2025 Author: Howard Calhoun | [email protected]. Last modified: 2025-01-24 13:10
Without lubricants, the operation of most modern metalworking tools is impossible. At the same time, the metal elements themselves, which are used in technology, cannot meet the functional requirements without appropriate maintenance with special substances. To date, cutting fluids (coolants) are on the market in more than 600 items. Among them you can find products for use in power units, for metalworking applications, as well as medical, insulating, shape-separating, biological and anti-corrosion oils. Most of these fluids are used by industrial plants and the construction industry.
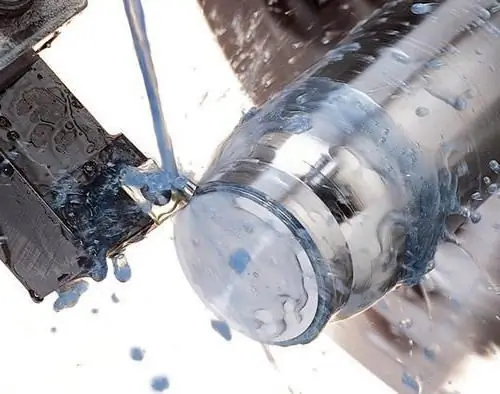
What are cutting fluids for?
Most often, lubricants are introduced into the working space between the rubbing elements in order to minimize wear in the mechanisms. Often this function is supplemented by an increase in efficiency. But this applies to traditional substances of this type, however, cooling materials are also necessary to protect equipment and working elements from overheating. For example, lubricantcoolants for metalworking allow you to optimize the temperature regime and relieve high pressure. As a result, such compensation not only allows you to maintain the performance of cutters, but also improve the characteristics of the resulting products. There are also specialized protective products, in which the main emphasis is on providing anti-corrosion, insulating and sealing properties. This category of materials is most common in construction.
Coolant composition
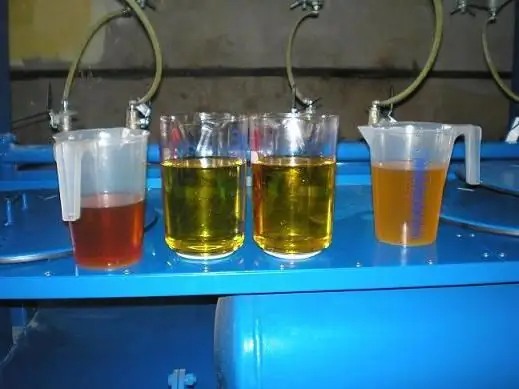
Any lubricant is made according to a special recipe. There are basic regulatory compositions, as well as modifications that are obtained in order to provide special performance. Most often, the basis is a low-viscosity oil mixture. Lubricating fluids are produced from it, the composition of which is also modified with chlorinated paraffin, zinc dialkyldithiophosphates, multi-ash calcium sulfonate and other additives. Such compositions are commonly used in cutting high temperature alloys and stainless steel parts. A feature of the action of this composition is to prevent sticking of the material to the tool. The use of a low-viscosity deep-hydrogenated fraction of sour oil as a basis is also widespread. Working fluids on this basis are used in electroerosive machines of varying degrees of power, in the implementation of finishing and turning operations on mechanical assembly production lines.
Main characteristics of liquids
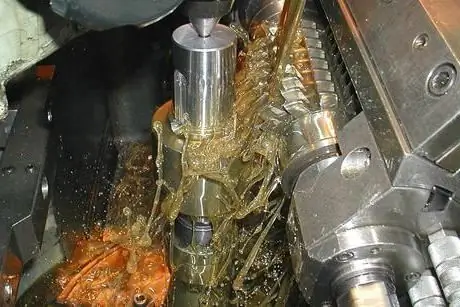
The appearance characteristics of these fluids vary greatly depending on the additives used. As a rule, it is a liquid brown mass, the shades of which may vary. From the point of view of the working function, one of the most important characteristics is the density. A standard cooling effect lubricant has a density ranging from 1100 to 1200 kg/m3. However, this indicator can be varied in the manufacture of the concentrate. Also, cutting fluids in some formulations contain active ions. For a 1% aqueous solution, this value can be on the order of 10 pH. Manufacturers generally recommend using concentrated formulations with a factor of 1-3%. But depending on the location of the operation being performed and the target material, this value may increase. So, to ensure the grinding function, it is recommended to use a 4% concentrate, and for complex metalworking, the indicator increases to 7%.
