2025 Author: Howard Calhoun | [email protected]. Last modified: 2025-01-24 13:10
The process of operation of technical units, machines and individual elemental groups of equipment is inevitably accompanied by wear. The mutual mechanical impact of parts on each other with varying degrees of intensity leads to abrasion of their surfaces and destruction of the internal structure. In addition, the environment often has a similar effect in the form of erosion and cavitation. As a result, there is a loss of equipment performance or at least a decrease in operational properties. The following reviews of powdered friction and anti-friction materials will help you understand ways to minimize unwanted friction. Such materials are recommended for use in industrial equipment and household appliances, as well as for construction tools.
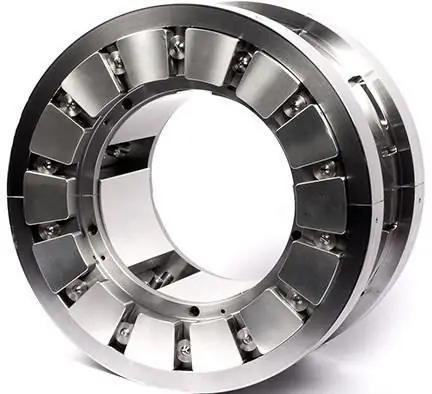
Differences between friction and anti-friction materials
Consideration of these materials in one context is due to the fact that their function is related to the general characteristic of the operation of mechanisms - the coefficient of friction. But if antifriction elements and additives are responsible for lowering this value, then friction elements, on the contrary, increase it. In this case, for example, powder alloys with increasedcoefficient of friction provide wear resistance and mechanical strength of the target working group. To achieve such qualities, refractory oxides, boron, silicon carbides, etc. are introduced into the composition of friction raw materials. Unlike antifriction elements, friction elements often represent full-fledged functional organs in mechanisms. This, in particular, can be brakes and clutches.
Providing the task of increasing friction, they simultaneously perform specific technical tasks. At the same time, both friction and anti-friction materials undergo rigorous laboratory testing before use. The same alloys for brakes undergo full-scale and bench tests, during which the expediency of their application in practice is determined. The most technologically advanced friction materials from polymers are today manufactured by various methods. So, for the mechanisms of the brake group, the pressing technique is used - blocks, plates and sectors are made on the forms. Tape materials are produced using a woven technique, and overlays are produced by rolling.
Properties of antifriction materials
Parts with an anti-friction function must meet a wide range of requirements that determine their basic performance. First of all, the material must be compatible with both the mating part and the working environment. Under conditions of compatibility before and after running in, the material provides the required degree of friction reduction. Here it is necessary to note the running-in as such. This property defines the element's ability to naturally adjust the surface geometry.under the optimal shape, which is suitable for a particular place of operation. In other words, an extra structure with microroughnesses is erased from the part, after which the running-in will provide working conditions with minimal loads.
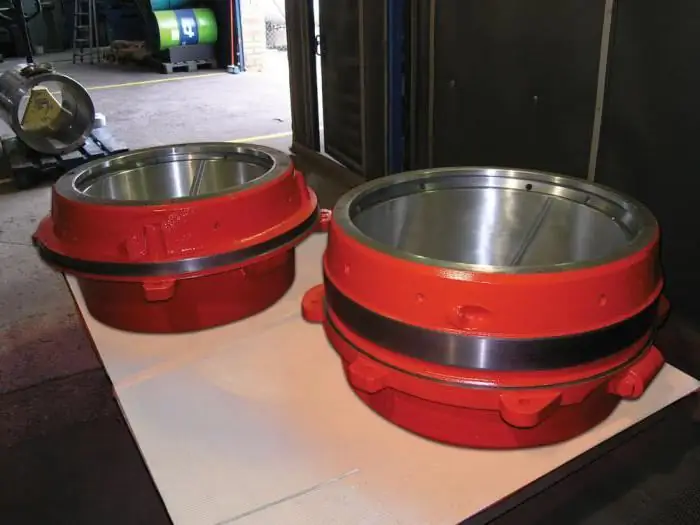
Wear resistance is also an important property possessed by these materials. Anti-friction elements must have a structure that provides resistance to various types of wear. At the same time, the part must not be excessively rigid and hard, as this will increase the risk of seizing, which is undesirable for anti-friction material. Moreover, technologists single out such a property as the absorption of solid particles. The fact is that friction to varying degrees can contribute to the release of small elements - often metal. In turn, the anti-friction surface has the ability to “press” such particles into itself, eliminating them from the working area.
