2025 Author: Howard Calhoun | [email protected]. Last modified: 2025-01-24 13:10
Automation of control systems (ACS) is an information system that is designed for the automated implementation of management processes. It should be noted that the introduction of such technology should be justified from a technical and economic point of view. Most often, the installation of such a system makes it possible to reduce the number of working personnel, increase management efficiency, and improve the quality of the facility.
Requirements for ACS
There are some requirements for the automation of the control system.
Firstly, it is very important that all elements can be connected to each other, and also have a connection with an automated system that is connected to the automated control system. In addition, it is very important here that the system has the possibility of expansion, development and modernization. This is done with the expectation that in the future the enterprise will develop and a more modernized system will be needed.
Second, but not least, the control automation systemmust have a sufficient degree of reliability. In other words, it must be 100% secure when working with the initially set parameters. Another important requirement is adaptability. The system must be configured in such a way that it can change in the face of changing parameters. However, it should be said here that the range of changes is discussed in advance, before the installation of the automated control system, and therefore these limits of changes are entered into the system in advance.
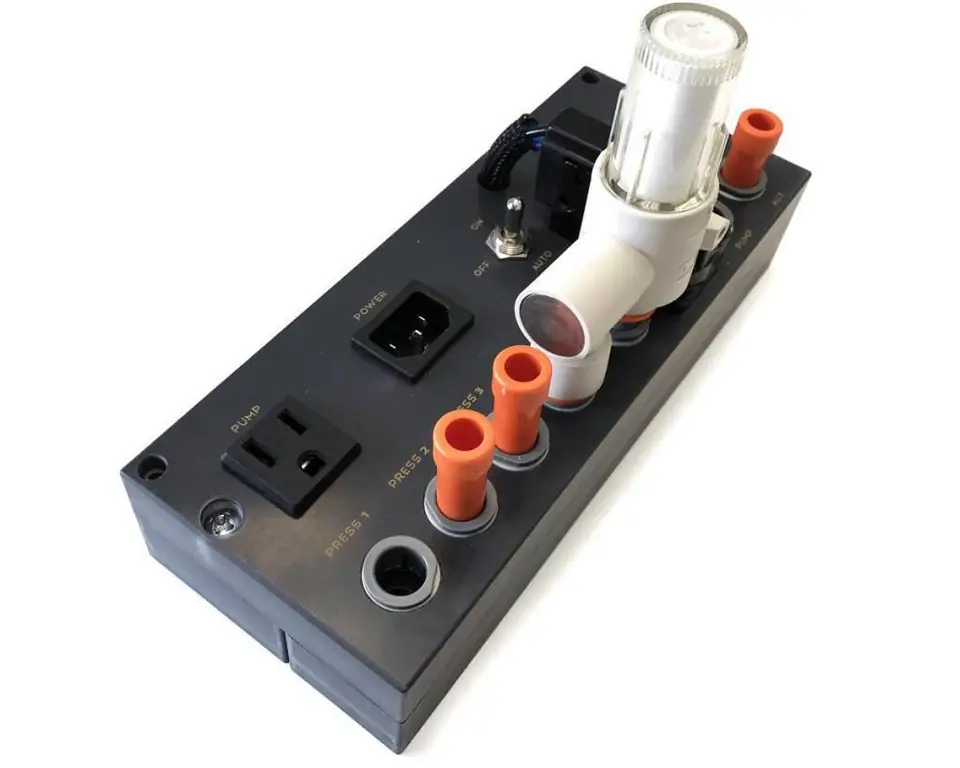
The control automation system should provide the ability to control its work. In addition, it is very important that in the event of a malfunction, the system can diagnose and indicate the place, type and cause of a particular problem. The last important requirement for an automated control system is protection against incorrect actions of personnel. In case of accidental or intentional changes in parameters that can lead the object to a critical state, the control system must be protected. This rule also applies in case information is leaked somewhere.
Parts of ACS. Functional
At present, any information system, including an enterprise management automation system, can be conditionally divided into two components. The first is functional, the second is providing. The first part is responsible for the aspect of actions in which each individual system is created. The combination of these individual tasks creates a functional part of the overall system.
