2025 Author: Howard Calhoun | [email protected]. Last modified: 2025-06-01 07:12
A significant amount of construction of the main facilities in the oil refining, metallurgical, food industries is given to the arrangement of technological pipelines. They play a crucial role in the functioning of strategically important systems. Also, technological pipelines are used in agro-industrial complexes, heat supply systems and in many other industries.
Basic concepts
A pipeline is a device designed to transport a variety of substances. It consists of pipe sections, connecting and shut-off valves, automation and fasteners.
What is the meaning of the term "technological pipelines?" The definition designates them as supply systems for industrial enterprises through which semi-finished and finished products are transported, as well as substances that ensure the conduct of the entire process.
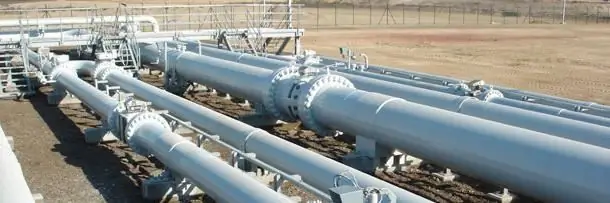
Pipe locations
In the process of laying it is necessary to follow these recommendations:
- Process piping should be as short as possible;
- insagging and stagnation are unacceptable to the system;
- providing free access for technological control;
- possibility of locating the necessary lifting and transport vehicles;
- providing insulation to prevent moisture penetration and retain heat;
- protect pipelines from possible damage;
- free movement of fire fighting equipment and lifting gear.
Slope angles
Operation of technological pipelines provides for forced shutdowns. To do this, slopes are laid in the project, which will ensure arbitrary emptying of pipes. Process piping arrangement provides the following slope angle depending on the conveyed medium (values are given in degrees):
- gaseous medium: in the direction of movement - 0.002, against it - 0.003;
- liquid highly mobile substances - 0.002;
- acidic and alkaline - 0.005;
- substances of high viscosity or fast setting - up to 0.02.
The design may not provide for a slope, then special measures must be taken to empty the pipelines.
Preparatory work
Installation of process pipelines must first be accompanied by the following steps:
- Checked all project details and made necessary changes.
- The degree of readiness of building structures and structures for installation has been determined.
- The complete set of lines with the necessary fittings, elements anddetails.
- Accepted individual pipeline units and components, in accordance with regulatory documents.
- Checked the readiness of temporary sites for installation work, equipped with lighting, power sources for welding, devices for working at height.
- The necessary recommendations for the installation of process pipelines in accordance with safety regulations have been observed.
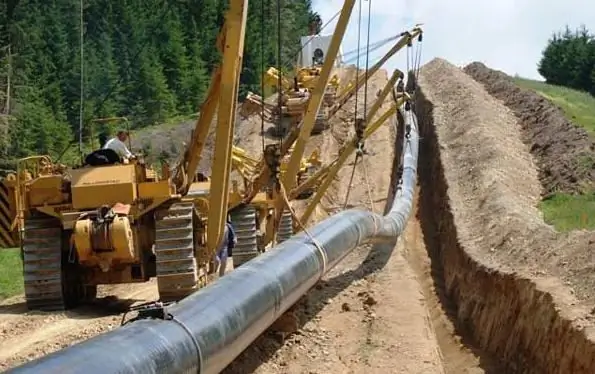
Route markings
This operation consists in transferring the axes of reinforcement and compensators fastening directly to the place where technological pipelines will be laid. Determination of the markup location can be performed by the following tools:
- roulettes;
- plumb lines;
- level;
- hydraulic level;
- templates;
- gons.
If a large number of technological pipelines are laid for a building structure, the time allotted for marking is significantly reduced due to the use of special layouts. They give a visual representation of the location of the pipeline lines in relation to the building structure. All applied elements after marking are compared with the project, after which they begin to fix the supporting structures.
Installation of supports and mounts
During the arrangement of the foundation of the building, holes must be provided in it for laying bolts, fastening supports. They can be made by mechanized equipment. During the installation of supports should befollowing recommendations were taken into account:
- Technological pipelines, which have fixed supports, described above, require the installation of fasteners in close proximity to the apparatus and fittings. The installation of pipes on such supports must be tightly fixed, not allowing shifts. The same requirements apply to clamps.
- Mobile supports are mounted with the possibility of free movement of the pipeline in order to easily extend it if necessary. The thermal insulation must also be protected from potential movement away from the expansion.
