2025 Author: Howard Calhoun | [email protected]. Last modified: 2025-06-01 07:12
Gear shaping machines in a modern design are equipped with a rigid structure and a powerful electric motor. Vertical units are also equipped with hydrostatic bearings, cooling system and slotting spindle. The high performance indicator is due to the possibility of increasing the rotational speed of the working part up to two thousand revolutions per minute. The functionality and technical parameters of the models are expanded thanks to the CNC, as well as the movable spindle carriage, which allows you to change the position of the chiseling element in relation to the processed gear part.
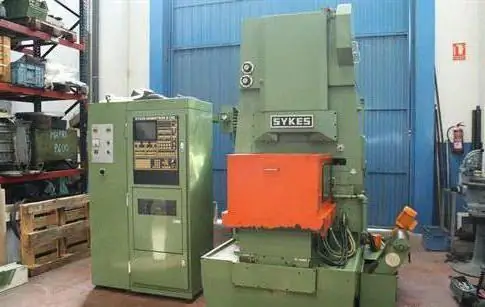
Varieties
Gear shaping machines are divided into three main types:
- Modifications with a table movable in a horizontal plane, which allows for infeed. It also includes a fixed stand.
- Versions with a fixed table and a horizontally movable stand to transport the tool while plunging.
- Models with a static table, a horizontally moving stand and a carriage capable of vertically extending the mortising tip by changing the position of its stroke.
The fixed table automated machine has more advantages than its counterparts. To be able to manufacture conical teeth, one of the tool axes is mounted at a certain angle. On machines used in mass production, an intermediate plate is provided under the vertical stand. Universal modifications are equipped with the ability to tilt the table or stand in the range of 10 degrees.
Gear Shaping Machines: CNC Models
In the modification with program control, complex kinematic schemes are replaced by separate motors for the main movement of the chiseling tool and for adjusting the unit along the axes. In the horizontal plane, the rack moves to change the diameter of machining parts with internal and external gearing, as well as radial feed.
The rack moves along the axes in the case of radial retraction of the slotting part at an angle and the finishing of special gear profiles. The movement of the carriage in the vertical plane causes a change in the processing area in height. The independent type spindle drive ensures the specified rotation of the workpiece, and the programmable interaction makes it possible to achieve maximum accuracy through the break-in.
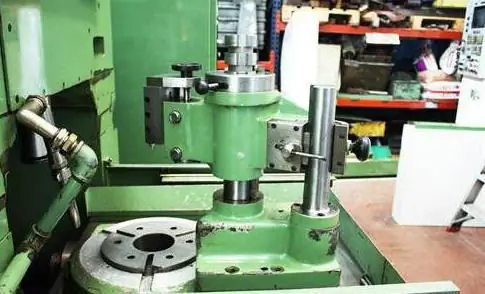
Technical capabilities
CNC gear shaping machines have the ability to change the mobility of the ram. The removal of the dollator on the reverse stroke is carried out by shifting back, which simplifies the design of the equipment, increasing its rigidity. You can correct the direction of the tooth usingslight tilt of the working part.
Due to the design features of CNC models, it is possible to expand the functionality, as well as comply with manufacturing accuracy in accordance with GOST 1643-81. Gear type rims have an identical module and are machined with one chiseling tool. The sequence of manipulations in one pass increases the productivity and accuracy of the placement of the crowns.
Working principle
Technical characteristics of gear shaping machines allow the cutting process to be carried out by reciprocating movement of the working part. Semi-automatic units have a vertical layout. Setting the center distance and cutting the tooth to the required depth is corrected using a table moved by a hydraulic cylinder. The equipment is capable of operating in adjustment and semi-automatic modes with the possibility of reusable finishing of products.
