2025 Author: Howard Calhoun | [email protected]. Last modified: 2025-01-24 13:10
In the construction industry and industry, there is a trend of transition from metal materials to high-strength plastics and modern composites. This is due to the fact that synthetic substitutes are close in characteristics to steel alloys, but at the same time they are free from the shortcomings of the metal, one of which is corrosion. At the same time, a complete rejection of traditional material is far from possible in all industries, therefore, the means to eliminate rust processes remain relevant. One of the most popular methods of this type is hot-dip galvanizing, which forms a durable and reliable protective layer on the surface of the product.
Zinc protection principle
After going through a series of preparatory procedures, the product or structure is applied with molten zinc. This is usually done by dipping the workpiece into a liquid mass in such a way that all the pores of the metal structure are filled. There are some nuances that must be taken into account before hot-dip galvanizing. The technology assumes that the high anodization of zinc in relation to the base metal will contribute to the independent penetration of zinc into the structure of the material already in the process.operation of the product. The filling rate of uncovered areas averages 2 mm per year.
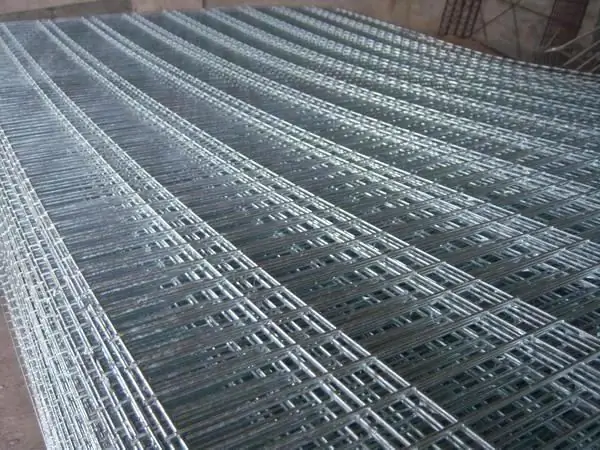
However, places with threads and nuts can later become sources of corrosion. You can prevent such processes with the help of the initial use of hardware with rust protection. This is especially important to take into account if hot-dip galvanizing of metal structures is carried out, the bolts in which carry a high power load.
Preparation for surgery
At the preparation stage, the main task is to clean the surfaces of the product and ensure potential homogeneity in the reactions of zinc and iron when immersed in a container with an active mass. This is achieved through several technological steps, including degreasing and washing. Further operations of etching and fluxing will follow. Degreasing is reduced to the removal of particles of dirt and oil - this will affect the efficiency of penetration of zinc into the metal structure.
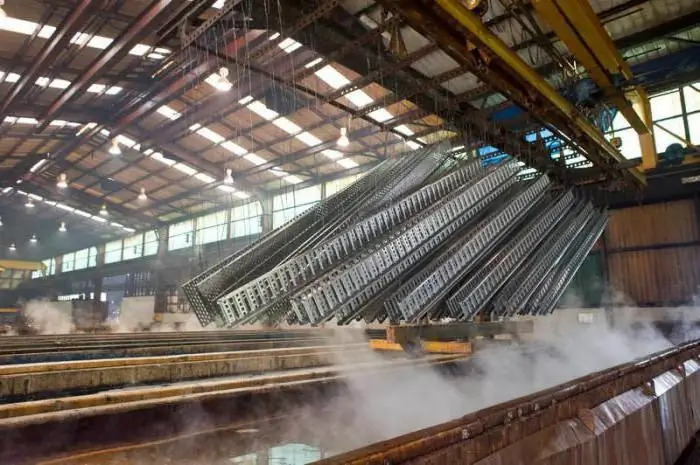
As a rule, this operation is carried out using degreasing reagents in order to obtain high-quality hot-dip galvanizing in the future. The flushing technology is implemented after degreasing. At this stage, it is important to remove all excess that was used to rid the surfaces of traces of oil. In particular, foam is eliminated from solutions and reagents that dissolve chemistry.
