2025 Author: Howard Calhoun | [email protected]. Last modified: 2025-01-24 13:10
The whole surface of the grinding wheel is covered with a lot of hard particles. Simply put, this is the grit of the grinding wheel. These particles are usually distributed evenly over the entire area of the circle. Before proceeding with the choice of a circle for processing material, it is imperative to understand this characteristic.
Grinding wheels
The analysis should begin with the fact that you need to understand what a circle is. It is a cutting abrasive tool. It is worth saying that there are circles that are used for manual processing, as well as for working on machines. Naturally, the grit size of the grinding wheels of professional tools is selected as precisely as possible to ensure the most efficient processing.
There are quite a few criteria by which circles are divided into several categories, but the most important are abrasive materials and binding elements. According to this parameter, there are the following circles:
- silicon carbide grains;
- elbora;
- electrocorundum;
- artificial or natural diamond.
Here it is important to understand that it is the grain size of the grinding wheel that determines its main functional purpose. It is the abrasive material that cuts off the microscopic layer of the material. For its bundle, there are a variety of substances that can be both artificial and natural. Another feature of grinding wheels is the presence of a porous structure, which provides the roughness of the coating.
Grain overview
The choice of grit size of the grinding wheel depends on what requirements are imposed on the cleanliness of the surface to be machined. In order not to be mistaken, each circle has a special designation (marking).
If you know the markings, then choosing a suitable circle, in principle, is not difficult. It is very important to know that the grain size of grinding wheels for metal and wood coatings is significantly different, and therefore you need to pay attention to this fact when choosing a tool. If after work or during work, notches, cracks and other defects appear on the surface of the circle, then a mistake was made at the stage of choosing the grain size of the working tool. How to determine this parameter correctly? Two factors must be taken into account: the required purity of processing, as well as the mode of operation, which plays an important role.
Currently, 60, 100 and 120 grits are the most commonly purchased tools.
Circle choice and recommendations
If it is necessary to perform surface grinding, which is actually carried out with the endwheel, the grit should be from 16 to 36. Cylindrical rough grinding is performed using a wheel with a grit index of 24-36. The grit of the grinding abrasive wheel for round fine grinding should be from 60 to 100. There is such an operation, which is called the finishing of a multi-blade tool, which is performed by a wheel with a grit of 170-220. Fine grinding is carried out with a wheel characteristic from 180 to 320. There is a procedure called thread grinding. The essence of the process is clear from the name, and to perform the operation, the grain size of the circle is from 100 to 280.
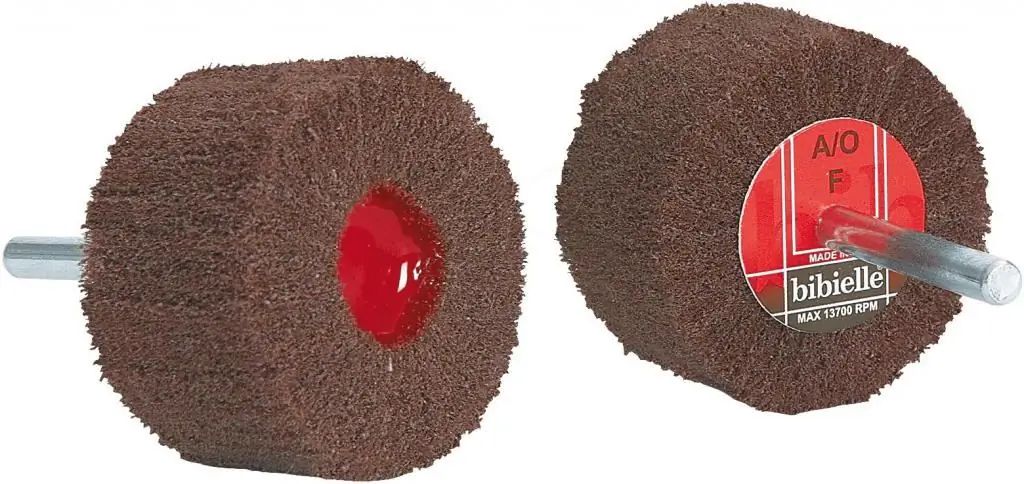
There is an easier way to define graininess. Semi-finishing or finishing of the material requires the presence of fine grain fractions. Roughing, on the contrary, is carried out with coarse grains.
