2025 Author: Howard Calhoun | [email protected]. Last modified: 2025-01-24 13:10
People today take it for granted that the items and services they consume should work well as soon as they buy them. In fact, many industrial and post-industrial societies have simply discarded what doesn't work. However, there was a time when quality and efficiency were not a priority for suppliers of goods and services. An intense focus on quality began to develop largely after World War II, particularly in the 1980s, in response to a market that rejected cheapness of manufacture. In this connection, consumer demand increased for durable goods that took into account human needs.
This article will look at the history of one of the outstanding principles of management - total quality management (TQM). Readers will learn how this can help make profits and make nonprofits more efficient and cost effective. In addition, other industry directions will be considered and TQM will be compared with such philosophies of quality andmethodologies like Six Sigma and Kaizen.
Term Definition
TQM as total quality management describes a system in which a company makes progress through commitment to customer requirements. An organization meets these requirements when it enables every employee in every department to maintain high standards and strive for continuous improvement. Total Quality Management is the forerunner of many quality management systems such as Six Sigma, Lean and ISO.
Total Quality Management is a company-wide initiative to involve everyone in doing the right thing for the customer.
Basics of the term
TQM as total quality management is a measure of the level of acceptability of a product or service. Its management consists of four parts of the quality management system in process management to achieve maximum customer satisfaction at the lowest total cost to the organization.
The system is divided into:
- Quality planning.
- Quality control (defect prevention).
- Quality control (which includes product testing and other elements such as competence).
- Quality improvement.
The correct historical circumstances influenced the formation of the current structure. During this period, new methods of mass production were introduced, such as the Ford assembly line and the urgent demand for materials during the two world wars for this particular innovation. The military to some extent required that everyonethe product they got was good, because the soldiers literally live on the quality of the products that the factories process and produce. Whether it was dry rations or cartridges, these wars sparked a revolution in manufacturing to focus on the idea of getting high performance.
TQM as total quality management is governed by many analytical tools. Statistics play an integral role in this process, since being able to predict the outcome is much cheaper than checking the details. Moreover, sometimes the inspection is simply inconvenient. For example, a fast food restaurant needs to know that every hamburger is of the right quality, without looking up from making them.
General Principles
Total Quality Management concept TQM does not have a single common knowledge, such as for Project Management Group (PMBOK). Likewise, there are no prescribed activities for the implementation of TQM methods and tools. Organizations are free to deploy and adapt TQM as they see fit, yielding to many methodology definitions.
Despite these standardization issues, generally accepted principles can be described:
- Customer satisfaction.
- Employee commitment to the consumer through learning and suggestion mechanisms.
- Fact-based decision making. Teams collect data and process statistics to ensure that the work meets the established requirements.
- Effective communications. Always mustbe an open dialogue within the entire organization.
- Strategic thinking. Quality should be part of the organization's long-term vision.
- Integrated system. The shared vision, including the knowledge of commitment to the principles of quality, allows everyone to connect to the company. Even suppliers are an important part of the system.
- Deconstructing each action into processes, finding and repeating the best processes.
- Continuous improvement. Every employee should always think about how best to do their job.
The overall goal of the system is as follows: "It is necessary to do everything right, controlling and developing each process separately." The concept of total quality management TQM recognizes the development and planning of each activity in stages. At the same time, not only the management of the company is involved, but also its employees.
TQM history
There is no single agreed source for TQM. Some experts believe it came from two books by top quality management thinkers: Total Quality Control by Armand Feigenbaum and Kaoru Ishikawa What is Total Quality Control? Japanese Way. Others say the terminology originated from an initiative by the United States Navy to adopt the recommendations of management guru William Deming, which they called total quality management. The method did not become widespread until the 1980s.
TQM total quality management system dates back to the beginning of the 20th century and the principlesscientific management Frederick Taylor, who advocated a consistent approach to completing tasks and checking completed work to prevent defective products from leaving the store. Further innovations came in the 1920s with the development by W alter Shehart of statistical control processes that could be applied at any point in the manufacturing process to predict quality levels. It was Shehart who developed the control chart used today to manage with Kanban and Agile.
