2025 Author: Howard Calhoun | [email protected]. Last modified: 2025-01-24 13:10
Shelving is a storage structure that is used to store various materials, goods and equipment. The safety of the personnel serving them depends on their quality. When a structure collapses, the loss can amount to thousands, millions of rubles. To prevent the negative consequences of violating the integrity of the nodes and elements of the system, racks are periodically tested.
There are a number of features of such a process. Various methods are applied. How the process of testing the strength of structures is organized and carried out will be discussed further.
Need verification
Test racks (GOST 55525-13) is made for a number of reasons. First of all, when creating a new design, there may be certain errors in the casting of its elements. In this case, the structure will not be able to withstand the intended loads.
To avoid destruction of the structure, the manufacturer tests the objects it creates. At the same time, he fixes the facts of miscalculation during the technological cycle. Errors in drawings are fixed.
Alsothe manufacturer must establish the conformity of the real indicators of the rack with the declared characteristics. This allows you to prevent an accident during the operation of the facility. In this case, it is possible to significantly reduce the likelihood of not only the occurrence of economic damage, but also injury or even death of warehouse employees. This is one of the effective environmental measures.
What time is the inspection?
Shelving test instructions involve testing in four main cases. The first time such testing is carried out in production. When a new structure is created according to new drawings, a trial structure is made. It is subjected to testing to identify errors during development. If all requirements are met, the product goes into series production.
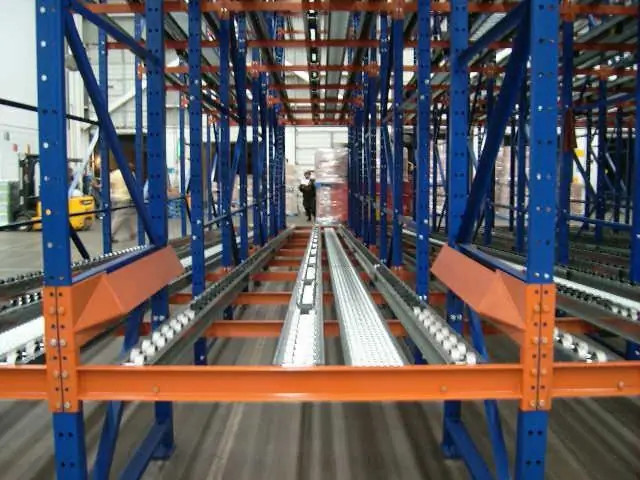
After manufacturing a batch of similar systems, several trial units are selected from them. If the characteristics of the warehouse equipment meet the standards, all created products go on sale.
Before installing the racks, the storage conditions are checked. After installation, the strength of all connections of each shelf and support is also tested. During operation, the product is also periodically checked. The approximate frequency is once every two years. This procedure is carried out up to the write-off of the structure from the balance of the company.
What the check looks for
There is a certain list of issues that inspectors pay attention to. The results are fixeddocumented. For this, an act of testing racks is drawn up, a sample of which is presented below.
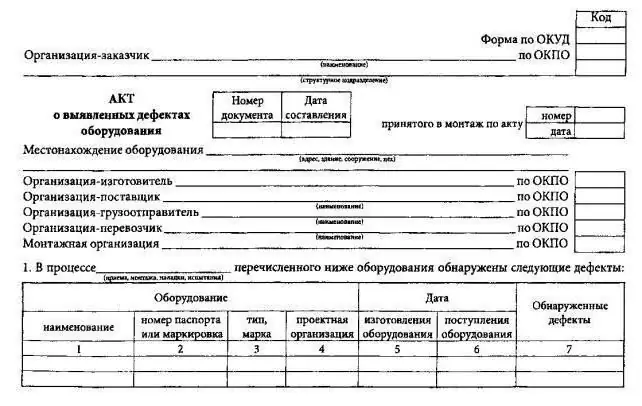
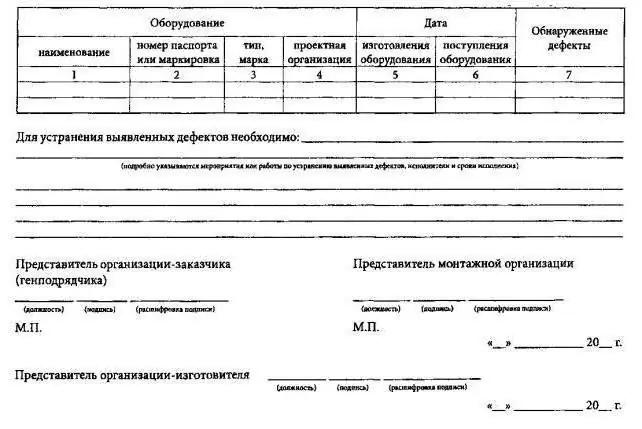
Deviations from the horizontal, vertical level of racks and beams are investigated. At the same time, the features of warehouse racks must be taken into account.