Characteristics in terms of coolant supply
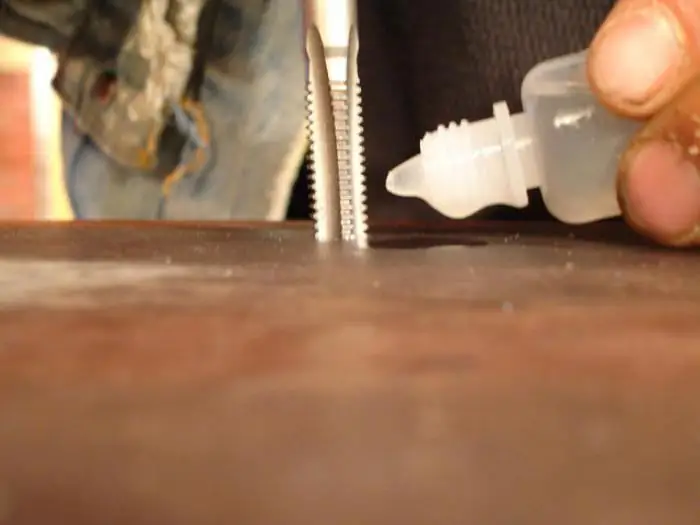
There are different methods for supplying, applying and distributing lubricating fluids to functional surfaces. Not all of them impose special requirements on the lubricant in terms of physical properties, but in some cases they are important because they determine the nature of the interaction with the working environment. Ultimately, this affects the efficiency of the function of the substance itself. For example, if a cutting fluid for metalworking machines is used, then speed comes to the forethe supplied jet. Accordingly, the lighter the components, the more effective the lubrication of the cutting element during operation will be. The fraction of individual particles in the composition of the liquid is also taken into account. At high feed rates, they can adversely affect the properties of the surface, deforming it. In addition, machine operators must take jet temperature into account and allow for possible adjustments to this value for site conditions.
Technical and operational properties
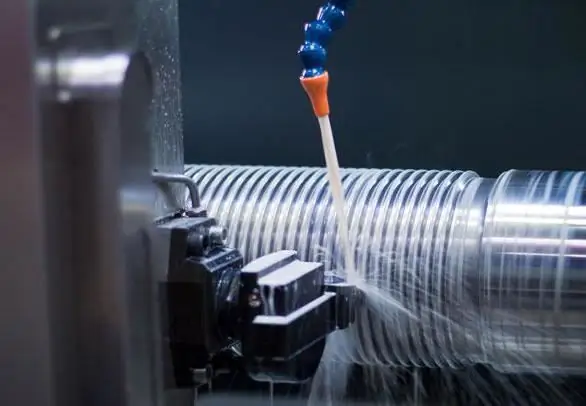
Basic qualities refer to providing optimum lubrication and cooling properties. Also, in some areas, high requirements are placed on washing functions, which allows timely cleaning of the surfaces of parts during the operation of the mechanism. The additional qualities that modern cutting fluids are endowed with include bactericidal, environmentally friendly, hygienic, chemical and extreme temperature resistance. It is important to consider that lubricating components themselves have a considerable chemical effect on various materials, therefore, when choosing a product, you should compare the quality of the fluid with the target material.
