2025 Author: Howard Calhoun | [email protected]. Last modified: 2025-06-01 07:12
In recent years, construction is coming out of a protracted crisis, the number of houses under construction, industrial complexes, roads, and other infrastructure facilities is increasing. Accordingly, high-tech engineering techniques are becoming more and more in demand to reduce time and labor costs.
General information
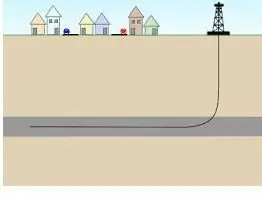
These include directional drilling. It is known that wells are both vertical (standard) and inclined. Moreover, the deviation from the vertical / horizontal required for this is small: only 2 degrees for standard drilling, more than 6 degrees for deep drilling (artesian wells, oil or gas production).
It is natural that the presence of this deviation can be due not only to artificial, but also to completely natural reasons. They are divided into several groups (geological, technical, technological). If you know about all these factors thoroughly, you can control the position with high accuracy.wells in space.
Accordingly, artificial deviation is understood as any “curvature” of the well channel, which was originally conceived. It is important to understand that directional drilling implies strict control of the direction of movement of the drill throughout the work.
Features of drilling oil and gas wells
Especially many difficulties are caused by such work in the aspect of the oil and gas industry. There, inclined drilling has to be carried out using special guide profiles. It is also important to remember that the upper pit is always (!) made strictly vertical, and the deviation begins at the lower horizons, in the planned azimuth.
Especially often, inclined drilling is used not in the development of deposits, but only in their exploration. It is much cheaper to check for "markers" by making a sufficiently long inclined hole than to immediately try to drill the rock to a sufficient depth vertically.
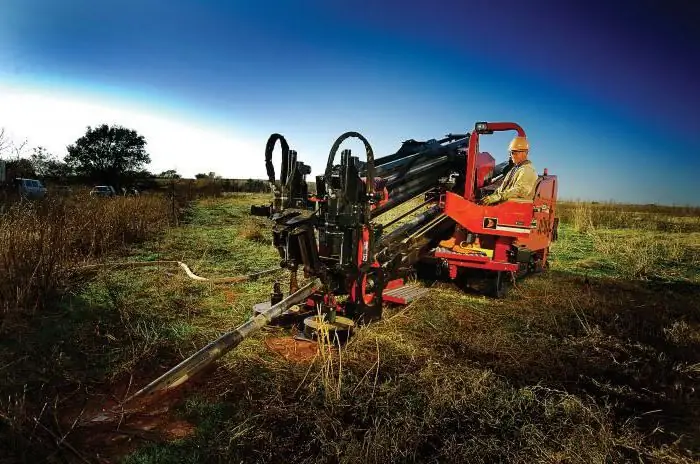
How is directional drilling done in general? The technology is relatively simple: first, the main pit is punched, then, with the help of bending devices, an oblique or horizontally directed drill is brought to the right place, with which an additional shaft is already being made. In order to accurately maintain the direction set by the project, it is necessary to use "markers", they are also beacons. In many cases, special cameras are used to visualize the drilling process.
Important notes
NeedIt should be noted that in some cases, such wells are forced by the features of geological rocks. So, sometimes it is cheaper to drill a pit over the location of some kind of solid igneous rock than to punch it.
Also note that directional drilling implies the penetration of strictly horizontal holes. All wells obtained by this method are divided into single and multilateral wells. In the latter case, several layers depart from the main trunk. A similar drilling method in the oil and gas industry is widely used in the following cases:
- When opening oil or gas-bearing formations that lie between parallel faults.
- If it turned out that the developed reservoir abruptly changes its direction.
- In the case when oil or gas bearing horizons lie under s alt domes (due to the difficulties of drilling through the latter).
- When it is necessary to bypass collapse zones in mines.
- Deviated (horizontal, in particular) drilling is indispensable if the productive formation lies under some kind of reservoir or on the seabed, under residential areas or detached buildings.
- On drilling racks and platforms located directly at sea, in 90% of cases this method of pit drilling is used.
- In addition, directional drilling is indispensable if you need to conduct a multilateral well in an area with a very rugged terrain (ravines, hills, etc.).
