2025 Author: Howard Calhoun | [email protected]. Last modified: 2025-01-24 13:10
Galvanizing is an effective and inexpensive, and therefore a common way to protect ferrous metals from corrosion. Most often it is used in the production of hardware and fasteners, as well as steel mesh.
Zinc Coating Methods
Anti-corrosion galvanizing is carried out in various ways, and the service life of the coating depends on the thickness of the protective layer.
The method of coating depends on its required properties, the size of the product, the conditions for its further operation.
The simplest and most technologically advanced, but insufficiently providing resistance to mechanical stress of the protective layer, is cold galvanizing using primers, which contain large amounts of highly dispersed zinc powder.
In terms of the volume of galvanizing production, hot-dip galvanizing occupies the second place. The coating obtained in this way is high-quality and durable, but environmentally unsafe, since zinc melt is used, and a large amount of electricity is needed to maintain its temperature a little less than 500 ° C, chemical methods of surface preparation.
Very similar to hot dip galvanizing moretechnological, but less productive method of thermal diffusion deposition of a protective layer. It is used when high demands are placed on the thickness and appearance of the coating.
Another method of galvanizing is gas-thermal spraying, which is used to protect large-sized products and structures that simply cannot be placed in a bath.
Galvanized galvanizing is devoid of many of the disadvantages of other coating methods and has its positive aspects.
Advantages of zinc plating
Zinc plating by electrolysis is the most common method.
The main advantage, due to which galvanic galvanizing of metal is used, is a high degree of protection of the surface of the material from corrosion. A thin layer of zinc increases the service life of products several times, and therefore reduces the cost of their maintenance and replacement.
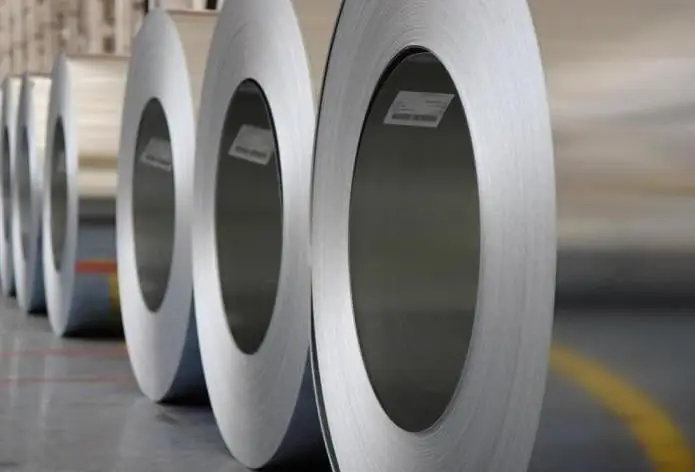
The coating is even, without streaks and drops, and the shape and size of the product is preserved. You can apply it to objects of any, even the most complex shape.
Smooth and shiny decorative coatings do not require additional processing in most cases.
In addition, the zinc coating process itself requires little expense, and the galvanizing units are highly productive.
Disadvantages of zinc plating
The method of applying a protective coating by electrolysis is not without drawbacks.
The main disadvantage islow adhesion of zinc to metal, due to which the surface of the product must be carefully cleaned.
The downside is also the formation of toxic waste during the coating process, requiring serious cleaning.
Failure to comply with the regimes can lead to hydrogen filling of the base metal, which leads to the fragility of the product itself and to a violation of the quality of the coating.
Operation principle
Galvanizing is based on the principle of protective effect, which is determined by the difference in the electrochemical potentials of zinc and iron. Since zinc has a lower electrochemical potential, its coating is a sacrificial protection for ferrous metals. That is, in a humid environment, it is he who undergoes electrochemical corrosion.