Varieties of coolants
The main classification of lubricants with a cooling effect is based on the origin of the product. The most common industrial oils that are used in industry and the manufacturing sector. Mostly these are petroleum fluids supplemented with modifiers. One of the popularvarieties of such additives are also coarse emulsions of petroleum products, which are formed in the aquatic environment. Stable microemulsion types of cutting fluids allow the formation of semi-synthetic or synthetic compounds based on organics. Low-boiling, evaporating mixtures based on halogen derivatives of hydrocarbons with additives have also become widespread.
Application of coolant
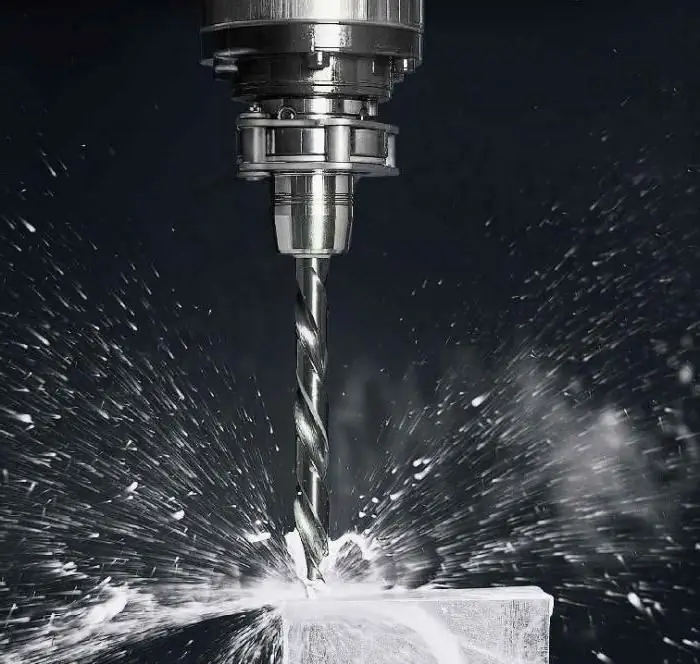
Lubricants are most widely used in the production of metal parts, as well as their processing. They not only protect working equipment from premature wear, but also improve the quality of manufactured products. The second place in demand for such materials can be attributed to the construction industry. In this industry, the use of cutting fluids is due to the desire to provide protective qualities to building materials, insulating and decorative coatings.
Manufacturer Reviews
Proma, Univeko and Messer can be singled out among the largest coolant manufacturers. The first brand became famous due to the release of effective tools that allow you to reliably process metals using cold and hot methods. Feedback from users of this fluid notes that during the production process it is possible to minimize rejection rates, increase productivity and increase processing accuracy. The production of lubricating fluids of the Univeco company has also been established at the modern level. This group of mixtures is made on the basis ofcorrosion inhibitors and activated aquatic environment, which is especially appreciated by consumers in the construction sector. As for the Messer brand, its products are more often used in high-precision machining operations. Users attribute high anti-corrosion properties, resistance to micro-fermentation, as well as environmental friendliness to the advantages of such liquids.
Conclusion
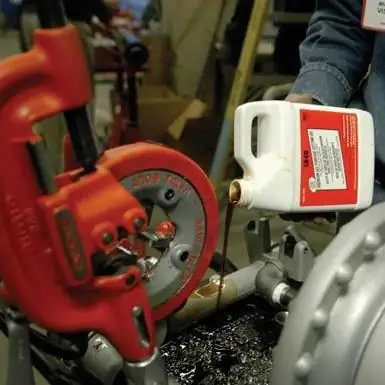
Modern technologies for processing metal parts are gradually moving away from traditional mechanical methods of impact. Against this background, the consumption of protective and stability-enhancing products is also decreasing. Nevertheless, there are industries where cutting fluids are still relevant. This is primarily construction, mechanical engineering, medicine and electrical engineering. Another thing is that in highly specialized areas, materials that are more and more perfect in terms of their technical and operational properties are required, requiring the use of high-tech additives and modifiers.
