2025 Author: Howard Calhoun | [email protected]. Last modified: 2025-01-24 13:10
During the preparation of the budget, sales and production plans are transformed into indicators of income and expenses of departments. In order for each of the departments to be able to achieve the intended goals, it is necessary to purchase materials within the cost plan. For this purpose, a procurement budget is being formed.
Procurement Organization Model 1
The first step is to determine the purpose of creating a purchasing department. Based on the specifics of the product and the number of suppliers, it forms a department of 2-5 people (maximum 7 suppliers per manager). Each of them is responsible for the timing of deliveries, the state of stocks, payments, and the implementation of contracts. The work of the department cannot be carried out only on the instructions of the head. The division is created to implement the sales plan, which is drawn up for the month, quarter and year. A bonus is provided for his fulfillment of the plan:
- basic income: 40% for a manager, 60% for an executive;
- bonuses: 50% - for the manager, 30% - for the head;
- premium - 10%.
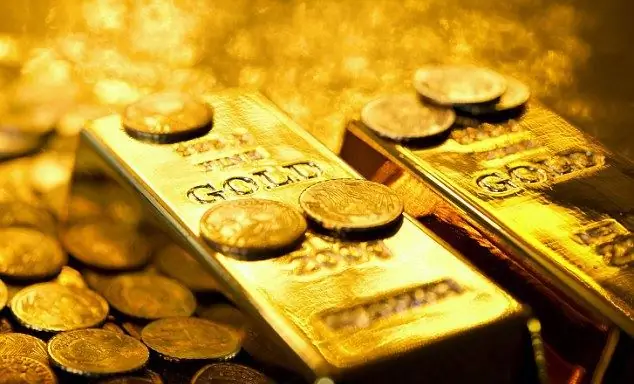
Bonuses for managers are accrued based on performance indicators:
- delivery on time;
- volume of illiquid goods;
- average inventory turnover.
For bonuses, you can also use qualitative indicators, for example, the service coefficient, that is, the number of goods in the application, which can be satisfied immediately.
Procurement Organization Model 2
This scheme differs from the previous one in that, based on the sales plan, the head of the department calculates the purchase budget. That is, a separate financial control center is created within the unit. A more efficient selection of managers is carried out, since logistics costs and delivery conditions are taken into account. All employees are interested in the implementation of the procurement plan, and hence the development of the company. In turn, management will be able to reduce the kickback scheme to a minimum.
It will take 1.5-2 months to build the first work model. The task of the director is to recruit staff with experience. In the second case, it will take 6-18 months to build a department. The main problem lies in the psychological work. The director needs to turn employees into individual businessmen. Not everyone can handle this role.
Operational planning
The operational budget reflects the planned activities for the year for a segment or a specific function of an enterprise. It is developed in all responsibility centers and then consolidated into one consolidated budget. Drawing up a document can be considered as an accounting and management process. The difference lies in the fact that the report reflects the activities of the enterprise in the future, and notfixation of previous events. It consists of budgets for purchases, sales, administrative, production costs. Let's look at each of these elements.
Sales
The volume of sales and its structure determine the nature of the enterprise. Therefore, one of the first is a sales plan. When preparing it, one must take into account not only sales for previous periods, but also analyze the factors that may affect them (seasonality, promotions, etc.).
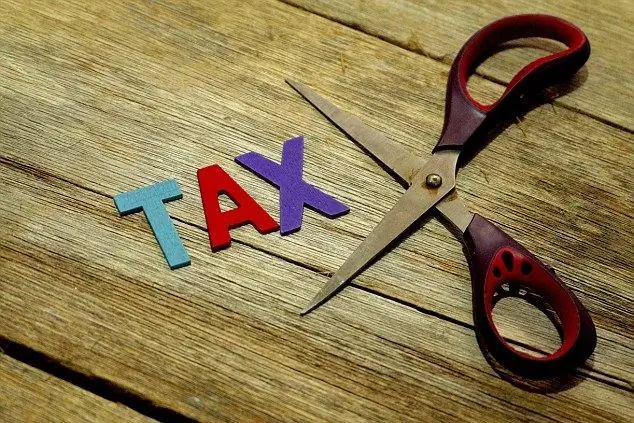
The sales budget is compiled taking into account the level of demand, geography of sales, buyers. It includes a target level of revenue that can be reflected in the cash budget. But the calculation of this indicator causes difficulties, since the company cannot manage the actions of customers. The planned amount of expenses is calculated based on the activities of the organization. It's the easiest to calculate. Sales as a business process is of great importance. For organizations that are engaged in the sale of products, it is the sales plan that sets the error in the calculations. If it is written incorrectly, it will affect all other areas of activity.
