2025 Author: Howard Calhoun | [email protected]. Last modified: 2025-01-24 13:10
This type of porous concrete has been on the list of first building materials for a long time. Therefore, many factories and companies are engaged in its manufacture. With the development of technology, autoclaved aerated concrete can be found in various shapes, sizes and colors.
Autoclaved aerated concrete consists of three main components:
- cement;
- quartz sand;
- gasifiers.
Structure
It contains pores up to three millimeters in size.
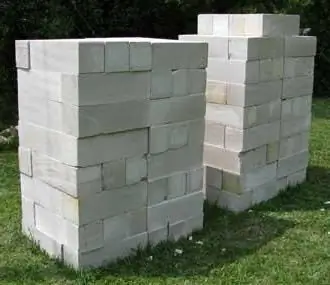
It is considered a type of cellular concrete. The common thing in a concrete mix is a binder base, filler and water. Aerated concrete can be classified according to the type of binder in the base, it can be:
- cement;
- lime;
- slag;
- gas gypsum.
Autoclaved aerated concrete based on cement together with lime is widely used.
In order to achieve a porous structure, a chemical reaction is created in concrete in which gas is released.
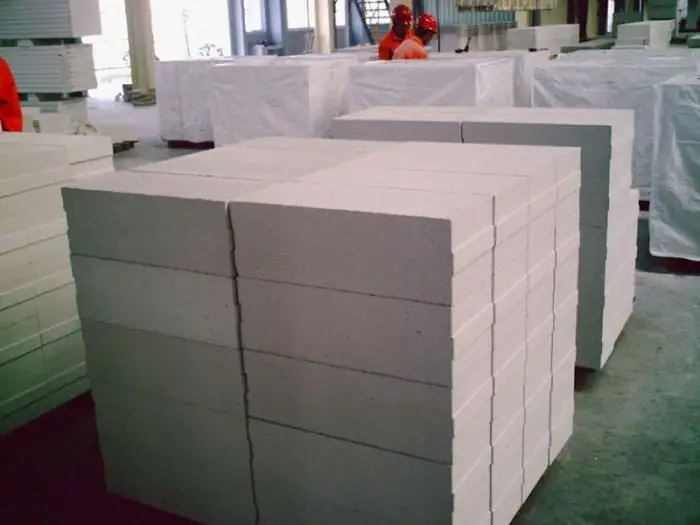
To create such a process, aluminum powder or paste is used. If it is necessary to give the material special properties, additional substances are introduced into its composition.
Production Methods
You can get autoclaved aerated concrete in this way: a thin mixture of concrete is poured into special forms by half the volume. At the same time, a shock load acts on it. In this case, heat is released due to the quenching of lime. The temperature of the autoclave increases to 80 degrees.
After this, the lime reacts with aluminum, from which oxygen is released. Due to this, the mass of concrete rises to the edge of the form. Pressure, like temperature, increases. Under the influence of these values, the cement hardens, while the pores remain, and inside them there is already air instead of hydrogen. Thus, the formation of a concrete structure occurs, the pores in which occupy up to 80 percent of the volume. You can influence the percentage of porosity by changing the amount of aluminum powder.
After a couple of hours, the hardened mass is taken out of the autoclave and cut into segments of the desired size. Then the finished blocks are sent back to the autoclave, where full curing will be achieved only after 12 hours. In this case, the temperature regime should be at least 190 degrees at a pressure of 1.2 MPa.
Usually in the volume of concrete cement is not more than 20%, and Portland cement is more often used.
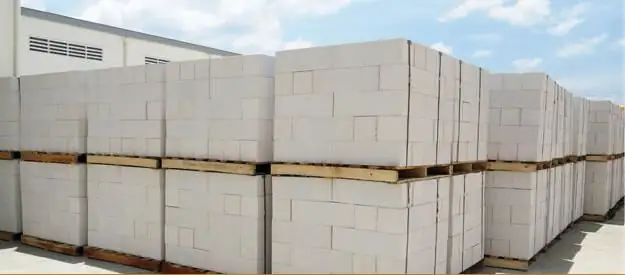
In a larger volume, autoclaved aerated concrete consists of quartz sand (approximately 60%). Lime is the same as cement, no more than 20%. The aluminum content can be no more than one percent.
