2025 Author: Howard Calhoun | [email protected]. Last modified: 2025-01-24 13:10
Now there is a huge amount of technology that allows you to quickly and reliably connect electrical wires and cables. Each of the methods has both pros and cons. Wires and cables are connected by welding or soldering. You can use twisting or fasten the conductors with terminal blocks, PPE. All of these methods are good and effective. But when you need to get a really high-quality connection, crimping leads will help.
The result of this method is a good contact, protected from oxidative processes and a particularly strong connection. The only downside is inseparability. Disconnecting the two cables will not work. You just have to cut. Crimping of wires is carried out using special tips - sleeves. They can be purchased at any hardware store or market. The cost of these items is about $1 per item.
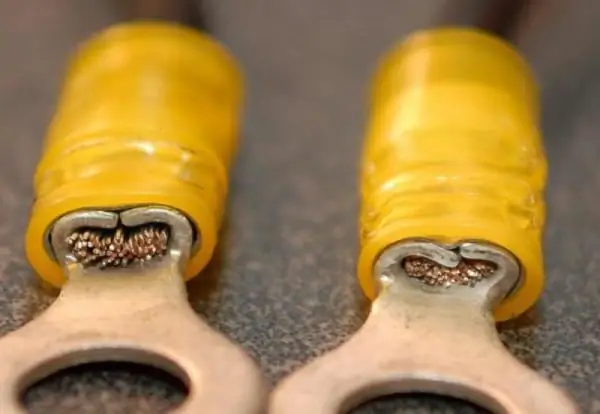
Cores are inserted into them. And the sleeve itself then with the helphand press is deformed, due to which a reliable electrical connection is created.
Why is crimping reliable?
Connecting wires by crimping is the strongest way to connect. No existing mounting option can provide such reliability. In order to obtain a quality connection, sufficient contact area and strength must be provided. The twisting of two conductors, popular with home craftsmen, does not give either one or the other. When twisting, conductors often oxidize (even in the presence of electrical tape). And this is not very good for electrical contact. The use of insulating clips or PPE can improve some strength characteristics for simple twisting.
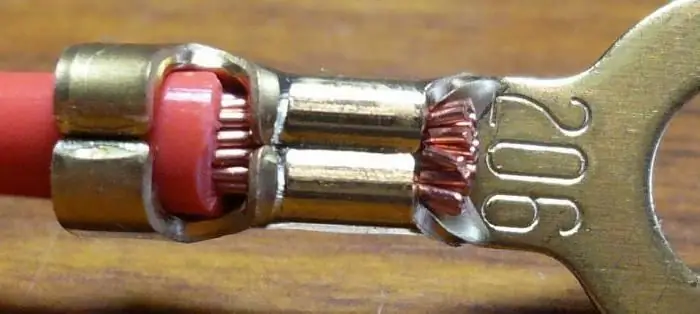
However, there is no absolute guarantee of the reliability of such a connection here either. Terminal blocks are the ideal solution, but in the case of high current they are not suitable. A good contact can be hollowed out by soldering. Here and strength, and excellent contact. But there are downsides to this connection. Solder can get hot if there is a lot of current flowing through the conductors. Also soldering wires is not always convenient and safe.
Perfect contact can be achieved by welding. However, the tools for creating such a connection are quite expensive and not available to everyone. Also, working with these devices requires certain skills. Crimping wires allows you to get the perfect electrical contact, and the connection itself will be as reliable as possible in terms of strength. Break similar fastenersquite difficult.
Connection Features
The technology implies two options for crimping. This is a method of local indentation and continuous compression. Copper or aluminum wires are used for work. The sleeve must also be of these materials. There are also elements made of copper-aluminum alloy.
