2025 Author: Howard Calhoun | [email protected]. Last modified: 2025-01-24 13:10
Sheet metal processing often involves cutting blanks to size, forming edges by bending the sides at certain angles. Such work leads to the fact that all sorts of stresses arise in the parts, including compression of the inner bending line and expansion in the outer part. The hemming machine makes it possible to minimize these negative consequences. Its design is arranged in such a way that the bending force is manifested simultaneously along the entire length of the workpiece. In this regard, the deformation occurs synchronously, while the metal does not break, there are no places potentially susceptible to corrosion on it.
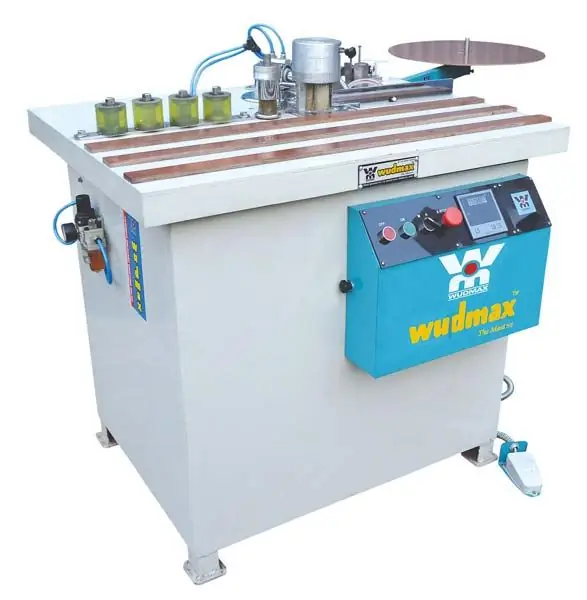
Varieties
Flanging machines differ from each other by the principle of operation and structural device. With their help, bending of sheets and edges from two millimeters is performed. The highest quality process is carried out on stationary modifications that are operated at metalworking plants. Compact and mechanical counterparts are focused on installation in private households and small repair shops. Alsothey are used directly on the installation of metal roofing, water supply or ventilation elements.
The equipment under consideration is divided into the following types according to the design features:
- rotational modifications;
- rotary options;
- Press action fixtures.
According to the principle of action, they are:
- manual hemming machines;
- mechanical models with rotary type flywheel;
- electromagnetic or electromechanical specimens;
- pneumatic;
- hydraulic.
Units with any drive can process black and galvanized steel, aluminum, copper. When bending painted blanks, the protective layer is not damaged. The main direction of work is the manufacture of complex structural elements and parts (chutes, boxes, stands, bottoms, special narrow profiles).
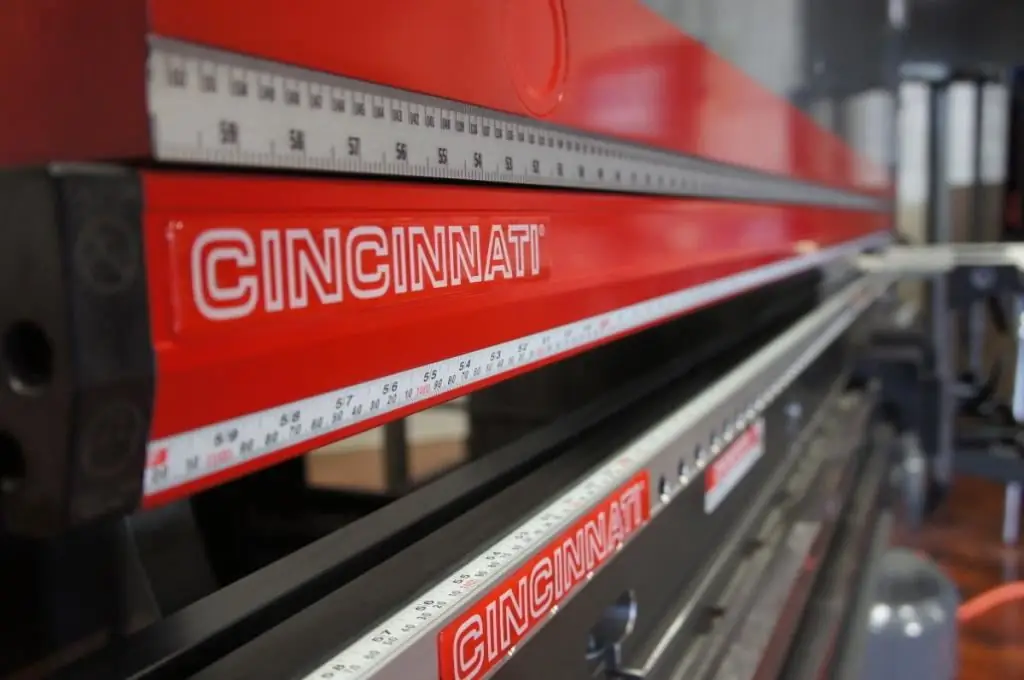
Device
The design of any bending machine includes a mandatory set of parts, depending on the functionality. For example, segment-type models are focused on metal processing along non-parallel lines. This allows the production of triangular, trapezoidal and segmental parts. Feed-through versions only bend the material in a parallel direction, since the pressure head and the bending beam do not move along the longitudinal axis.
