2025 Author: Howard Calhoun | [email protected]. Last modified: 2025-01-24 13:10
New technologies for processing solid materials allow you to quickly and efficiently deal with almost any structure. Metal can be easily cut with abrasive and laser devices. Even traditional mechanical heads with diamond discs provide high-quality cutting of thick sheets. One of the most effective ways to solve such problems is cutting metal with plasma. The photo below illustrates this process.
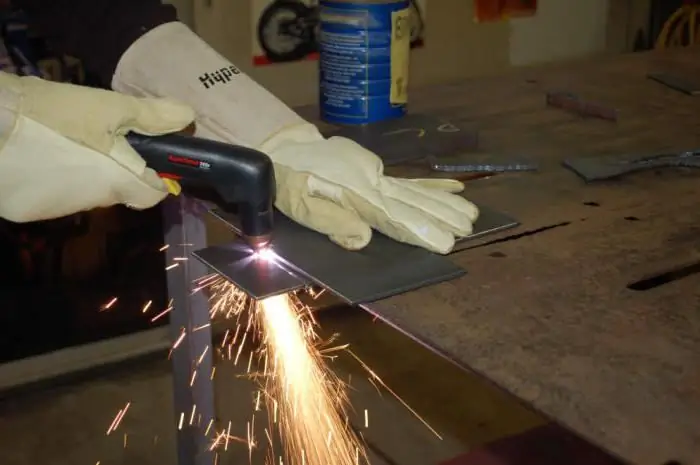
Technology overview
The technique is specially designed for metal processing without the use of saw tools. Like other thermal cutting techniques, this method consists in creating a cut in the structure of the material by pointing the beam to the work area. Direct plasma cutting is performed by thermal radiation, the source of which is a special tool. As a rule, this is a machine equipped with a plasma torch.
In general, the process resembles classical welding, but there are also fundamental differences. For example, blowing out air currents as a result forms a cavity with a molten mass. The substrate prepared in this way is more pliable, so plasma cutting allows the operator to cut with high precision, regardless ofworkpiece parameters.
Application of plasma cutting
Plasma processing equipment allows you to perform operations with workpieces from non-ferrous and ferrous metals. Also, depending on the device, the user can cut alloys and refractory workpieces with a thickness of about 40 mm. This technology is successfully used in art workshops. In part, this area of \u200b\u200buse of such tools can be compared with forging. Specialists make original decorative items for decorating gates, fences and furniture. Making objects with a curved cutting line also allows plasma cutting. The photo below shows an example of curly processing.
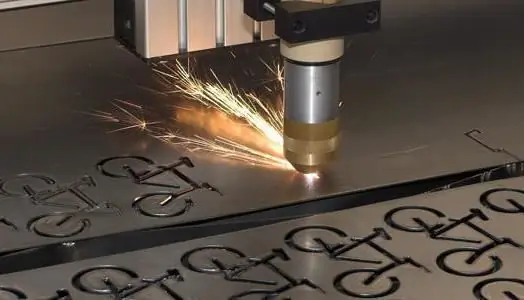
In addition to creative areas, the method is used in production, as well as in the construction industry. Plasma can process any metal that conducts electricity. In some areas, it is not so much the cutting of workpieces that is important, but the processing of the edges. Similar operations are also performed by plasma cutters.
The principle of the plasma cutter
The process begins with the fact that an electric arc is formed between the workpiece and the electrode in the plasma cutter. Sometimes a separate ignition occurs in contact between the nozzle of the apparatus and the electrode. The formation of a plasma flow is realized due to the gas supplied to the head of the device. Further, under high pressure, an electric arc is generated with a temperature regime of about 15,000 °C. Depending on the characteristics of the material, one or another gaseous medium is used. For example, cutting sheet metal with plasmausing hydrogen or nitrogen is suitable for colored varieties. On the other hand, oxygen will be the best option for processing ferrous metal. During operation, the operator is required to have full control of the active jet. Immediately after the activation of the electric arc, the generation of the on-duty plasma flow begins. By controlling the device, the user adjusts the parameters of the formed torch, directing it to the cutting line in the workpiece.
