2025 Author: Howard Calhoun | [email protected]. Last modified: 2025-01-24 13:10
This type of wells is built purely for household needs. With the help of such a structure, it is possible to collect underground water. In this case, the fluid intake can be carried out by one of the methods chosen by civil engineers. It is worth noting that the shaft well is considered the simplest option of all varieties of such structures.
General description of the device
Schematically, the design is a vertical shaft. It is allowed to use both round and square sections. At the mine itself, the bottom remains open, and its location must cross the aquifers of the soil. The side walls require mandatory fixing with one of the selected materials. The latter can only be waterproof options, such as plastic, brick samples, wood or reinforced concrete.
Due to the simplicity of the design of shaft wells, this type is the most widely used. The final quality of the water extracted from the subsoil depends to a certain extent on the correct installation. Such a device can functiona sufficiently long period of time without any repairs.
The location should be chosen by qualified specialists, since the location of the well depends on what type of water it will produce according to the degree of purification. In turn, underground sources are divided into soil, soil and interstratal. The last type of water is the most suitable for use in terms of the degree of purification, and the first is less than others.
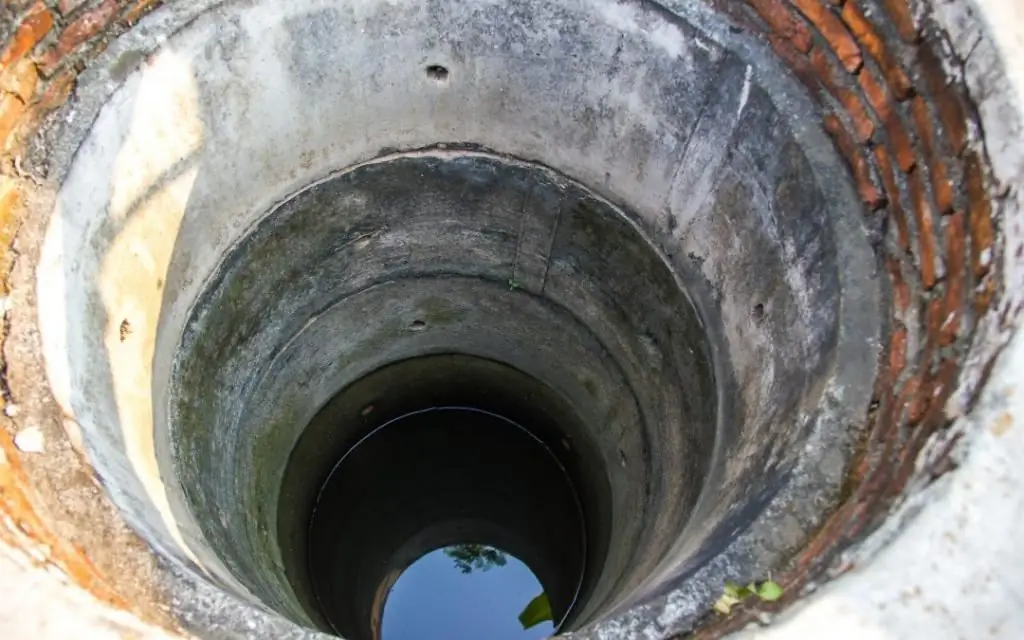
Construction Requirements
There are a number of specific rules that must be observed when installing wells. First of all, the bottom of the shaft should be mentioned: it should be covered with gravel with a layer thickness of at least 30 cm. The walls should be raised above ground level by about one meter. It is important to build in accordance with the slope of the site, and therefore above any source of pollution. A distance of 30 to 50 m must be observed between the latter and the shaft of the shaft well. In fact, this is a kind of preventive measure in relation to disinfection and repair. If there is still a source of pollution above the mine, then the distance from it to the shaft, according to current standards, cannot be less than 80-100 m. In this case, in some cases it is better to measure 120-150 m.
The design of mine wells implies the presence of a clay castle around the shaft with a blind area, which serves to hold the flow of dirty water and prevent them from getting inside the structure. Creating such a barrier involves digging a hole 1 m wide and 2 m deep. Fill in the resultingspace need special greasy clay. On the surface above the castle, the ground part of the structure itself is placed directly. Sand is poured on top, and then cement or concrete mortar is added. SanPiN norms provide for the creation of a ditch for drainage and interception of contaminated fluid flows. In addition, it is recommended to create enclosing elements that do not allow cars and other vehicles to park.