The main structural elements of the equipment in question:
- skeleton (bed);
- rear desktop,which serves to install the workpiece to be processed, move it in the required direction and carry out basic operations;
- flexor and cutter;
- front adjustment supports to set the width of the workpiece to be cut;
- knife roller configuration, which is used to form the specified segments and align the edges;
- angular and sharp tires;
- flexor with goniometers;
- pressure beam;
- controllers responsible for adjusting the height of the board;
- drive and controls.
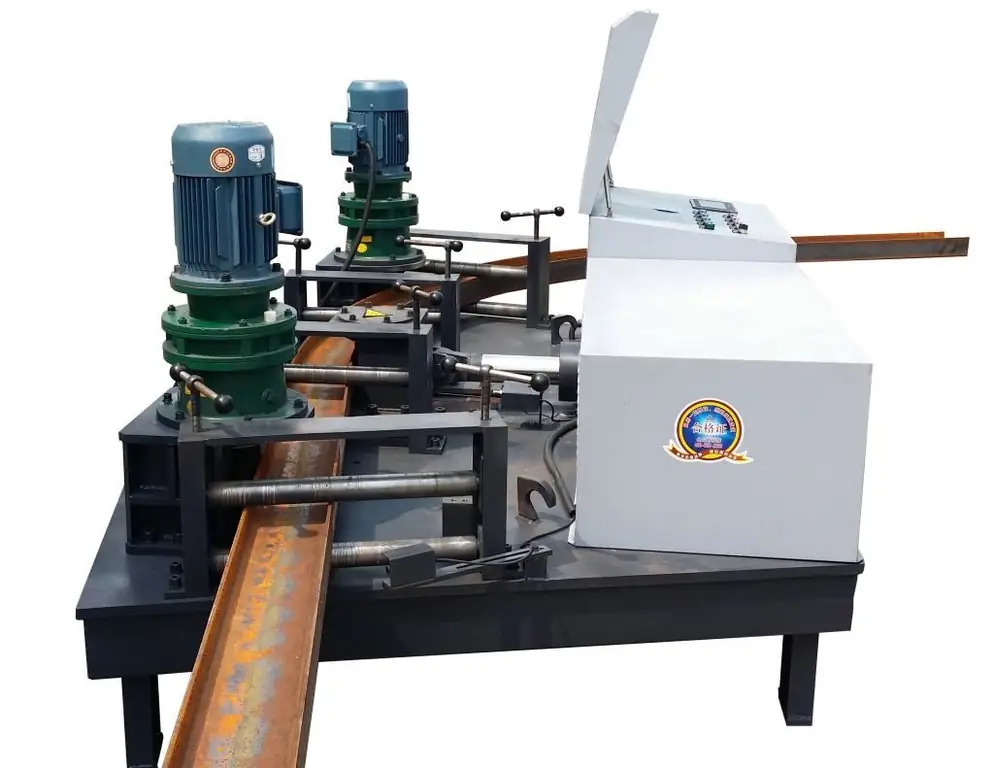
Working principle
The metal sheet is mounted on the table of the bending machine, pressed with a beam of suitable shape to the surface. The bending element rises, capturing the workpiece or edge being processed. The part is pressed against the tire, which plays the role of a kind of matrix, after which it is bent to the desired angle.
In manual models, the necessary force is applied using a special handle in the form of a lever. When processing metal with a thickness of up to one millimeter, excessive exposure is not required; a person with average physical fitness can cope with such a task. On the specified equipment, the edge is bent by 125-135 degrees, further fine-tuning (up to 180 °) is carried out by means of an eccentric coupler. For sheets two millimeters or more thick, equipment with hydraulic or other powerful drive will be required.