The error in the deviation of the cross-sectional index of the bearing elements is determined. Such deviations provoke very high loads. Also, researchers must evaluate the appearance of beams, racks, shelves, pallets.
It is important to pay attention to the integrity of the seams left after welding, or threaded connections (using bolts). Compliance with the standards for the spacing of the placement of bearing supports and crossbars is being tested. At the end of the check, the compliance of the load capacity of the rack with the characteristics stated in the passport is established.
External inspection
After the inspection, the manufacturer and the user must draw up a test report for the racks. It contains the data of the conducted researches. This is an official document, the design of which is regulated by the relevant standards.
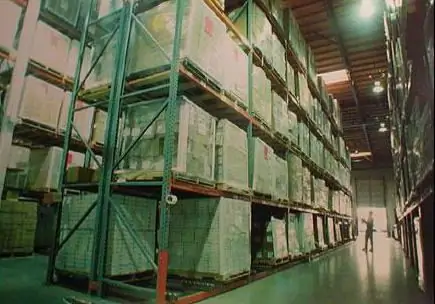
In order to understand the entire verification procedure, it is necessary to consider in more detail the stages of its implementation. First, a visual inspection is performed. The inspector assesses the quality of the materials. He must inspect the surfaces of all elements for defects. The protective layer that prevents the material from breaking down must remain intact. It does notmust be chipped and scratched.
After that, the geometry of the beams and supporting pillars is evaluated. Their value must comply with the standards. If there are traces of oxidative reactions on the surface of metals, their degree is established. The presence of burrs, delaminations and other defects is taken into account.
Welds
Before testing the racks, the joints of all elements of the system are inspected. They can be attached to each other with screws or welded. In these places, as a rule, the structure is most susceptible to the negative effects of the load. Therefore, the quality of welds is determined in special ways.
It can be ultrasonic, acoustic, luminescent or chemical method. Each of the selected methods allows you to assess the state of the joints. At the same time, the presence of sagging, inclusions of slag or incomplete penetration is excluded at the seams. There should be no cracks or undercuts at the joints.
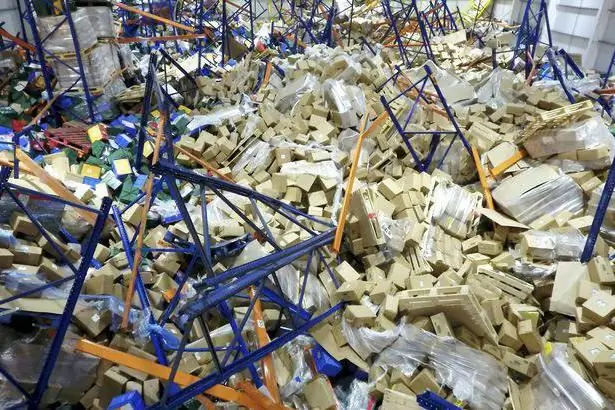
Also, the test establishes the cleanliness of the welds. They must be free of scale or contamination. Otherwise, the system will quickly collapse.
If the connections are classified as screw type, their screed is evaluated. Paired elements (nut and bolt) must be firmly tightened.
Test Method
When checking the quality and strength of racks, in addition to visual inspection and assessing the quality of joints, other methods are also used. They are addressed only after a satisfactory external condition of the structure. In this case, the testracks per load.
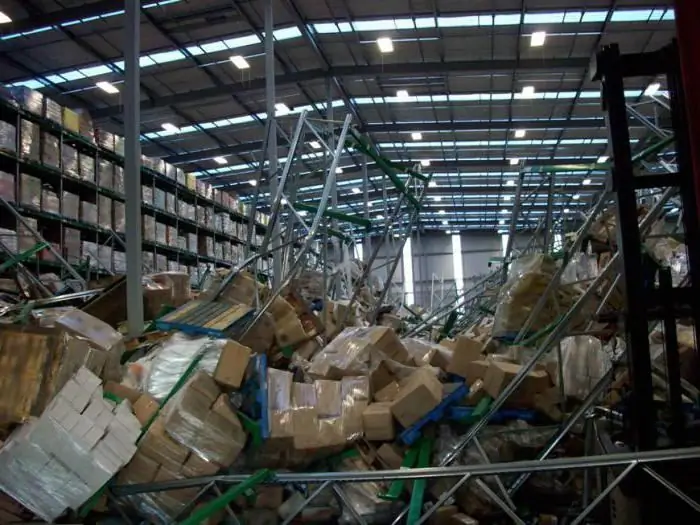
Such a check is performed in two directions. In the first case, the constituent elements are subjected to a vertical load, and in the second - a horizontal one. These are effective methods that allow you to objectively assess the condition of the racks.