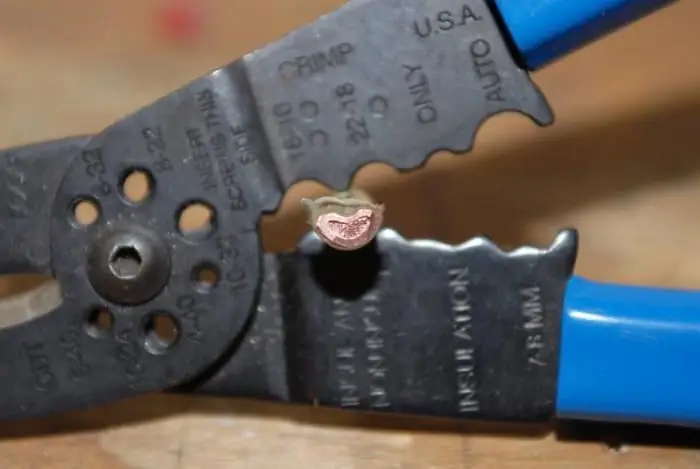
Since aluminum cables are prone to the appearance of oxidation films on them, the sleeve must first be cleaned and treated with special lubricants. Copper wires are also pre-treated. The use of lubricants in the process reduces the risk of possible wire damage. The friction force is also noticeably reduced. Crimping is carried out with a manual or hydraulic tool. In the latter case - figure press. It is usually used in large industries.
How does it work? The two ends of the cable are crimped until they take a round shape. Next, the core is inserted into the sleeve until it stops. You can connect not exactly end-to-end. But in this case, the cross section of all the cores does not exceed the sleeve. In the case of local compression, the contact directly depends on the depth of the pits. The latter can be measured with a caliper. If solid compression is used, then the cross-sectional area is checked. Then, when the crimping of the wires is successful, it is necessary to process the outer layer with electrical tape or an elbow. Next, the wire and cable are neatly laid in the junction box.
Required tool
In order to connect wires or cable cores in this way, you will needspecial tool. These are mechanical press pliers. They allow you to quite tightly clamp the ends of the sleeve along its entire length.
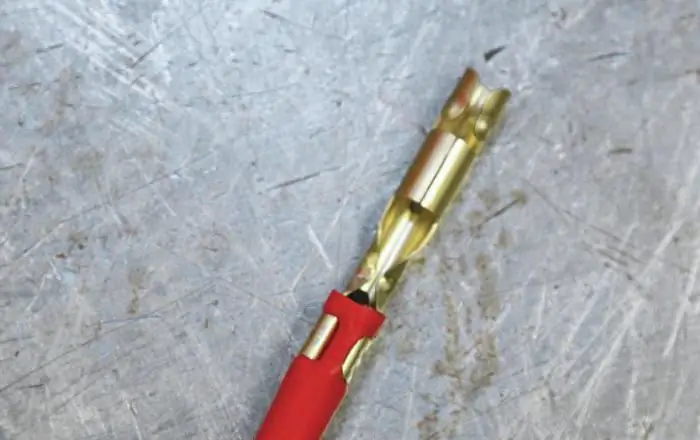
The hand tool allows you to compress a tip that is less than 120 mm in section2. The larger sleeve is compressed with a hydraulic tool. If the task is to connect several cable cores of various sizes, then it is better to use a crimping tool for other types of wires. Such pliers are equipped with interchangeable punches and dies for different sections.
Sleeves for wires for crimping and their varieties
To get the perfect connection, you need to choose the right sleeve or tip. In the technical documents, the sleeves for crimping wires have certain designations. So, there are the following types of tips:
- Copper.
- Aluminum.
- Combined.
- Insulated tips.
GM and GML
Copper parts are used to work purely with copper cables and conductors. They are divided into two types - GM and GML. The first are ordinary copper connecting sleeves. They are not protected in any way, they do not have protective coatings, they are not pre-treated. The appearance resembles nothing more than an ordinary tube. GML is also a copper sleeve, but it is tinned.
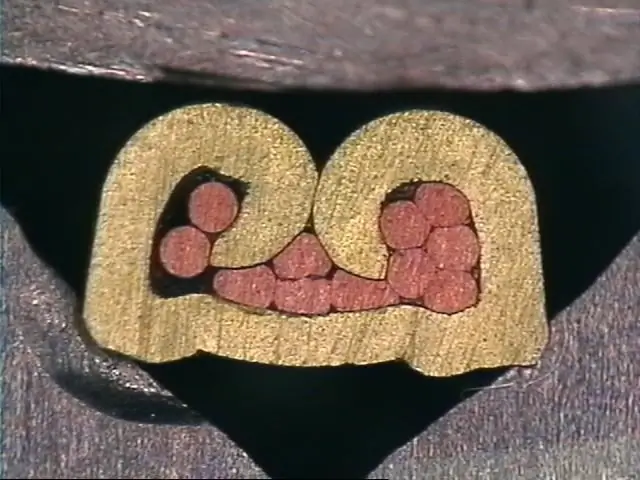
The surface of such a tip is covered with a layer of a special tin-bismuth alloy. This protective layer prevents oxidative andcorrosion processes. Copper oxidizes quickly, and the protective alloy avoids this. After connection using HML, copper wires do not enter into oxidation reactions. Some experts use tinned copper sleeves for crimping wires along with aluminum conductors. According to the masters, the tin layer does not provide direct contact between the conductor and the copper sleeve. But this is not recommended. In the process of deformation, the integrity of the protective layer is violated, and corrosion is only a matter of time.
