2025 Author: Howard Calhoun | [email protected]. Last modified: 2025-01-24 13:10
The market economy is a constant and uncompromising struggle for clients, finances and high-level specialists. Any production begins with the work of each employee and depends on the personal contribution of each employee to the common cause of the company. Only if this condition is met, it is possible to build a competitive high-tech production. The problem of stimulating employees is especially acute in large industrial enterprises. Raising salaries does not always lead to an increase in the results of company employees. You can stimulate creativity and employee engagement with quality circles.
Quality Circles over the 40 years of their existence have allowed a number of companies to take a leading position in the world. At the moment, there are about a million quality circles that unite more than ten million people in the USA, Japan, China, South Korea, Germany and 50 other countries.
Definition
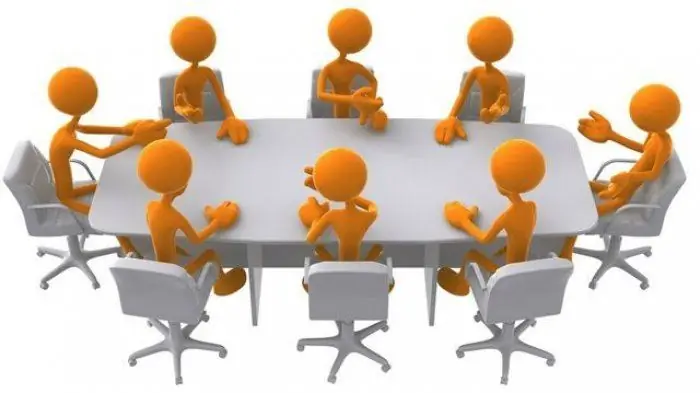
Except existing ones onIn the enterprise of product quality management systems, whose activities are aimed at improving the quality characteristics of the final product, many enterprises introduce quality circles into the working environment. This experience is applied, as a rule, at foreign enterprises. Many leaders in our country mistakenly believe that this system cannot exist in Russia, especially in small enterprises. But this judgment is fundamentally wrong.
Quality circles are a form of stimulation for working groups of 5-10 people. At the heart of the circles is the personal interest of everyone in improving the product and simplifying the workflow. Groups meet on average once a week. The agenda includes issues of product quality, labor productivity, work speed, deadlines, working conditions, compliance with safety regulations, team relationships and many others.