Marking
The described tool has quite a lot of parameters, which are usually indicated in its name. Grit marking of grinding wheels is not specified separately, it is always included in the full wheel marking.
- The circle type is always listed first.
- The second important parameter is the dimensions of the device.
- The following indicates the type of abrasive used to create the wheel coating.
- Immediately after this, the grit designation of the grinding wheel is indicated.
- The marking always refers to the hardness of the material.
- Link structure.
- Type of bundle.
- Maximum working speedcircle.
- Accuracy class.
- Unbalance class.
The listed 10 items include both marking the grit size of the grinding wheel and specifying other parameters.
Distribution of circles into groups by grit
There are several groups of tools that differ in graininess. The group of large fixtures includes those tools that are marked 320 b, 250 b, 200 b, 160 b, 125 b and several others. The next group is the middle one, which includes such designations as 50 k, b, 40 k, b, 32 k, b, etc. The fine grit group includes such grades as 12 k, b, 10 k, b, 8 k, b and 3 k, b. The last group includes circles with the designations 5, 4, 3, as well as M63, M50, M40, M28.
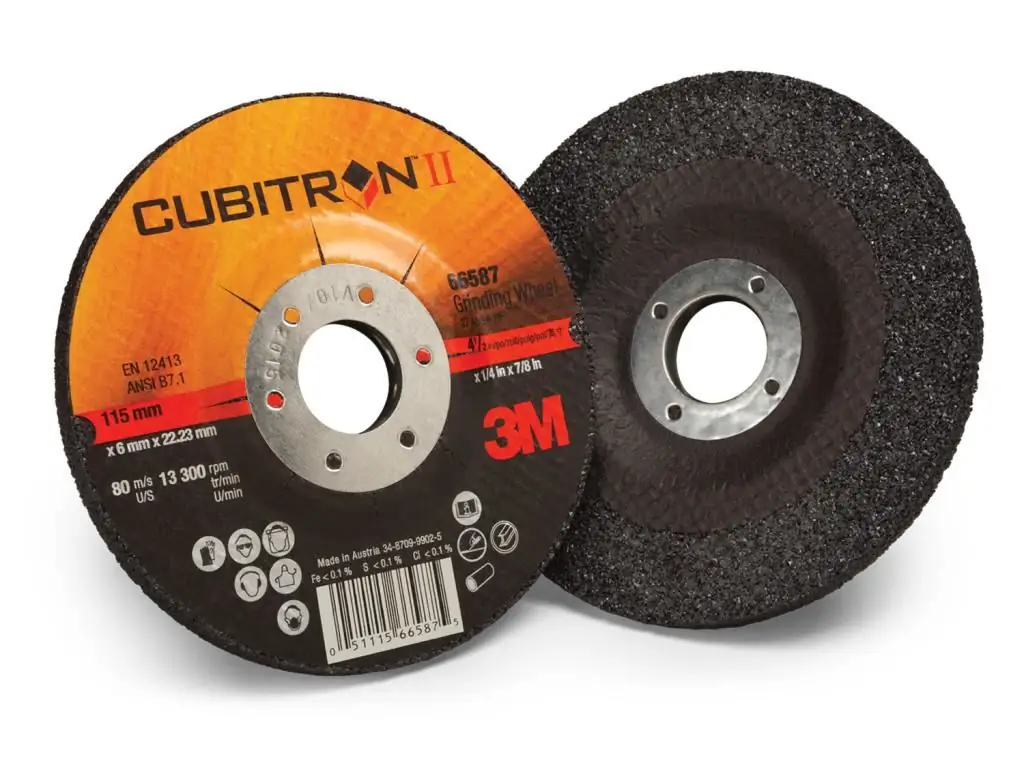
Using a tool according to the degree of grit
When choosing the right grit, it is important to know that varying degrees of grit affect the amount of material removed. For example, the high grain size of the flap wheels will allow even large metal pipes to be processed successfully. And when it comes to wood processing, you will have to purchase a wheel with much less abrasive material.
