2025 Author: Howard Calhoun | [email protected]. Last modified: 2025-01-24 13:10
Production strategy - a long-term program of actions adopted by the company related to the creation of products, their introduction to the market and sale. The object of the strategy is the company itself, as well as the management of production. The subject is relations of a managerial, technical, organizational nature. The development of the production strategy should proceed in accordance with the overall strategy of the company. It must also meet the foundations of the company, its goals and objectives in both the short, medium and long term development.
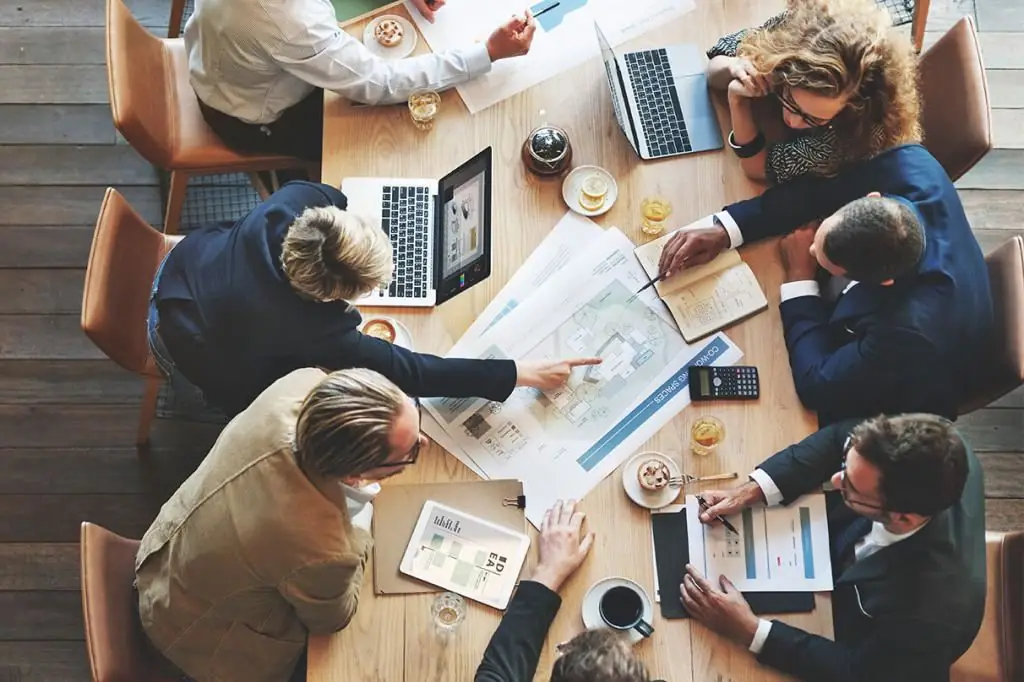
Strategy concept
There are many meanings for this term. In management, a strategy is a certain model of actions that is designed to analyze and achieve specific company goals. The strategy includes sequential decision making that is used for variouslines of business.
In most cases, it is chosen for a sufficiently long period of time, included in various programs and practical actions of the company, in the process of their implementation, the strategy is implemented. Any strategy requires a lot of time, resources and labor, so it is rare that a company can afford to change it often, perhaps only slightly adjust.
The concept of production strategy
In management, there are different types of company strategies. The production strategy is considered to be a program adopted for a long time ahead, which determines the company's actions to create, market and sell products. Strategic actions can be taken in the following areas of the company:
- improving the organization of production;
- improvement of production infrastructure;
- production management;
- product quality control;
- capacity control;
- organization of favorable relationships with the company's counterparties: suppliers and other partners;
- use of production staff.
Basic Strategy
In management, strategy is about finding a balance between the volume of products that a company produces and the production capacity of the workforce involved. It is important to consider points such as:
- necessary level of labor resources for the stable operation of production;
- sufficient qualification of the workforce;
- required technical level for a continuous production process;
- availability of opportunities to upgrade production equipment;
- creation of conditions and the possibility of emergency reconfiguration of equipment, in case of possible changes in terms, as well as volumes of production orders.