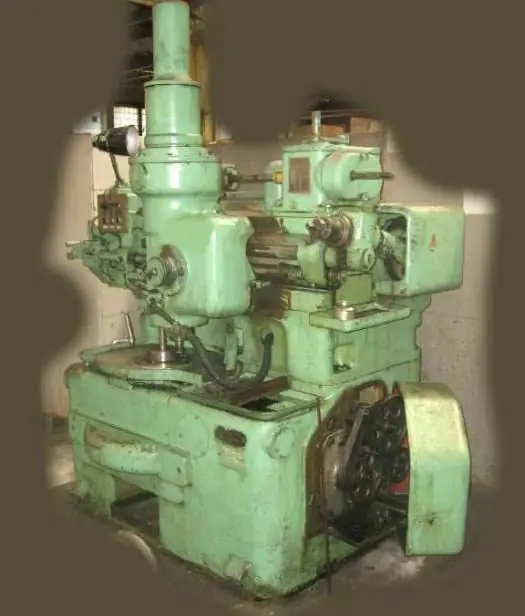
Change the circular feed allows a DC electric motor. It is powered by a special amplifier with an automatic machine that switches the cycle of processing the workpiece. With a three-speed main drive motor, double tool movements per minute can be converted. Radial insertion is carried out by the operation of a wedge slider moved by a hydraulic cylinder. The total plunging range is carried out through the stops, and the retraction at idle is carried out by means of the spindle. Retraction of the part at an angle is realized by shifting the rack relative to the axial part of the table. Workpiece revolutionsare taken into account by the electronic pulse controller, which makes it possible to adjust the rolling arc. The machining of gears with internal gears provides for the automatic withdrawal of the tool up.
Setting up the gear shaping machine
The main cut is made from an electric motor with three speed ranges. It aggregates with a pair of spur and interchangeable gears, as well as bevel gears and a toothed belt drive. The force is transformed to the drive shaft, which transfers the reciprocating effect to the spindle of the working tool.
Circular feed is provided by a DC motor through toothed cylindrical elements. The main moment on the spindle is transmitted through a worm gear to the ram. The feed can be changed by adjusting the motor speed.
Among other settings for gear shaping machines, the following aspects are distinguished:
- Division chain - used for kinematic interaction when rotating the workpiece and tool.
- Node for retraction of the working part at idle - carried out by means of the caliper rolling through the eccentric, thrust, pusher and roller.
- The accelerated rotation of the part. This process is carried out through a chain from the motor to the cylindrical wheels. In this mode, part of the kinematics is deactivated by opening the elements of the pressure guitar.
- Center distance adjustment system. This distance is maintained by a thrust nut and a wedge-shaped slider. The position of the chain is adjusted by rotating the nut according to the correctivescrew.
- Manual spindle drive control is mechanically activated by the revolutions of the square through gears.
- High position drive system.
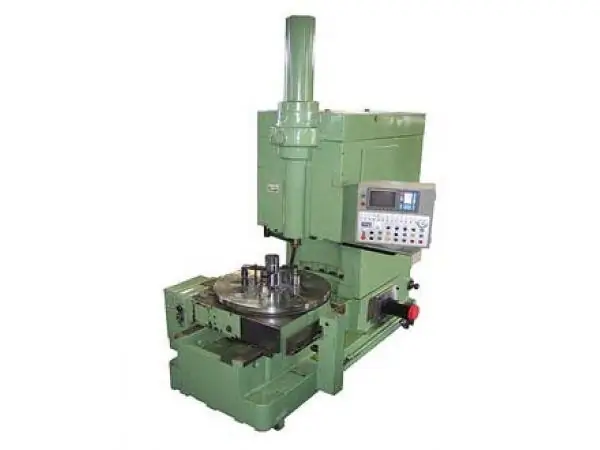
Preparation for work
Before starting the operation of the equipment, it is necessary to activate the introductory automatic switch, which is located on the side of the electrical cabinet. The rest of the fixtures must be brought to their original position:
- Set the table in the allotted position.
- Plunger slider must be in pre-working state.
- The spindle moves to the top position.
- The engagement wheel with the crown must be removed from the manual engagement square.
The switches are then set to "on" mode, after which the equipment is ready for operation.
