength and structural stability is a prerequisite for spindles used in systems with fluid friction.
In the simplified layout of the control room, the requirements for materials are not so high. Elements with simple shapes can be made of steel grades 20Kh, 12KhNZA and 18KhGT, but even in this case, the blanks are preliminarily subjected to quenching, carburizing and tempering.
ShU structural models
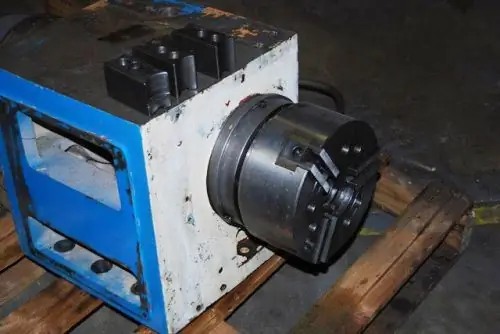
The main share of spindle mechanisms used in modern machine tools has a two-bearing device. This configuration is optimal in terms of equipment optimization and convenience of the technical organization.production process. However, large enterprises also use models with additional support from the third pillar.
Bearing placement configurations are also ambiguous in terms of implementation methods. Today, there are trends towards transferring critical regulatory functions to the headstock area, which reduces the impact of thermal effects. In simple models of the spindle assembly, roller bearings are used, which also minimizes the risk of deformation from heat generation and increases the efficiency of adjustment. At the same time, along with an increase in rigidity and an increase in the accuracy of rotation, such mechanisms have a drawback in the form of a decrease in speed. Therefore, this configuration is best suited for lathes with low speeds.
Slow-speed grinding units are also equipped with roller bearings in the front support part, and the rear side is provided with a duplex of angular contact elements. In particular, this is how spindle units are implemented in the designs of circular and internal grinding machines. To simplify the functional system of the unit, tapered roller bearings also allow. Such a solution in relation to milling units eliminates the need to include an axial bearing group. As a result, the optimum amount of rigidity is maintained, but with it the problems of heat generation with limited torque do not go anywhere.
Product quality control
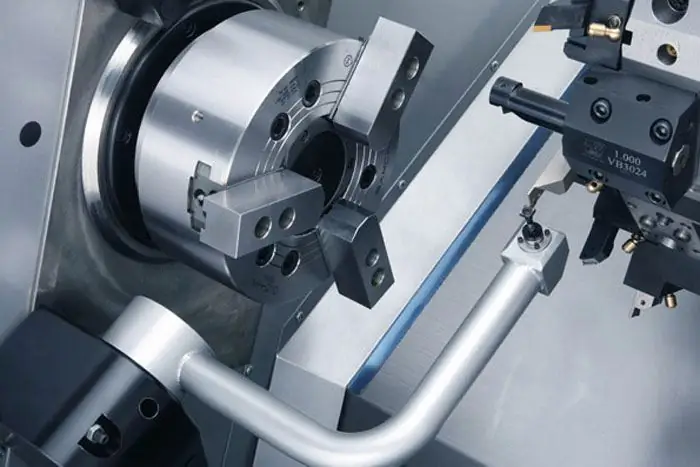
After assembling the headstock, the clearance-preload of the bearing group is checked. This operationnecessary to assess the readiness of the mechanism for full-fledged workloads. The check is carried out by loading the device with a jack and a dynamometer. Measurements are taken directly with indicator devices, including measuring heads, sensors, microcators, etc. The measuring device is installed on the headstock as close as possible to the front bearing. When fixing a step load change, a graph of displacements of the spindle end is built.
The rigidity of the turning spindle assembly with supporting elements is controlled by the two-point measurement method. First, two control points are set on the linear section of the load curve. Further, deformation data are recorded for each line, after which a comparison is performed. As standard indicators, both design values and figures from the general technical requirements for the machine can be used. Moreover, complex data for comparison, obtained as a result of tests, should be presented in the form of arithmetic mean values. In the same way, measurements of axial and radial loads are performed with fixation of the gaps formed between the bearings.
If deviations from the standard values are detected, the clearance-preload is adjusted. When servicing the spindle assemblies of a lathe for such tasks, the technique of heating supports is used. Under the conditions of thermal exposure of thermometers and thermocouples in a certain range, the nuts are tightened and adjusted.