Metal anti-friction materials
Products on a metal basis make up the most extensive range of elements of the antifriction group. Most of them are focused on operation in the fluid friction mode, that is, under conditions when the bearings are separated from the shafts by a thin oil layer. And yet, when the unit is stopped and started, the so-called boundary friction mode inevitably occurs, in which the oil film can be destroyed under the influence of high temperatures. Metal parts used in bearing groups can be divided into two types: elements with softstructure and solid inserts and alloys with a rigid base and soft inserts. If we talk about the first group, then babbits, brass and bronze alloys can be used as antifriction materials. Due to their soft structure, they run in quickly and retain their oil film characteristics for a long time. On the other hand, solid inclusions cause increased wear resistance in mechanical contacts with adjacent elements - for example, with the same shaft.
Babbits are an alloy, the basis of which is formed by lead or tin. Also, in order to improve individual qualities, alloying alloys can be added to the structure. Among the improved properties, corrosion resistance, hardness, toughness and strength can be noted. The change in one or another characteristic is determined by what alloying materials were used. Anti-friction babbits can be modified with cadmium, nickel, copper, antimony, etc. For example, a standard babbit contains about 80% tin or lead, 10% antimony, and the rest is copper and cadmium.
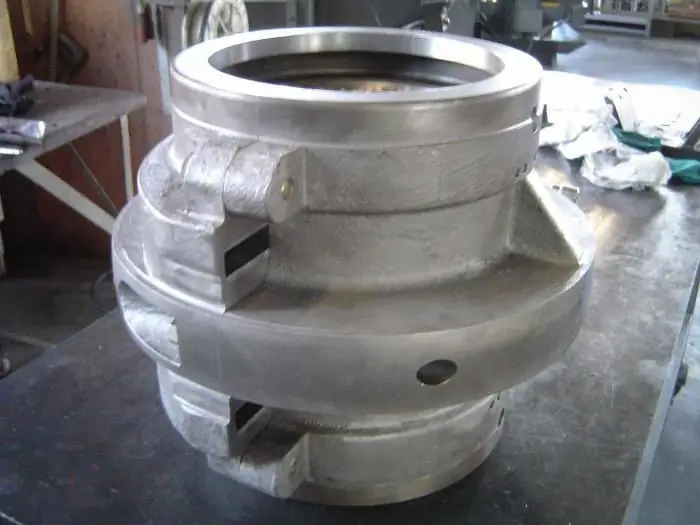
Lead alloys as a means of minimizing friction
The entry level of anti-friction alloys are lead babbits. Affordability determines the specifics of the operation of this material - in the least critical work functions. The lead base, in comparison with tin, provides babbits with less high mechanical resistance and low corrosion protection. True, even in such alloys it cannot do without tin - its content canreach 18%. In addition, a copper component is also added to the composition, which prevents segregation processes - an uneven distribution of metals of different masses in the volume of the product.
The simplest lead materials with antifriction properties are characterized by a high degree of brittleness, so they are used in conditions with reduced dynamic loads. In particular, bearings for track machines, diesel locomotives and heavy engineering components are a target niche where such materials are used. Anti-friction alloys using calcium can be called a modification of lead alloys. In this case, such qualities as high density and low thermal conductivity are noted. The basis is also lead, but in significant proportions it is also supplemented by inclusions of sodium, calcium and antimony. As for the weak points of this material, they include oxidizability, therefore, it is not recommended to use it in chemically active environments.