Etching the workpiece
This procedure can also be attributed to the stages of cleaning a metal surface. But if inIn previous cases, the material got rid of deposits of dirt and oil, but this time you will have to deal with the scale formed during heat treatment. In the etching process, hydrochloric acid is used, the chemical action of which makes it possible to obtain not only a clean, but also a shiny surface. Almost every hot dip galvanizing plant develops its own unique recipes for active media, which in different proportions may include the inclusion of inhibitors to eliminate hydroxyls and oxides. Compliance with clear proportions is necessary for the reason that, in addition to scale, such solutions also affect the structure of the base. Therefore, technologists strive to limit the excessive effect of chemistry on the metal, preventing the risks of hydrogen saturation.
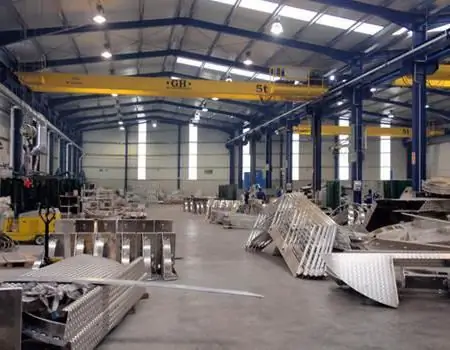
Fluxing
There are several tasks involved in the fluxing process. The main one is the completion of the preparation of the metal surface for the main galvanizing procedures. In particular, there is a dissolution of oxides, which can be re-formed during washing. In addition, fluxing provides material protection through a passivated film. This coating in some way begins the creation of a protective base, which will continue the hot-dip galvanizing of the metal, and in particular its internal structure. But if zinc protects the material from external influences during its use, then the passivated layer prevents oxidation during galvanizing, and at the same time increases the wettability of the molten mass.
Stagezinc plated
At this stage, the product is immersed in a bath containing molten zinc. The processes that are carried out at this stage will be represented by the destruction of the flux and the interaction of the structures of the two metals. The duration of the dive depends on the size of the structure. This usually takes 5 to 10 minutes. It is much more important to determine the optimal speed of immersion and extraction of the workpiece. For example, hot dip galvanizing at a slow dipping rate will help free the metal from the pre-passivated coating.
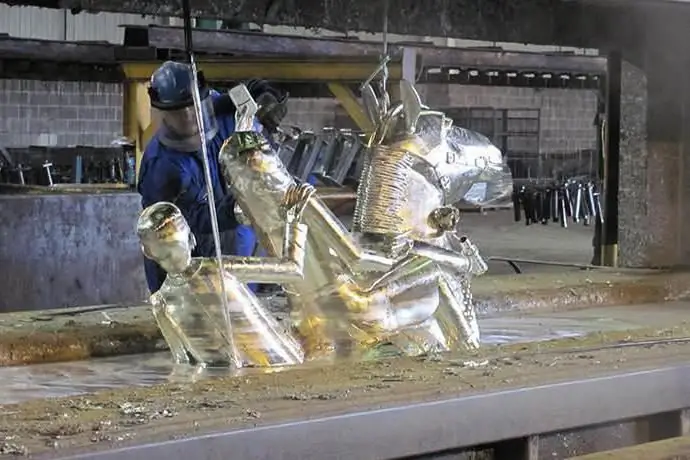
On the other hand, high speed leads to the capture of s alt residues on the surface, which inevitably reduces the quality of the result. The optimal speed is selected based on the size of the object, the duration of the dive and the characteristics of the surfaces.
Hot dip galvanizing quality control
Basically, the quality of the resulting product is judged by two characteristics: strength and coating thickness. To evaluate these parameters, specialists perform an analysis of threaded joints and welded assemblies, which are considered the most vulnerable areas from a technical point of view. As for checking the thickness, here one should rely on the requirements that GOST imposes. Hot-dip galvanizing in accordance with the standards must be carried out in such a way that the thickness in places remote from the knurling, corners and threads by 5 mm corresponds to the design ones. The specific values of the layer parameters are determined based on the requirements for a particular product, but the methodchecks should be carried out precisely on free sites.