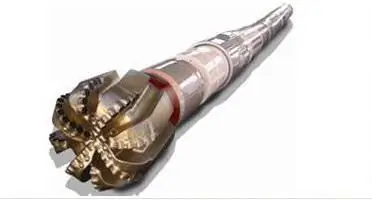
A similar method is indispensable ifFor some reason (collapse, shift of tectonic rock), the shaft of the mine shifted to the side, and therefore there was a need to bypass the problem area. This is also done if it is necessary to take a core sample from the main borehole, since it is impossible to do this in other ways.
Also, directional drilling is used when you need to quickly extinguish a well that has caught fire for some reason, as well as in cases where the lower part of the pit needs to be expanded for operational reasons. In a similar way, the drainage surface is increased in old wells when it is required to increase production volumes.
This is practiced when it is initially known that the deposit does not belong to the category of the rich, but it is required to “milk” it quickly. Then "cluster" drilling is used, with multiple and multiple withdrawal from the main pit of side ones. If in this case to use standard methods, then the return from the field will be low, and the well will be quickly depleted.
The method of directional drilling breaks primary pits through coal pastes, since in this situation they must first be freed from possible gas pockets. If this is not done, there is a high probability of ignition and even explosion already during the operation of the well.
Downhole motors (turbodrills, occasionally electric drills, screw motors) are used to break through the hole. Drilling method - rotary.
Main methods
The main method (both here and abroad) is the dynamic use of terrain features. And this is understandable, since ideally flat plains and steppes are far from being everywhere.
As a rule, typical traces (profiles) are taken as a sample, which are built in advance, and mathematical modeling methods are used for this. It is important to note that the “typical” method can only be applied (!) to already developed fields, all the features of which have long been known. The peculiarity of this method is that they do not try to control the curvature of the terrain, but adapt to it. Alas, but at the same time, a significant drawback is manifested, expressed in a noticeable increase in the cost of drilling.
In the design profile, places with the maximum degree of curvature are necessarily marked, since without this data it is not advisable to draw up a finished project. Design in this case is the responsibility of a trained directional drilling engineer.
Changing the layout of the drilling rig to correct the bend of the well
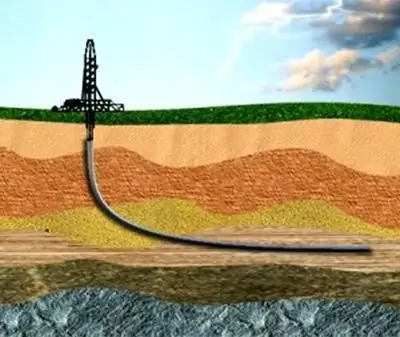
The most common way when it comes to controlling the bend of the hole directly during its punching. The method is good because you do not have to use special equipment. Its disadvantage lies in the severe limitation of accelerated drilling modes.
Use of artificial diverters
For this type of work, bent subs, eccentric nipples, wedges, and other deflecting devices are used. All devices are selected individually, depending on the specific situation and type of terrain.
Spruce variety
An important method of directional drilling is pad drilling. At the same time, the beginning of all pits is located at one point, and the end sections are where the layers of the discovered deposits go.
The method is good in that it allows you to significantly reduce the amount of installation work on the site, significantly reduce the number of required communication lines, including roads to areas where work is being done, and the need for water supply and power supply lines is reduced. This type of drilling was first tested in the USSR, more precisely, in Azerbaijan, during installation work on Artem Island.
The main disadvantages include the importance of preventing the crossing of mine mouths. In addition, it is necessary to conserve the pits already working by the time of the secondary drilling, as this is required by fire safety rules. Finally, a huge disadvantage of cluster pits is the complexity of their subsequent maintenance and repair, and in marine conditions it can be extremely difficult to eliminate breakthroughs.
In what conditions is cluster drilling used?
So when is cluster directional horizontal drilling used? The reasons for its use are divided into the following groups:
- Technogenic - drilling under buildings, including residential, other technical structures.
- Technological - when it is likely that the development of a standard well will disrupt the operation of existing pits. The bush method is not so "traumatic" in this regard.
- Geological -when minerals lie in uneven layers, on different horizons. In this case, directional drilling rigs are the only option when you need to establish production in the shortest possible time without spending phenomenal amounts of money on it.
- Orographic - the most common group of reasons, including the need to open a field located under the surface of the sea, lake, in the case of rugged terrain, as well as when laying pits from the base of offshore platforms, as well as overpasses.