Gear shaping machine 5B150
This universal unit is designed for cutting teeth on cylindrical gears of various meshing with a diameter of up to 80 cm and a module of not more than 12 mm. The working process is carried out with a chiseling tool made of high-speed steel. It is in a vertical position and performs reciprocating movements with synchronous running of the workpiece.
The workpiece to be cut is fixed on a horizontal faceplate with a special mount. To control the runout of the product, the element can rotate in an accelerated mode, regardless of the table, which can move along the horizontal guide parts of the skeleton.
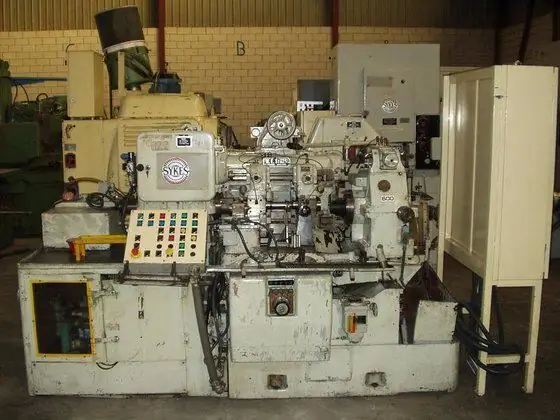
Features
The gear shaping machine, the purpose of which is discussed above, can provide the following manipulations:
- Independent drive rapid motion for exemplary mounting to home position.
- Mechanical type slow motion for precise positioning of workpiece and adjustment of plunging depth.
- Radial feed for inserting the chiseling device into the part by a given value. In this case, the unit operates in closed automatic mode.
- Achieve uniform workpiece dimensions by automatically adjusting faceplate movements.
Characteristics of 5V 150 gear shaping machines:
- The limiting diameter/module of machined wheels is 100/12 mm.
- Maximum stroke/mortiser size 200/200mm.
- The distance between the axes of the chisel and the table is 700 mm maximum.
- Faceplate in diameter - 800 mm.
- Radial/circular/double feed limits - 5, 4/1, 5/188 strokes per minute.
- Holler/table acceleration - 3/1, 7 rpm.
Model 5122
Gear shaping machines 5122 are also designed for cutting gear circles of cylindrical type by running in with a chiseling tool. Aggregates are used in mass and single production.
Hardware parameters:
- The maximum dividing size of the processed workpiece is 200 mm.
- Gear module - 5.
- Maximum width of the processed crown - 50mm.
- The working surface of the table in diameter is 250 mm.
- The face value of the cutter is 100 mm.
- Weight - 4, 4 t.
- Dimensions - 2/1, 45/1, 96 m.
- The power of the power plant is 3 liters. s.
- The number of double strokes of the working part in one minute is 200/280/305/400/430/560/615/850.
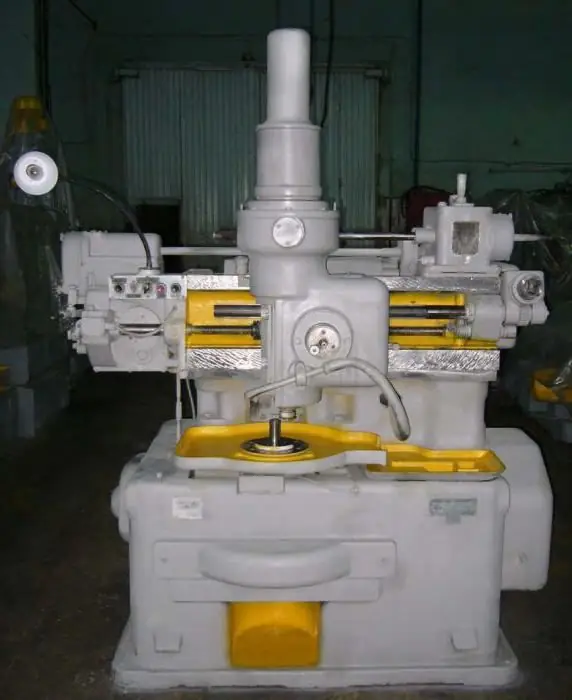
Modification 5M14
Universal mechanical gear shaping machine 5M14, like its analogues, is designed for cutting teeth of various types of cylindrical wheels. The chiseling tip of the equipment has a small overrun, which allows cutting gears in blocks. The workflow is carried out by rolling the part with circular modular fixtures.