Autoclaved aerated concrete manufacturers at their enterprises ensure that pressure and temperature make a special mineral from the component - tobermorite. It is due to this formation that the material has high strength and is not subject to shrinkage. Another important point of artificial conditions is that the production time is reduced, which allows the production of large batches.
Production cycle
The accuracy in the structure of the production process depends on what kind of cellular concrete is produced. The general processes are as follows:
- preparing the required number of ingredients;
- preparing the mixture and introducing a blowing agent into it;
- shape fill;
- removing excess mixture;
- exposure time.
Sizes
Like any building material, aerated concrete has standardization.
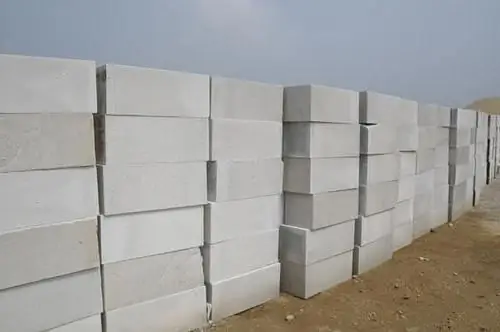
The size of such blocks is much larger than bricks. Everything has to do with less weight. Blocks for building have dimensions:
- length - 625mm;
- width varies from 100mm to 400mm;
- height - from 200 to 250 mm.
Naturally, the increased dimensions make it possible to simplify and accelerate the speed of their installation. And their insignificant weight will not interfere with manual work with it.
Autoclaved aerated concrete production has a huge advantage, and it is the shape of the blocks. They have an ideal shape, the corners and edges of which are even and smooth. Block sizes do not change over time. Even different batches of blocks have minor errors in their size - only 1.5 mm. For blocks of the lowest category, this parameter can be 3 mm, but compared to the entire block, this figure is negligible.
Properties
Autoclaved aerated concrete has a low weight with a large volume - this is the most important positive property of such a material. Its specific gravity is not more than 700 kg/m³. Also, thanks to the method of production in an autoclave, the compressive strength is significantly increased - up to 50 kg / cm².
If you change the porosity of concrete, it can lead to a change in thermal conductivity and strength. With an increase in its strength decreases, but the thermal insulation properties increase. Reducing this indicator leads to the opposite effect.
Change in porosity leads to the fact that concrete is divided into three main classes:
- Heat-insulating. The density of this material class is 400 kg/m³. Its purpose is areas with cold climatic conditions, but buildings from it can be built low.
- Constructional. This aerated concrete has the highest density - 700 kg / m³. It can be used for the construction of high-rise buildings or for the structures of load-bearing structures. When used in residential buildings, it must be covered with an additional layer of thermal insulation.
- Structural and heat-insulating. This aerated concrete with an average density value (500 kg / m³) is widely used, as it has both good strength and sufficient thermal insulation.
Differences in production
There are two ways to produce aerated concrete: in an autoclave and without it. There is aerated concrete autoclaved and non-autoclaved. How to understand the difference?
Both types have the same production structure - by releasing gas as a result of a chemical reaction.
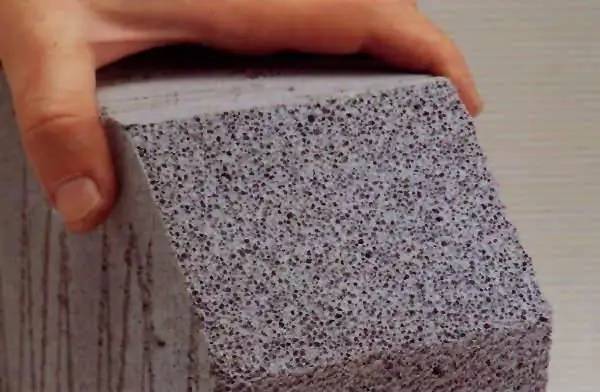
But these are fundamentally different schemes. The way the blocks harden makes a difference in the properties of cellular concrete.
Non-autoclaved aerated concrete has a large percentage of Portland cement in its composition. The mixture is left to dry naturally, without the use of a special oven - an autoclave. This type of cellular concrete has minimal production costs. But in terms of its properties, it is much inferior to aerated concrete obtained using a kiln.