Recommended:
Universal lathes: overview, specifications and reviews
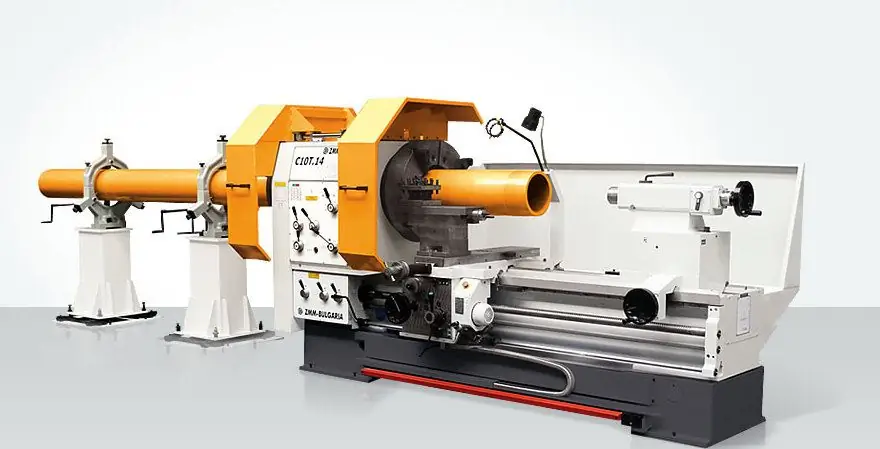
For standard operations with workpieces and not only, universal lathes with DRO are suitable. Simplified design and savings on electrics allows you to produce equipment that has a low cost. Sometimes for many customers this is the determining factor
Industrial milk purifier separator: specifications and reviews
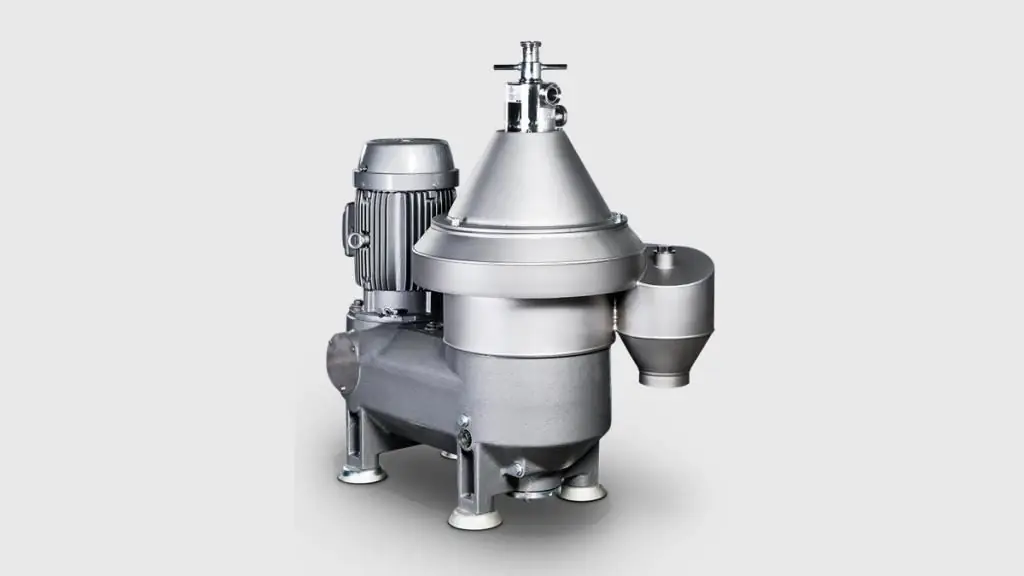
The basis for the production of meat and milk today are giant farms, where cattle are kept in quantities of more than tens of thousands of heads. With so many animals - including almost constant milking - such farms produce tons of milk per day. And of course, industrial separators are needed to filter milk
CNC small business machines - overview, types, specifications and reviews
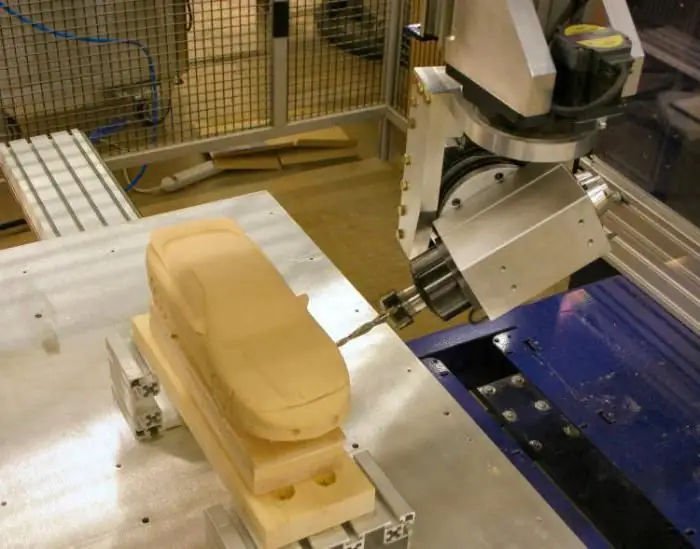
CNC machines for small businesses: types, descriptions, features, photos. CNC machines for small businesses: overview, specifications, reviews