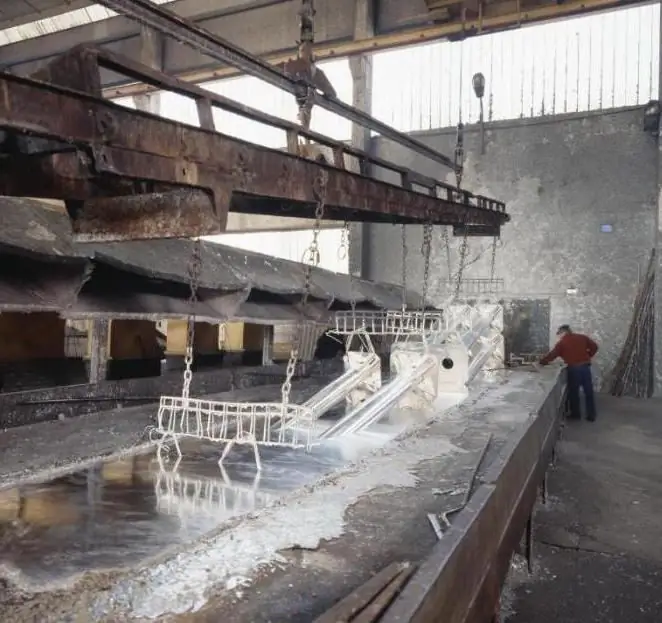
When iron is oxidized, oxides are formed that have a larger volume than the original metal. The oxide film becomes loose and passes oxygen to the still unoxidized metal. And on zinc, during oxidation, the film forms thin and dense, it does not let oxygen deep into the metal, protecting not only the coating, but also the base metal underneath.
Types of zinc plating
Galvanic galvanizing is a technology that is electrolysis, i.e. electrochemical redox processes in an electrolyte under the action of a direct electric current.
According to the composition of the electrolyte, zinc plating is divided into three types: acid, cyanide and alkaline.
The most commonly used zinc coating method in slightly acidicelectrolytes, especially for cast iron and steel parts of complex configuration. Products made of carbon and alloy steels with this type of galvanizing are less subject to the occurrence of hydrogen embrittlement, and the appearance is excellent, with a wonderful decorative effect in a wide range of colors.
Additional galvanizing protection
The protective effect of zinc coatings depends on its thickness, which is only 5 microns when electroplated, and the nature of the electrolyte.
In some cases, the protective properties of zinc coatings are enhanced by passivation, phosphating or painting.
Passivation (chromating) - chemical treatment of products in solutions with chromic acid or its s alts, as a result of which chromate films are formed on the surface. This process enhances not so much the protective properties as the decorative ones, because as a result the gloss of the coating is enhanced, and it can be painted in various colors.
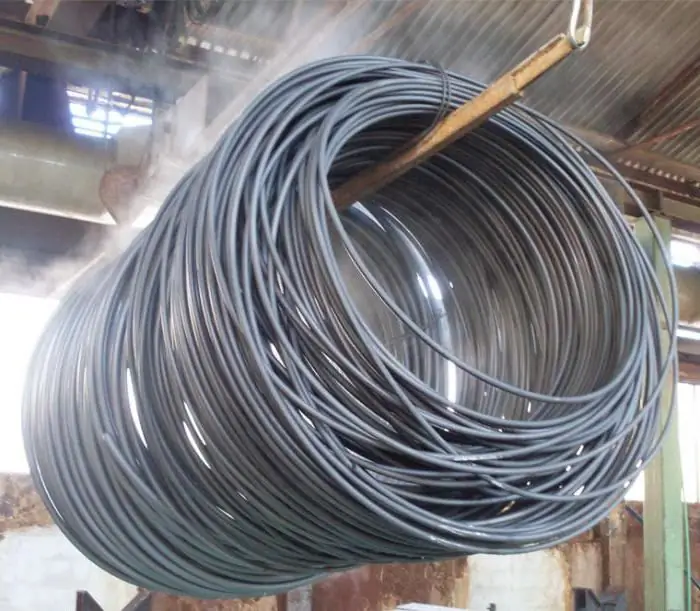
When phosphating (treatment in phosphoric acid s alts) of galvanized products, a phosphate film is formed on the surface. After phosphating, paint can still be applied.
Stages of zinc plating
In production, galvanizing consists of several technological processes, each of which is completed by washing with water in a flowing bath or a brush-washing method.
First, the products are thoroughly cleaned of rust, scale, process grease, coolant residuesliquids or paints and degreased in alkaline solutions. Then electrolytic degreasing takes place.