Production and stocks
Product release plan is based on sales volume. It also takes into account production capacity, inventory changes, and purchasing budgets. The calculation is carried out according to the following formula:
Product output=stock at the end of the period + sales volume - stock at the beginning of the period.
The volume of production is calculated based on the characteristics of the production of products.
Overall production costs are those associated with the manufacture of products. At the same time, a separate line takes into account labor costs in two parts: fixed and piecework (employee bonuses based on the implementation of the production plan).
Budget for commercial, administrative costs
Selling expenses are all costs associated with the sale, promotion of goods. Their volume depends on decisions in the field of management. The decision to change the area of the premises will affect the costs associated with the storage of goods. The amount of variable costs is formed by the commission, the cost of packaging, processing, transportation. All other fixed costs are administrative.
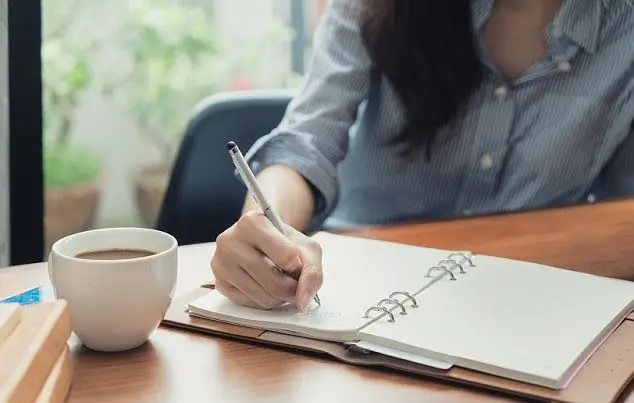
Procurement budget
Procurement plan by type of goods or by suppliers shows how many products the company should purchase from external and internal suppliers. The procurement budget is formed based on the sales plan, inventory level, production workload, terms and procedure for repaying accounts payable.
Purchasing=planned usage + end-of-period stock - start-of-period stock.
Stocks for production
The need for permanent production materials is determined by the cost of equipment repair, construction plan and preparation of new products. Often economists make the mistake of ignoring these costs when budgeting.
The planned amount of expenses depends on the type of resources and how they are consumed. The budget is formedbased on the norms of resource consumption in production, in economic centers and the need for fixed assets. The first article is calculated by multiplying the planned production volume by the norms. This requirement is adjusted for stock balances and inventory standards. This is how the procurement budget is formed in kind. To convert it into value terms, you need to multiply by the planned price.
Example
Steel plant plans to produce 3,000 tons of products next year. This will require copper and oleic acid. Consumption rate per 1 ton: copper - 0.06 kg, acid - 0.0058 l. The balance of copper at the beginning of the year is 100 kg, and at the end - 50 kg. The price of raw materials is 4,500 rubles. /t. copper and 10,000 rubles. / liter of acid.
Need for the year:
- 30000, 006=180 kg of copper
- 30000.0058=17.4 liters of acid
Planned purchase volume:
- (180 kg / (100 - 50))4500=1,035,000 rubles. - for copper.
- (17, 410,000)=174,000 rubles. - for acid.
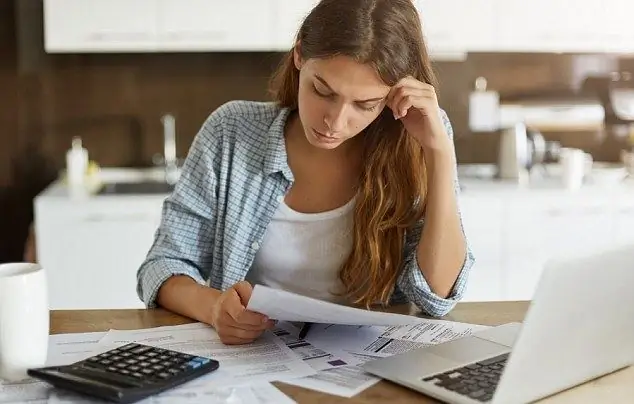
ADC stocks
Procurement budget planning in administrative and economic activities (AHA) is carried out differently. The range of goods is very wide (from stationery to materials for office renovation), and there are no consumption rates. There are three ways to determine inventory requirements:
- Use requests from structural units. The supply service collects applications, processes, evaluates balances, updates prices and calculates the budget.