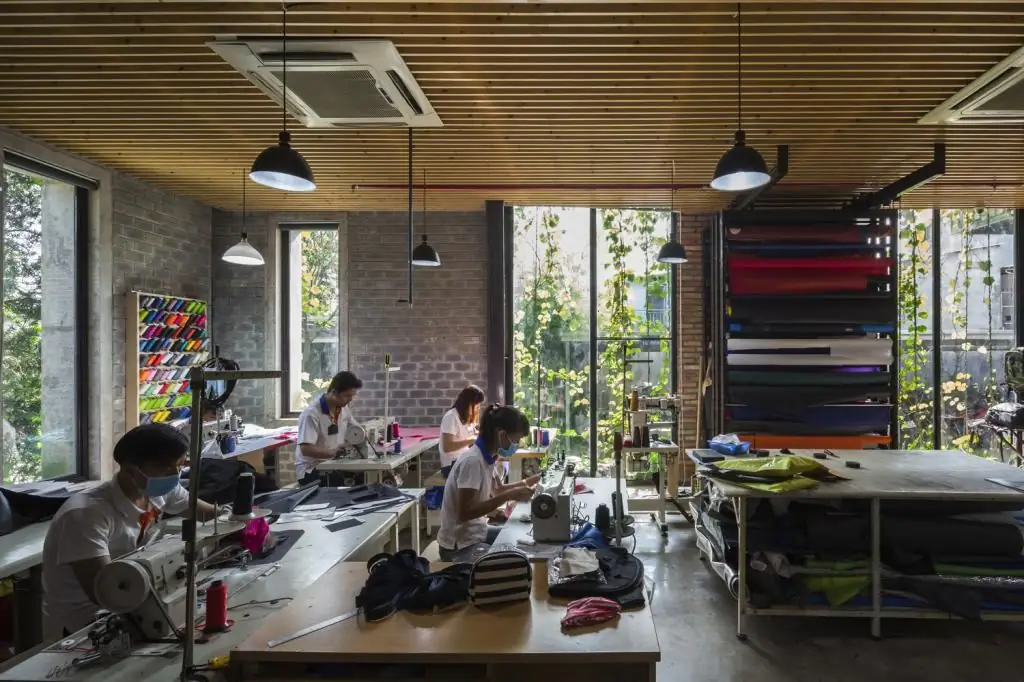
Full demand strategy
The production strategy of the enterprise exists in several alternatives.
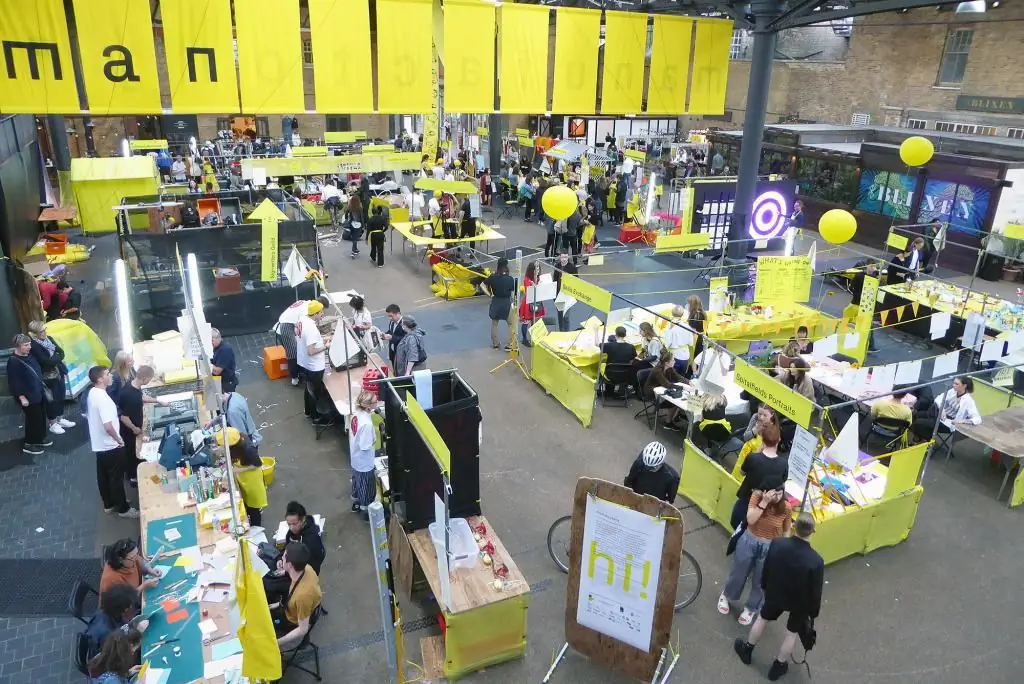
With a strategy to fully satisfy consumer demand, the company strives to produce the quantity of products that is required in the market. At the same time, with minimal stocks of products in warehouses, rather high production costs are observed due to possible fluctuations in output.
