2025 Author: Howard Calhoun | [email protected]. Last modified: 2025-01-24 13:10
Different types of plastics provide ample opportunities for creating certain designs and parts. It is no coincidence that such elements are used in a variety of fields: from mechanical engineering and radio engineering to medicine and agriculture. Pipes, machine parts, insulation materials, appliance cases, and household products are just a few of the many things plastic can create.
Main varieties
The types of plastics and their applications are based on whether the polymers are natural or synthetic. They are subjected to heating, pressure, after which molding of products of varying complexity is performed. The main thing is that during these manipulations the shape of the finished product is preserved. All plastics are thermoplastic, that is, reversible, and thermoset (irreversible).
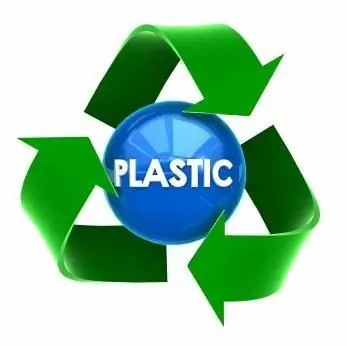
Reversible become plastic under the influence of heating and further pressure, while fundamental changes in the composition are notare happening. A product that has already been pressed and has already become solid can always be softened and given a certain shape. Such types of plastics (thermoplastic) as polyethylene and polystyrene are known. The first is resistant to corrosion and dielectric properties. Based on it, pipes, films, sheets are produced, it is widely used as an insulating material.
From styrene to polystyrene
As a result of the polymerization of styrene, polystyrene is obtained. From it, various parts are subsequently created on the basis of casting or pressing. These types of plastics are widely used for the production of large parts and products, such as elements for refrigerators or bathrooms. Among thermosetting plastics, the most commonly used are press powders, laminates, fibers, which can be further processed to obtain various parts.
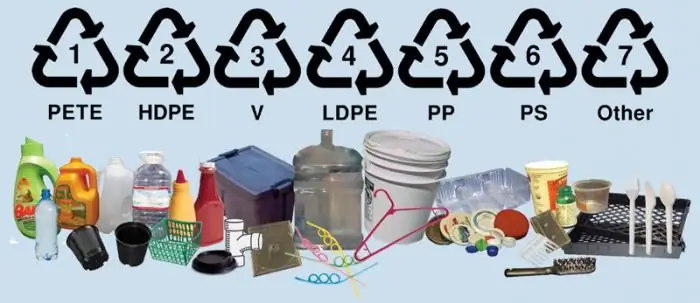
Plastic is a very easy-to-use material, on the basis of which you can create many products. Depending on the thermal properties, the following types of plastic processing are distinguished:
- Pressing. This is the most popular way to produce products from thermosetting materials. Molding is carried out in special molds under high temperatures and pressures.
- Injection molding. This method makes it possible to create products of various shapes. To do this, special containers are filled with molten plastic. The process itself is highly productive and economical.
- Extrusion. Through this processingreceive many types of plastic products, such as pipes, threads, cords, films for various purposes.
- Blowing out. This method is an ideal opportunity to create three-dimensional products that will have a seam at the closure of the mold.
- Stamping. This method creates products from plastic sheets and plates using special shapes.
Features of polymerization
Plastic can be obtained by polymerization and polycondensation. In the first case, monomer molecules bind, forming polymer chains without releasing water and alcohol, in the second case, by-products are formed that are not associated with the polymer. Various methods and types of polymerization of plastics make it possible to obtain compositions that differ in their initial properties. The correct temperature and heat of reaction play an important role in this process in order for the molding material to polymerize correctly. During polymerization, it is important to pay attention to the residual monomer - the less it is, the more reliable and longer the plastic will be in operation.