Only a large autoclaved aerated concrete plant can produce such blocks in large quantities, while foam blocks can be produced even at a small enterprise.
Benefits
Its dimensional stability allows for the laying of blocks on the mortar with a minimum thickness (about 3 mm). This advantage gives a high degree of protection against external temperature. Since the masonry mortar has a lower degree of heat protection, its insignificance will only be a plus. Due to the fact that the edges and corners are even, the appearance of the masonry will be noble.
Another advantage is its malleability to any building tool. Autoclaved aerated concrete blocks can be planed, cut, drilled and warped. You can easily screw a screw into it or hammer itnail.
Building a house with this material
For a person who is just going to build a house, the main criteria for selecting materials will be their reliability, durability, environmental friendliness and comfort. In the context of economic problems, the criterion of efficiency is also important. All of the above signs will correspond to a material such as autoclaved aerated concrete.
This is an artificial stone, but it is made from natural ingredients. The microclimate of such a house is the same as in a house made of wood. All due to the fact that the structure of the blocks is porous, this allows the building to "breathe".
Even though the porous structure, hygroscopicity (moisture absorption) is within the normal range.
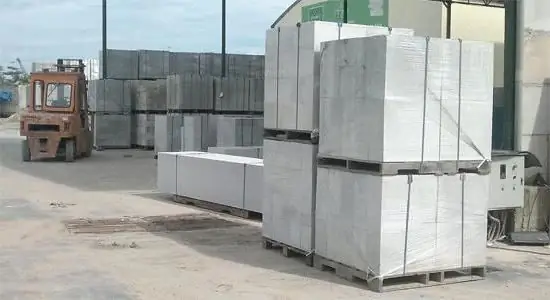
Its percentage is no more than 5%. If we compare this indicator with the hygroscopicity of some types of wood, then the percentage there will be several times higher. Heating a house made of aerated concrete is easier than that of a brick one. This will significantly save energy costs.
The thickness of the walls of aerated concrete is only 1 block, this will be enough for thermal insulation. Whereas for brick, an additional layer is required. Therefore, the cost of such walls will be minimal.
Humidity in aerated concrete rooms cannot lead to the formation of mold or fungi. In such houses, the process of decay and decomposition is excluded. The use of innovative technologies has made it possible to reduce the thickness of the walls, while not reducing their strength. It is profitable to build a house from autoclaved aerated concrete due to the minimumlabor costs. Even a beginner can cope with the installation of such a wall.
Fire safety
Another advantage of the material is its absolute fire safety. Walls made of autoclaved aerated concrete do not heat up even when exposed to open fire. Since it is not capable of burning, it cannot emit hazardous substances. The construction of such a house will be carried out in terms much lower than those that can be spent on other types of materials.
Block stacking
It is possible to install aerated concrete wall blocks using a warm or cement-sand mortar, but a special adhesive would be the best option. It can be applied in a thin layer, which will eliminate cold bridges. The first row of blocks must be laid on a well-prepared horizontal surface. Reinforcement of such masonry is carried out according to the project. The first row of blocks, the lower window and supporting surfaces of the lintels must be reinforced.
Wall decoration
A properly executed aerated concrete wall does not require plastering.
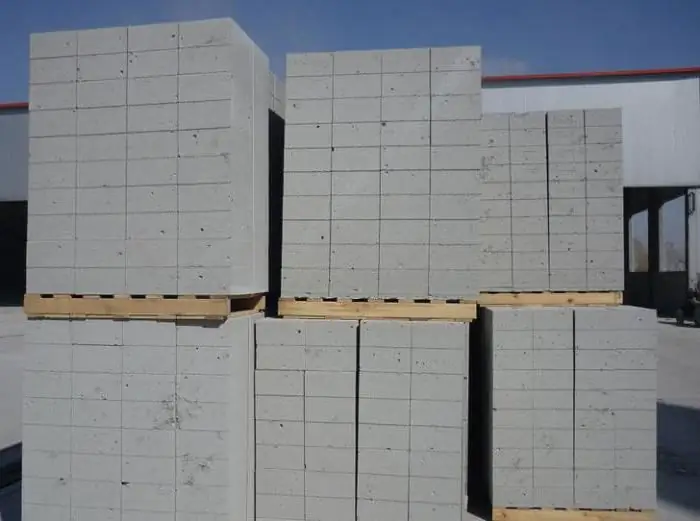
The outer surface does not have to be finished, but it can be done to give a beautiful appearance. In bad weather conditions, the blocks can get wet and absorb moisture, but not more than two centimeters. In order to avoid this, you need to properly craft roof drains and visors and provide protection for the plinth.