The advantage of the strategy is the ability to keep the stock of material and production resources at a minimum level.
Production of goods depending on the average level of demand
Adhering to this strategy, the company produces an average volume of products. When demand falls, the manufactured product goes into stock, as soon as the demand for the product increases, it is satisfied at the expense of the accumulations that were made earlier.
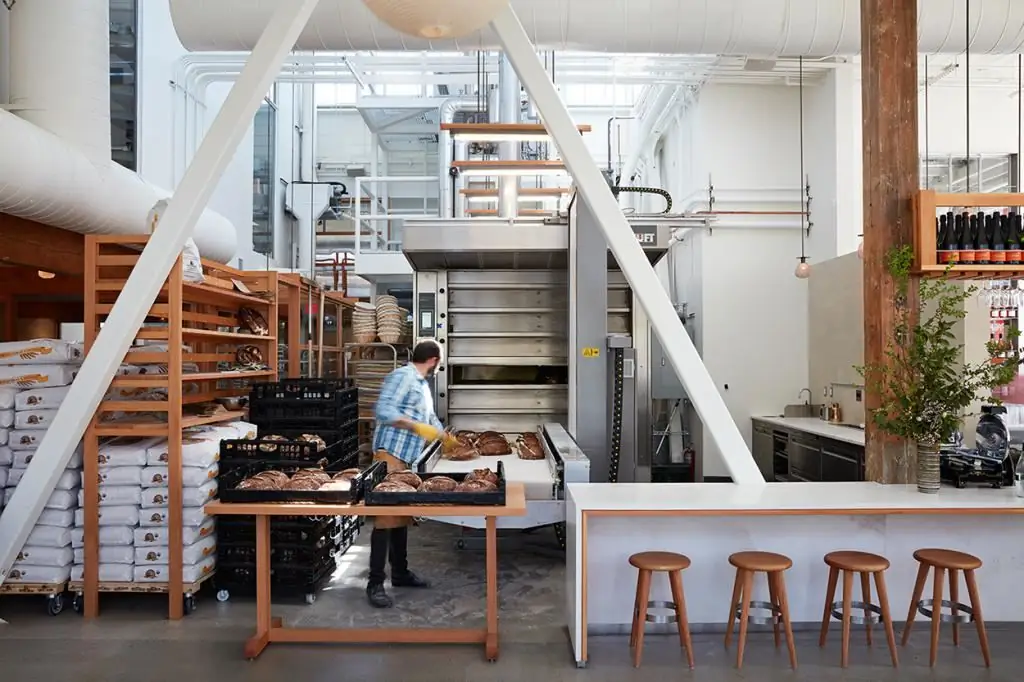
The advantage of this type of strategic model is that production is involved on an ongoing basis, no additional funds are spent on changing the volume of manufactured products. Companiesnor does it have to keep additional resources to increase the level of productivity in order to be able to meet the needs of all customers at the peak of demand. The strategy also has disadvantages, namely, the accumulation of excess stocks of materials during periods when demand is balanced at the lower limit.
Producing goods at the lowest level of demand
The company, adhering to this production strategy, puts on the market the volume of products that corresponds to the minimum fixed level of demand. The missing volume of demand is covered by goods produced by competing companies. This strategy is also called the pessimist strategy.
Also, the company can subcontract, which will produce additional volume of products to meet consumer demand. The advantage is the fact that the company, without producing a surplus of products, does not generally lose the number of customers. And also during periods of low demand does not have excess balances in warehouses. The disadvantage is the increased cost of production through subcontracting. Since the cost of additional volume will be higher, which means that the profit is less than if the company itself produced the required volume of goods.