The unit has a vertical layout; During operation, the cutter receives translational-return movement and synchronous rotation around its own axis. At the beginning of the operation, the working part after each move moves relative to the axis of the workpiece in automatic mode. This process continues until the required tooth height is reached.
Processing and stopping of the equipment are carried out under the control of an automatic controller.
Unit parameters 5M14
Let's consider the technical characteristics of the gear shaping machine:
- The size range of workpieces is 20-500mm.
- The maximum width of cut teeth with externalengagement - 105 mm.
- The same indicator for internal gearing - 75 mm.
- Spindle travel - 125mm max.
- Teeth angle up to 23 degrees
- Longitudinal movement of the caliper to the maximum - 50 cm.
- The distance between the ram and the table is from 45 to 170 mm.
- Double chisel strokes - 124/179/265/400.
The following is a diagram and designation of the machine controls:
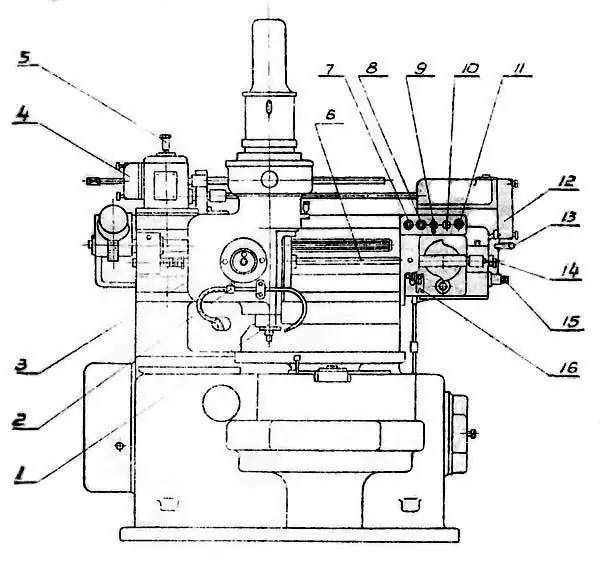
- Spindle of chiseling tool.
- Cooling system fluid regulator.
- Caliper fixing nut.
- Circular feed element.
- Reversible handle.