Types of cutting equipment
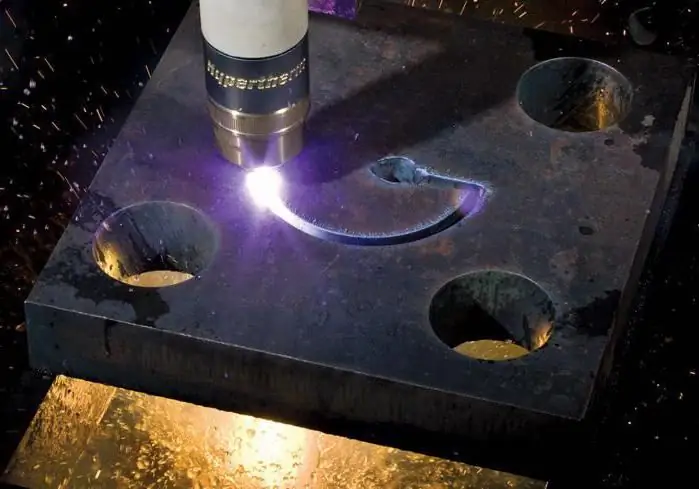
As a rule, plasma cutters are divided into transformer devices and inverter type devices. The first group is represented by models specially designed for cutting metal sheets with a thickness of 35-40 mm. Inverters are modest in size and at the same time have higher performance compared to transformers. However, high quality processing at lower power consumption is ensured only in cases where plasma cutting of metal is carried out, the thickness of which does not exceed 30 mm. Also, the devices differ in the type of nozzle cooling system - in particular, there are liquid and air models. In the first case, a jet of water acts as a cooling medium, and in the second, a gas. In large units, water is more often used, which makes it possible to increase the accuracy of operations. In order to ensure a high working resource, technologists recommend using gas cooling systems.
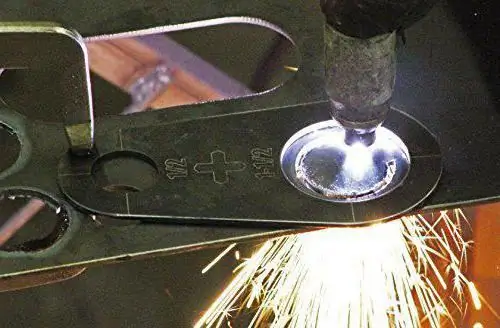
What is the advantage of plasma cutting?
Typically, competition between cutting technologies for solid materials occurs inparameters of accuracy and cutting speed. However, the emergence of new methods has expanded the possibilities of processing, increasing the basic requirements for the quality of operations. In terms of performance indicators, plasma cutting is one of the most profitable technologies of this type. First of all, this is due to the possibility of point local cutting without deformation of the surrounding zone. Even plasma cutting of stainless steel is performed without thermal deformation of the workpiece, although the processing of such material requires the use of a high power machine. In addition, the high cutting speed is emphasized. If you select the appropriate current strength, then a thin sheet can be handled in a matter of seconds without loss of quality.
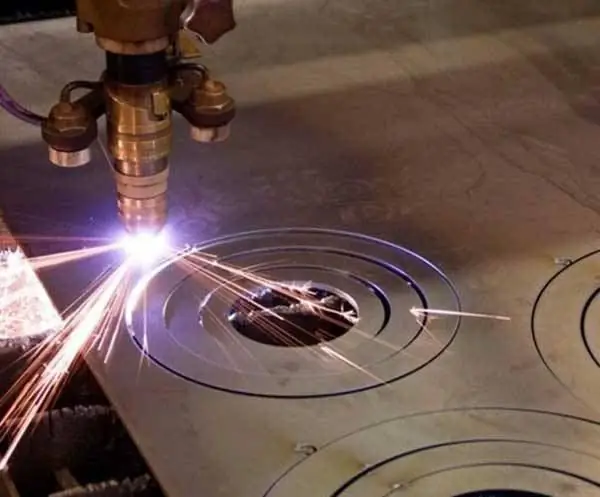
What to consider when choosing a plasma cutter?
As already noted, in choosing a device, the current strength of the device is of considerable importance, which will allow you to cope with one or another type of metal. For example, 40-50 Amp models are suitable for working with brass, copper, aluminum and other non-ferrous metals, but their potential is not enough for high-quality and confident cutting of steel. To work with black grades of metal, it is advisable to initially focus on devices whose current strength is at least 100 A. And this is without taking into account the thickness of the workpiece. As a rule, plasma cutting is performed at the rate of 5 A per 1 mm. It is also worth considering the duration of the active work of the plasma cutter. For representatives of the entry level, for example, this interval is no more than 10 minutes, after which the operator has to dotechnical break.