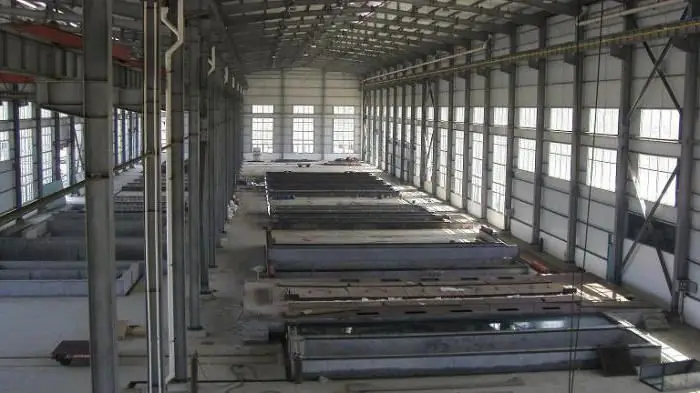
After it, they are pickled in an aqueous solution of hydrochloric acid, in which the surface is finally cleaned without disturbing the surface layer and it is decapitated - activated before applying the zinc coating. Only then is the actual galvanizing.
After it, if necessary, the products are clarified and cleaned of the oxide film in an aqueous solution of nitric acid, then phosphated, passivated and dried.
When galvanizing various products, additional operations may be performed. For example, a strip is unwound before galvanizing, the ends are welded, straightened, and after it they are oiled and wound up.
Equipment for zinc plating
A galvanizing line is a specific sequence of rinsing and technological baths in which a single or multi-layer zinc coating with the required functional properties is created.
In accordance with production volumes, equipment with varying degrees of mechanization is used. At large enterprises, mechanized lines with automatic control are installed. There are lines with partial or full manual control, as well as mini-lines.
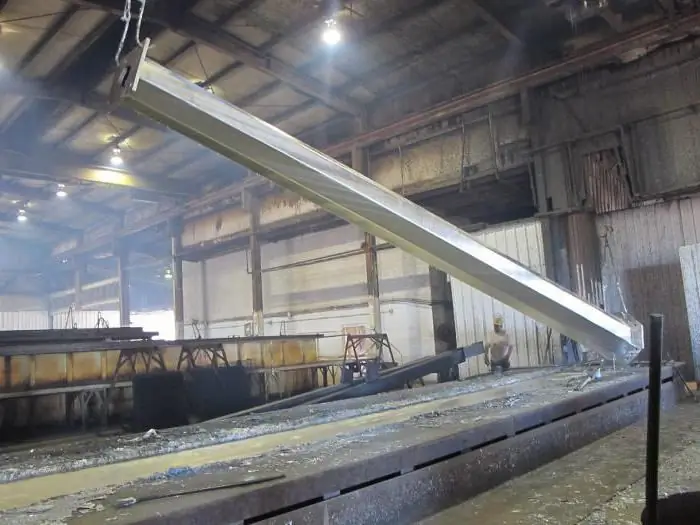
The galvanizing line consists of more than just baths. It includes transport systems of various designs, equipment for wastewater treatment,auxiliary equipment, which includes devices for galvanizing, heating elements, heat exchangers, cathode and anode rods.
Additional equipment includes ventilation systems, drying chambers and cabinets, refrigeration equipment, filtering units, demi-water production equipment, pumps.
Electrolytes for zinc plating
For galvanic galvanizing, depending on the purpose of the product, electrolytes are used, which are divided into two main groups.
Electrolytes, in which zinc is in the form of simple hydrated ions, are called simple acidic. These are hydroboric, sulfate and chloride solutions.
Complex complex acidic and alkaline electrolytes contain zinc in complex ions with a positive and negative charge. These are ammonia, pyrophosphate, cyanide and other solutions.
The type of electrolyte used primarily determines the rate of deposition and then the quality of zinc deposits on the product (cathode).
From complex electrolytes, zinc settles on the cathode with high ion scattering. As the current density increases, the yield of metal decreases and the yield of hydrogen increases.
Therefore, zinc plating in complex electrolytes is carried out at a low current density, and the coating is very high quality, fine-grained and uniform.