Vertical load is applied to the beams. It exceeds by 25% the maximum allowable weight limit that the object can support. The data is taken from the passport of the structure. During the study, deflection indicators are measured. It should not exceed 1/200 of the beam length.
The horizontal load of the shelves is 50% of the maximum value. The perpendicular deviation should be as small as possible.
Completion of verification
After testing the racks, the residual deformation is measured. Again, a visual inspection of the object is performed. Welds or screw connections are also re-inspected.
After the check is completed, an act is drawn up. It contains all measurement parameters. It also sets the level of risk. The European system of standards is most often used for evaluation. It involves three levels of risk.
If the equipment is classified as a green zone, it has minimal damage that does not affect the load-bearing qualities of the structure. The amber zone includes shelving units that are slightly damaged. However, their use is permitted. If the object is in the red zone, its use is dangerous and is strictly prohibited.
Verification Benefits
Todaytesting of racks is carried out without fail by all warehouse organizations and industries that produce such equipment. This allows you to assess the state of the object of study, as well as approximately calculate the period of its operation.
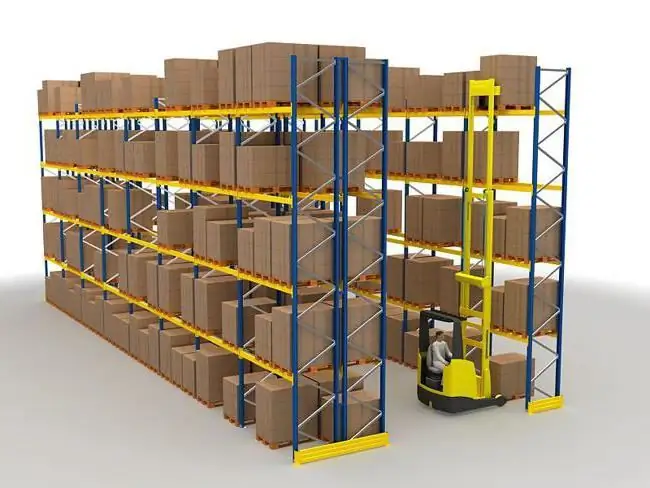
Metal beams, girders and support posts build up stress over time. In this case, the surfaces are periodically subjected to mechanical damage. This does not improve the condition of the shelving. If you do not pay attention to the defects that have arisen in time, the collapse of the structure cannot be avoided. It is the verification that makes it possible to determine the impossibility of operating the structure even before the fatal consequences.
The inspection process also takes into account the features of operation, maintenance of racks by warehouse personnel. For example, rented warehouses need to be inspected more frequently because they tend not to be run sparingly.
Having considered the procedure for testing racks, you can qualitatively assess the condition of the structure. This will protect the object from destruction, injury and loss of life.
