2025 Author: Howard Calhoun | [email protected]. Last modified: 2025-01-24 13:10
From primary production to direct use, gas mixtures go through several technological stages. To optimize transportation and intermediate storage between these processes, the raw material is subjected to compressor compression. Technically, similar tasks are implemented by gas compressor units (GPU) at different nodes of backbone networks.
Design and equipment design
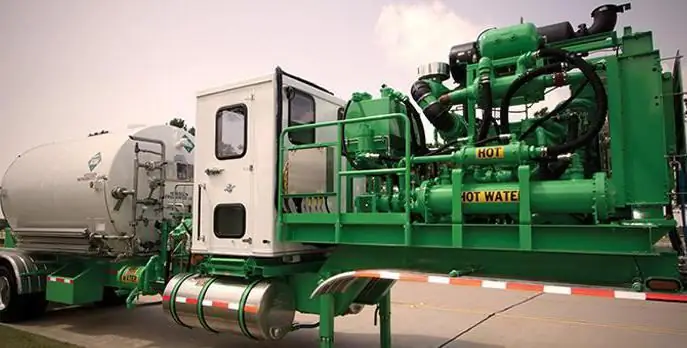
The unit is a multi-component functional component of gas pipelines. Its main parts include compressors, fans and blowers. The installation is driven by an engine represented by an electric motor or a gas-air turbine. By the way, the power range of a gas turbine gas compressor unit varies on average from 4 to 25 MW. The equipment has a special shelter in a modular design, which protects the working stuffing from external influences. The frame is made fromhigh-strength sheet steel having technological outlets. Buffer storages, fuel outlet channels, exhaust systems, heating and air conditioning modules can be used as additional functional blocks. The security system necessarily includes fire protection equipment, emergency shutdown automation and sensors for monitoring individual network parameters such as pressure and temperature.
Working principle
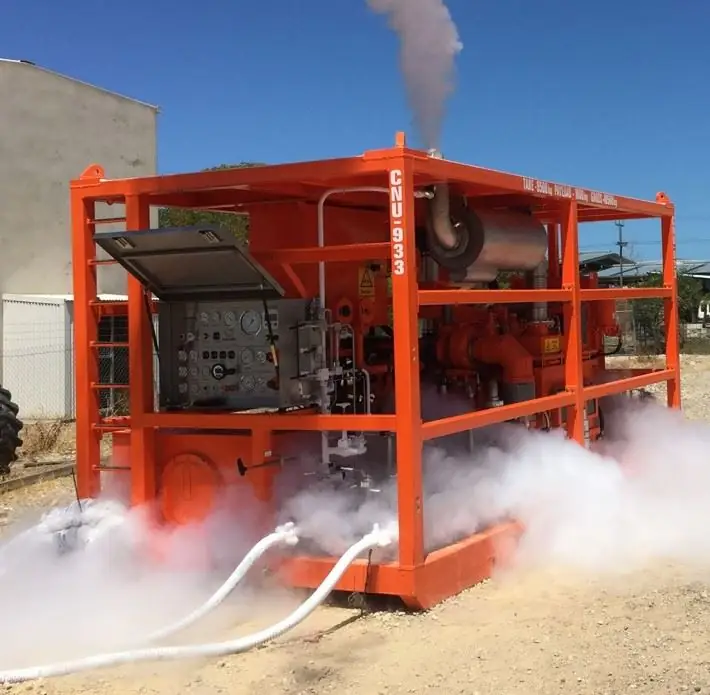
A unit connected to the line, after starting the drive unit, starts the rotation of the compressor. The rotor impeller is designed in such a way that the pressure increases during its rotation and air is sucked into the compressor. If necessary, pressure correction, as well as air conditioning and air purification, are carried out by connected fans. Compression of the transported mixture is carried out by gas pumping units during an adiabatic process, that is, without a sharp increase in temperature (about 200 ° C). Further, the gas-air mixture is supplied to the distributor block, to the pipeline for further delivery through nozzles with filters or to the buffer storage zone.
Units with reciprocating compressor
Traditional GPA version, which uses two- or four-stroke engines directly coupled to the compressor unit. According to the level of maintained pressure, piston units are divided as follows:
- Low pressure systems (up to 2 MPa). They are used on the head compressor units as part of the transport network, the sourcegas raw materials in which are depleted deposits.
- Medium pressure systems (average 3-5 MPa). They are mainly used in the infrastructure of intermediate stations in order to normalize the throughput indicators of gas pipelines.