- Climatic. In recent years, in many regions of the Far North, there has been a steady trend towards permafrost thawing, which is why specialists are simply forced to resort to the cluster drilling method. Other methods are fraught with the collapse of the well lumen.
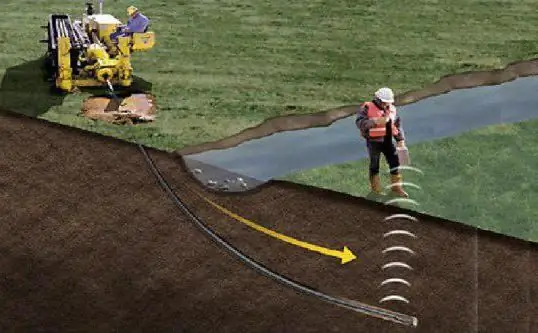
Note that the maximum effect from the operation of cluster wells is observed in swampy, often flooded areas. It is important to note that when inclined drilling under the surface of water bodies, it is extremely important to have experienced personnel capable of properly using navigational equipment, without which it becomes impossible to break through a hole in such specific conditions.
Thus, directional drilling vacancies must necessarily include the search for technically savvy, educated personnel.
Important features of the method
Volumetric bushes look like pyramids or cones, the size of which, as you can understand, depends on the size and"blurring" of the developed field. Accordingly, the number of punched holes is determined by technical capabilities. It is very important to understand that determining the size of the bush should be treated as responsibly as possible, since the area of the alienated territory depends on this indicator.
This is especially important when developing pits within the boundaries of the settlement. An important role in the operation of a finished well is played by the location of the wellheads. It is not surprising that directional drilling of gas pipelines has become the main method widely used in practice in the last 15-20 years.
Positive effects of cluster drilling
In general, this method significantly reduces the cost of organizing the extraction of minerals or the construction of industrial facilities, contributes to the volume of automation of all production operations and processes. More importantly, this approach contributes to the protection of the environment by minimizing the impact on nature.
The fact is that when performing cluster drilling, it becomes quite possible to completely collect drilling waste, preventing it from entering groundwater, and also reduces the likelihood of a decrease in the level of the latter. This is often seen with conventional drilling as it destroys aquifers.
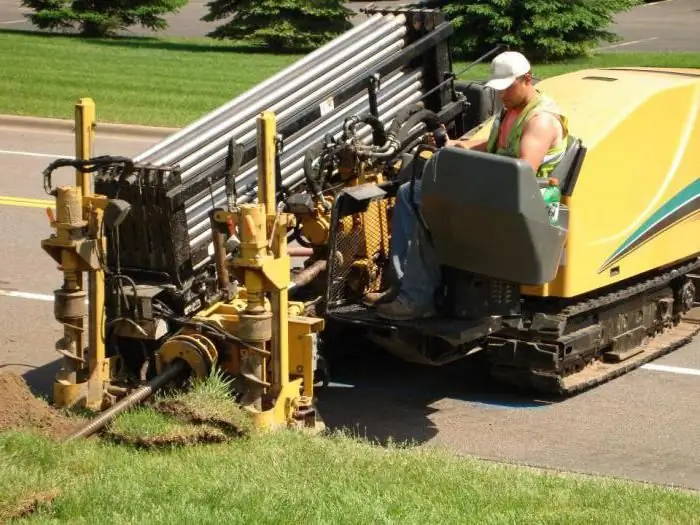
One pad contains at least two wells. As a rule, oilmen in our country practice grouping pits of 18-24 pieces, but in some cases their number exceedsfor 30. However, this is far from a record, since in foreign practice there are cases when 60 "sprouts" could depart from one mine. In particular, the notorious BP company drilled on a small bulk island 60 × 60 m … 68 pits at once. This made it possible to dramatically increase the amount of oil received from one field.
So the drilling of directional and horizontal wells in the modern economy is extremely in demand precisely because of the conservation of material and financial resources.
Multihole drilling type
Currently, due to the depletion of many old deposits, the only reliable way to obtain minerals is to use progressive mining methods, which include multilateral drilling. At the same time, several new “sprouts” are removed from the main pit at a certain depth at once. Because of this, the area of the well in the productive horizon increases significantly, and the volume of mining increases. In addition, at the same time it is possible to reduce drilling volumes in the upper, unproductive horizons.
