2025 Author: Howard Calhoun | [email protected]. Last modified: 2025-01-24 13:10
Alloyed iron is a material that is produced by smelting in blast furnaces. It can contain different amounts of carbon. Depending on the quantitative content of this substance, two types of cast iron are distinguished. The first is called conversion, or white, and the second is gray, or foundry.
Description of types of cast iron
The first type is pig iron. This is the name of a material in which carbon is presented in the form of a substance such as cementite. In a break it has a white color, hence its name. Such cast iron is characterized by high hardness and brittleness. It is very difficult to machine. At the same time, about 80% of all smelted pig iron is white. The main purpose of this type of material is the further remelting into steel.
Gray alloy cast iron is a metal in which carbon is present in the form of ductile graphite. In a break, its color is gray, which also determined its name. The brittleness and hardness of such cast iron is less than that of white cast iron, but it is much better machined.
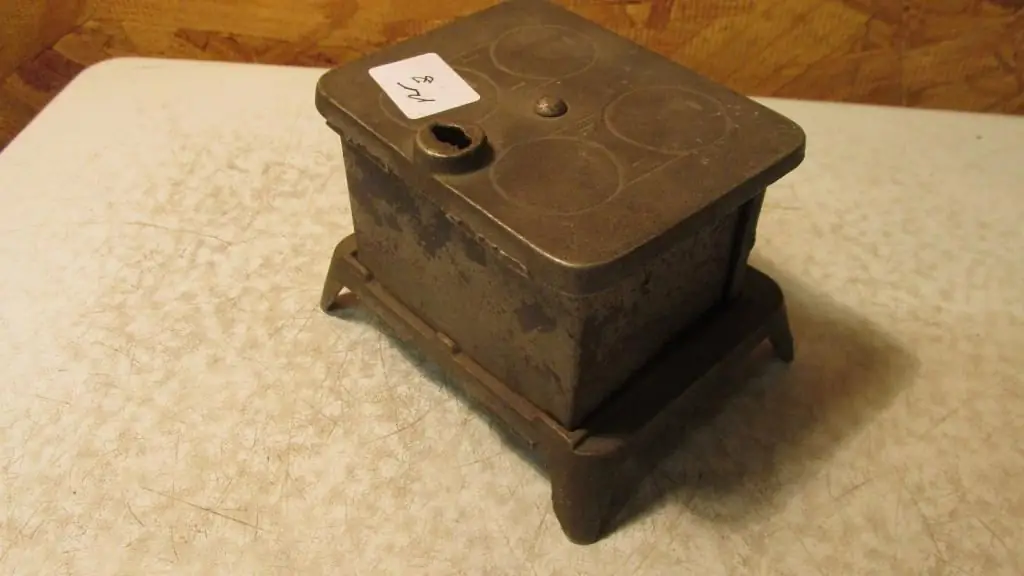
The properties of alloy cast iron of this type are as follows:
- First of all, it resists compressive loads very well.
- Secondly, this metal is insensitive to surface defects, and also has a good resistance to fatigue failure.
However, foundry alloyed cast iron has a rather weak impact strength, as well as low ductility. Due to these two drawbacks, it is quite difficult to use such material for structural purposes.
General description of gray cast iron grades
Today, there are such grades of alloyed gray cast iron: SCH 10, SCH 15, SCH 18, SCH 20 and several others. The letters SCh in the marking indicate that it is gray cast iron, and the next two digits indicate the maximum load that the metal can withstand when stretched. The tensile strength in this case is measured in MPa.
Varieties of gray cast iron
Foundry alloyed iron has several subtypes. One of them was ductile iron. This conditional name was given to the material, which is distinguished by the fact that it is softer and more viscous than gray. Get it from white cast iron. To do this, use the annealing procedure, which lasts a long time. The markings here are about the same, for example KCh 30-6, KCh 33-8, KCh 37-12. The letters indicate that this cast iron is malleable, and the next two numbers determine the tensile strength. But as for the last one or two digits, they characterize the maximum relative elongation, whichmeasured as a percentage.