- Installinventory standards for the most popular items, such as stationery, detergents. The budget is calculated based on available stocks.
- Set a stock purchase limit for AHD as a percentage of the cost of basic materials.
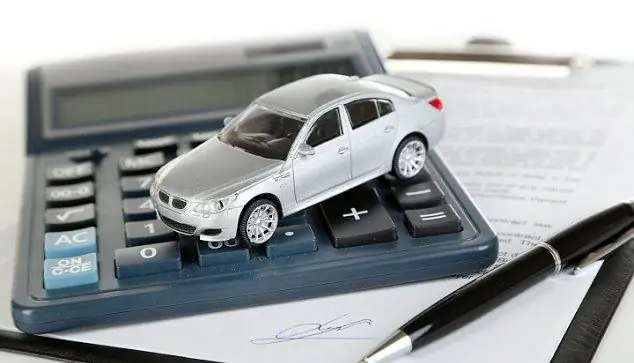
Special attention should be paid to the compilation of stocks to identify excess resources. When forming the procurement budget, such materials should be adjusted downwards. Especially if the supply is not limited.
Procurement budget functions
- A budget is a planning tool that indicates how resources can be used based on opportunities. It is also a means of monitoring and evaluating performance by comparing planned and actual indicators.
- The work of managers can be assessed by the structure and degree of implementation of the procurement budget. Organizations use them to evaluate the performance of their management units.
- The budget of the purchasing department can perform a motivational function if it contains the goal of the activity. For example, the department was given the task to purchase raw materials for half a million rubles on a post-paid basis. If the goal is achieved, then the head and his deputies will receive a bonus, which will increase the expenditure side of the budget in the next period.
- The employee must understand what tasks are set for him. If the organization's development goals are kept secret, they will not be achieved. In this sense, the budget forms the communication environment in the team, as well as betweenemployees and subordinates.
Work with tenders
In order to form a budget for the purchase of materials, tenders can be held - to find the best suppliers of goods of a certain category. According to the regulatory documents, a strategy is developed for distributing materials by groups, quality indicators, and counterparties are classified. A tender list with suppliers' proposals is being formed. The "winner" is automatically determined according to the specified evaluation criteria. Further, work is underway to conclude a contract and form a procurement budget.
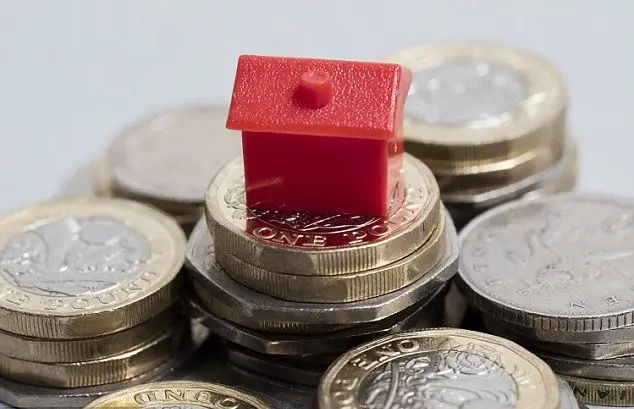
Purchase options:
- One batch. It simplifies the process of preparing documents, but the organization will need large warehouses to store supplies. The risk of losses caused by product spoilage increases.
- Small batches. Rapid capital turnover and reduced storage space.
- As needed. The goods are delivered on invoices (without concluding a contract) in small lots on a full prepayment basis.
Procurement control
In order to control the implementation of the budget, purchases can be calculated by financial responsibility centers. At the same time, planning is carried out at two levels:
- Forward-looking management - the formation of the need for materials for the year, broken down by quarters / months. After the formation of the annual plan, the selection of suppliers and the conclusion of long-term contracts are carried out.
- Calendar management - the formation of monthlyand ten-day / weekly plans for the purchase in order to uninterruptedly supply the enterprise with specific raw materials. This is the annual plan detail.