In slightly acidic simple electrolytes, galvanizing, including at home, takes place at a high current density, with a higher speed than when using complex solutions. The appearance of the products is good, butthe coating is not of very high quality and is only suitable for products of a fairly simple shape.
Galvanized zinc plating
Technological process of direct galvanizing takes place in a bath with electrolyte. Products made of ferrous metal are lowered into it, to which an electric current (cathode) is supplied through special electrodes, and pure zinc in the form of balls or plates laid in special mesh sections (anode).
During an electrochemical reaction, under the influence of an electric current with a density of 1 to 5 A/dm, zinc dissolves in the electrolyte, then its ions settle on the cathode, forming a 4-25 micron thick galvanic coating.
It is with the use of this technology that fasteners (bolts and nuts) are obtained with a uniform and shiny coating.
Automated Galvanizing Line
The modern galvanizing line is a fully automated line, which performs all stages of coating, including welding and high-quality degreasing of products for various purposes and configurations.
The automatic line generally consists of a set of technological electroplating baths, modular rectifiers, a loading / unloading stand, transport equipment, equipment for exhaust ventilation, water supply and sewage disposal, a metal frame with a service ladder.
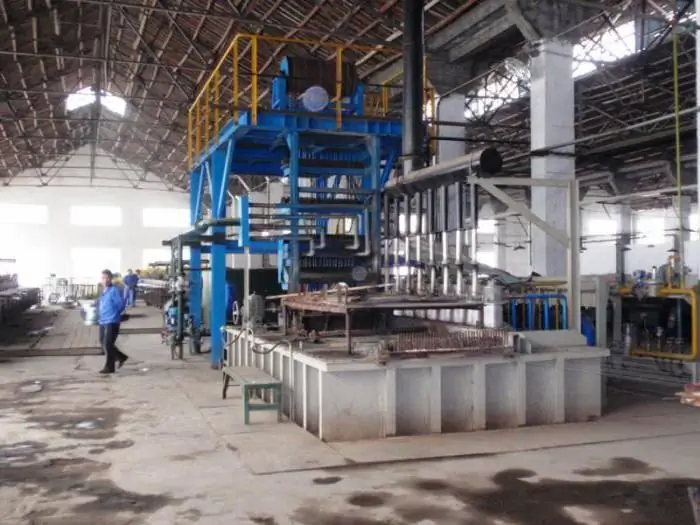
Electroplating baths can be made of stainless steel, plastic lined steel or rubber. Modern baths, welded from sheet polymers, are increasingly replacing metal containers. The choice of bath material depends on the composition and concentration of the electrolyte and the operating temperature.
Communications of water supply and sewerage systems, and in most cases ventilation are located under the baths and are also made of polypropylene.
The dimensions of the line are determined by its productivity and the dimensions of the electroplating baths.
Galvanic galvanizing occurs with the formation of wastewater with a high concentration of heavy metal ions. Therefore, they are defended, filtered, neutralized, chemical precipitation, sorption and other processes are used in containers made of engineering polymers.
Electrolytic zinc plating at home
Galvanic galvanizing, produced by one's own hands, begins with the selection of materials. The electrolyte can be a solution of zinc chloride and hydrochloric acid in distilled water. This is the so-called soldering acid, which is most often used at home. Craftsmen pickle zinc in battery sulfuric acid and get electrolyte ZnSO4, but this process is dangerous, because explosive hydrogen and heat are released during the reaction. In no case should there be a precipitate of undissolved s alt crystals in the electrolyte.
Pure zinc can be bought at a chemical store or radio market, or can be obtained from s alt batteries or fuses from the Soviet Union.