- High pressure systems (10-15 MPa). Used to pump raw materials into underground gas storage facilities at large compressor stations.
The advantages of piston gas compressor units with a gas turbine drive include a high degree of technical reliability, maintainability and the ability to use in a wide range in terms of pressure.
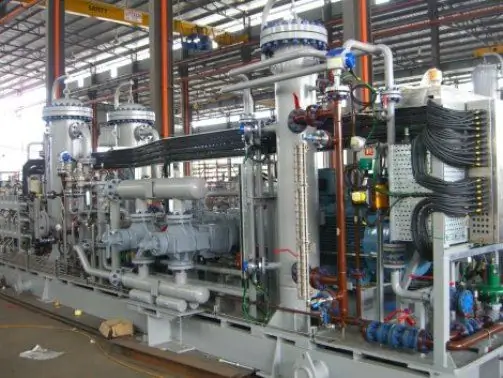
Centrifugal units
This equipment is characterized by a higher productivity of about 20-30 million m3/day. and the ability to compress gas-air mixtures by 1.5-1.7 times. Centrifugal blowers do not have mechanical rubbing elements, which prolongs their service life, eliminating the need for regular use of lubricating fluids. This design feature determines the uniformity of gas flows at high speed without pulsations. If we talk about the weaknesses of centrifugal gas compressor units, then a high degree of compression is achieved only by connecting several stations in series into one complex. Therefore, with high performance, fuel consumption also increases.
GPA control system
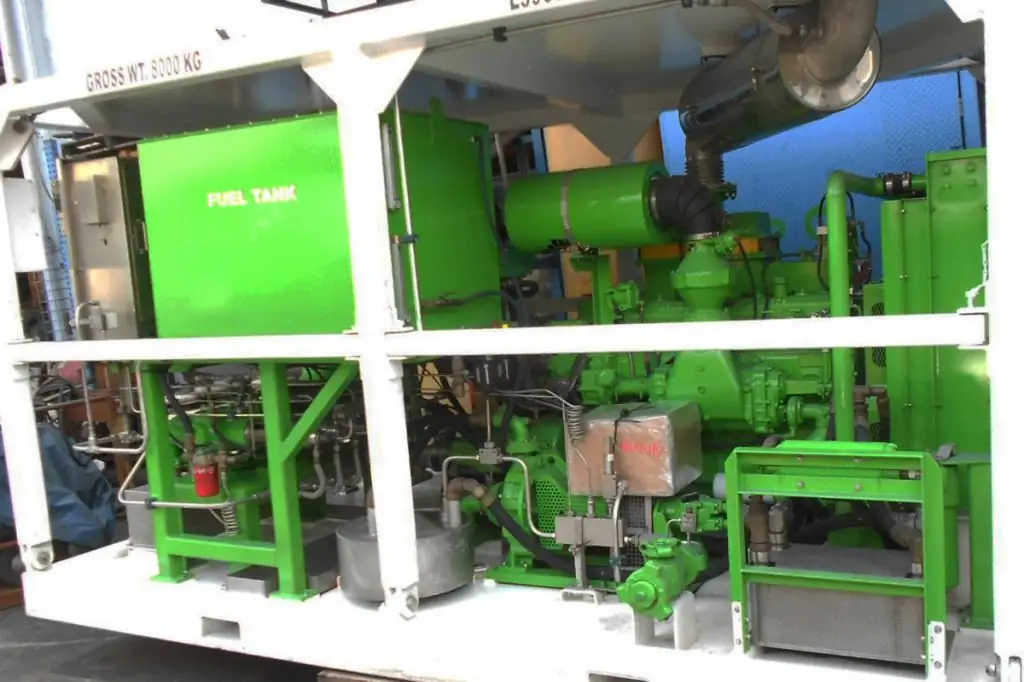
Modern gas pumping complexes are providedautomation for monitoring workflows and the status of functional modules. In particular, the following tasks are being implemented:
- Adjusting the supercharger speed when supplying the fuel mixture to the engine.
- Adjustment with minimum surge margin control.
- Control of emergency conditions.
- Regulation of mechanical parts of the compressor.
- Registering, processing and displaying information on the dispatcher's display.
In addition, the operation of gas pumping units provides for the control of serviceability and proper adjustment of actuators, sensors and communication lines. For this, input and output channels are used. Legacy equipment may still use analog devices such as thermocouples and discrete controllers.