Meetings are held before the start of the working day or after the completion of work. Employees of one workshop or department, as well as higher-level managers, are involved in the discussion. This gives employees the opportunity to express their opinion directly to superiors, avoiding paperwork and saving time. Management gets the opportunity to quickly solve urgent tasks that require permission from higher authorities. For managers, quality circles are an opportunity to listen to employees' ideas for improving the workflow and evaluate the creativity of each employee.
Experience of Japanese specialists
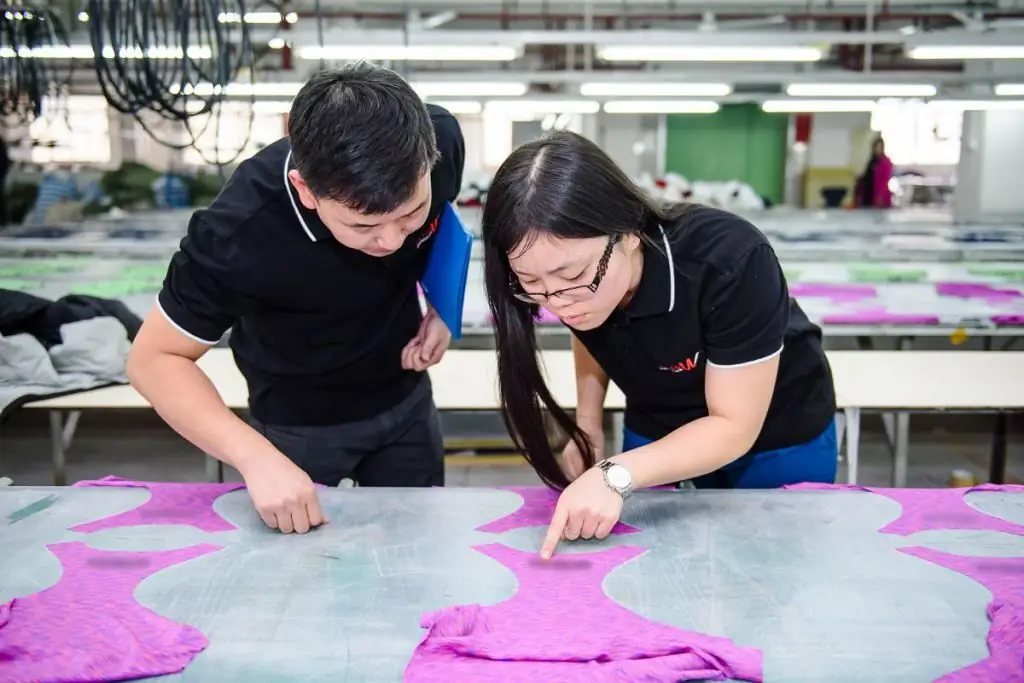
Mugsqualities invented by Japanese experts. In the 60s of the last century, Japanese company executives began to face a decline in the quality of their products. The reason was the decrease in the degree of satisfaction of workers with monotonous work and simple tasks. Monetary reward ceased to have a stimulating effect. Bonuses grew, but the quality of work remained unchanged. Basically, this was due to the development of the quality of education in Japan. About 93% of the population in Japan have higher education, this is the best indicator in the world. Employees needed intellectual work, involvement in solving complex production problems.
How did quality mugs appear in Japan? Employees of the enterprise independently began to unite in small groups to discuss current problems and coordinate their search for solutions. Company managers who noticed the trend began to stimulate and encourage such an initiative. Meetings that take place outside of business hours are paid. And in order to promptly resolve issues, these meetings of employees began to be attended by top managers.
The emergence of Japanese quality circles prompted workers around the world to create similar initiative groups that sought to achieve zero-defect production, discussed issues of safety, technical support and much more. The experience of workers from Japan was greeted with incredible enthusiasm. This model is also used in automated production. With the help of such circles, workers are retrained, who were replaced by robots.
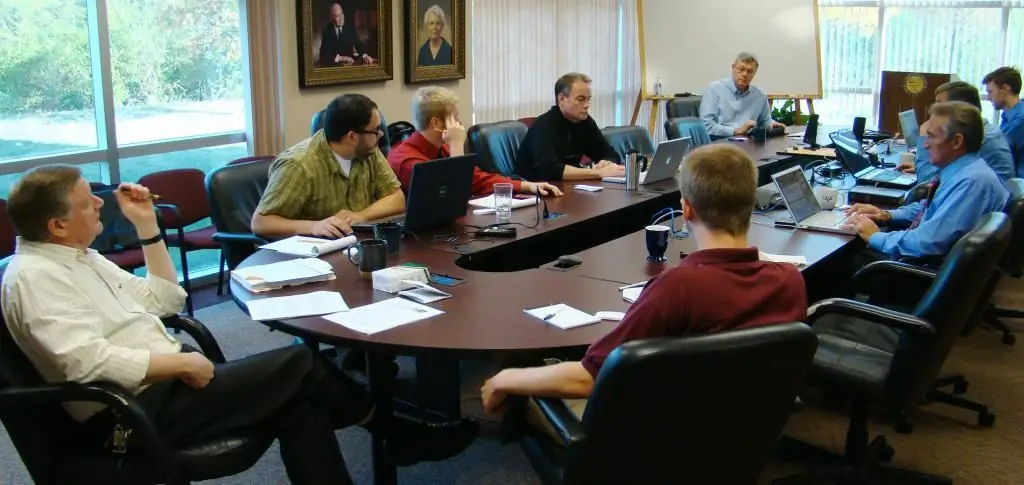
Quality Circle Ideas
The essence of quality circles comes down to a set of ideas:
- Teams are created to improve production quality, eliminate product defects and reduce scrap rates.