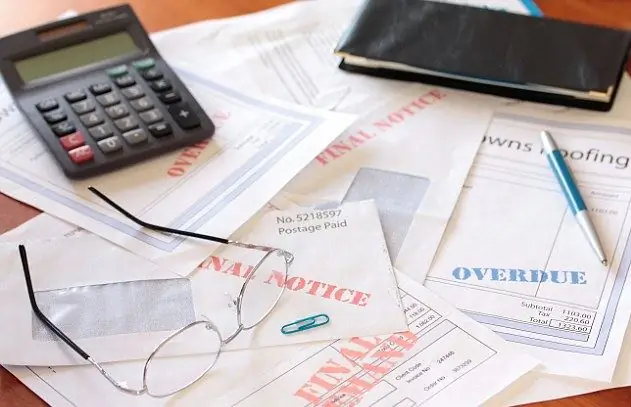
In order to calculate the monthly purchase budget, you should follow this algorithm:
- Calculate the need for materials for production, taking into account current balances, expected receipts and safety stocks.
- Requirement is adjusted for orders, items and allowed replacements.
- In case of changes in production plans, the purchase budget is adjusted.
- A schedule for the delivery of raw materials and a payment plan for suppliers is being formed.
- If the delivery fails, a step back is made and a new supplier is selected. If it is not possible to change the supplier, a change in the procurement or material grade is initiated.
Here's how to budget your purchases.
Recommended:
Contributory pension: the procedure for its formation and payment. Formation of insurance pension and funded pension. Who is en titled to funded pension payments?
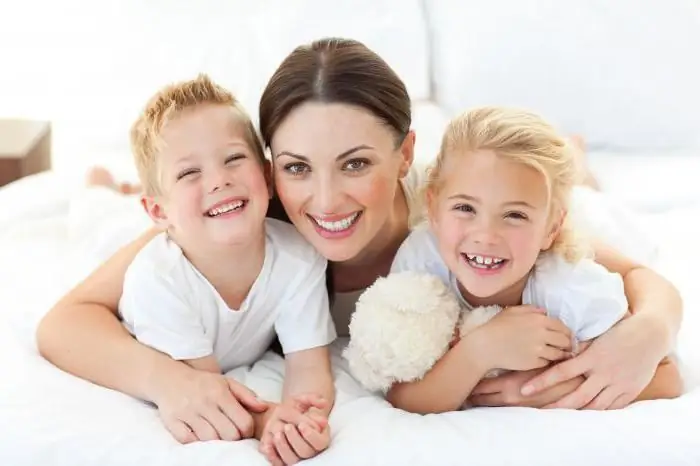
What is the funded part of the pension, how you can increase future savings and what are the prospects for the development of the investment policy of the Pension Fund of the Russian Federation, you will learn from this article. It also reveals answers to topical questions: "Who is en titled to funded pension payments?", "How is the funded part of pension contributions formed?" and others
Product manufacturability indicators: types of indicators and evaluation methods