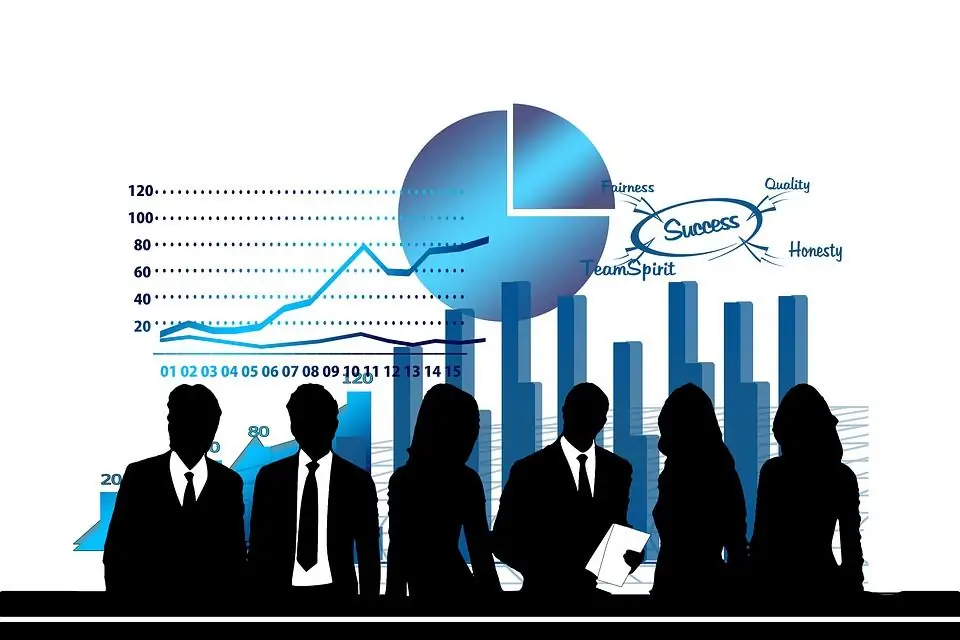
During the 1920s and 1930s, Shehart's friend and ward William Deming developed the theory of TQM, which he eventually used to help the US Census in the early 1940s. This was the first use of statistical process control in a non-manufacturing environment. Further, the tool, created on the basis of the theory, was applied in other industries throughout the country for many years. However, other mechanisms were created in parallel to help shape the new system of standards.
Appearance of the method in Japan
Total Quality Management TQM is a complex process that has been developed over decades in different countries. After the war, other American quality theorists, including Deming, who achieved hero status in Japan, advised Japanese industry on how to improve processes and outcomes to rebuild their war-ravaged economy. At the time, the Japanese-made term was synonymous with TQM. Already in 1945 suchvisionaries like electrical engineer Homer Sarason have talked about controlling the change process and monitoring for better results.
As a result, in the 1950s, TQM became the basis for Japanese manufacturing. Quality concerns not only management, but also all levels of the company. In the 1960s, quality circles began to appear in Japanese workplaces to allow employees to discuss problems and consider solutions, which they then presented to management. Starting from the factory, quality circles are extended to other functional departments. The system-wide emphasis on this may also provide a clue to the origin of the phrase universal quality.
Development of the US system
Total Quality Management Methodology TQM is also an assembled set of measures to optimize production. For the first time scientists from America started talking about it. By the 1970s, the term used in the US was no longer a badge of pride. Since the end of World War II, the main efforts of American factories have been to produce large quantities of items, maintain a production schedule, and save money. Application and durability rarely mattered until problems with lack of product quality reached high levels. As Japan successfully challenged the United States for industrial leadership, American industry has now taken a page from Japan's quality improvement book. A new interest in quality management emerged, building on the work of Shehart's students such as Deming, Josef Juran, and Kaoru Ishikawa in Japan. Influential businessmenthe likes of Philip Crosby championed this trend.
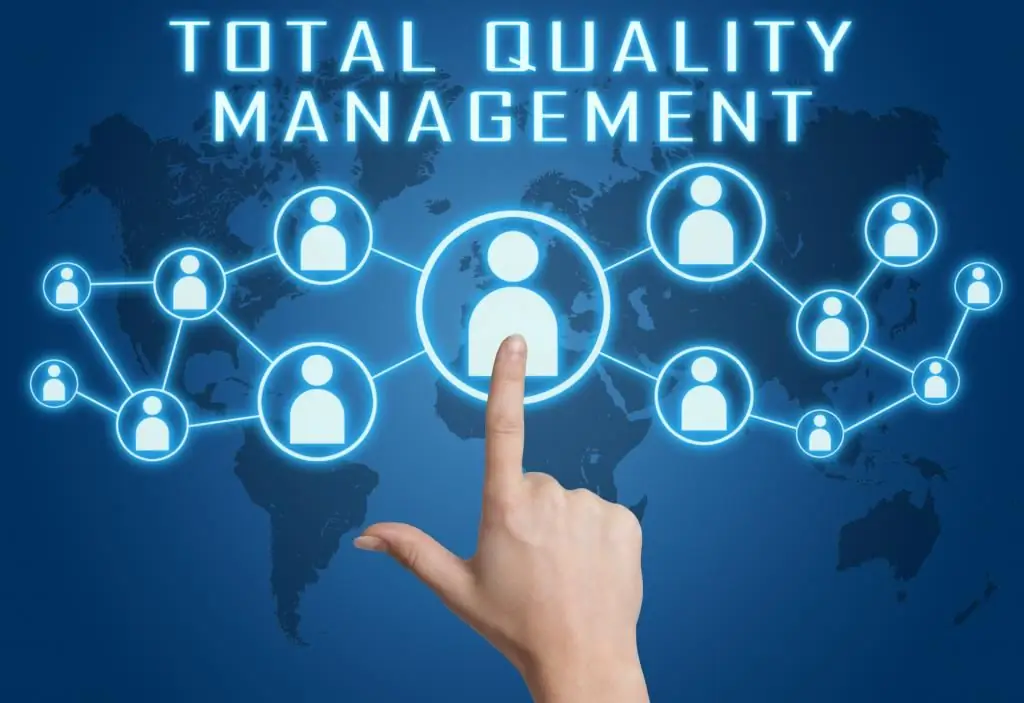
There have been many attempts to implement the TQM TPM system of total quality management. For the first time, the model proved to be an effective management tool in the military industry. Although the rise in demand appears to have taken place exclusively within the walls of industry, the main outlines of the concept are largely associated with the Navy project of the 1980s, which used the Shewhart PDKA (plan, do, check, act) model. and Deming. The Navy's guidelines articulated the idea that customer requirements should define quality and continuous improvement should be shared throughout the organization. The Navy's success with the methodology led to the adoption of TQM by other armed services such as the Army and Coast Guard, and eventually the rest of the US government. Congress established the Federal Institute for Quality in 1988 to emphasize the need for quality management in business and rewards for successful implementations.