On the territory of our country, the first well of this type was drilled in 1953, in Bashkiria. But the pit, which passed directly into the thickness of the formation, could only be made at the end of the 50s. It happened in the Samara region. It was immediately revealed that the daily return of such wells is about 40% higher than that of cores made by the standard, vertical method.
It was then that directional drilling began to develop in our country. Training for thisspeci alty was introduced in all technical institutes of the country.
If the multilateral method is used, the total length of the hole in the reservoir increases significantly, the drainage and filtration zone increases. This contributes not only to increasing the return from the well, but also improves the quality of the product obtained during its operation. This kind of pits are divided into the following varieties:
- Inclined, branched type.
- Horizontally branched.
- Radial pits.
In the latter case, directional drilling (horizontal directional drilling) is used in difficult terrain and uneven concentration of working horizons. This method allows (while minimizing costs) to maximize the volume of mining.
Characteristics of multihole holes
As you might guess, obliquely-branched pits consist of the main shaft of the mine and the child processes extending from them, located in different planes. The horizontally directed type proper is a variation of the type just described. The only difference is that the “sprouts” depart from the main trunk in a strictly horizontal plane, at an angle of 90 degrees.
Accordingly, for radial pits, the main shaft also goes strictly vertically, and the additional ones - along the circumference, that is, in the radial direction. In recent years, branched wells have been considered a very promising direction of drilling, since their use on an industrial scale allows solving many issues,arising from the development of underground resources:
- Maximum efficient development of oil fields with uneven horizons. In this case, vertical drilling is not economically feasible, since the final cost is too high.
- Directional drilling can significantly reduce the number of wells used. This leads to a reduction in the cost of work, and also minimizes the impact on the environment.