- Screw for longitudinal movement of the caliper.
- Start button.
- Stop key.
- Switch from setup to work phase.
- Switch for local lighting.
- Control for push.
- Radial feed block.
- Engaging the radial clutch.
- Main switch.
- Square for manual drive.
- Strap for counting mechanism.
As you can see, the unit in question has a fairly reliable and understandable design, while it is characterized by high performance and versatility in use.
Recommended:
Market "Amber" in Barnaul: description and mode of operation
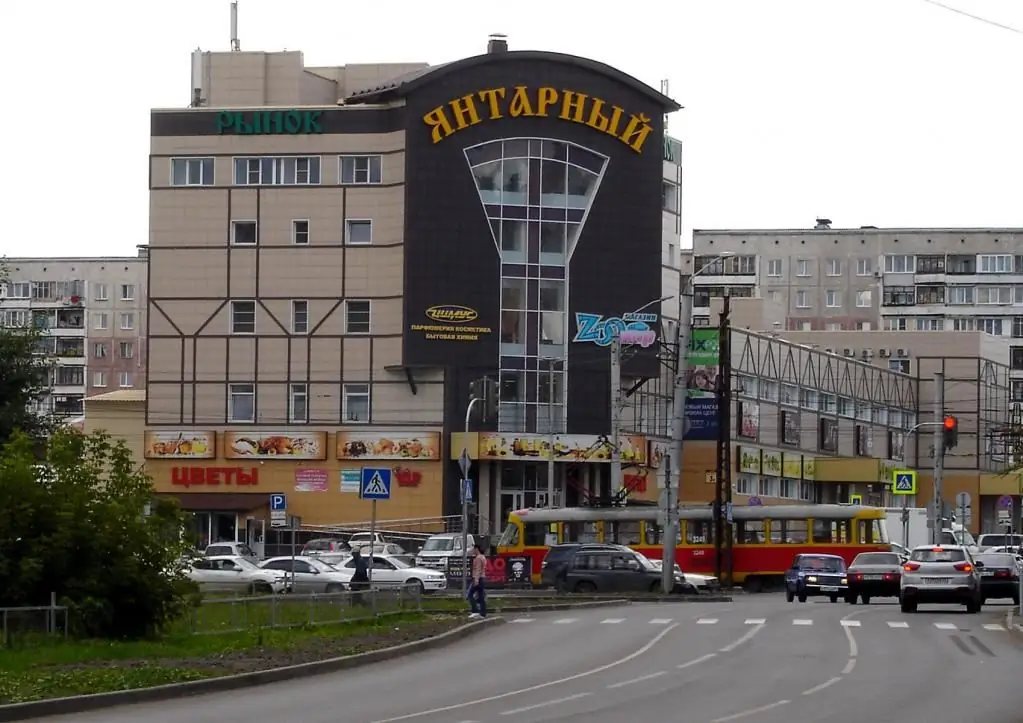
The Yantarny market in Barnaul is a unique place that combines an abundance of goods from a simple market and the convenience of a shopping center. In it you can buy food, things, shoes, appliances and cosmetics. All products undergo regular quality control
Machines for furniture production: types, classification, manufacturer, characteristics, instructions for use, specification, installation and operation features
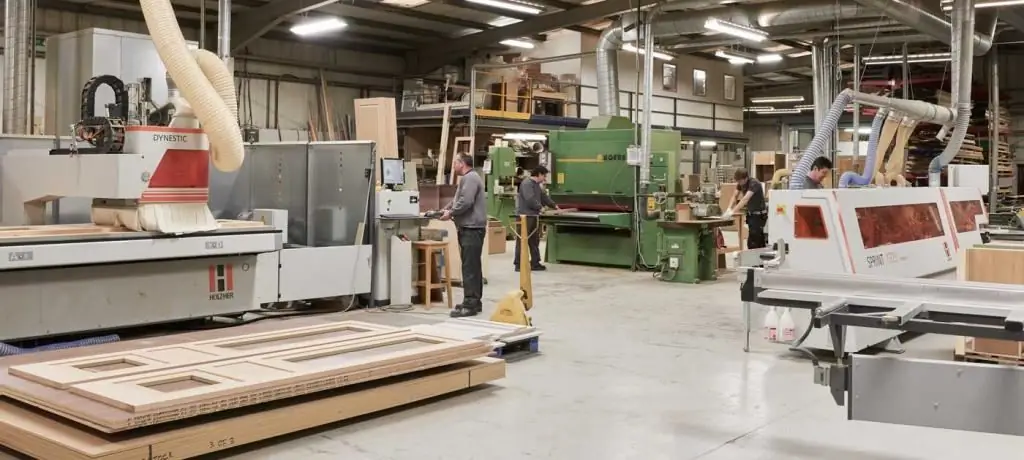
Modern equipment and machines for furniture manufacturing are software and hardware tools for processing blanks and fittings. With the help of such units, craftsmen perform cutting, edging and adding parts from MDF, chipboard, furniture board or plywood