Ball check valve: description, specifications, device and reviews
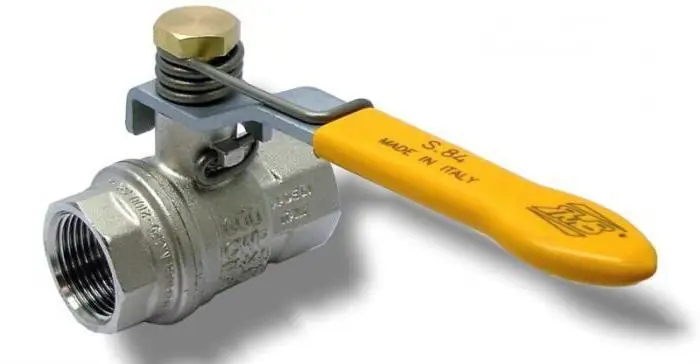
The creators of piping systems expected that water or any other product would move in one direction. But practice shows that there are exceptions. To avoid emergency situations, if the flow goes the other way, a check valve or one of its varieties is used in the pipelines - a ball valve
"2 shores": reviews on the quality of dishes and service, conditions for ordering food and delivery. "Two Shores": employee reviews
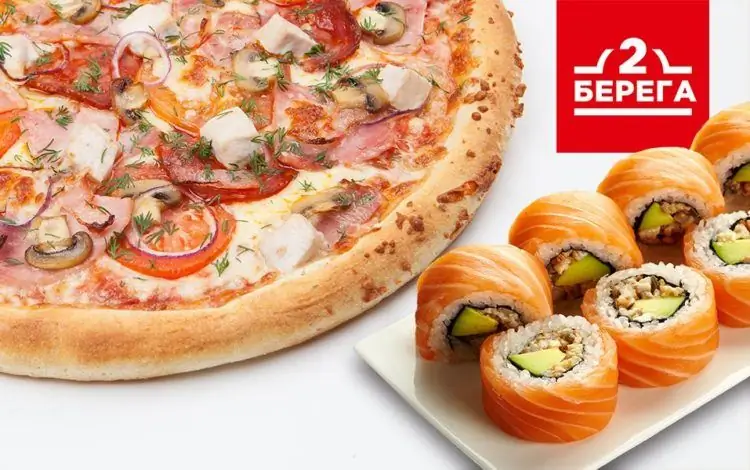
Food delivery is a great way to save time and do something that makes you happy instead of cooking. But not all establishments are ready to provide gourmet cuisine, and sometimes the food is so mediocre that the buyer regrets that he did not cook it himself. In today's article we will talk about such a company as "Two Shores". Reviews written on the Internet about her are quite contradictory