Porosity
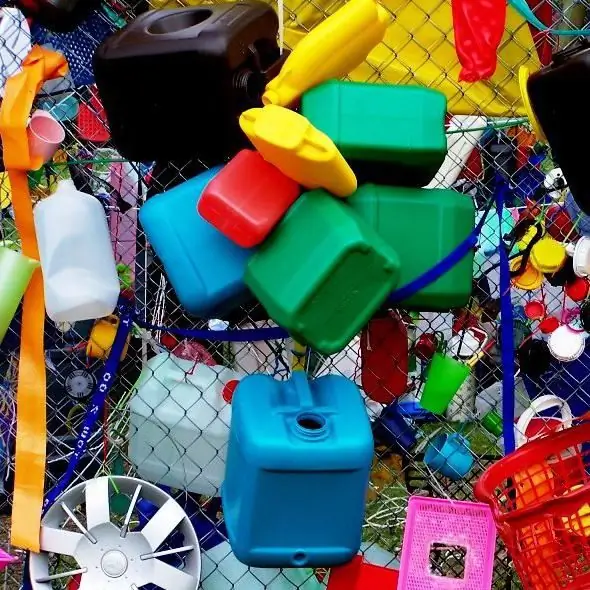
If the polymerization modes were violated, this can lead to defects in finished products. Bubbles, stains and increased internal stress will appear in them. There are different types of plastic porosity:
- Gas. It appears due to the fact that the polymerization mode is violated, and benzoyl peroxide boils. If gas pores form in the thickness of the prosthesis, then it needs to be redone.
- Granular porosity occurs due to excess polymerpowder, evaporation of monomer from the surface of the material, or poor mixing of the plastic compound.
- Compression porosity. Occurs due to a decrease in the volume of the polymerizing mass under the influence of insufficient pressure or lack of molding mass.
What to consider?
You should be aware of what types of porosity plastics are, and avoid defects in the final product. It is necessary to pay attention to the fine porosity on the surface of the prosthesis. This happens due to too much monomer, and the porosity is not subjected to grinding. If an internal residual stress develops while working with plastic, the product will crack. This situation occurs due to a violation of the polymerization regime, when the object is in boiling water for too long.
In any case, the deterioration of the mechanical properties of polymeric materials eventually leads to their aging, and therefore the production technology must be observed entirely.
Basic plastics - what is it?
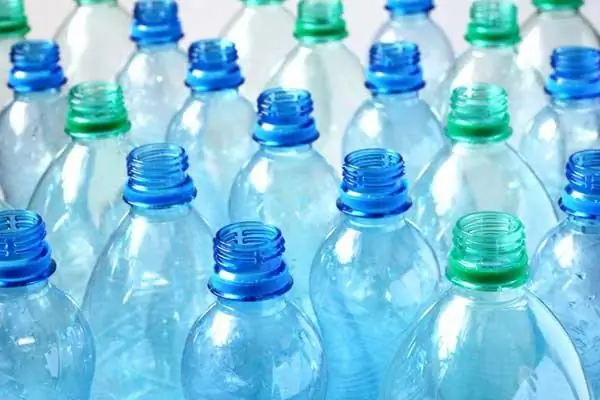
The material under consideration is widely used in the manufacture of bases for removable lamellar dentures. The most popular types of base plastics have a synthetic base. Mass for bases, as a rule, is a combination of powder and liquid. When they are mixed, a molding compound is created that hardens when heated or spontaneously. Depending on this, a hot curing or self-hardening material is obtained. Hot cure base resins include:
- etacryl (AKP-15);
- Acrel;
- fluorax;
- acronil.
Materials for creating removable dentures are elastic plastics, which are needed as soft shock-absorbing pads for bases. They must be safe for the body, firmly connected to the basis of the prosthesis, maintain elasticity and constant volume. Among these plastics, attention should be paid to eladent, which is a lining for removable denture bases, and orthoxyl, which is obtained on the basis of siloxane resin.
Building materials
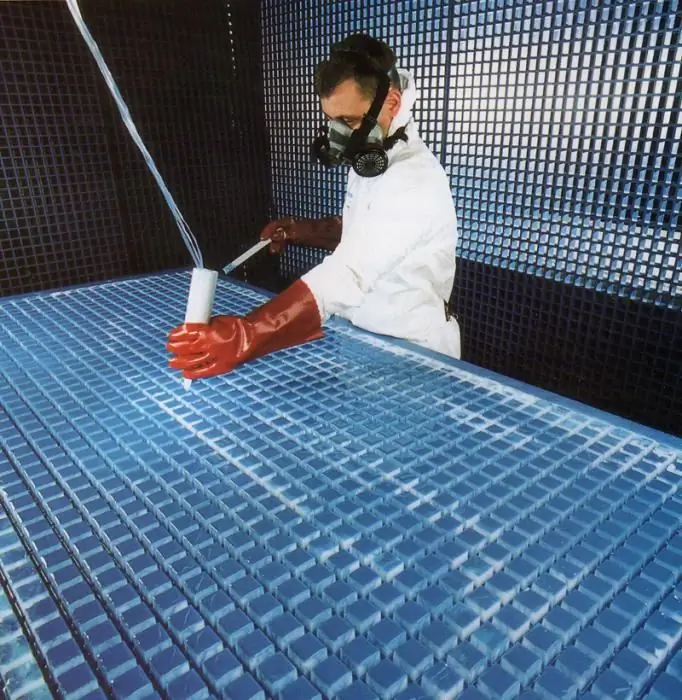
The main types of plastics are used in different areas of construction, depending on the composition. The most popular content includes the following:
- Polymer concrete. This is a composite plastic, which is created on the basis of thermosetting polymers. The best in terms of physical and mechanical properties are polymer concrete based on epoxy resins. The fragility of the material is compensated by fibrous fillers - asbestos, fiberglass. Polymer concretes are used to create structures that are resistant to chemicals.