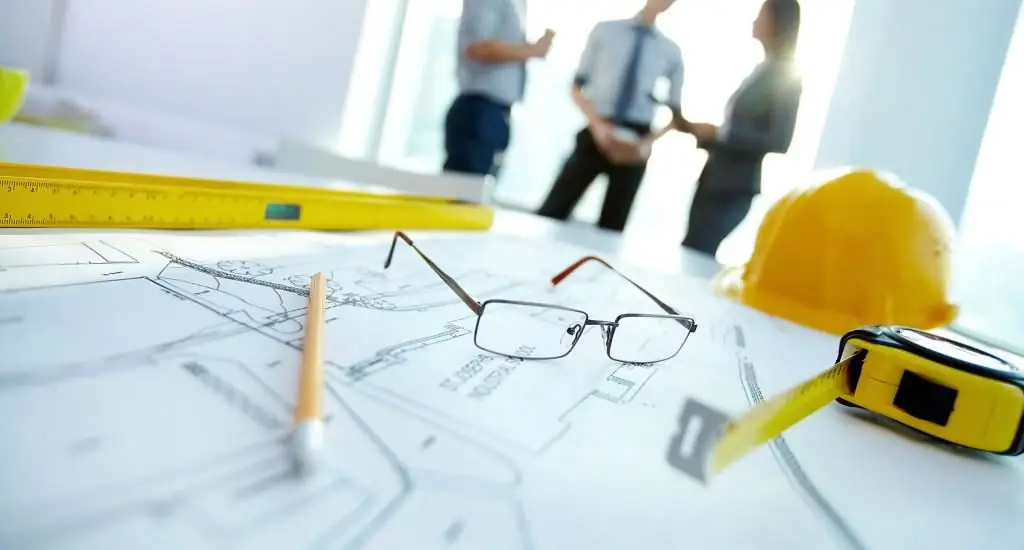
Requirements for the construction of wells
The main purpose of the construction of such structures was to provide water to one or several plots of land at once. The value of shaft wells for household or other needs could be different and was based on the overall performance of the devices. For example, these designs were often used to water plants or provide a reliable source of fire extinguishing fluid. As a rule, the water flow rate is from 0.5 to 3 cubic meters per hour. It was best to plan the installation of products with a shaft depth of about 20 m on sandy or gravelly soils. Additional advantages of such wells include their accessibility for cleaning, ease of operation and repair, as well as immunity to flooding rains.
According to the rules, the liquid is taken using electric pumps or simple buckets. Wells with low extraction intensity are the most susceptible to pollution. Stagnation of water leads to the appearance of a musty smell inside the mine. Free-standing unguarded open-type wells are also subject topollution caused by the ejection of any foreign objects into the structure. The personnel carrying out the installation work must understand the design of such structures. Choosing the wrong place for digging an adit that does not meet the requirements for the construction of shaft wells can lead to contamination of incoming water, collapse of the walls of the shaft and gas contamination inside the structure itself. For the cleaning and operation of such facilities, there are separate sets of standards and rules.