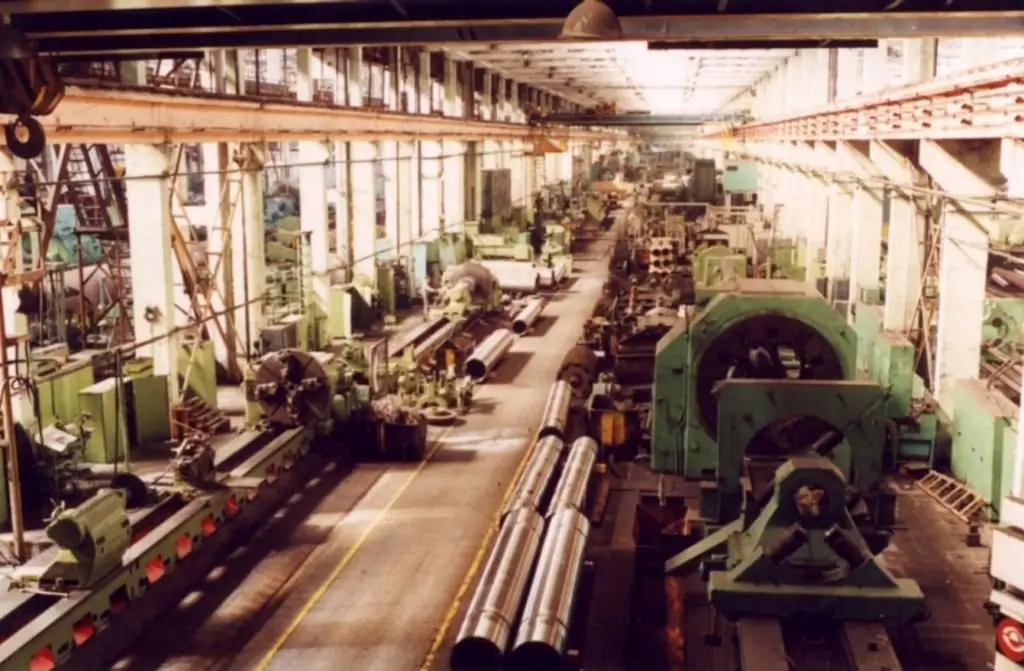
Product manufacturability indicators are the most important component of assessing the quality characteristics of products, designs, parts, and so on. They make it possible to compile a comprehensive description of the effectiveness of technological products in relation to the adaptability of the design to its application in specific conditions, for example, in production
How to find out the budget classification code? Budget classification codes for taxes
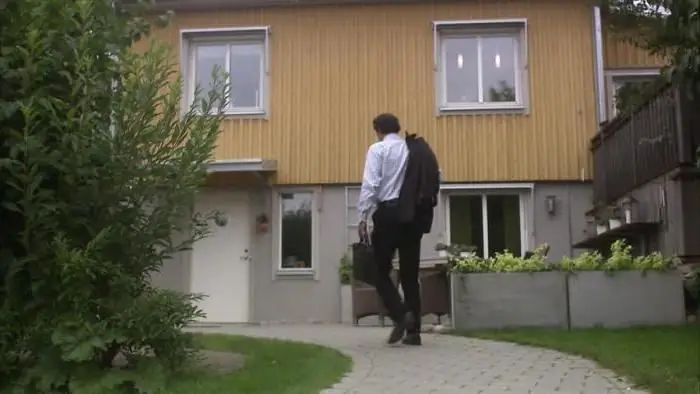
The problem of how to find out the budget classification code arises in front of almost every taxpayer when the deadline for paying taxes comes. No one can avoid it: neither the accountant of the organization responsible for the relevant transfers to the tax office, nor ordinary citizens who own housing, land, a car or a simple outboard motor
Good Forex indicators. The best Forex trend indicators
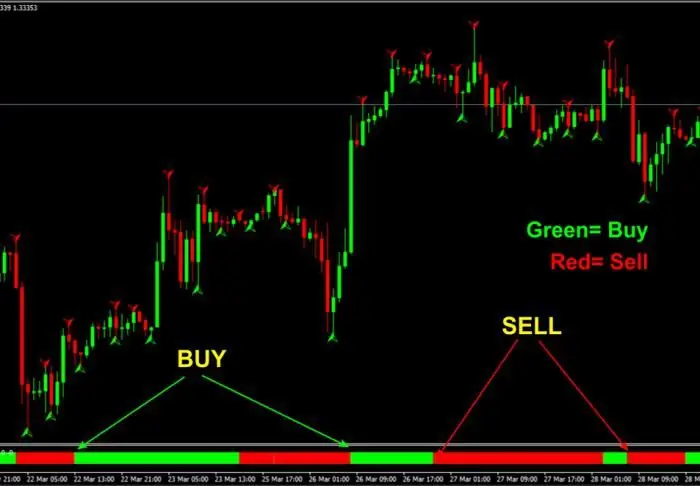
Forex indicator is an important currency market analysis tool that helps traders make optimal trading decisions
The most accurate indicators for MT4: rating. The best indicators for MT4
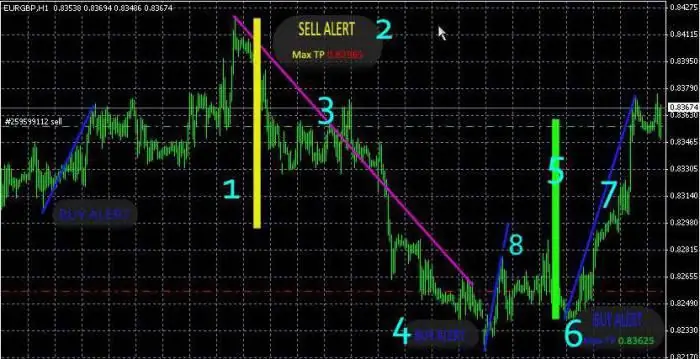
Are you a trader? Do you need the best indicators for MT4? We will talk about them in the article. In Forex trading, traders use an impressive number of various indicators with which they can accurately enter the market