TQM World Practice
Companies around the world began to pay attention to TQM TPM total quality management. Further, the system began to be distributed and change its appearance. Quality management began in manufacturing, and TQM, like subsequent methodologies, has adapted well to finance, he althcare, and other areas. The list of leading companies that have adopted TQM includes Toyota, Ford and Philips.
TQM quality as a steel planning modelintegrate into many companies. All over the world, countries such as Germany, France, the UK and Turkey have set TQM standards. But by the 1990s, TQM had been replaced by ISO (International Organization for Standardization), which became the standard for much of continental Europe and another 1980s methodological response to Six Sigma's quality problems. Nevertheless, TQM principles form the basis for much of ISO and Six Sigma. For example, PDCA appears as part of the Six Sigma DMAIC (Define, Measure, Analyze, Improve, Control) framework. And in the 2000s, the ISO governing body recognized TQM as the foundation of the philosophy. TQM lives on in data-driven methods to control all manufacturing processes.
William Deming's influence on the system
Much of our current understanding of the value and commitment to quality in TQM is tracked by the theory of William Deming. This American statistician, engineer and management consultant laid many of the foundations for the use of statistics in production and job management. He introduced statistical process methods to the US Census Bureau in the early 1940s, noting that they were first used in the business or service sector. During World War II, he taught American business and government about statistical methods to help with wartime production planning. After the war, Deming was hired by General Douglas MacArthur to advise Japanese officials to use census models to estimate war damage and rebuild. Deming distinguished himself frommany occupying forces, showing a sincere interest in Japan and its culture. Perhaps unsurprisingly, the Japanese revere him for his role in bringing about the Japanese economic miracle.
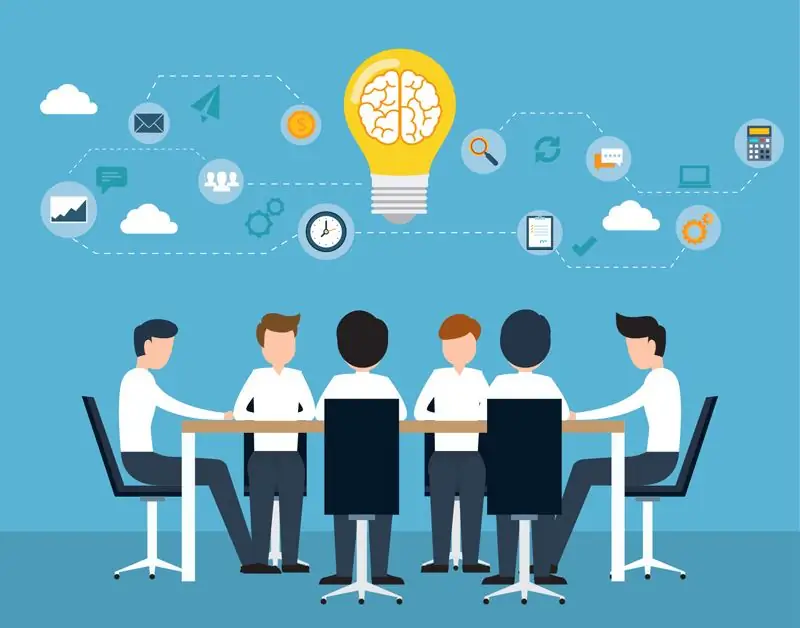
The total quality of TQM has influenced the development of markets in Asia. Because Japan did not have abundant natural resources, executives viewed exporting goods around the world as the main path to financial success. Their post-war reputation presented a particular challenge to this goal. Deming was invited to Japan by the Union of Japanese Scientists and Engineers (JUSE), of which Kaoru Ishikawa was president, to discuss quality management, the idea that formed the basis of what later became known as TQM. Japanese products have gradually been recognized as the best for convenience and durability. In 1960, on behalf of Japanese industry, Deming received the Medal of Merit from the Emperor of Japan. During the 1970s, Japanese exports surpassed US exports.