Various degree of this characteristic is necessary to enable preliminary operations when peeling with a large depth of cut is required. Wheels with a different degree are well suited for wiping operations, and a separate group is required for working with copper, brass and aluminum.
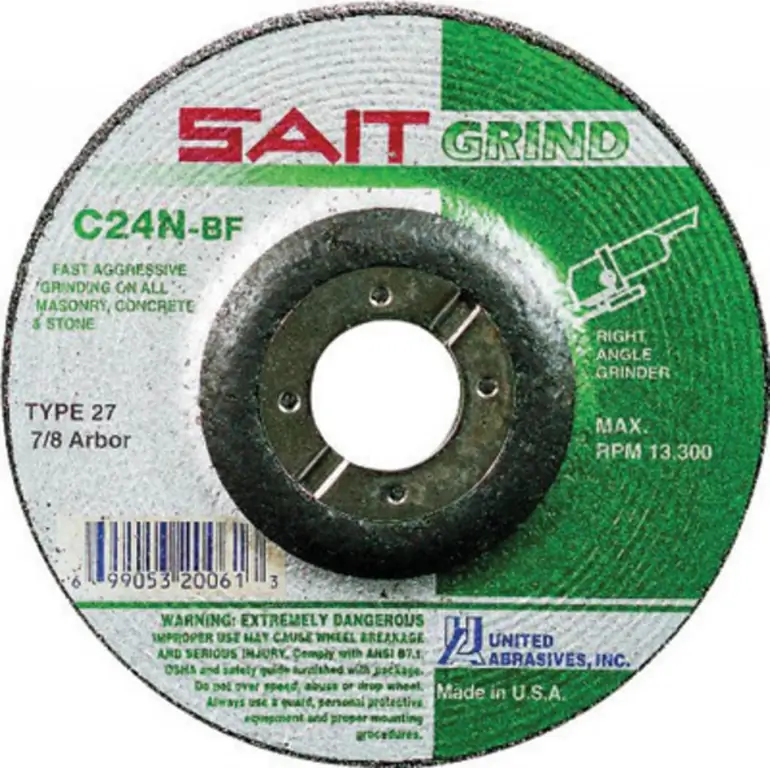
Coarse wheel grit is most often required when grinding is carried out with the end of the wheel. In addition, they are also used when internal grinding is necessary. Most often, such devices are used on machines that are characterized by increased rigidity and processing power.
Medium and fine grit wheels are used for operations such as:
- hard metal alloy grinding;
- machining hardened steels;
- surface finishing;
- sharpening of other tools.
Medium-grained and fine-grained wheels are also used when very high precision is required from the job. At present, this characteristic must comply with GOST R 52381-2005. This GOST grinding wheel grit has replaced the previous document with the number 3647.
The difference between the designations according to GOST
It is worth saying that you should know the marking from both documents, since it still remains on many old samples. In accordance with GOST 3647-80, the granularity of the circle is indicated in units that are equal to 10 microns, for example, 20=200 microns. If the composition contains micropowder, then the letter M is added to the micron. As for the new sample, the grain size of the circle is indicated by the letter F with a number.