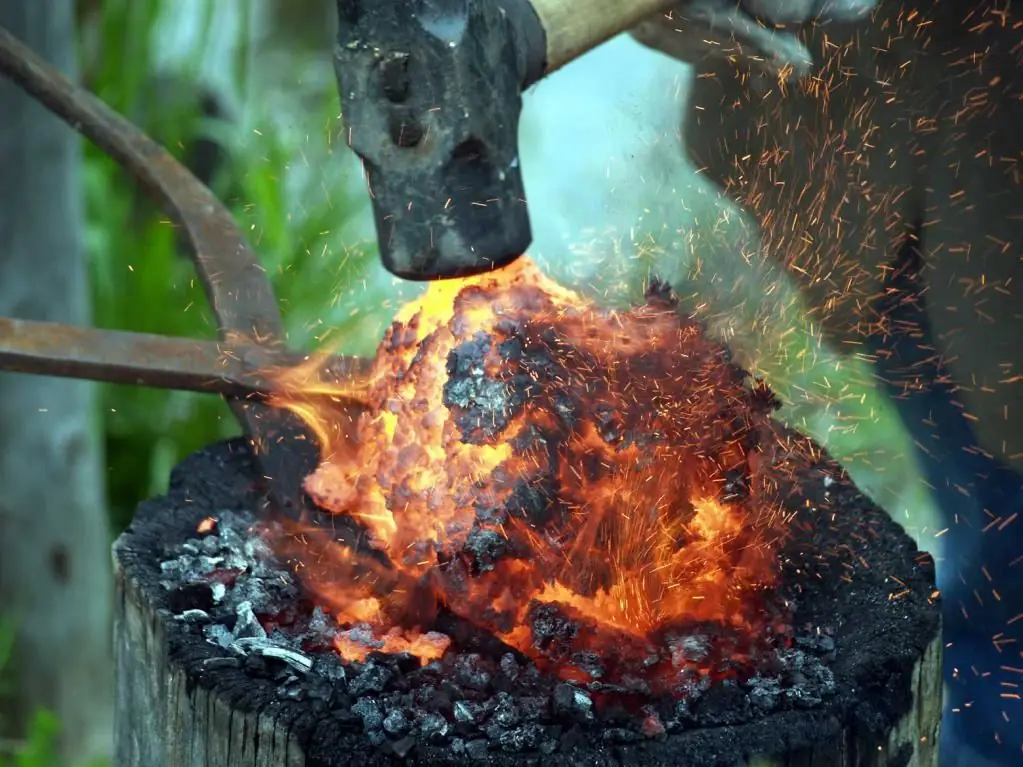
Another subtype of foundry alloyed iron is modified. In order to get it, you need to add special elements to gray. Such modifiers are added before pouring the substance. Aluminum, silicon, calcium and others can be used as additives. These additives significantly increase the number of crystallization centers. In other words, they contribute to significant reduction of graphite.
Thanks to these additives, special alloy cast iron is characterized by higher strength characteristics, less brittleness, and increased resistance to cracking. It is worth adding that all the best grades of this alloy are obtained from such a modified material.
Types of alloy alloy
What does alloy cast iron mean? Alloying is an operation to introduce various impurities into the composition of a material that can improve its characteristics. For cast iron, titanium, chromium, vanadium and others have become such additives. The introduction of alloying elements into the composition can increase such characteristics as strength, hardness, wear resistance, corrosion resistance and many others.