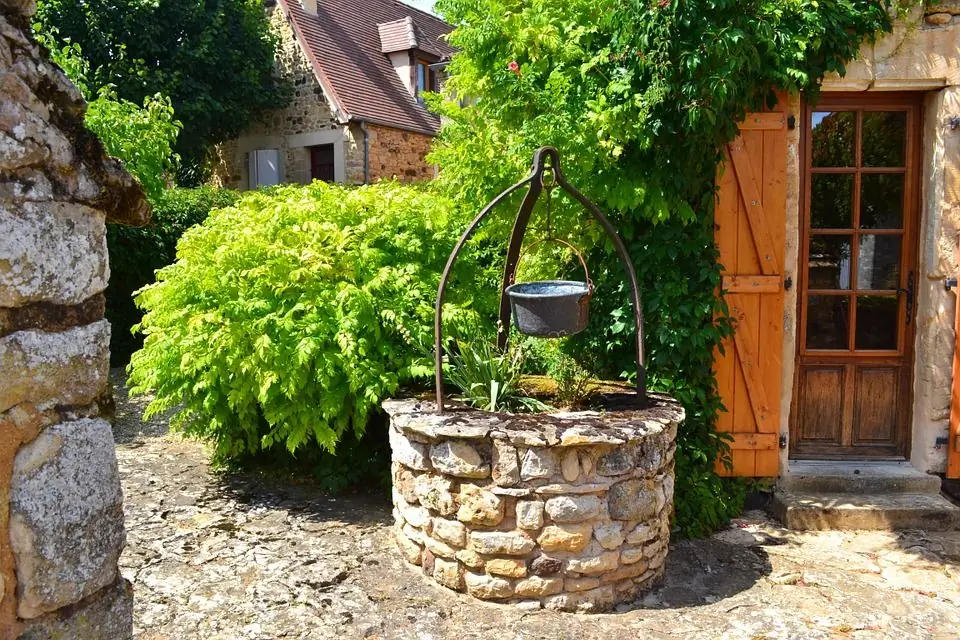
Construction and operation conditions
Those who plan to dig a well will first need to familiarize themselves with the current list of SNiP rules. In particular, it refers to the impossibility of installing mine shafts made of plastic pipes in areas where there is increased seismic activity. If the indicator on the Richter scale exceeds the 7-point mark, then the commission will not approve the construction. In addition, SNiP imposes other requirements on the shaft well, the material for the walls of which is plastic. So, for example, the natural water saturation of the soil should have a coefficient of 2.0. The design temperature and density should also be taken into account. These soil indicators for plastic wells should be 50 degrees Celsius and 1.8 tons / cubic meter, respectively.
In some cases, the construction of walls is possible only from concrete with a thickness of 150 mm or more. In particular, this applies to the construction of shaft wells on water-saturated soils. All digging or restoration work may be carried out inany time of the year, but you should avoid the time when the snow begins to melt. If there is a swamp on the site, then it is best to build a well in the fall or winter. The operating conditions include a clause that at some intervals the owner of the device needs to check the presence of gas in the mine. In fact, such a procedure is required for each inspection, repair or restoration of the well. A check is made for the presence of gas by lowering a bunch of grass or a lit candle into the trunk.
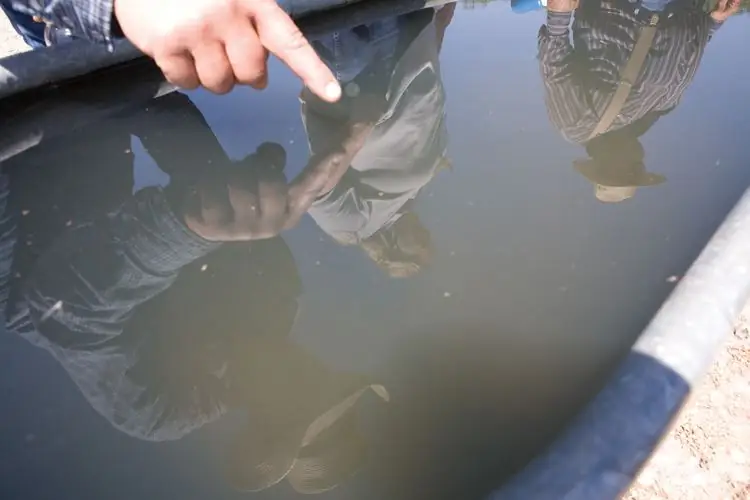
Advantages and disadvantages
Wells of this type have both a number of undoubted advantages and some obvious disadvantages. The benefits of such devices include the following:
- Long lack of need for repairs. As a rule, the operational life without breakdowns for mine wells with water is from 50 to 70 years.
- Almost complete absence of problems with the execution of permits for construction. At the same time, immediately after the construction of the well, you should contact the BTI to go through the registration procedure.
- General cheapness of construction compared to other design options. For comparison, you can bring any well with the need to drill a mine. Otherwise, digging is much cheaper.
- A simple procedure for cleaning produced water. There is no need to burden yourself with a complex and ornate technological process, as well as hire specialized personnel.
