2025 Author: Howard Calhoun | [email protected]. Last modified: 2025-01-24 13:10
Acoustic emission of pipelines is the occurrence and propagation of elastic vibrations in the process of deformation of the structure under study. Quantitatively, it acts as an indicator of the integrity of the material under various loads. Acoustic emission testing can be used to detect defects at the initial stage of structural failure. The main diagnostic method is the passive collection of information and its subsequent processing.
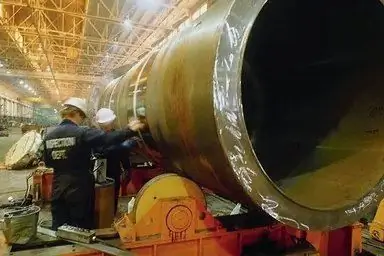
General characteristics
Acoustic emission is used to detect and establish coordinates, monitor deformation sources on surfaces or in the volume of walls, welded joints and structural elements. Diagnostics is performed only when a stress state is created. It initiates the work of vibration sources in the object. Acoustic emission occurs when exposed to pressure, force, temperature field, and so on. The choice of a specific load is determined by the design features, the conditions in which it is used, and the specifics of the tests.
Acoustic emission method
Fordetermining the reliability index of the structure, its parameters and properties are checked, in which its integrity and suitability for use and operation should not be violated. Traditional methods (ultrasonic, eddy current, radiation, and others popular in practice) make it possible to identify geometric inhomogeneities by emitting a certain energy into the structure of an object. Acoustic emission suggests a different approach. First of all, the material itself acts as a signal source, and not an external object, since this is a passive method of verification, and not active, as indicated above. In addition, acoustic emission makes it possible to detect not static inhomogeneities, but the movement of a defect. Accordingly, it can be used to identify developing and, therefore, the most dangerous damage. This method allows you to quickly detect the growth of small cracks, liquid or gas leaks, faults and other processes that cause the occurrence and propagation of vibrations.
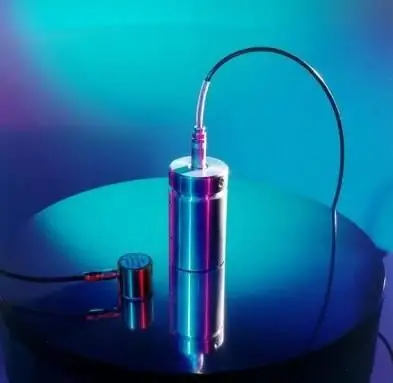
Nuances
In theoretical and practical terms, any defect is capable of producing its own signal. It can cover quite large distances (several tens of meters) until it is detected by an acoustic emission sensor. Moreover, destruction can be detected not only remotely. Defects are also established by calculating the difference in the time of arrival of waves to the catching sensors located in different areas. Crack growth, delamination, inclusion fracture, friction, corrosion, liquid/gas leakage are examples of processes thatproducing vibrations that can be detected and effectively investigated.
Features
The main advantages of the method over traditional methods of non-destructive testing are:
- Integrity. It consists in the fact that, using one acoustic emission transducer, fixedly mounted on the surface of the structure, it is possible to check the entire structure. This property is especially relevant when studying hard-to-reach or inaccessible areas.
- No need for careful preparation of the surface of the object under study. It follows from this that the control process itself, as well as its results, will not depend on the state of the structure and the quality of its processing. If there is an insulating cover, then it should be removed only in the areas where the trapping devices are installed.
- Identification and registration of only developing destruction. This makes it possible to classify defects not by their size or other indirect indicators (position, shape, orientation), but by the level of their danger (degree of influence on the strength of the object).
- High performance. It is many times higher than the corresponding indicators for traditional (radiographic, ultrasonic, magnetic, eddy current, etc.) methods of control.
- Distance. Testing the strength of an object can be performed at a considerable distance from the operator. This feature makes it possible to apply the method in monitoring the state of large-sized, especially dangerous, extended structures withoutdecommissioning and threats to personnel.
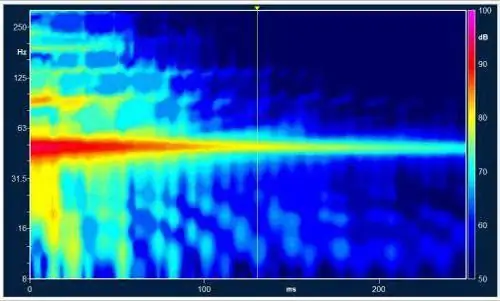
Another advantage is the ability to monitor various technical processes and assess the state of the structure in the current time mode. This allows you to prevent the accidental destruction of the object. It should also be noted that the acoustic emission method optimally combines quality and cost parameters.