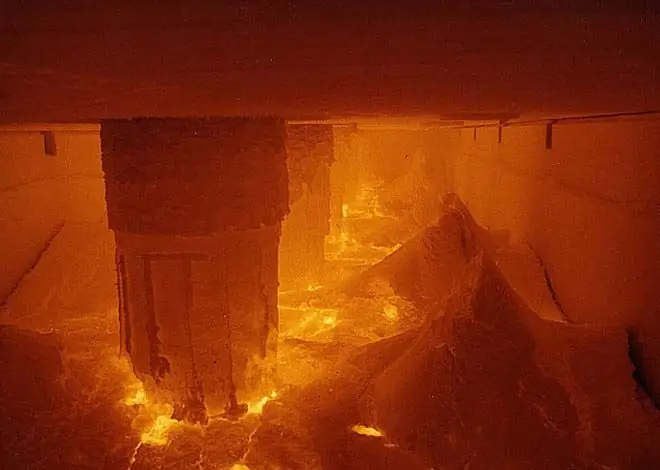
Today, depending on the amount of alloying elements in cast iron, three types can be distinguished:
- If additives are contained in amounts up to 2.5% of the total mass, then this is low-alloy cast iron.
- Medium-alloyed materials are those materials whose content of substances is in the range from2, 5 to 10%.
- The last type is highly alloyed, if the content of modifiers in total exceeds 10%.
Substances for alloying, marking
According to GOST, alloyed cast iron must contain a certain amount of substances for use in a certain area. In addition, the labeling is also standard. For example, ChN15D7Kh is a high-strength alloy containing 15% nickel, 7% copper and approximately 1% chromium. As you can see, in the marking, alloying elements are marked with one letter, followed by a number indicating the quantitative content of the additive. However, it may also be that the figure is missing, as after chromium. This means that the content of the substance in the composition is about 1%.
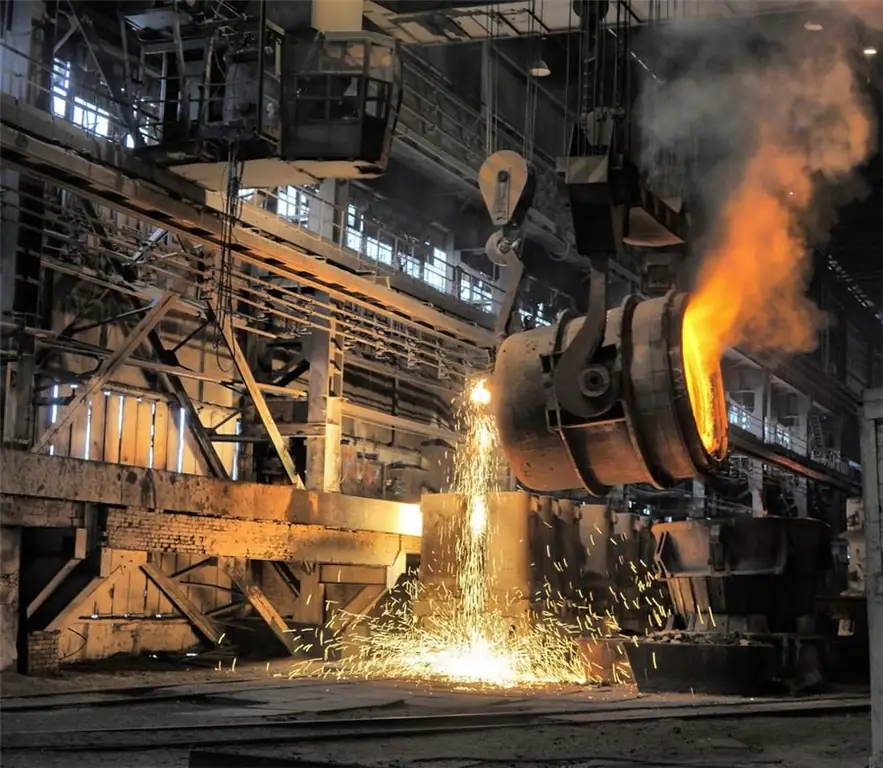
As for the manufacture of such cast iron, it is quite inexpensive. At the same time, the final product has sufficiently high performance properties. Thanks to these two factors, the scope of the described material is constantly increasing.
Types of alloy alloy
It is natural that the addition of any substance to the composition will increase any particular characteristic. Therefore, several classes of alloyed materials are distinguished.