- Due to the large diameter of the shaft, one of the selected types of water can be liftedpumps. Automation is successfully replacing traditional buckets that require physical effort. It is enough to install a vibration, centrifugal or deep pumping system.
It is also worth giving a list of shortcomings that are relevant for the mine type of wells:
- High costs of time and labor of specialists. For example, equipping a tube well is somewhat easier according to these indicators.
- Increased responsibility for the installation of the mine shaft. If the docking of waterproofing joints or sealing of pipe joints is not done at the proper level, then water pollution one way or another becomes inevitable over time. This, in turn, will lead to a violation of sanitary standards and the need for a new laying of the mine shaft.
- The hydraulic structure requires annual cleaning and disinfection. For other types of wells, there is no need to carry out these procedures so often.
- The mine cannot be idle for a long time. It is mandatory to pump out or take in water, since the structure will simply overflow with liquid.
- In the absence of a reliable filter, the quality of the resulting product is likely to be very low and of little use for its intended purpose.
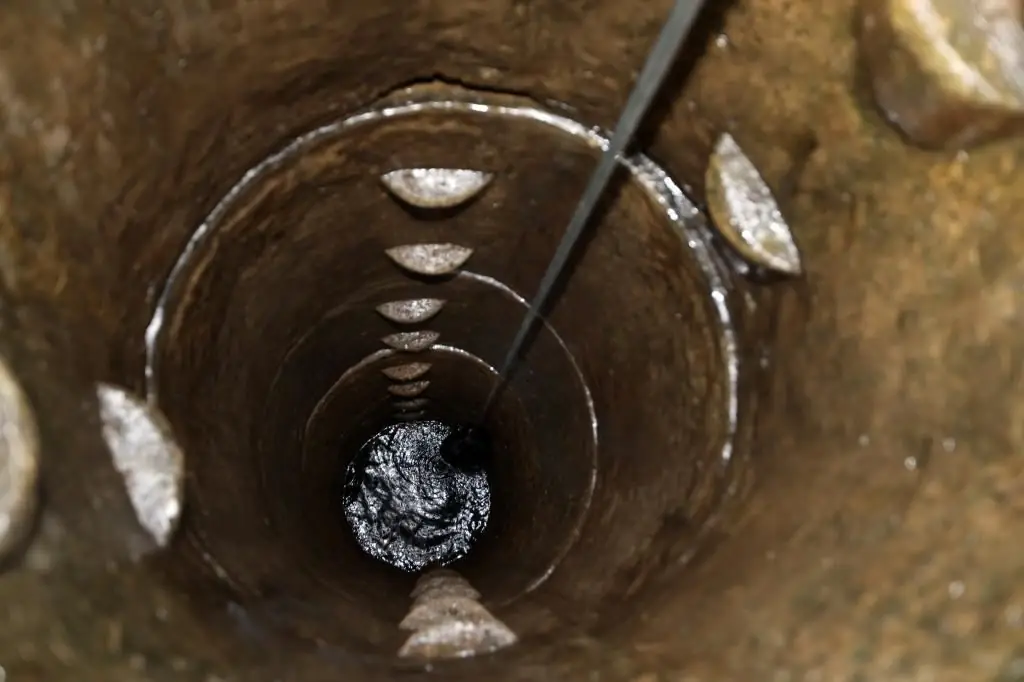
Types of erected structures
In general, there are three design options, the differences in which are due to different working scenarios. An incomplete or imperfect arrangement of a shaft well means that the shaft does not reach the water-resistant layer. The meaning is that the liquidaccumulates both through the walls and through the bottom of the structure. If we talk about perfect or complete wells, then in them the mine rests on the same water-resistant layer. The flow of liquid in this case is made only through the side walls of the mine.
There is also a variation of the perfect well with a grenade launcher. This type shows itself best in a situation where the liquid penetrates the shaft too slowly. In this case, it is required to install an additional grenade launcher tank, which is otherwise called a sump. For the correct operation of such an element, it is required to deepen it below the aquifer.
Incomplete wells have proven themselves in small garden areas. In this case, you need to pay attention to the water level. When it does not exceed 30-50 cm, the well deepens and then can turn into a full one. You should build on the daily fluid intake and leave exactly this amount in the mine.