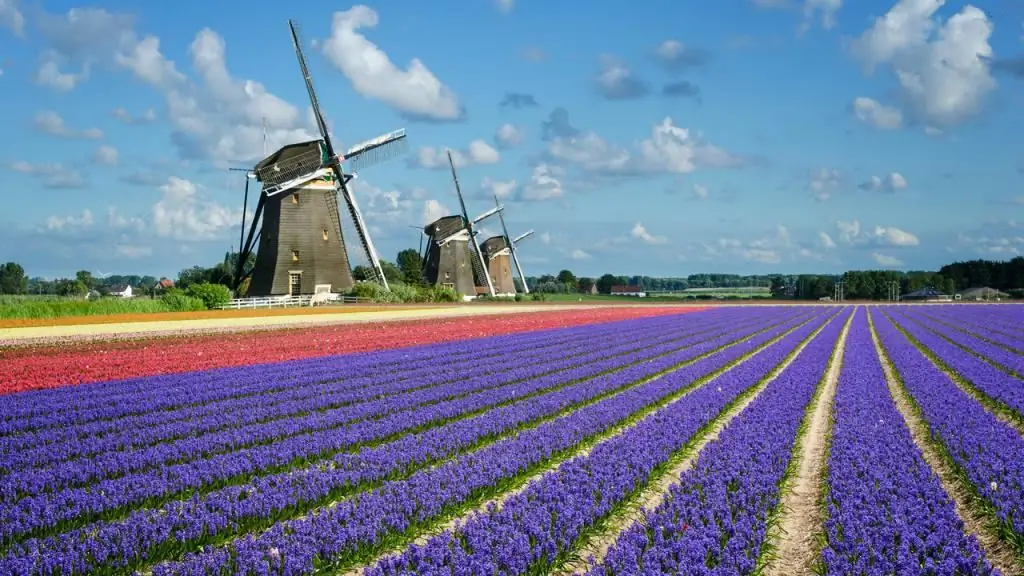
An example is a cut flower growing company. During the year, the volume of output fluctuates approximately at the same level with small bursts, but once a year there is a period of increased demand - March 8th. In order not to have too muchproduction of products with a short life within a year, the company has a small production capacity, which is not enough during the holiday period. To do this, a subcontractor is involved in February to fulfill the required volume of holiday orders. The company, thanks to the involvement of a subcontractor, fully fulfills the increased volume of orders from its own customers, who also make purchases throughout the year, but in other volumes.
Production location strategy
This strategy is mostly used in large companies that have developed cooperation within the company. When developing a production strategy, an enterprise should consider the following factors:
- what are the necessary transportation costs if there are remote branches;
- how skilled the workforce is;
- are the economic benefits offered by the management of the company's location area available;
- availability of sources of raw materials, semi-finished products and materials.
Production strategy
The concept of the organization's strategy lies in the fact that the company puts a focus on the consumer. This is determined by the following distinguishing features:
- indicators such as production volume, product quality, assortment and delivery time by the company are set depending on the forecasts of customer needs for future periods;
- goods are delivered to sales outlets at the right time and in the right quantity.
Organization strategy programsproduction
The program called production synchronization aims to determine the set of actions required to organize a system that can quickly respond to changes in consumer demand. To do this, it is necessary to establish the simultaneous receipt of all the necessary components and synchronous production and installation.