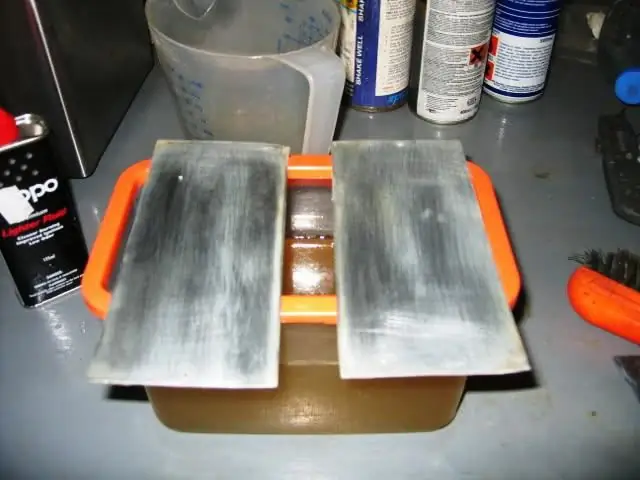
Galvanicthe bath can be a glass or plastic container. Stands for the anode and cathode are installed in it. The anode is a zinc plate to which the "plus" is connected from the power source. The larger the anode, the more uniform the coating will be on the cathode, the product on which the protective coating will be applied. There can be several anodes, they can be placed around the cathode at the same distance so that its surface is covered with zinc evenly and simultaneously from all sides. The “minus” of the power source is connected to the cathode.
Even when galvanizing is done at home, the technology necessarily includes thorough cleaning and degreasing of the part, as well as its activation in an acid solution.
The power source is a car battery with a low power incandescent lamp or another consumer in the circuit so that the current in the circuit is lower, or a power supply with a constant output voltage. The main thing is that there should be no rapid boiling of the electrolyte during the galvanizing process.
Actually, galvanizing occurs when the anodes and cathode are lowered into the electrolyte and the electrical circuit is closed. The longer the process takes, the thicker the zinc layer is on the product.
With the help of galvanizing, the protective coating on products becomes precise, uniform and smooth, with a decorative effect. It is used both in industry and at home, despite the fact that wastewater treatment from environmentally hazardous waste is required.
Recommended:
How to open a cheese factory: where to start, equipment, technology, paperwork
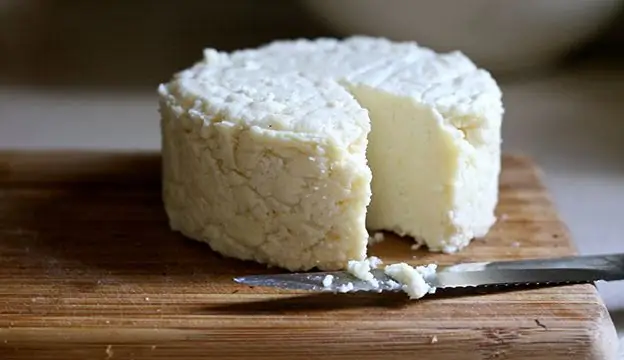