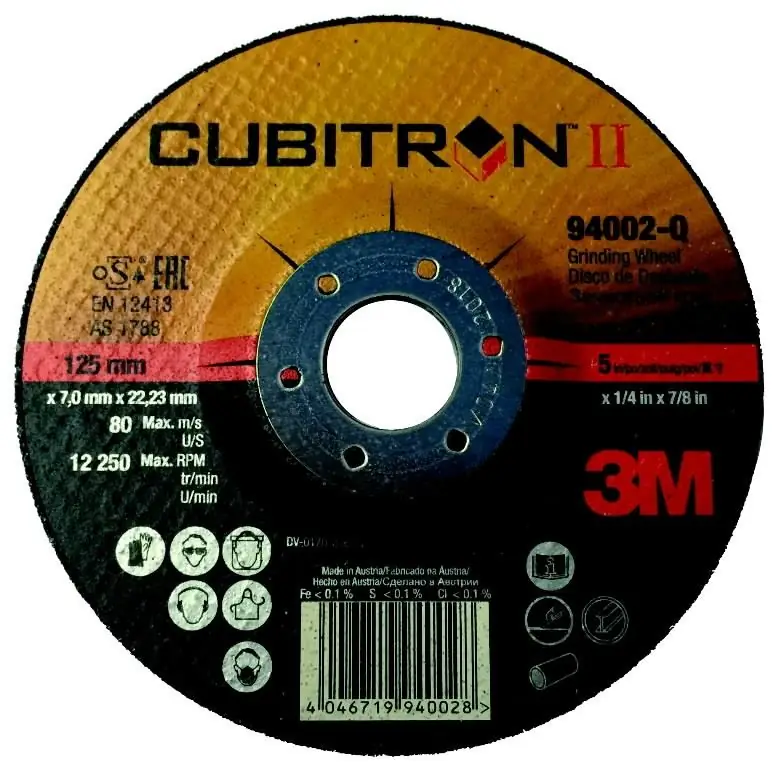
Let's say, according to the old standard, the grain size of a circle is indicated by the number 200, which on average is 2500-2000 microns. According to the new GOST, the same circle will be designated as F8 or F10. Exemplarythe size of the first circle is 2460 µm, and the second is 2085 µm.
Tool types
As it has already become clear, the cleanliness of the surface to be sanded depends on the grain size of the abrasive material. However, it is worth saying that there are also different grains in their form. They can be presented in the form of intergrowths or small crystalline fragments with an arbitrary shape. There are high-quality grinding wheels, which not only have a good grain size, but the grain itself is presented in the form of a full-fledged crystal. If we talk about the parameter of the grain itself for the grinding wheel, then it is worth highlighting three main parameters: thickness, width and length of the grain.
However, it is immediately worth noting here that experts in this field most often use width as the main and only characteristic. Depending on the size of the grain, it will depend on how much material the wheel can remove in one pass, and hence the overall performance of the grinding wheel.
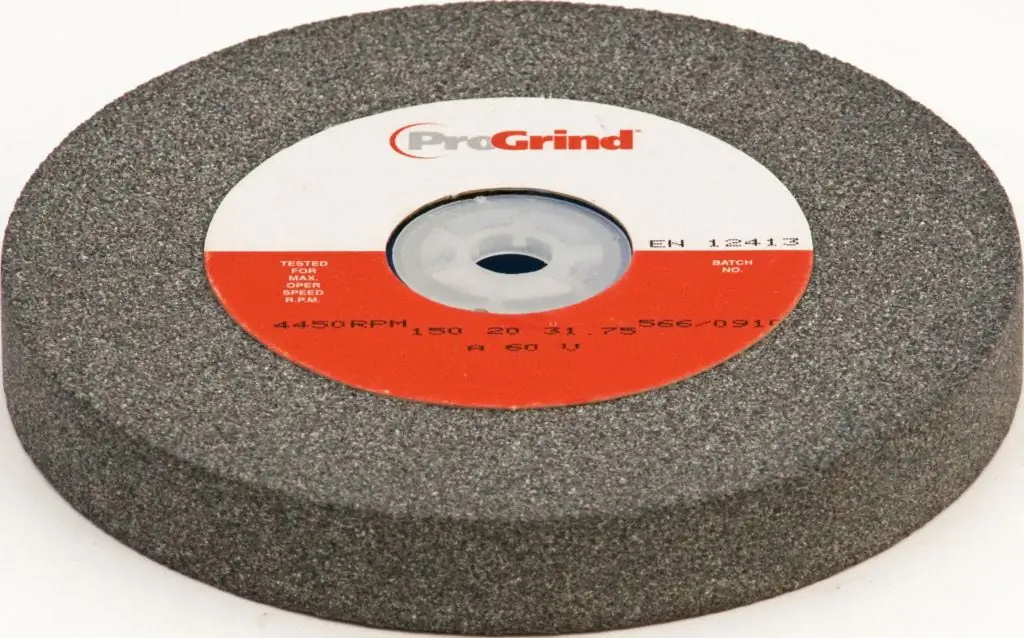
If we talk about deciphering the labeling of the material, then it is quite simple. The essence of graininess marking is as follows: the prefix indicates a numerical indicator of the characteristic. The higher the specified number, the higher the quality of the abrasive material.