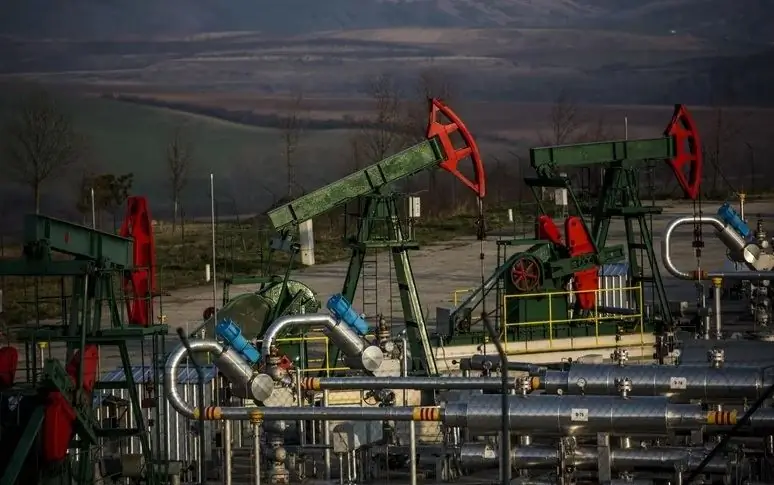
Maintenance of GPU
Gas pumping stations have a maintenance schedule with a set of works aimed at maintaining the mechanics and software in working order. During the audit of the unit, the structural integrity and correct functioning of the executive bodies are checked, indirect operating parameters are evaluated, system diagnostics are carried out, etc. Based on the results of the audit, a decision is made on the possible repair of the gas compressor unit with defectoscopy of operational parts and assemblies. During a major overhaul, worn-out elements can be replaced, structural parts and segments can be restoredoil lines, etc. Minor repair operations are usually associated with restoring the tightness of containers, eliminating leaks and updating consumables.
Reviews on the work of the GPU
The combination of pipeline networks and compressor units is still considered the best solution for optimizing the transportation processes in relation to oil and gas raw materials. As employees of enterprises in this field note, GCU equipment allows increasing the energy efficiency of trunk lines without reducing the reliability and safety indicators for fuel delivery. At the same time, the list of functions of gas pumping units is regularly expanded due to the same automation, which allows saving on the organization of auxiliary points for monitoring the operation of the transport infrastructure. As for the negative reviews, they are associated with the high cost of modern GPUs and technological complexity, which requires appropriate qualifications from the maintenance personnel.
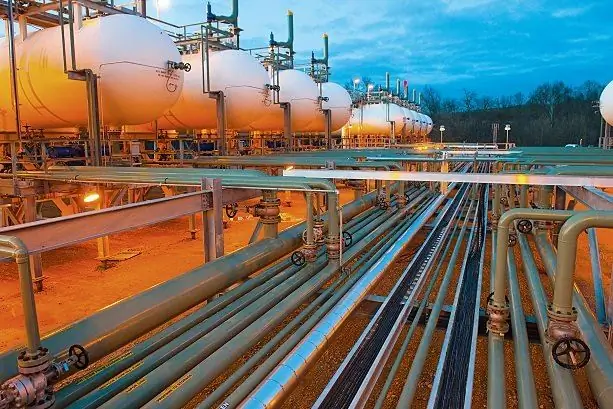
Conclusion
In recent years, the oil and gas industry is going through a stage of abandonment of technical means that were put into operation in the 20th century. The technical infrastructure is approaching service life limits, requiring upgrades. Among the first places in this list are compressor stations. Oil and gas enterprises are increasingly introducing new generation gas pumping units into their workflow, using the principles of computer modeling. Combined with the latest supervisory control tools, thisprovides extensive control over gas transportation. The real effect of modernization today is confirmed by actual data on the operational characteristics of compressor equipment and transmission lines.