- Mugs are designed to improve the economic performance of the enterprise, reduce production costs.
- Groups are a strong motivational boost for employees and enhance corporate culture.
- Quality circles are a way to create democratic relationships with a high degree of respect for each member of the team and their work.
- Teams stimulate the involvement of all levels of company management in the production process.
- Quality circles strengthen he althy competition among employees, contribute to the prompt resolution of conflict situations.
- Group work distracts workers from day-to-day problems in the workplace and increases their involvement in the production process.
Goals of quality circles
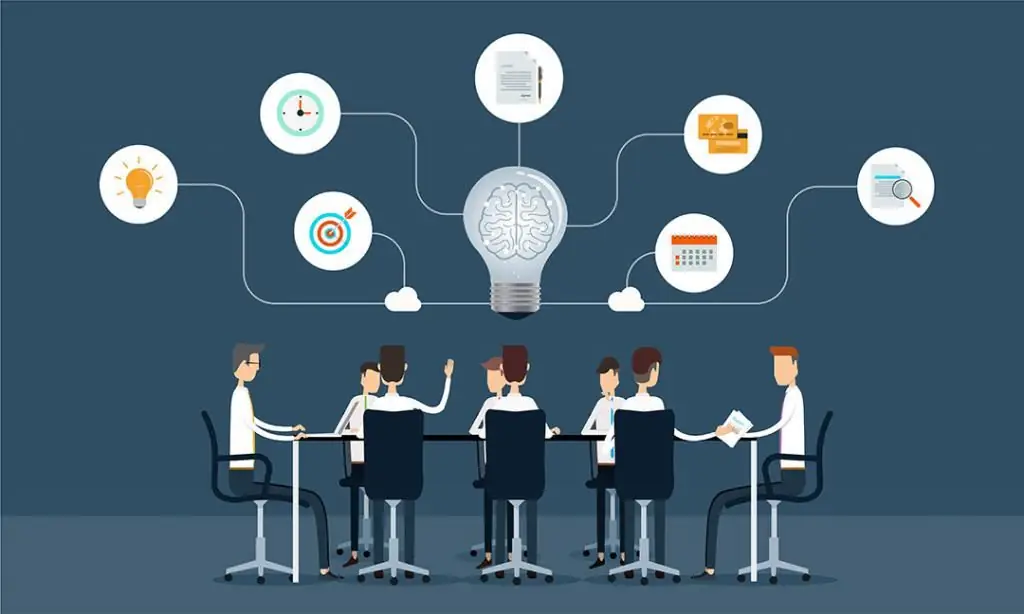
Goals of creating quality circles at the enterprise:
- Searching for new ways of effective management by lower-level managers and shop supervisors.
- Improving the moral attitude of workers to the production process, creating conditions for the independent development of employees.
- The interest of each person from the group in improving quality characteristics, reducing the level of marriage and product defects.
Create a group
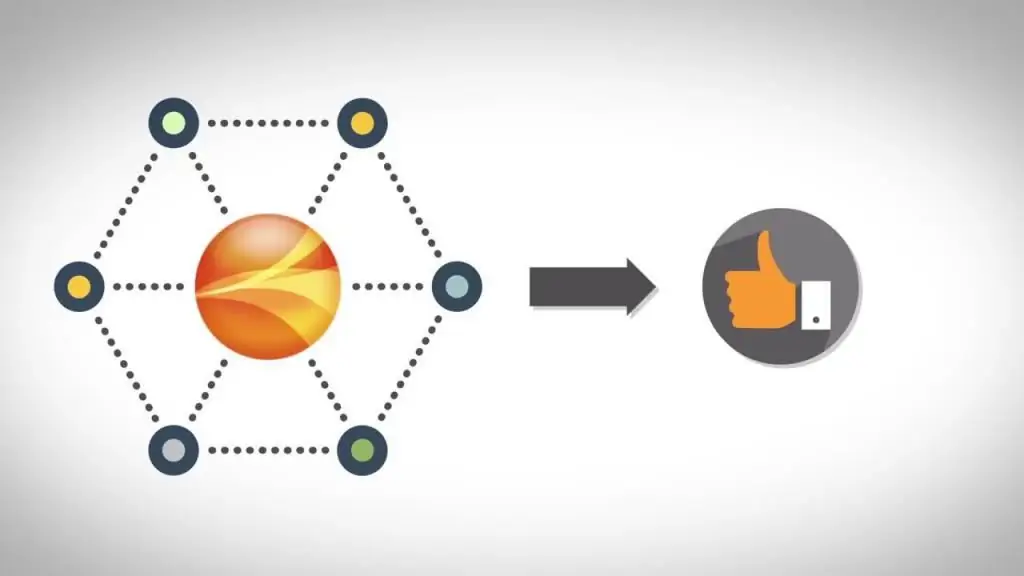
The quality circle method requires certain workers to be included and others to be excluded. The group should be holistic and consist of people interested in improving the quality of work and self-improvement. At the same time, each member must perform their functions and help the rest of the team members.