Aluminum sleeves
In technical documents, they are referred to as "HA" and are only suitable for working with aluminum. Do not use them for wires of other materials.
Combination Sleeve
These are aluminum-copper tips. They are designated in documents as GAM.
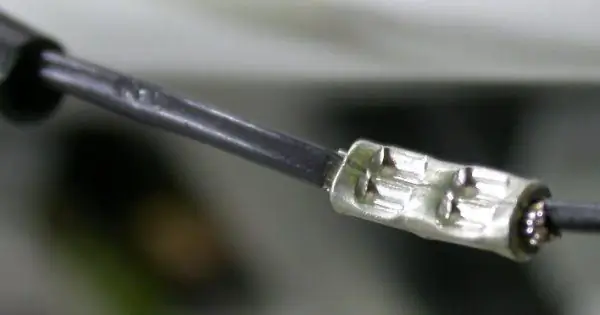
With their help, copper wires are crimped end-to-end with aluminum ones. These devices are perfect in cases where you need to build a new cable with old wiring. On the one hand, a copper core is inserted into the cartridge, on the other - aluminum. Two parts of such a cartridge are interconnected by friction welding.
GSI sleeves
These are insulated wire lugs for crimping. This sleeve is a conventional tin alloy tip. The top part is covered with polyvinyl chloride insulation. With the help of such a device, multi-core cables with copper components are perfectly interconnected. GSI is good and easy to use - there is no needremove the insulation from it before the process.
Tip sizes, design features
Minimum available sections for GML - 1.5 mm2. Further, the sizes grow - 2, 4, 6, 10 mm2 and above. According to these values, we can say that the cross sections of the sleeves are equal to those of wires and cables. Deciphering the designations of the tips is quite simple. For example, GML-6 is a copper tip, tinned. The cross section is 6 mm2. In the case of combined sleeves, two sizes are indicated in the marking - for aluminum wire and for copper. For example, GAM 16/10 - 16 for aluminum, and 10 for copper.
By design, the sleeves can be through in the form of a hollow tube or with a partition. The latter are used if the wires are crimped with end-to-end lugs. These partitions are located in the middle of the sleeve. With their help, you can adjust the depth of the cable entry. If you need to build it up, then both ends will go into the tip to the same length.
Mistakes in crimping work
Often, novice electricians can make mistakes. They are especially performed by home craftsmen in the process of repairing a house or apartment. Consider the most typical of them, which are allowed in the process of connection by crimping. The cross section of the sleeve is smaller than the wire. Never try to shrink the cable and adjust it to fit the ferrule when connecting.
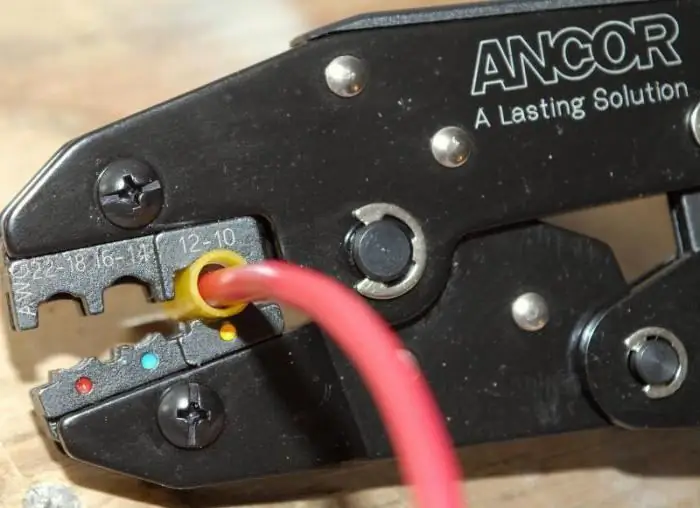
This may increase the electrical resistance and reduce the throughput. In places like thisconnections, the core will become very hot, and over time it will simply collapse. The second popular mistake is the sleeve, the diameter of which is larger than necessary. In this case, it will not be possible to obtain the required mechanical strength of the joint. Even after bending the core several times, you still can't get a good connection.