When choosing an exterior finish, consider that it must also be permeable, like aerated concrete. It will look beautiful well-madeventilated facade from any available materials. You can use, for example, autoclaved aerated concrete, user reviews of which are only positive. Users note that it is possible to finish everything without pretreatment of internal walls.
Finishing can be done directly on the blocks. Pre-plastering the walls is not necessary, the more simple putty will be enough. Vapor barrier should be applied in rooms with high humidity.
Recommended:
Robotization of production in the world: scope, examples, pros and cons
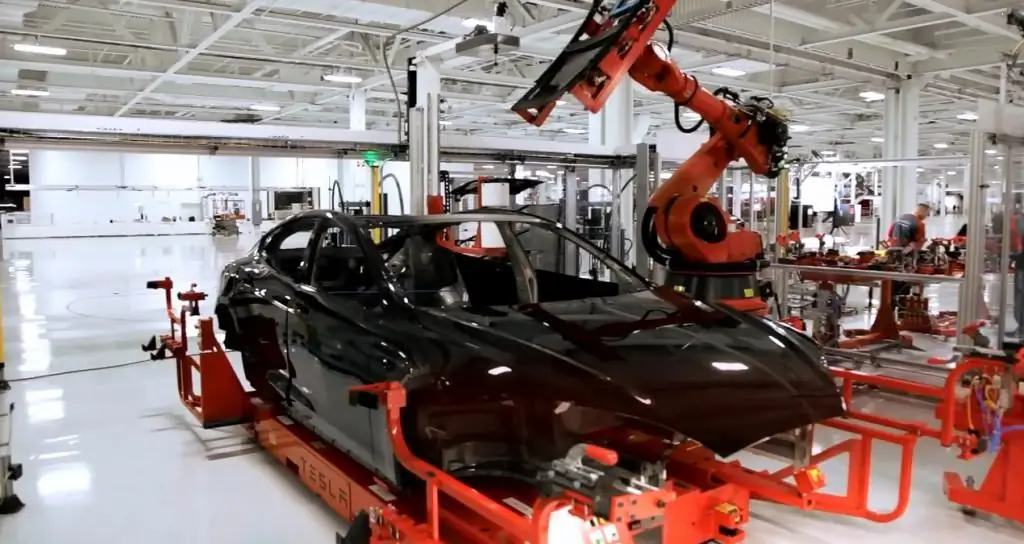
Improving, humanity is constantly facilitating its work, shifting it to artificial intelligence. Robotization of production made it possible to get rid of a number of professions, for example, telephone service today is carried out only by electronics, although at the beginning of the last century, female telephone operators connected two subscribers. Today, progress has stepped even further, and people have begun to create real artificial machines capable of performing certain mechanical operations - robots
Concrete strength meters. Concrete testing methods
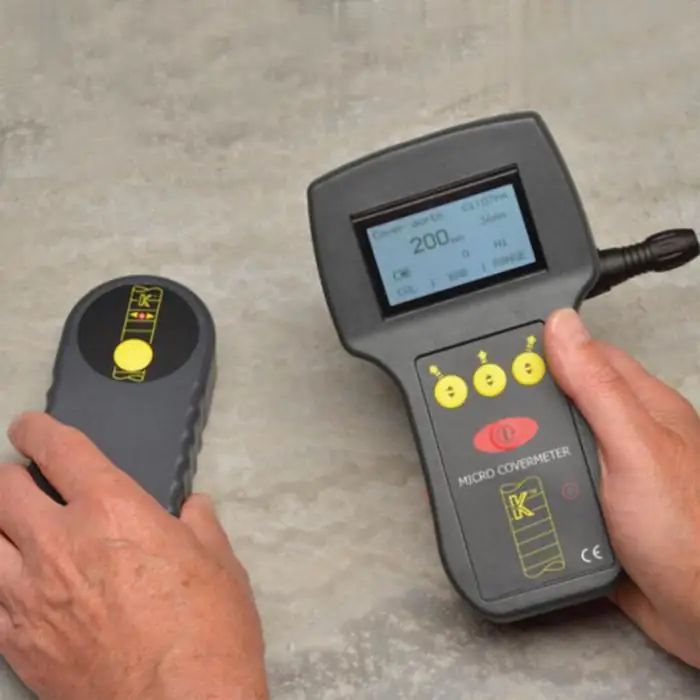