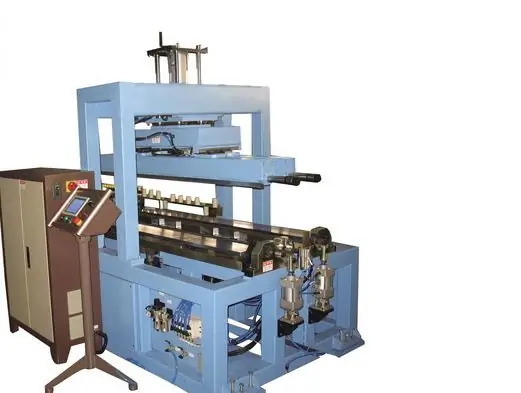
Industrial press brakes and machines
Kthis category includes multifunctional metalworking devices. They are often CNC-equipped and can be used for piece or large-scale production. Consider the features of the work of press-bending machines on the example of the IB-1424 machine. It is produced by the Nelidovo plant for the production of hydraulic presses.
This equipment does not belong to the most powerful category, however, it performs all the provided processes quickly and efficiently. This type of edge bending machines is capable of processing sheets and strips of various materials, develops a force of about 25 t/s. Key Features:
- rectilinear bending with a minimum bead height of 5mm;
- cutting blanks;
- hole making;
- processing profiles of complex configuration;
- Maximum piece length up to 2500mm.
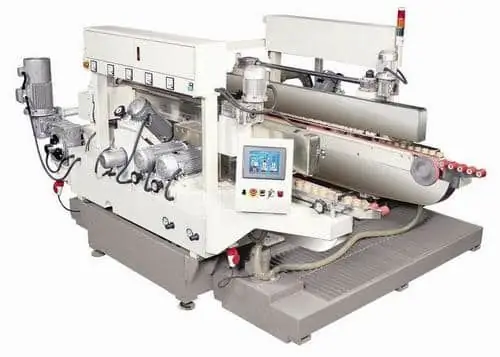
Features
To enable the processing of metal sheets of various thicknesses, bending presses are equipped with interchangeable punches that allow you to provide the required bending angle, regardless of the complexity of the profile. In addition, the equipment is equipped with special matrices that differ in width from each other. Replaceable elements are mounted quickly, reconfiguration of devices for a different type of product is carried out as quickly as possible.
The force of the machine is adjusted in a fairly wide range. In order to avoid the appearance of a critical parameter leading to deformation of the workpiece, special force tables have been developed. They provideinformation that takes into account the length of the bend line, the thickness of the material and the working radius. The hydraulic version differs from the rotary bending machine in smooth force adjustment, minimal noise, compliance with the calculated pressure throughout the entire technological process.
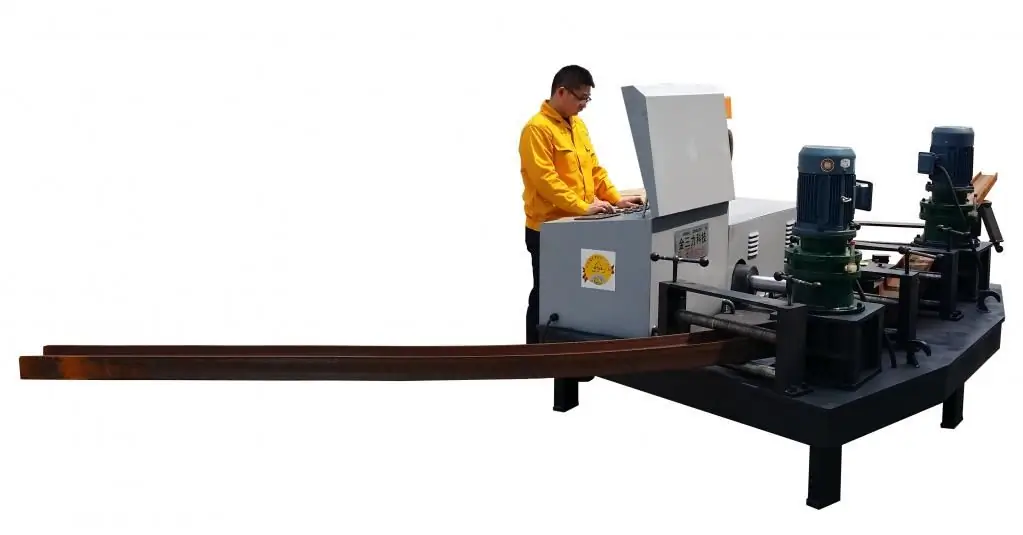
HDS Model
This is another popular hydraulic press brake. The unit processes metal blanks up to 3.5 millimeters thick, belongs to the middle class in terms of performance. The maximum length of the cut part is 3050 mm, and the bending of the edges is up to 1350 mm. Developed force - 16 MPa. Despite the fact that there is no numerical control, the press has a wide range of settings.