- GRPs are modern types of building plastics, which are sheet materials made of glass fibers, fabrics bound by a polymer. Fiberglass is created from oriented or chopped fibers, as well as fabrics or mats.
- Floor materials. They are represented by different types of roll coatings and liquid-viscous compositions based on polymers. Widely used in constructionlinoleum based on polyvinyl chloride, which has good thermal and sound insulation. A seamless mastic floor can be created based on a mixture of raw materials with oligomers.
Plastic and its labeling
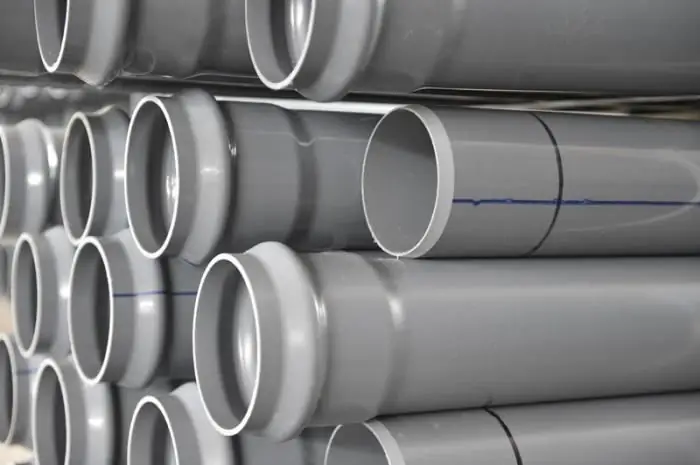
There are 5 types of plastics that have their own designation:
- Polyethylene terephthalate (labeled PETE or PET). It is economical and has a wide range of applications: it is used to store various drinks, oils, cosmetics.
- High density polyethylene (marked as HDPE or PE HD). The material is economical, lightweight, resistant to temperature extremes. Used for making disposable tableware, food storage containers, bags, toys.
- Polyvinyl chloride (marked as PVC or V). Window profiles, furniture parts, stretch ceiling film, pipes, floor coverings and much more are created from this material. Due to the content of bisphenol A, vinyl chloride, phthalates, PVC is not used in the manufacture of products (containers, dishes, etc.) for food storage.
- Polyethylene (LDPE or PEBD marking). This cheap material is used to make shopping bags, trash bags, linoleum and CDs.
- Polypropylene (letter marked PP). It is durable, heat-resistant, suitable for the production of food containers, food packaging, toys, syringes.
Popular plastics are polystyrene and polycarbonate. They have found wide application in variousindustries.
Application areas
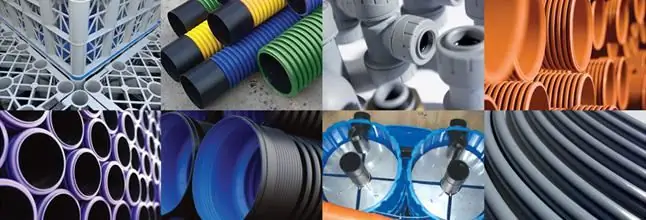
Different types of plastics are used in a variety of industries. At the same time, the requirements for them are approximately the same - ease of operation and safety. Let's take a closer look at the types of thermoplastic plastics and their applications.