Speaking in general about babbits, we can state that this is far from the most effective solution for minimizing friction, but in terms of its combination of qualities, it turns out to be beneficial from the point of view of operation. These are materials whose antifriction properties can be leveled by reduced fatigue resistance, which worsens the performance of the element. However, in some cases, the lack of strength is compensated by the inclusion of steel or cast iron hulls in the design.
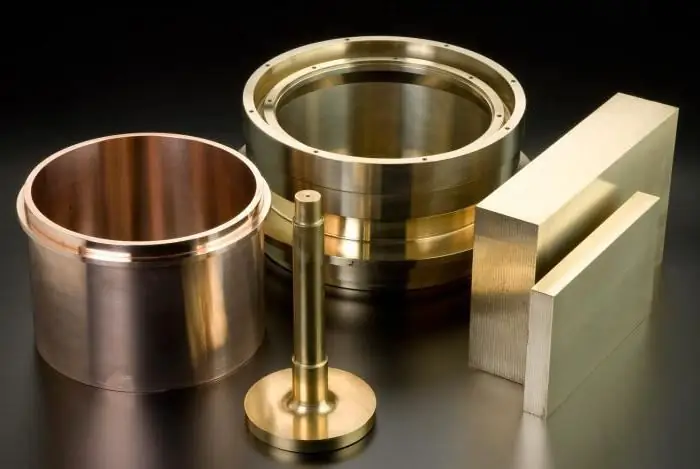
Features of bronze anti-friction alloys
Physical and chemical properties of bronzeare organically combined with the requirements for anti-friction alloys. This metal, in particular, provides sufficient indicators of specific pressure, the ability to operate under shock loads, high bearing rotation speed, etc. But also the choice of bronze for certain functions will depend on its brand. The same format for the operation of liners under shock loads is acceptable for the BrOS30 brand, but is not recommended for BrAZh. There are also differences in the class of bronze materials in terms of mechanical properties. This group of qualities will depend on the nature of the interface with hardened shafts and on the use of a trunnion, which may have additional hardening. And again, it is impossible to talk about the solidity of the alloy structure.
Bronze items may also include tin, brass, lead. At the same time, if all of the listed metals can be used as the basis of babbitt, copper-based anti-friction materials are used extremely rarely. In this case, the copper component often acts as the same additive with a content ratio of 2-3%. Tin-lead combinations of inclusions are considered optimal. They provide sufficient performance of the alloy as an antifriction component, although they lose to other compositions in terms of mechanical strength. Combined bronze materials are used in the manufacture of solid bearings for electric motors, turbines, compressor units and other units that operate at high pressure and low sliding speed.
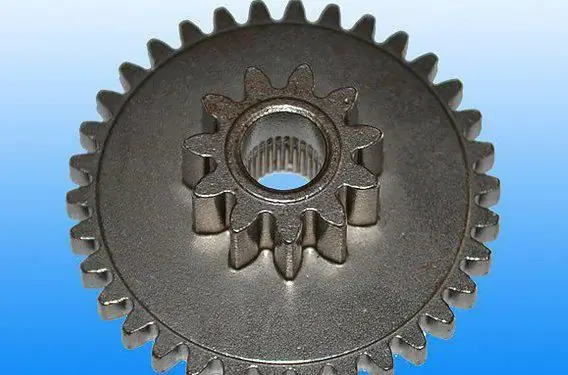
Powderfriction materials
Such materials are used in compositions intended for transmission and brake units of caterpillar vehicles, automobiles, machine tools, building mechanisms, etc. Finished products based on powder components are produced in the form of sector linings, discs and pads. At the same time, the starting materials for the antifriction type of powder alloys are formed by the same nomenclature as in the case of friction components - iron and copper are most often used, but other combinations exist.