Recommended:
Mechanization of an aircraft wing: description, principle of operation and device
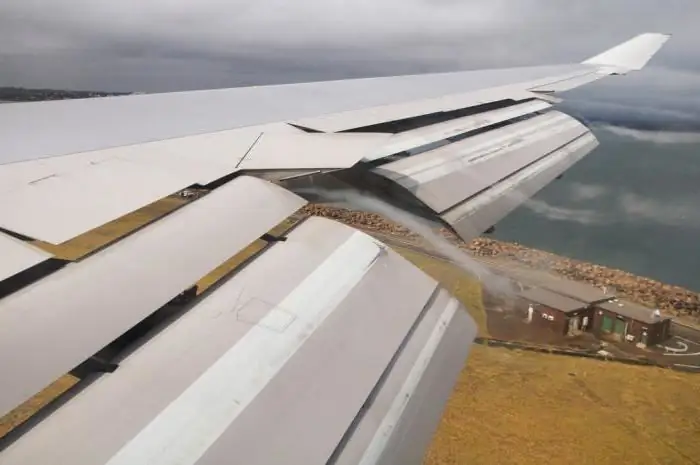
How do planes take off and stay in the air? For many people, this is still a mystery. However, if you start to understand this, then everything is quite amenable to a logical explanation. The first thing to understand is wing mechanization
Mobile gas station: description, device, principle of operation, application
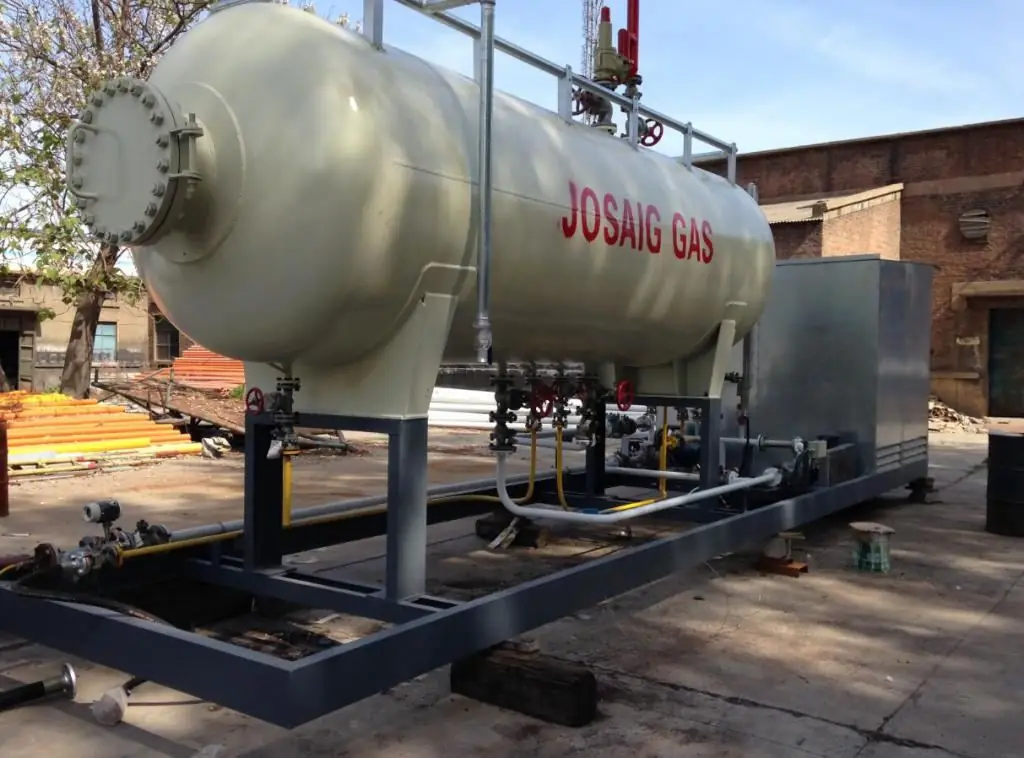
Mobile gas station is quite a popular business idea these days. Therefore, the achievement of any success in this area can only be possible if you pay maximum attention to the various key points that are described in this article
Electric locomotive 2ES6: history of creation, description with photo, main characteristics, principle of operation, features of operation and repair
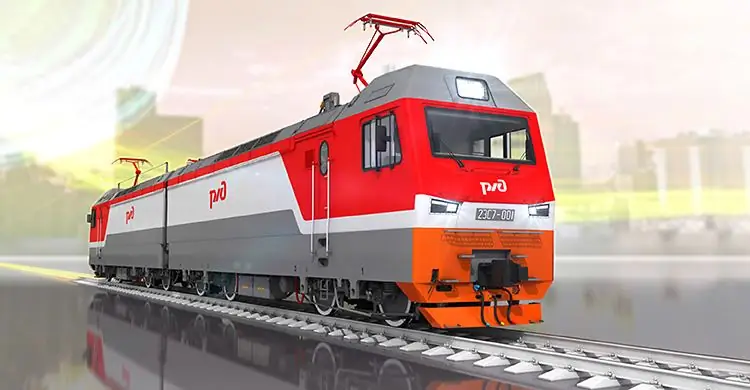