Diamond Tools
The most expensive and high-quality wheels for grinding material are diamond. These devices have such a thing as the concentration of the diamond layer, which is expressed in the number of diamonds per cubic millimeter of powder.abrasive layer. This parameter is considered one of the main ones, as it affects the efficiency and economy. It is worth saying that the indicated concentration directly depends on the grain size of the diamond grinding wheels. In other words, the higher the grit index, as well as the harder the material to be processed, the number of diamond crystals in the abrasive layer will also increase.
Today, several groups of diamond wheels are produced. They can have 150-, 100-, 75-, 50- and 25% concentration of diamonds. Currently, a 100% concentration is considered to be the presence of 4.39 carats. One carat is equal to 0.2 grams contained in 1 cubic centimeter.
Grit for diamond wheels
Grinding for diamond grinding wheels is the size of the diamond grains themselves in the abrasive layer or intergrowths of crystals. The three main indicators are the same three indicators as for ordinary grains, but here, too, only the width is taken into account. Grit for diamond wheels is selected based on what kind of roughness should be in the end, on the type of material and on the size of the allowance.
Earlier it was said that with a decrease in the size of the grains, the quality of grinding increases. This is true, however, fine grain is not always preferred. The fact is that the use of such tools leads to their strong clogging, and the treated coating can be cauterized during the grinding process. If we talk about productivity, then small grains also negatively affect this parameter.
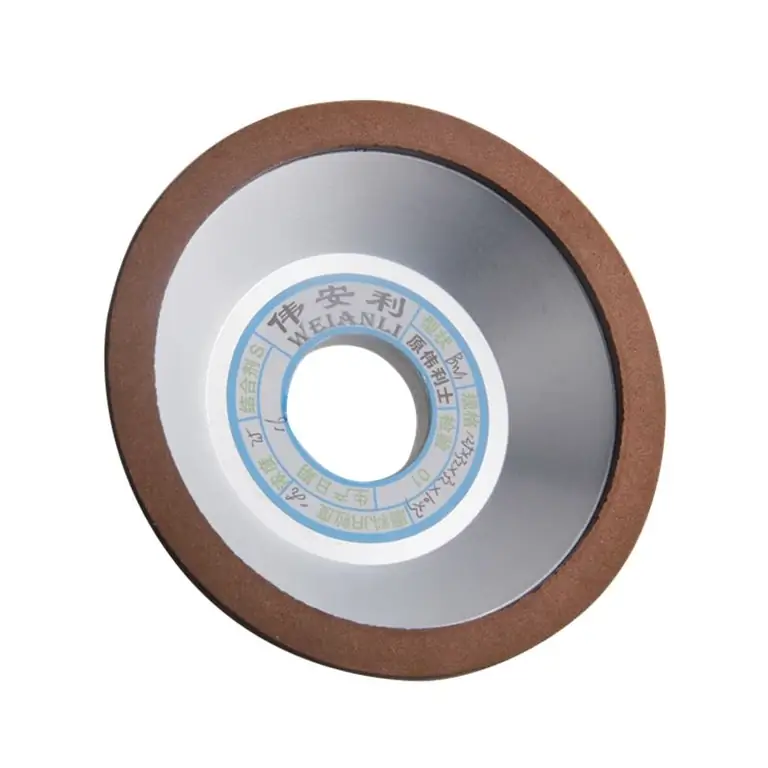
Today, there are four main categories into which diamond grinding wheels are divided, depending on their grit. Fine 100/80, Medium 125/100, Coarse 160/125, Larger 200/165.
Fine grit wheels are used for finishing other tools such as knife blades, chisels or other tools. The middle group is well suited for maximizing the sharpness of any cutting surface, while the larger wheels are already applied directly to the top layer.
Wood circles
Sandpaper is considered the most suitable material for wood processing. However, circles may well have both polymer and metal brushes. In addition, you can use traditional tools with grains. If it is necessary to carry out a large peeling of wood, then a grit from 40 to 60 will be required, for medium cleaning, the figure increases by 20 and ranges from 60 to 80. The finest grit is from 100 to 120 and is used for finishing surface grinding.