- When extracting very viscous grades of oil, which are pumped out at extremely great depths.
- The same method is used when it is necessary to build a geothermal station that uses the energy of underground hot water.
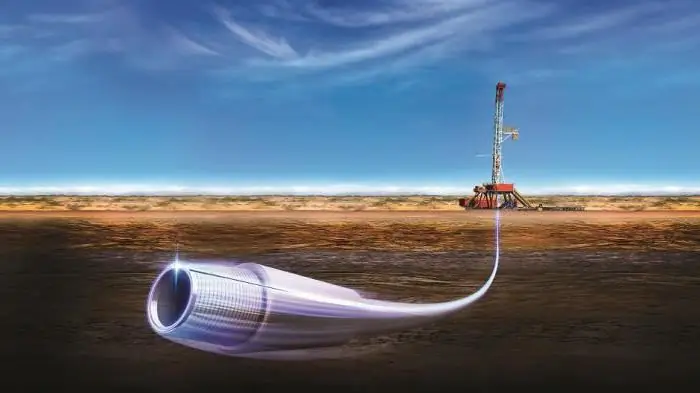
Thus, directional well drilling is a technique widely used in today's oil and gas and construction industries.
Recommended:
Leasing: advantages and disadvantages, main function, classification, tips and tricks
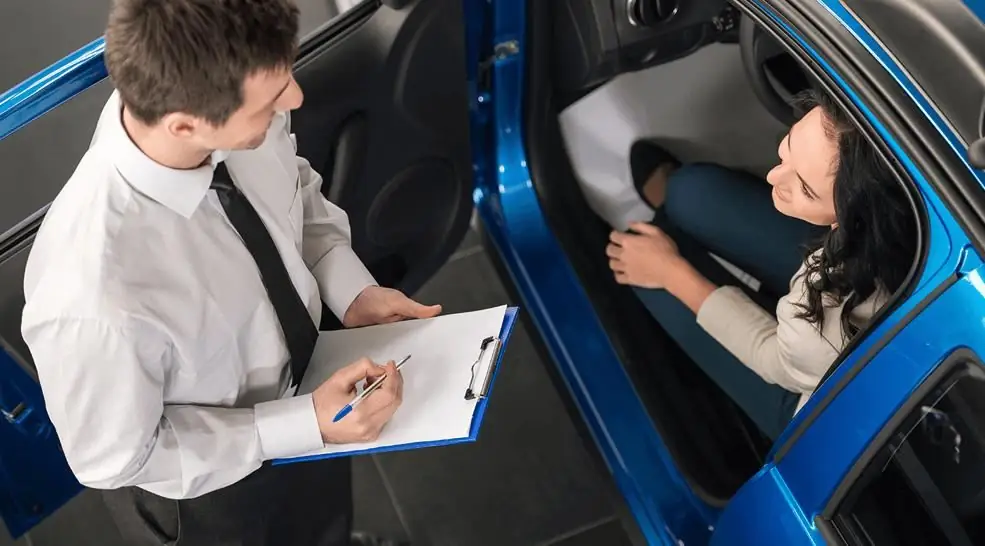
Definition, functions, advantages and disadvantages of leasing as a form of financial activity. General information, classification of leasing relations. Pros and cons of buying a car on lease, as the most common product. Recommendations for choosing a leasing company
Medical Representatives: Key Responsibilities and Sample Resume. Advantages and disadvantages of the profession
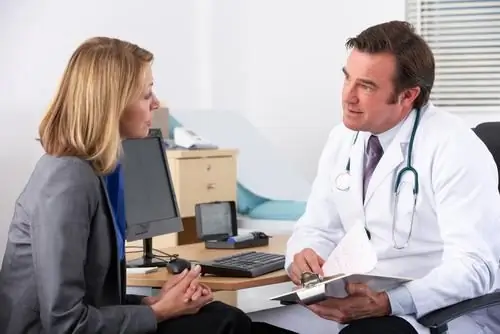
On the modern Russian pharmaceutical market today there are qualitative changes, its active growth is observed. Due to the introduction of new production technologies and the promotion of drugs by domestic manufacturers, their own competitiveness increases
Exploratory drilling: features, equipment. Assistant driller for production and exploration drilling
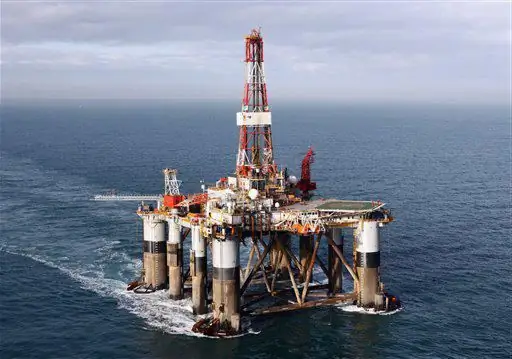
Exploration drilling is an activity aimed at finding raw materials in the bowels of the earth. At the beginning of the 19th century in France, they searched for water in this way. In the 50s of the same century, oil was searched for with the help of exploratory drilling
HDD - drilling technology. Horizontal directional drilling
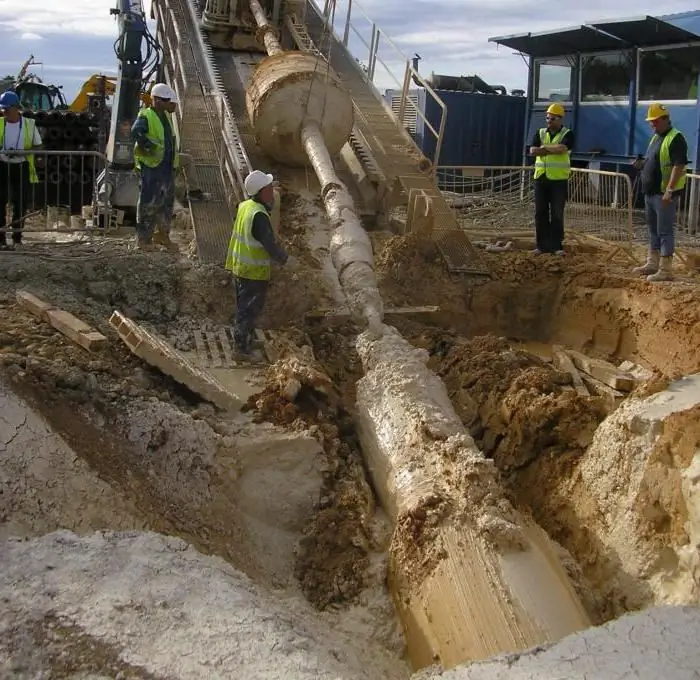
The article is devoted to the technology of horizontal directional drilling. The features of the method, the nuances of its implementation, etc. are considered
Drilling is a type of mechanical processing of materials. drilling technology. Drilling equipment

Drilling is one of the types of material machining by cutting. This method uses a special cutting tool - a drill. With it, you can make a hole of different diameters, as well as depths. In addition, it is possible to create multifaceted holes with different cross sections