Next, you need to pay attention to the fact that any automated control system must performfollowing steps:
- it must collect, process and analyze all information related to the state of the object;
- the system must be able to develop control methods when the need arises;
- The automated control system must also be able to transfer control actions to the executive elements, as well as transfer data to the operator for control;
- implementation and control of the developed control actions also lies with the control system.
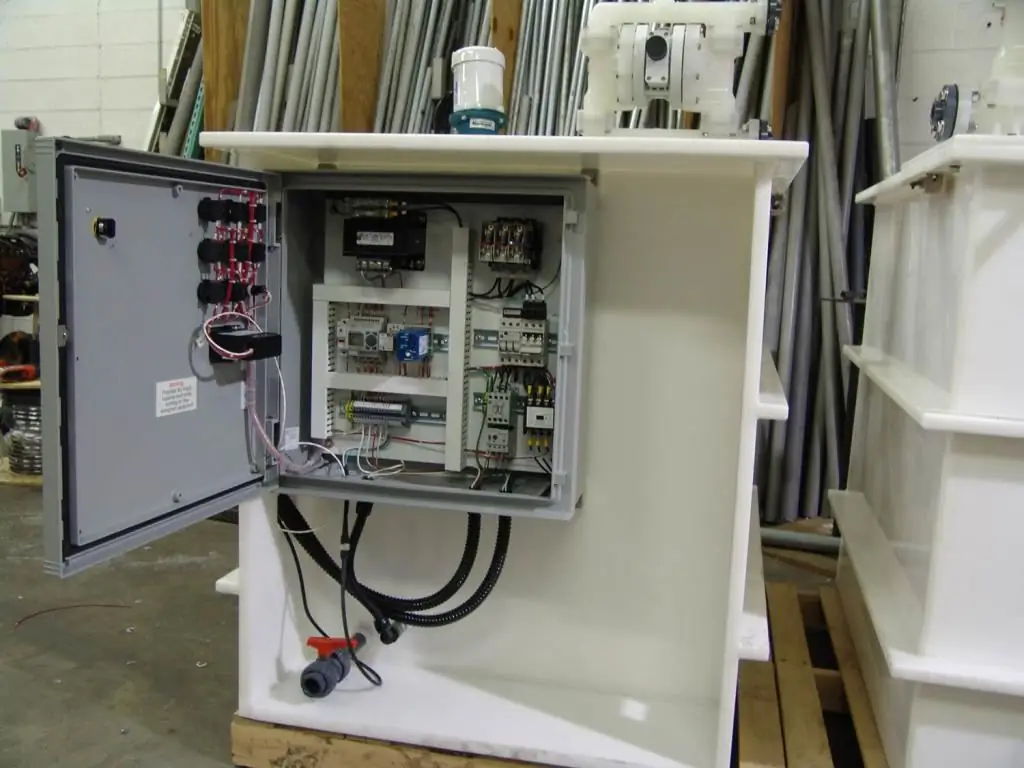
Providing part of the automated control system. Information part
The second big part is providing. It is somewhat more complicated, and it is conditionally divided into several smaller performing groups, which include the following sections:
- program-mathematical;
- informational;
- technical;
- methodological and organizational;
- linguistic;
- personnel.
The operation of the enterprise management automation system, or rather its supporting part, is based on the fact that it collects complete information about the object. Based on the information received, which includes data on encoding, addressing methods, data formats, etc., the ACS will operate. You need to understand that a large amount of information requires storage space. For this reason, all received data is collected in large databases, which are subsequently stored on machine media.
It is important to understand here that to store all information from the beginning of work to this dayImpossible because there is too much of it. Therefore, all stored data is overwritten on media with a certain frequency, which is necessary for the normal operation of the object. In addition, each such process automation system has some kind of backup data storage. It is intended to be able to recover the loss of information if any device fails.