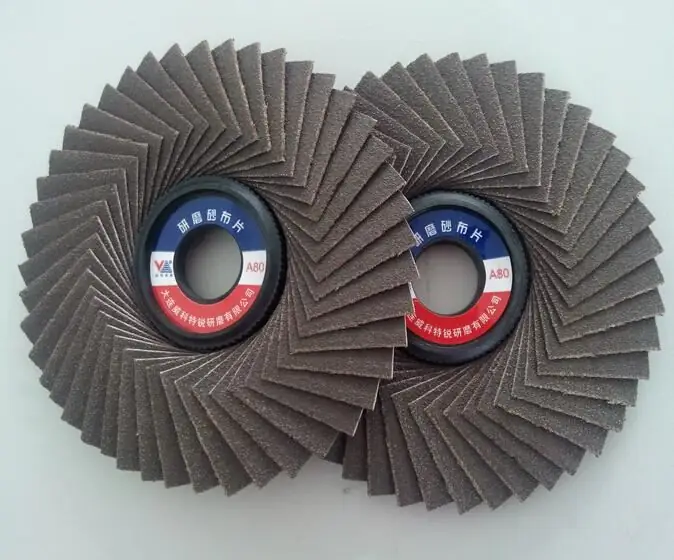
In addition, as with metal, you need to choose the right grit for wood, depending on what operation will be performed.
Recommended:
The size of the dollar in millimeters. Do banknotes vary in size?
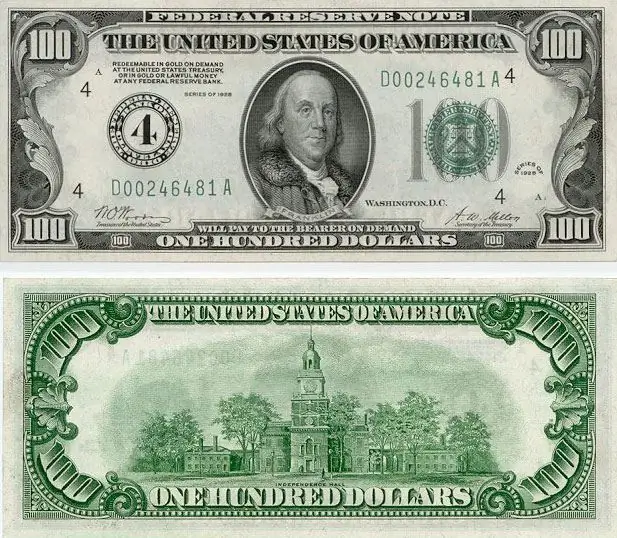
What is the size of the US dollar in millimeters? Does the size of a banknote depend on its denomination? What is the rarest currency in the United States? Why is 1 dollar the most common in the world, what is the reason for this? Circulation of the monetary unit outside the country and within it
Sanding paper: GOST, size, marking, types, manufacturer
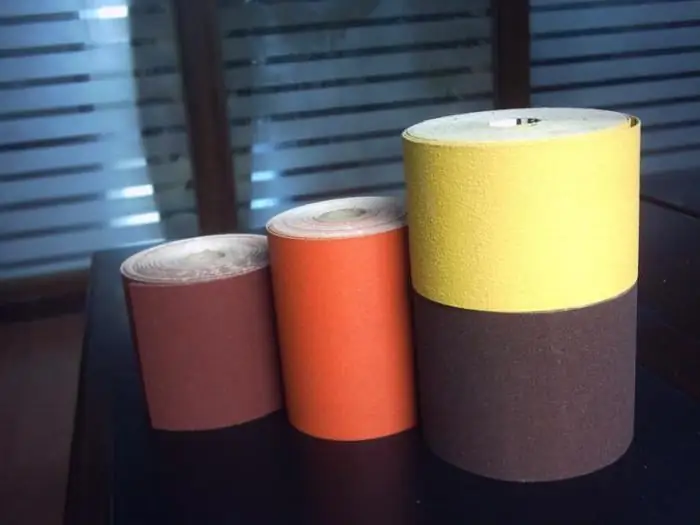
During construction or some other work, sometimes it becomes necessary to make the material smoother, remove all hooks from it, etc. It is for such purposes that sanding paper is used