So, cast iron can be wear resistant. The material belonging to this group is characterized in that it has an increased resistance to abrasion, which occurs during surface friction. This category includes anti-friction and friction cast iron. The first of these has a very lowcoefficient of friction. Due to this, the main application of alloyed cast iron of the named type is the production of parts such as plain bearings, bushings for them and other parts with similar requirements.
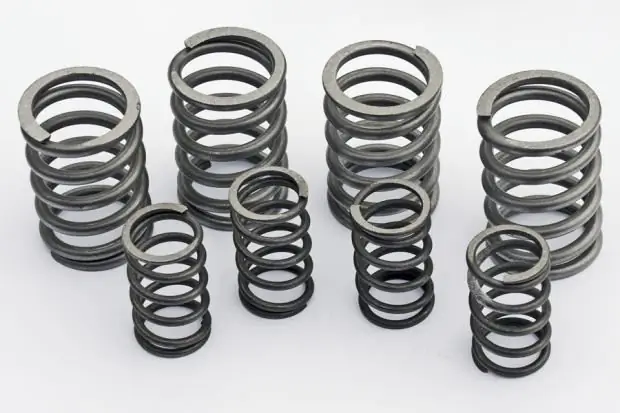
Friction material, on the contrary, is characterized by a fairly high coefficient of friction, and therefore it is most often used in the production of brake devices for a variety of mechanisms, equipment, etc.
Stainless cast iron
Many people know that there is a metal called stainless steel. In fact, this is not a very accurate definition. Just such alloys differ in that their resistance to corrosion is quite high. The named cast iron has received the greatest distribution in shipbuilding. If more than 12% chromium is added to the composition of iron as an alloying element and the carbon content is reduced as much as possible, then such an alloy will be obtained as a result.
ChNHT, ChN1KhMD, ChN15D7Kh2 became its most common brands. They differ in that they retain high corrosion resistance even in aggressive environments, have good resistance to cavitation and wear in a steam-water environment.
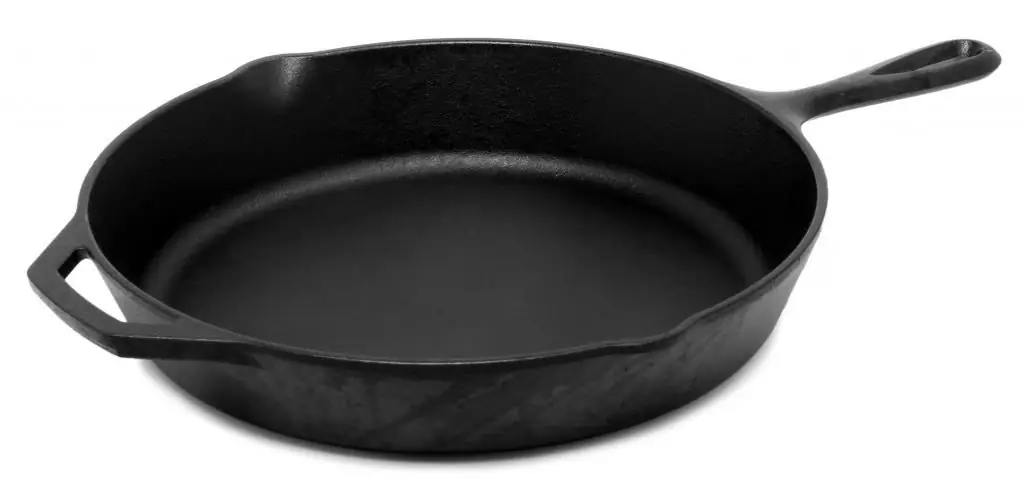
A small but still quite popular group is heat-resistant cast iron. The main advantage of the material is that it is rather difficult to oxidize, and also retains its qualities well at elevated temperatures.
Introduction of copper
Currentlytime, more and more often begin to use cast iron with the addition of copper. The introduction of this additive into the alloy significantly improves its casting qualities. Best of all, this affects the fluidity of the material. In addition, the tendency to cracking and shrinkage porosity is greatly reduced.