Construction on various soils
The construction process begins with earthworks. The time it takes to dig a space for a trunk is largely dependent on the type of soil. The list below shows the features of the construction of shaft wells for various types of land on the site:
- Quicksnappers. A very difficult type of soil for construction. Workers need to continuously pump out water and install tongue-and-groove walls during the construction of the mine. If quicksands are located in interlayer layers under high pressure, then construction may be completely impractical due to increaseddifficulties.
- Loose soils. These include gravel, crushed stone, pebbles and sand. In the process, it is necessary to strengthen the walls of the mine, since there is a high chance of a collapse.
- Soft soils. There is only a weak bond between the particles of clay or loam. Specialists have to act quite carefully, since the risk of a collapse of the mine is just as great as when building a well on loose soils.
- Weak soils. They include slags, soft limestones, gypsum and many others. The work is easy and quick, provided that there is no pressure and there is a weak flow of liquid.
- Medium soils. It is very difficult to dig a mine on sandstone, dense shales or calcareous spar. With excessively intense water pressure, the task becomes impossible.
- Strong soils. These include feldspars, quartzes, granites, etc. Manual work is virtually impossible or very difficult. Digging a mine in this case, as a rule, is simply not financially profitable.
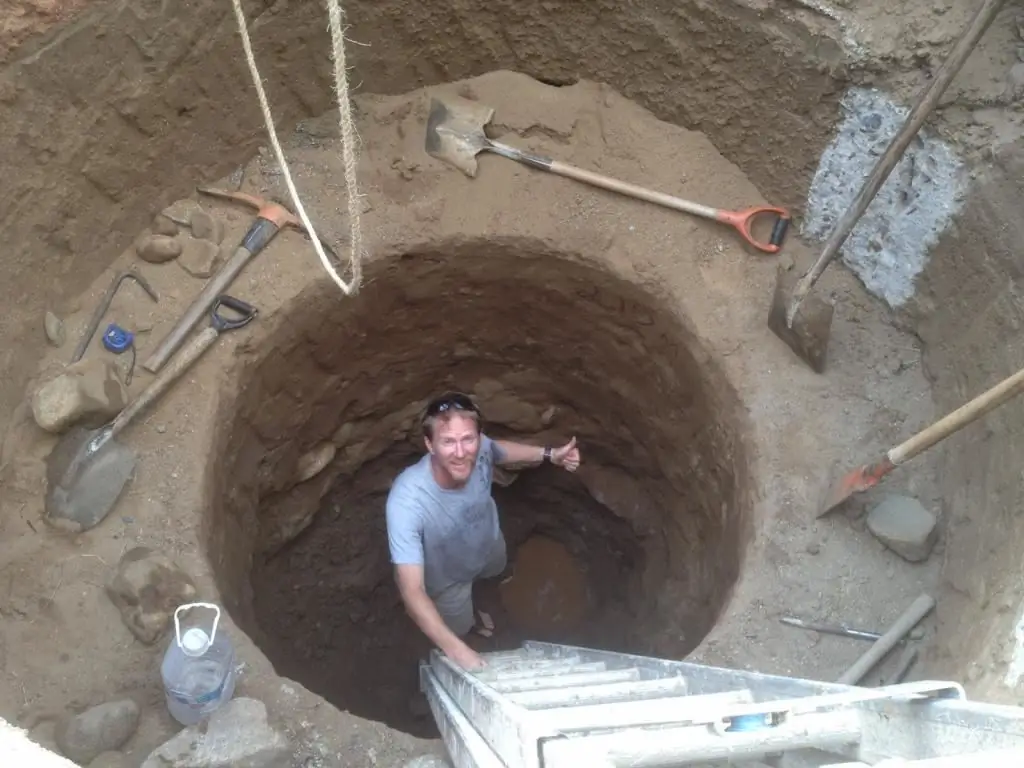
Operating hygiene standards
Contamination of drinking water from a well is considered unacceptable in the modern world. If used incorrectly, the fluid may be subjected to chemical or microbial contamination. For this reason, there are clear hygienic requirements for the construction of shaft wells. For example, in a 20-meter radius, in no case should you wash cars, arrange a watering hole for animals and birds, or engage in rinsing and washing clothes. It is prescribed that any other types ofactivities that directly or indirectly contribute to the contamination of the liquid in the well.