Cutting the sleeve
When crimping copper wires or any other in conditions of scarcity of sleeves, many try to cut the tip into several parts. It has to do with saving money. But such an action will only lead to an increase in resistance and heating. Also, the wire will not be crimped well. The connection is carried out only with a tool designed for this. You should not try to perform the task of crimping and crimping with hammers, pliers or other other tools. The element will not take the desired shape and will not secure the wire. This can damage the sleeve and cable.
CV
Crimping is a reliable way to connect two wires or strands and get good contact. But it is necessary to use only devices intended for this purpose. As a result, you will get a high-quality one-piece connection that will not oxidize.
Recommended:
Cylinder head crimping: technology and crimping process
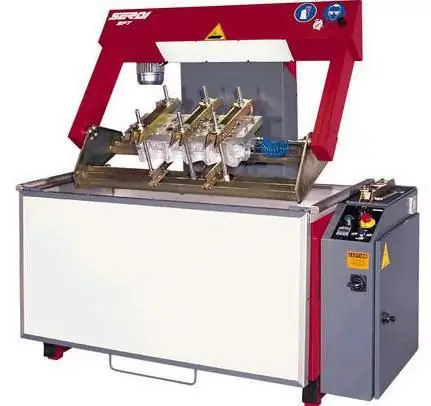
The article is devoted to cylinder head pressure testing. The technology of the operation, the variety of approaches and the nuances of its home use are considered
Twisting wires in a junction box: step by step instructions, tips from the masters
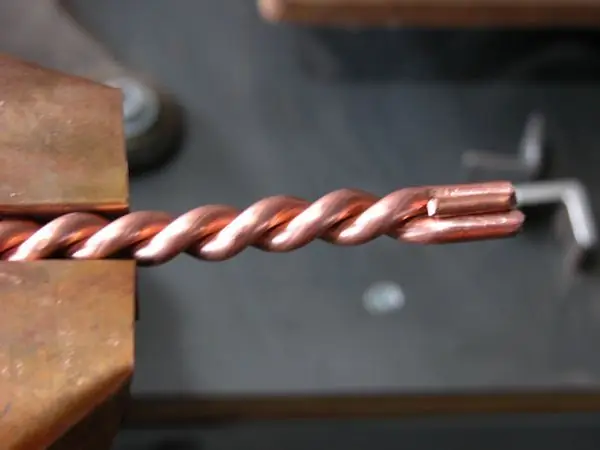