Seals for SHU mechanism
The composition of the headstock includes andspecial seals that increase the insulating and sealing properties of the mechanism. What is it for? Since the workflow of a lathe is associated with the release of large volumes of fine waste under lubricating conditions, clogging of functional parts is common. Accordingly, when assembling the spindle assembly, devices must be provided that protect the working elements from dust, dirt and moisture. That's what the sealant is for. As a rule, this is a consumable in the form of a ring, which is mounted on the spindle using a centering belt. During the operation of the mechanism, its periodic replacement or adjustment of the position is required. In conditions of increased external contamination, a protective slip ring can be additionally used. If the machine is running at medium or low speeds, then the lip seal must also be fixed.
SHU Maintenance
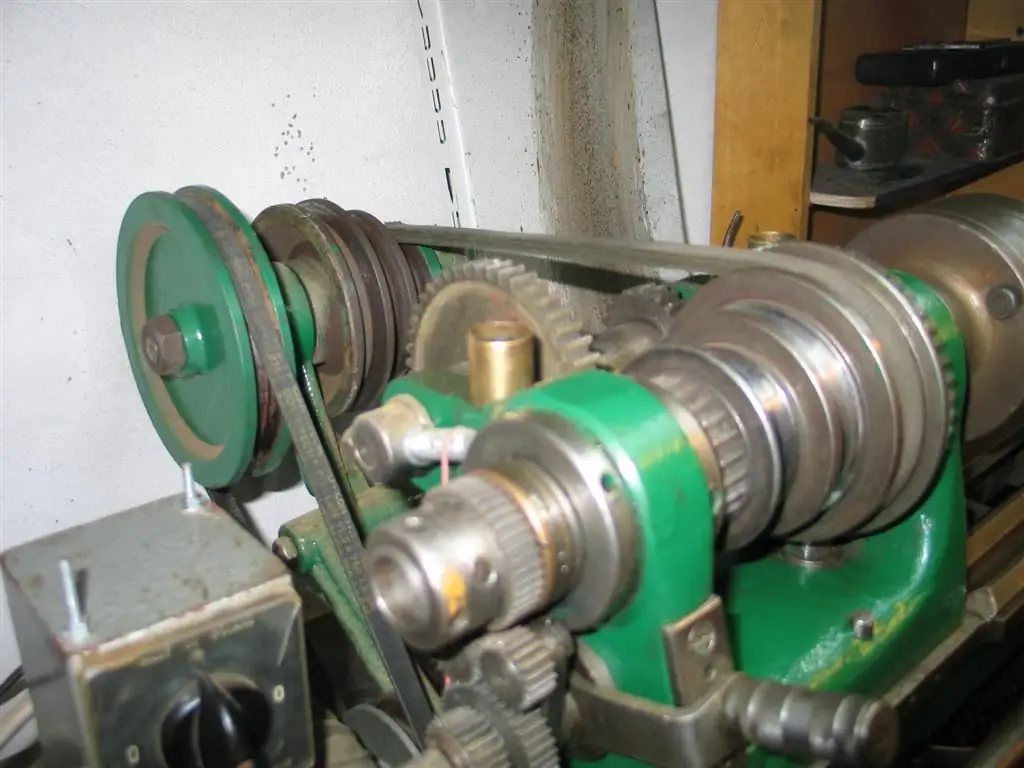
The main task of the staff during the operation of the headstock is to monitor the lubrication of its parts. This is usually done by spraying on the surfaces of rotating gears, impellers and disk components. The optimal composition for this type of lubricant should have a viscosity index of 20 when heated to 50 ° C. The designs of the milling spindle assembly provide for the possibility of directing oil into the bearing through a collector or directly to the working group. Moreover, part of the oil should remain even after the completion of the working session. The old contaminated fluid is replaced with a new one. To simplify the filling process in modern machines, circulating oil supply is organized simultaneously to the gearbox and spindle in automatic mode as the waste mass is drained.
In addition to updating the oil, it is necessary to maintain the technical condition of the mechanism. Technical and structural problems can arise due to overheating, excessive deformation, high vibrations or inter-turn short circuit. A typical repair of spindle assemblies as part of the manufacturing process may be to replace damaged parts, consumables, or rebuild seats. For example, when deforming or installing new elements, additional correction of the sockets or the parts themselves is sometimes required by sharpening, grinding, lapping or building up.