Neighbourhood should not use their own buckets to draw water from the mine. The procedure is performed only with a device attached to the well. Every year it is necessary to carry out a scheduled cleaning, as well as to check the equipment and fasteners for wear. Any repair is accompanied by subsequent disinfection with the help of special substances that include chlorine-containing reagents. At the end of the procedure, the final flushing of the water intake is carried out.
Suitable building materials
The most popular variant of such wells is made of concrete rings. To simplify the process of lowering future walls, the diameter does not exceed one meter. The construction of concrete rings is quite fast, and the design itself is incredibly reliable. Sanitary requirements for mine wells in this case prescribe not to use any chemical products such as sealants, mortars or mastic. All of these products have a direct negative impact on water quality. Work is suspended at the moment when the keys begin to beat at the bottom. The water should be pumped out, another small layer of soil removed, and then the structure should not be touched for 12 hours.
Wooden wells are considered slightly more expensive and difficult to manufacture and install. Nevertheless, the foreseeable service life of the structure is 25 years in the ground part and 100 years in the underwater part. To date, there are two actual ways to build such wells. In the firstcase, a shaft is dug out and the walls are built up from top to bottom. The second option involves adding bars from below. Sanitary standards require mandatory pre-treatment of all wooden elements. When reaching the springs, the water is pumped out twice - this is how the bottom filter is formed. The procedure is completely similar to that for wells made of concrete rings. After that, you can begin to operate the structure.
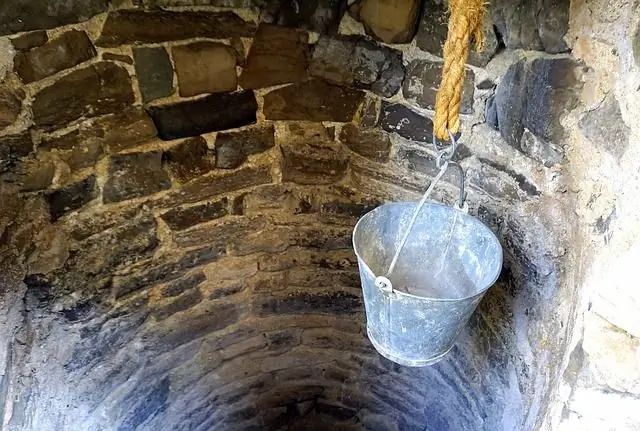
Advantages of building a brick shaft
You should responsibly approach the choice of a specific material. The brick should be red, since silicate is subject to mechanical destruction in the ground. From natural stones, dense limestones, slates and sandstones are used. A properly built brick structure easily meets all sanitary requirements for mine wells.
Most often, a round shape is chosen, and the thickness of the masonry is not less than 25 cm. The seams should be as less noticeable as possible. The ground structure is treated with plaster, and the underwater one is poured with a solution with sand and cement in the composition. It is also acceptable to reinforce the masonry with steel anchor rods, as this greatly reduces the chance that the mine will fall apart when the soil collapses.