In the process of repair, the owners of a house or apartment are faced with the need to install junction boxes. The wires in them must be properly mounted. The most famous way in this case is twisting. It has certain advantages and disadvantages. Almost everyone can do the twisting in the junction box with their own hands. But at the same time, you need to learn about all the nuances of such work. How to twist will be discussed in the article
Internet in a private home. Without phone and wires
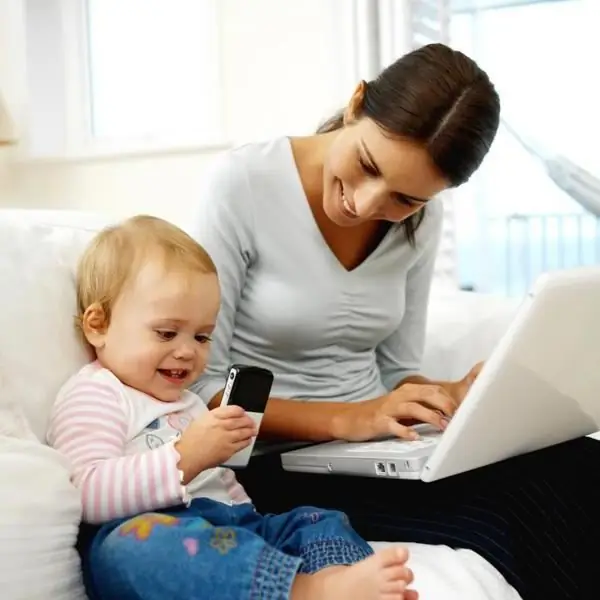
Wiring the Internet to a private house without a telephone has become not only popular, but also very convenient for a modern person. An increasing number of users are abandoning wired Internet in a private home, preferring wireless
Durite sleeves: description, characteristics, types
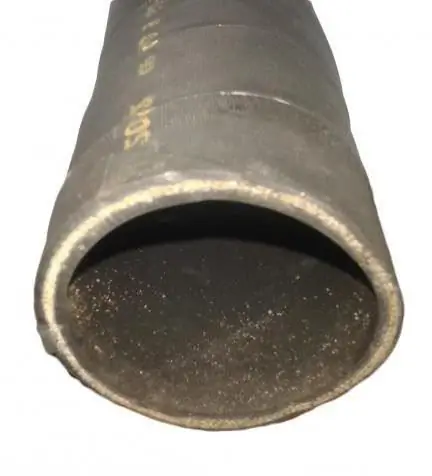
Currently, the industry is developed quite powerfully. Many industries use different types of fuel. Durite sleeve is often used to supply this raw material
Welding wires in a junction box: step by step instructions, rules, tips and tricks
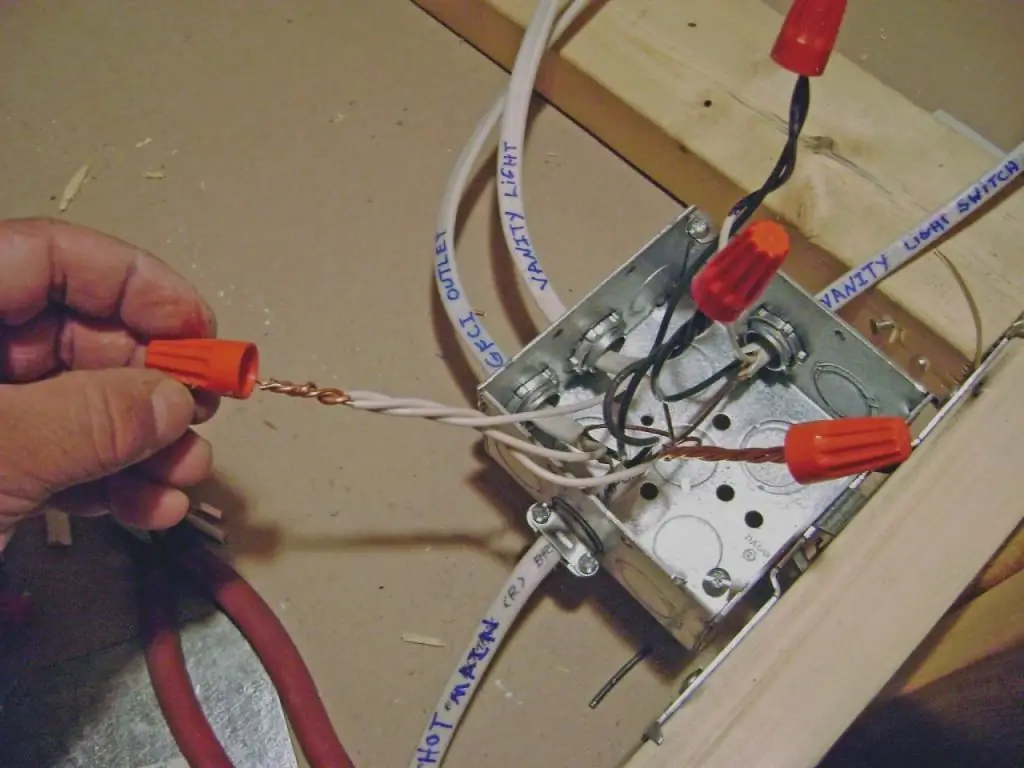
Features of welding wires in a junction box with your own hands. The main advantages of the welding connection of wires and the technology of the welding process. Electrodes that are used in the welding of copper conductors. Apparatus for welding. DIY step-by-step instructions for making a welding machine