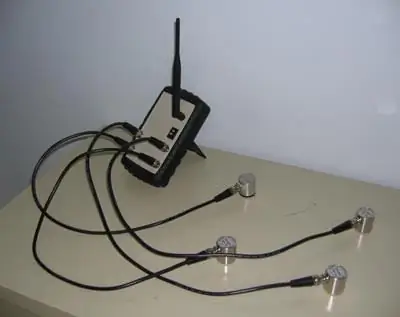
Extra
Control using acoustic emission provides a huge amount of information, allows you to quickly adjust and extend the operation cycle of critical industrial installations with minimal costs. The results of the performed checks are used in predicting accidental damage. This method of control can be used in the study of various properties of materials, structures, substances. Today, without its use, it is impossible to create, as well as reliable operation of many critical industrial facilities.
Cons
The method of acoustic emission also has some drawbacks. The main disadvantage is the complexity of deciphering the indicators obtained during the verification. This disadvantage significantly limits the wide application of the method in practice. The complexity is due to the fact that the wave processes during acoustic emission are superimposed by the so-called parasitic indicators of multiply reflected noise, waves from the operation of the equipment, the loading object, and the environment. The use of protection systems and various filters allowsonly partially reduce the impact. In addition, the uniqueness of the equipment used in the control is considered a disadvantage. In industry, it is not mass produced. It also prevents the method from being extended beyond the field of experimental use.
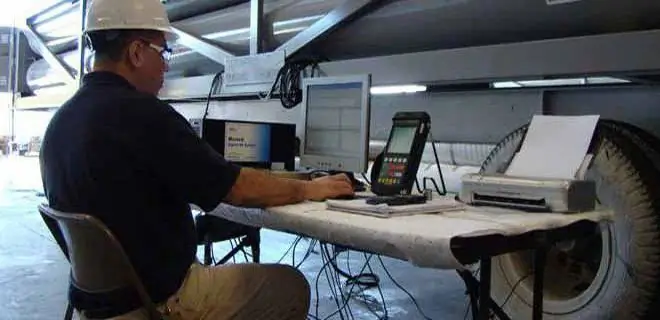
Application areas
As mentioned above, at present, the method of acoustic emission is used by various enterprises engaged in various economic sectors. The main ones include:
- Chemical and oil and gas industry.
- Metallurgy and pipe production.
- Thermal and nuclear power industry.
- Rail transport.
- Aviation and space complex.
The method is widely used by enterprises working with lifting, bridge structures, concrete and reinforced concrete structures.
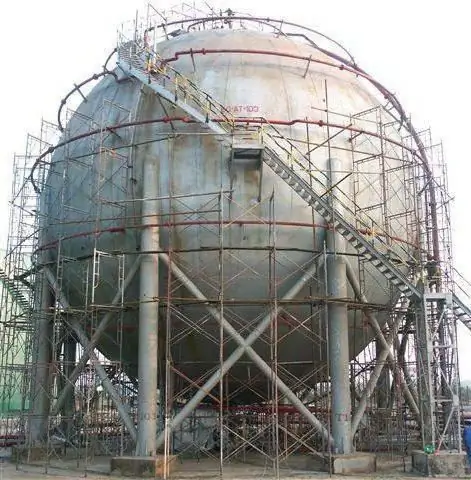
Conclusion
The acoustic emission method is today considered one of the most effective ways to perform non-destructive testing and assess the state and properties of materials. It is based on the identification of elastic waves generated when a sudden deformation of a structure under load occurs. The resulting oscillations depart from their source and are sent directly to the sensor, where they are transformed into electrical signals. They are measured with special devices. After that, the processed information is displayed. Based on it,subsequent assessment of the state and behavior of the structure of the objects under study.