Conclusion
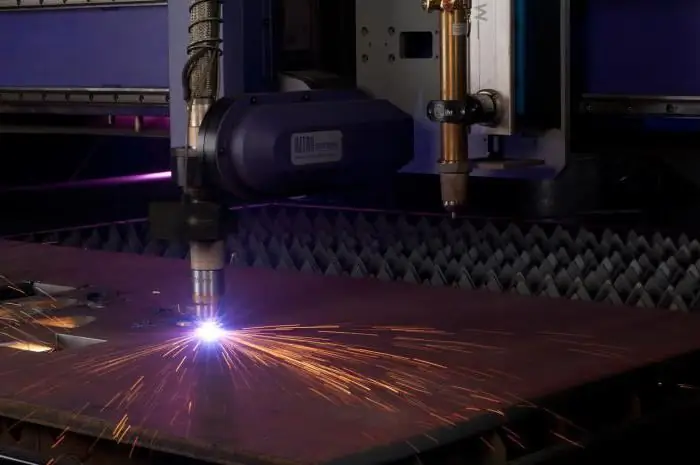
For all the advantages of plasma technology, it is not the best way to cut metal. For example, the waterjet technique is distinguished by the possibility of cutting in blanks of almost any thickness. At the same time, the equipment is cheaper to maintain and requires minimal energy consumption. In turn, plasma cutting of metal offers high speed and corresponding quality of the result. Most importantly, the technical organization of this process involves only the purchase of a special apparatus. Anyone can use a plasma cutter at home - but, of course, with proper training. In comparison, an abrasive operation is not complete without the use of massive units that supply jets of water or air mixed with sand particles.
Recommended:
Metal band saw. Metal cutting machine
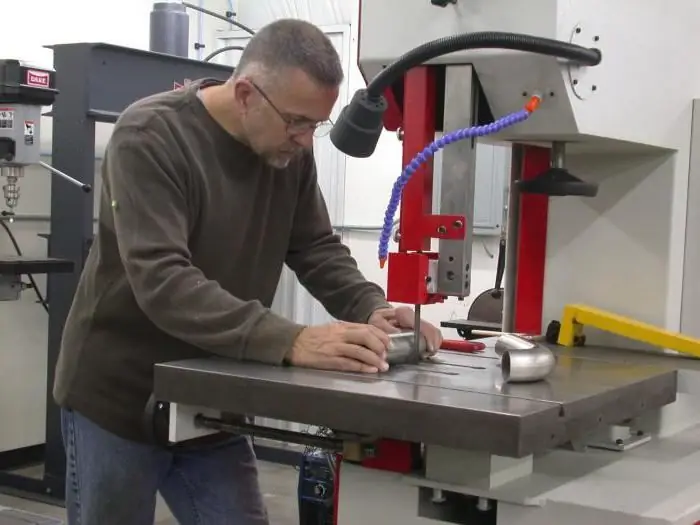
Metal band saw is a high-performance equipment that is responsible for a variety of functions, such as cutting metals and cutting a variety of strong and high-strength materials
Sheet metal cutting: description, types. metal bending