Today, communication between different cities, passenger transportation, delivery of goods is carried out in a variety of ways. One of these ways was the railroad. Electric locomotive 2ES6 is one of the types of transport that is currently actively used
Gas piston power plant: the principle of operation. Operation and maintenance of gas piston power plants
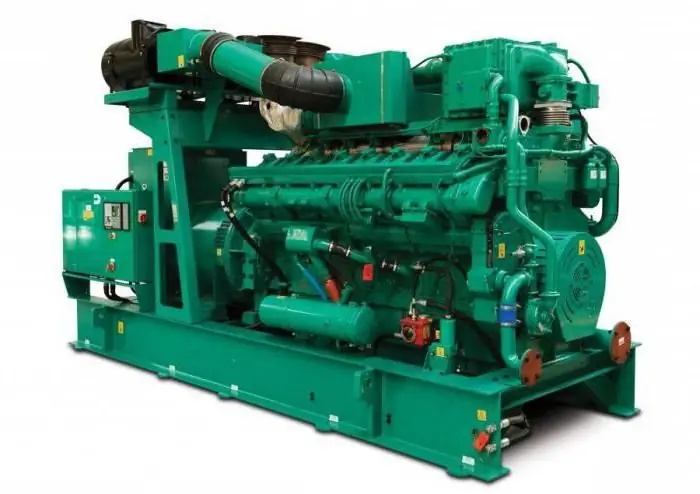
Gas piston power plant is used as a main or backup source of energy. The device requires access to any type of combustible gas to operate. Many GPES models can additionally generate heat for heating and cold for ventilation systems, warehouses, industrial facilities
A burner is Description, device, principle of operation, classification, photos and reviews
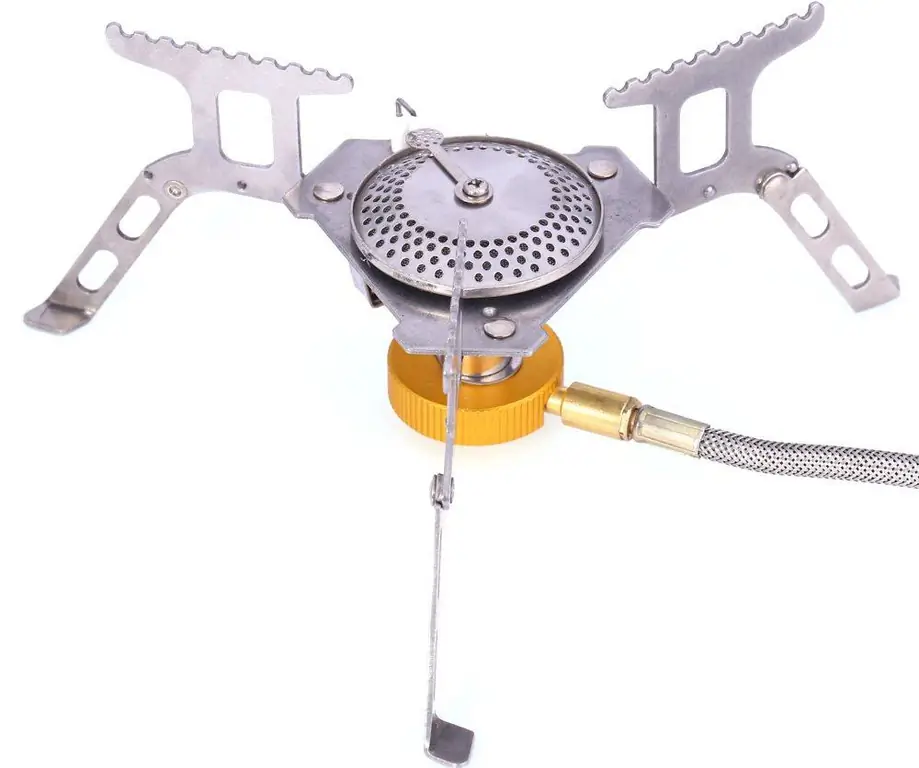
By burning the resulting mixture, a variety of tasks are solved - from the release of thermal energy to thermal cutting action. The simplest tool for carrying out such operations is a burner - this is a small-sized apparatus in which a torch flame is formed from burning fuel