Total quality TQM was further used to compare different categories of goods from producing countries. As a result, American products gained a reputation for poor design and defects. As early as 1940, Juran noticed that the production of goods and meeting deadlines took precedence, and quality was relegated to the final check. Deming believed that once the war was over, the US industry would lose interest in statistical methods of achieving quality. Ironically, it was Deming who, in the late 70s and early 80s, introduced the principles of quality management to the United States and Great Britain,which he taught in Japan 30 years ago. In 1967, he published the article "What Happened in Japan?" in the journal Industrial Quality Control. Pros believe this is an early version of his famous 14 points and PDCA cycle.
The elements of TQM at each stage began to be traced in other management systems thanks to Deming. Although well known in quality control academia, the scientist achieved greater prominence when he was interviewed for the 1980 NBC documentary If Japan Can, Why Can't We? In the program, Deming stressed that if productivity gains are made, it will only be because people work smart. This is the total profit and it is multiplied several times.
The documentary featured another act in Deming's life that described him as a quality consultant for American business. He gained a reputation for being rude and fearless in the presence of senior leaders. Legend has it that he told Ford executives that 85% of quality problems were caused by poor management decisions. Some companies have rejected it. However, on his advice, Ford conducted user surveys before designing and building the Ford Taurus in 1992. The advantages of the TQM were clear and it was this car model that was in demand for many years.
In his 1986 book Out of Crisis, the scientist considered 14 points of control. The following year, at age 87, he was awarded the National Medal of Technology. In 1993, the year of hisdeath, he founded the Deming Institute.
Why the method matters to organizations
The elements of a TQM strategy become effective not when an organization creates a specialized quality department, but when it includes the entire company in pursuit of such a result. An example is the quality circle, in which workers directly involved in the brainstorming process discover solutions. People are an incredible resource that is often underused. Management does not recognize the value they bring to the everyday workplace. Employees know how to fix problems.
In addition to using your own resource, implementing the philosophy and development of TQM can help an organization:
- Ensure customer satisfaction and loy alty.
- Get more revenue and productivity.
- Reduce waste and inventory.
- Improve design.
- Move to changing markets and regulatory environments.
- Increase productivity.
- Improve the market image.
- Fix defects.
- Improve work safety.
- Improve employee morale.
- Reduce costs.
- Increase profitability.
Based on existing methods, it is possible to significantly improve not only the work of the team, but also speed it up. To do this, the company can select the necessary structure. The elements of TQM presented are general. Depending on the type of company and its product, not all of the above results may be achieved.
Expenses forimplementation
A fundamental principle of TQM is that the cost of completing tasks the first time is much less than the potential cost of reuse. There are also residual losses when customers abandon products and brands for quality reasons. Some companies view quality as a cost that cannot be recouped. Khuran, Deming and Feigenbaum took a different view.
There are four main cost categories:
- Appraisal costs. The costs cover inspection and testing throughout the entire production cycle. This includes verifying that the materials received from the supplier meet specifications and ensure that products are acceptable at every stage of production.
- Preventive costs. The costs include proper workplace setup for efficiency and safety, as well as preparation and planning. This type of expenditure also includes reviews. Prevention activities often receive the smallest share of a company's budget.
- External costs. This category refers to the costs of issues following the release of the product on the market. These may include warranty issues, product recalls, returns and repairs.
- Internal cost of failure. Internal failures are the costs of problems before products reach customers. Examples of internal failures include faulty machines that cause delays and downtime, poor materials, product waste, and designs that need rework.
Activemodels and rewards for them
The principles of the TQM system do not have a single generally valid body of knowledge. Organizations are trying to apply already compiled systems in their production to achieve the proper level of quality.
The Deming Application Prize was created in Japan in 1950 by the Union of Japanese Scientists and Engineers (JUSE) to recognize companies and individuals around the world for their successful efforts to implement TQM. The winners included Ricoh, Toyota, Bridgestone Tire and many more.