- All installation supports must be checked by the process piping installer for horizontal and vertical alignment. Possible deviations are foreseen, which cannot exceed the following limits:
- intrashop pipelines - ± 5 mm;
- outdoor systems - ±10 mm;
- slopes - 0.001 mm.
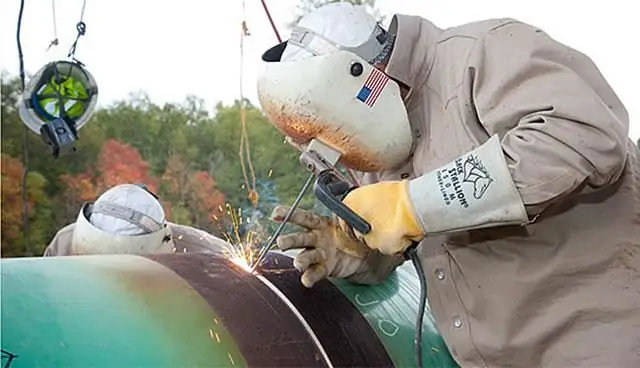
Piece into existing systems
Special permits are required for this, and a process piping installer must be present on site to service these lines. Insertion is carried out when a new mounted component is connected to an existing system. Usually, for such cases, the installation of shut-off equipment is provided, but if there is none in the existing system, then they resort to a tie-in. There are several features here:
- The existing pipeline must be shut down andempty.
- Pipes transporting flammable and explosive media must be neutralized and washed.
- The welded fitting must pass preliminary tests. The steel grade is also set according to the documentation.
- Welding work must be carried out by a highly qualified specialist with a special permit for critical structures.
- Before the installation of process pipelines begins, the connecting assembly must pass all tests.
Purge and flush
The assembled pipeline is subjected to cleaning, the method of which depends on the size of the pipe:
- diameter up to 150 mm - washed with water;
- over 150 mm - blown with air;
The area to be cleaned must be isolated from other piping lines with plugs. Flushing with water is carried out until water begins to flow from the pipe without contamination. Purge is carried out for 10 minutes. These methods are used if the technology does not provide for other cleaning standards. After the work done, you can proceed to the tests, which are performed in two ways: hydraulic and pneumatic.
Hydraulic testing
Before checking, technological pipelines are divided into separate conditional sections and the following activities are carried out:
- control by external inspection;
- checking technological documentation;
- installation of air valves, temporary plugs (the use of permanent equipment is prohibited);
- off testcut;
- connect test section to hydraulic pump.
Thus, the strength and density of the pipeline are checked simultaneously. To determine the degree of strength, a special value of the test pressure is taken into account:
- Steel pipelines operated at operating pressures up to 5 kgf/m². The value of the test parameter is 1.5 of the working pressure, but not less than 2 kgf / m².
- Steel pipes operating at pressures exceeding 5 kgf/m². The parameter value for testing will be 1.25 working pressure;
- Cast iron, polyethylene and glass - 2 kgf/m².
- Non-ferrous metal pipelines - 1 kgf/m².
- For pipes made of other materials - 1.25 working pressure.
The holding time under the set pressure value will be 5 minutes, only for glass pipelines it is quadrupled.
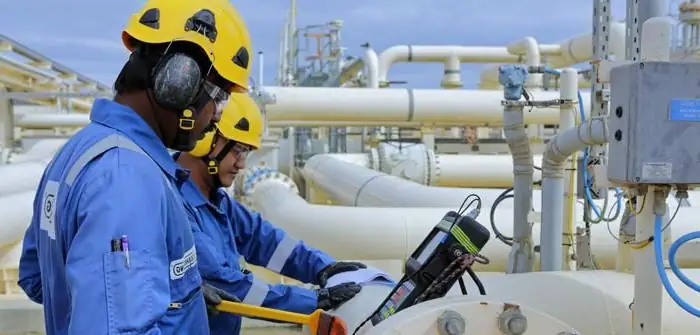
Pneumatic tests
Compressed air or inert gas is used for testing, which is taken from factory networks or from portable compressors. This option is preferred in cases where hydraulic tests are not possible for a number of reasons: lack of water, very low air temperature, and also when dangerous stresses can arise from the weight of water in the pipeline structure. The value of the ultimate test pressure depends on the pipeline size:
- with pipe diameter up to 200 mm - 20 kgf/m²;
- 200-500 mm - 12 kgf/m²;
- over 500 mm - 6 kgf/m².
If the pressure limit is different, special test instructions should be developed for such conditions.