Plastic | Scope of application |
Polyethylene (high and low pressure) | Production of packaging, non-loaded parts of machines and equipment, cases, coatings, foils. |
Polystyrene | Production of equipment, insulating films, styropian. |
Polypropylene | Found wide application in the production of pipes, car parts, elements for refrigeration equipment. |
Polyvinyl chloride (PVC) | Production of chemical equipment, pipes, various parts, packaging, flooring. |
Polycarbonates | Production of precision machine parts, apparatus, radio and electrical engineering. |
Thermosetting types of plastics (table)
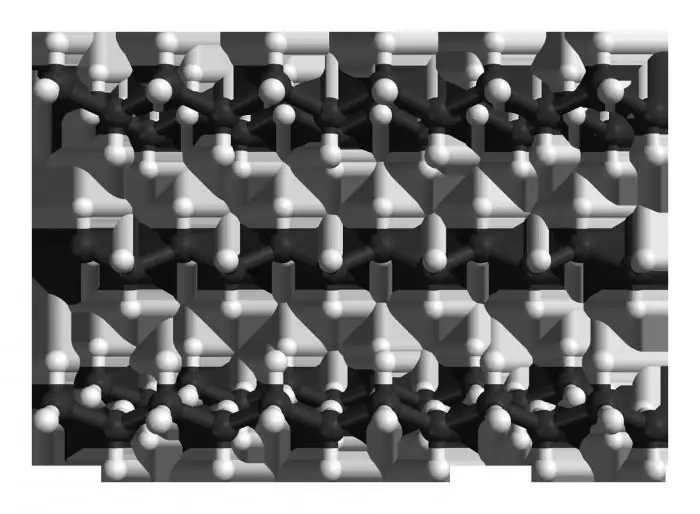
Material | Scope of application |
Phenoplasts | Used to create haberdashery products (buttons, etc.), ashtrays, plugs, sockets, radio andtelephone sets. |
Aminoplasts | Used for wood glue, electrical parts, haberdashery, thin coatings for decoration, foam materials. |
Fiberglass | Used in the manufacture of power electrical parts in mechanical engineering, large-sized products of simple shapes (car bodies, boats, instrument cases, etc.). |
Polyesters | Rescue boats, car parts, furniture, glider and helicopter hulls, corrugated roof boards, lamp shades, antenna masts, skis and poles, fishing rods, safety helmets and the like are made from polyesters. |
Epoxy resin | Used as an electrical insulating material in electrical machines, transformers (as high-voltage insulation) and other devices, in the production of telephone fittings, in radio engineering (for the manufacture of printed circuits). |
Instead of a conclusion
In this article, we looked at the types of plastics and their applications. When using such materials, many factors are taken into account, ranging from physical and mechanical properties to the features of work. For all its cost-effectiveness, plastic has a sufficient level of safety, which significantly expands the scope of its application.
Recommended:
Laminated plastics: properties and applications
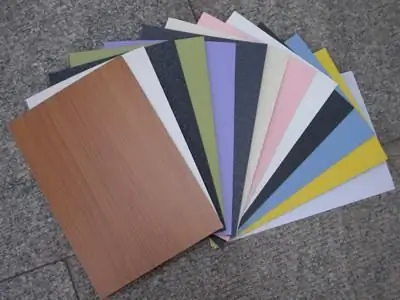