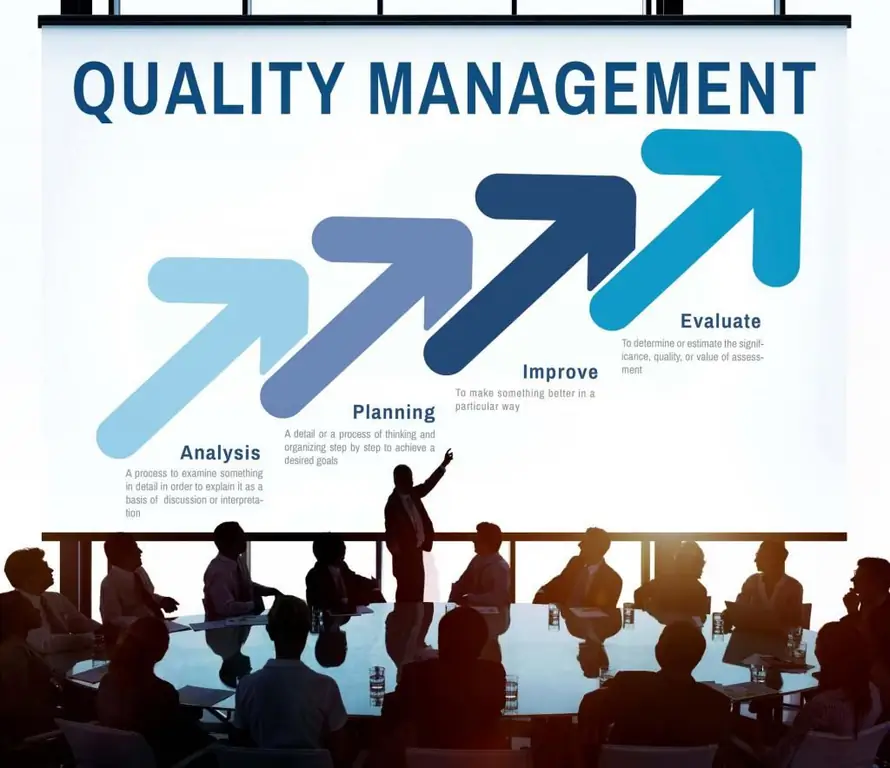
Congress established the Malcolm Baldridge National Quality Award (MBNQA) in 1987 to raise awareness of the quality of TQM models. The National Institute of Standards and Technology (NIST) administers the award.
It issues it to large and small companies and non-profit organizations that demonstrate excellent performance in the following areas:
- Providing growing customer and stakeholder value contributing to organizational sustainability.
- Improve overall organizational performance and capability.
- Introducing organizational and personal learning.
The non-profit European Foundation for Quality Management (EFQM) was established in 1989 to provide a quality framework for organizations across Europe and Russia.
They support the EFQM Excellence Model which covers the following prescriptions:
- Adding value for customers.
- Creating a sustainable future.
- Developmentorganizational capabilities.
- Using creativity and innovation.
- Comparison with vision, inspiration and integrity.
- Control with agility.
- Interest in people's talent.
- Keeping outstanding results.
Participating organizations may participate in training and assessment tools and may qualify for the EFQM Excellence Award. The International Organization for Standardization (ISO 9000) publishes guidelines and specifications for parts, processes, and even documentation to ensure quality is consistent throughout the company, organization, and system.
System management in an organization
TQM processes, like PDCA, are at the heart of many quality assurance efforts of the 20th century. PDCA began in the 1920s as a concept by engineer and statistician W alter Shehart. It was originally called PDSA (plan, do, study, act), widely used by Demin, who called it the Shewhart cycle. It is now often referred to as the Deming cycle.
Parse the wording of the PDSA method:
- P-Plan - The planning phase is the most important. This is where management, along with their peers, identifies issues to see what really needs to be addressed, namely day-to-day things that might be happening but that management is unaware of. So they try to determine the root cause. Sometimes employees do research or high-level monitoring to narrow down where the problem is.
- D-Do - The execution phase is the decision phase. Are being developedstrategies to address those problems identified during the planning phase. Employees can implement solutions, and if the solution doesn't work, it goes back to the drawing board. Unlike Six Sigma, this has less to do with measuring profits and more about what employees think of the job.
- S-Study - verification phase - before and after. So, after the changes are made, it becomes clear how they work in practice.
- A-Act - the current stage is the presentation or documentation of the results, so that all employees can see how it was done and what results were obtained. This is a new way, and this is what it should pay attention to.
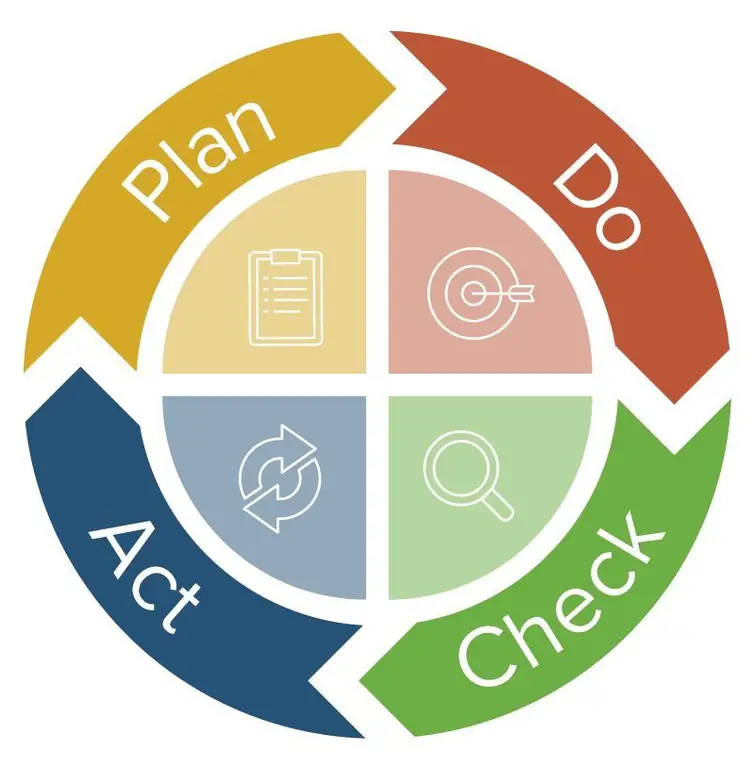
The introduction of TQM based on this principle made it possible to develop through the system and other methods. In 2000, ISO recognized PDCA as a fundamental method. It reappears in Six Sigma as a DMAIC (Define, Measure, Analyze, Improve, Control) method. W alters notes that TQM is much more about people, while Six Sigma is a process.