Recommended:
Where can I find out the cadastral value of an apartment? Cadastral value of an apartment: what is it and how to find out
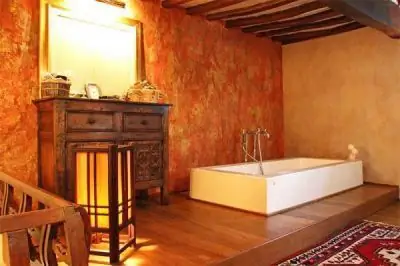
Not so long ago in Russia, all real estate transactions were carried out only on the basis of market and inventory value. The government decided to introduce such a concept as the cadastral value of an apartment. Market and cadastral value have now become two main concepts in the assessment
What is the difference between the cadastral value and the inventory value? Determination of the cadastral value
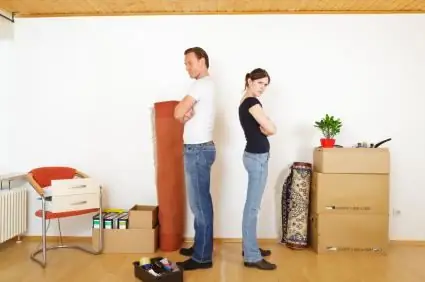
Recently real estate has been valued in a new way. The cadastral value was introduced, providing for other principles for calculating the value of objects and as close as possible to the market price. At the same time, the innovation led to an increase in the tax burden. The article describes how the cadastral value differs from the inventory value and how it is calculated
Well development: methods, process description, safety. Well repair
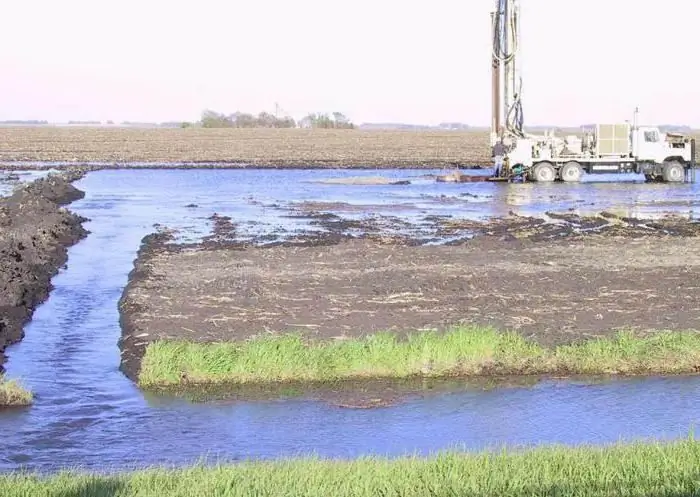
The article is devoted to the development of wells. The methods, features and nuances of the implementation of this event, as well as security measures and repair work are considered
Well survey operator: job description and requirements
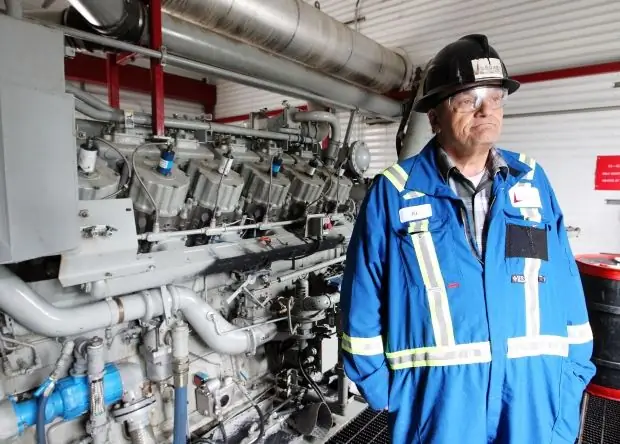
The employee accepted for this position is a worker. To be accepted, he needs to get a professional education and pass a special qualification training. The well survey operator must also have worked in this position for a grade below for at least a year
Primary milk processing: technology and sanitary requirements
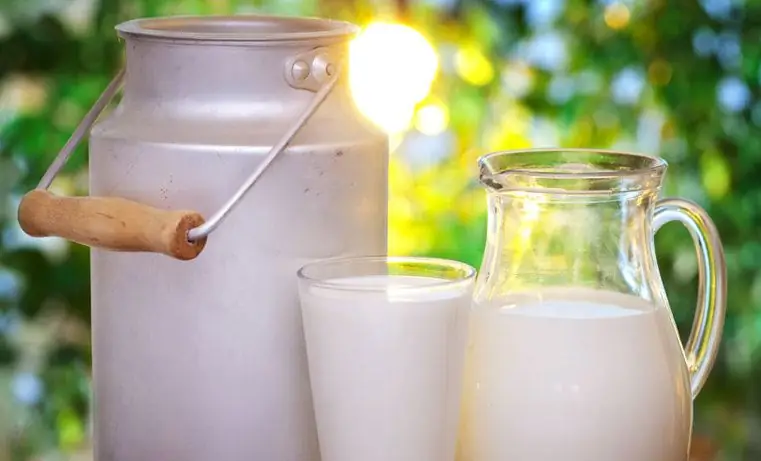
Milk, as you know, is a perishable product. It must be stored and transported properly. Otherwise, a product that is not very tasty, and possibly even unsafe for he alth, will reach the consumer