Who should be involved?
- Informal group leaders. To identify such employees in the team, it is enough to invite each of them to make a proposal for discussion. Those whose proposals will receive the most positive responses will be informal leaders.
- Employees whose professional experience is not questioned. Such a person has great authority among colleagues and has sufficient skills and abilities to train other employees.
- Enthusiasts. Even under the condition that these people are “new” in the team, such personnel are able to quickly learn and betray their interest in the work to other members of the team.
Who should be excluded
This question is fundamentally important for many. Nobody wants to be redundant. However, the experience of Japanese specialists suggests that such workers should be excluded from the circle:
- Relatives of the commanding staff. This may cause a negative reaction in the group.
- Those employees whose opinion is ignored by the group.
- Employees who are in a difficult life situation (debts, divorce), as they, with any motivation, do notwill be able to fully concentrate on solving work tasks.
- Negative workers. This category includes people who have a bad attitude towards their work, organization, the idea of creating quality circles.
- Conflict people. They undermine the atmosphere in the team and do not accept new ideas.
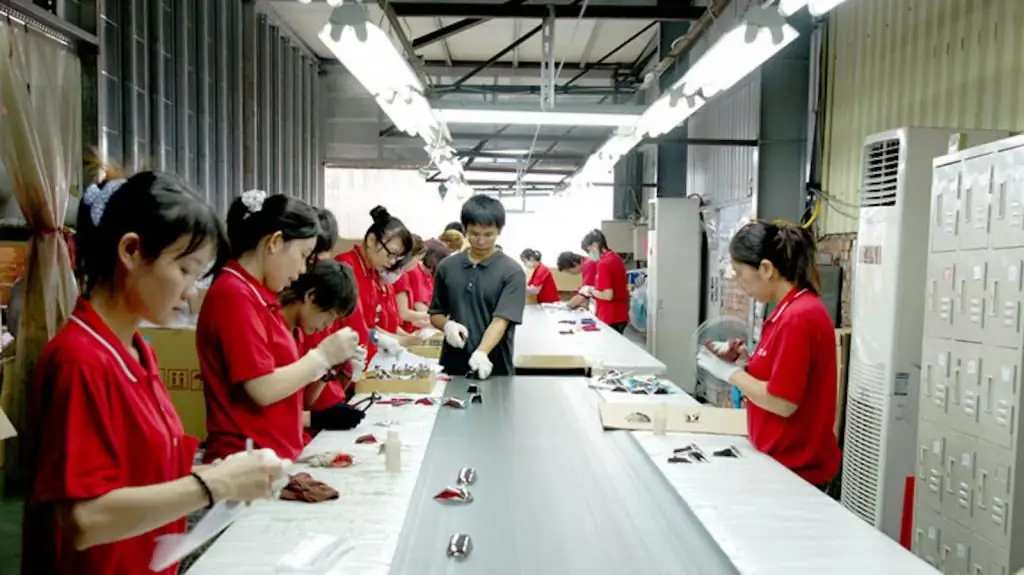
Building steps
Let's see how these circles are created.