Recommended:
Analysis of the financial performance of the enterprise: goals, methodology
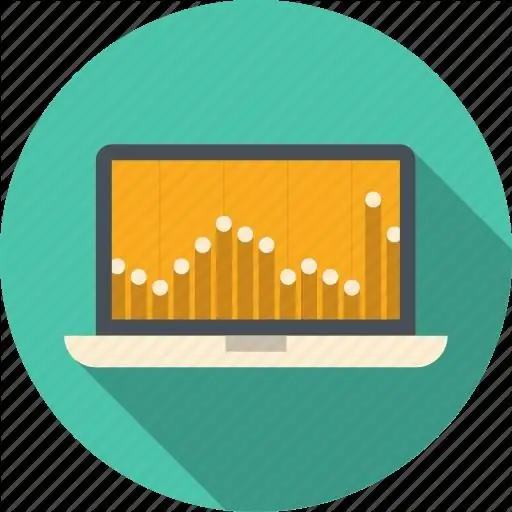
Control, of course, is an important part of the work to ensure the activities of any organization. It can take many different forms, each of which has its own characteristics and specifics. Control can be current when carried out in the course of activity. It is also based on data that are summed up as a result for a certain time period. In this case, first of all, they recall the analysis of the financial results of the enterprise / organization
Methodology of Mark Belov. User Reviews
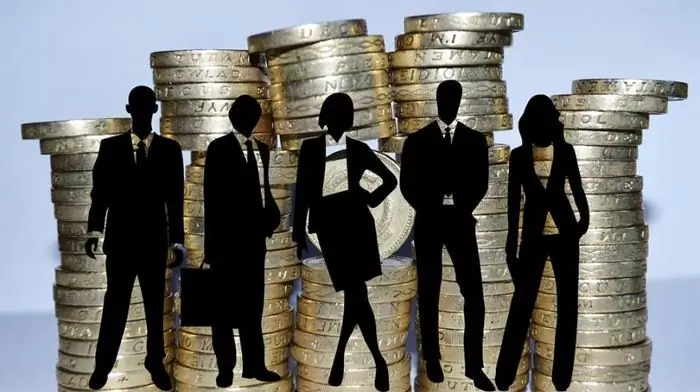
According to the assurances of those who left rave reviews about Mark Belov and his training videos, today's online businessmen no longer bother to write feature articles
Slow-moving assets: solvency analysis methodology
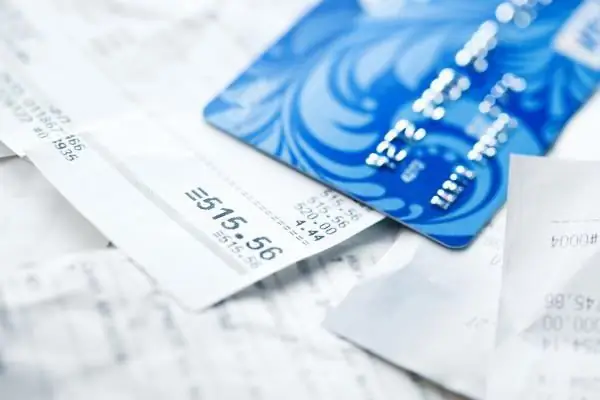
The value of slow-moving assets is the most important indicator in the analysis of the company's solvency. How are these assets determined? How are they used to evaluate the effectiveness of business management?
Methodology for calculating lease payments
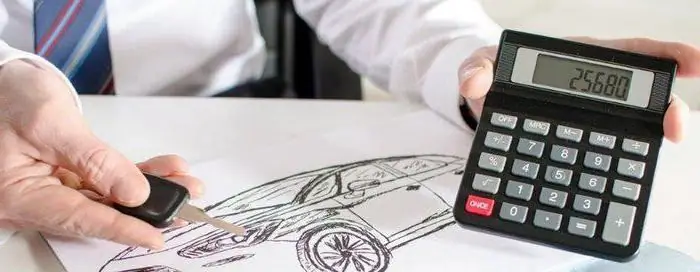
The word "leasing" has English roots. Translated, the term means "rent". Leasing is a type of financial services, a specific form of lending for the acquisition of fixed assets by enterprises or expensive goods by individuals
Unified methodology for calculating damages under OSAGO. Unification of the calculation of damage under OSAGO
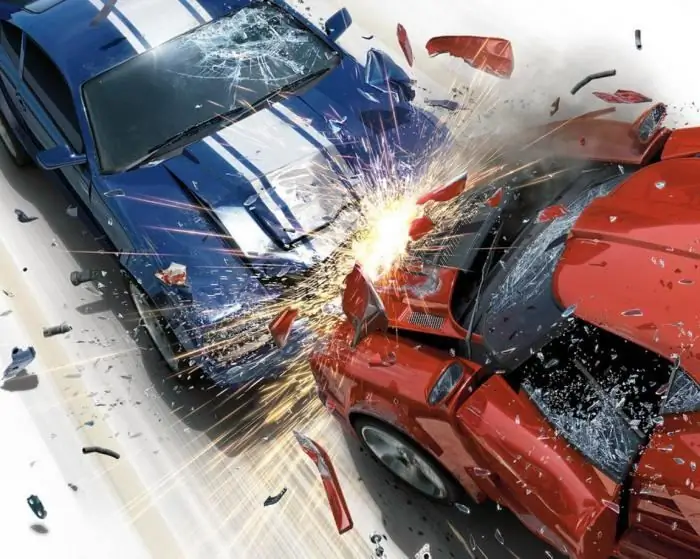
In 2014, a new methodology for assessing damage after an accident came into force. The project and concepts of pre-trial dispute resolution were developed by the Ministry of Transport in 2003, but for 11 years they have not been used. Insurers all this time calculated the damage in their own way. But, when the plenum of the Supreme Court extended the law “On Protection of Consumer Rights” to OSAGO, they decided to recall the document