Mathematical part
It should be noted right away that it is the most important in any management system today. The software part of this type includes any software that performs all the tasks assigned to the system, and also ensures the normal operation of the entire complex of technical means used in this enterprise. The mathematical part is the totality of all mathematical formulas, models, algorithms used in the operation of the information system.
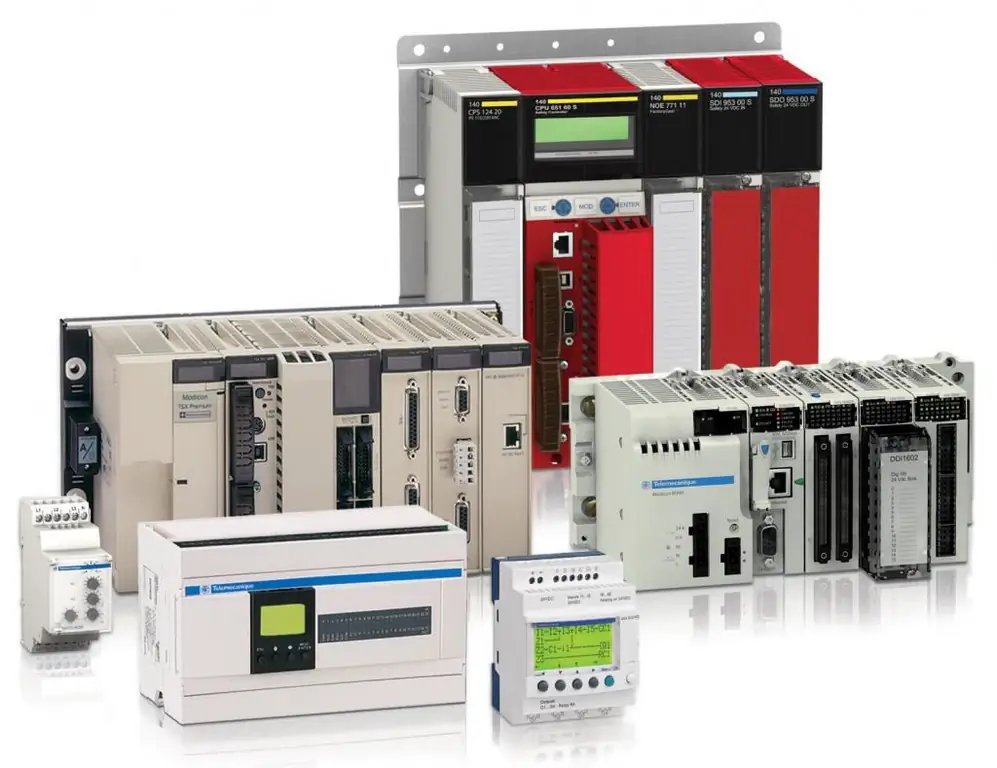
The software of the process automation control system must fully satisfy the performance of all functions that are required from the automation object. It is important to note here that all these functions are implemented using computational tools. There are several specific properties that the software part of the ACS must satisfy:
- Functional sufficiency. That is, the system must be complete.
- It is important that the system is not only reliable, but also has the propertyself-healing, as well as determine the cause of the breakdown.
- The system must adapt to the changing parameters of the object.
- It should be possible to modify if necessary.
- Modularity of construction, as well as ease of use, are also important components of the system.
Technical section
Everything is quite simple here. The technical support includes the availability of all the technical means that are necessary to ensure the maximum functionality of the automated control system. This section is most affected by the development of computer technology and computer technology. Thanks to the development of these two areas, the variety of technical measuring instruments is becoming wider, and by themselves they are able to solve an ever wider range of problems.
Currently, systems and technical means of automation and control can be divided into two large groups. The first group is the means of communication, and the second is the means of organizational technology.