- Presentation of the idea to potential group members. At this stage, you need to talk about the system of quality circles, the idea and mission. The issue of obtaining the benefit of the participants should not be overlooked. If the company already has a positive experience in introducing circles, then it is worth mentioning it. The main thing is to interest.
- Define roles. It is necessary to determine who will play the role of leader, who will fix all ideas on paper, who will implement new tasks in production.
- Conducting classes. To do this, select non-working hours. According to studies by Japanese companies, efficiency can be achieved by conducting classes 2 times a month for 1.5 hours. Next, you need to determine the methodology for creating the agenda. For example, ask participants in advance what they would like to discuss at the upcoming meeting.
- Discussion and recording of results. Here it is worth discussing in advance with the participants the etiquette that they must adhere to during the speech of colleagues. In addition, it is worth thinking about how the most effective solutions will be selected. Possibility of voting.
- Introduction. The purpose of quality circles isnot only the discussion and implementation of new technology in their workplace, but also the involvement of the rest of the team members in innovation.
Quality circles in the USSR and Russia
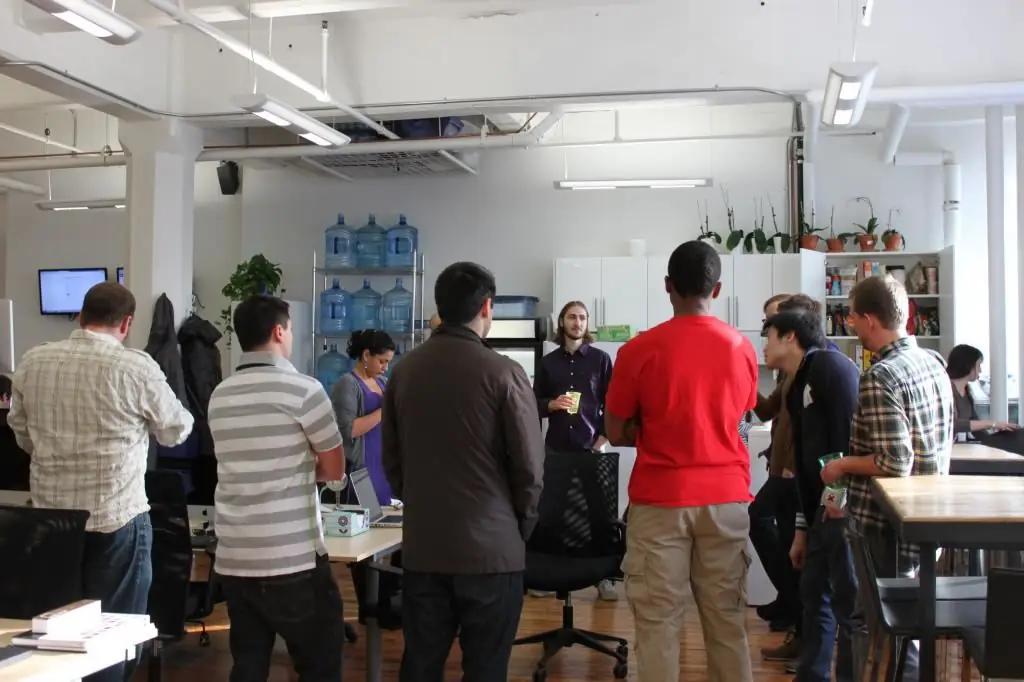
It's no secret that everything new is well-forgotten old. And in the 80s of the last century, they already successfully began to introduce quality circles in the USSR. In 1990, the number of circles reached 55,000. Many modern Russian enterprises continue this tradition. Often quality circles in Russia are called "talkers". Meetings are held once or twice a month. They discuss current problems and ways to solve them. Now they are trying to introduce quality circles not only in industrial production, but also in other areas of activity. This is important because in the battle to enter the export market, quality is key. There are international standards that not all Russian companies meet yet.
Conclusion
Quality circles are an almost free way to improve the quality of the final product, involve heads of departments and workers in the process of creating products, improve production technology, and create a competitive environment among employees. Each participant feels his involvement in the affairs of the company, participates in its development and management. All this leads to profit growth and further development of the enterprise.