Incorporation of 0.5% Cu (copper) makes cast iron suitable enough to be cast into parts with wall thicknesses ranging from 10 to 25 mm. If it is necessary to increase the wall thickness of future elements, then it will be necessary to increase the quantitative content of copper, as well as its complexes. It is worth noting here that the effect of adding copper can be enhanced if elements such as antimony or bismuth are introduced into the alloy.
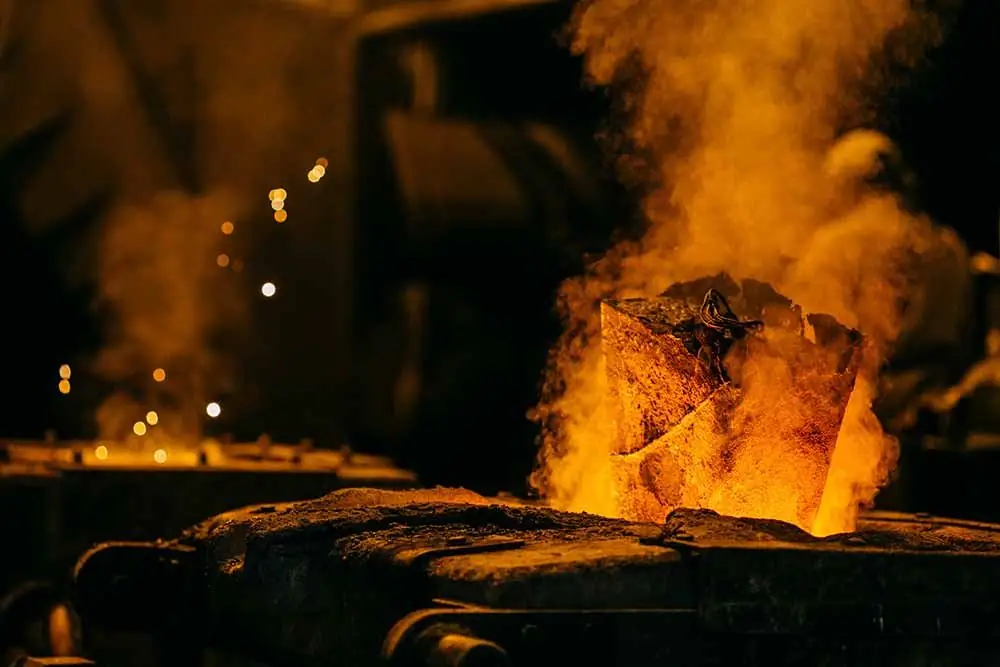
If the carbon equivalent will increase, then the influence of copper on the crystallization of graphite will decrease. Alloying cast iron with copper can also prevent bleaching in the surface layers, and also greatly increase the hardness towards the middle. This is quite noticeable when smelting cylinder liners, cast iron block heads, and other items.
Complex alloy cast iron
In order to successfully smelt cast iron that can be used for casting cylinder liners, it is necessary to use not only a variety of ferroalloys, but also an induction furnace. To carry out the casting of such parts, the IChKhN4, ChN1KhMD and ChNMSh brands and several other types are used. Their distinctive feature is that all parts are smelted into a thin-walled or massive mold.
Needlestructure and high strength material
A small variety of gray cast iron, which belongs to the wear-resistant group, is a material with an acicular structure. The degree of doping in such a material is quite low. The content of silicon and carbon in it is also quite low. In this case, the amount of substances such as copper, molybdenum, nickel and some other modifiers increases depending on the resulting wall thickness required, as well as depending on the casting method to be used.