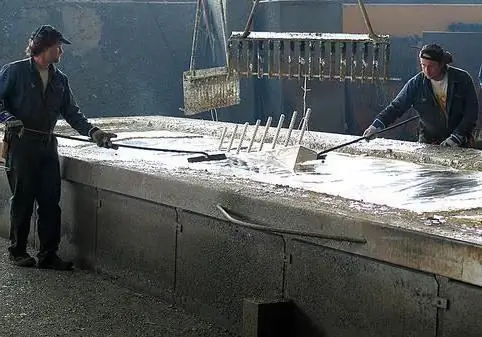
How much does hot dip galvanizing cost?
On average, the cost of hot-dip galvanizing is 30-35 thousand rubles. per 1 ton. At the same time, there are also deviations from this corridor when it comes to non-standard orders. Affects the price tag and the condition of the products. Often, enterprises offer a full service cycle, which involves multi-stage hot-dip galvanizing. The price of a full cycle, which will include preparatory operations, can reach 50 thousand. For this amount, as a rule, it is proposed to use high-quality reagents, dry the processed products in special chambers and confirm the quality of the work done with expert documentation.
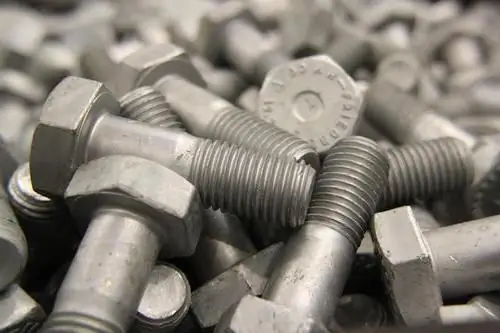
Advantages and disadvantages of the method
For large industries that work with large volumes of rolled metal, this method of corrosion protection is optimal primarily for economic reasons. In addition, the technology provides a reliable barrier against corrosion processes and at the same time does not reduce the thermal and electrical conductivity of the material. As for the disadvantages, hot-dip galvanizing of metal structures requires a high consumption of components for the active mass and careful organization of the overall processing process. The disadvantages of hot-dip galvanizing include the limitations of its use in relation to small parts - in this case it is simply impractical to apply a thin layer.
Conclusion
Metal protection technologygalvanizing has been used for quite a few years, and to this day there is no worthy alternative to it. The prevalence of the method is due to the fact that hot galvanizing qualitatively copes with the main task - preventing the formation of rust. This reliable method has proven itself both in industry and in construction.
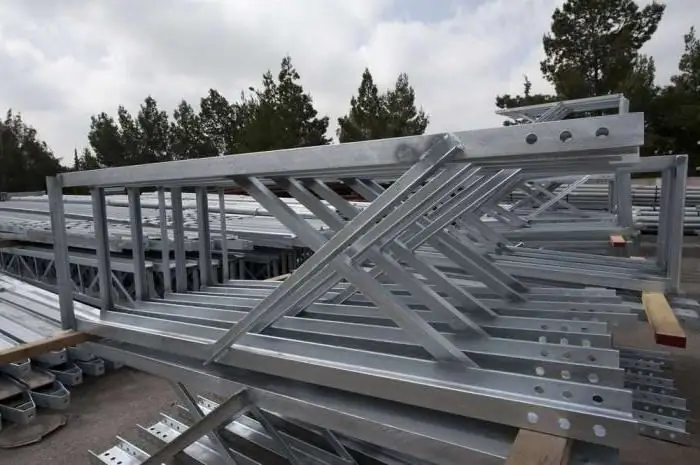
Where it is the issues of achieving the strength and durability of metal structures that come to the fore, zinc coating also pays off.