Wheel sets of wagons. Malfunctions of wheel sets of railway wagons
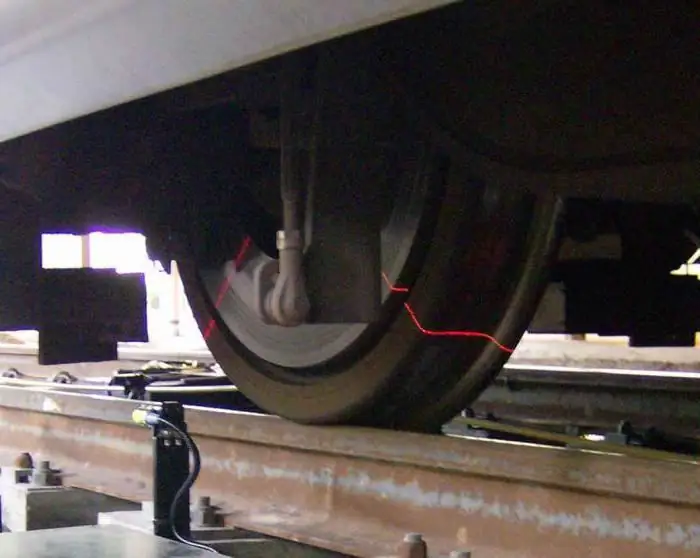
The article is devoted to malfunctions of wheelsets in railway transport. Describes common types of wear and deformation, as well as the nuances of maintenance and repair
How to choose the right business card size, paper and design?
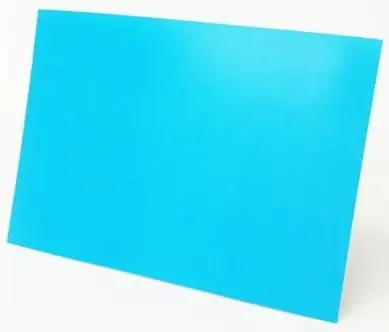
This article explains how big a business card should be, what paper it can be printed on, and how to choose the right design to reflect the essence of your business
How to choose a manicure table: tips and photos. manicure table size
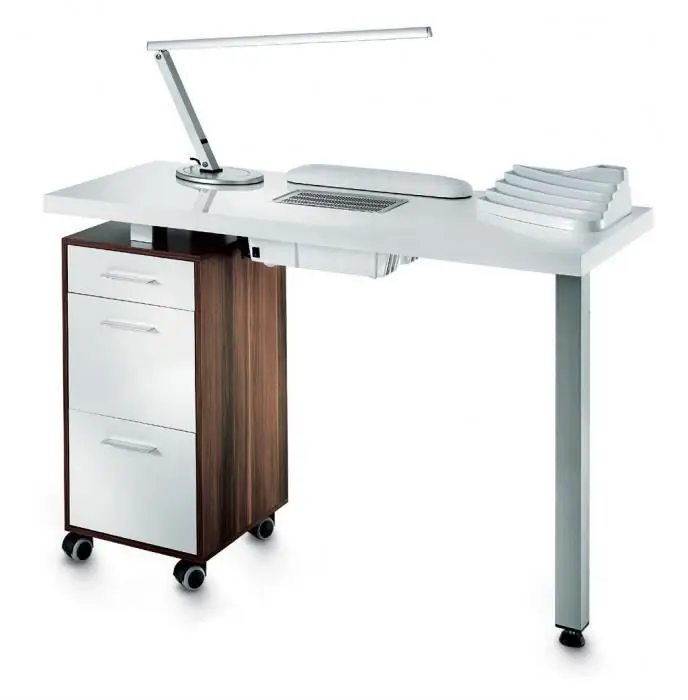
Intending to take up nail services, the manicurist meticulously chooses items for his salon. The size of the manicure table plays a decisive role when buying, depending on the size of the room. How to choose it and what to look for - we will tell in our article