Special composite materials are used in the insulation systems of complex devices and structures that are subject to increased operational requirements. As a rule, these are not universal, but highly specialized products, oriented to work in extreme thermal and humidity conditions. Such insulators include the following laminated plastics: getinaks, textolite, fiberglass, as well as their modifications
Reserves of banks and their formation. Required bank reserves and their norm
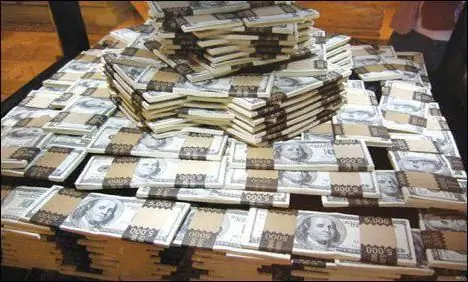
Bank reserves ensure the availability of funds for the uninterrupted fulfillment of payment obligations regarding the return of deposits to depositors and settlements with other financial institutions. In other words, they act as a guarantee
Main types and types of business plans, their classification, structure and application in practice
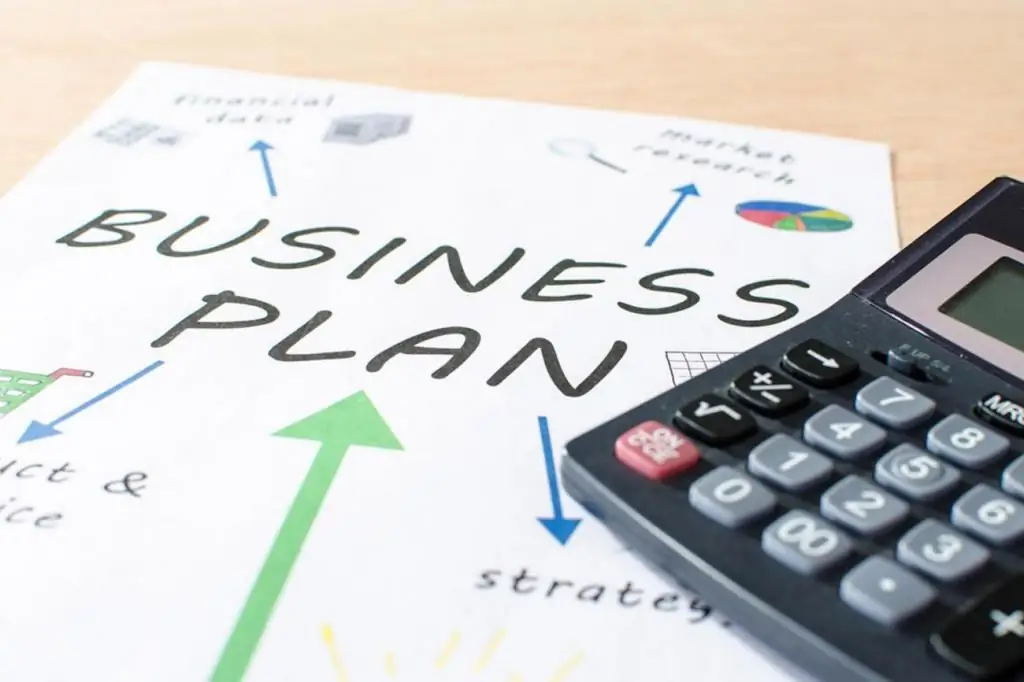
Each business plan is unique, because it is developed for certain specific conditions. But you need to familiarize yourself with the features of various types of business plans in order to understand their key features. Experts recommend doing this before compiling your own similar document
Welding of ultrasonic plastics, plastics, metals, polymeric materials, aluminum profiles. Ultrasonic welding: technology, harmful factors
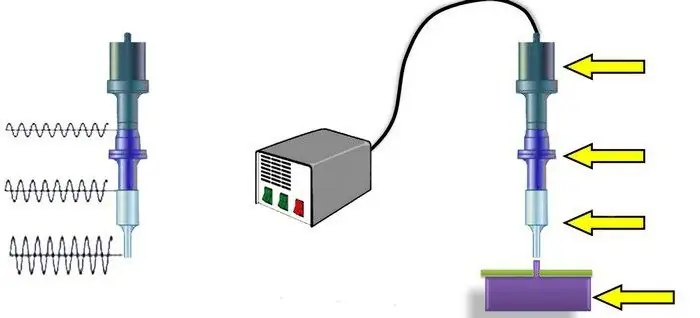
Ultrasonic welding of metals is a process during which a permanent joint is obtained in the solid phase. The formation of juvenile areas (in which bonds are formed) and the contact between them occur under the influence of a special tool
Laser engraving on plastic: types of plastic, choice of pattern, necessary laser equipment and patterning technology
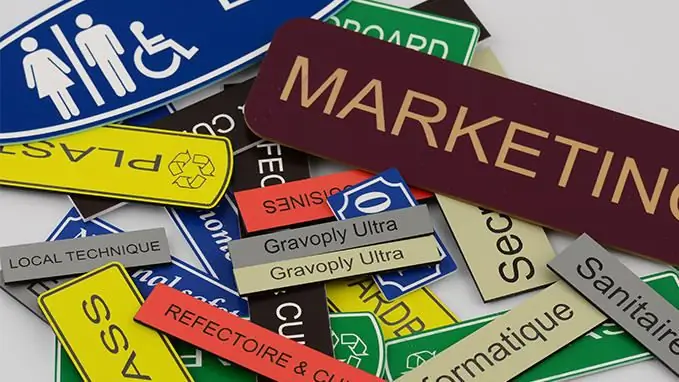
What types of plastic are used when applying laser engraving. Designs suitable for engraving and their types. How to edit and prepare photos for laser engraving. Necessary equipment for work, principles of its operation