For example, materials made of aluminum and tin bronzes, which include graphite and lead, effectively manifest themselves in friction conditions at a sliding speed of parts of the order of 50 m/s. By the way, when bearings operate at a speed of 5 m/s, metal powder products can be replaced by metal-plastic raw materials. This is already an anti-friction composite material with a flexible working structure and reduced strength. The most advantageous in terms of use in conditions of increased loads are materials made of iron and copper. Graphite, silicon oxide or barium are used as additives. The operation of these elements is possible at a pressure of 300 MPa and a sliding speed of up to 60 m/s.
Powder antifriction materials
Anti-friction products are also produced from powder raw materials. They are characterized by high wear resistance, low coefficient of friction and the ability to quickly run in to the shaft. Also, anti-friction powder materials have a number of advantages compared to friction-minimizing alloys. Suffice it to say that their wear resistance is on average higher than that of the same babbits. The porous structure formed by the powdered metals allows effective impregnation with lubricants.
Manufacturers have the opportunity to form end products in different forms. These can be frame or matrix parts with intermediate cavities filled with other softened raw materials. And, on the contrary, in some areas, antifriction powder materials with a soft frame base are more in demand. In special honeycombs, solid inclusions of different levels of dispersion are provided. This quality is of great importance precisely from the point of view of the possibility of regulating the parameters that determine the intensity of friction of parts.
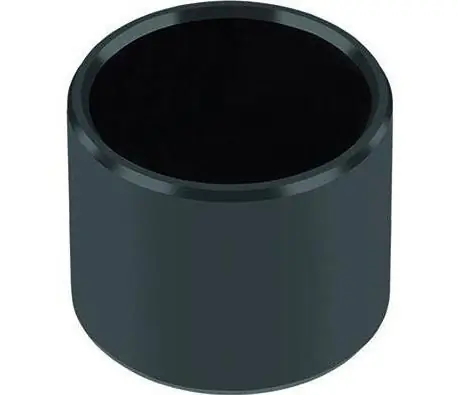
Anti-friction polymer materials
Modern polymer raw materials make it possible to obtain new technical and operational qualities for parts that reduce friction. Both composite alloys and metal-plastic powders can be used as a basis. One of the main distinguishing properties of such materials is the ability to evenly distribute additives throughout the structure, which will later perform the function of a solid lubricant. Graphites, sulfides, plastics and other compounds are noted in the list of such substances. The working properties of polymeric and antifriction materials largely converge at the basic level without the use of modifiers: this is a low coefficient of friction, and resistance to chemically active media, andpossibility of operation in the aquatic environment. Speaking of unique qualities, polymers can perform their tasks even without reinforcement with a special lubricant.
Application of anti-friction materials
Most of the anti-friction elements are initially designed for use in bearing groups. Among them are parts designed to increase wear resistance, and components that improve sliding. In mechanical engineering and machine tool building, such products are used in the manufacture of engines, pistons, coupling units, turbines, etc. Here, the basis of consumables is antifriction materials of plain bearings, which are introduced into the structure of running and stationary equipment.
The construction industry also cannot do without an anti-friction function. With the help of such parts, engineering structures, mounting structures and masonry materials are strengthened. In the construction of railways, they are used in the installation of structural elements of rolling stock. The use of polymer-based anti-friction materials is also widespread, which find their place, for example, as a connecting structure of pulleys, gears, belt drives, etc.