Recommended:
Product is.. Production of products. Finished products

The economy of every country is based on industrial enterprises that produce products or provide services. The number of products manufactured by an enterprise is an indicator for assessing the effectiveness of a company, industry, and even the entire national economy
Galvanic galvanizing of metal: technology, equipment
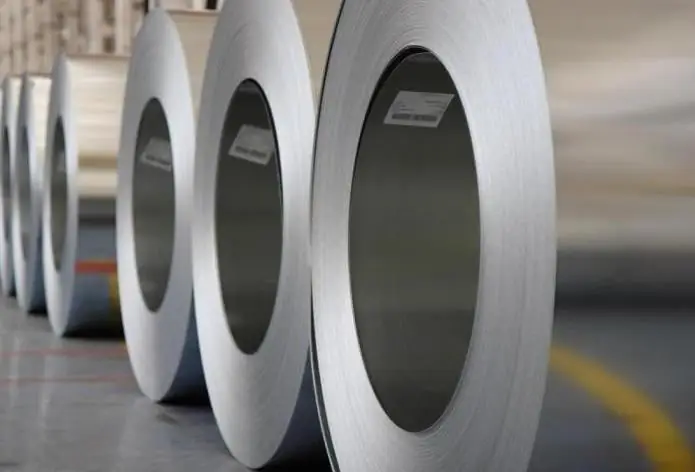
Galvanizing is effective and inexpensive, and therefore the most common way to protect ferrous metals from corrosion both in industry and at home
Material consumption of products characterizes manufacturability of products
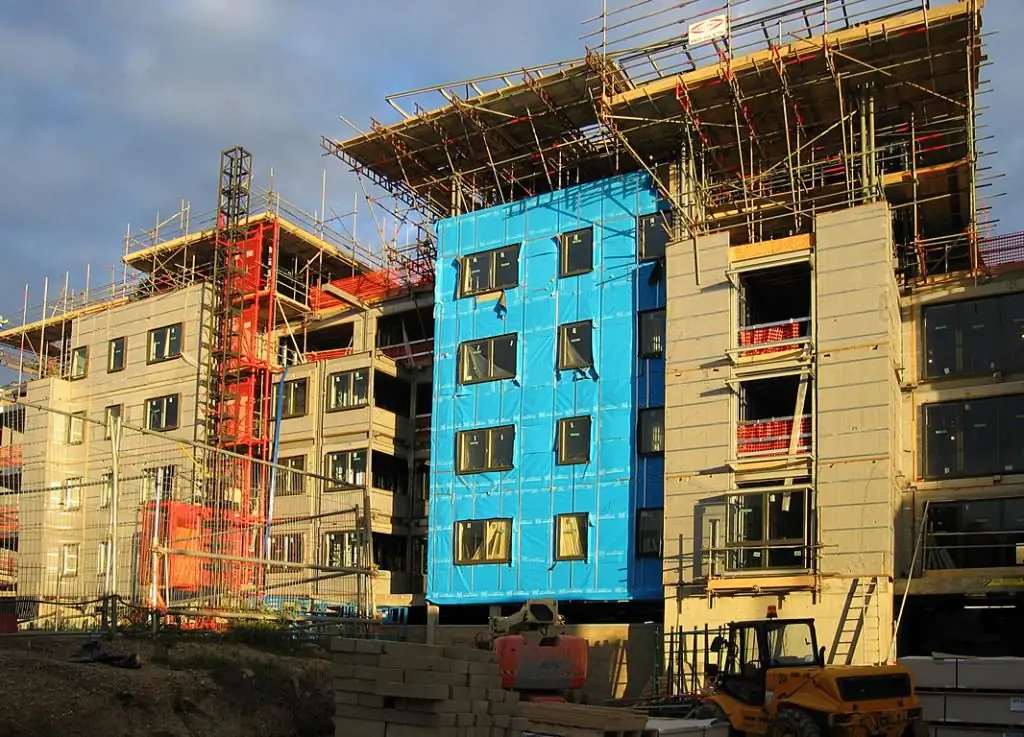
To analyze the perfection of the developed design, a number of technical and economic indicators are used, one of which is the material consumption of products. This parameter allows you to evaluate the level of manufacturability of the product and compliance with the required technical standards