Pneumatic test requirements
Pneumatic testing is prohibited for surface cast iron and glass structures. For all other materials from which process pipelines can be made, there are special test requirements:
- pipeline pressure rises gradually;
- inspection can be carried out when the pressure reaches 0.6 of the working value (it is unacceptable to increase it during work);
- leak test is done by smearing with soapy water, tapping with a hammer is prohibited.
The results of hydraulic and pneumatic tests are considered satisfactory if there was no pressure drop on the pressure gauge during the test.
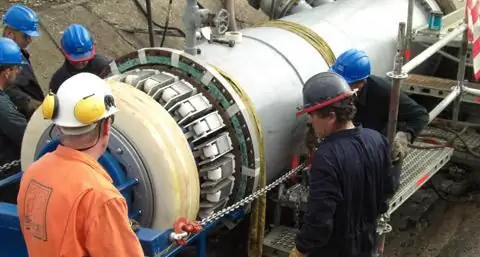
Transfer of pipelines to operation
At all stages of installation, relevant documents are drawn up, fixing the types of work, tolerances, tests, etc. They are transferred at the stage of delivery of pipelines as accompanying documentation, they include:
- acts of delivery of supporting structures;
- certificates for welding consumables;
- pipeline internal cleaning protocol;
- acts of quality control of welded joints;
- conclusion on testing valves;
- actsstrength and density tests;
- list of welders who made the connections and documents confirming their qualifications;
- diagrams of pipeline lines.
Technological pipelines are put into operation along with industrial plants, buildings and structures. Separately, only intershop systems can be rented.
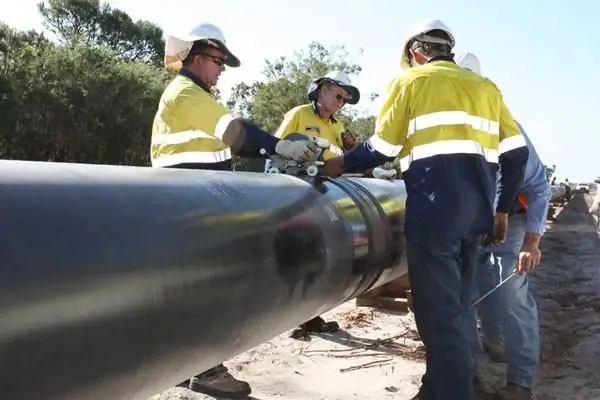
Recommendations for the operation of process pipelines
Periodic control should include the following operations:
- Checking the technical condition during external inspection and non-destructive methods.
- Checking areas subject to vibration with special devices that determine its frequency and amplitude.
- Troubleshooting issues that were fixed during previous checks.
No less important is the safe operation of process pipelines, which is ensured by compliance with all established rules.
Monthly system he alth check should cover the following:
- flange connections;
- welds;
- insulation and coating;
- drainage systems,
- support mounts.
If leaks are detected, for safety reasons, the operating pressure must be reduced to atmospheric pressure, and the temperature of the heating lines must be lowered to 60ºС to carry out the necessary troubleshooting measures. The results of the check should be recorded in special journals.
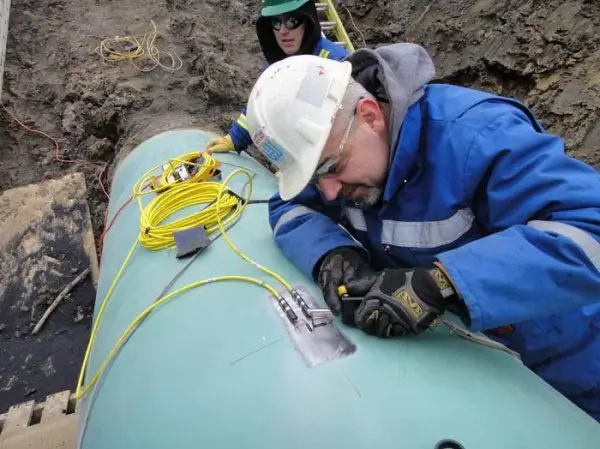
Revision
This control method is used to determine the condition and operational capability of pipelines. It is advisable to conduct an audit in areas where the operation of process pipelines is carried out in particularly difficult conditions. The latter include vibration, increased corrosion.
Revision of pipelines includes the following operations:
- Checking the thickness of the structure by non-destructive methods.
- Measuring areas prone to creep.
- Inspection of welded joints that are in doubt.
- Checking threaded connections.
- Status of support mounts.
The first revision control should be carried out after a quarter of the appointed time in the regulatory documents, but no later than 5 years after the launch of the facility. As a result of the timely conduct of all checks, the safe operation of process pipelines will be ensured.