Production of SHU in Russia
Some of the spindle components required for completing machine tools are produced by domestic manufacturers at their own machine-tool facilities, relying on the developments and experience of Soviet industry. There are practically no problems with the manufacture of conventional drive spindle assemblies for a milling machine or turning units that are not focused on high-precision machining. However, modern high-tech electrospindles are produced in Russia only in parts and on the basis of imported components. These limitations are connected not only with the lack of advanced technologies in this area, but also with the shortage of qualified personnel who must solve engineering and production problems.
Conclusion
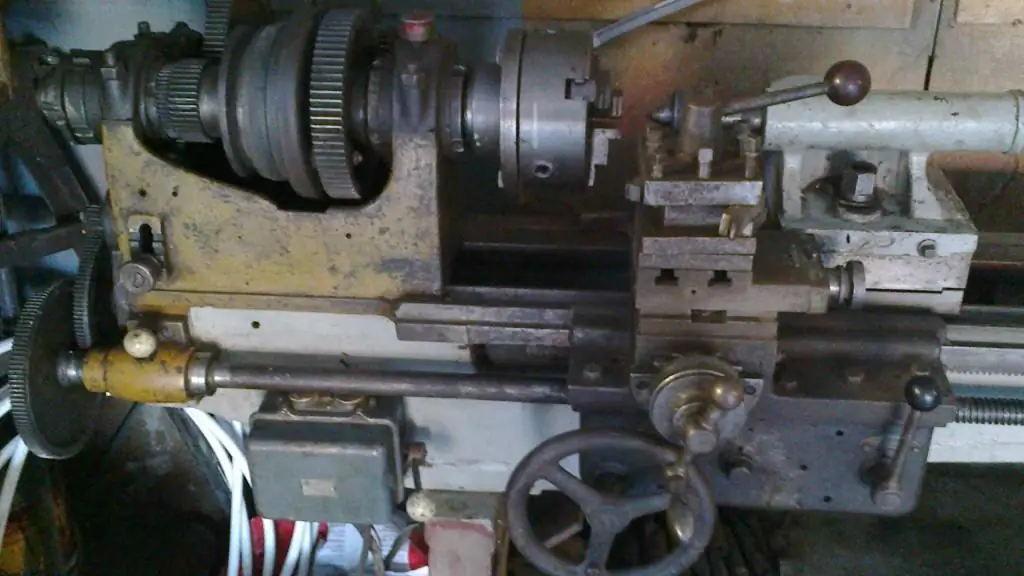
The spindle is one of the central functional components of various types of machine tools. The accuracy of performance of work operations, the ergonomics of equipment control and the efficiency of regulation of the power potential of the drive mechanism depend on the quality of its main functions. Therefore, it is so important to pay attention to the characteristics of the spindle assembly in the lathe when choosing it. And this applies not only to the industrial segment, where in-line machining operations are performed. An ordinary home master who performs simple operations in a garage or country house should also have basic knowledge of the headstock. Skills in handling the spindle mechanism will make the operation more reliable and the maintenance of the machine more economical.
Recommended:
Monetary unit - what is it? Definition of the monetary unit and its types
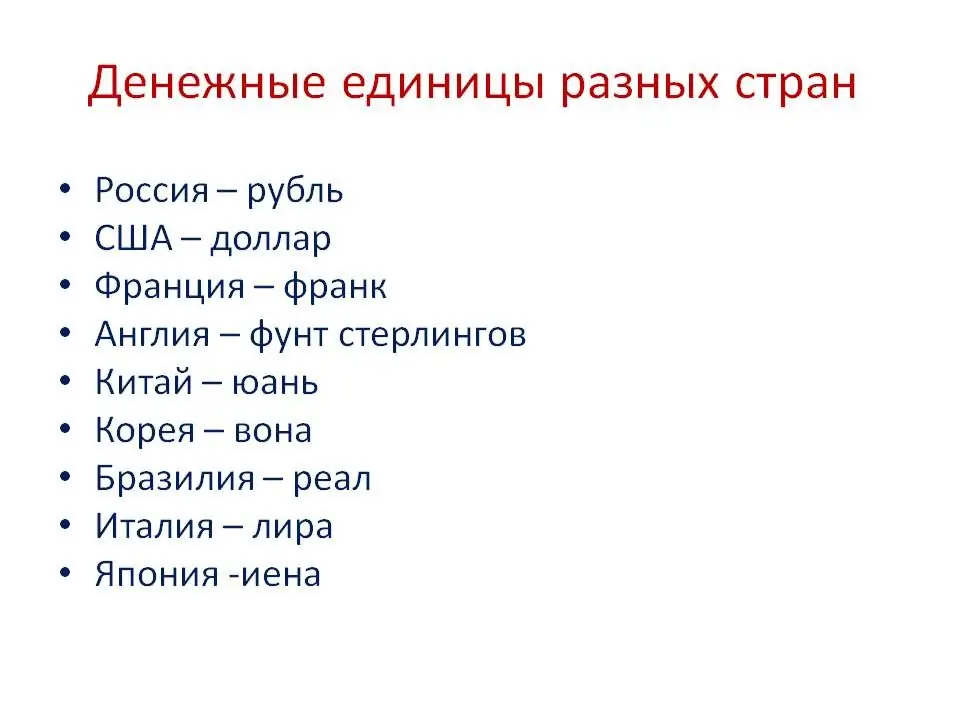
The monetary unit serves as a measure for expressing the value of goods, services, labor. On the other hand, each monetary unit in different countries has its own measure of measurement. Historically, each state sets its own unit of money
What is performance: concept, criteria and performance indicators
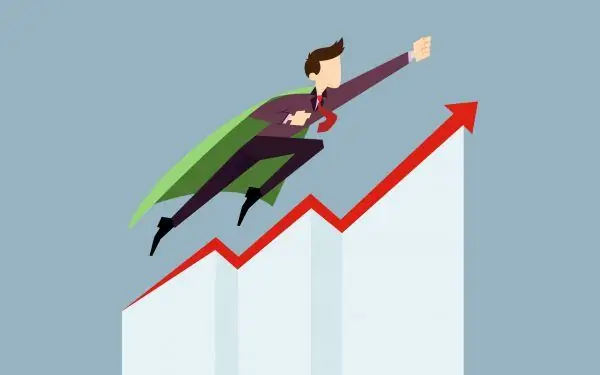
To build a system of staff motivation and to improve management, it is necessary to understand how efficiently employees and managers work. This makes the concept of efficiency extremely relevant in management. Therefore, you need to know what performance is, what are its criteria and evaluation methods
Automatic lathe and its characteristics. Automatic lathe multi-spindle longitudinal turning with CNC. Manufacturing and processing of parts on automatic lathes
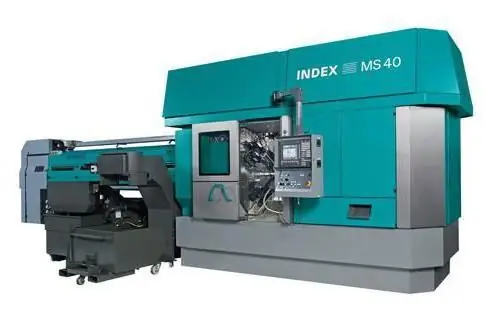
Automatic lathe is a modern equipment used mainly in mass production of parts. There are many varieties of such machines. One of the most popular types are longitudinal turning lathes
Turning various parts
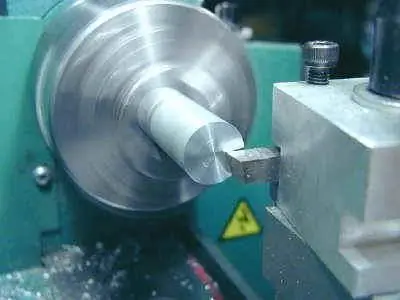
Turning today allows you to make a variety of products. This production uses both wood and metal
What is the optimal spindle for CNC?
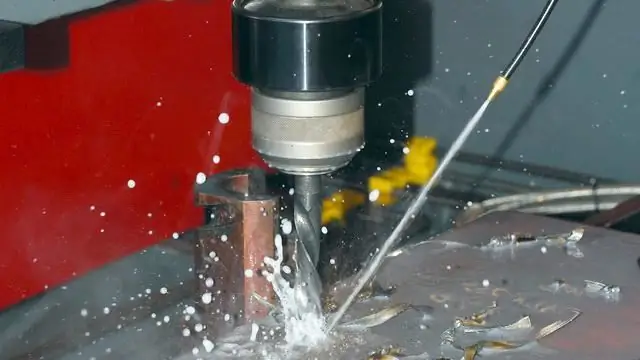
The spindle can have a single design with built-in current-carrying windings and a separate one. The kinematic connection for the latter is carried out by means of a belt drive or gearbox, and a gearbox with manual and automatic operation can also be used