LGS-26 version
Description of edge bending machines will continue with a manual compact version, which is part of a series of equipment manufactured by the Lipetsk Profile Bending Plant. This unit is optimally suited for small workshops and field operation directly on the site. It is designed to work with metals, the thickness of which does not exceed 0.7 millimeters. The main purpose is high-quality and fast production of shaped parts, including slopes, ebbs, stands, skates, narrow strips and profiles.
When processing parts, the edge is bent by 15 millimeters at an angle of up to 180 °. Evenness of sheet cutting is guaranteed by the presence of rollers made of durable alloys in the design. The standard equipment of the unit includes:
- main mechanism withclamp;
- beam;
- bender;
- goniometer;
- cutting machine;
- frontal stops speeding up the process of cutting manipulations;
- set of spare knives.
The bending machine under consideration is a fairly practical and thoughtful design. It is quite realistic to use it as a prototype for creating a do-it-yourself bending machine. It is worth noting that all parts are made using standard metalworking tools and welding. In a small workshop, such a machine can be made at minimal cost. Assembled from ready-made parts, the unit will cost 2-3 times cheaper than purchased in finished form.
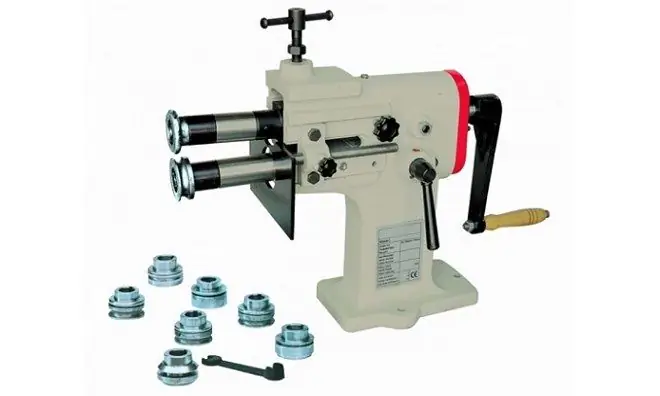
Result
Plate bending machines and presses greatly simplify a lot of metal construction and installation work. Due to the differences in design and purpose, it will not be difficult to choose the right equipment, taking into account the main use and price. For a home workshop, manual modifications that you can do yourself are quite suitable.
Recommended:
Electric locomotive 2ES6: history of creation, description with photo, main characteristics, principle of operation, features of operation and repair
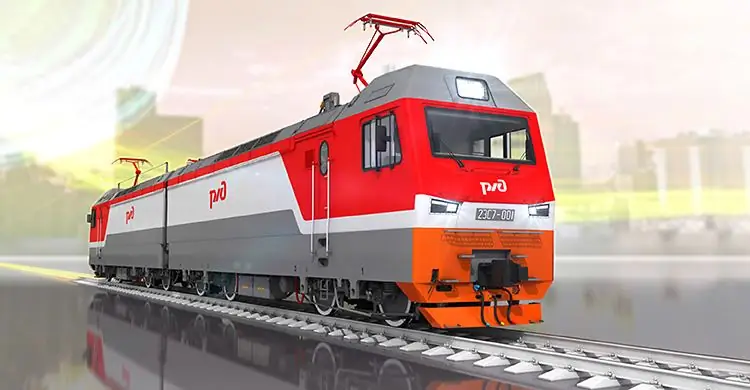