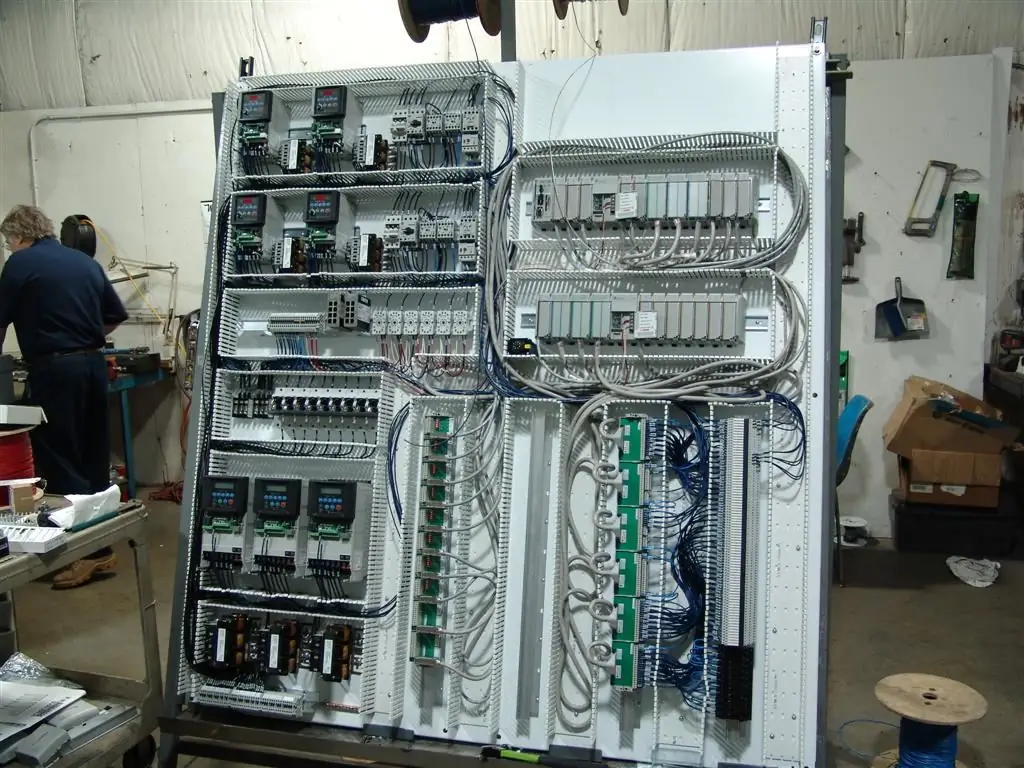
Here it is necessary to understand that the technical means of automation are used at all stages of the operation of the automated control system, from fixing the parameters to their storage, and also with their help it is possible to connect the entire control system into a single network. If we talk separately about the means of communication, then they, first of all, play the role of transmitters of information from one device to another. In some rare cases, they work together with computers. Organizational technology is a device that allowsperform various operations with previously obtained information.
A rather important rule is that any technical means of the automated control system, in the event of a breakdown, should be replaced with a similar one without any problems, without the need to reconfigure it.
Methodological and organizational section of the system
Designing a control automation system implies the presence of such a section as methodological and organizational. This branch of the automated control system is a set of methods, tools and some special documents that establish the operating procedure not only for the system itself, but also for the personnel who maintain it. In addition, there are also documents that systematize the procedure for the work of personnel when interacting with each other. This also includes some methods, as a result of which personnel are trained to work with a particular information system. In other words, this is a section that affects not only the system itself, but also the human factor.
The main purpose of this section is to keep the system up and running as well as allowing it to be further developed if necessary. It may be added that this section contains instructions that relate to what personnel need to do during the operation of the ACS in order to maintain its normal functioning. It also stores files that carry information about what needs to be done if the system goes into emergency mode or simply does not function as it should.
Linguistics
The last section of the supporting part of the ACS is linguistic. Naturally, this system is a language set. This includes the languages of communication of the personnel who services the production management automation system, as well as its users with such parts of the system itself as technical, informational, and program-mathematical. There are also transcripts of all the terms and definitions used by the ACS during its work.
During operation, it is very important that operators can communicate with the control system in a timely and convenient manner. It is due to linguistic support that the required convenience, unambiguity and stability of this communication is achieved. It is only necessary to add that here it is necessary to have technical means that will correct errors, if any, during communication between the user and the automation system. To date, there are two different approaches to working with ACS.