Cheese is a popular product on the Russian market: on average, a Russian consumes 6.4 kg of cheese per year. Until now, since the introduction of sanctions, this segment of the market has not been completely filled. That is, the demand for some varieties remains unsatisfied. This pushes people to open their own cheese factory. The article will tell you how to do this
Plastic processing: technology, equipment
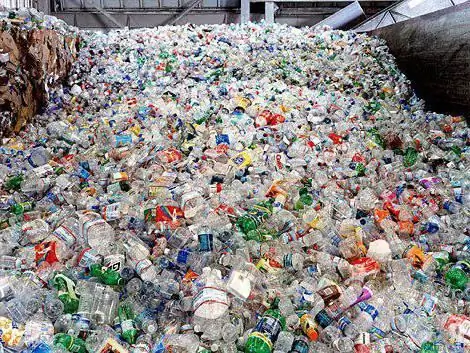
Plastic materials over the past 10-15 years have formed a wide range of applications in which their products can be used. The synthetic material itself is currently undergoing a period of radical technological changes, as a result of which the market for building materials is filled with new proposals. Suffice it to mention the families of composites that displace both metals and wood
Oxyfuel cutting of metal: technology, necessary equipment, safety precautions
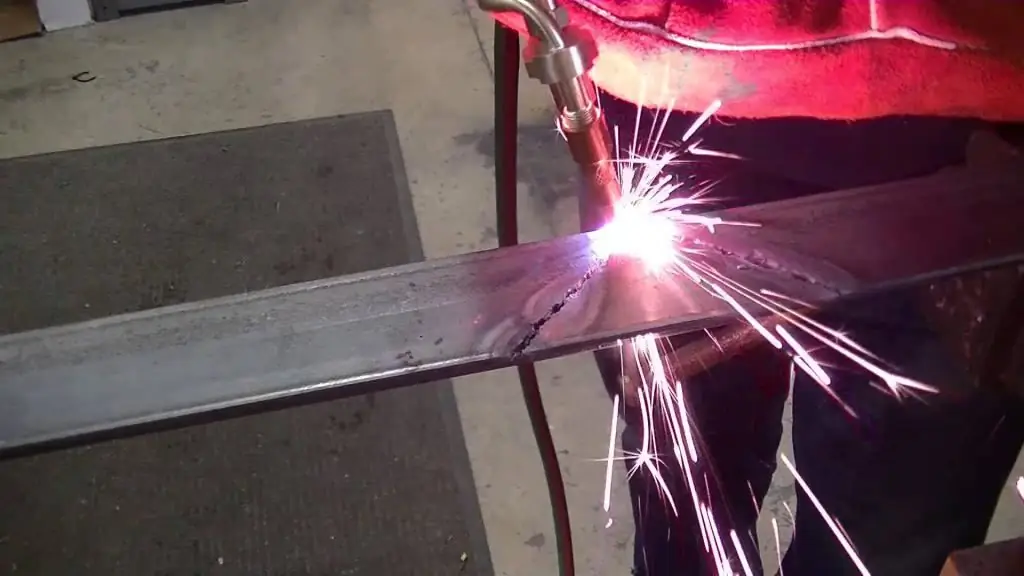
Oxy-fuel cutting of metals (in the literature you can find the term "oxy-fuel cutting") is actively used in industry for cutting sheet material from steel and other alloys into workpieces of the required length. The article contains information about the technology itself, about the necessary equipment and basic safety precautions for oxygen cutting of metals and other materials
Hot galvanizing. The process of galvanizing metal products
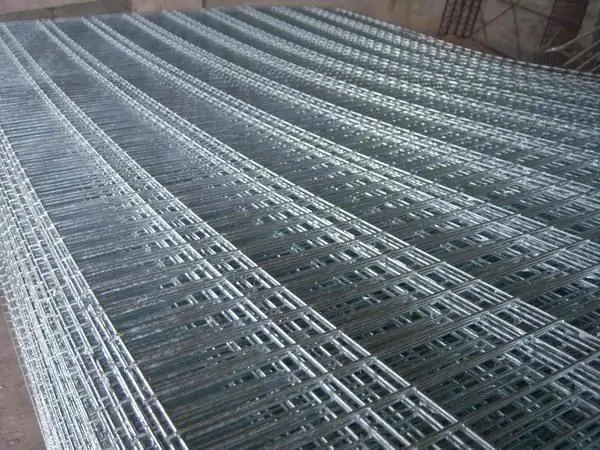
The article is devoted to hot-dip galvanizing technology. Its features, technological stages, pros and cons, cost, etc. are considered
Sheet metal processing: technology and equipment
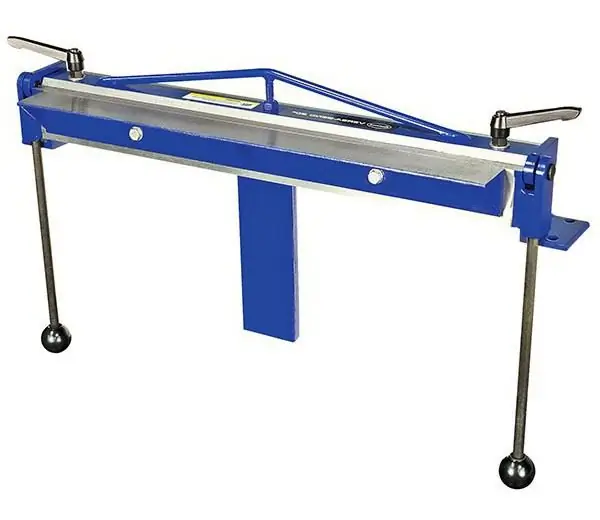
Today, sheet metal is one of the most sought-after materials. Sheet metal processing is a process that allows you to change the characteristics of raw materials and bring them to the desired values. In addition, there are many ways to process