Where TQM, KAIZEN and SIX SIGMA apply
While TQM is used by employees as a source of ideas and solutions that can help companies, Six Sigma's focus on process and measurement drives data-driven decision making with undeniable benefits.
Through TQM techniques, most companies want to develop brand loy alty, even if their product is essentially the same as a competitor. If TQM is used, management hopes thatthe product will be of better quality, so customers must come back. With TQM, the organization will have to wait for customers to confirm that the product is really good. With Six Sigma, the company does not guess or assume how good the product is, in fact, it already knows it. If a firm correctly identifies its market and its product is the best fit for the niche, it knows it has the best product in terms of process. This leads to longer relationships with customers.
If Six Sigma can offer end-to-end results for an existing process, and the concept of TQM can help deliver results over time, the question is where Kaizen fits in. Kaizen is a Japanese word for the philosophy of improvement.
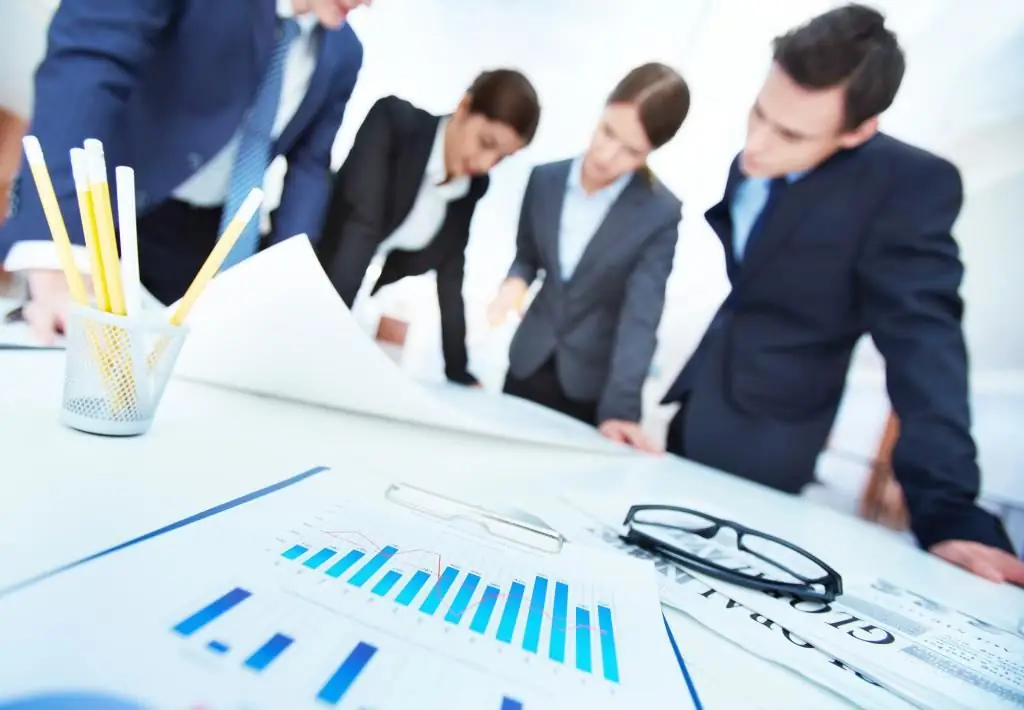
It includes 5 principles: seiri, seiton, seiso, seiketsu and shitsuke. Translated, they mean - sorting, ordering, brightness, standardization and support. Kaizen is seen more as a philosophy of organizing the workspace and place, about how to properly relate to work and colleagues.
TQM Quality System and Kaizen events are improvement efforts that involve small teams that spend a short amount of time, usually about a week, reviewing and testing improvements. The team then presents their findings to management. Management periodically reviews solutions to ensure they continue to benefit the team.
Like TQM, Kaizen is committed to results, the whole company is responsible for quality and that improvement shouldbe continuous.
Seven basic controls
According to experts, basic TQM strategies and controls allow anyone to collect data to highlight most problems and identify possible solutions.
Here are the seven basic TQM tools:
- Control sheet. This is a preliminary form for collecting one type of data over time. Therefore, it is only useful for frequently repeated data.
- Pareto chart. The chart shows that 80% of the problems are due to 20% of the causes. This helps determine which issues are categorized.