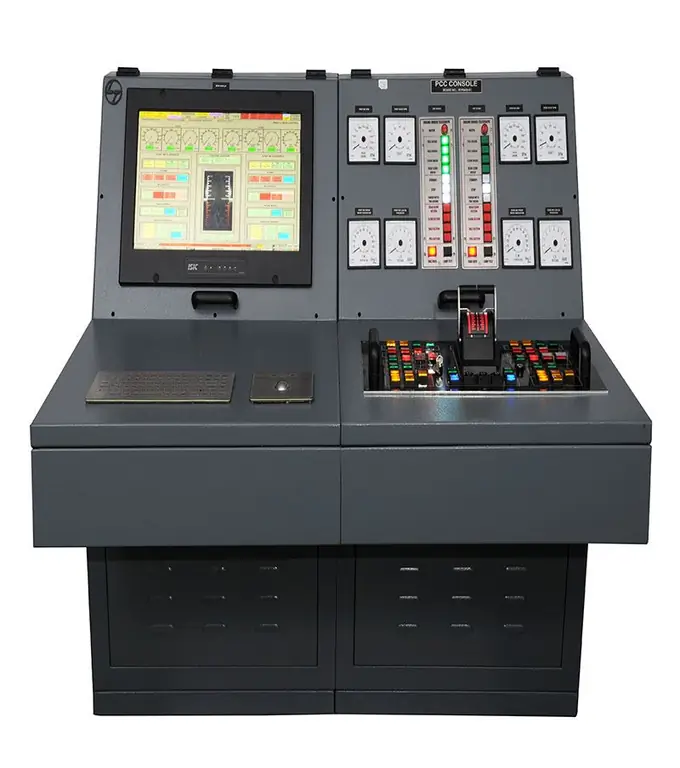
The first way in which the automation management process is carried out is the installation and use of computer technology. These tools will be used only to simplify some of the operations that occur when working with documents. To date, this method is considered ineffective, since it does not allow you to fully unlock the potential of the current level of computer technology.
The second method is fundamentally different from the first and lies in the fact that the enterprise creates an integrated management automation systemobjects. In this case, not only document management is transferred to the technician, but also databases, expert systems, communication tools, as well as many other functions.
Lower and middle level of ACS
Any process control system today can be conditionally divided into several levels. Automation of the control system currently has three such levels.
The lower level is the sensors, as well as measuring devices that control the controlled characteristics. In addition, this also includes actuators, on which the value of the characteristics depends. At this level, only minimal control is carried out, which consists in matching the signal from the sensor with the input of the control device. There is also an exchange of signals generated by these devices with actuators.

The next middle level is equipment management. In other words, programmable logic controllers are located on this control step. These PLCs are capable of receiving signals from measuring equipment as well as from sensors that monitor the state of the process. In accordance with the information received, as well as the data that is set by the user, the PLC generates a control signal that is transmitted to the actuator with a clear command.
Top Level
Automation of control in technical systems also has a third, higherlevel. Such equipment is operator and dispatching stations, network equipment, industrial servers. It is at this stage that full control over the course of technological operations at the facility is exercised by a person. In addition, communication with the two previous levels is also provided here, which allows you to successfully collect any necessary information.
At this stage, HMI, SCADA is used. The first is a human-machine interface, with the help of which the dispatcher is able to monitor the progress of technological operations at the facility. This includes various monitors or graphic panels, which are most often installed on automation cabinets and are intended only to display information about the object and the progress of the process. In order to control the automation equipment and the control system, there is a SCADA system, which implies the presence of supervisory control and the ability to collect data. In simple terms, this network allows you to install software that can be configured and installed on dispatchers' computers.