Insurance products are The concept, process of creating and selling insurance products
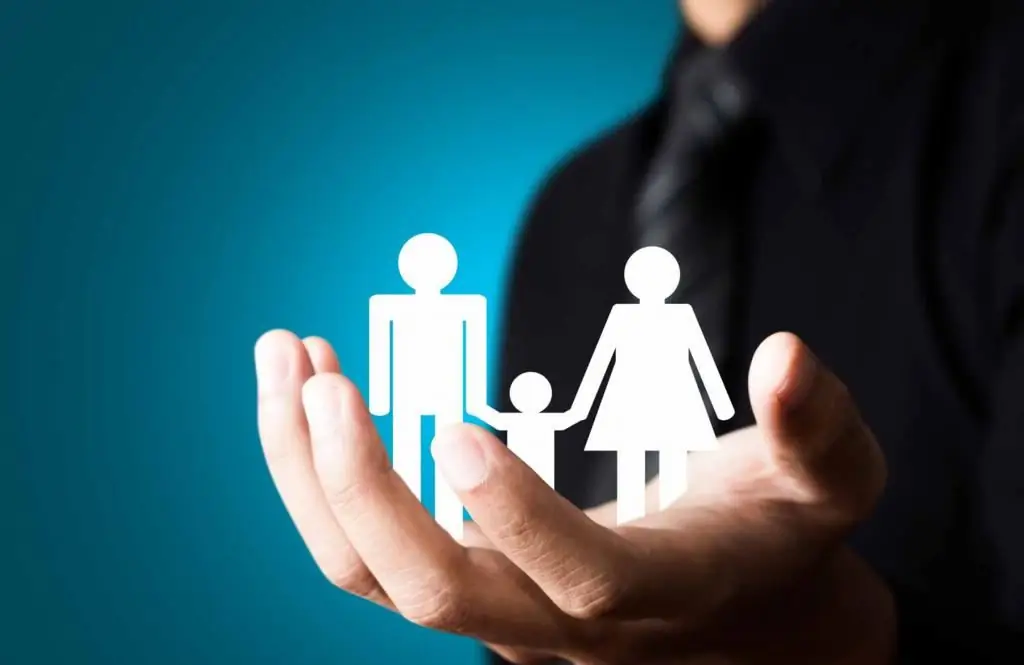
Insurance products are actions in the system of protecting various kinds of interests of individuals and legal entities for whom there is a threat, but it does not always happen. Evidence of the purchase of any insurance product is an insurance policy
Factory of bakery products "Dedovskiy Khleb": history, products, address
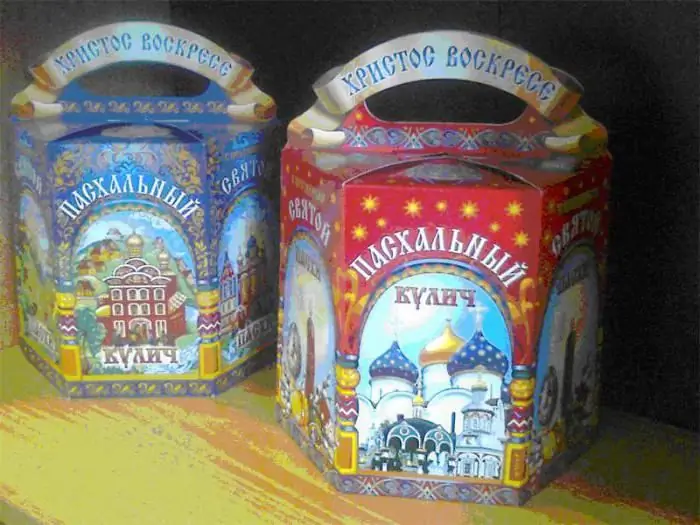
Dedovskiy Khleb bakery is known in the metropolitan area as a manufacturer of high quality bakery products. Loaves, "bricks", fragrant buns, Easter cakes, cakes, waffles are in constant demand among consumers. The key to success lies in the strict observance of GOSTs and technological standards laid down back in the 80s of the last century. Products are baked on modern equipment