Today, communication between different cities, passenger transportation, delivery of goods is carried out in a variety of ways. One of these ways was the railroad. Electric locomotive 2ES6 is one of the types of transport that is currently actively used
Industrial flotation machines for wastewater treatment: types, device, principle of operation
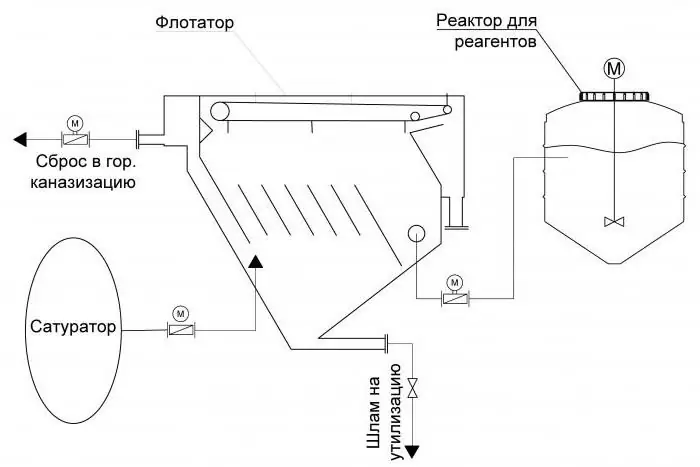
2017 has been declared the year of environmental protection in Russia, and therefore environmental education is one of the tasks for this year. Wastewater generated during the economic activities of enterprises contains a large amount of pollutants in concentrations exceeding the permissible and normative ones. As a rule, we are talking about heavy metals (iron, nickel, copper, lead, mercury, cadmium, etc.), oil products, suspended solids, aluminum, and surfactants. These substances, getting into water bodies, violate the norms
Differential pressure gauge: principle of operation, types and types. How to choose a differential pressure gauge
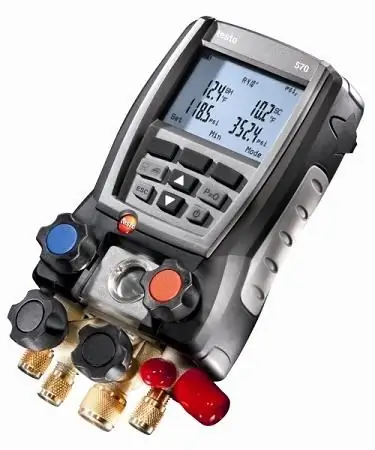
The article is devoted to differential pressure gauges. The types of devices, the principles of their operation and technical features are considered
AC machines: device, principle of operation, application
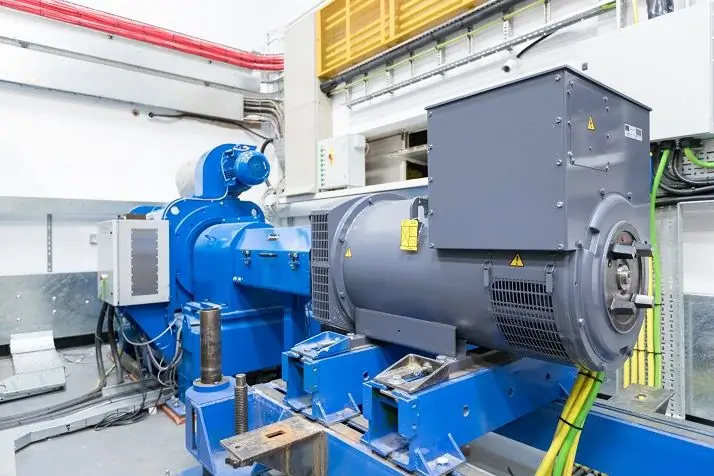
Electric machines perform the critical function of energy conversion in working mechanisms and generating stations. Such devices find their place in different areas, supplying the executive bodies with sufficient power potential. One of the most demanded systems of this type are AC machines (MCT), which have several varieties and differences within their class
Bending machines: types, description of designs, characteristics, settings
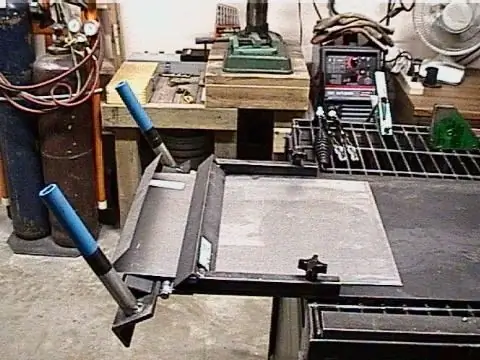
Bending machines: types, design features, application, photo. Description of machines, technical characteristics, settings, modifications