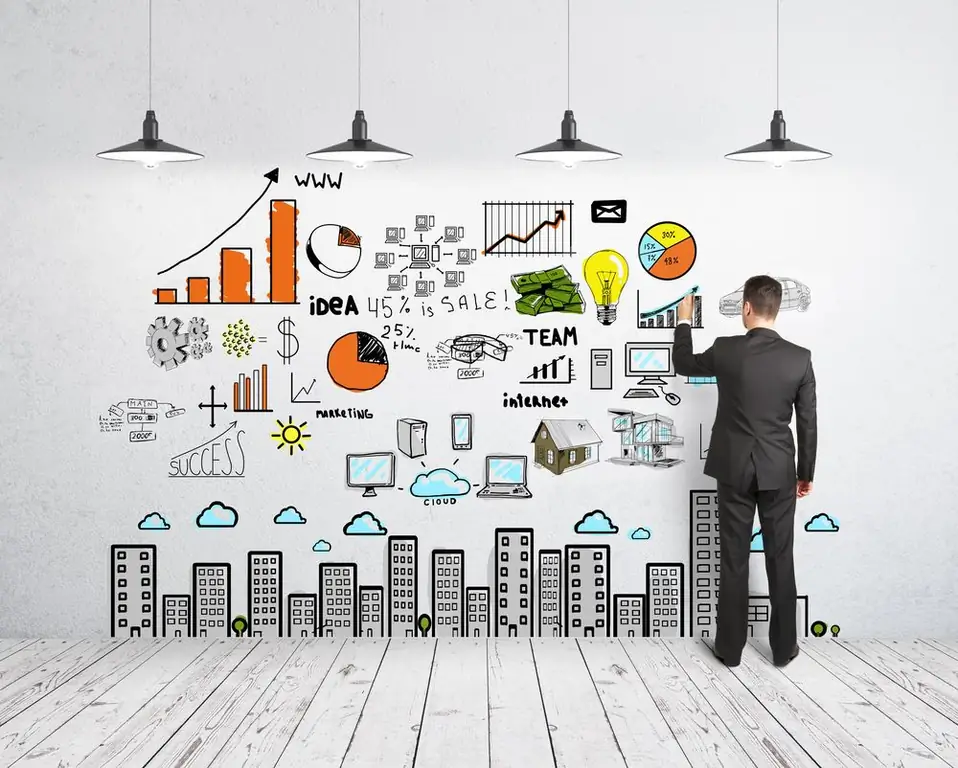
The program involves the implementation of the following strategic decisions:
- necessary to define methods to achieve synchronization of each individual stage of production;
- creating rules for the proper organization of synchronous production;
- Creating alternative delivery methods for the program.
The material flow management program is a work that is interconnected with each other, forming an integral system of material flow management. To carry out strategic decisions on the implementation of the program, you must:
- justify the methods of the production logistics system;
- develop systems for end-to-end material flow management, including both the procurement stage and the production itself, and product sales.
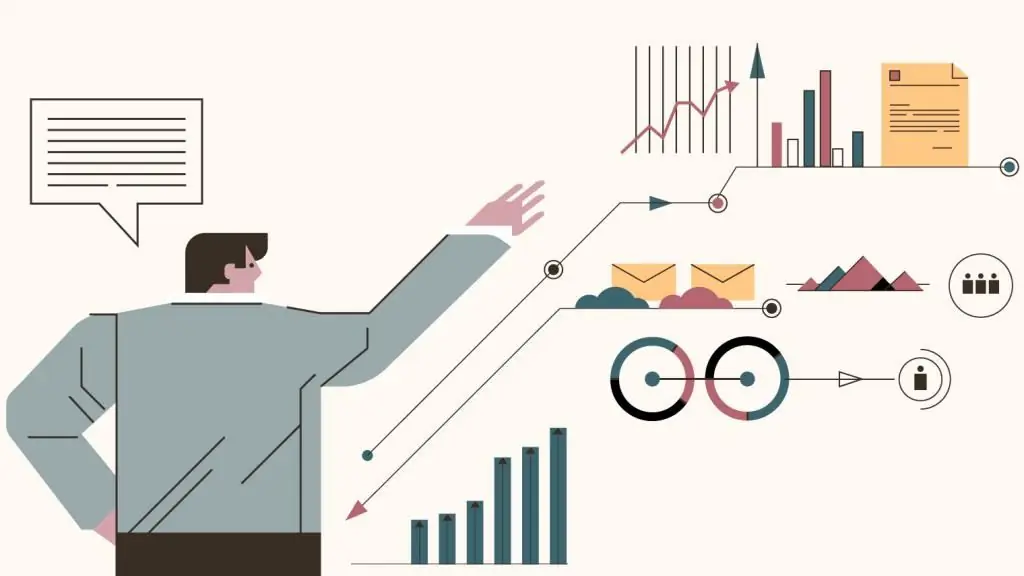
The program to increase the flexibility of production from the organizational side assumes the integrity of actions that establish and connect organizational, economic and technical solutions aimed at the formation of flexible production. To implement the program you need:
- determining boost methodsorganizational flexibility;
- analysis and development of a methodological approach to the formation of flexible production.