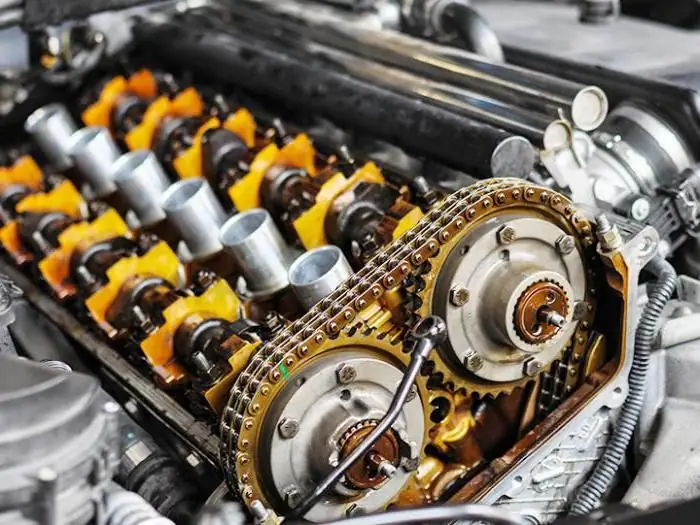
Conclusion
The task of reducing friction only at first glance may seem secondary and often optional. The improvement of lubricating fluids really makes it possible to get rid of some mechanisms from auxiliary technical elements that reduce the wear of the main working group. A transitional link from the classicalbabbitt to a modified high-performance lubricant can be called anti-friction polymer materials, which are characterized by a softer structure and versatility in terms of working conditions. However, the operation of metal parts under high pressure and physical impact still requires the inclusion of solid state anti-friction liners. Moreover, this class of materials not only does not become a thing of the past, but also develops by improving the characteristics of strength, hardness and mechanical stability.
Recommended:
Protective materials: types, properties and applications
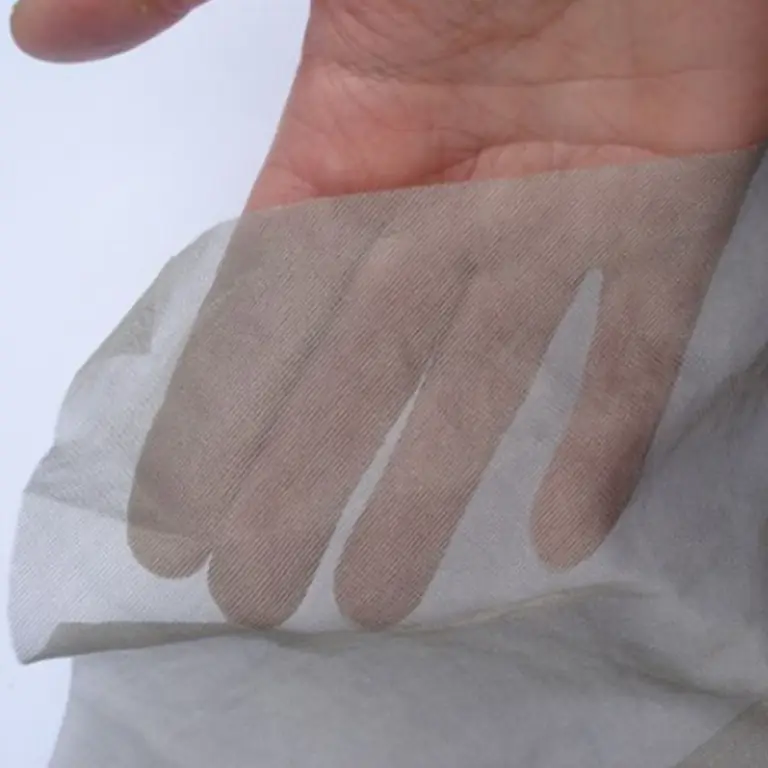
Today, people actively use a wide variety of devices, devices, etc. All this is made of parts that sooner or later become unusable, due to which the equipment stops working normally. To delay this moment as much as possible, protective materials are used
Electrical materials, their properties and applications
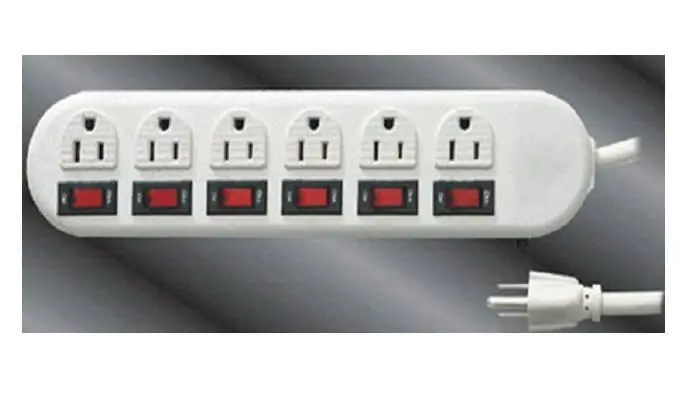