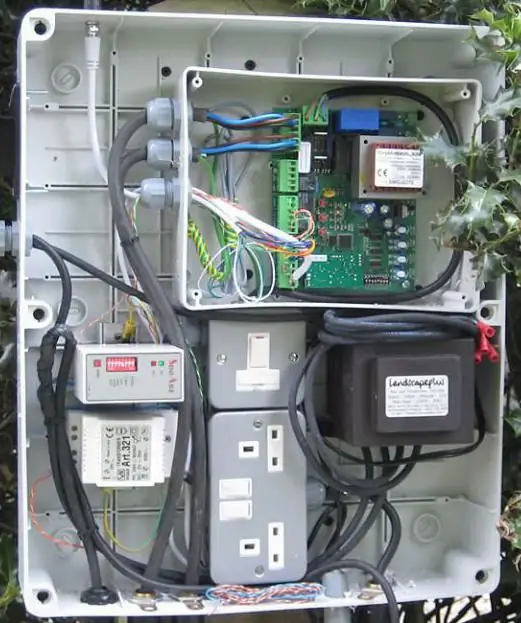
All the most important data that the PLC collects at the middle level are collected, archived and visualized using this system. The basis of automation lies precisely here, since SCADA is able not only to receive information, but also to compare it with the one that was entered by the operator. If there is a deviation of any parameter from the set value, the system notifies the user about this by means of an alarm. Somesystems have the ability not only to control, but also to automatically change any values in order to return a value that has gone beyond the established limits.
Automation tools
The automation system for personnel management, the technological process is carried out at the expense of technical means of automation, or TCA. In other words, these are devices that can either be a technical tool in themselves and carry out any activity, or be part of a hardware-software complex.
Most often, TCA is the basic element of an automation system. This includes all equipment that captures, processes, transmits information. With the help of such tools it is possible to control, adjust and monitor the automated aspects of the production process. There are TCAs that control some parameter. These can be pressure, temperature, level sensors, capacitive sensors, laser sensors, etc. Next are informational TSAs, the main task of which is to transfer the information received from the sensors. In other words, it is the link between the lower level and the higher level control equipment.
Control equipment has the ability to completely or partially stop the production process until the cause of the stop is eliminated. Also, some advanced systems can do their own troubleshooting. In this case, they refer to self-healing control and management systems.