Recommended:
Shelf life of water meters: period of service and operation, verification periods, operating rules and time of use of hot and cold water meters

The shelf life of water meters varies. It depends on its quality, the condition of the pipes, the connection to cold or hot water, the manufacturer. On average, manufacturers claim about 8-10 years of operation of devices. In this case, the owner is obliged to carry out their verification within the time limits established by law. We will tell you more about this and some other points in the article
Diamond boring machine: types, device, operating principle and operating conditions
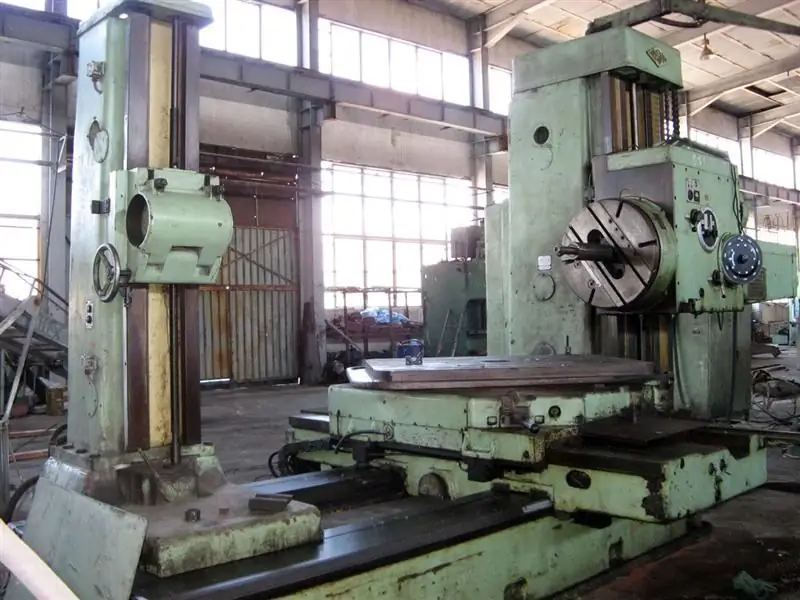
The combination of a complex cutting direction configuration and solid-state working equipment allows diamond boring equipment to perform extremely delicate and critical metalworking operations. Such units are trusted with the operations of creating shaped surfaces, hole correction, dressing of ends, etc. At the same time, the diamond boring machine is universal in terms of application possibilities in various fields. It is used not only in specialized industries, but also in private workshops
Duration of the operating cycle. What is an operating cycle?
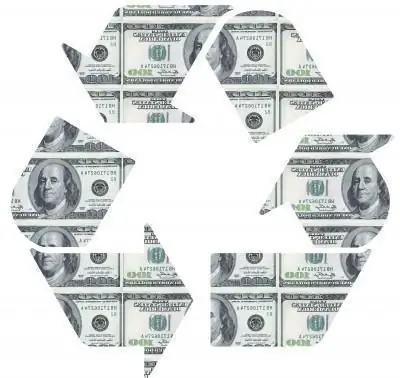
The company will not have problems with a lack of current assets if the management begins to strictly control the proportions between equity and debt capital, through which operations are financed
What is a technology project? Development of a technological project. Example of a technological project
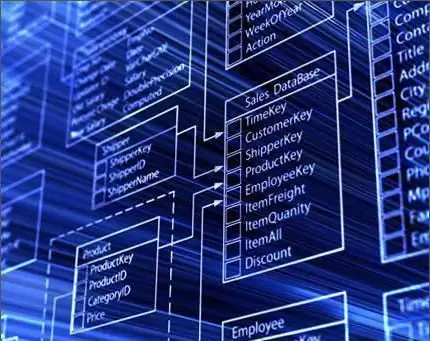
As part of the article, we will find out what a technological project is, and also work out the issues of its development
Categories of pipelines. Determining the pipeline category. Classification of pipelines by categories and groups
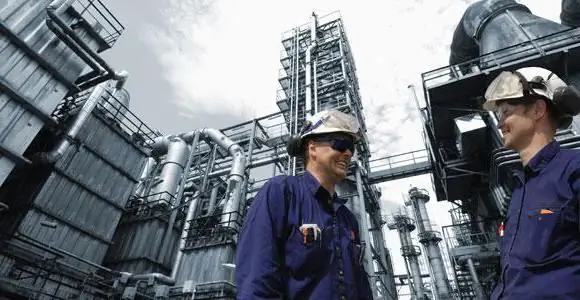
Modern industry cannot do without quality pipelines. There are many types of them. What are the categories of pipelines, how to determine them, is described in the article