Recommended:
Tread protection against corrosion. The main ways to protect pipelines from corrosion
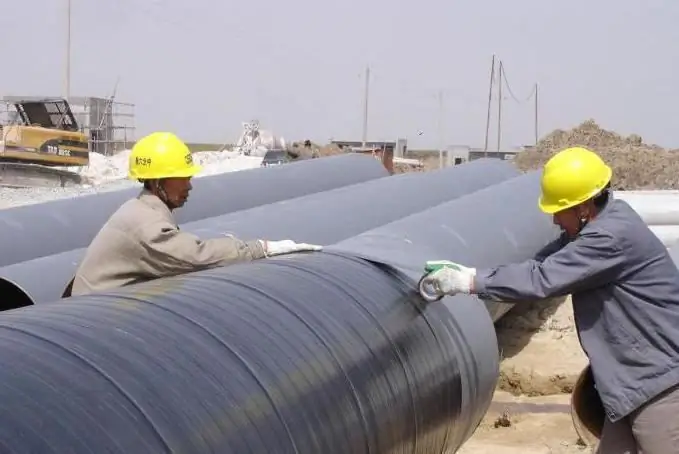
Protective corrosion protection is a universal solution when it is required to increase the resistance of metal surfaces to moisture and other external factors
Pipeline transport: Russian oil pipelines
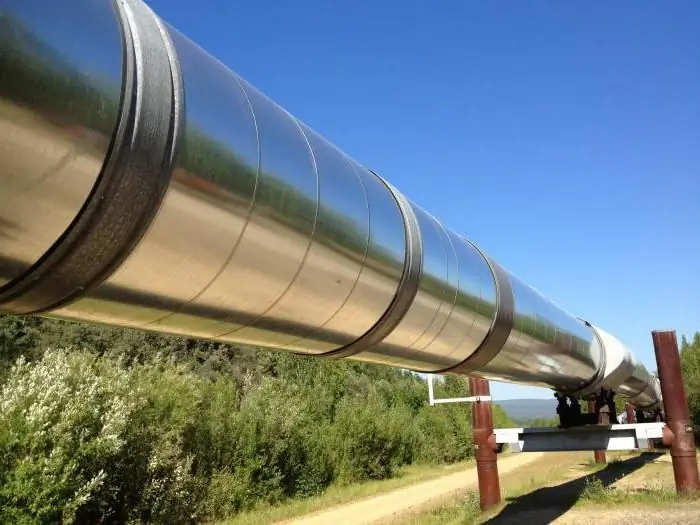
Russian oil pipelines are one of the key components of the fuel and energy sector of the country's economy. Today, the Russian Federation has an extensive network of oil pipelines, gas pipelines and oil product pipelines of various significance. Pipeline transport connects the territories of most subjects of the Federation, and also serves to export hydrocarbons and products of their processing
Technological pipelines: installation, recommendations and operating rules
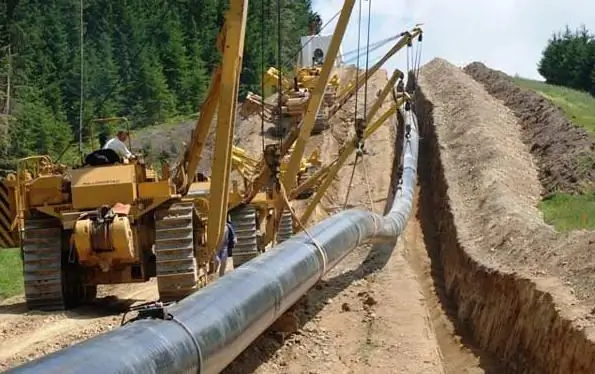
A significant amount of construction of the main facilities in the oil refining, metallurgical, food industries is given to the arrangement of technological pipelines
Categories of pipelines. Determining the pipeline category. Classification of pipelines by categories and groups
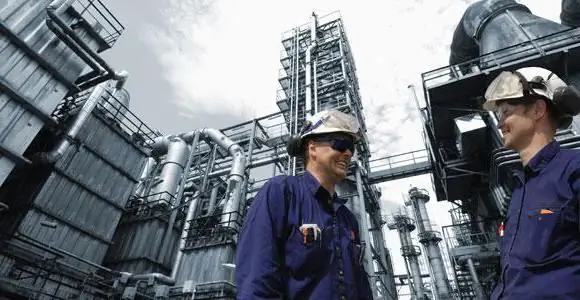
Modern industry cannot do without quality pipelines. There are many types of them. What are the categories of pipelines, how to determine them, is described in the article
Cathodic corrosion protection of pipelines: equipment, principle of operation
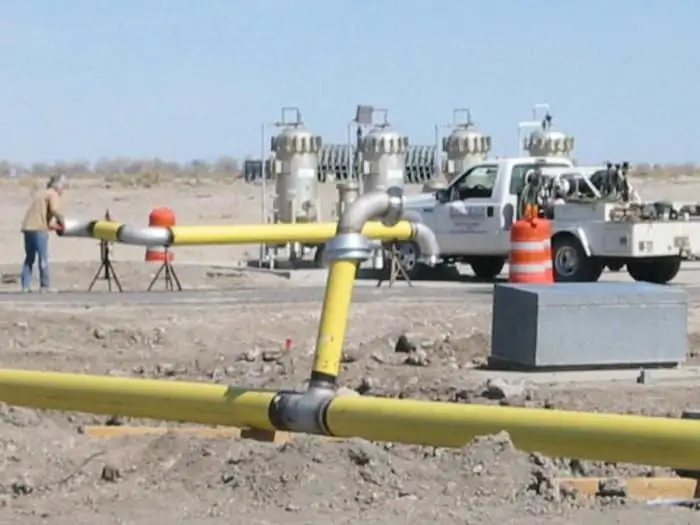
The article is devoted to the cathodic protection of pipelines from corrosion. The types of stations that implement such protection and the principle of operation of the technique are considered