- Diagram of causes and effects or Ishikawa diagram. This diagram allows you to visualize all the possible causes of a problem or effect and then categorize them.
- Control chart. This chart is a graphical description of how processes and outcomes change over time.
- The bar chart shows the frequency of the problem and how and where the result cluster works.
- Diagram of axes. This chart plots data on the x and y axes to see how the results change as variables change.
- Flow diagram or stratification diagram. This is a representation of how different factors come together in a process.
Main members
To be successful with a total quality management program or any other improvement methodology, managers must understand the quality improvement goals for their product or company. Then they must communicate those goals,despite the benefits of TQM, companies as employees play a vital role by contributing to day-to-day knowledge of product creation and processes.
Suppliers are an important part of the system. Companies must screen new agents to ensure materials meet standards.
Customers are the most important part of management. After all, they are the cause of the TQM Total Quality Management system. In addition to the obvious feedback provided by the sales team, customers - users of products or services - provide information about what they want from the product in the future.
Certificates issued to organizations
Since its heyday in the 1990s, TQM has been largely superseded by Six Sigma and ISO 9000. The fact is that Lean and Six Sigma have a very specific set of methods to achieve these goals effectively. ISO is a universal standard and it is very clear to companies what they must do to achieve it.
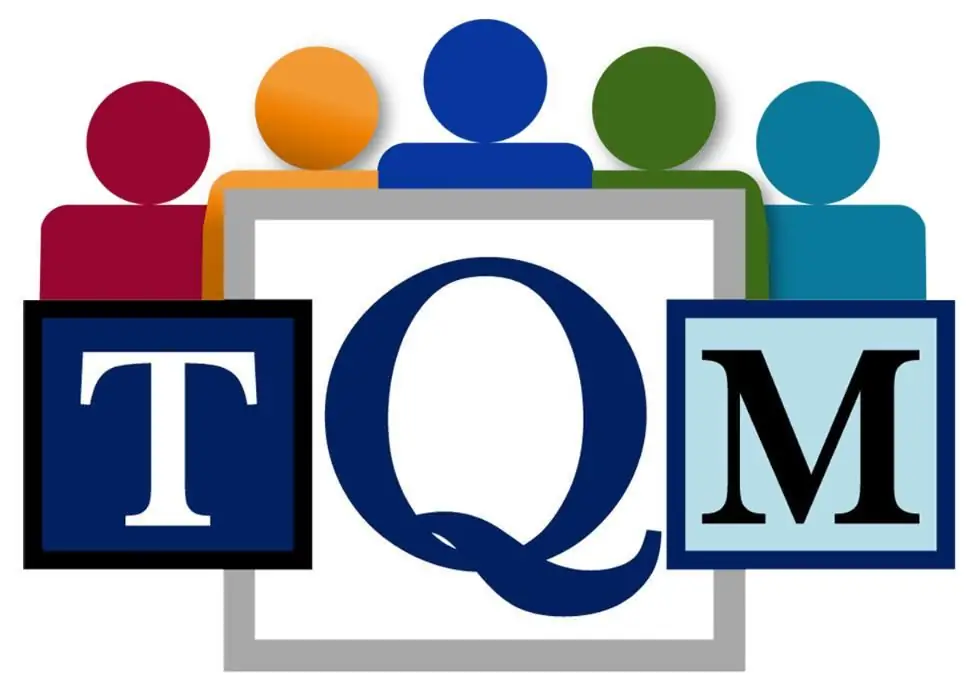
Obtaining one of these types of certificates empowers a company and sets it apart from its competitors. Europe and Russia adopted the international ISO standard in the 1990s. Today, formal training in TQM as TQM is rare. The main users of the TQM system are organizations located in Japan and the United States. Therefore, already at the initial stages of the formation of a new management system, management and employees should decide on a common model thatwould work more efficiently in a specific market where the manufactured products will be supplied.