Efficient and durable operation of electrical machines and installations directly depends on the state of insulation, for which electrical materials are used. They are characterized by a set of certain properties when placed in an electromagnetic field, and are installed in devices taking into account these indicators
Materials released to production (posting). Accounting for the disposal of materials. accounting entries
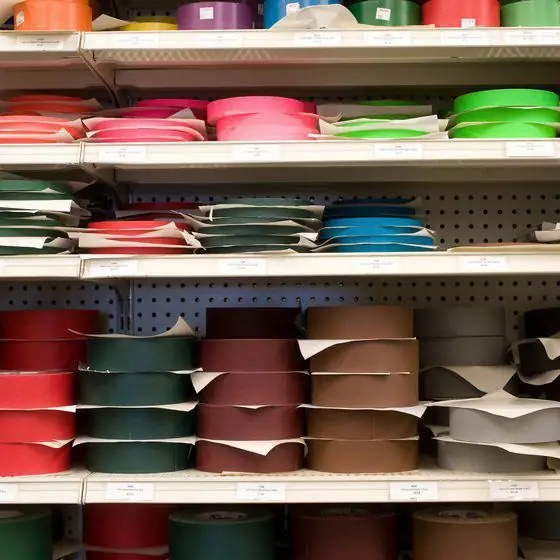
Most of all existing enterprises can not do without inventories used to produce products, provide services or perform work. Since inventories are the most liquid assets of the enterprise, their correct accounting is extremely important
Anti-aircraft missile system. Anti-aircraft missile system "Igla". Anti-aircraft missile system "Osa"
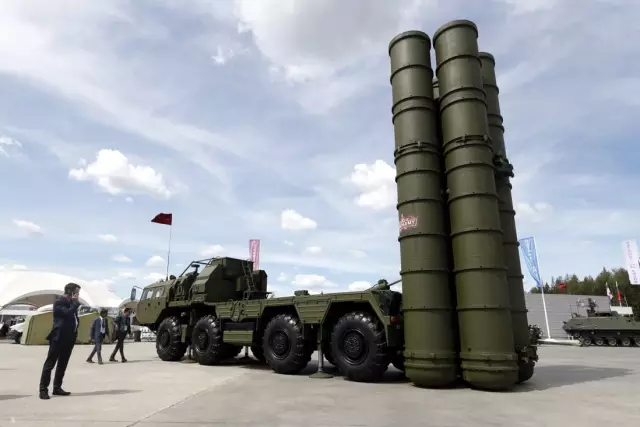
The need to create specialized anti-aircraft missile systems was ripe during the Second World War, but scientists and gunsmiths from different countries began to approach the issue in detail only in the 50s. The fact is that until then there simply were no means of controlling interceptor missiles
What is fabric made of? Classification of fabrics by type of raw materials, properties and purpose
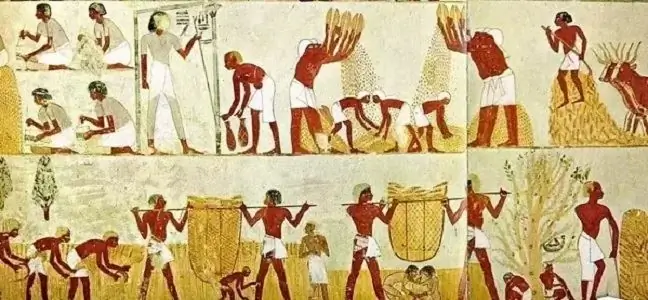
Using fabric in everyday life, one does not even have thoughts about how significant this invention was for mankind. But without fabrics, life would be uncomfortable and unthinkable! A person is surrounded by tissues in all his life activities. When did the first fabric appear, and what is it currently made of? Let's talk about it in the article