Recommended:
Functional strategy is The concept, types and role of functional strategy in management
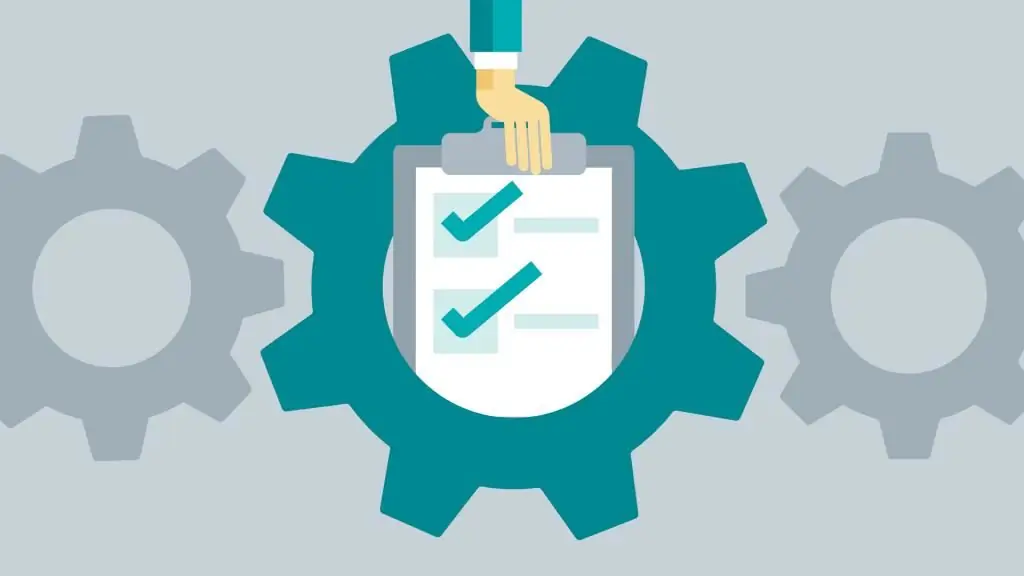
A well-formed functional strategy is one of the most important elements of the structure of the company itself and a guarantee of high efficiency. In order to properly plan activities and determine priority areas, it is necessary to accurately divide the powers, responsibilities and goals for each department and the employees themselves
Personnel policy and personnel strategy: concept, types and role in enterprise development
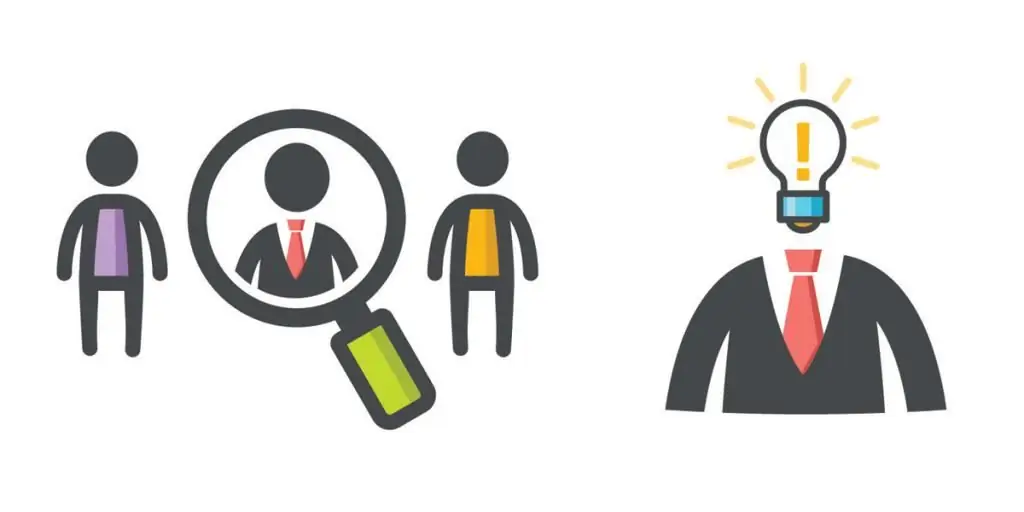
Now the personnel management function is moving to a new qualitative level. Now the emphasis is not on the execution of direct instructions from line management, but on a holistic, independent, ordered system, which contributes to improving efficiency and achieving the goals of the organization. And this is where HR policy and HR strategy help
Production and production systems: concept, patterns and their types