Another variety is a high-strength material. This is a small variety of gray cast iron, which is distinguished by the content of nodular graphite. In order to obtain such a structure, it is necessary to introduce magnesium, cerium and bismuth into the alloy. The addition of these three alloying elements turns the ductile graphite of the casting material into a spheroidal graphite. This type differs in that its mechanical qualities are much higher than that of other types of cast iron. To date, approximately 10 different grades of the alloy of this category are being produced. Such material can be perfectly used in shipbuilding instead of malleable type. And the most common type of ductile iron is magnesium (with a large amount of magnesium in the composition).
Recommended:
Diameters and dimensions of cast iron sewer pipes. Types and features
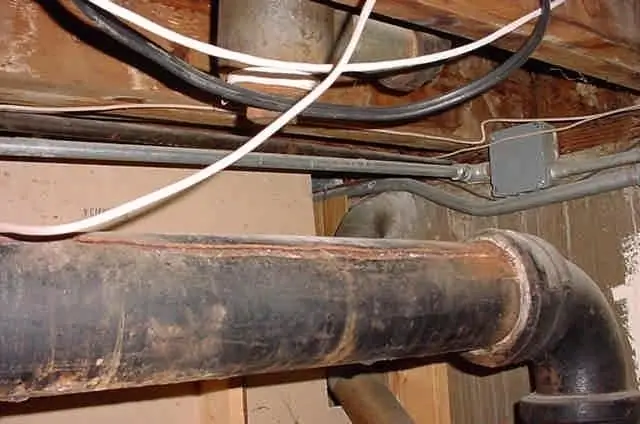
Cast iron pipes are used today in the laying of external and internal sewerage systems. Products can be channelless and channel. Their service life can reach 100 years. Connecting elements and assortment of sewer pipes is determined by GOST 6942-98. After reading the documentation, you will be able to understand what parameters the pipes should have
Alloy is a homogeneous composite material. Alloy properties
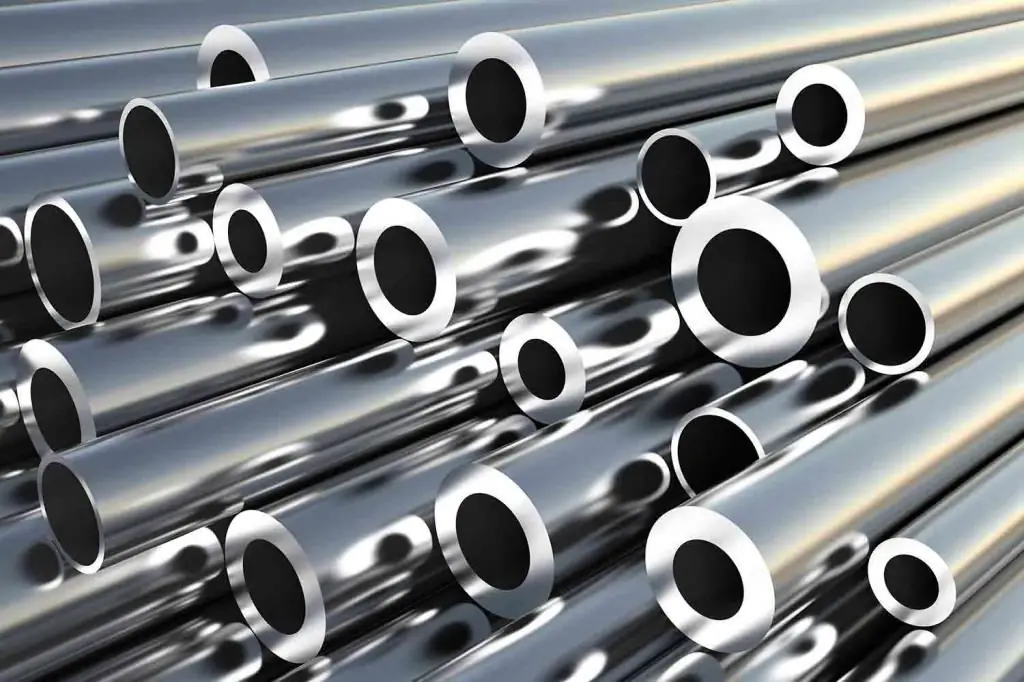