Recommended:
Japanese Brands: Products, Brand Names, Top Best Brands and Famous Japanese Quality
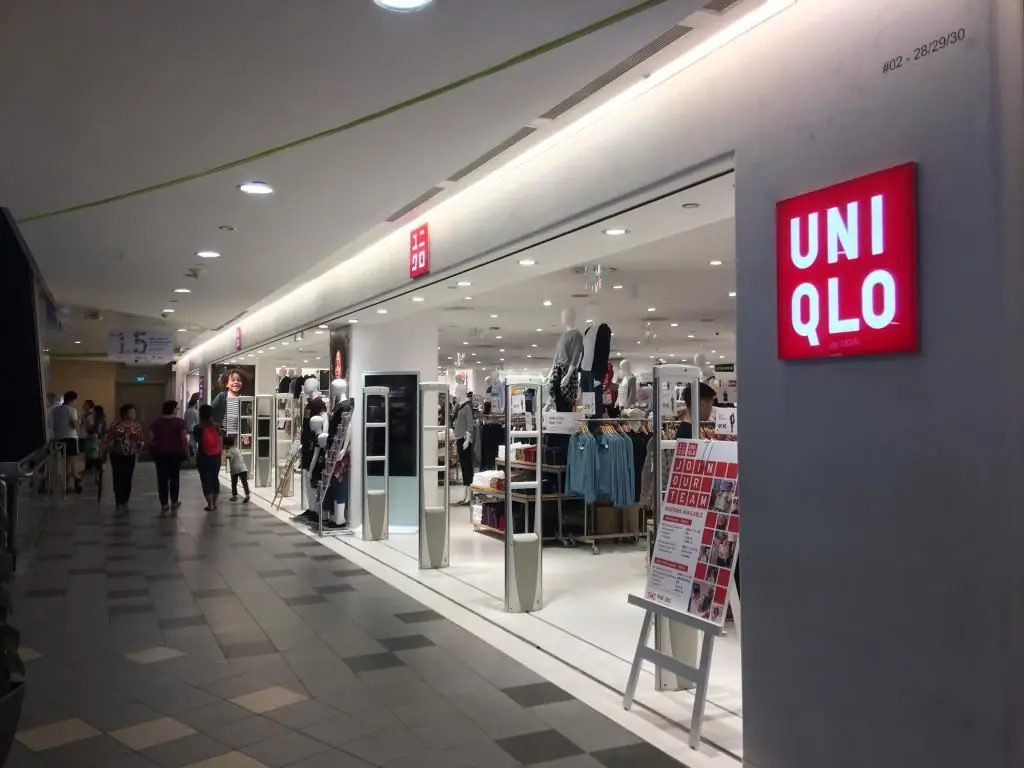
Every kind of goods is produced in Japan. Given the huge number of manufacturers, it is often difficult for the buyer to decide on the choice of products. Everyone knows what Japanese brands of cars and household appliances exist. But this country also produces excellent clothes, perfumes, and cosmetics. We offer a rating of brands of these products
Centralized management: system, structure and functions. Principles of the management model, pros and cons of the system
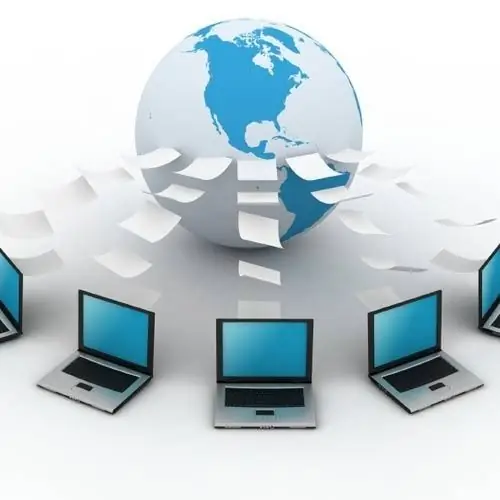
Which management model is better - centralized or decentralized? If someone in response points to one of them, he is poorly versed in management. Because there are no bad and good models in management. It all depends on the context and its competent analysis, which allows you to choose the best way to manage the company here and now. Centralized management is a great example of this
Reserves of banks and their formation. Required bank reserves and their norm
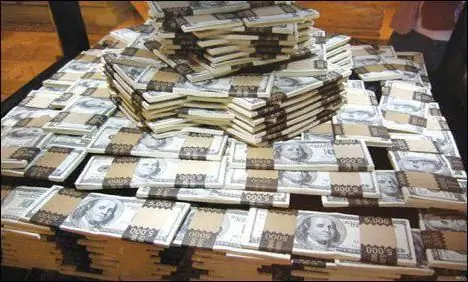