Recommended:
Hydraulic system: calculation, scheme, device. Types of hydraulic systems. Repair. Hydraulic and pneumatic systems
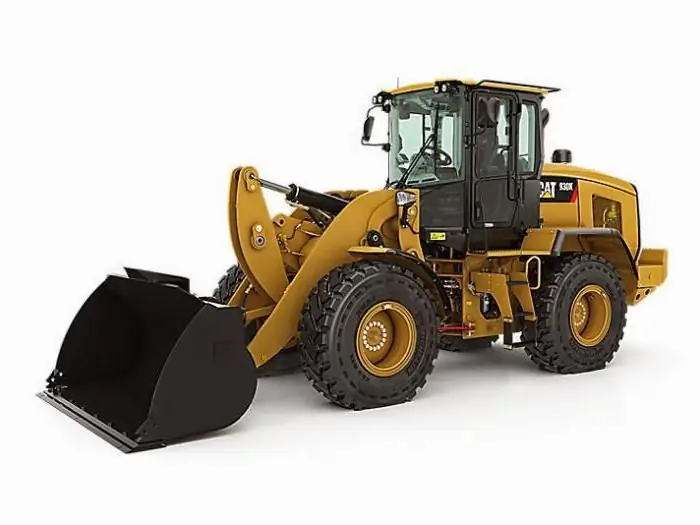
The hydraulic system is a special device that works on the principle of a liquid lever. Such units are used in the braking systems of cars, in loading and unloading, agricultural machinery and even in the aircraft industry
Small business automation: forms, programs, tools
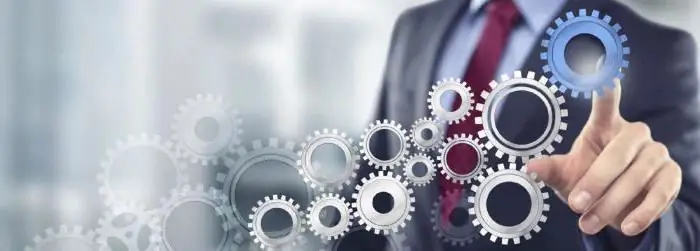
Small business automation tools make workflow more efficient, streamlined
Control of cash operations of the bank. Overview of cash transactions control systems
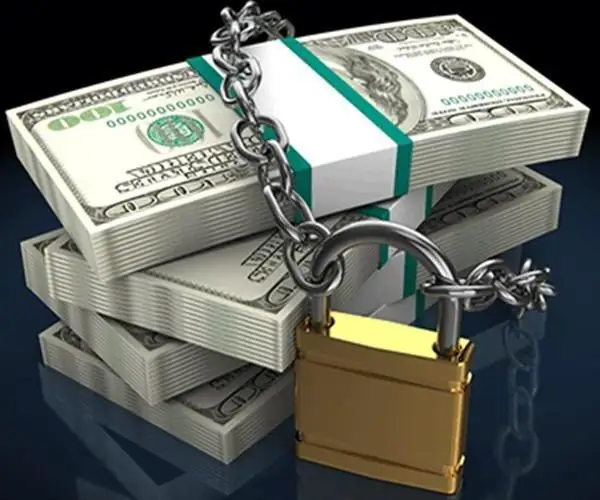
Since various kinds of fraud often occur in the field of cash register accounting, every year the control of cash transactions becomes more and more complicated, tougher and modernized. This article discusses the role of the cash desk in the enterprise, the rules of conduct, as well as methods and systems for monitoring operations
Automation of business systems: tools and technologies
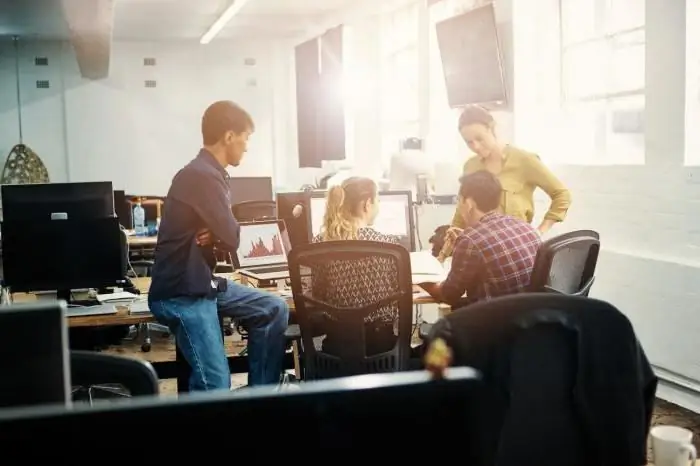
CRM-systems, ERP-solutions, WEB-tools and BPM-concepts - all these terms fall upon today's entrepreneurs who are striving to modernize their business. What's this?
Visa and Mastercard systems in Russia. Description of Visa and Mastercard payment systems
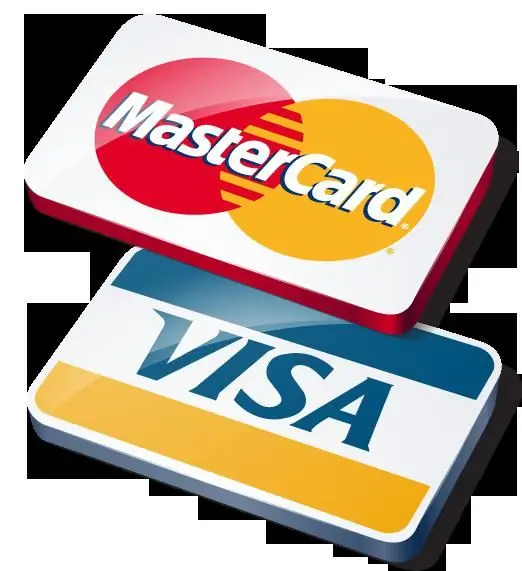
Payment system - a commonality of methods and tools used for money transfers, settlements and regulation of debt obligations between participants in economic turnover. In many countries, they differ significantly from each other due to the diverse provisions in the levels of economic development and the characteristics of banking legislation