Electric locomotive 2ES6: history of creation, description with photo, main characteristics, principle of operation, features of operation and repair
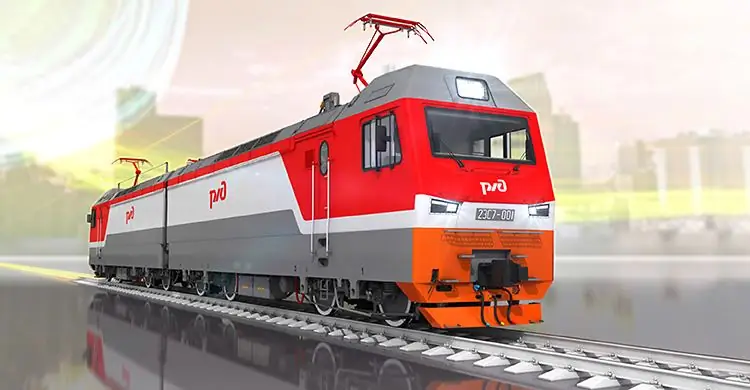
Today, communication between different cities, passenger transportation, delivery of goods is carried out in a variety of ways. One of these ways was the railroad. Electric locomotive 2ES6 is one of the types of transport that is currently actively used
Bending machines: types, description, principle of operation
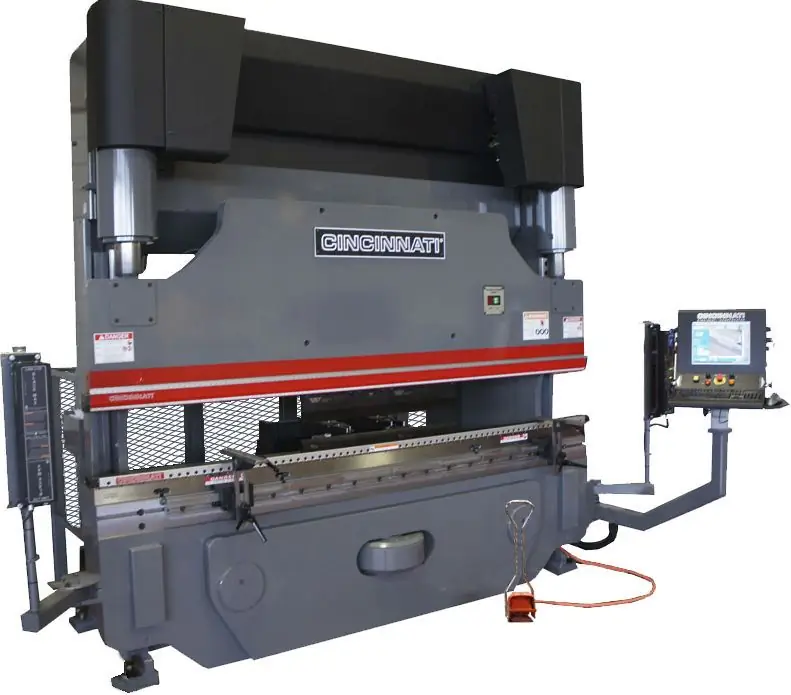
Bending machine: description, specifications, features, principle of operation, photo. Edge bending machines: varieties, device, design, parameters, manufacturers. Manual and rotary hemming machines: what's the difference?
Steel support: types, types, characteristics, purpose, installation rules, operation features and applications
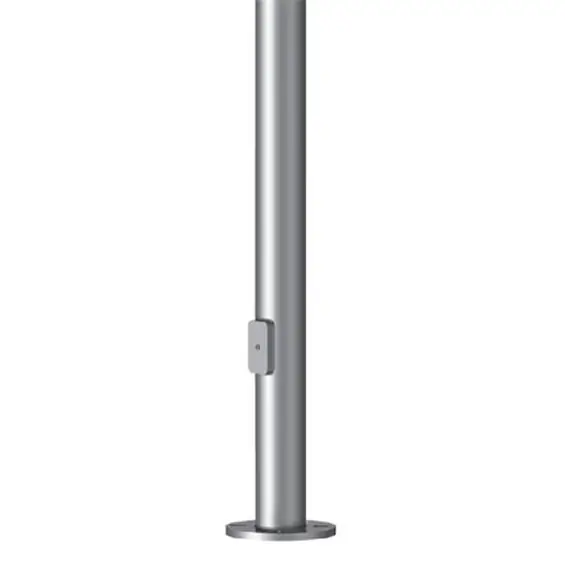
Steel poles today are most often used as lighting poles. With their help, they equip the lighting of roads, streets, courtyards of residential buildings, etc. In addition, such structures are often used as supports for power lines