Bank reserves ensure the availability of funds for the uninterrupted fulfillment of payment obligations regarding the return of deposits to depositors and settlements with other financial institutions. In other words, they act as a guarantee
Pulse welding: advantages and possibilities
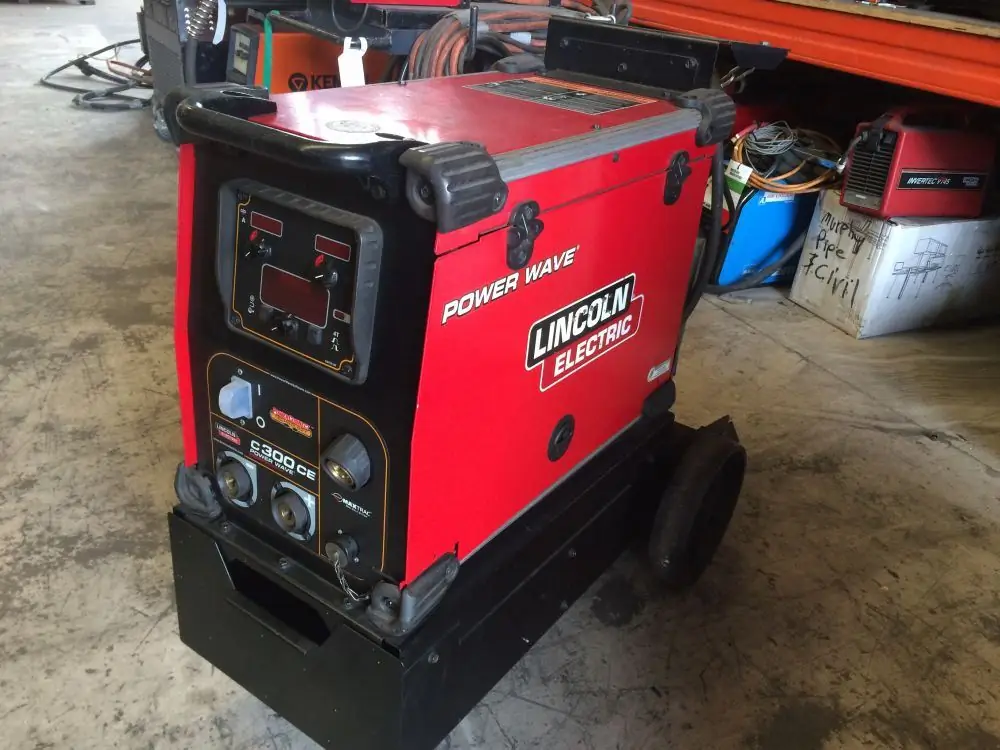
Semi-automatic welding in protective gas environments is by far the most advanced technological approach to the implementation of metal joints. But even this group of welding methods is not free from shortcomings, which manifest themselves both in the splashing of the melt and in the difficulties of maintaining the standard parameters of the arc. Pulse welding, which requires the use of special equipment and compliance with special organizational rules, helped to solve these problems in many ways
Event management is the management of the organization of events. Event management and its development in Russia

Event management is a complex of all activities carried out to create mass and corporate events. At the same time, the former are called upon to provide powerful support to advertising companies, while the latter are aimed at strengthening the spirit within corporations