Everyone has heard the word "alloy", and some consider it synonymous with the term "metal". But these concepts are different. Metals are a group of characteristic chemical elements, while an alloy is a product of their combination. In its pure form, metals are practically not used, moreover, they are difficult to obtain in their pure form. While alloys are ubiquitous
Types of cast iron, classification, composition, properties, marking and application
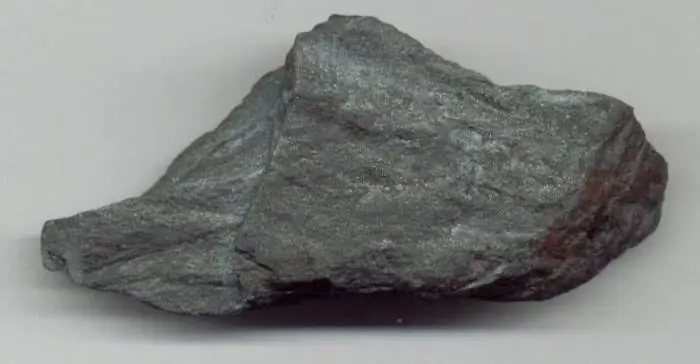
The types of cast iron that exist today allow a person to create many products. Therefore, we will talk about this material in more detail in this article
Aluminum grades: types, properties and applications
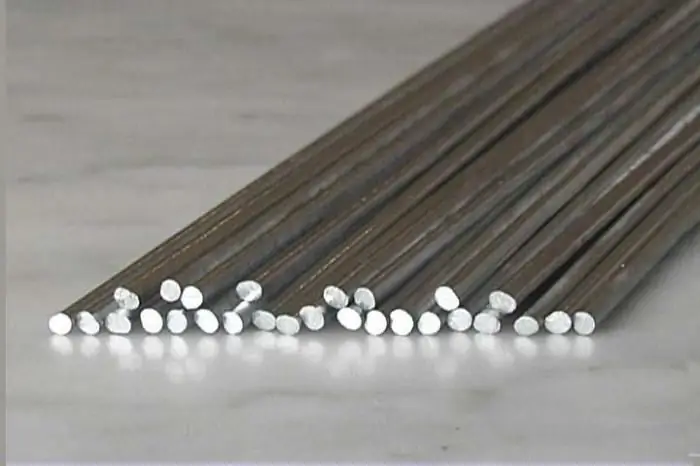
Today, aluminum is used in almost all industries, from the production of food utensils to the creation of spacecraft fuselages. For certain production processes, only certain grades of aluminum are suitable, which have certain physical and chemical properties
White cast iron: properties, application, structure and features
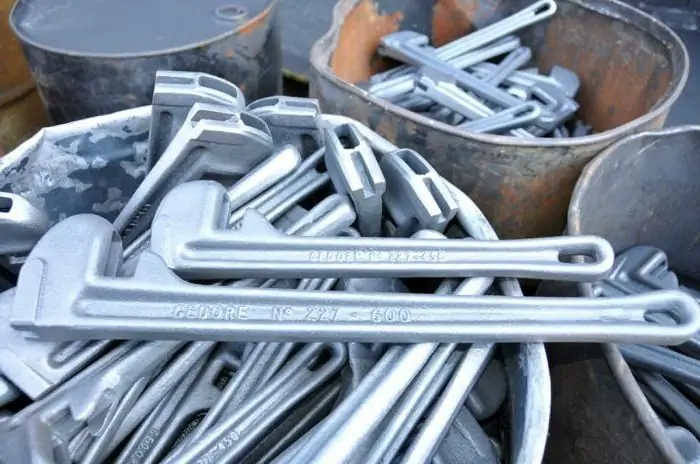
Initially, the technology of casting iron was first mastered in China in the 10th century, after which it became widespread in other countries of the world. A prominent representative of such an alloy is white cast iron, which is used in mechanical engineering for the manufacture of parts, in industry and in everyday life