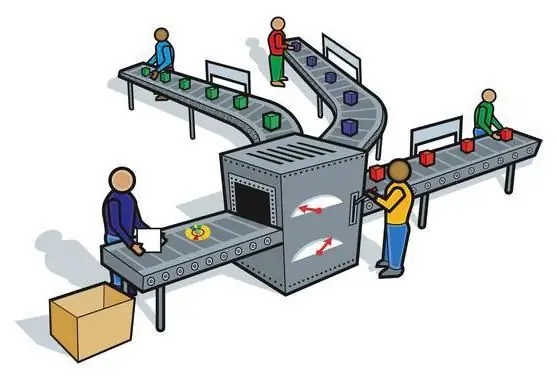
Production systems are structures that involve people and equipment working together. They perform their functions in a certain space, conditions, working environment in accordance with the tasks
Insurance: essence, functions, forms, concept of insurance and types of insurance. The concept and types of social insurance
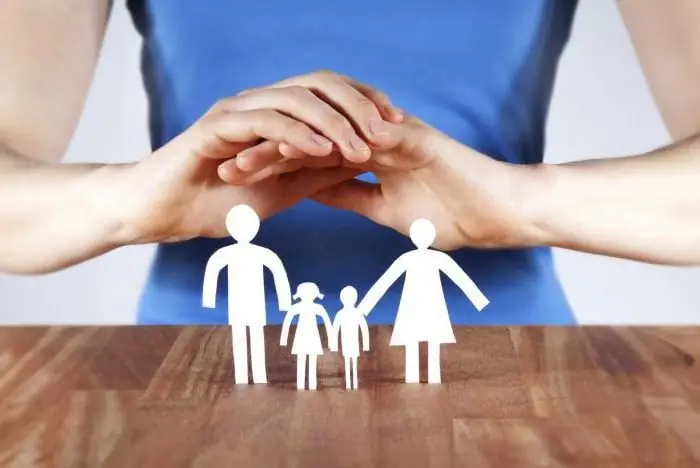
Today, insurance plays an important role in all spheres of life of citizens. The concept, essence, types of such relations are diverse, since the conditions and content of the contract directly depend on its object and parties
Differentiation strategy is Advantages and disadvantages of the strategy
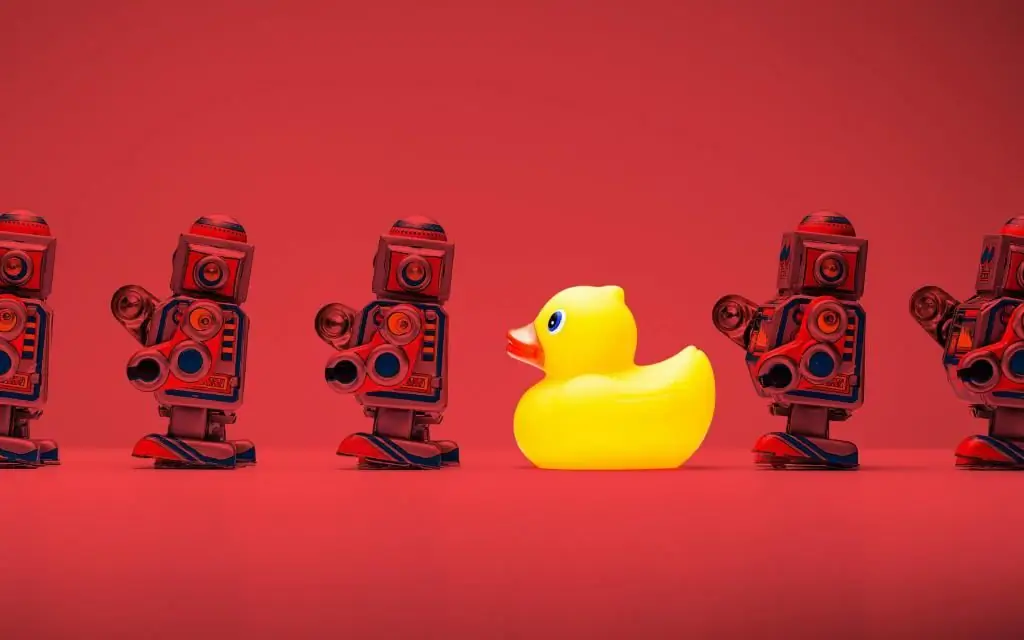
Strategy of differentiation is one type of strategy aimed at gaining an advantage over competitors. At the same time, the activity of the enterprise is aimed at providing more benefits to consumers by offering high-level goods, along with a full range of additional services, while the prices are justifiably high