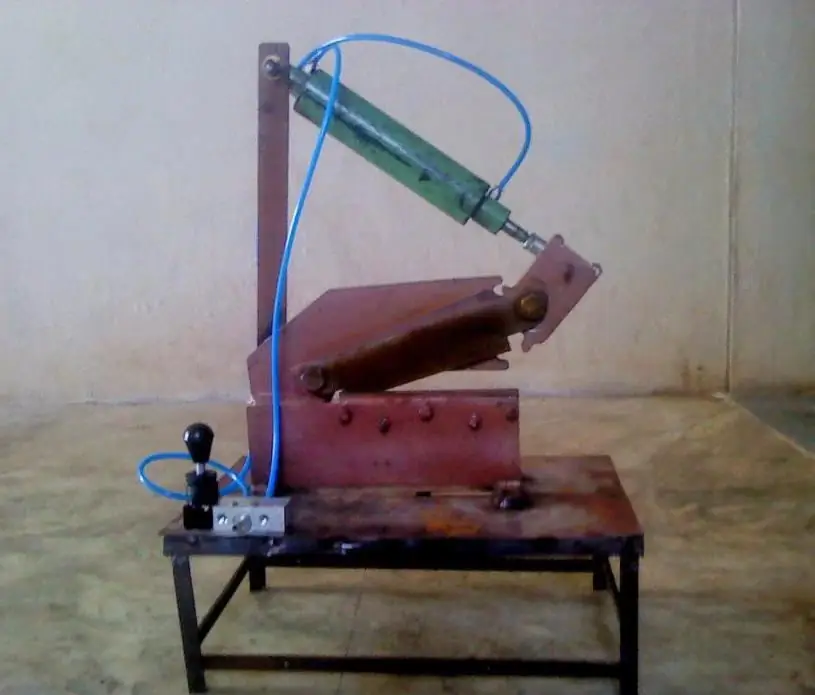
Today, sheet metal cutting is one of the fairly common technological processes that allows you to get blanks of the desired size and shape. However, there are many methods for performing this procedure and a wide variety of equipment
Cutting mode for milling. Types of cutters, calculation of cutting speed
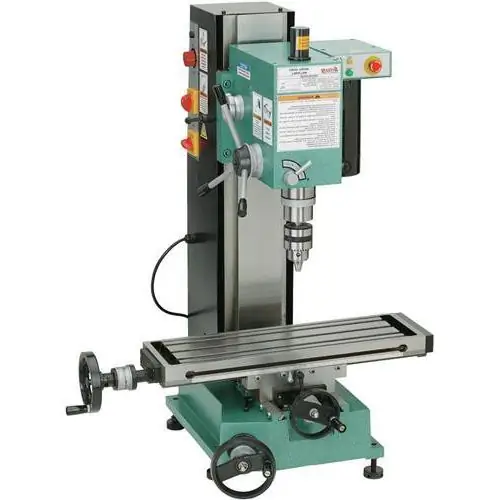
One of the ways to finish materials is milling. It is used for processing metal and non-metal workpieces. The workflow is controlled by cutting data
Metal cutting machine. Plasma metal cutting machine
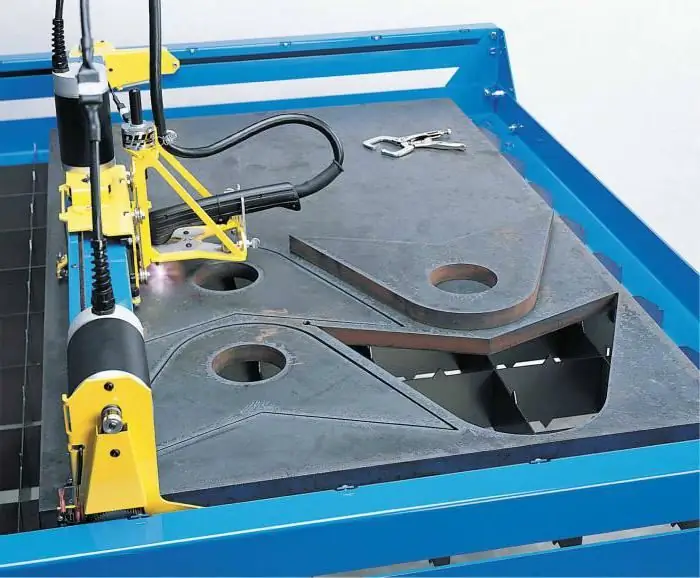
The article is devoted to the apparatus for cutting metal. The technology of plasma cutting, as well as the device and features of the equipment are considered
Metal cutting with plasma. Metalworking equipment
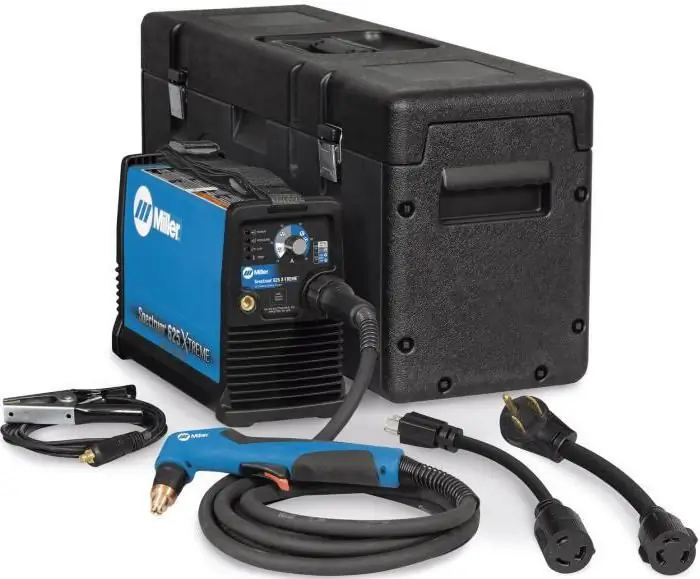
When buying a plasma cutter, you should always prioritize quality. Beware of the temptation to buy a cheap low-quality device, as its rapid wear and tear in the long run will lead to much higher costs