Recommended:
"Quality Circles" is a quality management model. Japanese "Quality Circles" and the possibilities of their application in Russia
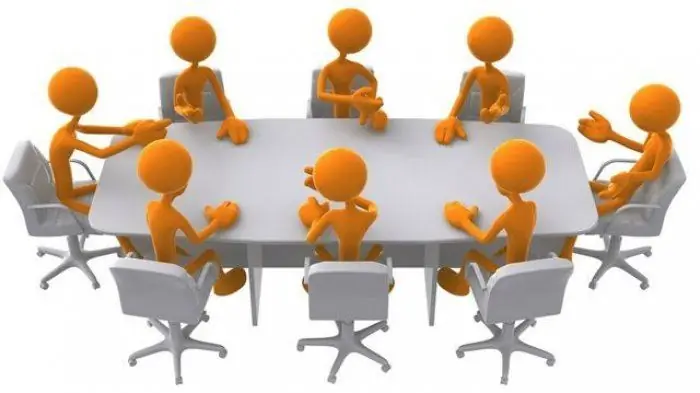
Modern market economy requires companies to constantly improve their technological processes and staff training. Quality circles are a great way to involve active employees in the workflow and implement the most productive ideas in the enterprise
Administrative management: directions, administrative and classical methods, features and principles
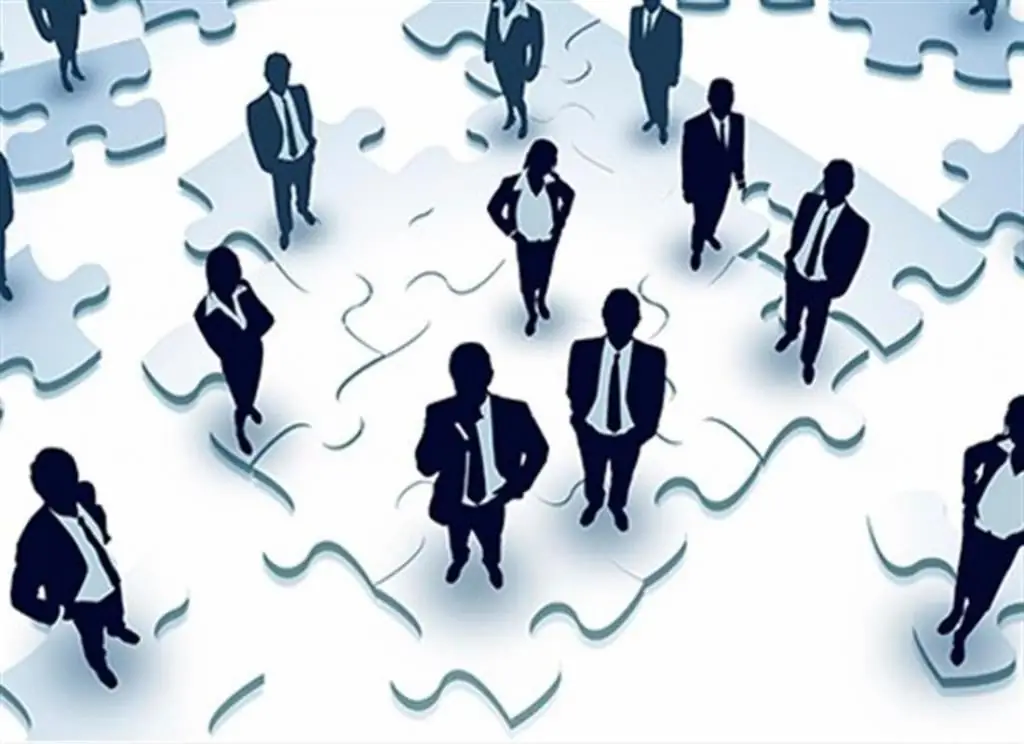
Administrative management is one of the directions of modern management, which studies the administrative and administrative forms of management. At the same time, administration itself is an organization of the actions of personnel, which is based on formalization, strict incentives and strict regulation
Centralized management: system, structure and functions. Principles of the management model, pros and cons of the system
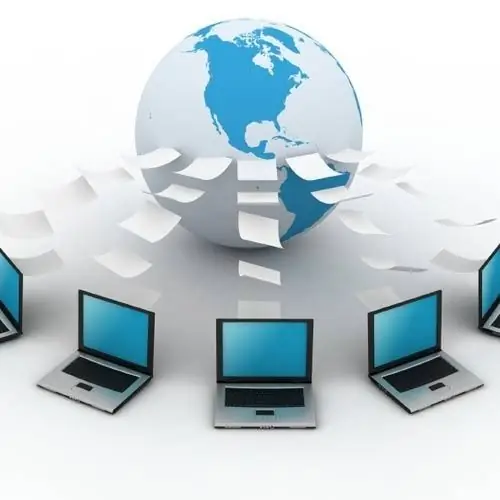
Which management model is better - centralized or decentralized? If someone in response points to one of them, he is poorly versed in management. Because there are no bad and good models in management. It all depends on the context and its competent analysis, which allows you to choose the best way to manage the company here and now. Centralized management is a great example of this
Project implementation methods. Methods and tools for project implementation
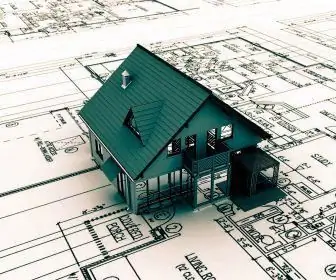
The term "project" has a specific practical meaning. Under it is understood something once conceived. The project is a task with some initial data and goals (required outcomes)
Quality policy at the enterprise: management, quality improvement. Examples
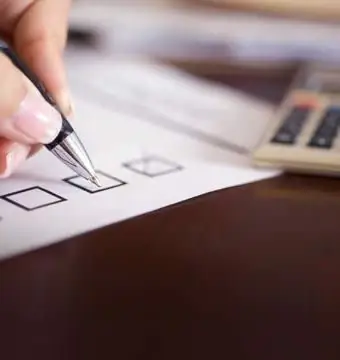
Quality policy - these are the main goals and directions of the organization that relate to the quality of its product