When constructing buildings and structures, it is very important to monitor the strength of concrete. For this, special devices are used. Measurement parameters can vary quite a lot
Determination of concrete strength: methods, equipment, GOST. Control and evaluation of concrete strength
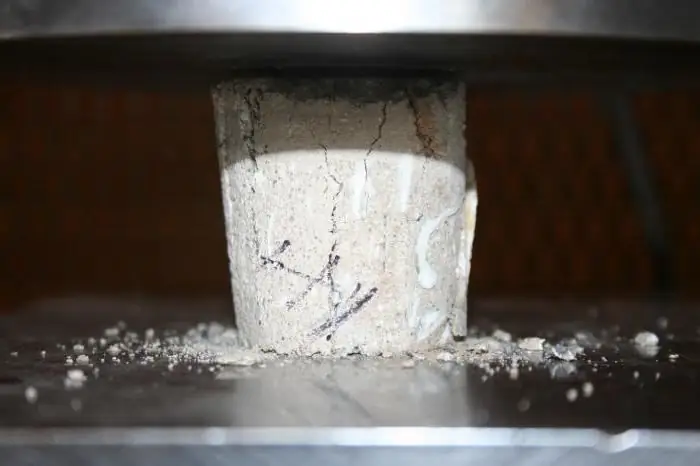
When checking building structures, the determination of the strength of concrete is carried out to determine their state at the current time. Actual performance after the start of operation usually does not match the design parameters
Aerated concrete blocks: disadvantages and advantages
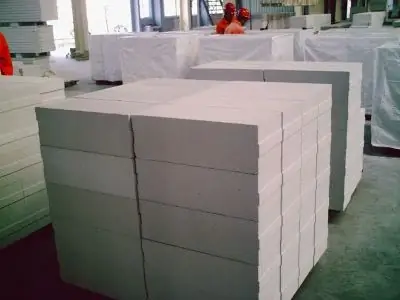
In the modern world, construction is developing at a rapid pace, thereby increasing the demand for materials. Cellular concrete has become in demand in the domestic market. At one time, the products were widely advertised, and the demand for them is now high
Concrete mix: properties, composition, types, grades of concrete, characteristics, compliance with GOST standards and application
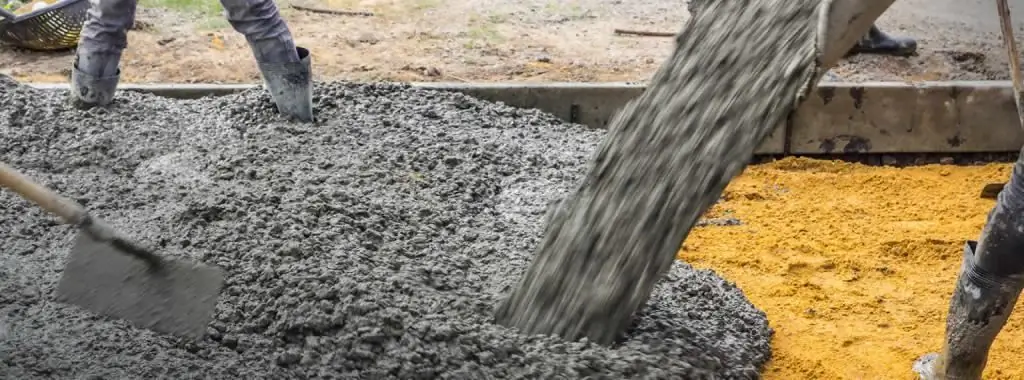
Among the main properties of the concrete mixture, which is also called hydrotechnical concrete, it is necessary to highlight the increased water resistance. Buildings are being built from this material to be used in swampy areas or in regions that are prone to flooding